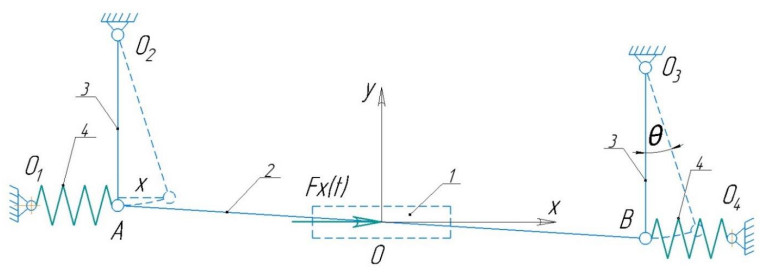
This article presents the results of a study of the sieve mill of a grain cleaning machine with a drive based on a linear asynchronous motor instead of a classic mechanical drive. The purpose of this work is to describe the structural and technological parameters of a sieve mill with a linear asynchronous drive to implement a mathematical model of the technological process of a grain cleaning machine work. A kinematic study of the flat hinged mechanism of the sieve mill of a grain cleaning machine was carried out, for which all geometric dimensions are known and the laws of motion of the leading link - the electric drive of the sieve mill based on a linear asynchronous motor are determined. As a result, the following were determined: kinematic modes kP > kB > kH of sieve mill vibrations under various technological conditions; laws of motion of all parts of the mechanism of the sieve mill, movement, speed (0.34... 0.36 m/s) and acceleration (5.8... 6.9 m/s2) of the driven links; a mathematical model of the kinematic scheme of a sieve mill of a grain cleaning machine with a drive from a linear induction motor has been developed. The use of a linear induction motor compared to existing (classical) drive designs as a drive of a sieve mill in a grain-cleaning machine significantly reduces the metal consumption of the structure (drive shafts, transmission mechanisms, connecting rods, bearings are excluded from the structure), and energy consumption is also reduced due to pulse drive operation; makes it possible in a wide range of technological parameters regulation for various crops, including various physical and mechanical parameters of the crop being cleaned.
Citation: Rustam Aipov, Andrey Linenko, Ildar Badretdinov, Marat Tuktarov, Salavat Akchurin. Research of the work of the sieve mill of a grain-cleaning machine with a linear asynchronous drive[J]. Mathematical Biosciences and Engineering, 2020, 17(4): 4348-4363. doi: 10.3934/mbe.2020240
[1] | Michele La Rocca, Cira Perna . Nonlinear autoregressive sieve bootstrap based on extreme learning machines. Mathematical Biosciences and Engineering, 2020, 17(1): 636-653. doi: 10.3934/mbe.2020033 |
[2] | Tangsheng Zhang, Hongying Zhi . A fuzzy set theory-based fast fault diagnosis approach for rotators of induction motors. Mathematical Biosciences and Engineering, 2023, 20(5): 9268-9287. doi: 10.3934/mbe.2023406 |
[3] | Yang Zhao, Xin Xie, Xing Zhang, Yi Ding . A revocable storage CP-ABE scheme with constant ciphertext length in cloud storage. Mathematical Biosciences and Engineering, 2019, 16(5): 4229-4249. doi: 10.3934/mbe.2019211 |
[4] | Xiaobo Zhang, Donghai Zhai, Yan Yang, Yiling Zhang, Chunlin Wang . A novel semi-supervised multi-view clustering framework for screening Parkinson's disease. Mathematical Biosciences and Engineering, 2020, 17(4): 3395-3411. doi: 10.3934/mbe.2020192 |
[5] | Koji Oshima, Daisuke Yamamoto, Atsuhiro Yumoto, Song-Ju Kim, Yusuke Ito, Mikio Hasegawa . Online machine learning algorithms to optimize performances of complex wireless communication systems. Mathematical Biosciences and Engineering, 2022, 19(2): 2056-2094. doi: 10.3934/mbe.2022097 |
[6] | Annalisa Vitale, Rossella Villa, Lorenzo Ugga, Valeria Romeo, Arnaldo Stanzione, Renato Cuocolo . Artificial intelligence applied to neuroimaging data in Parkinsonian syndromes: Actuality and expectations. Mathematical Biosciences and Engineering, 2021, 18(2): 1753-1773. doi: 10.3934/mbe.2021091 |
[7] | Anlu Yuan, Tieyi Zhang, Lingcong Xiong, Zhipeng Zhang . Torque control strategy of electric racing car based on acceleration intention recognition. Mathematical Biosciences and Engineering, 2024, 21(2): 2879-2900. doi: 10.3934/mbe.2024128 |
[8] | Ying Chang, Lan Wang, Yunmin Zhao, Ming Liu, Jing Zhang . Research on two-class and four-class action recognition based on EEG signals. Mathematical Biosciences and Engineering, 2023, 20(6): 10376-10391. doi: 10.3934/mbe.2023455 |
[9] | Sai Zhang, Li Tang, Yan-Jun Liu . Formation deployment control of multi-agent systems modeled with PDE. Mathematical Biosciences and Engineering, 2022, 19(12): 13541-13559. doi: 10.3934/mbe.2022632 |
[10] | József Z. Farkas, Peter Hinow . Physiologically structured populations with diffusion and dynamic boundary conditions. Mathematical Biosciences and Engineering, 2011, 8(2): 503-513. doi: 10.3934/mbe.2011.8.503 |
