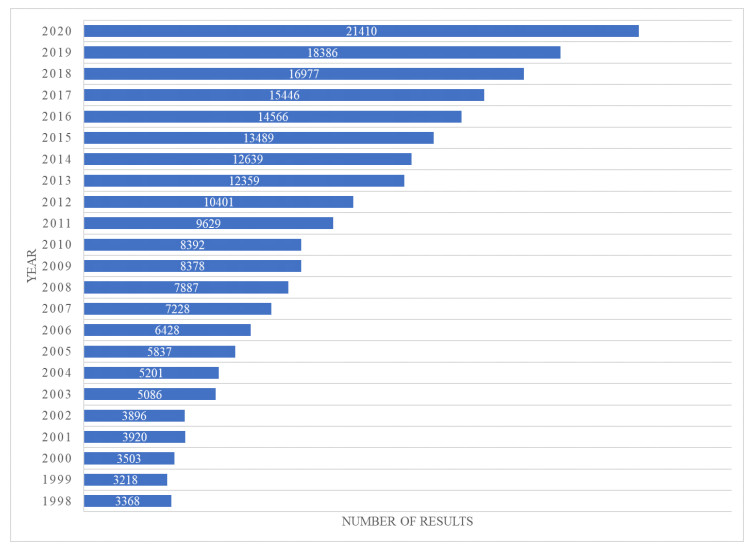
Traceability can be a tool for safety and quality assurance for food perishables as well as for process optimization and economic gain. However, it is often considered mere bureaucracy and an economic burden. Such is prevalent in small and medium-sized enterprises. As they constitute most of food sector, the adoption of traceability systems is quite slow and mostly to satisfy legal requirements.
To determine the main advantages and disadvantages of traceability models, implementation and technologies, a literature review and Small and Medium Enterprises (SME) focused analysis was performed in the part Ⅰ of this study.
In Part Ⅱ, a low cost open-source traceability focused on food safety and quality is developed. It is based on HACCP flowcharts to define gateways for quality evaluation and encompasses external verification and product history maintenance.
Economic gains, more quality and safety, better efficiency and a more direct contact with consumers are some of the main advantages. High implementation costs, poorly defined benefits, lack of compatibility, consumer focused perspective and exposure of sensitive information are some of the main issues.
This study serves to expose these issues and suggest solutions, aiming to encourage the adoption of traceability systems, with last-end benefits to producers, retailers, and consumers.
Citation: João Paulo Curto, Pedro Dinis Gaspar. Traceability in food supply chains: Review and SME focused analysis-Part 1[J]. AIMS Agriculture and Food, 2021, 6(2): 679-707. doi: 10.3934/agrfood.2021041
[1] | João Paulo Curto, Pedro Dinis Gaspar . Traceability in food supply chains: SME focused traceability framework for chain-wide quality and safety-Part 2. AIMS Agriculture and Food, 2021, 6(2): 708-736. doi: 10.3934/agrfood.2021042 |
[2] | Giuseppe Timpanaro, Paolo Guarnaccia, Silvia Zingale, Vera Teresa Foti, Alessandro Scuderi . The sustainability role in the purchasing choice of agri-food products in the United Arab Emirates and Italy. AIMS Agriculture and Food, 2022, 7(2): 212-240. doi: 10.3934/agrfood.2022014 |
[3] | Giulia Mastromonaco, Simone Blanc, Antonina Sparacino, Chiara Medoro, Stefano Predieri, Marta Cianciabella . Challenges and opportunities of sustainability, certifications and traceability in the Italian beekeeping sector. AIMS Agriculture and Food, 2025, 10(2): 314-336. doi: 10.3934/agrfood.2025016 |
[4] | Wei Yang, Bryan Anh, Phuc Le . Do consumers care about environmentally sustainable attributes along the food supply chain? —A systematic literature review. AIMS Agriculture and Food, 2023, 8(2): 513-533. doi: 10.3934/agrfood.2023027 |
[5] | Daniela Torello Marinoni, Paola Ruffa, Vera Pavese, Nicole Roberta Giuggioli . Apple juice evaluation: Qualitative analysis and microsatellite traceability. AIMS Agriculture and Food, 2022, 7(4): 819-830. doi: 10.3934/agrfood.2022050 |
[6] | Mohamed-Yousif Ibrahim Mohamed . Campylobacteriosis in North Africa. AIMS Agriculture and Food, 2024, 9(3): 801-821. doi: 10.3934/agrfood.2024043 |
[7] | Ralph Kwadwo Osei, Marco Medici, Martin Hingley, Maurizio Canavari . Exploring opportunities and challenges to the adoption of blockchain technology in the fresh produce value chain. AIMS Agriculture and Food, 2021, 6(2): 560-577. doi: 10.3934/agrfood.2021033 |
[8] | Giacomo Staffolani, Giulia Chiaraluce, Deborah Bentivoglio, Bruno Vodo, Pier Paolo Miglietta, Adele Finco . Blockchain for the valorization of Made in Italy extra virgin olive oil: A discrete choice experiment on young consumers. AIMS Agriculture and Food, 2025, 10(3): 596-617. doi: 10.3934/agrfood.2025030 |
