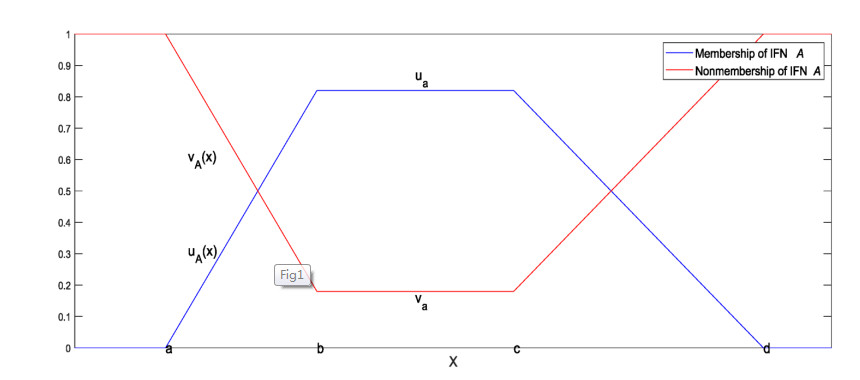
The relentless advancement of modern technology has given rise to increasingly intricate and sophisticated engineering systems, which in turn demand more reliable and intelligent fault diagnosis methods. This paper presents a comprehensive review of fault diagnosis in uncertain environments, focusing on innovative strategies for intelligent fault diagnosis. To this end, conventional fault diagnosis methods are first reviewed, including advances in mechanism-driven, data-driven, and hybrid-driven diagnostic models and their strengths, limitations, and applicability across various scenarios. Subsequently, we provide a thorough exploration of multi-source uncertainty in fault diagnosis, addressing its generation, quantification, and implications for diagnostic processes. Then, intelligent strategies for all stages of fault diagnosis starting from signal acquisition are highlighted, especially in the context of complex engineering systems. Finally, we conclude with insights and perspectives on future directions in the field, emphasizing the need for the continued evolution of intelligent diagnostic systems to meet the challenges posed by modern engineering complexities.
Citation: Chong Wang, Xinxing Chen, Xin Qiang, Haoran Fan, Shaohua Li. Recent advances in mechanism/data-driven fault diagnosis of complex engineering systems with uncertainties[J]. AIMS Mathematics, 2024, 9(11): 29736-29772. doi: 10.3934/math.20241441
[1] | Shichao Li, Zeeshan Ali, Peide Liu . Prioritized Hamy mean operators based on Dombi t-norm and t-conorm for the complex interval-valued Atanassov-Intuitionistic fuzzy sets and their applications in strategic decision-making problems. AIMS Mathematics, 2025, 10(3): 6589-6635. doi: 10.3934/math.2025302 |
[2] | Tareq Saeed . Intuitionistic fuzzy variational inequalities and their applications. AIMS Mathematics, 2024, 9(12): 34289-34310. doi: 10.3934/math.20241634 |
[3] | Zhuonan Wu, Zengtai Gong . Algebraic structure of some complex intuitionistic fuzzy subgroups and their homomorphism. AIMS Mathematics, 2025, 10(2): 4067-4091. doi: 10.3934/math.2025189 |
[4] | Nour Abed Alhaleem, Abd Ghafur Ahmad . Intuitionistic fuzzy normed prime and maximal ideals. AIMS Mathematics, 2021, 6(10): 10565-10580. doi: 10.3934/math.2021613 |
[5] | Doaa Al-Sharoa . (α1, 2, β1, 2)-complex intuitionistic fuzzy subgroups and its algebraic structure. AIMS Mathematics, 2023, 8(4): 8082-8116. doi: 10.3934/math.2023409 |
[6] | Muhammad Qiyas, Neelam Khan, Muhammad Naeem, Saleem Abdullah . Intuitionistic fuzzy credibility Dombi aggregation operators and their application of railway train selection in Pakistan. AIMS Mathematics, 2023, 8(3): 6520-6542. doi: 10.3934/math.2023329 |
[7] | Admi Nazra, Jenizon, Yudiantri Asdi, Zulvera . Generalized hesitant intuitionistic fuzzy N-soft sets-first result. AIMS Mathematics, 2022, 7(7): 12650-12670. doi: 10.3934/math.2022700 |
[8] | Adela Khamis, Abd Ghafur Ahmad . On fundamental algebraic characterizations of complex intuitionistic Q-fuzzy subfield. AIMS Mathematics, 2023, 8(3): 7032-7060. doi: 10.3934/math.2023355 |
[9] | Salma Iqbal, Naveed Yaqoob . Ranking of linear Diophantine fuzzy numbers using circumcenter of centroids. AIMS Mathematics, 2023, 8(4): 9840-9861. doi: 10.3934/math.2023497 |
[10] | Zhichun Xie, Rong Ma, Deqing Li, Qianhui Wan, Wenyi Zeng, Xianchuan Yu, Zeshui Xu . Intuitionistic fuzzy monotonic DOWA operators. AIMS Mathematics, 2023, 8(12): 30445-30461. doi: 10.3934/math.20231555 |
The relentless advancement of modern technology has given rise to increasingly intricate and sophisticated engineering systems, which in turn demand more reliable and intelligent fault diagnosis methods. This paper presents a comprehensive review of fault diagnosis in uncertain environments, focusing on innovative strategies for intelligent fault diagnosis. To this end, conventional fault diagnosis methods are first reviewed, including advances in mechanism-driven, data-driven, and hybrid-driven diagnostic models and their strengths, limitations, and applicability across various scenarios. Subsequently, we provide a thorough exploration of multi-source uncertainty in fault diagnosis, addressing its generation, quantification, and implications for diagnostic processes. Then, intelligent strategies for all stages of fault diagnosis starting from signal acquisition are highlighted, especially in the context of complex engineering systems. Finally, we conclude with insights and perspectives on future directions in the field, emphasizing the need for the continued evolution of intelligent diagnostic systems to meet the challenges posed by modern engineering complexities.
Tapezoidal intuitionistic fuzzy number (TIFN), as a special intuitionistic fuzzy set on a real number, has the best capability to model ill-known quantities [1,2]. TIFNs are useful to deal with uncertain knowledge and data in management decision and financial engineering problems. Intuitionistic fuzzy number, as the extension of fuzzy number, has more flexibility in many real-time uncertain application fields such as multi-criteria decision [3,4,5,6], portfolio selection [7,8], and agammaegation [9]. Recently, the possibility measure theory of TIFN plays an important role in many application fields like mulit-criteria decision and portfolio selection problem. For example, Chakraborty [10] utilized possibility, necessity and credibility measure to solve intuitionistic fuzzy optimization problem. Garai [11] applied possibility-necessity-credibility measures of generalized trapezoidal intuitionistic fuzzy number (GTIFN) to multi-product manufacturing system.
As is well known, based on possibility theory the possibilistic mean and variance of fuzzy numbers were presented by Carlsson and Full´er [12] and had been widely applied in solving fuzzy portfolio decision problems [13,14,15,16,17,18,19,20]. Recently, inspired by the above-mentioned fuzzy possibilistic mean theory Wan [21] proposed a definition of possibilistic mean and variance of intuitionistic fuzzy number (IFN). And Wan [22,23,24] utilized the possibilistic mean and variance to intuitionistic fuzzy group decision-making and matrix game problems with incomplete information. Later, Chen [25] also discussed the mean-variance-skewness portfolio selection problems based on intuitionistic fuzzy optimization under the assumption that the returns of assets are intuitionistic fuzzy numbers. Although the possibilistic mean and variance of intuitionistic fuzzy numbers will have a lot of application prospects, there is few study on the relationship between the possibilistic mean, variance and covariance of two generalized trapezoidal intuitionistic fuzzy numbers, and it is not clear whether subsethood entails smaller variance for generalized trapezoidal intuitionistic fuzzy number.
Moreover, we notice that the existing definitions of possibilistic mean and variance by Wan [21] have some flaws. In his definitions the denominators of the fraction of possibilistic mean and variance are improper because the level λ value and γ value are taken in [0, 1] for granted. However, the level λ value and γ level value of generalized trapezoidal intuitionistic fuzzy number ˜A indeed lie in the limited interval [0, ua] and [va, 1], respectively. To overcome the flaw of Wan's definition [21], in this paper we will correct it and introduce the new definitions of lower and upper possibilistic mean, variance of generalized trapezoidal intuitionistic fuzzy numbers based on possibility distributions. We also give some properties of possibilistic mean, covariance and variance, such as that the possibilistic variance of linear combinations of generalized trapezoidal intuitionistic fuzzy numbers can easily be computed like in probability theory and that subsethood does entail smaller variance. Moreover, in this paper we show that the possibilistic mean of generalized trapezoidal intuitionistic fuzzy number remains additive in the sense of addition of GTIFNs. In particular, we easily deduce Var(˜A)=Cov(˜A,˜A)=Cov(˜A,−˜A), which is not consistent with the properties of covariance in crisp probability theory. The contribution of this work is as follows. We show that the presented possibilistic variance and covariance of generalized trapezoidal intuitionistic fuzzy numbers reserve many important properties of variance and covariance in traditional probability theory, which is different from the known investigation results. We also investigate the important relationship between two kinds of possibilistic variance var(˜A) and var′(˜A) for generalized trapezoidal intuitionistic fuzzy numbers.
Let us first introduce some basic concepts of trapezoidal intuitionistic fuzzy numbers, which will be employed in the following sections.
Definition 1 [11,21]. A generalized trapezoidal intuitionistic fuzzy number (GTIFN) ˜A=((a,b,c,d);ua,va) is a special kind of intuitionistic fuzzy set on the real number set R, whose membership function and nonmembership function are defined as following forms, respectively (see Figure 1).
μ˜A(x)={ua(x−a)/(b−a),ifa⩽x<b,ua,ifb⩽x⩽c,ua(d−x)/(d−c),ifc<x⩽d,0,otherwise.v˜A(x)={va+(1−va)(b−x)/(b−a),ifa⩽x<b,va,ifb⩽x⩽c,va+(1−va)(x−c)/(d−c),ifc<x⩽d,1,otherwise. |
where ua,va are the greatest membership and the least nonmembership degree, respectively. And ua,va∈[0,1], 0⩽ua+va⩽1, π˜A(x)=1−μ˜A(x)−ν˜A(x) is called the hesitation degree of x∈˜A.
Remark 1 [22,24]. If b=c, then the generalized trapezoidal intuitionistic fuzzy number ˜A=((a,b,c,d);ua,va) is reduced to a generalized triangular intuitionistic fuzzy number ˜A=((a,b,d);ua,va).
Definition 2. Let ˜Ai=((ai,bi,ci,di),ui,vi), i=1,2, be two generalized trapezoidal intuitionistic fuzzy numbers, the addition and scale multiplication of GTIFNs [2,11,21,24,26] are defined as follows.
(1) ˜A1+˜A2=((a1+a2,b1+b2,c1+c2,d1+d2);ua1∧ua2,va1∨va2).
(2) x˜Ai=((xai,xbi,xci,xdi);ui,vi), ∀x⩾0. x˜Ai=((xdi,xci,xbi,xai);ui,vi), ∀x<0.
Definition 3 [22,24]. Let ˜A=((a,b,c,d);ua,va) be a generalized trapezoidal intuitionistic fuzzy number, the λ-level cut set and γ -cut set of membership and nonmembership of GTIFN ˜A are, respectively, defined as
˜A[λ]={x/μ˜A(x)⩾λ}=[a−(λ),a+(λ)]=[a+(b−a)λ/ua,d−(d−c)λ/ua)]; |
˜A[γ]={x/ν˜A(x)⩽γ}=[a−(γ),a+(γ)]=[(b−ava−γ(b−a))/(1−va),(c−dva+γ(d−c))/(1−va))]. |
where λ∈[0,ua], γ∈[va,1], and 0⩽λ+γ⩽1.
Theorem 1 [11,21]. Let ˜A1=((a1,b1,c1,d1);ua1,va1) , ˜A2=((a2,b2,c2,d2);ua2,va2) be two generalized trapezoidal intuitionistic fuzzy numbers, for any positive real number λ∈(0,ua], γ∈[va,1] , we can easily get
(1) (˜A1+˜A2)[λ]=˜A1[λ]+˜A2[λ]=[a1−(λ)+a2−(λ),a1+(λ)+a2+(λ)], ∀λ∈(0,ua];
(2) (˜A1+˜A2)[γ]=˜A1[γ]+˜A2[γ]=[a1−(γ)+a2−(γ),a1+(γ)+a2+(γ)], ∀γ∈[va,1];
(3) (x˜A)[λ]=x˜A[λ]=[xa−(λ),xa+(λ)],∀x⩾0; (x˜A)[λ]=x˜A[λ]=[xa+(λ),xa−(λ)],∀x<0;
(4) (x˜A)[γ]=x˜A[γ]=[xa−(γ),xa+(γ)],∀x⩾0; (x˜A)[γ]=x˜A[γ]=[xa+(γ),xa−(γ)],∀x<0.
The proof is straightforward from Definition 3 and Zadeh's fuzzy extension principle.