This article presents the results of a study of the sieve mill of a grain cleaning machine with a drive based on a linear asynchronous motor instead of a classic mechanical drive. The purpose of this work is to describe the structural and technological parameters of a sieve mill with a linear asynchronous drive to implement a mathematical model of the technological process of a grain cleaning machine work. A kinematic study of the flat hinged mechanism of the sieve mill of a grain cleaning machine was carried out, for which all geometric dimensions are known and the laws of motion of the leading link - the electric drive of the sieve mill based on a linear asynchronous motor are determined. As a result, the following were determined: kinematic modes kP > kB > kH of sieve mill vibrations under various technological conditions; laws of motion of all parts of the mechanism of the sieve mill, movement, speed (0.34... 0.36 m/s) and acceleration (5.8... 6.9 m/s2) of the driven links; a mathematical model of the kinematic scheme of a sieve mill of a grain cleaning machine with a drive from a linear induction motor has been developed. The use of a linear induction motor compared to existing (classical) drive designs as a drive of a sieve mill in a grain-cleaning machine significantly reduces the metal consumption of the structure (drive shafts, transmission mechanisms, connecting rods, bearings are excluded from the structure), and energy consumption is also reduced due to pulse drive operation; makes it possible in a wide range of technological parameters regulation for various crops, including various physical and mechanical parameters of the crop being cleaned.
Increasing the volume and improving the quality of agricultural products, reducing their cost and energy costs are closely related to the development and use of high-performance machines, the effectiveness of which is largely determined by the used electric drive [1,2]. The current trend in the development of electric drives is the reduction of resources and consumables due to the improvement and expansion of the functionality of control devices, which has become possible due to the development of technologies in power and microprocessor electronics [3].
Among technological processes in agriculture, food and mining, separation occupies a large share of labor and energy costs. At the same time, the productivity and technological efficiency of separating machines decisively affects the production capacity of enterprises, the yield of finished products and their quality [1,2].
Universal and popular are separating machines with the oscillatory movement of flat separating sieves: oscillation and vibration separators, in which separation is carried out due to gravitational forces with the action of vibrational forces that ensure the separation of particles relative to the sieve holes [4,5]. The vibrational forces are composed of the forces of forced and natural vibrations of the sieve and the kinematic drive system [4,5,6,7,8], therefore, the more complex the kinematic drive scheme, the more are the factors affecting the efficiency of the process, which become more and more negative as their mechanical parts wear out and become older [9,10,11,12].
In Aradwad et al. [13], the authors developed, manufactured, and tested a solar screen cleaner for separating impurities from soybean, lentil, and chickpea grains. This machine aims to provide good grain quality at an affordable cost of energy for small farmers in rural India. However, the drive of the presented machines in the works of Aradwad et al. [13], Ma et al. [6], Popov et al. [7], Shevtsov and Beznosov [8], Steponavičius et al. [5], is built on a traditional complex scheme with a converter of rotating motion into reciprocating. The complexity of the kinematic scheme of the machine's drive increases the cost of the machine, reduces energy efficiency and reliability due to the large number of rubbing and wearing surfaces and metal consumption. The metal consumption increases due to inertial flywheels designed to smooth out periodic force pulses, which is confirmed by the results of Vyngra et al. [14]. Due to the large inertia of the drive, the acceleration time of the drive also increases, which also increases energy losses, and, moreover, it is possible that the drive will not be able to accelerate to rated speed. In the work of Yarullin et al. [15], the design of a vibratory machine with widely adjustable parameters of the frequency and amplitude of oscillations using the vibrator counterbalances is proposed, in which the amplitude is automatically adjusted with increasing frequency during operation of the machine according to the hyperbolic law using a complex mechanical system. In this paper, the launching problem is proposed to be solved at the cost of even more complicated kinematics —the use of additional spring-loaded counterbalances.
Faced with the impossibility of further growth along the path of the classical sieve drive circuit, in the work of Modrzewski and Wodziński [16] it is proposed to use two rotational vibrators with the same or different static moments. The trajectory of the sieve (screen) is characterized by two different speeds of rotation of the drive eccentric vibrators. Based on the results of studies on a two-frequency screen on a laboratory scale, a concept has been developed for constructing an industrial screen: the inclination of the sieve relative to the level, the installation of motors relative to the middle part of the sieve, the exciting forces generated by the engines, and the engine speed. In the work, the novelty of the drive design consists only in complicating the kinematics by cascading superposition of two drives with rotary electric motors.