[9] | Monsuru Adekunle Salisu, Yusuf Opeyemi Oyebamiji, Omowunmi Kayode Ahmed, Noraziyah A Shamsudin, Yusoff Siti Fairuz, Oladosu Yusuff, Mohd Rafii Yusop, Zulkefly Sulaiman, Fatai Arolu . A systematic review of emerging trends in crop cultivation using soilless techniques for sustainable agriculture and food security in post-pandemic. AIMS Agriculture and Food, 2024, 9(2): 666-692. doi: 10.3934/agrfood.2024036 |
[10] | Antonino Marvuglia, Tomás Navarrete Gutiérrez, Paul Baustert, Enrico Benetto . Implementation of Agent-Based Models to support Life Cycle Assessment: A review focusing on agriculture and land use. AIMS Agriculture and Food, 2018, 3(4): 535-560. doi: 10.3934/agrfood.2018.4.535 |
Traceability can be a tool for safety and quality assurance for food perishables as well as for process optimization and economic gain. However, it is often considered mere bureaucracy and an economic burden. Such is prevalent in small and medium-sized enterprises. As they constitute most of food sector, the adoption of traceability systems is quite slow and mostly to satisfy legal requirements.
To determine the main advantages and disadvantages of traceability models, implementation and technologies, a literature review and Small and Medium Enterprises (SME) focused analysis was performed in the part Ⅰ of this study.
In Part Ⅱ, a low cost open-source traceability focused on food safety and quality is developed. It is based on HACCP flowcharts to define gateways for quality evaluation and encompasses external verification and product history maintenance.
Economic gains, more quality and safety, better efficiency and a more direct contact with consumers are some of the main advantages. High implementation costs, poorly defined benefits, lack of compatibility, consumer focused perspective and exposure of sensitive information are some of the main issues.
This study serves to expose these issues and suggest solutions, aiming to encourage the adoption of traceability systems, with last-end benefits to producers, retailers, and consumers.
There are several definitions and principles of traceability that result in its development taking different directions. As such, there is not a common understanding about the definition and structure for food traceability systems [1].
Food traceability can be defined as the ability to track a product batch and its history through the whole, or part, of a production chain from harvest through transport, storage, processing, distribution, and sales or internally in one of the steps in the chain. Traceability is a generic issue and independent of the type of product, production, and the control system it serves. Traceability is a quality control tool and should be implemented systemically, leading to the development of a traceability system that records information about a product and its movements [2].
Other definitions of traceability exist. ISO 8402 defines traceability as the ability to trace the history, application, or location of an entity by means of recorded identifications [3]. This standard was then superseded by the ISO 9000 that defines traceability as the ability to trace the history, application, or location of that which is under consideration [4]. The standard ISO 22005 is identical to the ISO 9000 but is specific to food supply chains [5]. All these standards have an additional clause that indicates that when relating to products, the information about the origin of materials and parts, the processing history, and the distribution and location of the product after delivery should be kept. The Codex Alimentarius defines traceability as the ability to follow the movement of a food through specified stage(s) of production, processing, and distribution [6]. The General Food Law, defines traceability the ability to trace and follow a food, feed, food-producing animal or substance intended to be, or expected to be incorporated into a food or feed, through all stages of production, processing and distribution [7].