Definition 4 [21]. Let ˜A=((a,b,c,d);ua,va) be a generalized trapezoidal intuitionistic fuzzy number, the lower and upper possibilistic mean value of the membership function of GTIFN ˜A are, respectively, defined as
M−μ(˜A)=∫ua0pos(μ˜A⩽a−(λ))a−(λ)dλ∫ua0pos(μ˜A⩽a−(λ))dλ=∫ua0λa−(λ)dλ∫ua0λdλ=2u2a∫ua0λa−(λ)dλ=13(a+2b); |
M+μ(˜A)=∫ua0pos(μ˜A⩾a+(λ))a+(λ)dλ∫ua0pos(μ˜A⩾a+(λ))dλ=∫ua0λa+(λ)dλ∫ua0λdλ=2u2a∫ua0λa+(λ)dλ=13(d+2c). |
The possibilistic mean of membership of GTIFN ˜A can also be defined as
Mμ(˜A)=[M−μ(˜A)+M+μ(˜A)]2==1u2a∫ua0λ(a−(λ)+a+(λ))dλ=16(a+2b+2c+d). |
Definition 5. ˜A=((a,b,c,d);ua,va) be a generalized trapezoidal intuitionistic fuzzy number, the lower and upper possibilistic mean value of the nonmembership function of GTIFN ˜A are, respectively, defined as
M−ν(˜A)=∫1vapos(b⩾ν˜A⩾a−(γ))a−(γ)dγ∫1vapos(b⩾ν˜A⩾a−(γ))dγ=∫1vaγa−(γ)dγ∫1vaγdγ=21−v2a∫1vaγa−(γ)dγ |
=11−v2a[(b−ava)(1+va)−23(b−a)(1+va+v2a)]; |
M+ν(˜A)=∫1vapos(c⩽ν˜A⩽a+(γ))a+(γ)dγ∫1vapos(c⩽ν˜A⩽a+(γ))dγ=∫1vaγa+(γ)dγ∫1vaγdγ=21−v2a∫1vaγa+(γ)dγ |
=11−v2a[(c−dva)(1+va)+23(d−c)(1+va+v2a)]. |
The possibilistic mean of nonmembership of GTIFN ˜A can also be defined as
Mν(˜A)=[M−ν(˜A)+M+ν(˜A)]2=11−v2a∫1vaγ(a−(γ)+a+(γ))dγ=11−v2a[12(b+c−(a+d)va)(1+va)+13(a−b−c+d)(1+va+v2a)]. |
Definition 6. Let ˜A=((a,b,c,d);ua,va) be a generalized trapezoidal intuitionistic fuzzy number, the possibilistic mean value of GTIFN ˜A is defined as M(˜A)=12[Mμ(˜A)+Mν(˜A)].
Definition 7. Let ˜A=((a,b,c,d);ua,va) be a GTIFN with λ,γ cut set ˜A[λ]=[a−(λ),a+(λ)], ˜A[γ]=[a−(γ),a+(γ)] of membership and nonmembership of ˜A, the possibilistic variance of membership and nonmembership of GTIFN ˜A are respectively defined as [21,22],
varμ(˜A)=12∫ua0(a−(λ)−a+(λ))2λdλ=124u2a[(d−a)2−2(d−a)(b−c)+3(b−c)2]; |
varν(˜A)=12∫1va(a−(γ)−a+(γ))2γdγ=124(1−va)[6(1+va)M2+8(1+va+v2a)MN+3(1+va+v2a+v3a)N2], |
where M=c−b+(a−d)va, N=d−c+b−a.
Hence, the variance of GTIFN ˜A can be defined by var(˜A)=12[varμ(˜A)+varv(˜A)].
Definition 8. Let ˜A1=((a1,b1,c1,d1);ua,va) be a GTIFN with λ,γ cut set ˜A1[λ]=[a−1(λ),a+1(λ)], ˜A1[γ]=[a−1(γ),a+1(γ)] and GTIFN ˜A2=((a2,b2,c2,d2);ua,va) with λ,γ cut set ˜A2[λ]=[a−2(λ),a+2(λ)], ˜A2[γ]=[a−2(γ),a+2(γ)] of membership and nonmembership, the possibilistic covariance of membership and nonmembership of GTIFNs ˜A1,˜A2 are respectively defined as [17,19],
covμ(˜A1,˜A2)=12∫ua0(a+1(λ)−a−1(λ))(a+2(λ)−a−2(λ))λdλ; |
covν(˜A1,˜A2)=12∫1va(a+1(γ)−a−1(γ))(a+2(γ)−a−2(γ))γdγ. |
The covariance of GTIFNs ˜A1,˜A2 can be also defined by cov(˜A1,˜A2)=12[covμ(˜A1,˜A2)+covv(˜A1,˜A2)].
Definition 9. ˜A=((a,b,c,d);ua,va) be a GTIFN with λ cut set ˜A[λ]=[a−(λ),a+(λ)] of membership and γ cut set ˜A[γ]=[a−(γ),a+(γ)] of nonmembership, the new possibilistic variance of membership and nonmembership of GTIFN ˜A are respectively defined as
var′μ(˜A)=∫ua0[(Mμ(˜A)−a−(λ))2+(Mμ(˜A)−a+(λ))2]λdλ; |
var′ν(˜A)=∫1va[(Mv(A)−a−(γ))2+(Mv(A)−a+(γ))2]γdγ. |
The new possibilistic variance of GTIFN ˜A can also be computed by var′(˜A)=12[var′μ(˜A)+var′v(˜A)]; where a−(λ),a+(λ) is the lower bound and upper bound of λ level interval value of membership of GTIFN ˜A, var′μ(˜A) expresses the weighted deviation squares between the membership mean and lower bound, upper bound of λ level interval of membership of ˜A; and a−(γ),a+(γ) is the lower bound and upper bound of λ level interval of nonmembership of GTIFN ˜A, var′ν(˜A) expresses the weighted deviation squares between the nonmembership mean and lower bound, upper bound of λ level interval of nonmembership of ˜A. However, the existing varμ(˜A) only indicates the weighted deviation squares between lower bound and upper bound of λ level interval of membership of ˜A; varv(˜A) only indicates the weighted deviation squares between lower bound and upper bound of λ level interval of nonmembership of ˜A. Moreover, the above-mentioned definition 9 of possibilistic variance coincides with the definition of crisp variance, so it is more meaningful and rathional than the existing possibilistic variance of GTIFN ˜A.
Definition 10. Let ˜A1=((a1,b1,c1,d1);ua,va) be a GTIFN with λ,γ cut set ˜A1[λ]=[a−1(λ),a+1(λ)] , ˜A1[γ]=[a−1(γ),a+1(γ)] and TIFN ˜A2=((a2,b2,c2,d2);ua,va) with λ,γ cut set ˜A2[λ]=[a−2(λ),a+2(λ)] , ˜A2[γ]=[a−2(γ),a+2(γ)] of membership and nonmembership, the new possibilistic covariance of membership and nonmembership of TIFNs ˜A1,˜A2 are respectively defined as
cov′μ(˜A1,˜A2)=∫ua0[(Mμ(˜A1)−a1−(λ))(Mμ(˜A2)−a−2(λ))+(Mμ(˜A1)−a1+(λ))(Mμ(˜A2)−a2+(λ))]λdλ;cov′ν(˜A1,˜A2)=∫1va[(Mν(˜A1)−a1−(γ))(Mν(˜A2)−a−2(γ))+(Mν(˜A1)−a1+(γ))(Mν(˜A2)−a2+(γ))]γdγ. |
The new covariance of GTIFNs ˜A1,˜A2 can be computed by cov′(˜A1,˜A2)=12[cov′μ(˜A1,˜A2)+cov′v(˜A1,˜A2)].
Theorem 2. Let
(1) M(˜A1+˜A2)=M(˜A1)+M(˜A2);
(2) M(x˜A1)=xM(˜A1), ∀x∈R;
(3) M(x1˜A1+x2˜A2)=x1M(˜A1)+x2M(˜A2), ∀x1,x2∈R.
Proof. (1) It follows from Definitions 4, 5 and Theorem 1 that
Mμ(˜A1+˜A2)=1u2a∫ua0λ[(a−1(λ)+a−2(λ))+(a+1(λ)+a+2(λ))]dλ=1u2a∫ua0λ[(a−1(λ)+a+1(λ))+(a−2(λ)+a+2(λ))]dλ |
=1u2a[∫ua0λ(a−1(λ)+a+1(λ))dλ+∫ua0λ(a−2(λ)+a+2(λ))dλ] |
=Mμ(˜A1)+Mμ(˜A2); |
Mv(˜A1+˜A2)=11−v2a∫1vaγ[(a−1(γ)+a−2(γ))+(a+1(γ)+a+2(γ))]dγ=11−v2a∫1vaγ[(a−1(γ)+a+1(γ))+(a−2(γ)+a+2(γ))]dγ |
=11−v2a[∫1vaγ(a−1(γ)+a+1(γ))dλ+∫1vaγ(a−2(γ)+a+2(γ))dγ] |
=Mv(˜A1)+Mv(˜A2). |
Therefore, we have
M(˜A1+˜A2)=Mμ(˜A1+˜A2)+Mv(˜A1+˜A2)2=M(˜A1)+M(˜A2). |
(2) By Definitions 4, 5 and Theorem 1, for any x≥0 we easily get
Mμ(x˜A1)=1u2a∫ua0[x(a−1(λ)+a+1(λ))]λdλ=x[1u2a∫ua0λ(a−1(λ)+a+1(λ))dλ]=xMμ(˜A1); |
Mv(x˜A1)=11−v2a∫1va[x(a−1(γ)+a+1(γ))]γdγ=x[11−v2a∫1vaγ(a−1(γ)+a+1(γ))dγ]=xMv(˜A1). |
For any x<0, we also get
Mμ(x˜A1)=1u2a∫ua0[x(a+1(λ)+a−1(λ))]λdλ=x[1u2a∫ua0λ(a+1(λ)+a−1(λ))dλ]=xMμ(˜A1); |
Mv(x˜A1)=11−v2a∫1va[x(a+1(γ)+a−1(γ))]γdγ=x[11−v2a∫1vaγ(a+1(γ)+a−1(γ))dγ]=xMv(˜A1). |
So we have
M(x˜A1)=Mμ(x˜A1)+Mv(x˜A1)2=xMμ(˜A1)+xMv(˜A1)2=xM(˜A1). |
(3) From (1), (2) we easily conclude that, for any x1,x2∈R,
Mμ(x1˜A1+x2˜A2)=Mμ(x1˜A1)+Mμ(x2˜A2)=x1Mμ(˜A1)+x2Mμ(˜A2); |
Mv(x1˜A1+x2˜A2)=Mv(x1˜A1)+Mv(x2˜A2)=x1Mv(˜A1)+x2Mv(˜A2). |
Hence, M(x1˜A1+x2˜A2)= Mμ(x1˜A1+x2˜A2)+Mv(x1˜A1+x2˜A2)2=x1M(˜A1)+x2M(˜A2).
Theorem 3.1. Let ˜A1=((a1,b1,c1,d1);ua1,va1) be a GTIFN with λ,γ cut set ˜A1[λ]=[a−1(λ),a+1(λ)] , ˜A1[γ]=[a−1(γ),a+1(γ)] and GTIFN ˜A2=((a2,b2,c2,d2);ua2,va2) with λ,γ cut set ˜A2[λ]=[a−2(λ),a+2(λ)] , ˜A2[γ]=[a−2(γ),a+2(γ)] and μa1=μa2=μa,va1=va2=va , and let constant θ∈R . Then we have
(1) cov(˜A1,˜A2)=cov(˜A2,˜A1);
(2) var(˜A1)=cov(˜A1,˜A1)=cov(˜A1,−˜A1);
(3) var(˜A1+θ)=var(˜A1).
Proof. (1), (2) can be directly verified by Definition 8 of cov(˜A1,˜A2) and Definition 7 of var(˜A1).
(3) For any θ∈R, by Zadeh's fuzzy extension principle we can know that (˜A1+θ)(x)=˜A1(x−θ), and
(˜A1+θ)[λ]=˜A[λ]1+θ=[a−1(λ)+θ,a+1(λ)+θ]; (˜A1+θ)[γ]=˜A[γ]1+θ=[a−1(γ)+θ,a+1(γ)+θ]. |
So, varμ(˜A1+θ)=12∫ua0[(a1−(λ)+θ)−(a1+(λ)+θ)]2λdλ=12∫ua0[a1−(λ)−a1+(λ)]2λdλ=varμ(˜A1);
varv(˜A1+θ)=12∫1va[(a1−(γ)+θ)−(a1+(λ)+θ)]2γdγ=12∫1va[a1−(γ)−a1+(λ)]2γdγ=varv(˜A1).
Hence, we have var(˜A1+θ)=varμ(˜A1+θ)+varv(˜A1+θ)2=varμ(˜A1)+varv(˜A1)2=var(˜A1).
Theorem 3.2. Let ˜A1=((a1,b1,c1,d1);ua1,va1) be a GTIFN with λ,γ cut set ˜A1[λ]=[a1−(λ),a1+(λ)], ˜A1[γ]=[a1−(γ),a1+(γ)] and GTIFN ˜A2=((a2,b2,c2,d2);ua2,va2) with λ,γ cut set ˜A2[λ]=[a2−(λ),a2+(λ)], ˜A2[γ]=[a2−(γ),a2+(γ)], and μa1=μa2=μa,va1=va2=va, and for any constant θ∈R, we also obtain
(1) cov′(˜A1,˜A2)=cov′(˜A2,˜A1);
(2) var′(˜A1)=cov′(˜A1,˜A1);
(3) var′(˜A1+θ)=var′(˜A1).
Proof. (1), (2) can be directly proved by Definition 10 of cov′(˜A1,˜A2) and Definition 9 of var′(˜A1).
(3) Since (˜A1+θ)(x)=˜A1(x−θ), we know that
(˜A1+θ)[λ]=˜A[λ]1+θ=[a−1(λ)+θ,a+1(λ)+θ]; (˜A1+θ)[γ]=˜A[γ]1+θ=[a−1(γ)+θ,a+1(γ)+θ]. |
So, var′μ(˜A1+θ)=∫ua0[(Mμ(˜A1+θ)−(a1−(λ)+θ))2+(Mμ(˜A1+θ)−(a1+(λ)+θ))2]λdλ |
=∫ua0[(Mμ(˜A1)+θ−a1−(λ)−θ)2+(Mμ(˜A1)+θ−a1+(λ)−θ)2]λdλ=∫ua0[(Mμ(˜A1)−a1−(λ))2+(Mμ(˜A1)−a1+(λ))2]λdλ=var′(˜A1); |
var′ν(˜A1+θ)=∫1va[(Mv(˜A1+θ)−(a1−(γ)+θ))2+(Mv(˜A1+θ)−(a1+(γ)+θ))2]γdγ=∫1va[(Mv(˜A1)−a1−(γ))2+(Mv(˜A1)−a1+(γ))2]γdγ=var′ν(˜A1); |
So, we get var′(˜A1+θ)=var′(˜A1).
