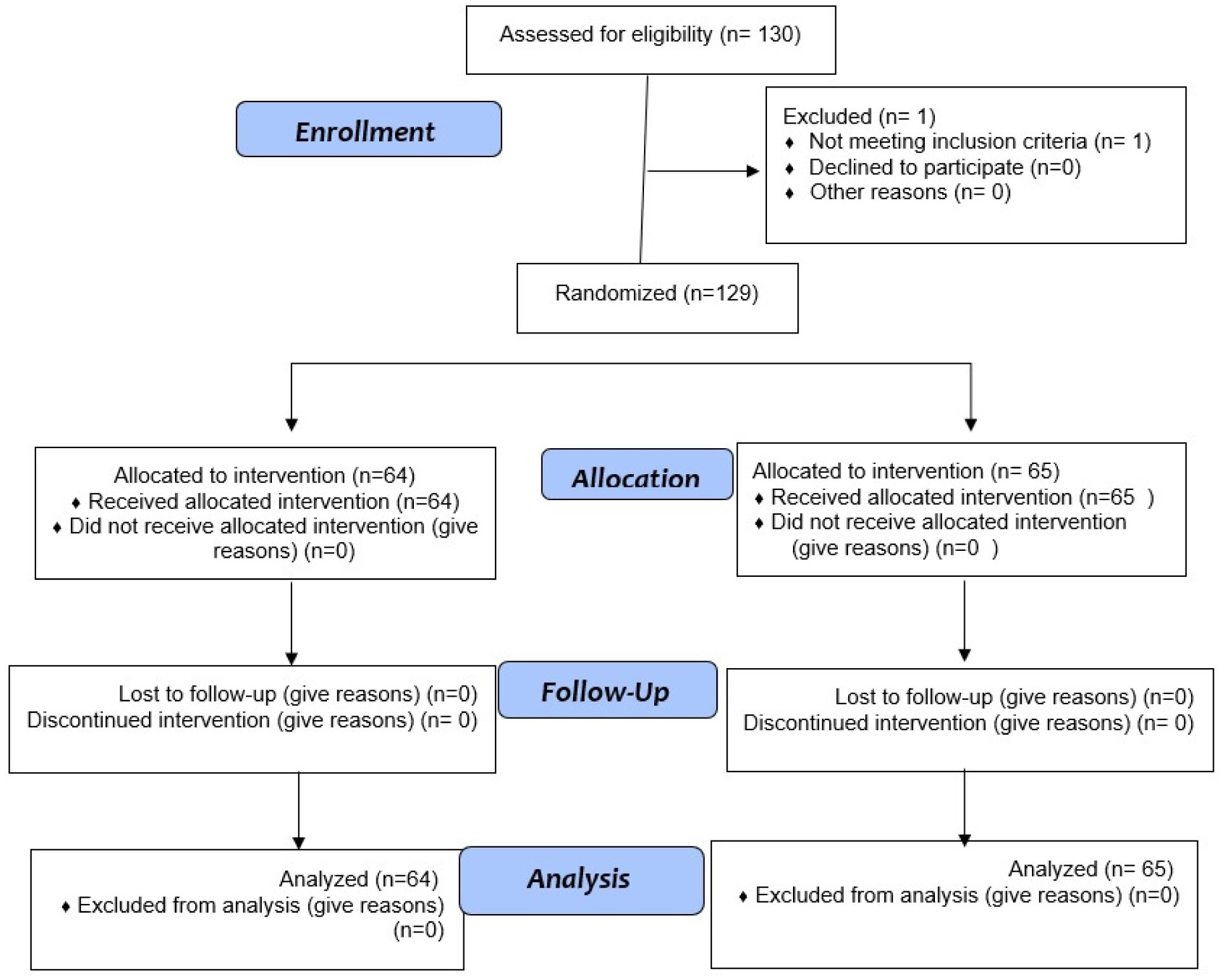
Citation: Saleh Rasras, Nour Mohammad Mamizadeh, Hossein Safari, Arash Kiani, Zahra Rahimi. Oral tranexamic acid for bleeding during spinal surgery: A randomized double-blind placebo clinical trial[J]. AIMS Medical Science, 2020, 7(2): 57-68. doi: 10.3934/medsci.2020005
[1] | Van Tuan Nguyen, Anh Tuan Tran, Nguyen Quyen Le, Thi Huong Nguyen . The features of computed tomography and digital subtraction angiography images of ruptured cerebral arteriovenous malformation. AIMS Medical Science, 2021, 8(2): 105-115. doi: 10.3934/medsci.2021011 |
[2] | Victor Okey Dinwoke, Michael Oluchukwu Amara, Linda Uzo Amara . Abdominal pregnancy—a diagnosis never to miss. AIMS Medical Science, 2022, 9(2): 342-347. doi: 10.3934/medsci.2022015 |
[3] | Taha Gökmen Ülger, Muhittin Tayfur, Funda Pınar Çakıroğlu, Çiğdem Özcan . The role of duodenal jejunal bypass liner in obesity treatment. AIMS Medical Science, 2021, 8(3): 224-236. doi: 10.3934/medsci.2021019 |
[4] | Sapana Shinde, Sayantoni Mukhopadhyay, Ghada Mohsen, Sok Kean Khoo . Biofluid-based microRNA Biomarkers for Parkinsons Disease: an Overview and Update. AIMS Medical Science, 2015, 2(1): 15-25. doi: 10.3934/medsci.2015.1.15 |
[5] | Annekathryn Goodman . Vitamin C and Cancer. AIMS Medical Science, 2016, 3(1): 41-51. doi: 10.3934/medsci.2016.1.41 |
[6] | Anuj A. Shukla, Shreya Podder, Sana R. Chaudry, Bryan S. Benn, Jonathan S. Kurman . Non-small cell lung cancer: epidemiology, screening, diagnosis, and treatment. AIMS Medical Science, 2022, 9(2): 348-361. doi: 10.3934/medsci.2022016 |
[7] | Juan José Rodríguez, Luis Ortega-Paz, Salvatore Brugaletta, Manel Sabaté . Impact of SGLT2i on cardiovascular outcomes and heart failure in patients with type 2 diabetes. AIMS Medical Science, 2018, 5(1): 67-79. doi: 10.3934/medsci.2018.1.67 |
[8] | Paul J Ross, Krishnie Srikandarajah, Julien de Naurois . Right versus left-sided colon cancer: Is it time to consider these as different diseases?. AIMS Medical Science, 2018, 5(3): 303-315. doi: 10.3934/medsci.2018.3.303 |