The work Linenko et al. [17] is also based on the theory that the efficiency of separating machines with complex vibrations of the working body is higher than that of machines with rectilinear vibrations due to an increase in the orienting ability of the material, the complex oscillation is realized through the use of the normal component of the force of a plane linear asynchronous motor (LAM). The authors proposed an adaptive LAM control system, which allows maintaining the oscillation parameters of the sieve mill constant, despite the effect of destabilizing factors. LAM allows to directly receive the movement of the working body, bypassing various kinds of transducers of the type of movement, and to implement an energy-efficient electric drive of oscillatory motion with adjustable vibration parameters together with the elastic elements. Similarly, in the work of Aristov et al. [18] it is emphasized that gearless oscillatory electric drives based on LAM allow, in particular, to provide almost the entire necessary range of vibration parameters generated and controlled by these drives. However, the present work does not talk about the introduction of LAM in specific technological machines, and their study.
In addition to linear asynchronous motors, reciprocating motion can be obtained by other electric machines. For example, Chen et al. [19] presented a linear reciprocating pulse jet engine for refrigeration compressors. A control system is proposed in which the reciprocating movement is achieved using leaf springs and a pushing regulator. The position controller is designed to control movement. To monitor the maximum efficiency of the engine, an efficiency controller is used, based on the method of searching for the optimal mode. The motor current is regulated through a PWM driver and a current regulator. The results of studies are presented in which the unidirectional power engine control system is simple, efficient, and can stably control the refrigerator compressor. The proposed technical solution is aimed at working with power from a single-phase network, however, in the presence of a three-phase network, there is the possibility of using a three-phase electric motor, the efficiency of which is considered to be higher, including LAM.
In the work of L. A. Neyman and V. Y. Neyman [20], it is noted that linear electromagnetic transducers are widely used in vibration engineering systems. The development of the mechatronic approach to dynamic analysis and modern methods of analysis and synthesis of such systems require the improvement of mathematical models. A mathematical model of an electromechanical system with reciprocating motion of interacting inertial masses connected by spring bonds and excited by a coil of an alternating electromagnetic field is proposed. In the work of Solomin and Chekhova [21], it is proposed to change the resistance of the secondary LAM element and control the speed with starting and traction forces in a wide range. The resistance of the short-circuited winding of the secondary LAM element is changed using a movable element capable of shorting a different number of conductors in each groove. Adjustable linear induction motors can be used as traction machines for magnetic levitation transport. However, in electric drives with reciprocating movement of the working bodies in the frequency range of the oscillations of the sieves of grain cleaning machines, it is not advisable to constantly change the resistance of the secondary element circuit in the proposed way, because this method leads to intensive wear of the rubbing parts and creates additional resistance to movement.
In the considered works with LAM, mathematical models are given that make it possible to analyze electromechanical processes in transient, stationary and resonant modes of an electric drive, taking into account the degree of mobility of inertial masses and the properties of spring bonds. However, when modeling and researching machines, the question of the influence of the features of the drive with LAM drive directly on the separation process is not considered, which is possibly related to the specifics of modeling these processes, the difference in scientific directions and the research goals pursued.
The purpose of this work is to study the structural and technological parameters and modes of oscillation of a sieve mill driven by a linear induction motor.
One of the most important functional evaluating parameters of the movement of the cleaned grain heap on the surface of the sieve is the Froude number, which is expressed by the ratio of the forces acting on the grain material lying on the sieve, the amplitude of oscillations of the sieve and gravity [4,5].
Figure 1 shows the calculation scheme for determining the coordinates of the nodal points of the sieve mill 2 of the grain cleaning machine for calculating their speed and acceleration of motion, inertia forces acting on the grain heap lying on the surface of the sieve. The given oscillatory system of the sieve mill of the grain cleaning machine is a "hybrid" of the mathematical and spring pendulum. The sieve mill АВ is a link in the parallel four-link mechanism АВО2О3. Elastic elements 4 (springs) are attached to the sieve mill suspended on suspensions 3 of length l on both sides, placed in a horizontal plane and perpendicular to the suspension. In the equilibrium position, the suspensions are vertical and the springs are not deformed. The installation of the plane of the sieve mill AB is determined by the angle α of inclination to the horizontal (in our case, α = 70).
Let ai, x and bi, y be the coordinates of the fixed reference points Oi, i = 1, 2, 3, 4. As a reference system, we take a right-handed Cartesian coordinate system, and place the origin of the coordinate system at the drive point O of the sieve mill Fx(t). Let us single out the nodal points of the sieve mill to compose the equations of geometric constraints, the trajectories of which are known: A and B. These points move along circles of radii l = О2А = О3В. Point A simultaneously belongs to crank О2А and connecting rod AB, point B simultaneously belongs to crank О3В and also connecting rod AB.
The sieve mill is driven into oscillation when it deviates from the equilibrium position by an angle θ due to the positive horizontal direction of the force pulse Fx(t) created by the linear induction motor 1. If we denote by x the linear displacement of the sieve mill from the equilibrium position along the arc with a radius of equal length suspensions l, then its angular displacement is θ = x/l(Figure 1).