Theorem 3.1-3.2 show that possibilistic covariances have symmetry, the covariance between GTIFN itself reduces to the possibilistic variance of GTIFN. And if a GTIFN shifts a constant, the possibilistic variance is not altered.
Theorem 3.3. Let ˜A1=((a1,b1,c1,d1);ua1,va1) be a GTIFN with λ,γ cut set ˜A1[λ]=[a1−(λ),a1+(λ)] , ˜A1[γ]=[a1−(γ),a1+(γ)] and GTIFN ˜A2=((a2,b2,c2,d2);ua2,va2) with λ,γ cut set ˜A2[λ]=[a2−(λ),a2+(λ)] , ˜A2[γ]=[a2−(γ),a2+(γ)] , and μa1=μa2=μa,va1=va2=va , for any x1,x2∈R , then
var(x1˜A1+x2˜A2)=x12var(˜A1)+x22var(˜A2)+2|x1x2|cov(˜A1,˜A2) |
Proof. We only verify that the above formula holds in the case (1) if x1<0, x2>0.
By employing Theorem 1 we can easily know that
(x1˜A1+x2˜A2)[λ]=[x1a+1(λ)+x2a−2(λ),x1a−1(λ)+x2a+2(λ)]; |
(x1˜A1+x2˜A2)[γ]=[x1a+1(γ)+x2a−2(γ),x1a−1(γ)+x2a+2(γ)]; |
So, by Definitions 7, 8 we easily get
varμ(x1˜A1+x2˜A2) |
=12∫ua0λ[(x1a+1(λ)+x2a−2(λ))−(x1a−1(λ)+x2a+2(λ))]2dλ |
=12∫ua0λ[x1(a+1(λ)−a−1(λ))−x2(a+2(λ)−a−2(λ))]2dλ=12{∫ua0λx21(a+1(λ)−a−1(λ))2dλ+∫ua0λx22(a+2(λ)−a−2(λ))2dλ−∫ua02λx1x2(a+1(λ)−a−1(λ))(a+2(λ)−a−2(λ))dλ}=x12varμ(˜A1)+x22varμ(˜A2)−2x1x2covμ(˜A1,˜A2) |
=x12varμ(˜A1)+2|x1x2|covμ(˜A1,˜A2)+x22varμ(˜A2); |
and
varv(x1˜A1+x2˜A2) |
=12∫1vaγ[(x1a+1(γ)+x2a−2(γ))−(x1a1−(γ)+x2a+2(γ))]2dγ=12{∫1vaγx21(a+1(γ)−a−1(γ))2dγ+∫1vaγx22(a−2(γ)−a+2(γ))2dγ−∫1va2γx1x2(a+1(γ)−a−1(γ))(a+2(γ)−a−2(γ))dγ}=x12varv(˜A1)+x22varv(˜A2)−2x1x2covv(˜A1,˜A2) |
=x12varv(˜A1)+2|x1x2|covv(˜A1,˜A2)+x22varv(˜A2). |
So, we get var(x1˜A1+x2˜A2)=varμ(x1˜A1+x2˜A2)+varν(x1˜A1+x2˜A2)2
=x12var(˜A1)+2|x1x2|cov(˜A1,˜A2)+x22var(˜A2). |
Similar reasoning holds for the other cases (2) x1>0, x2>0, (3) x1>0, x2<0 and (4) x1⩽0, x2⩽0.
It follows that var(x1˜A1+x2˜A2)=x12var(˜A1)+x22var(˜A2)+2|x1x2|cov(˜A1,˜A2) for any x1,x2∈R.
Theorem 3.3 show that the possibilistic variance of linear combinations of generalized trapezoidal intuitionistic fuzzy numbers can be computed like in probability theory, which reserves the same property of crisp variance.
Theorem 3.4. Let ˜A1=((a1,b1,c1,d1);ua1,va1) be a GTIFN with λ,γ cut set ˜A1[λ]=[a1−(λ),a1+(λ)] , ˜A1[γ]=[a1−(γ),a1+(γ)] and GTIFN ˜A2=((a2,b2,c2,d2);ua2,va2) with λ,γ cut set ˜A2[λ]=[a2−(λ),a2+(λ)] , ˜A2[γ]=[a2−(γ),a2+(γ)] , and μa1=μa2=μa,va1=va2=va , for any x,x1,x2∈R , then
var′(x1˜A1+x2˜A2)=x12var′(˜A1)+x22var′(˜A2)+2|x1x2|cov′(φ(x1)˜A1,φ(x2)˜A2), |
where φ(x) is a signal function of x∈R.
Proof. We only need to prove it in the case (1) when x1>0, x2<0.
By using Theorem 1 we easily have
(x1˜A1+x2˜A2)[λ]=[x1a−1(λ)+x2a+2(λ),x1a+1(λ)+x2a−2(λ)]; |
(x1˜A1+x2˜A2)[γ]=[x1a−1(γ)+x2a+2(γ),x1a+1(γ)+x2a−2(γ)]. |
With Definitions 9, 10 and Theorem 2 we get
var′μ(x1˜A1+x2˜A2)=∫ua0[Mμ(x1˜A1+x2˜A2)−(x1a1−(λ)+x2a2+(λ))]2λdλ+[Mμ(x1˜A1+x2˜A2)−(x1a1+(λ)+x2a2−(λ))]2λdλ=∫ua0{[x1Mμ(˜A1)+x2Mμ(˜A2)−x1a1−(λ)−x2a2+(λ)]2+[x1Mμ(˜A1)+x2Mμ(˜A2)−x1a1+(λ)−x2a2−(λ)]2}λdλ=∫ua0{[x1(Mμ(˜A1)−a1−(λ))+x2(Mμ(˜A2)−a2+(λ))]2+[x1(Mμ(˜A1)−a1+(λ))+x2(Mμ(˜A2)−a2−(λ))]2}λdλ=x12var′μ(˜A1)+2x1x2∫ua0λ[(M(˜A1)−a1−(λ))(Mμ(˜A2)−a2+(λ))+(Mμ(˜A1)−a1+(λ))(Mμ(˜A2)−a2−(λ))]dλ+x22var′μ(˜A2)=x12var′μ(˜A1)−2x1x2∫ua0λ[(M(˜A1)−a1−(λ))(Mμ(−˜A2)+a2+(λ))+(Mμ(˜A1)−a1+(λ))(Mμ(−˜A2)+a2−(λ)))]dλ+x22var′μ(˜A2)=x12var′μ(˜A1)−2x1x2cov′μ(˜A1,−˜A2)+x22var′μ(˜A2)=x12var′μ(˜A1)+2|x1x2|cov′μ(φ(x1)˜A1,φ(x2)˜A2)+x22var′μ(˜A2); |
By Definitions 9, 10 and Theorem 2 we also get
var′v(x1˜A1+x2˜A2)=∫1va[Mv(x1˜A1+x2˜A2)−(x1a1−(γ)+x2a2+(γ)]2γdγ+[Mv(x1˜A1+x2˜A2)−(x1a1+(γ)+x2a2−(γ))]2γdγ=∫1va[x1Mv(˜A1)+x2Mv(˜A2)−x1a1−(γ)−x2a2+(γ)]2+[x1Mv(˜A1)+x2Mv(˜A2)−x1a1+(γ)−x2a2−(γ)]2}γdγ=∫1va[x1(Mv(˜A1)−a1−(γ))+x2(Mv(˜A2)−a2+(γ))]2+[x1(Mv(˜A1)−a1+(γ))+x2(Mv(˜A2)−a2−(γ))]2}γdγ=x12var′v(˜A1)−2x1x2∫1vaγ[(Mv(˜A1)−a1−(γ))(Mv(−˜A2)+a2+(γ))+(Mv(˜A1)−a1+(γ))(Mv(−˜A2)+a2−(γ))]dγ+x22var′v(˜A2)=x12var′v(˜A1)−2x1x2cov′v(˜A1,−˜A2)+x22var′v(˜A2)=x12var′v(˜A1)+2|x1x2|cov′v(φ(x1)˜A1,φ(x2)˜A2)+x22var′v(˜A2). |
Hence, we verify that
var′(x1˜A1+x2˜A2)=12[var′μ(x1˜A1+x2˜A2)+var′v(x1˜A1+x2˜A2)] |
=x12var′(˜A1)+2|x1x2|cov′(φ(x1)˜A1,φ(x2)˜A2)+x22var′(˜A2). |
Similar reasoning holds for the other cases (2) x1>0 , x2>0; (3) x1<0 , x2>0 and (4) x1⩽0, x2⩽0, which ends the proof.
Theorem 3.4. shows that the new possibilistic variance of linear combinations of generalized trapezoidal intuitionistic fuzzy numbers can also be computed like in probability theory, which reserves the similar property of crisp variance in traditional probability space.
Theorem 3.5. Let ˜A1=((a1,b1,c1,d1);ua1,va1) be a GTIFN with λ,γ cut set ˜A1[λ]=[a1−(λ),a1+(λ)] , ˜A1[γ[=[a1−(γ),a1+(γ)] and GTIFN ˜A2=((a2,b2,c2,d2);ua2,va2) with λ,γ cut set ˜A2[λ]=[a2−(λ),a2+(λ)] , ˜A2[γ[=[a2−(γ),a2+(γ)] , μa1=μa2=μa,va1=va2=va , and ˜A1⊂˜A2 . Then we have
(1) var(˜A1)⩽var(˜A2), (2) var′(˜A1)⩽var′(˜A2).
Proof.
(1) From ˜A1⊂˜A2 it follows that a−2(λ)⩽a−1(λ)⩽a+1(λ)⩽a+2(λ) and a−2(γ)⩽a−1(γ)⩽a+1(γ)⩽a+2(γ).
For all λ∈(0,ua), γ∈(va,1). That is to say, M−μ(˜A2)⩽M−μ(˜A1)⩽M+μ(˜A1)⩽M+μ(˜A2).
Hence, varμ(˜A1)=12∫ua0[a+1(λ)−a−1(λ)]2λdλ⩽12∫ua0[a+2(λ)−a−2(λ)]2λdλ=varμ(˜A2),
varv(˜A1)=12∫1va[a+1(γ)−a−1(γ)]2γdγ⩽12∫1va[a+2(γ)−a−2(γ)]2γdγ=varv(˜A2).
So, we have
var(˜A1)=varμ(˜A1)+varν(˜A1)2⩽varμ(˜A2)+varν(˜A2)2=var(˜A2). |
(2) From Definition 9, we know that
var′μ(˜A2)−var′μ(˜A1)=∫ua0{[Mμ(˜A2)−a2−(λ)]2+[Mμ(˜A2)−a2+(λ)]2}λdλ−∫ua0{[Mμ(˜A1)−a1−(λ)]2+[Mμ(˜A1)−a1+(λ)]2}λdλ=∫ua0[Mμ(˜A2)−Mμ(˜A1)+a1−(λ)−a2−(λ)][Mμ(˜A2)+Mμ(˜A1)−a1−(λ)−a2−(λ)]λdλ+∫ua0[Mμ(˜A2)−Mμ(˜A1)+a1+(λ)−a2+(λ)][Mμ(˜A2)+Mμ(˜A1)−a1+(λ)−a2+(λ)]λdλ |
By Definition 4 and Tchebycheff inequalities we infer that
var′μ(˜A2)−var′μ(˜A1)⩾∫ua0[Mμ(˜A2)−Mμ(˜A1)+a1−(λ)−a2−(λ)]λdλ×∫ua0[Mμ(˜A2)+Mμ(˜A1)−a1−(λ)−a2−(λ)]λdλ+∫ua0[Mμ(˜A2)−Mμ(˜A1)+a1+(λ)−a2+(λ)]λdλ×∫ua0[Mμ(˜A2)+Mμ(˜A1)−a1+(λ)−a2+(λ)]λdλ=(u2a2)2[Mμ(˜A2)−Mμ(˜A1)+M−μ(˜A1)−M−μ(˜A2)]×[Mμ(˜A2)+Mμ(˜A1)−M−μ(˜A1)−M−μ(˜A2)]+(u2a2)2[Mμ(˜A2)−Mμ(˜A1)+M+μ(A1)−M+μ(A2)]×[Mμ(˜A2)+Mμ(˜A1)−M+μ(A1)−M+μ(A2)]=u4a2[(M+μ(˜A2)−M−μ(˜A2)2)2−(M+μ(A1)−M−μ(A1)2)2]⩾0 |
Similarly we can verify that var′ν(˜A2)−var′ν(˜A1)⩾0.
So, we have var′(˜A2)=var′μ(˜A2)+var′ν(˜A2)2⩾var′μ(˜A1)+var′ν(˜A1)2=var′(˜A1).
The above Theorem 3.5 in fact indicates that the subsethood of generalized trapezoidal intuitionistic fuzzy number does entail smaller variance.
Theorem 3.6. Let ˜A=((a,b,c,d);ua,va) be a generalized trapezoidal intuitionistic fuzzy number with λ,γ cut set ˜A[λ]=[a−(λ),a+(λ)], ˜A[γ]=[a−(γ),a+(γ)] of the corresponding membership and nonmembership of ˜A, respectively, and 0⩽ua+va⩽1, then we obtain var(˜A)⩽var′(˜A).