[9] | Derek A. Corica, Dylan M. Schaap, Trenton G. Mayberry, Braydon C. Cowan, Mark R. Wakefield, Yujiang Fang . New depths: exploring the current landscape of colorectal cancer. AIMS Medical Science, 2025, 12(1): 105-123. doi: 10.3934/medsci.2025008 |
[10] | Maureen C. Ashe, Khalil Merali, Nicola Edwards, Claire Schiller, Heather M. Hanson, Lena Fleig, Karim M. Khan, Wendy L. Cook, Heather A. McKay . Integrating research into clinical practice for hip fracture rehabilitation: Implementation of a pragmatic RCT. AIMS Medical Science, 2018, 5(2): 102-121. doi: 10.3934/medsci.2018.2.102 |
Spinal surgery is often associated with a high risk for intraoperative and postoperative bleeding, and most patients require transfusions of blood products [1]. Intraoperative and postoperative bleeding is recognized throughout the world as a crisis in the operating room [2],[3]. Bleeding in sensitive areas such as the nervous system is the main concern for surgical and anesthesiology teams; the discontinuation of blood vessels makes bleeding unavoidable. Moreover, accurate hemostasis may be inadequate, although it is an important principle of surgery. Reducing bleeding to maintain the hemodynamic stability of the patient and improve the field of surgery is important and reduces the need for the transfusion of blood products, thereby reducing complications such as hemolytic and non-hemolytic reactions, acute injury, viral and bacterial infections, hypothermia and coagulation disorders [4],[5]. Various methods have been investigated in studies, including the induction of controlled-hypotension during operation, the injection of various drugs during surgery, or replacing mechanical ventilation with positive pressure during anesthesia in patients to reduce the risk of intraoperative bleeding and the need for transfusion of blood products during and after the operation and to avoid the possible complications associated with transfusion. In many cases, the study results were positive [6]–[10]. Intraoperative and postoperative bleeding could lead to anemia, hematoma, and required blood transfusions, which may affect surgical outcomes [11]. Moreover, the associated blood transfusion may increase the risk of immunological complications and the mortality rate [12].