Although international regulations exist for traceability, each country can implement additional regulations to increase the comprehensiveness and effectiveness of traceability. In Europe, regulations are already comprehensive and establish Europe as the leader and example to follow [8]. Thus, a robust traceability platform exists that can benefit from the automation of information exchange as a way to facilitate the enforcement of regulations, speed up sanctions and limit the dissemination of improper commodities, as, according to Lupien [9], the possibility of occurrence of alimentary quality and safety flaws still exists.
Traceability is used in several activities as information technology, statistical analysis, electronics, biology, logistics, supply chain management and food industry. Traceability systems have the potential to increase security, quality, reliability, and precision. These advantages have an impact in consumer protection and company productivity [10].
Traceability allows the consumers to trust consumed products and pay the correct price. It also prevents the occurrence of health issues, increases environmental sustainability and prevents the invasion of non-indigenous species [11].
According to Opara [12], the demand for traceability systems has been growing significantly in the last years due to faults in alimentary security and the emergence of genetically modified organisms. These situations contribute to the reduction of consumers' trust and increase the concern with the potentially negative consequences of existing practices. To prevent those consequences, new regulations were introduced and aim to hold responsible entities that neglect safety. To correctly determine responsibility, enterprises must demonstrate that all diligences were complied with. Consequently, rises the necessity of a system that can assure product quality and allows regulators and companies to know the time and space evolution of quality and safety of food products to better deal with eventual food crisis. Thus, a traceability system based on quality and safety functions as a preventive tool as it helps producers to effectively manage the quality, locate and isolate threats to food safety. The evolution of information and communication technologies (ICT) has increased the speed and precision of data collection and thus, can present reliable and transparent information to the consumers.
Traceability can be part of a system that provides information about all production stages. To achieve chain-wide traceability, it is necessary that all stakeholders can monitor and store information internally and be able of transmitting it externally to connect outputs (selling) and inputs (buying).
In addition to the existence of considerably different traceability systems and their lack of compatibility, traceability suffers from issues that need to be solved, as the exposure of sensitive information, emergence of copies, necessary investment, and loss of autonomy.
This review aims to clarify the main issues associated with traceability models and systems. Although some issues arise on a general level, the analysis and solutions proposed in this paper give special consideration to the implementation of these systems in Small and Medium Enterprises (SME), due to the general specificities of this kind of companies, such as the reduced number of collaborators, lack of expert technicians, the reduced available amount for research and development activities and for the acquisition of traceability systems, either hardware (data loggers, communication systems, network devices, among others) or software (alert systems, support decision-making applications, among others).
Making use of the Elsevier's Science Direct, Mendeley and Scopus, and IEEE Xplore, several papers were analyzed. Initially, key words such as "food traceability" were used as search criteria. As seen in Figure 1, this search provides thousands of results with the tendency to increase in number over the years as the subject of food traceability becomes increasingly important.
However, throughout the analysis of the results, several relevant options are recurrently mentioned in the form of definitions, or by the lack thereof, and models that clearly demonstrate its importance to traceability systems, even if not on an initial stage. Thus, it became important to demonstrate trending unresolved issues throughout the years by making use of base scientific literature, starting in 1998 with Moe [2] and ending with Óskarsdóttir & Oddsson [13] in 2019, giving in the process an historic perspective on the evolution of traceability.