Proof. From Definitions 7, 9, 4 we easily know that
varμ(˜A)=12∫ua0[(a+(λ))2+(a−(λ))2]λdλ−∫ua0a+(λ)a−(λ)λdλ |
var′μ(˜A)=∫ua0{[Mμ(˜A)−a−(λ)]2+[Mμ(˜A)−a+(λ)]2}λdλ=∫ua0[(a+(λ))2+(a−(λ))2]λdλ−∫ua02(Mμ(˜A))[a−(λ)+a+(λ)]λdλ+2∫ua0(Mμ(˜A))2λdλ=∫ua0[(a+(λ))2+(a−(λ))2]λdλ−2(Mμ(˜A))2u2a+(Mμ(˜A))2u2a. |
From the Jensen inequality and ∫ua02λu2adλ=1, we get
[∫ua02λu2a(a−(λ)+a+(λ))dλ]2⩽∫ua02λu2a(a−(λ)+a+(λ))2dλ. |
That is,
4u4a[∫ua0λ(a−(λ)+a+(λ))dλ]2⩽ 2u2a∫ua0λ(a−(λ)+a+(λ))2dλ.
i.e., 1u2a[∫ua0λ(a−(λ)+a+(λ))dλ]2⩽12 ∫ua0λ(a−(λ)+a+(λ))2dλ.
So, varμ(˜A)−var′μ(˜A)
=−12∫ua0[(a+(λ))2+(a−(λ))2]λdλ−∫ua0a+(λ)a−(λ)λdλ+2(Mμ(˜A))2u2a−(Mμ(˜A))2u2a=−12∫ua0[(a+(λ))2+(a−(λ))2]λdλ−∫ua0a+(λ)a−(λ)λdλ+(Mμ(˜A))2u2a=−12∫ua0[a+(λ)+a−(λ)]2λdλ+1u2a[∫ua0λ(a−(λ)+a+(λ))dλ]2⩽0. |
Similarly, by Definitions 7, 9, 5 we can prove
varν(˜A)=12∫1va[(a+(γ))2+(a−(γ))2]γdγ−∫1vaa+(γ)a−(γ)γdγ;var′ν(˜A)=∫1va{[Mν(˜A)−a−(γ)]2+[Mν(˜A)−a+(γ)]2}γdγ=∫1va[(a+(γ))2+(a−(γ))2]γdγ−∫1va2(Mν(˜A))[a−(γ)+a+(γ)]γdγ+2∫1va(Mν(˜A))2γdγ=∫1va[(a+(γ))2+(a−(γ))2]γdγ−2(Mν(˜A))2(1−v2a)+(Mν(˜A))2(1−v2a). |
From the Jensen inequality and ∫1va2γ1−v2adγ=1, we get
[∫1va2γ1−v2a(a−(γ)+a+(γ))dγ]2⩽∫1va2γ1−v2a(a−(γ)+a+(γ))2dγ. |
That is, 4(1−v2a)2[∫1vaγ(a−(γ)+a+(γ))dγ]2⩽ 2(1−v2a)∫1vaγ(a−(γ)+a+(γ))2dγ.
i.e., 1(1−v2a)[∫1vaγ(a−(γ)+a+(γ))dγ]2⩽ 12∫1vaγ(a−(γ)+a+(γ))2dγ.
So, varν(˜A)−var′ν(˜A)
=−12∫1va[(a+(γ))2+(a−(γ))2]γdγ−∫1vaa+(γ)a−(γ)γdγ+2(Mv(˜A))2(1−v2a)−(Mv(˜A))2(1−v2a)=−12∫1va[(a+(λ))2+(a−(λ))2]λdλ−∫1vaa+(λ)a−(λ)λdλ+(Mν(˜A))2(1−v2a)=−12∫1va[a+(λ)+a−(λ)]2λdλ+11−v2a[∫1vaγ(a−(γ)+a+(γ))dγ]2⩽0. |
Therefore, we get var(˜A)=varμ(˜A)+varν(˜A)2⩽var′μ(˜A)+var′ν(˜A)2=var′(˜A).
The above Theorem 3.6 indicates that the new presented possibilistic variance var′(˜A) of generalized trapezoidal intuitionistic fuzzy number is greater than the existing variance var(˜A) because it considers all the weighted deviation squares between the lower bound, upper bound of level cut interval of membership of ˜A and possibilistic mean.
Remark 2. If ˜A=((a,b,c,d);ua,va) is a symmetric generalized trapezoidal intuitionistic fuzzy number, ua,va are two constants satisfying 0⩽ua+va⩽1, then we have var(˜A)=var′(˜A).
Proof. Since ˜A=((a,b,c,d);ua,va) is a symmetric TIFN, we know a+d=b+c and d−c=b−a.
For any λ∈[0,ua], γ∈[va,1], the λ-level cut set and γ -cut set of TIFN ˜A can be expressed as follows.
˜A[λ]={x/μ˜A(x)⩾λ}=[a−(λ),a+(λ)]=[a+(b−a)λ/ua,d−(d−c)λ/ua)] |
=[b−s(λ),c+s(λ)]; |
˜A[γ]={x/ν˜A(x)⩽γ}=[a−(γ),a+(γ)]=[(b−ava−γ(b−a))/(1−va),(c−dva+γ(d−c))/(1−va)]. |
=[b−q(γ),c+q(γ)]. |
where s(λ)=b−a−(b−a)λ/ua, q(γ)=[(a−b)va+γ(b−a)]/(1−va).
According to Definitions 4, 5 of possibilistic mean of TIFN ˜A, one easily get
M(˜A)=1u2a∫ua0λ[a−(λ)+a+(λ)]dλ=1u2a∫ua0λ[b−s(λ)+c+s(λ)]dλ=12(b+c),Mν(˜A)=11−v2a∫1vaγ[a−(γ)+a+(γ)]dγ=11−v2a∫1vaγ[b−q(γ)+c+q(γ)]dγ=12(b+c). |
Hence,
varμ(˜A)=12∫ua0[a−(λ)−a+(λ)]2λdλ=12∫ua0[(b−s(λ))−(c+s(λ))]2λdλ=12∫ua0[b−c−2s(λ)]2λdλ;varν(˜A)=12∫1va[a−(γ)−a+(γ)]2γdγ=12∫1va[(b−q(γ))−(c+q(γ))]2γdγ=12∫1va[b−c−2q(γ)]2γdγ. |
And var′μ(˜A)=∫ua0[(Mμ(˜A)−a−(λ))2+(Mμ(˜A)−a+(λ))2]λdλ
=∫ua0λ([b+c2−(b−s(λ))]2+[b+c2−(c+s(λ))]2)dλ |
=∫ua0λ([c−b2+s(λ)]2+[b−c2−s(λ)]2)dλ=∫ua02λ([b−c2−s(λ)]2)dλ=12∫ua0λ[b−c−2s(λ)]2dλ=varμ(˜A); |
var′ν(˜A)=∫1va[(Mv(˜A)−a−(γ))2+(Mv(˜A)−a+(γ))2]γdγ |
=∫1vaγ([Mv(˜A)−(b−q(γ))]2+[Mv(˜A)−(c+q(γ)]2)dγ |
=∫1vaγ([b+c2−(b−q(γ))]2+[b+c2−(c+q(γ))]2)dγ=∫1vaγ([c−b2+q(γ))]2+[b−c2−q(γ)]2)dγ=12∫1vaγ[b−c−2q(γ)]2dγ=varν(˜A). |
Thus, var(˜A)=varμ(˜A)+varν(˜A)2=var′μ(˜A)+var′ν(˜A)2=var′(˜A).
Recently, some arithmetic operations of generalized trapezoidal intuitionistic fuzzy numbers have been utilized in analyzing fuzzy system reliability [26,27]. Also, many multi-attribute decision making and programming methods based on generalized trapezoidal intuitionistic fuzzy number have been studied in [28,29,30]. Although GTIFNs have been applied in dealing with uncertain problem, there is few study on the possibilistic mean and variance of GTIFN. In this section we will discuss some advantages of the proposed possibilistic mean and variance of GTIFN below.
In fact, for any GTIFN ˜A=((a,b,c,d);ua,va), the possibilistic mean M(˜A) may be respectively viewed as the central value of GTIFN ˜A, and the possibilistic variance Var(˜A) may be regarded as the global spreads of GTIFN ˜A. Thus, from the membership function point of view, the larger the possibilistic mean, the greater the GTIFN; the smaller the possibilistic variance, the greater the GTIFN.
Hence, we can define the rank index of generalized trapezoidal intuitionistic fuzzy number as
Rank(˜A)=M(˜A)−ρVar(˜A), |
where ρ represents the risk attitude of decision-maker(DM). If 0⩽ρ<0.5, it shows that DM is risk-like; If ρ=0.5, it shows that DM is risk-neutral; If 0.5<ρ⩽1, it shows that DM is risk-averse.
The new ranking method of GTIFNs {˜Ai} can be obtained according to the ascending order of rank index as following:
(1) If Rank(˜Ai)<Rank(˜Aj) then ˜Ai<˜Aj;
(2) If Rank(˜Ai)=Rank(˜Aj) then ˜Ai=˜Aj;
(3) If Rank(˜Ai)>Rank(˜Aj) then ˜Ai>˜Aj.
In this part, we discuss the portfolio decision problem with generalized trapezoidal intuitionistic fuzzy number returns. Let us consider a fuzzy portfolio selection problem. Suppose investor has initial wealth 1 and may buy m assets in the capital investment. The investor intends to allocate his/her wealth among the m risky assets for making accounting investment plan. X=(x1,x2,⋯,xm) is the investor portfolio vector representing the capital allocation vector among m securities, xi is the investment capital proportion of risky asset i; li, ui are the lower bound and upper bound of the capital invested in risky asset i(1⩽i⩽m), respectively. Suppose the future return rates of the alternative m assets are easily assessed by GTIFN ˜Ai=((ai,bi,ci,di);uai,vai), ∀i=1,2,⋯,m. In order to construct the intuitionistic fuzzy portfolio decision model, we first introduce two important concepts which will be used in the proposed inutitionistic fuzzy portfolio decision model.
By using the previous Theorem 2 and Definition 6 we can compute the expected mean of fuzzy return of portfolio X=(x1,x2,⋯,xm) as E(X)=∑mj=1xiM(˜Ai). By using the above-mentioned Theorem 3.4 and Definition 9 we can evaluate the possibilistic variance of intuitionistic fuzzy return of portfolio X=(x1,x2,⋯,xm) as
Var(X)=Var(∑mi=1xi˜Ai)=∑mi=1Var(˜Ai)+2∑1⩽i<j<mxixjcov(˜Ai,˜Aj). |
Assume that the whole investment process is self-financing, that is, the investor does not invest the additional capital during the portfolio selection. Inspired by the classic Markovitz portfolio theory, we establish the following intuitionistic fuzzy portfolio model by maximizing the expected mean of portfolio return and minimizing the possibilistic variance risk of portfolio as below.
maxE(X)=∑mi=1xiM(˜Ai)s.t.{Var(∑mi=1xi˜Ai)≤κ∑mi=1xi=10≤li≤xi≤ui≤1, |
where κ is the selected parameters by investor reflecting the risk attitude of investor. It means the upper bound of risk tolerance of the portfolio movement.
By applying Lingo or Matlab Optimization Toolbox we can easily solve the above programming models. Finally, we can obtain the optimal portfolio strategy X∗=(x∗1,x∗2,⋯,x∗m), which is the optimal solver corresponding to the maximum objective function value, x∗i is the optimal investment wealth proportion in risky asset i (1⩽i⩽m) under the risk constraints.
In this article, we introduce some notes of possibilistic variance of generalized trapezoidal intuitionistic fuzzy number and then discuss some important properties about possibilistic mean and variance of GTIFN based on possibility theory. The presented possibilistic mean and variance of GTIFN can be used to measure the expected return and risk of portfolio with GTIFN return. In the future, we will investigate the intuitionistic fuzzy portfolio decision-making and selection problem by maximizing possibilistic mean and minimizing possibilistic variance of portfolio.
We thank the Editor and the anonymous referees for their good suggestions and comments. This paper is supported by the Guangdong Basic and Applied Basic Research Foundation under Grant No. 2018A030313996.
The authors declare no conflict of interest in this paper.