Antifibrinolytic therapy during the perioperative phase has been used to minimize blood loss and the need for blood transfusion [13]. This procedure has been shown to reduce blood loss during other types of surgery [14],[15]. Tranexamic acid (TXA) is a long-established antifibrinolytic drug and a derivative of the amino acid lysine, which causes the reversible competitive blockade of lysine binding sites on plasmin, plasminogen, and tissue plasminogen activators [16]. TXA has been shown to prevents platelet degradation by inhibiting plasmin and increases the formation of blood clots [11]. Numerous studies have shown that intraoperative blood loss decreased in response to the perioperative use of TXA [17]–[20]. Tranexamic acid has anti-thrombolytic anti-fibrinolytic effects. The antifibrinolytic potency of the drug is 5–10 times that of aminocaproic acid. In oral use, 30–50% of the drug is absorbed through the gastrointestinal tract and is not affected by food. Less than 5% of the drug is metabolized in the body.
It binds very little to protein (3%) and binds to plasminogen initially and in therapeutic concentrations but does not bind to albumin. The half-life of the drug is about 2 hours (in case of intravenous administration of 1 gram of the drug). The therapeutic concentrations of the drug (10 mcgr/ml) remain for 7–8 hours, including intravenous administration of 4 mg/Kg10 doses and oral administration (mg/Kg25). The maximum of the drug (95%) is excreted unchanged through the glomerular network of the kidney. In the case of intravenous administration of a dose (mg/Kg10) of the drug, about 90% of the drug is excreted within 24 hours after administration. The indications for use the drug include: bleeding control in oral surgery in hemophilia patients (prophylaxis and treatment to reduce the need for coagulation factor); treatment of severe local secondary hemorrhage for hyperfibrinolytic conditions, including nosebleeds, hyphema, menorrhagia and hemorrhage following surgery; bleeding due to thrombolytic agents such as alteplase (hereditary tissue plasminogen activator) anistreplase (streptokinase-plasminogen activating complex) Streptokinase or furokinase; bleeding after heart surgery or shunt portocaval, prostatectomy, nephrectomy or bladder surgery; accompanied by blood disorders such as aplastic anemia, hepatitis, cirrhosis, polycystic neoplastic disease or neoplastic disease of the urogenital system; treatment of hereditary angioedema (reduction of severity and frequency of severe bleeding). Due to the importance of bleeding during and after lumbar surgeries, the role of oral transgenic acid in this field has been less considered. Oral, topical, and intravenous routes are common for the administration of TXA; however, most studies have used TXA intravenously [20],[21]. Considering its advantages, including rapid absorption and painless administration, the oral administration of TXA may offer some protection against adverse effects. The current study aimed to evaluate the effect of oral Tranexamic acid (TXA) on the amount of bleeding during spinal surgery.
In this double-blind clinical trial, patients included those who had lumbar spinal cord and back pain disease, who needed fusion or who were candidates for bilateral or more or equal to two levels surgeries, and who referred to the Department of Neurosurgery, Golestan Hospital, Ahvaz, Southwest of Iran.
Inclusion criteria for the current study included: being in the age range of 20 to 75 years, lacking of cardiovascular disease, having discopathies with spinal fusion, and discopathies more than two levels or having a two-sided spinal cord.
Exclusion criteria included an unwillingness to participate in the study, abnormal bleeding (history of petechiae hemoptysis, purpura, hematemesis and so on), a platelet count < 150,000 (k), a history of thrombosis or embolism, severe allergies, use of intermittent medications with hemostasis in the blood, uncontrolled high blood pressure (BP > 160/90), and obesity (BMI > 30).
All patients underwent magnetic imaging, and after diagnosis, they became candidates for surgery. Patients included in the study provided informed consent for participation and the research objectives were explained to them. All patients meeting the study criteria were randomly divided into two equal groups (double-blind). TXA capsules were purchased and used as a drug. Also, the drug contents of the same TXA capsule were emptied and the empty TXA capsule was used as a placebo so that it did not differ in form from the original drug. It has a similar shape that was packaged separately in packs of 10, and on the packages the number 1, which contains the drug, and the number 2, which contains the placebo.
Based on pharmacological doses and according to previous studies, TXA was administered orally at 25 mg/kg four times a day before surgery and 500 mg in the morning of surgery.
QID dose of 25 mg/kg is a pharmacological dose of the drug that has been used in previous studies and has not shown certain side effects, yet. The double-blind was performed with a TXA capsule and a similar tablet. These packages were administered intermittently to patients who had been selected for study, and the patient and the statistical analyst did not know the type of drug or placebo. Depending on the time of referral of patients for surgery that were selected for study, the first patient was given medication (pack 1) and the second patient was given a placebo (pack 2), respectively. Patients were visited by an anesthetist and transferred to the operating room after a safe line for surgery. All patients with ASA I or II risk factors were included in the study and underwent general anesthesia by the same anesthetist. Only patients with decreased hemoglobin were given blood transfusions.