Let us consider the oscillatory system of a sieve mill, on which, at displacements x in the interval xstart…xstop and in motion in the positive direction, the LAM force Fx acts:
Fx(t)={Fx,ifxstop−|x|≥0,и˙x≥00,otherwise. |
LAM is controlled by the control unit according to the parameters of the sieve oscillations. The control unit can adjust the duration and amplitude of the pulses of the forces Fx.
The work of the control unit in the model is implemented using the Heaviside function:
Ф(x)={1,x≥0,0,x<0. |
When the sieve mill deviates from the equilibrium position, a torque M arises, which tends to return it to the equilibrium position.
M=Jϵ, | (1) |
where J=ml2 is the moment of inertia, ϵ=d2θdt2 is the angular acceleration.
Torque M is created by three forces: elasticity, gravity, resistance.
The equation of the dynamics of the oscillatory motion of a sieve mill with small deviations θ under the action of a disturbing force Fx(t) created by a linear induction motor
ml2⋅d2θdt2=−mgl⋅sinθ−kl2⋅sinθ⋅cosθ−f⋅dθdt⋅l2+Fx(t), | (2) |
where k is the stiffness coefficient, Н/м, g is the acceleration of gravity, m/s2, f is the resistance coefficient.
d2θdt2=−gl⋅sinθ−km⋅sinθ⋅cosθ−fm⋅dθdt+Fx(t)m, | (3) |
This second-order nonlinear differential equation in ordinary functions is not integrated. Given small deviations θ, if we expand sin θ in a series
sinθ=θ−θ33!+θ55!−⋯ |
and neglect the terms of the expansion above the first order, we obtain a second-order inhomogeneous differential equation with constant coefficients
d2θdt2+(gl+km)⋅θ+fm⋅dθdt=Fx(t)m, | (4) |
or, if we denote by moving x,
d2xdt2+(gl+km)⋅x+fm⋅dxdt=Fx(t)m, | (4*) |
We denote fm=2β, where β is the damping coefficient, ω0=√gl+km is the circular frequency of oscillations. The oscillation period T=2π√ml2kl+mg. The frequency of the damped oscillations ωz=√ω02−β2ω – has physical meaning at ω0≥β.
The left side of the expression (4) is a second-order linear differential equation that describes damped free oscillations, and the right side, which clearly depends on time, is a driving force.
To find the law of motion of a sieve mill, it is necessary to solve this equation under certain initial conditions: t = 0; х = х0; dxdt=v0. The general solution to this equation is the sum of two functions
x(t)=x1(t)+x2(t), | (5) |
where x1(t) is the general solution of the homogeneous equation (left side (4*)), x2(t) is the particular solution of the inhomogeneous equation (right side (4*)).
The type of general solution of the left-hand side (4*) is known, which is a damped oscillation that disappears over time:
x1=C1sinωt+C2cosωt≡Csin(ωt+γ), (C1=const,C2=const,C=const,γ=const), | (6) |
where (C = const, γ = const) are the integration constants, C=√C21+C21=A⋅e−βt is the amplitude of free vibrations of the sieve mill, (ωt + γ) – the oscillation phase of the mill, γ is the initial oscillation phase. Or
x1|t→∞=limt→∞(A⋅e−βtsin(√ω02−β2t+γ))=0. | (6*) |
The steady-state oscillations of the sieve mill xsteady=x1|t→∞will consist only of forced oscillations under the action of a forcing force, which is determined by the right-hand side (4*). A particular solution to this equation must be sought in the form
x2=Bsin(δt+μ), |
where B is the amplitude of the forced oscillations, B=Fx(t)m√(ω02−δ2)2+4β2δ2; sinμ=2BmβδFx(t);cosμ=Bm(ω02−δ2)Fx(t); δ is the frequency of forced oscillations; μ is the angle determining the phase shift of the forced oscillations and the disturbing force.