[1] |
L. Jia, Q. Gao, Z. P. Liu, H. B. Tan, L. W. Zhou, Multidisciplinary fault diagnosis of complex engineering systems: A case study of nuclear power plants, Int. J. Ind. Ergon., 80 (2020), 103060. https://doi.org/10.1016/j.ergon.2020.103060 doi: 10.1016/j.ergon.2020.103060
![]() |
[2] |
Y. B. Li, B. Li, J. C. Ji, H. Kalhori, Advanced fault diagnosis and health monitoring techniques for complex engineering systems, Sensors, 22 (2022), 10002. https://doi.org/10.3390/s222410002 doi: 10.3390/s222410002
![]() |
[3] |
C. Wang, H. G. Matthies, Random model with fuzzy distribution parameters for hybrid uncertainty propagation in engineering systems, Comput. Meth. Appl. Mech. Eng., 359 (2020), 112673. https://doi.org/10.1016/j.cma.2019.112673 doi: 10.1016/j.cma.2019.112673
![]() |
[4] |
F. Villecco, A. Pellegrino, Evaluation of uncertainties in the design process of complex mechanical systems, Entropy, 19 (2017), e19090475. https://doi.org/10.3390/e19090475 doi: 10.3390/e19090475
![]() |
[5] |
E. Hüllermeier, W. Waegeman, Aleatoric and epistemic uncertainty in machine learning: An introduction to concepts and methods, Mach. Learn., 110 (2021), 457–506. https://doi.org/10.1007/s10994-021-05946-3 doi: 10.1007/s10994-021-05946-3
![]() |
[6] |
H. R. Fan, C. Wang, S. H. Li, Novel method for reliability optimization design based on rough set theory and hybrid surrogate model, Comput. Meth. Appl. Mech. Eng., 429 (2024), 117170. https://doi.org/10.1016/j.cma.2024.117170 doi: 10.1016/j.cma.2024.117170
![]() |
[7] |
M. Mansouri, R. Fezai, M. Trabelsi, M. Hajji, M.-F. Harkat, H. Nounou, et al., A novel fault diagnosis of uncertain systems based on interval Gaussian process regression: Application to wind energy conversion systems, IEEE Access, 8 (2020), 219672–219679. https://doi.org/10.1109/access.2020.3042101 doi: 10.1109/access.2020.3042101
![]() |
[8] |
X. X. Liu, Y. T. Ju, X. H. Liu, S. Miao, W. G. Zhang, An imu fault diagnosis and information reconstruction method based on analytical redundancy for autonomous underwater vehicle, IEEE Sens. J., 22 (2022), 12127–12138. https://doi.org/10.1109/jsen.2022.3174340 doi: 10.1109/jsen.2022.3174340
![]() |
[9] |
D. Yu, Fault diagnosis for a hydraulic drive system using a parameter-estimation method, Control Eng. Practice, 5 (1997), 1283–1291. https://doi.org/10.1016/s0967-0661(97)84367-5 doi: 10.1016/s0967-0661(97)84367-5
![]() |
[10] |
G. C. Zhang, L. Chen, K. K. Liang, Fault monitoring and diagnosis of aerostat actuator based on pca and state observer, Int. J. Model. Identif. Control, 32 (2019), 145. https://doi.org/10.1504/ijmic.2019.102367 doi: 10.1504/ijmic.2019.102367
![]() |
[11] |
Y. Song, M. Y. Zhong, J. Chen, Y. Liu, An alternative parity space-based fault diagnosability analysis approach for linear discrete time systems, IEEE Access, 6 (2018), 16110–16118. https://doi.org/10.1109/access.2018.2816970 doi: 10.1109/access.2018.2816970
![]() |
[12] |
V. Venkatasubramanian, R. Rengaswamy, S. N. Kavuri, A review of process fault detection and diagnosis, Comput. Chem. Eng., 27 (2003), 313–326. https://doi.org/10.1016/s0098-1354(02)00161-8 doi: 10.1016/s0098-1354(02)00161-8
![]() |
[13] |
S. W. Pan, D. Xiao, S. T. Xing, S. S. Law, P. Y. Du, Y. J. Li, A general extended kalman filter for simultaneous estimation of system and unknown inputs, Eng. Struct., 109 (2016), 85–98. https://doi.org/10.1016/j.engstruct.2015.11.014 doi: 10.1016/j.engstruct.2015.11.014
![]() |
[14] |
E. Walker, S. Rayman, R. E. White, Comparison of a particle filter and other state estimation methods for prognostics of lithium-ion batteries, J. Power Sources, 287 (2015), 1–12. https://doi.org/10.1016/j.jpowsour.2015.04.020 doi: 10.1016/j.jpowsour.2015.04.020
![]() |
[15] |
S. Nolan, A. Smerzi, L. Pezzè, A machine learning approach to Bayesian parameter estimation, npj Quantum Inform., 7 (2021), 169. https://doi.org/10.1038/s41534-021-00497-w doi: 10.1038/s41534-021-00497-w
![]() |
[16] |
R. Tarantino, F. Szigeti, E. Colina-Morles, Generalized luenberger observer-based fault-detection filter design: An industrial application, Control Eng. Practice, 8 (2000), 665–671. https://doi.org/10.1016/s0967-0661(99)00181-1 doi: 10.1016/s0967-0661(99)00181-1
![]() |
[17] |
L. A. Rusinov, N. V. Vorobiev, V. V. Kurkina, Fault diagnosis in chemical processes and equipment with feedbacks, Chemometrics Intell. Lab. Syst., 126 (2013), 123–128. https://doi.org/10.1016/j.chemolab.2013.03.015 doi: 10.1016/j.chemolab.2013.03.015
![]() |
[18] |
F. Pierri, G. Paviglianiti, F. Caccavale, M. Mattei, Observer-based sensor fault detection and isolation for chemical batch reactors, Eng. Appl. Artif. Intell., 21 (2008), 1204–1216. https://doi.org/10.1016/j.engappai.2008.02.002 doi: 10.1016/j.engappai.2008.02.002
![]() |
[19] |
H. M. Odendaal, T. Jones, Actuator fault detection and isolation: An optimised parity space approach, Control Eng. Practice, 26 (2014), 222–232. https://doi.org/10.1016/j.conengprac.2014.01.013 doi: 10.1016/j.conengprac.2014.01.013
![]() |
[20] |
C. J. Duan, Z. Y. Fei, J. C. Li, A variable selection aided residual generator design approach for process control and monitoring, Neurocomputing, 171 (2016), 1013–1020. https://doi.org/10.1016/j.neucom.2015.07.042 doi: 10.1016/j.neucom.2015.07.042
![]() |
[21] |
P. Zhang, S. X. Ding, Disturbance decoupling in fault detection of linear periodic systems, Automatica, 43 (2007), 1410–1417. https://doi.org/10.1016/j.automatica.2007.01.005 doi: 10.1016/j.automatica.2007.01.005
![]() |
[22] |
Q. Wang, C. Taal, O. Fink, Integrating expert knowledge with domain adaptation for unsupervised fault diagnosis, IEEE Trans. Instrum. Meas., 71 (2022), 1–12. https://doi.org/10.1109/tim.2021.3127654 doi: 10.1109/tim.2021.3127654
![]() |
[23] | P. Zhao, X. D. Mu, Z. R. Yin, Z. X. Yi, An approach of fault diagnosis for system based on fuzzy fault tree, 2008 International Conference on MultiMedia and Information Technology, Three Gorges, China, 2008,697–700. https://doi.org/10.1109/mmit.2008.142 |
[24] |
Z. N. Lin, Y. X. Wang, H. Q. Xu, F. R. Wei, A novel reduced-order analytical fault diagnosis model for power grid, IEEE Access, 12 (2024), 59521–59532. https://doi.org/10.1109/access.2024.3392905 doi: 10.1109/access.2024.3392905
![]() |
[25] |
C. Cheng, X. Y. Qiao, H. Luo, W. X. Teng, M. L. Gao, B. C. Zhang, et al., A semi-quantitative information based fault diagnosis method for the running gears system of high-speed trains, IEEE Access, 7 (2019), 38168–38178. https://doi.org/10.1109/access.2019.2906976 doi: 10.1109/access.2019.2906976
![]() |
[26] | J. P. Shi, W. G. Tong, D. L. Wang, Design of the transformer fault diagnosis expert system based on fuzzy reasoning, 2009 International Forum on Computer Science-Technology and Applications, Chongqing, China, 2009,110–114. https://doi.org/10.1109/ifcsta.2009.34 |
[27] |
A. R. Sahu, S. K. Palei, A. Mishra, Data-driven fault diagnosis approaches for industrial equipment: A review, Expert Syst., 41 (2024), 13360. https://doi.org/10.1111/exsy.13360 doi: 10.1111/exsy.13360
![]() |
[28] |
G. Wang, J. Y. Zhao, J. H. Yang, J. F. Jiao, J. L. Xie, F. Feng, Multivariate statistical analysis based cross voltage correlation method for internal short-circuit and sensor faults diagnosis of lithium-ion battery system, J. Energy Storage, 62 (2023), 106978. https://doi.org/10.1016/j.est.2023.106978 doi: 10.1016/j.est.2023.106978
![]() |
[29] |
Z. Zhang, X. He, Active fault diagnosis for linear systems: Within a signal processing framework, IEEE Trans. Instrum. Meas., 71 (2022), 1–9. https://doi.org/10.1109/tim.2022.3150889 doi: 10.1109/tim.2022.3150889
![]() |
[30] |
R. N. Liu, B. Y. Yang, E. Zio, X. F. Chen, Artificial intelligence for fault diagnosis of rotating machinery: A review, Mech. Syst. Signal Proc., 108 (2018), 33–47. https://doi.org/10.1016/j.ymssp.2018.02.016 doi: 10.1016/j.ymssp.2018.02.016
![]() |
[31] |
Y. Q. Liu, B. Liu, X. J. Zhao, M. Xie, A mixture of variational canonical correlation analysis for nonlinear and quality-relevant process monitoring, IEEE Trans. Ind. Electron., 65 (2018), 6478–6486. https://doi.org/10.1109/tie.2017.2786253 doi: 10.1109/tie.2017.2786253
![]() |
[32] |
G. Lee, C. H. Han, E. S. Yoon, Multiple-fault diagnosis of the tennessee eastman process based on system decomposition and dynamic pls, Ind. Eng. Chem. Res., 43 (2004), 8037–8048. https://doi.org/10.1021/ie049624u doi: 10.1021/ie049624u
![]() |
[33] |
G. Yu, C. N. Li, J. Sun, Machine fault diagnosis based on Gaussian mixture model and its application, Int. J. Adv. Manuf. Technol., 48 (2010), 205–212. https://doi.org/10.1007/s00170-009-2283-5 doi: 10.1007/s00170-009-2283-5
![]() |
[34] |
W. Deng, S. J. Zhang, H. M. Zhao, X. H. Yang, A novel fault diagnosis method based on integrating empirical wavelet transform and fuzzy entropy for motor bearing, IEEE Access, 6 (2018), 35042–35056. https://doi.org/10.1109/access.2018.2834540 doi: 10.1109/access.2018.2834540
![]() |
[35] |
J. B. Guo, Fault diagnosis method of flexible converter valve equipment based on ensemble empirical mode decomposition and temporal convolutional networks, J. Electr. Syst., 20 (2024), 344–352. https://doi.org/10.52783/jes.2386 doi: 10.52783/jes.2386
![]() |
[36] |
D. J. Yu, M. Wang, X. M. Cheng, A method for the compound fault diagnosis of gearboxes based on morphological component analysis, Measurement, 91 (2016), 519–531. https://doi.org/10.1016/j.measurement.2016.05.087 doi: 10.1016/j.measurement.2016.05.087
![]() |
[37] |
L. Ciabattoni, F. Ferracuti, A. Freddi, A. Monteriu, Statistical spectral analysis for fault diagnosis of rotating machines, IEEE Trans. Ind. Electron., 65 (2018), 4301–4310. https://doi.org/10.1109/tie.2017.2762623 doi: 10.1109/tie.2017.2762623
![]() |
[38] |
W. E. Sanders, T. Burton, A. Khosousi, S. Ramchandani, Machine learning: At the heart of failure diagnosis, Curr. Opin. Cardiol., 36 (2021), 227–233. https://doi.org/10.1097/hco.0000000000000833 doi: 10.1097/hco.0000000000000833
![]() |
[39] |
Y. G. Lei, B. Yang, X. W. Jiang, F. Jia, N. P. Li, A. K. Nandi, Applications of machine learning to machine fault diagnosis: A review and roadmap, Mech. Syst. Signal Proc., 138 (2020), 106587. https://doi.org/10.1016/j.ymssp.2019.106587 doi: 10.1016/j.ymssp.2019.106587
![]() |
[40] |
Z. N. An, F. Wu, C. Zhang, J. H. Ma, B. Sun, B. H. Tang, et al., Deep learning-based composite fault diagnosis, IEEE Jour. Emer. Select. Top. Circu. Syste., 13 (2023), 572–581. https://doi.org/10.1109/jetcas.2023.3262241 doi: 10.1109/jetcas.2023.3262241
![]() |
[41] |
D. T. Hoang, H. J. Kang, A survey on deep learning based bearing fault diagnosis, Neurocomputing, 335 (2019), 327–335. https://doi.org/10.1016/j.neucom.2018.06.078 doi: 10.1016/j.neucom.2018.06.078
![]() |
[42] |
X. Y. Fan, J. Li, H. Hao, Review of piezoelectric impedance based structural health monitoring: Physics-based and data-driven methods, Adv. Struct. Eng., 24 (2021), 3609–3626. https://doi.org/10.1177/13694332211038444 doi: 10.1177/13694332211038444
![]() |
[43] |
Q. Ni, X. M. Li, Z. W. Chen, Z. L. Zhao, L. L. Lai, A mechanism and data hybrid-driven method for main circuit ground fault diagnosis in electrical traction system, IEEE Trans. Ind. Electron., 70 (2023), 12806–12815. https://doi.org/10.1109/tie.2023.3260356 doi: 10.1109/tie.2023.3260356
![]() |
[44] |