One hundred twenty-nine patients were divided randomly into two groups. The intervention group included 64 patients who received 25 mg/kg of TXA four times a day before the surgery and 500 mg in the morning of surgery. The placebo group included 65 patients who received a placebo. Randomization process was by patient selection based on the order of referral and surgical treatment, so that the first patient received the drug and the next patient received the placebo, and the sequence continued in the same manner.
Patients' vital signs were checked by electrocardiogram (ECG), pulse oximetry and non-invasive blood pressure measurements. The amount of bleeding during surgery was calculated based on the number of sterile pads used during the operation and the amount of bleeding collected in the suction device in milliliters. Each sterile pad soaked in blood was calculated to be 50 ml of bleeding. The suction blood contents at the end of the operation, which are marked in milliliters, are also collected by bleeding in sterile pads and reported in milliliters.
Patients received blood products if required. Coagulation was checked during and for 72 hours after the operation, and coagulation products were administered if necessary. Postoperative bleeding was calculated based on the amount of blood secreting within the Homo naval drain so that the blood content of each vacuum line of the drain was calculated to be 50 cc. Hemoglobin levels and blood counts were measured one day after surgery. Patients were followed up until discharge.
By eliminating at-risk groups, such as the elderly and those with heart disease, and having criteria for being excluded from the study, we wanted the study to be performed without any particular harm to patients.
Neither statistical analyst nor patients were aware of the type of prescription drug. After the data and the analysis results were collected, the type of each drug was identified and all surgeries were performed to control the confounding factors by a surgeon. All patients were anesthetized by the same anesthesiologist.
All ethical principles were observed. The researcher first obtained permission to conduct the study from the Research Deputy of Ahvaz Jundishapur University of Medical Sciences (IR.AJUMS.REC.1396.1125). The work and its cause were explained to all patients and informed consent was obtained from them. All patients were also assured that they could leave the study at any time, and their treatment would not be affected if they chose not to participate. Trial id: 40532; Clinical trial registry: IRCT20190525043701N1; Registration date: 2019-08-02.
Before the start of the study, by referring to Shapiro's article [22] in which the standard deviation and the volume of blood lost in the two groups of TXA and control are 1944 and 1795 units, respectively, and according to the researcher's opinion that the difference of 2000 units of lost blood volume is between the two groups are clinically important, using the software, a sample size of 114 people was calculated; however, the study was performed on 129 patients; although 114 patients were sufficient in terms of statistical calculation, we intended to include more samples in the study so that there would be more statistically accuracy.
According to statistical studies, at least 114 samples were needed and this study was performed on 129 patients. A multivariate analysis was performed. A normality test has been used. Data are presented as mean ± standard deviation. Fisher's exact test or the chi-square test (for categorical variables) and independent samples t-test (for numerical data) were used to assess between-group differences. Statistical analyses were performed using SPSS version 16.0 software (SPSS Inc., Chicago, IL, USA). All p-values less than 0.05 were considered indicative of a statistically significant difference. Statistical analysts were satisfied with the analysis method results.
Of the 129 patients, 69 (53.5%) were male and 60 (46.5%) were female. The mean age of the patients was 43.83 ± 11.87 years (range = 20–75 years).
The case group comprised 64 (49.6%) patients, and the control group was made up of 65 patients (50.4%). The mean age of the patients in the case group was 44.68 ± 11.99 years, and the mean age of the patients in the control group was 42.99 ± 11.79 years (range of all patients = 20–75 years). CONSORT 2010 Flow Diagram of both groups studied is shown in Figure 1.
Mann-Whitney's nonparametric test results of every six hypotheses are shown in Table 1.