Before starting the review and analysis, it is important to provide some definitions and brief explanation on some terms that will be used throughout this study. RFID, radio-frequency identification, uses radio waves to identify and keep track of compatible tags; PDA, personal digital assistant, precursor device to information management functions now commonly found in smartphones; ER model, Entity-Relationship model, describes the connection (relationship) between points of interest (entities); RDBMS, Relational DataBase Management System, a tool that allows for the definition, creation and maintenance of a database based on the relational model; GS1, Global Standards 1, a nonprofit organization focused on developing and maintaining standards for business communication. EPC, Electronic Product Code, is a universally identifiable code for physical objects; EPCglobal, organization focusing on increasing the use and standardization of EPC; EPCIS, EPC Information Services, is a standard to create a share data. EDI, Electronic Data Interchange, is the communication of information in digital form between businesses; HACCP, Hazard Analysis and Critical Control Points, a preemptive mechanism to ensure food safety; FIFO, First-In, First-Out, an inventory technique to avoid spoilage based on first processing and selling the first received materials; FEFO, First Expired, First Out, is another inventory management technique that differs from the previous by processing and selling according to expiration dates; LSFO, Least Shelf-life, First Out, is a third inventory management technique focused on how long a product is salable; IT, Information Technology, uses computers to manipulate information; IoT, Internet of Things, a perspective focused on creating a communication network via IT and related methods; UML, Unified Modelling Language, a tool to design software; IDEF0, Intergraded computer aided manufacturing for function modelling, is a tool to describe manufacturing functions; XML, eXtensible Markup Language, is used for creating documents that can be read by both man and machine. Finally, SME are enterprises characterized by limited numbers of employees.
Following these concepts, it is then easier to read and understand the review presented in the next chapter.
The scientific review is divided into three sections. It starts gathering and analyzing scientific research work related to the application of traceability systems and its granularity. Granularity is the quantity of matter represented by a single identifier. Usually, a fine granularity implies large investment in a system capable to sustain it but enables the collection of more information that adds value to the commodity or is useful for logistics. For coarse granularity, implement cost is much lower but becomes difficult to obtain useful information. There is an optimum level of granularity that allows a company to obtain more gains with a lower investment. An internal evaluation is usually required to determine that level, since it depends on the product and processes.
The second section uses some research work to provide insights about the benefits, necessity, requirements, obstacles, and components of traceability systems. Afterwards, the analysis and discussion focus on models, methods, algorithms, and supply chain management. Each section includes a table of reviewed content and the concepts used for review. This division should not be considered exclusive as each study has much more content that what can be exposed here.
There has been a scientific effort to develop several traceability systems in this last decade to deal with the new requirements of governments, companies, and consumers. This section provides the analysis and discussion of the application of traceability systems in food context and their granularity.
Beulens et al. [14] presented a practical case of the implementation of a traceability system that assures quality and safety throughout a food supply and distribution chain. A structure was developed for the information exchange and quality standards that can be applied to all stakeholders. It was necessary a common syntax, as well as the functional integration of the traceability system in the administrative systems, quality control and automation systems. It also required the automation of attribution and reading of identification codes, automatic generation of reports and process optimization. An impartial entity was defined to control the integrity of the system, consumer, and order records to allow more efficiency in recalls. This structure was conceived to be applied in the short term and be continuously developed in the long term. These concepts are fundamental to the introduction of a broad traceability system.
Bollen et al. [15] analyzed the production of apples aiming to determine the steps where mixing of input units occurred and how to minimize them, as traceability is lost because of mixing of inputs without an obvious separation. The mixing of input units causes loss of information related to product origin and product series. The authors observed the whole process with cameras and used markers. It allowed to segment the continuous process without interference and develop a probability model that allowed the prediction of the mixing in each pack. Thus, the packaging process became less random and kept the information relative to the processing series, but not to anterior processing stages. However, this study suffers from some issues as the development of a system only usable by the company analyzed and for its present situation. The system may present some difficulty in transmitting information to other entities further down the supply chain due to lack of compatibility between systems. There will also be some difficulty when the production process changes because it will be necessary to implement a new system that is adequate to the new process. This kind of information, although useful for logistics, does not add value to the product. Thus, it is required a system that does not have to be reformulated when the processing changes, that is compatible with other systems and is able to value products.