The forced oscillations of the sieve mill described above under the action of a disturbing force Fx(t) are harmonic (undamped) oscillations with a frequency δ. Under any initial conditions, the vibrations of the sieve mill over time, free vibrations will disappear, only forced vibrations will remain, supported by the driving force Fx(t) (Figure 2), which during modeling is determined by the electromechanical energy conversion equation – the Park-Gorev differential equation with ODQ coordinate system, motionless relative to the traveling magnetic field [22]:
{ϕd1=∫T0(Ud1−πτV0⋅R1XrXsXr−X2mϕd1+πτV0⋅R1XmXsXr−X2mϕd2+πτV0ϕq1)dt;ϕq1=∫T0(Uq1−πτV0⋅R1XrXsXr−X2mϕq1+πτV0⋅R1XmXsXr−X2mϕq2−πτV0ϕd1)dt;ϕd2=∫T0(−πτV0⋅R2XsXsXr−X2mϕd2+πτV0⋅R2XmXsXr−X2mϕd1+πτ(V0−Vв)ϕq2)dt;ϕq2=∫T0(−πτV0⋅R2XsXsXr−X2mϕq2+πτV0⋅R2XmXsXr−X2mϕq1−πτ(V0−Vв)ϕd2)dt;Fx=3π2fτ⋅XmXsXr−X2m(ϕd2ϕq1−ϕd1ϕq2). | (8) |
Where τ is the pole division of the winding LAM, m;
Xs = X1+Xm, Xr = X'2+Xm are the resistance values of the inductor circuit and the secondary LAM element, respectively, Ohm;
R1, X1, R'2, X'2 – respectively, the active and reactive resistances of the inductor and the secondary element, reduced to the coil of the inductor, Ohm;
Xm is the mutual induction resistance between the inductor and the secondary element, Ohm;
V0 is the velocity of the magnetic field of the LAM, V0 = 2τf, m/s;
Vв is the velocity of the secondary LAM element, m/s;
ϕd1, ϕq1, ϕd2, ϕq2 are the flux linkages along the axes OD, OQ, respectively of the inductor and the secondary element, Wb;
ω0 is the circular frequency of the supply network, s-1;
Ud1, Uq1 is the inductor voltage along the axes OD, OQ, V.
As can be seen from expression (8), the power of the LAM is determined by the parameters of the motor equivalent circuit and the network parameters, including voltage and current frequency in the network.
Figure 3 shows the mechanical and acceleration characteristics of the LAM installed in the drive of the test machine. The characteristics are obtained by modeling in the program MATLAB-Simulink.
The parameters of the equivalent circuit determine the form of the mechanical characteristic – the dependence of the electric motor on the speed of the secondary element (Figure 3a), and the force, as is known, is quadratic depending on the voltage.
Electric motors operating in intermittent operation are at risk of overheating due to high inrush currents. In addition, reducing the supply voltage of an induction motor is considered to be ineffective, moreover, a destructive method of speed regulation. However, if the LAM is designed and manufactured with the expectation of such a regime, then the starting currents for it will be considered nominal (normal).
The practical implementation of the model was carried out by the fourth-order Runge-Kutta method according to the standard method in the Mathcad application program.
The condition ensuring the movement of grain heaps on the surface of a sieve mill AB oscillating with frequency ω and located at an angle α to the horizontal. Provided that the movement of the grain heap is carried out down the sieve, the inertia acting on the grain will be directed downward, the friction force on the sieve will be upward along the surface of the sieve, the gravity downward and the normal reaction of the sieve will be upward perpendicular to the surface of the sieve. By the direction of the acting forces on the particle of the grain heap, it is possible to establish the nature of their trajectory of movement relative to the oscillating sieve mill. The mode of moving the grain heap over the sieve is set in this way: the contact time of the particles of the grain heap with the sieve should be maximum to ensure more efficient separation, and at the same time, to increase the performance of the grain cleaning machine, the contact time of the particles of the grain heap with the sieve should be minimal (the speed of movement of the grain heap on a sieve should be maximum in order to increase productivity). These requirements contradict each other. Thus, it becomes necessary to solve the optimization problem.
One of the most important functional parameters of the motion of the layer on the surface of the sieve is the Froude number (an indicator of the kinematic mode of operation kР), which expresses the ratio of the forces acting on the particle lying on the sieve, the amplitude of oscillations of the sieve and gravity. This number can be expressed as follows
Fr=kP=ϵg, | (9) |
In order for the grain material to move along the sieve without separation from the plane with sliding down and up, and more down than up, the indicator of the working kinematic mode kр should be in the ratio:
kP>kB>kH, | (10) |
where kB is the indicator of the kinematic mode at which the grains move up along the plane of the AB sieve mill, kH is the indicator of the kinematic mode in which the grains move down along the plane of the AB sieve mill.
kB=tan(α+ϕ) | (11) |
where φ is the angle of friction of the particles of the grain heap on steel (tgφ = f, where f is the coefficient of friction), φ = 18…300.
kH=sin(ϕ−α)cos(α−ϕ), | (12) |
The trajectories of the velocity and acceleration of the links, which are obtained by the results of modeling and calculation in the Mathcad program, are presented in Figures 4–10.
Figure 4 shows that the (harmonic) oscillations of the sieve mill begin and increase under the action of the driving force Fx(t) created by the linear induction motor, and after t = 2 s stabilize, it goes into steady state.
Analyzing Figure 5, according to the results of a numerical solution, it was determined that the maximum speed of the sieve mill of the grain cleaning machine is 0.34... 0.36 m/s.
The acceleration developed by the sieve mill is 5.8... 6.9 m/s2.
For φ = 180, condition (10) is fulfilled, so the grain heap moves down and up along the oscillating sieve mill, but mainly down, and for φ = 300 it turns out kB≥kP>kH, which means that the grain heap moves only down on the sieve mill.