Variables | Study groups | Number | Mean | Standard deviation | p-value |
Effect of oral TXA on the amount of bleeding (ml) | Intervention | 64 | 410.8 | 271.3 | 0.0002 |
Control | 65 | 824.3 | 475.9 | ||
Effect of oral TXA on the Hb levels (one day after surgery) | Intervention | 64 | 11.2 | 1.1 | 0.447 |
Control | 65 | 11.1 | 1.1 | ||
Effect of oral TXA on PTT levels | Intervention | 64 | 34.7 | 4.6 | 0.0001 |
Control | 65 | 31.7 | 3.3 | ||
Effect of oral TXA on PT levels | Intervention | 64 | 1.3 | 0.1 | 0.252 |
Control | 65 | 1.2 | 0.2 | ||
Effect of oral TXA on the hospitalization duration (based on numbers) | Intervention | 64 | 3.5 | 1.1 | 0.0001 |
Control | 65 | 4. | 1.5 | ||
Effect of oral TXA on the amount of blood lost from drains (50 cc for each drain line) | Intervention | 64 | 177.7 | 77.1 | 0.018 |
Control | 65 | 210.1 | 84.1 |
As Table 1 shows, the effect of oral TXA on the amount of bleeding during spinal surgery was statistically significant (p = 0.0002). Its effect on the difference in postoperative Hb levels compared with preoperative surgery levels in patients undergoing spinal surgery was not statistically significant. For INR levels, the p-value was higher than the error level. Therefore, the effect of oral TXA on the level of INR after spine surgery was not statistically significant, because the value of P was 0.2, which is higher than the error level. For PT levels, the p-value was higher than the error level. Therefore, the effect of oral TXA on PT levels after spinal surgery was not statistically significant. Its effects on the hospitalization duration of the patients undergoing spinal surgery and on the amount of blood lost from drains postoperatively in patients undergoing spinal surgery were statistically significant. The pre-and post-operative Hb levels of the two groups were also compared. The results of the Mann-Whitney Nonparametric test of the oral TXA effect on the incidence of nausea and vomiting after spinal surgery are shown in Table 2.
Groups | Nausea and vomiting | Frequency | Frequency percentage | P-value |
Intervention group | Yes | 24 | 37.5 | 0.0001 < 0.05 |
No | 40 | 62.5 | ||
Total | 64 | |||
Control group | Yes | 4 | 6.2 | |
No | 61 | 93.8 | ||
Total | 65 |
The effect of oral TXA on the incidence of nausea and vomiting after spinal surgery was statistically significant as was its effect on the level of coagulation tests after spinal surgery.
The results of the chi-square test of the second hypothesis for both groups are shown in Table 3.
Groups | Hb level | Before the operation | After the operation | p-value |
Intervention group | Mean | 12.8 | 11.2 | 0.002 < 0.05 |
Control group | Mean | 12.3 | 11.1 | 0.003 < 0.05 |
Nowadays, spine surgery has experienced the ever-increasing use of TXA. Early studies evaluating the efficacy of TXA included mainly of retrospective cohort and case series studies with heterogeneous patients [23],[24]. More new studies have included prospective clinical trials evaluating its efficacy in people undergoing various spinal procedures of different complexity [18],[25]. In 2008, an earlier meta-analysis on the use of TXA in spine surgery did not show an obvious advantage somewhat because of constraints in the method employed in the investigations [26]. Additional systematic reviews and meta-analyses of the available literature have emphasized the need for higher-powered studies with more consistency in terms of the procedure, dosage, and regimen utilized [27],[28]. TXA with a 100% bio-availability can be administrated through some ways—orally, topically, or intravenously [29].
It appears that no prior study has investigated the effect of oral TXA on reducing bleeding in spinal surgery. Therefore, this study investigated the effect of this drug on reducing bleeding and compared it with other studies. In our study, we used a TXA dose of 25 mg per kilogram of body weight divided into four doses in one day. For example, an 80 kg patient was given 2000 mg per day before surgery in four doses of 500 mg (two 250 mg capsules) and a single dose of 500 mg the morning before surgery. The results showed that oral TXA had a positive effect on the amount of intraoperative bleeding, the volume of intradrain blood loss after the operation and the hospitalization duration, and reduced the number of cases. However, there was no significant difference in the postoperative Hb levels in preoperative and coagulation factors, including PT, and PTT levels were even increased. According to the results, oral TXA increased the incidence of nausea and vomiting in the intervention group.
The results of a study by Paul et al. showed that the amount of intraoperative bleeding and the duration of hospitalization were significantly lower among patients receiving TXA than in the placebo group, which was consistent with the results of the current study [30].
Cheryian et al. investigated the effect of TXA on the rate of intraoperative bleeding during spinal surgery. The results of their study showed that oral TXA was associated with a reduction in intraoperative bleeding and a reduction in transfusion levels during the operation, compared with the placebo. Their results are consistent with those of the current study [31].
Cordoba et al. revealed the effect of TXA administration on reducing the volume of 24-hour bleeding in patients. The current results showed a significant difference between the patient and control groups in terms of volume of postoperative intradrain bleeding, which is consistent with the results of Cordoba et al. [32].