Skoglund & Dejmek [16] used fuzzy traceability to limit the consequences of mixing in continuous production. In this situation, the only obvious separations between inputs were cleaning operations. The deterministic approach of traceability should be complemented by fuzzy traceability as is necessary to acknowledge the presence of elements whose origin cannot be easily determined or quantified. To solve this problem, a turbulent diffusion was used to quantify the presence of an element in another, since this study refers to milk production. By quantifying diffusion, it becomes possible to quantify the percentage of elements corresponding to each origin, as it is possible to identify and quantify the mixing zone. This type of traceability is for internal use and allows to avoid mixing of materials with different qualities, besides facilitating the implementation of management and control systems. Again, this is an application of traceability whose consequences have been discussed above. Still, this type of traceability is very important and useful. The collected information can be transmitted to others by using an external traceability system, but it requires access to company data and equipment to implement it.
Frosch et al. [17] dealt with a practical case of an application of a traceability system. However, due to low granularity and low recording frequency, records are kept manually. Measures to improve the system are provided, since it is only applied fish products and not the ingredients added to it. A decade ago, it was underlined the reluctance of companies to the implementation of more capable traceability systems as they consider that the existing methods were enough and that they would not have enough benefits from the investment in more comprehensive systems.
Wang et al. [18] developed a traceability system that monitors current quality and predicts its future variation. It is based on wireless sensors and RFID and is constituted by a graphical interface, quality decay prediction module and warning module. The system uses Global Positioning System (GPS) data relative to the vehicle position and information given by the sensors monitoring the commodities. The graphical interface provides real time data, warnings and how to deal with the situation. The warnings are given as soon as the prediction module finds an anomaly that interferes with the satisfaction of an order while in route. This system serves to aid transportation and does not collect traceability information along an entire food supply chain and is restricted to wireless sensors and RFID.
Li et al. [19] presented a very simple traceability system applied to cucumber production. The objective is to determine the amount of fertilizer to use. The system is composed by a computer, acting as a server, where the information is stored and can be accessed by the decision-support module that will indicate the amount of fertilizer needed in a certain part of the plantation. The access is made via PDA. Despite being a simple and very specific traceability system, it demonstrates very clearly the necessity for traceability systems that do not involve a large investment and shows the availability of technology to implement it.
Thakur et al. [20] analyzed a grain elevator. The grain was transported to silos where it was analyzed and stored without recording information about its origin. So, it became impossible to link inputs and outputs. To solve this problem, an entity-relationship (ER) model was used. In this model, all entities are characterized by whichever relevant characteristics and relationships are the interaction between entities. Then, a database was created in which entity is assigned a unique identifier and based on the relationship with other entities, a new identifier is generated. A relational database management system (RDBMS) is used to implement the model. By having a well-defined structure for the assignment of identifiers it becomes possible to keep traceability information. Still, some information loss will occur due to mixing within the silos. This study also suffers from the issues mentioned above, but by having the proposed structure it is possible to greatly reduce information loss and it becomes much easier to identify problems' causes and responsibility.
Karlsen et al. [21] analyzed a traceability system used in the production of farmed salmon with the objective of determining Critical Traceability Points (CTPs) at different levels of granularity. To determine CTPs, the results from triangulating qualitative interviews, observation and documentation analysis were compiled to cover the flaws of each method. Granularity is the quantity of matter represented by a single identifier. Fine granularity implies heavy investment in a system capable to sustain it but enables the collection of more information that increases value or is useful for logistics. For coarse granularity, implement cost is much lower but becomes difficult to obtain useful information. There is an optimum that allows a company to obtain more gains with an acceptable investment. To determine that point, an internal evaluation was necessary. According to the characteristics of production, several batch sizes were determined and subsequently analyzed to determine which yielded the best results for process control and optimization. The analysis criteria are the capability of maintenance of existing methods, the repetition of information, phenomenon associated with a too fine granularity, and the uselessness of information obtained, which will occur if granularity is too coarse. Granularity does not depend exclusively on the companies, it also depends on regulators, consumers' expectations and the type and amount of information they wish to access. This type of analysis is of extreme importance for the correct application of a traceability system on a SME, as correctly determining granularity provides an equilibrium between usable data, investment to make, risk and responsibility.