Figure 7 shows that the sieve mill oscillates and the angle of deviation of the suspensions relative to the vertical axis varies within −3.780≤θ≤4.110.
On the phase curve (Figure 8), speed jumps are clearly visible, leading to an increase in the oscillation amplitude when the next portion of the force impulse Fx(t) created by the linear asynchronous motor is transmitted to the sieve mill. Over time (steady state), the phase curve approaches many lines (attractor).
Let us consider the energy ratio.
Figure 10 shows the calculation results of the potential Ep(t), kinetic Ek(t) and total energy Eo(t) = Ep(t) + Ek(t). It can be seen from the figure that the kinetic energy oscillates with a doubled circular frequency with respect to the sieve mill vibration. When the potential energy is maximum, then at this time the kinetic energy is minimal, and vice versa. The oscillation process of the sieve mill under consideration is explained by the transition of one type of energy to another. Thus, the energy ratios in the system are decisive. In our case, they reflect the law of conservation of energy.
The experimentally obtained data on the kinematic mode of operation of the sieve mill driven by a linear induction motor showed compliance with a workable effective state (Figures 8 and 9), and at the same time, the LAM turns on and transfers the force to the sieve mill in a pulsed mode. Thus, the load on the LAM is reduced, the efficiency of the drive and the resource are increased. Since the main share of grain cleaning units is sieve machines, most of which have exhausted their life and the main cause of the main failures and breakdowns is the drive mechanism of the sieve mill, this is described in Mudarisov and Badretdinov [1], Mudarisov et al. [2], Shevtsov and Beznosov [8]. Also, due to wear or incorrect operation of the drive mechanism, structural vibrations and a violation of the kinematic mode can be observed. The influence of the kinematic regime on the cleaning process was studied by the authors [4,5,6,9,12,23,24,25,26]. A comparative analysis of the separation process at sieve mills and the possibility of representing in the form of laws: normal, Weibull, gamma and beta distribution were carried out by the authors of Voicu et al. [26]. A statistical analysis of the versatility of the physico-mechanical characteristics of crops and their impact on the cleaning process was carried out by Dal-Pastro et al. [24]. The mathematical model for the separation of seeds on flat sieves using the theory of dimensional analysis was performed by Casandroiu et al. [23], and Ma et al. [6].
Shevtsov and Beznosov [8] studied the effect of the drive device of the sieve mills of grain cleaning machines, which ensures the operation of sieves of different purposes in different kinematic modes. The disadvantage of the classic drive sieve mills which they found out is that spike and sowing sieves, performing different functions, work in the same kinematic mode.
The study of determining the inertia and mobility of bulk material and its effect on the inertial and dissipative loads, calculations and comparative analysis of the kinematic schemes of grain sorting machines with eccentrics shifted by π and π / 2 were carried out by Popov et al. [7].
The obtained characteristics of the functioning of the sieve mill from LAM in this work allow to develop recommendations for optimizing the structural and technological parameters of the sieve mill of the grain cleaning machine itself, improving the sieve drive itself, which in the future will significantly increase the resource and efficiency of the grain cleaning machine, and reduce energy consumption.
The mathematical model of the kinematic scheme of the sieve mill of a grain cleaning machine with an electric drive from a linear induction motor has been developed. Based on the simulation results, the nature of the oscillatory movement of the sieve mill is determined, its graphs of movement, speed, and acceleration are constructed. The maximum speed of the sieve mill was 0.34... 0.36 m/s, and the acceleration developed by the sieve mill varies within 5.8... 6.9 m/s2. During oscillatory movement of the sieve mill, the suspension angles on which the sieve mill is mounted deviate relative to the vertical axis by an angle θ∈[3.780;4.110].
The kinematic operating mode kP>kB>kH was determined for various angles of friction of the particles of the grain heap against steel φ = 18…300 (the coefficient of friction of the grain heap against steel). So at smaller friction angles φ, the grain heap moves up and down along the oscillating sieve mill, but mainly down, and for large φ ≥ 300, kB≥kP>kH is obtained, in this case the grain heap moves only down the sieve mill, there is no moving up. The Froude number, which characterizes the ratio between the forces of inertia and gravity, in the field of which the movement occurs, for the sieve mill is Fr = 0.7 and corresponds to the condition Fr < 1, which according to the accepted classification corresponds to the "calm flow" mode. The proposed method for modeling grain cleaning machines with a sieve cleaning system makes it possible to study the kinematics of the drive mechanism, the separation process by flat oscillating working bodies, to analyze the degree of contact of the particles of the grain pile components with the sieve, to identify problem areas and makes it possible to improve the design and technological parameters of the sieve mill of any seed cleaning machine. The developed model can be used repeatedly, so there is no need for investment in the manufacture and conduct of laboratory verification tests. You can set the correct modes of operation of the separation process for different crops and make recommendations for production.
Authors declare that they have no conflict of interests.