In a double-blinded study, Deylamani et al. examined the effect of TXA on reducing the amount of intraoperative bleeding in patients undergoing endoscopic sinus surgery, the rate of bleeding, the MAP (Mean Arterial Blood Pressure) during the operation and the duration of the operation. Their results showed that there was a significant difference between the two groups regarding the amount of intraoperative bleeding (p = 0.002) and MAP (p = 0.001). They concluded that the use of TXA is effective in reducing bleeding from endoscopic sinus surgery, which is consistent with the results of the present study for reducing the volume of intraoperative bleeding [33].
Aghadavoudi et al. reviewed 69 patients who had undergone a mastoidectomy during a randomized clinical trial and investigated the effect of TXA on intraoperative bleeding and surgeon satisfaction. The results of their study showed that the administration of TXA in mastoidectomy was associated with a reduction in the amount of intraoperative bleeding, which is consistent with the results of the current study, and with higher surgeon satisfaction [34].
In a clinical trial, Sarzaeem et al. examined 200 knee osteoarthritis patients who were candidates for knee replacement for the effect of TXA on intraoperative bleeding and Hb changes. In terms of reducing the amount of intraoperative bleeding, the results were consistent with the current study. Their results showed that TXA prevented Hb decline after surgery, but the results of the current study showed no significant difference between the measured Hb differences after surgery compared to before surgery. Thus, they were not consistent with the results achieved by Sarzaeem et al. This difference may be due to the difference in the number of examinations or the sample size [35]. The results of a study conducted by Shapiro et al. showed that TXA was effective in reducing intraoperative bleeding in scoliosis surgery, which was consistent with the results of the present study [22]. Cardenas et al. achieved results similar to those of the present study. In their study, the effects of the administration of TXA and a placebo in patients with spinal fusion surgery were compared. Their results indicated TXA was effective in reducing the amount of intraoperative bleeding.
The current research had some limitations, including a small sample size. More studies with a greater number of sample cases can be helpful in investigating the effect of TXA on spinal surgery. Also, surgical operations performed by a single surgeon and studies of a particular type of operation, such as single-tube discectomy, and surgeons accompanied by a single anesthetist may lead to better and more accurate results.
As a general conclusion, it can be stated that oral TXA significantly reduced the amount of bleeding during and after surgery and the duration of hospitalization in patients undergoing spinal surgery. Due to its anti-fibrinolytic properties, TXA helps control bleeding effectively. Consequently, the amount of intraoperative bleeding decreases with the administration of the TXA, but the related nausea and vomiting can affect the acceptance of routine use of TXA in patients. This medication has no effect on Hb changes and coagulation tests after the operation.
[1] | Smorgick Y, Baker KC, Bachison CC, et al. (2013) Hidden blood loss during posterior spine fusion surgery. Spine J 13: 877-881. |
[2] | Irita K (2011) Risk and crisis management in intraoperative hemorrhage: Human factors in hemorrhagic critical events. Korean J Anesthesiol 60: 151-160. |
[3] | Irita K (2014) Present status of critical hemorrhage and its management in the operating room. [Article in Japanese] Rinsho Byori 62: 1275-1279. |
[4] | Yang L, Vuylsteke A, Gerrard C, et al. (2013) Postoperative fibrinogen level is associated with postoperative bleeding following cardiothoracic surgery and the effect of fibrinogen replacement therapy remains uncertain. J Thromb Haemost 11: 1519-1526. |