Borit & Olsen [22] used a traceability system to help stopping illegal fishing by using globally unique identifiers. Uniqueness is guaranteed by GS1 coding. Records of activity compliant with necessary regulations are associated to an identifier and products can be sold and bought.
Huang et al. [23] presented a very simple, non-isolated, traceability system in which there is cooperation between producers and retailers (supermarkets). It was developed to a client that wishes to access the product data use a machine that reads a code and reports the information. However, it requires the user to have a username and password registered in the system. Although that necessary personal account can serve future purposes like studying consumer trends, it is considered, for this study, that such would be cumbersome as it introduces unwanted complexity on a simpler traceability system with no added benefit. End consumers should access product history without need for registration in the traceability system.
Pizzuti et al. [24] developed a non-isolated traceability system applicable to agri-food products in which clients can access product history via browser. Such facilitates information sharing, however proprietary tools were used, and the developed structure is here deemed too complex to be applicable to small producers and, with some limitations, to medium sized producers.
Lavelli [25] studied a particular and isolated case of the implementation of a traceability system on a medium-sized corporation dealing with poultry meat. The system is presented as a tool that promotes quality, organization, risk management and product value. The possible requirement of a fuzzy algorithm to determine contamination is highlighted as its absence can translate into a wrong evaluation of contamination and consequently excessively increase the scale of recalls.
Hu et al. [26] developed a traceability system applicable to an entire vegetable production and distribution chain. The presented system is very comprehensive and possible to adapt to other supply chains due to fundamentals concepts upon which it was conceived. These fundamental concepts include monitoring of all processing stages, transport and distribution as well as using web-based services to effectively report information. This kind of comprehensiveness is important to the correct application of traceability systems as it maximizes the utility of the collected information and facilitates its transmission.
Trebar et al. [27] developed a sensor-based traceability system. The sensor performance is well discussed per comparison to the traceability system. This system is based in the implementation of gateways in predetermined points where monitoring is executed per opposition of continuous monitoring. Such allows the simplification of traceability systems without too great efficiency loss as well as allows the development of a platform for immediate use, due to simplicity and lower implementation costs, that can be further developed over time and company necessities and capacities change.
Parreño-Marchante et al. [28] used the EPCglobal Architecture Framework to map a process, collecting information through interviews. Based on that information, a traceability system adequate to the situation is devised, being capable of not losing information between entities. The system includes a production and distribution chain and, even though it is a single use case, implementation problems are reduced as they only affect entities outside the chain.
Liu et al. [29] presented a traceability method for a specific case, a company that produces and commercializes eggs. The presented method is simple in theoretical terms but hard to apply as it needs a significant investment in technology capable of dealing with large volumes of data typical of a video-surveillance system.
Wang et al. [30] applied a traceability system based on a wireless sensor network that considers Hazard Analysis and Critical Control Points (HACCP) standards to assure quality and safety. The traceability system and the information flow along the whole process are modeled. Despite being a comprehensive work, as it monitors and reports information since the beginning of the process to the end until the final consumer, it is an isolated case and as such, suffers from already discussed issues although not as severely due to its comprehensiveness.
As demonstrated, traceability systems can have a profound impact in productivity, logistics and sustainability. To achieve those benefits, it is necessary to implement traceability systems correctly. Although the presented systems correctly fulfill the application they were destined to, they sometimes lack comprehensiveness, are applicable to a single company in its present situation or are too demanding to SME's. Thus, it rises the necessity of developing a traceability model that can be applied to an entire food supply chain, that is flexible enough to allow each company to adjust granularity, with reduced capital investment and that is able to be developed and adapted over time. Figure 2 includes the main concepts and application of traceability systems in food context and their granularity that are gathered chronologically in Table 1.