D. An, N. H. Kim, J. H. Choi, Practical options for selecting data-driven or physics-based prognostics algorithms with reviews, Reliab. Eng. Syst. Saf., 133 (2015), 223–236. https://doi.org/10.1016/j.ress.2014.09.014 doi: 10.1016/j.ress.2014.09.014
![]() |
[45] |
J. Guo, Z. Y. Li, M. Y. Li, A review on prognostics methods for engineering systems, IEEE Trans. Reliab., 69 (2020), 1110–1129. https://doi.org/10.1109/tr.2019.2957965 doi: 10.1109/tr.2019.2957965
![]() |
[46] |
L. Kou, C. Liu, G. W. Cai, J. N. Zhou, Q. D. Yuan, S. M. Pang, Fault diagnosis for open-circuit faults in npc inverter based on knowledge-driven and data-driven approaches, IET Power Electron., 13 (2020), 1236–1245. https://doi.org/10.1049/iet-pel.2019.0835 doi: 10.1049/iet-pel.2019.0835
![]() |
[47] |
X. X. Xiao, C. H. Li, J. Huang, T. Yu, Fault diagnosis of rolling bearing based on knowledge graph with data accumulation strategy, IEEE Sens. J., 22 (2022), 18831–18840. https://doi.org/10.1109/JSEN.2022.3201839 doi: 10.1109/JSEN.2022.3201839
![]() |
[48] | K. Sachin, M. Torres, Y. C. Chan, M. Pecht, A hybrid prognostics methodology for electronic products, 2008 IEEE International Joint Conference on Neural Networks, Hong Kong, China, 2008, 3479–3485. https://doi.org/10.1109/IJCNN.2008.4634294 |
[49] | S. F. Cheng, M. Pecht, A fusion prognostics method for remaining useful life prediction of electronic products, 2009 IEEE International Conference on Automation Science and Engineering, Bangalore, India, 2009,102–107. https://doi.org/10.1109/COASE.2009.5234098 |
[50] | H. G. Zhang, R. Kang, M. Pecht, A hybrid prognostics and health management approach for condition-based maintenance, 2009 IEEE International Conference on Industrial Engineering and Engineering Management, Hong Kong, China, 2009, 1165–1169. https://doi.org/10.1109/ieem.2009.5372976 |
[51] |
M. A. Chao, C. Kulkarni, K. Goebel, O. Fink, Fusing physics-based and deep learning models for prognostics, Reliab. Eng. Syst. Saf., 217 (2022), 107961. https://doi.org/10.1016/j.ress.2021.107961 doi: 10.1016/j.ress.2021.107961
![]() |
[52] |
T. T. Li, Y. Zhao, C. B. Zhang, J. Luo, X. J. Zhang, A knowledge-guided and data-driven method for building hvac systems fault diagnosis, Build. Environ., 198 (2021), 107850. https://doi.org/10.1016/j.buildenv.2021.107850 doi: 10.1016/j.buildenv.2021.107850
![]() |
[53] |
L. H. Ye, X. Ma, C. L. Wen, Rotating machinery fault diagnosis method by combining time-frequency domain features and cnn knowledge transfer, Sensors, 21 (2021), 8168. https://doi.org/10.3390/s21248168 doi: 10.3390/s21248168
![]() |
[54] |
W. Xu, Y. Wan, T. Y. Zuo, X. M. Sha, Transfer learning based data feature transfer for fault diagnosis, IEEE Access, 8 (2020), 76120–76129. https://doi.org/10.1109/ACCESS.2020.2989510 doi: 10.1109/ACCESS.2020.2989510
![]() |
[55] |
X. P. Niu, R. Z. Wang, D. Liao, S. P. Zhu, X. C. Zhang, B. Keshtegar, Probabilistic modeling of uncertainties in fatigue reliability analysis of turbine bladed disks, Int. J. Fatigue, 142 (2021), 105912. https://doi.org/10.1016/j.ijfatigue.2020.105912 doi: 10.1016/j.ijfatigue.2020.105912
![]() |
[56] | M. Valdenegro-Toro, D. S. Mori, A deeper look into aleatoric and epistemic uncertainty disentanglement, 2022 IEEE/CVF Conference on Computer Vision and Pattern Recognition Workshops (CVPRW), New Orleans, LA, USA, 2022, 1508–1516. https://doi.org/10.1109/cvprw56347.2022.00157 |
[57] |
C. Wang, H. G. Matthies, M. H. Xu, Y. L. Li, Dual interval-and-fuzzy analysis method for temperature prediction with hybrid epistemic uncertainties via polynomial chaos expansion, Comput. Meth. Appl. Mech. Eng., 336 (2018), 171–186. https://doi.org/10.1016/j.cma.2018.03.013 doi: 10.1016/j.cma.2018.03.013
![]() |
[58] |
A. D. Kiureghian, O. Ditlevsen, Aleatory or epistemic? Does it matter?, Struct. Saf., 31 (2009), 105–112. https://doi.org/10.1016/j.strusafe.2008.06.020 doi: 10.1016/j.strusafe.2008.06.020
![]() |
[59] |
M. E. Paté-Cornell, Uncertainties in risk analysis: Six levels of treatment, Reliab. Eng. Syst. Saf., 54 (1996), 95–111. https://doi.org/10.1016/s0951-8320(96)00067-1 doi: 10.1016/s0951-8320(96)00067-1
![]() |
[60] |
C. Wang, H. R. Fan, X. Qiang, A review of uncertainty-based multidisciplinary design optimization methods based on intelligent strategies, Symmetry-Basel, 15 (2023), 1875. https://doi.org/10.3390/sym15101875 doi: 10.3390/sym15101875
![]() |
[61] |
C. Wang, X. Qiang, M. H. Xu, T. Wu, Recent advances in surrogate modeling methods for uncertainty quantification and propagation, Symmetry-Basel, 14 (2022), 1219. https://doi.org/10.3390/sym14061219 doi: 10.3390/sym14061219
![]() |
[62] |
D. Di Francesco, M. Girolami, A. B. Duncan, M. Chryssanthopoulos, A probabilistic model for quantifying uncertainty in the failure assessment diagram, Struct. Saf., 99 (2022), 102262. https://doi.org/10.1016/j.strusafe.2022.102262 doi: 10.1016/j.strusafe.2022.102262
![]() |
[63] |
P. Manfredi, Probabilistic uncertainty quantification of microwave circuits using Gaussian processes, IEEE Trans. Microw. Theory Tech., 71 (2023), 2360–2372. https://doi.org/10.1109/TMTT.2022.3228953 doi: 10.1109/TMTT.2022.3228953
![]() |
[64] |
J. S. Wu, G. E. Apostolakis, D. Okrent, Uncertainties in system analysis: Probabilistic versus nonprobabilistic theories, Reliab. Eng. Syst. Saf., 30 (1990), 163–181. https://doi.org/10.1016/0951-8320(90)90093-3 doi: 10.1016/0951-8320(90)90093-3
![]() |
[65] |
B. Hu, Q. M. Gong, Y. Q. Zhang, Y. H. Yin, W. J. Chen, Characterizing uncertainty in geotechnical design of energy piles based on Bayesian theorem, Acta Geotech., 17 (2022), 4191–4206. https://doi.org/10.1007/s11440-022-01535-3 doi: 10.1007/s11440-022-01535-3
![]() |
[66] |
K. Yao, J. Gao, Law of large numbers for uncertain random variables, IEEE Trans. Fuzzy Syst., 24 (2016), 615–621. https://doi.org/10.1109/TFUZZ.2015.2466080 doi: 10.1109/TFUZZ.2015.2466080
![]() |
[67] |
C. Zhang, Q. Liu, B. Zhou, C. Y. Chung, J. Li, L. Zhu, et al., A central limit theorem-based method for dc and ac power flow analysis under interval uncertainty of renewable power generation, IEEE Trans. Sustain. Energy, 14 (2023), 563–575. https://doi.org/10.1109/TSTE.2022.3220567 doi: 10.1109/TSTE.2022.3220567
![]() |
[68] |
C. Wang, Z. K. Song, H. R. Fan, Novel evidence theory-based reliability analysis of functionally graded plate considering thermal stress behavior, Aerosp. Sci. Technol., 146 (2024), 108936. https://doi.org/10.1016/j.ast.2024.108936 doi: 10.1016/j.ast.2024.108936
![]() |
[69] |
C. Wang, Evidence-theory-based uncertain parameter identification method for mechanical systems with imprecise information, Comput. Meth. Appl. Mech. Eng., 351 (2019), 281–296. https://doi.org/10.1016/j.cma.2019.03.048 doi: 10.1016/j.cma.2019.03.048
![]() |
[70] |
F. Arévalo, M. P. C. Alison, M. T. Ibrahim, A. Schwung, Adaptive information fusion using evidence theory and uncertainty quantification, IEEE Access, 12 (2024), 2236–2259. https://doi.org/10.1109/ACCESS.2023.3348270 doi: 10.1109/ACCESS.2023.3348270
![]() |
[71] |
H. R. Bae, R. V. Grandhi, R. A. Canfield, Uncertainty quantification of structural response using evidence theory, AIAA J., 41 (2003), 2062–2068. https://doi.org/10.2514/2.1898 doi: 10.2514/2.1898
![]() |
[72] |
Y. He, M. Mirzargar, R. M. Kirby, Mixed aleatory and epistemic uncertainty quantification using fuzzy set theory, Int. J. Approx. Reasoning, 66 (2015), 1–15. https://doi.org/10.1016/j.ijar.2015.07.002 doi: 10.1016/j.ijar.2015.07.002
![]() |
[73] |
C. Wang, H. G. Matthies, Hybrid evidence-and-fuzzy uncertainty propagation under a dual-level analysis framework, Fuzzy Sets Syst., 367 (2019), 51–67. https://doi.org/10.1016/j.fss.2018.10.002 doi: 10.1016/j.fss.2018.10.002
![]() |
[74] |
R. M. Rodríguez, L. Martínez, V. Torra, Z. S. Xu, F. Herrera, Hesitant fuzzy sets: State of the art and future directions, Int. J. Intell. Syst., 29 (2014), 495–524. https://doi.org/10.1002/int.21654 doi: 10.1002/int.21654
![]() |
[75] |
S. H. Khairuddin, M. H. Hasan, M. A. Hashmani, M. H. Azam, Generating clustering-based interval fuzzy type-2 triangular and trapezoidal membership functions: A structured literature review, Symmetry-Basel, 13 (2021), 239. https://doi.org/10.3390/sym13020239 doi: 10.3390/sym13020239
![]() |
[76] |
C. Wang, H. R. Fan, T. Wu, Novel rough set theory-based method for epistemic uncertainty modeling, analysis and applications, Appl. Math. Model., 113 (2023), 456–474. https://doi.org/10.1016/j.apm.2022.09.002 doi: 10.1016/j.apm.2022.09.002
![]() |
[77] |
X. Y. Zhang, Y. Y. Yao, Tri-level attribute reduction in rough set theory, Expert Syst. Appl., 190 (2022), 116187. https://doi.org/10.1016/j.eswa.2021.116187 doi: 10.1016/j.eswa.2021.116187
![]() |
[78] |
F. Y. Li, Z. Luo, G. Y. Sun, N. Zhang, An uncertain multidisciplinary design optimization method using interval convex models, Eng. Optimiz., 45 (2013), 697–718. https://doi.org/10.1080/0305215x.2012.690871 doi: 10.1080/0305215x.2012.690871
![]() |
[79] |
H. Lü, K. Yang, X. T. Huang, W.-B. Shangguan, K. G. Zhao, Uncertainty and correlation propagation analysis of powertrain mounting systems based on multi-ellipsoid convex model, Mech. Syst. Signal Proc., 173 (2022), 109058. https://doi.org/10.1016/j.ymssp.2022.109058 doi: 10.1016/j.ymssp.2022.109058
![]() |
[80] |
X. Qiang, C. Wang, H. R. Fan, Hybrid interval model for uncertainty analysis of imprecise or conflicting information, Appl. Math. Model., 129 (2024), 837–856. https://doi.org/10.1016/j.apm.2024.02.014 doi: 10.1016/j.apm.2024.02.014
![]() |
[81] |
C. Wang, X. Qiang, H. R. Fan, T. Wu, Y. L. Chen, Novel data-driven method for non-probabilistic uncertainty analysis of engineering structures based on ellipsoid model, Comput. Meth. Appl. Mech. Eng., 394 (2022), 114889. https://doi.org/10.1016/j.cma.2022.114889 doi: 10.1016/j.cma.2022.114889
![]() |
[82] |
C. Wang, H. G. Matthies, A modified parallelepiped model for non-probabilistic uncertainty quantification and propagation analysis, Comput. Meth. Appl. Mech. Eng., 369 (2020), 113209. https://doi.org/10.1016/j.cma.2020.113209 doi: 10.1016/j.cma.2020.113209
![]() |
[83] |
C. Wang, L. Hong, X. Qiang, M. H. Xu, Novel numerical method for uncertainty analysis of coupled vibro-acoustic problem considering thermal stress, Comput. Meth. Appl. Mech. Eng., 420 (2024), 116727. https://doi.org/10.1016/j.cma.2023.116727 doi: 10.1016/j.cma.2023.116727
![]() |
[84] |
L. X. Cao, J. Liu, L. Xie, C. Jiang, R. G. Bi, Non-probabilistic polygonal convex set model for structural uncertainty quantification, Analog Integr. Circuits Process., 89 (2021), 504–518. https://doi.org/10.1016/j.apm.2020.07.025 doi: 10.1016/j.apm.2020.07.025
![]() |
[85] |
L. P. Zhu, I. Elishakoff, J. H. Starnes, Derivation of multi-dimensional ellipsoidal convex model for experimental data, Math. Comput. Model., 24 (1996), 103–114. https://doi.org/10.1016/0895-7177(96)00094-5 doi: 10.1016/0895-7177(96)00094-5
![]() |
[86] |
C. Jiang, X. Han, G. Y. Lu, J. Liu, Z. Zhang, Y. C. Bai, Correlation analysis of non-probabilistic convex model and corresponding structural reliability technique, Comput. Meth. Appl. Mech. Eng., 200 (2011), 2528–2546. https://doi.org/10.1016/j.cma.2011.04.007 doi: 10.1016/j.cma.2011.04.007
![]() |
[87] |
J. Liu, Z. B. Yu, D. Q. Zhang, H. Liu, X. Han, Multimodal ellipsoid model for non-probabilistic structural uncertainty quantification and propagation, Int. J. Mech. Mater. Des., 17 (2021), 633–657. https://doi.org/10.1007/s10999-021-09551-z doi: 10.1007/s10999-021-09551-z