[5] | McQuilten ZK, Crighton G, Engelbrecht S, et al. (2015) Transfusion interventions in critical bleeding requiring massive transfusion: A systematic review. Transfus Med Rev 29: 127-137. |
[6] | Yuan L, Bao NR, Zhao JN (2015) Progress on hidden blood loss after hip replacement. [Article in Chinese] Zhongguo gu shang = China J Orthop Traumatol 28: 378-382. |
[7] | Iorio J, Bennett J, Orlando G, et al. (2013) Does Amicar affect blood loss in patients with adolescent idiopathic scoliosis treated with pedicle screws and Ponte osteotomies?. Surg Technol Int 23: 291-295. |
[8] | Dhawale AA, Shah SA, Sponseller PD, et al. (2012) Are antifibrinolytics helpful in decreasing blood loss and transfusions during spinal fusion surgery in children with cerebral palsy scoliosis?. Spine 37: E549-555. |
[9] | Samdani A, Torre-Healy A, Asghar J, et al. (2008) Strategies to reduce blood loss during posterior spinal fusion for neuromuscular scoliosis: A review of current techniques and experience with a unique bipolar electrocautery device. Surg Technol Int 17: 243-248. |
[10] | Thompson GH, Florentino-Pineda I, Armstrong DG, et al. (2007) Fibrinogen levels following Amicar in surgery for idiopathic scoliosis. Spine 32: 368-372. |
[11] | Winter SF, Santaguida C, Wong J, et al. (2016) Systemic and topical use of tranexamic acid in spinal surgery: A systematic review. Global Spine J 6: 284-295. |
[12] | Marik PE, Corwin HL (2008) Efficacy of red blood cell transfusion in the critically ill: A systematic review of the literature. Crit Care Med 36: 2667-2674. |
[13] | Ngo K, Khemani R, Choi P, et al. (2013) Tranexamic acid reduces PRBC transfusion after posterior spine surgery for idiopathic scoliosis from the operating room to post-operative day four. J Anesthe Clin Res 4: 7. |
[14] | Brown JR, Birkmeyer N, O'Connor GT (2007) Meta-analysis comparing the effectiveness and adverse outcomes of antifibrinolytic agents in cardiac surgery. Circulation 115: 2801-2813. |
[15] | Alshryda S, Sarda P, Sukeik M, et al. (2011) Tranexamic acid in total knee replacement: A systematic review and meta-analysis. J Bone Joint Surgery British 93: 1577-1585. |
[16] | Hardy JF, Desroches J (1992) Natural and synthetic antifibrinolytics in cardiac surgery. Can J Anaesth 39: 353-365. |
[17] | Neilipovitz DT, Murto K, Hall L, et al. (2001) A randomized trial of tranexamic acid to reduce blood transfusion for scoliosis surgery. Anesth Analg 93: 82-87. |
[18] | Elwatidy S, Jamjoom Z, Elgamal E, et al. (2008) Efficacy and safety of prophylactic large dose of tranexamic acid in spine surgery: A prospective, randomized, double-blind, placebo-controlled study. Spine 33: 2577-2580. |
[19] | Yang B, Li H, Wang D, et al. (2013) Systematic review and meta-analysis of perioperative intravenous tranexamic acid use in spinal surgery. PloS One 8: e55436. |
[20] | Neilipovitz DT (2004) Tranexamic acid for major spinal surgery. Eur Spine J 13: S62-65. |
[21] | Horrow JC, Van Riper DF, Strong MD, et al. (1996) The Dose-Response relationship of tranexamic acid. Survey Anesthesiol 40: 9. |
[22] | Shapiro F, Zurakowski D, Sethna NF (2007) Tranexamic acid diminishes intraoperative blood loss and transfusion in spinal fusions for duchenne muscular dystrophy scoliosis. Spine 32: 2278-2283. |
[23] | Newton PO, Bastrom TP, Emans JB, et al. (2012) Antifibrinolytic agents reduce blood loss during pediatric vertebral column resection procedures. Spine 37: E1459-1463. |
[24] | Yagi M, Machida M (2012) Does the intraoperative tranexamic acid decrease operative blood loss during posterior spinal fusion for treatment of adolescent idiopathic scoliosis?. Spine J 12: S99. |
[25] | Wong J, El Beheiry H, Rampersaud YR, et al. (2008) Tranexamic acid reduces perioperative blood loss in adult patients having spinal fusion surgery. Anesth Analg 107: 1479-1486. |
[26] | Gill JB, Chin Y, Levin A, et al. (2008) The use of antifibrinolytic agents in spine surgery: A meta-analysis. J Bone Joint Surg Am 90: 2399-2407. |
[27] | Yuan C, Zhang H, He S (2013) Efficacy and safety of using antifibrinolytic agents in spine surgery: A meta-analysis. PLoS One 8: e82063. |