Authors | Products | Granularity | Important concepts |
Beulens et al. [14] | Eggs | Undisclosed | Shared quality standards, shared information infrastructure, prototype traceability system in a SME supply chain |
Bollen et al. [15] | Apples | Output packages linked to input bins | Mixing causes traceability information loss, model to determine and minimize mixing |
Skoglund & Dejmek [16] | Milk | Output packages linked to input silos | Fuzzy traceability, batch virtualization, mixing algorithm |
Frosch et al. [17] | Fish | Output lots liked to fishing vessels | Measures to improve a manual traceability system scenario |
Wang et al. [18] | Undisclosed | Containers | Traceability as a tool to improve distribution and minimize capital loss and waste |
Li et al. [19] | Cucumbers | Terrain lot | Traceability as tool to aid production and comply with regulations |
Thakur et al. [20] | Grain | Shipment to customer | Implementation of traceability in a heavy mixing scenario, quality evaluation |
Karlsen et al. [21] | Fish | Several tested | Impact of granularity in usefulness and cost of a traceability system |
Borit & Olsen [22] | Fish | Dependent on the records of activity | Traceability as a tool to enforce regulations and quality |
Huang et al. [23] | Red jujubes | Final product batch | Consumer access to traceability information, traceability system composed by several different subsystems |
Pizzuti et al. [24] | Frozen vegetables | Dependent of the company | Model for frozen vegetables, supply chain traceability |
Lavelli [25] | Poultry meat | Final product lot | Fuzzy traceability as a tool to comply with regulations |
Hu et al. [26] | Vegetables | Variable, depend on stakeholder | Supply chain traceability |
Trebar et al. [27] | Fish | Box | Supply chain traceability based on wireless sensors |
Parreño-Marchante et al. [28] | Fish | Box | Application of a traceability system in two SME's |
Liu et al. [29] | Eggs | Dependent on the stakeholder | Real time traceability system in a Chinese egg supply chain |
Wang et al. [30] | Peach | Undisclosed | Sensor based supply chain traceability system |
This section highlights the benefits of traceability systems, required concepts for their correct operation, demonstrates their necessity, exposes obstacles to implementation and concepts or technology that composes them.
Jansen-Vullers et al. [31] indicated that traceability is composed of four elements: physical integrity, related to batch dimension and separation; data storage, related to movements and processes; product identification, linked to the previous element in order to identify how a commodity was produced; and report of the information obtained. Traceability has some requirements, namely historical relationships between batches, operations over batches and the values associated to those operations and used means. Batch is defined as the quantity jointly produced, sharing the same characteristics and production cost. The necessity of recording used raw material batches to determine the constitution of product batches is highlighted, as well as to avoid aggregating information relative to production within the product batches. Otherwise, it becomes difficult to determine the origin of problems that arise. Such data should be associated with the production stages. A traceability system should be able to model the relationship between stage dependent and independent data, and to model the composition of products, model operations, properties of the products and production assets. However, the scope of this study is restricted to non-cyclical and convergent processes, which is not always the case of the food industry.
Regattieri et al. [32] stated that traceability is based on four pillars: product identification, data to trace, product routing and traceability tools. Inadequate exposition of information can lead to the emergence of copies and increase in price, which can negatively affect the food sector as it can be susceptible to small price variations. Even so, the correct implementation of traceability systems translates in process optimization, increased security and quality, better marketing, and competitive edges. To be efficient, a traceability system must transmit information about commodities in a precise, timely, complete, and consistent manner. This also leads to faster problem resolution as they enable the efficient determination of issues and affected products.
Gessner et al. [33] discussed the importance of maintaining correct records using information technologies and their advantages per opposition to manual records. Information technologies can record information with a level of detail and precision that would be unfeasible manually. The authors refer some alimentary crisis that occurred in United States of America. It then becomes important to add that food crisis can never be fully averted due to the occurrence of errors related to limitations of the traceability systems themselves or inadequate use, but they can be greatly reduced through a broader and more effective quality control.
Jedermann & Lang [34] monitored a product's quality during transport through a wireless sensor network. The authors demonstrated that the products are subjected to greater and potentially more dangerous variations during transport than an average value can show. Thus, it emerges the necessity of careful quality monitoring during transport.