![]() |
[88] |
Z. Kang, W. B. Zhang, Construction and application of an ellipsoidal convex model using a semi-definite programming formulation from measured data, Comput. Meth. Appl. Mech. Eng., 300 (2016), 461–489. https://doi.org/10.1016/j.cma.2015.11.025 doi: 10.1016/j.cma.2015.11.025
![]() |
[89] |
L. Wang, J. X. Liu, Dynamic uncertainty quantification and risk prediction based on the grey mathematics and outcrossing theory, Appl. Sci.-Basel, 12 (2022), 5389. https://doi.org/10.3390/app12115389 doi: 10.3390/app12115389
![]() |
[90] |
Y. H. Yan, X. J. Wang, Y. L. Li, Non-probabilistic credible set model for structural uncertainty quantification, Structures, 53 (2023), 1408–1424. https://doi.org/10.1016/j.istruc.2023.05.011 doi: 10.1016/j.istruc.2023.05.011
![]() |
[91] |
T. Zhang, J. Y. Jiao, J. Lin, H. Li, J. D. Hua, D. He, Uncertainty-based contrastive prototype-matching network towards cross-domain fault diagnosis with small data, Knowledge-Based Syst., 254 (2022), 109651. https://doi.org/10.1016/j.knosys.2022.109651 doi: 10.1016/j.knosys.2022.109651
![]() |
[92] |
J. Chen, D. Zhou, Z. Guo, J. Lin, C. Lyu, C. Lu, An active learning method based on uncertainty and complexity for gearbox fault diagnosis, IEEE Access, 7 (2019), 9022–9031. https://doi.org/10.1109/ACCESS.2019.2890979 doi: 10.1109/ACCESS.2019.2890979
![]() |
[93] |
H. Ma, C. Ekanayake, T. K. Saha, Power transformer fault diagnosis under measurement originated uncertainties, IEEE Trns. Dielectr. Electr. Insul., 19 (2012), 1982–1990. https://doi.org/10.1109/tdei.2012.6396956 doi: 10.1109/tdei.2012.6396956
![]() |
[94] |
X. J. Shi, H. B. Gu, B. Yao, Fuzzy Bayesian network fault diagnosis method based on fault tree for coal mine drainage system, IEEE Sens. J., 24 (2024), 7537–7547. https://doi.org/10.1109/jsen.2024.3354415 doi: 10.1109/jsen.2024.3354415
![]() |
[95] |
R. X. Duan, Y. N. Lin, Y. N. Zeng, Fault diagnosis for complex systems based on reliability analysis and sensors data considering epistemic uncertainty, Eksploat. Niezawodn., 20 (2018), 558–566. https://doi.org/10.17531/ein.2018.4.7 doi: 10.17531/ein.2018.4.7
![]() |
[96] |
J. Wang, H. Peng, W. P. Yu, J. Ming, M. J. Pérez-Jiménez, C. Y. Tao, et al., Interval-valued fuzzy spiking neural p systems for fault diagnosis of power transmission networks, Eng. Appl. Artif. Intell., 82 (2019), 102–109. https://doi.org/10.1016/j.engappai.2019.03.014 doi: 10.1016/j.engappai.2019.03.014
![]() |
[97] |
A. Hoballah, D. E. A. Mansour, I. B. M. Taha, Hybrid grey wolf optimizer for transformer fault diagnosis using dissolved gases considering uncertainty in measurements, IEEE Access, 8 (2020), 139176–139187. https://doi.org/10.1109/access.2020.3012633 doi: 10.1109/access.2020.3012633
![]() |
[98] |
K. Zhou, J. Tang, Probabilistic gear fault diagnosis using Bayesian convolutional neural network, IFAC-PapersOnLine, 55 (2022), 795–799. https://doi.org/10.1016/j.ifacol.2022.11.279 doi: 10.1016/j.ifacol.2022.11.279
![]() |
[99] |
H. T. Zhou, W. H. Chen, L. S. Cheng, J. Liu, M. Xia, Trustworthy fault diagnosis with uncertainty estimation through evidential convolutional neural networks, IEEE Trans. Ind. Inform., 19 (2023), 10842–10852. https://doi.org/10.1109/TⅡ.2023.3241587 doi: 10.1109/TⅡ.2023.3241587
![]() |
[100] |
S. Huang, R. Duan, J. He, T. Feng, Y. Zeng, Fault diagnosis strategy for complex systems based on multi-source heterogeneous information under epistemic uncertainty, IEEE Access, 8 (2020), 50921–50933. https://doi.org/10.1109/ACCESS.2020.2980397 doi: 10.1109/ACCESS.2020.2980397
![]() |
[101] |
S. X. Liu, S. Y. Zhou, B. Y. Li, Z. H. Niu, M. Abdullah, R. R. Wang, Servo torque fault diagnosis implementation for heavy-legged robots using insufficient information, ISA Transactions, 147 (2024), 439–452. https://doi.org/10.1016/j.isatra.2024.02.004 doi: 10.1016/j.isatra.2024.02.004
![]() |
[102] |
T. Zhang, S. He, J. Chen, T. Pan, Z. Zhou, Toward small sample challenge in intelligent fault diagnosis: Attention-weighted multidepth feature fusion net with signals augmentation, IEEE Trans. Instrum. Meas., 71 (2022), 1–13. https://doi.org/10.1109/TIM.2021.3134999 doi: 10.1109/TIM.2021.3134999
![]() |
[103] |
A. Kulkarni, J. Terpenny, V. Prabhu, Sensor selection framework for designing fault diagnostics system, Sensors, 21 (2021), 6470. https://doi.org/10.3390/s21196470 doi: 10.3390/s21196470
![]() |
[104] |
C. Herrojo, F. Paredes, J. Mata-Contreras, F. Martín, Chipless-rfid: A review and recent developments, Sensors, 19 (2019), 3385. https://doi.org/10.3390/s19153385 doi: 10.3390/s19153385
![]() |
[105] |
T. Kalsoom, N. Ramzan, S. Ahmed, M. Ur-Rehman, Advances in sensor technologies in the era of smart factory and industry 4.0, Sensors, 20 (2020), 6783. https://doi.org/10.3390/s20236783 doi: 10.3390/s20236783
![]() |
[106] |
A. Leal, J. Casas, C. Marques, M. J. Pontes, A. Frizera, Application of additive layer manufacturing technique on the development of high sensitive fiber bragg grating temperature sensors, Sensors, 18 (2018), 4120. https://doi.org/10.3390/s18124120 doi: 10.3390/s18124120
![]() |
[107] |
G. D. Lewis, P. Merken, M. Vandewal, Enhanced accuracy of cmos smart temperature sensors by nonlinear curvature correction, Sensors, 18 (2018), 4087. https://doi.org/10.3390/s18124087 doi: 10.3390/s18124087
![]() |
[108] |
H. Landaluce, L. Arjona, A. Perallos, F. Falcone, I. Angulo, F. Muralter, A review of iot sensing applications and challenges using rfid and wireless sensor networks, Sensors, 20 (2020), 2495. https://doi.org/10.3390/s20092495 doi: 10.3390/s20092495
![]() |
[109] |
S. L. Wei, W. B. Qin, L. W. Han, F. Y. Cheng, The research on compensation algorithm of infrared temperature measurement based on intelligent sensors, Cluster Comput., 22 (2019), 6091–6100. https://doi.org/10.1007/s10586-018-1828-5 doi: 10.1007/s10586-018-1828-5
![]() |
[110] |
M. Tessarolo, L. Possanzini, E. G. Campari, R. Bonfiglioli, F. S. Violante, A. Bonfiglio, et al., Adaptable pressure textile sensors based on a conductive polymer, Flex. Print. Electron., 3 (2018), 034001. https://doi.org/10.1088/2058-8585/aacbee doi: 10.1088/2058-8585/aacbee
![]() |
[111] |
K. A. Mathias, S. M. Kulkarni, Investigation on influence of geometry on performance of a cavity-less pressure sensor, IOP Conf. Ser.: Mater. Sci. Eng., 417 (2018), 012035. https://doi.org/10.1088/1757-899x/417/1/012035 doi: 10.1088/1757-899x/417/1/012035
![]() |
[112] |
W. P. Eaton, J. H. Smith, Micromachined pressure sensors: Review and recent developments, Smart Mater. Struct., 6 (1997), 30–41. https://doi.org/10.1117/12.276606 doi: 10.1117/12.276606
![]() |
[113] |
M. Mousavi, M. Alzgool, S. Towfighian, A mems pressure sensor using electrostatic levitation, IEEE Sens. J., 21 (2021), 18601–18608. https://doi.org/10.1109/JSEN.2021.3091665 doi: 10.1109/JSEN.2021.3091665
![]() |
[114] |
A. P. Cherkun, G. V. Mishakov, A. V. Sharkov, E. I. Demikhov, The use of a piezoelectric force sensor in the magnetic force microscopy of thin permalloy films, Ultramicroscopy, 217 (2020), 113072. https://doi.org/10.1016/j.ultramic.2020.113072 doi: 10.1016/j.ultramic.2020.113072
![]() |
[115] |
A. Nastro, M. Ferrari, V. Ferrari, Double-actuator position-feedback mechanism for adjustable sensitivity in electrostatic-capacitive mems force sensors, Sens. Actuator A-Phys., 312 (2020), 112127. https://doi.org/10.1016/j.sna.2020.112127 doi: 10.1016/j.sna.2020.112127
![]() |
[116] |
M. L. Gödecke, C. M. Bett, D. Buchta, K. Frenner, W. Osten, Optical sensor design for fast and process-robust position measurements on small diffraction gratings, Opt. Lasers Eng., 134 (2020), 106267. https://doi.org/10.1016/j.optlaseng.2020.106267 doi: 10.1016/j.optlaseng.2020.106267
![]() |
[117] |
Y. J. Chan, A. R. Carr, S. Charkhabi, M. Furnish, A. M. Beierle, N. F. Reuel, Wireless position sensing and normalization of embedded resonant sensors using a resonator array, Sens. Actuator A-Phys., 303 (2020), 111853. https://doi.org/10.1016/j.sna.2020.111853 doi: 10.1016/j.sna.2020.111853
![]() |
[118] |
J. A. Kim, J. W. Kim, C. S. Kang, J. Y. Lee, J. Jin, On-machine calibration of angular position and runout of a precision rotation stage using two absolute position sensors, Measurement, 153 (2020), 107399. https://doi.org/10.1016/j.measurement.2019.107399 doi: 10.1016/j.measurement.2019.107399
![]() |
[119] |
L. E. Helseth, On the accuracy of an interdigital electrostatic position sensor, J. Electrost., 107 (2020), 103480. https://doi.org/10.1016/j.elstat.2020.103480 doi: 10.1016/j.elstat.2020.103480
![]() |
[120] |
K. Palmer, H. Kratz, H. Nguyen, G. Thornell, A highly integratable silicon thermal gas flow sensor, J. Micromech. Microeng., 22 (2012), 065015. https://doi.org/10.1088/0960-1317/22/6/065015 doi: 10.1088/0960-1317/22/6/065015
![]() |
[121] |
A. Moreno-Gomez, C. A. Perez-Ramirez, A. Dominguez-Gonzalez, M. Valtierra-Rodriguez, O. Chavez-Alegria, J. P. Amezquita-Sanchez, Sensors used in structural health monitoring, Arch. Comput. Method Eng., 25 (2018), 901–918. https://doi.org/10.1007/s11831-017-9217-4 doi: 10.1007/s11831-017-9217-4
![]() |
[122] | A. M. Shkel, Smart mems: Micro-structures with error-suppression and self-calibration control capabilities, Proceedings of the 2001 American Control Conference, Arlington, VA, USA, 2001, 1208–1213. https://doi.org/10.1109/ACC.2001.945886 |
[123] |
X. Insausti, M. Zárraga-Rodríguez, C. Nolasco-Ferencikova, J. Gutiérrez-Gutiérrez, In-network algorithm for passive sensors in structural health monitoring, IEEE Signal Process. Lett., 30 (2023), 952–956. https://doi.org/10.1109/lsp.2023.3298279 doi: 10.1109/lsp.2023.3298279
![]() |
[124] |
B. Jeon, J. S. Yoon, J. Um, S. H. Suh, The architecture development of industry 4.0 compliant smart machine tool system (smts), J. Intell. Manuf., 31 (2020), 1837–1859. https://doi.org/10.1007/s10845-020-01539-4 doi: 10.1007/s10845-020-01539-4
![]() |
[125] |
M. H. Zhu, J. Li, W. B. Wang, D. P. Chen, Self-detection and self-diagnosis methods for sensors in intelligent integrated sensing system, IEEE Sens. J., 21 (2021), 19247–19254. https://doi.org/10.1109/JSEN.2021.3090990 doi: 10.1109/JSEN.2021.3090990
![]() |
[126] |
J. Chen, P. Li, G. B. Song, Z. Ren, Y. Tan, Y. J. Zheng, Feedback control for structural health monitoring in a smart aggregate based sensor network, Int. J. Struct. Stab. Dyn., 18 (2017), 1850064. https://doi.org/10.1142/S0219455418500645 doi: 10.1142/S0219455418500645
![]() |
[127] |
C. Wang, Z. M. Peng, R. Liu, C. Chen, Research on multi-fault diagnosis method based on time domain features of vibration signals, Sensors, 22 (2022), 8164. https://doi.org/10.3390/s22218164 doi: 10.3390/s22218164
![]() |
[128] |
Z. F. Du, R. H. Zhang, H. Chen, Characteristic signal extracted from a continuous time signal on the aspect of frequency domain, Chin. Phys. B, 28 (2019), 090502. https://doi.org/10.1088/1674-1056/ab344a doi: 10.1088/1674-1056/ab344a
![]() |
[129] |
Y. Lu, J. Tang, On time-frequency domain feature extraction of wave signals for structural health monitoring, Measurement, 114 (2018), 51–59. https://doi.org/10.1016/j.measurement.2017.09.016 doi: 10.1016/j.measurement.2017.09.016
![]() |
[130] |
M. Imani, Modified pca, lda and lpp feature extraction methods for polsar image classification, Multimed. Tools Appl., 83 (2024), 41171–41192. https://doi.org/10.1007/s11042-023-17269-7 doi: 10.1007/s11042-023-17269-7
![]() |