[1] | S. G. Mudarisov, I. D. Badretdinov, Improving production lines for post-harvest grain processing in farms, in The collection: Achievements of Science - Agricultural Production Materials of the XLVII International Scientific and Technical Conference dedicated to the 100th anniversary of I.E. Ullman (2008), 28-33. |
[2] | S. G. Mudarisov, Z. S. Rakhimov, I. D. Badretdinov, A. V. Akbatyrov, I. M. Farkhutdinov, Modernization of grain processing lines taking into account business conditions, in The collection: Scientific support for the stable functioning and development of the agro-industrial complex materials of the All-Russian scientific-practical conference with international participation (2009), 122-126. |
[3] | R. W. De Doncker, Modern electrical drives: Design and future trends, in Conference Proceedings - IPEMC 2006: CES/IEEE 5th International Power Electronics and Motion Control Conference (2007), 31-38. |
[4] | A. Dorokhov, V. Khamyev, K. Lepeshkin, Modernization of grinding machines of grain cleaning machines, in MATEC Web of Conferences, ICMTMTE, 224 (2018), 05009. |
[5] | D. Steponavičius, L. Špokas, S. Petkevičius, The influence of position of the first straw walkerґs section on grain separation, Agron. Res. 6 (2008), 377-385. |
[6] | L. Ma, X. Song, H. Wang, X. Xu, T. Han, H. Guo, Screening Kinematics Analysis of Cleaning Organs and Extractives, IOP Conf. Ser. Mater. Sci. Eng., 452 (2018), 042123. |
[7] | I. P. Popov, V. G. Chumakov, A.D. Terentyev, Drive power reduction of sieve sorting machines, Scientific and Technical Statements of St. Petersburg State Polytechnic University, 2 (2015), 175-181. |
[8] | I. V. Shevtsov, V. A. Beznosov, Drive unit for sieve mills of grain cleaning machines, Agrar. Vestn. Urala, 2 (2014), 43-45. |
[9] | A. M. Giyevskiy, V. I. Orobinsky, A. P. Tarasenko, A. V. Chernyshov, D. O. Kurilov, Substantiation of basic scheme of grain cleaning machine for preparation of agricultural crops seeds, IOP Conf. Ser. Mater. Sci. Eng., 327 (2018), 042035. |
[10] |
M. Skakov, B. Rakhadilov, M. Scheffler, E. Batyrbekov, Microstructure and tribological properties of electrolyticplasma nitrided high-speed steel, Mat. Test., 57 (2015), 360-364. doi: 10.3139/120.110709
![]() |
[11] | P. Savinyh, Y. Sychugov, V. Kazakov, S. Ivanovs, Development and theoretical studies of grain cleaning machine for fractional technology of flattening forage grain, in Proceedings of 17th International Scientific Conference Engineering for Rural Development Engineering for Rural Development (2018), 124-130. |
[12] |
O. Vasylkovskyi, K. Vasylkovska, S. Moroz, M. Sviren, L. Storozhyk, The influence of basic parameters of separating conveyor operation on grain cleaning quality, INMATEH, 57 (2019), 63-70. doi: 10.35633/INMATEH_57_07
![]() |
[13] | P. P. Aradwad, J. P. Sinha, T. V. Arun Kumar, R. S. Yadav, D. V. K. Samuel, Development of solar powered screen cleaner, Indian J. Agric. Sci., 88 (2018), 1914-1919. |
[14] | A.V. Vyngra, B. A. Avdeyev, R. F. Abdurakhmanov, V. V. Yenivatov, I. K. Ovcharenko, Mathematical model of start for a piston compressor electric drive of a ship refrigerator, in Proceedings of the 2019 IEEE Conference of Russian Young Researchers in Electrical and Electronic Engineering, ElConRus, (2019), 373-376. |
[15] | R. Yarullin, R. Aipov, I. Gabitov, A. Linenko, S. Akchurin, R. Safin, et al., Adjustable driver of grain cleaning vibro-machine with vertical axis of eccentric masses rotation, J. Eng. Appl. Sci., 13 (2018), 6398-6406. |
[16] | R. Modrzewski, P. Wodziński, Selection of the construction parameters of double-frequency screen for classification of mineral wastes, Rocz. Ochr. Srodowiska, 12 (2010), 697-722. |
[17] | A.V. Linenko, I. I. Gabitov, V. G. Baynazarov, M.F. Tuktarov, R.S. Aipov, S.V. Akchurin, et al., The mechatronic module "linear electric drive - sieve boot" intelligent control system of grain cleaner, J. Balk. Tribol. Assoc., 25 (2019), 708-717. |