[28] | Yang B, Li H, Wang D, et al. (2013) Systematic review and meta-analysis of perioperative intravenous tranexamic acid use in spinal surgery. PloS one 8: e55436. |
[29] | Andersson L, Nilsson IM, Niléhn JE, et al. (1965) Experimental and clinical studies on AMCA, the antifibrinolytically active isomer of P-aminomethyl cyclohexane carboxylic acid. Scand J Haematol 2: 230-247. |
[30] | Myles PS, Smith JA, Forbes A, et al. (2017) Tranexamic acid in patients undergoing coronary-artery surgery. N Engl J Med 376: 136-148. |
[31] | Cheriyan T, Maier SP, Bianco K, et al. (2015) Efficacy of tranexamic acid on surgical bleeding in spine surgery: A meta-analysis. Spine J 15: 752-761. |
[32] | Cordoba R, Tapia B, Aramburu O, et al. (2014) Tranexamic acid reduces blood transfusion, postoperative blood loss and length of hospital stay in total knee arthroplasty. J Blood Disorders Transf 5: 207. |
[33] | Nuhi S, Tabrizi AG, Zarkhah L, et al. (2015) Impact of intravenous tranexamic acid on hemorrhage during endoscopic sinus surgery. Iran J Otorhinolaryngol 27: 349-354. |
[34] | Aghadavoudi O, Bonakdar HM, Hashempour H (2017) The effect of intravenous tranexamic acid on perioperative bleeding and surgeon's satisfaction during mastoidectomy. J Isfahan Med School 34: 1653-1659. |
[35] | Sarzaeem MM, Razi M, Kazemian G, et al. (2014) Comparing efficacy of three methods of tranexamic acid administration in reducing hemoglobin drop following total knee arthroplasty. J Arthroplasty 29: 1521-1524. |
Variables | Study groups | Number | Mean | Standard deviation | p-value |
Effect of oral TXA on the amount of bleeding (ml) | Intervention | 64 | 410.8 | 271.3 | 0.0002 |
Control | 65 | 824.3 | 475.9 | ||
Effect of oral TXA on the Hb levels (one day after surgery) | Intervention | 64 | 11.2 | 1.1 | 0.447 |
Control | 65 | 11.1 | 1.1 | ||
Effect of oral TXA on PTT levels | Intervention | 64 | 34.7 | 4.6 | 0.0001 |
Control | 65 | 31.7 | 3.3 | ||
Effect of oral TXA on PT levels | Intervention | 64 | 1.3 | 0.1 | 0.252 |
Control | 65 | 1.2 | 0.2 | ||
Effect of oral TXA on the hospitalization duration (based on numbers) | Intervention | 64 | 3.5 | 1.1 | 0.0001 |
Control | 65 | 4. | 1.5 | ||
Effect of oral TXA on the amount of blood lost from drains (50 cc for each drain line) | Intervention | 64 | 177.7 | 77.1 | 0.018 |
Control | 65 | 210.1 | 84.1 |
Groups | Nausea and vomiting | Frequency | Frequency percentage | P-value |
Intervention group | Yes | 24 | 37.5 | 0.0001 < 0.05 |
No | 40 | 62.5 | ||
Total | 64 | |||
Control group | Yes | 4 | 6.2 | |
No | 61 | 93.8 | ||
Total | 65 |
Groups | Hb level | Before the operation | After the operation | p-value |
Intervention group | Mean | 12.8 | 11.2 | 0.002 < 0.05 |
Control group | Mean | 12.3 | 11.1 | 0.003 < 0.05 |
Variables | Study groups | Number | Mean | Standard deviation | p-value |
Effect of oral TXA on the amount of bleeding (ml) | Intervention | 64 | 410.8 | 271.3 | 0.0002 |
Control | 65 | 824.3 | 475.9 | ||
Effect of oral TXA on the Hb levels (one day after surgery) | Intervention | 64 | 11.2 | 1.1 | 0.447 |
Control | 65 | 11.1 | 1.1 | ||
Effect of oral TXA on PTT levels | Intervention | 64 | 34.7 | 4.6 | 0.0001 |
Control | 65 | 31.7 | 3.3 | ||
Effect of oral TXA on PT levels | Intervention | 64 | 1.3 | 0.1 | 0.252 |
Control | 65 | 1.2 | 0.2 | ||
Effect of oral TXA on the hospitalization duration (based on numbers) | Intervention | 64 | 3.5 | 1.1 | 0.0001 |
Control | 65 | 4. | 1.5 | ||
Effect of oral TXA on the amount of blood lost from drains (50 cc for each drain line) | Intervention | 64 | 177.7 | 77.1 | 0.018 |
Control | 65 | 210.1 | 84.1 |
Groups | Nausea and vomiting | Frequency | Frequency percentage | P-value |
Intervention group | Yes | 24 | 37.5 | 0.0001 < 0.05 |
No | 40 | 62.5 | ||
Total | 64 | |||
Control group | Yes | 4 | 6.2 | |
No | 61 | 93.8 | ||
Total | 65 |
Groups | Hb level | Before the operation | After the operation | p-value |
Intervention group | Mean | 12.8 | 11.2 | 0.002 < 0.05 |
Control group | Mean | 12.3 | 11.1 | 0.003 < 0.05 |