[131] |
Z. Xia, Y. Chen, C. Xu, Multiview pca: A methodology of feature extraction and dimension reduction for high-order data, IEEE T. Cybern., 52 (2022), 11068–11080. https://doi.org/10.1109/TCYB.2021.3106485 doi: 10.1109/TCYB.2021.3106485
![]() |
[132] |
Y. Aliyari Ghassabeh, F. Rudzicz, H. A. Moghaddam, Fast incremental lda feature extraction, Pattern Recognit., 48 (2015), 1999–2012. https://doi.org/10.1016/j.patcog.2014.12.012 doi: 10.1016/j.patcog.2014.12.012
![]() |
[133] |
E. Parsaeimehr, M. Fartash, J. A. Torkestani, Improving feature extraction using a hybrid of cnn and lstm for entity identification, Neural Process. Lett., 55 (2023), 5979–5994. https://doi.org/10.1007/s11063-022-11122-y doi: 10.1007/s11063-022-11122-y
![]() |
[134] |
P. Wang, X. M. Zhang, Y. Hao, A method combining cnn and elm for feature extraction and classification of sar image, J. Sens., 2019 (2019), 6134610. https://doi.org/10.1155/2019/6134610 doi: 10.1155/2019/6134610
![]() |
[135] |
O. İrsoy, E. Alpaydın, Unsupervised feature extraction with autoencoder trees, Neurocomputing, 258 (2017), 63–73. https://doi.org/10.1016/j.neucom.2017.02.075 doi: 10.1016/j.neucom.2017.02.075
![]() |
[136] |
Y. Y. Wang, D. J. Song, W. T. Wang, S. X. Rao, X. Y. Wang, M. N. Wang, Self-supervised learning and semi-supervised learning for multi-sequence medical image classification, Neurocomputing, 513 (2022), 383–394. https://doi.org/10.1016/j.neucom.2022.09.097 doi: 10.1016/j.neucom.2022.09.097
![]() |
[137] |
W. X. Sun, J. Chen, J. Q. Li, Decision tree and pca-based fault diagnosis of rotating machinery, Mech. Syst. Signal Proc., 21 (2007), 1300–1317. https://doi.org/10.1016/j.ymssp.2006.06.010 doi: 10.1016/j.ymssp.2006.06.010
![]() |
[138] |
N. R. Sakthivel, V. Sugumaran, S. Babudevasenapati, Vibration based fault diagnosis of monoblock centrifugal pump using decision tree, Expert Syst. Appl., 37 (2010), 4040–4049. https://doi.org/10.1016/j.eswa.2009.10.002 doi: 10.1016/j.eswa.2009.10.002
![]() |
[139] |
Y. Y. Li, L. Y. Song, Q. C. Sun, H. Xu, X. G. Li, Z. J. Fang, et al., Rolling bearing fault diagnosis based on quantum ls-svm, EPJ Quantum Technol., 9 (2022), 18. https://doi.org/10.1140/epjqt/s40507-022-00137-y doi: 10.1140/epjqt/s40507-022-00137-y
![]() |
[140] |
A. H. Zhang, D. L. Yu, Z. Q. Zhang, Tlsca-svm fault diagnosis optimization method based on transfer learning, Processes, 10 (2022), 362. https://doi.org/10.3390/pr10020362 doi: 10.3390/pr10020362
![]() |
[141] |
T. Huang, Q. Zhang, X. A. Tang, S. Y. Zhao, X. N. Lu, A novel fault diagnosis method based on cnn and lstm and its application in fault diagnosis for complex systems, Artif. Intell. Rev., 55 (2022), 1289–1315. https://doi.org/10.1007/s10462-021-09993-z doi: 10.1007/s10462-021-09993-z
![]() |
[142] |
H. Fang, H. Liu, X. Wang, J. Deng, J. An, The method based on clustering for unknown failure diagnosis of rolling bearings, IEEE Trans. Instrum. Meas., 72 (2023), 1–8. https://doi.org/10.1109/TIM.2023.3251406 doi: 10.1109/TIM.2023.3251406
![]() |
[143] |
A. Rodríguez-Ramos, A. J. da Silva Neto, O. Llanes-Santiago, An approach to fault diagnosis with online detection of novel faults using fuzzy clustering tools, Expert Syst. Appl., 113 (2018), 200–212. https://doi.org/10.1016/j.eswa.2018.06.055 doi: 10.1016/j.eswa.2018.06.055
![]() |
[144] |
L. K. Chang, S. H. Wang, M. C. Tsai, Demagnetization fault diagnosis of a pmsm using auto-encoder and k-means clustering, Energies, 13 (2020), 4467. https://doi.org/10.3390/en13174467 doi: 10.3390/en13174467
![]() |
[145] |
J. Du, S. P. Wang, H. Y. Zhang, Layered clustering multi-fault diagnosis for hydraulic piston pump, Mech. Syst. Signal Proc., 36 (2013), 487–504. https://doi.org/10.1016/j.ymssp.2012.10.020 doi: 10.1016/j.ymssp.2012.10.020
![]() |
[146] |
Y. Y. Li, J. D. Wang, H. Y. Zhao, C. Wang, Q. Shao, Adaptive dbscan clustering and gasa optimization for underdetermined mixing matrix estimation in fault diagnosis of reciprocating compressors, Sensors, 24 (2024), 167. https://doi.org/10.3390/s24010167 doi: 10.3390/s24010167
![]() |
[147] |
C. X. Jian, K. J. Yang, Y. H. Ao, Industrial fault diagnosis based on active learning and semi-supervised learning using small training set, Eng. Appl. Artif. Intell., 104 (2021), 104365. https://doi.org/10.1016/j.engappai.2021.104365 doi: 10.1016/j.engappai.2021.104365
![]() |
[148] |
S. Zheng, J. Zhao, A self-adaptive temporal-spatial self-training algorithm for semisupervised fault diagnosis of industrial processes, IEEE Trans. Ind. Inform., 18 (2022), 6700–6711. https://doi.org/10.1109/TⅡ.2021.3120686 doi: 10.1109/TⅡ.2021.3120686
![]() |
[149] |
J. Y. Long, Y. B. Chen, Z. Yang, Y. W. Huang, C. Li, A novel self-training semi-supervised deep learning approach for machinery fault diagnosis, Int. J. Prod. Res., 61 (2023), 8238–8251. https://doi.org/10.1080/00207543.2022.2032860 doi: 10.1080/00207543.2022.2032860
![]() |
[150] |
K. Yu, H. Z. Han, Q. Fu, H. Ma, J. Zeng, Symmetric co-training based unsupervised domain adaptation approach for intelligent fault diagnosis of rolling bearing, Meas. Sci. Technol., 31 (2020), 115008. https://doi.org/10.1088/1361-6501/ab9841 doi: 10.1088/1361-6501/ab9841
![]() |
[151] |
L. Wang, D. F. Zhou, H. Tian, H. Zhang, W. Zhang, Parametric fault diagnosis of analog circuits based on a semi-supervised algorithm, Symmetry-Basel, 11 (2019), 228. https://doi.org/10.3390/sym11020228 doi: 10.3390/sym11020228
![]() |
[152] |
C. X. Jian, Y. H. Ao, Imbalanced fault diagnosis based on semi-supervised ensemble learning, J. Intell. Manuf., 34 (2023), 3143–3158. https://doi.org/10.1007/s10845-022-01985-2 doi: 10.1007/s10845-022-01985-2
![]() |
[153] |
X. Li, F. L. Zhang, Classification of multi-type bearing fault features based on semi-supervised generative adversarial network (gan), Meas. Sci. Technol., 35 (2024), 025107. https://doi.org/10.1088/1361-6501/ad068e doi: 10.1088/1361-6501/ad068e
![]() |
[154] |
L. Wang, H. Tian, H. Zhang, Soft fault diagnosis of analog circuits based on semi-supervised support vector machine, Analog Integr. Circuits Process., 108 (2021), 305–315. https://doi.org/10.1007/s10470-021-01851-w doi: 10.1007/s10470-021-01851-w
![]() |
[155] |
P. Xu, L. X. Fu, K. Xu, W. B. Sun, Q. Tan, Y. P. Zhang, et al., Investigation into maize seed disease identification based on deep learning and multi-source spectral information fusion techniques, J. Food Compos. Anal., 119 (2023), 105254. https://doi.org/10.1016/j.jfca.2023.105254 doi: 10.1016/j.jfca.2023.105254
![]() |
[156] |
P. F. Zhang, T. R. Li, Z. Yuan, C. Luo, G. Q. Wang, J. Liu, et al., A data-level fusion model for unsupervised attribute selection in multi-source homogeneous data, Inf. Fusion, 80 (2022), 87–103. https://doi.org/10.1016/j.inffus.2021.10.017 doi: 10.1016/j.inffus.2021.10.017
![]() |
[157] |
M. B. Song, Y. F. Zhi, M. D. An, W. Xu, G. H. Li, X. L. Wang, Centrifugal pump cavitation fault diagnosis based on feature-level multi-source information fusion, Processes, 12 (2024), 196. https://doi.org/10.3390/pr12010196 doi: 10.3390/pr12010196
![]() |
[158] |
L. L. Liu, X. Wan, J. Y. Li, W. X. Wang, Z. G. Gao, An improved entropy-weighted topsis method for decision-level fusion evaluation system of multi-source data, Sensors, 22 (2022), 6391. https://doi.org/10.3390/s22176391 doi: 10.3390/s22176391
![]() |
[159] |
Y. W. Liu, Y. Q. Cheng, Z. Z. Zhang, J. J. Wu, Multi-information fusion fault diagnosis based on knn and improved evidence theory, J. Vib. Eng. Technol., 10 (2022), 841–852. https://doi.org/10.1007/s42417-021-00413-8 doi: 10.1007/s42417-021-00413-8
![]() |
[160] |
J. Xu, Y. Sui, T. Dai, A Bayesian network inference approach for dynamic risk assessment using multisource-based information fusion in an interval type-2 fuzzy set environment, IEEE Trans. Fuzzy Syst., 32 (2024), 5702–5713. https://doi.org/10.1109/TFUZZ.2024.3425495 doi: 10.1109/TFUZZ.2024.3425495
![]() |
[161] | Y. C. Jie, Y. Chen, X. S. Li, P. Yi, H. S. Tan, X. Q. Cheng, Fufusion: Fuzzy sets theory for infrared and visible image fusion, In: Pattern recognition and computer vision, Singapore: Springer, 2024,466–478. https://doi.org/10.1007/978-981-99-8432-9_37 |
[162] |
F. Y. Xiao, Multi-sensor data fusion based on the belief divergence measure of evidences and the belief entropy, Inf. Fusion, 46 (2019), 23–32. https://doi.org/10.1016/j.inffus.2018.04.003 doi: 10.1016/j.inffus.2018.04.003
![]() |
[163] |
G. Koliander, Y. El-Laham, P. M. Djuric, F. Hlawatsch, Fusion of probability density functions, Proceedings of the IEEE, 110 (2022), 404–453. https://doi.org/10.1109/jproc.2022.3154399 doi: 10.1109/jproc.2022.3154399
![]() |
[164] |
Y. J. Pan, R. Q. An, D. Z. Fu, Z. Y. Zheng, Z. H. Yang, Unsupervised fault detection with a decision fusion method based on Bayesian in the pumping unit, IEEE Sens. J., 21 (2021), 21829–21838. https://doi.org/10.1109/jsen.2021.3103520 doi: 10.1109/jsen.2021.3103520
![]() |
[165] |
K. V. Kumar, A. Sathish, Medical image fusion based on type-2 fuzzy sets with teaching learning based optimization, Multimed. Tools Appl., 83 (2024), 33235–33262. https://doi.org/10.1007/s11042-023-16859-9 doi: 10.1007/s11042-023-16859-9
![]() |
[166] |
P. F. Zhang, T. R. Li, G. Q. Wang, C. Luo, H. M. Chen, J. B. Zhang, et al., Multi-source information fusion based on rough set theory: A review, Inf. Fusion, 68 (2021), 85–117. https://doi.org/10.1016/j.inffus.2020.11.004 doi: 10.1016/j.inffus.2020.11.004
![]() |
[167] |
Y. S. Wang, M. Y. He, L. Sun, D. Wu, Y. Wang, X. L. Qing, Weighted adaptive kalman filtering-based diverse information fusion for hole edge crack monitoring, Mech. Syst. Signal Proc., 167 (2022), 108534. https://doi.org/10.1016/j.ymssp.2021.108534 doi: 10.1016/j.ymssp.2021.108534
![]() |
[168] |
N. Guenther, M. Schonlau, Support vector machines, Stata J., 16 (2016), 917–937. https://doi.org/10.1177/1536867x1601600407 doi: 10.1177/1536867x1601600407
![]() |
[169] |
P. Cunningham, S. J. Delany, K-nearest neighbour classifiers-a tutorial, ACM Comput. Surv., 54 (2021), 128. https://doi.org/10.1145/3459665 doi: 10.1145/3459665
![]() |
[170] |
Z. Liu, S. B. Zhong, Q. Liu, C. X. Xie, Y. Z. Dai, C. Peng, et al., Thyroid nodule recognition using a joint convolutional neural network with information fusion of ultrasound images and radiofrequency data, Eur. Radiol., 31 (2021), 5001–5011. https://doi.org/10.1007/s00330-020-07585-z doi: 10.1007/s00330-020-07585-z
![]() |
[171] |
A. Y. Chen, F. Wang, W. H. Liu, S. Chang, H. Wang, J. He, et al., Multi-information fusion neural networks for arrhythmia automatic detection, Comput. Meth. Programs Biomed., 193 (2020), 105479. https://doi.org/10.1016/j.cmpb.2020.105479 doi: 10.1016/j.cmpb.2020.105479
![]() |
1. | Nik Muhammad Farhan Hakim Nik Badrul Alam, Ku Muhammad Naim Ku Khalif, Nor Izzati Jaini, Application of Intuitionistic Z-Numbers in Supplier Selection, 2023, 35, 1079-8587, 47, 10.32604/iasc.2023.024660 | |
2. | Wenjing Tang, Yitao Chen, Variance and Semi-Variances of Regular Interval Type-2 Fuzzy Variables, 2022, 14, 2073-8994, 278, 10.3390/sym14020278 | |
3. | Nik Muhammad Farhan Hakim Nik Badrul Alam, Ku Muhammad Naim Ku Khalif, Nor Izzati Jaini, Synergic ranking of fuzzy Z-numbers based on vectorial distance and spread for application in decision-making, 2023, 8, 2473-6988, 11057, 10.3934/math.2023560 | |
4. | P. Senthil Kumar, 2024, chapter 19, 9798369315781, 360, 10.4018/979-8-3693-1578-1.ch019 |