[18] | A.V. Aristov, A. A. Aristov, A. G. Yudintsev, Oscillating motion motors general theory problems, in Proceedings of the 7th International Scientific and Practical Conference of Students, Post-Graduates and Young Scientists: Modern Techniques and Technology, MTT (2001), 101-103. |
[19] | L. Chen, D. Li, J. Zhao, Control of a linear reciprocating switched reluctance motor for compressors, in Proceedings of the 14th IEEE Conference on Industrial Electronics and Applications, ICIEA (2019), 2003-2008. |
[20] | L. A. Neyman, V. Y. Neyman, Dynamic model of a vibratory electromechanical system with spring linkage, in Proceedings - 2016 11th International Forum on Strategic Technology, IFOST (2016), 23-27. |
[21] | A. V. Solomin, A. A. Chekhova, Magnetic field and current displacement in groove of secondary element of adjustable linear induction motor, in Proceedings - 2019 International Ural Conference on Electrical Power Engineering, UralCon (2019), 271-276. |
[22] | R. B. Yarullin, A. V. Linenko, On the dynamic characteristics of an induction motor, Electrical and Information Systems and Systems 2 (2013), 42-46. |
[23] | T. Casandroiu, M. Popescu, G. Voicu, A developing a mathematical model for simulating the seeds separation process on the plane sieves, U.P.B. Sci. Bull. Series D, 71 (2009), 17-27. |
[24] |
E. Dal-Pastro, P. Facco, E. Bezzo, E. Zamprogna, M. Barolo, Data-driven modelling of milling and sieving operations in wheat milling process, Food Bioprod. Process., 99 (2016), 99-108. doi: 10.1016/j.fbp.2016.04.007
![]() |
[25] |
V. E. Saitov, R. F. Kurbanov, A. N. Suvorov, Assessing the adequacy of mathematical models of light impurity fractionation in sedimentary chambers of grain cleaning machines, Procedia Eng., 150 (2016), 107-110. doi: 10.1016/j.proeng.2016.06.728
![]() |
[26] | G. Voicu, T. Casandroiu, C. Tarcolea, Testing stochastic models for simulating the seeds separation process on the sieves of a cleaning system and a comparison with experimental data, Agric. Conspec. Sci., 73 (2008), 95-101. |
1. | V. M. Drincha, Yu. S. Tsench, Evolution of Grain and Seed Cleaning Equipment in Russia, 2021, 15, 2618-6748, 24, 10.22314/2073-7599-2021-15-1-24-33 | |
2. | Yevhen Mykhailov, Natalia Zadosna, Marina Postnikova, Ganna Pedchenko, Vasyl Khmelovskyi, Mariia Bondar, Aleksey Ionichev, Michał Kozdęba, Wioletta Tomaszewska-Górecka, Energy Assessment of the Pneumatic Sieve Separator for Agricultural Crops, 2021, 25, 2449-5999, 147, 10.2478/agriceng-2021-0012 | |
3. | Remigiusz Modrzewski, Andrzej Obraniak, Adam Rylski, Krzysztof Siczek, A Study on the Dynamic Behavior of a Sieve in an Industrial Sifter, 2022, 12, 2076-3417, 8590, 10.3390/app12178590 | |
4. | Oleg Bazaluk, Marina Postnikova, Serhii Halko, Serhii Kvitka, Evgeniy Mikhailov, Oleksandr Kovalov, Olena Suprun, Oleksandr Miroshnyk, Vitalii Nitsenko, Energy Saving in Electromechanical Grain Cleaning Systems, 2022, 12, 2076-3417, 1418, 10.3390/app12031418 | |
5. | Adam Wróblewski, Pavlo Krot, Radosław Zimroz, Timo Mayer, Jyri Peltola, Review of Linear Electric Motor Hammers—An Energy-Saving and Eco-Friendly Solution in Industry, 2023, 16, 1996-1073, 959, 10.3390/en16020959 | |
6. | Oleg Bazaluk, Marina Postnikova, Serhii Halko, Evgeniy Mikhailov, Oleksandr Kovalov, Olena Suprun, Oleksandr Miroshnyk, Vitalii Nitsenko, Improving Energy Efficiency of Grain Cleaning Technology, 2022, 12, 2076-3417, 5190, 10.3390/app12105190 | |
7. | Marina Postnikova, Evgeniy Mikhailov, Serhii Kvitka, Serhii Kurashkin, Oleksandr Kovalov, Oleksandra Klymenko, Aleksandr Semenov, Vitaliy Kucher, Zbigniew Kowalczyk, The Grain Cleaning Production Lines’ Energysaving Operation Modes of Electromechanical Systems, 2022, 26, 2449-5999, 51, 10.2478/agriceng-2022-0005 | |
8. | Mohamed Abu Ali, Eid Abd El-Rahman, Gamal El-Deen Nasr, Design and Assessment of a Small-Scale Machine for Cleaning Wheat Grains, 2022, 25, 1338-5267, 13, 10.2478/ata-2022-0003 | |
9. | A.V. Chernyshov, V.I. Orobinsky, A.M. Gievsky, I.V. Baskakov, A. Valiev, B. Ziganshin, F. Nezhmetdinova, A. Taylan, R. Nizamov, Study of operation of four-screen shoes of grain-cleaning separators, 2024, 103, 2117-4458, 00010, 10.1051/bioconf/202410300010 |