Donnelly et al. [35] studied transformations in lamb meat and their impact on keeping traceability information. Transformations are critical points for traceability because it is easy to lose information about the constituents of a product and not always information is added about the transformations. This leads to loss of traceability as the lack of that information causes gaps in the product history.
Chrysochou et al. [36] inquired 107 persons from 12 different countries to study the factors that influence the consumers' perspective about traceability information carriers. The authors concluded that the most important factors are trust in information, convenience, impact on quality and safety of the products, consumer and environmental health impact and potential ethical consequences in what concerns privacy. This last factor is of extreme importance and constitutes a big obstacle to the implementation of comprehensive traceability systems.
Bosona & Gebresenbet [37] described traceability systems as an essential tool for food supply chain logistics. Using traceability systems based on information technologies allows an increase in planning capacity and in the efficiency of logistic procedures. The main driving forces that push the development of this systems are also described. They are: regulations, for example, the European General Food Law; social, as consumers become aware of what they consume and want more information in order to improve their capability to select products and to be able to trust what is consumed; safety and quality, as they prevent the transmission of diseases to the public and also enables the determination of infected products and halt their spread; economic, this is the less influential driving force, as it is common for the acquisition traceability systems to be initially expensive; technological, as the onset of cheaper technologies promotes the development of systems by considerably reducing the initial cost. Some advantages and obstacles of traceability systems are referred: increase of consumer satisfaction; better management in a crisis scenario; reduction of logistic costs; closer contact with the consumer and the development of more adequate products; contribution to technological and scientific development and to sustainability, resource limitations, limited available information, lack of information structure, limits in the ability to operate the system and lack of information about the benefits of traceability systems.
Storøy et al. [38] indicated some general principles of traceability systems: identification of units to trace, documentation of transformations and standardization of information exchange. Due to lack of standardization, information exchange is inefficient as it consumes much time and funds. On an individual level, large-dimension companies, have made significant progress in what concerns these systems. Still, those systems are often proprietary and for internal use. Such makes difficult to exchange information between entities. The food sector is very concerned with sharing data due to its sensitive nature and refuse to share it without safety guarantees. The structure used by the authors recommends GS1 and the use of a specific language for each activity sector. For this study, using GS1 is recommended for its worldwide use, but a specific language for each sector may introduce unnecessary complexity when uniqueness is guaranteed.
Aung & Chang [39] stated that globalization led food commodities to travel longer distances between producers and consumers. Due to food crisis, consumers demand quality, safety, and transparency. Alimentary crisis has repercussions on different levels. Socially, there is the danger to public health, damage to commerce and tourism and litigation. Economically, there is a reduction in activity and high health costs. Environmentally, there is an increase in waste, where due to decomposition methane is created. In this sense, traceability systems have been gaining importance as they can have a profound impact in efficiency and sustainability. They allow better management, quality and safety tracing and monitoring, and allow to differentiate products with attributes difficult to differentiate. There is necessity to monitor and trace quality throughout the entire chain to assure quality and safety. Thus, traceability systems should be characterized by their scope, the quantity of information obtained, depth, how high or low in the chain can a product's history be traced, and finally, precision, referent to the degree of safety that a given product can be identified and its movements described.
Asioli et al. [40] stated that exist few empirical studies about the determinants of different levels of traceability capacity at company level, the incentive to the implementation of traceability technologies and their performance. It is easy to define costs but hard to define benefits since they are often intangible. Sixty Italian companies belonging to the fishing sector were inquired and it is concluded that the implementation and maintenance costs were, usually, lower than expected, but so were the benefits. The authors also concluded that the precision of a traceability system is often more preponderant than its scope. Reduced benefits and the evaluation of traceability systems made from the point of view of the consumers has been making the adoption of this systems somewhat slow. It is stated that a traceability solution that is too comprehensive is unable consider the specificities of each company and that a more specific solution is required. For this study, it is considered that such specification would serve as an obstacle to information sharing between different entities, but that may be more efficient on an internal level.
Dabbene et al. [41] indicated the main causes of recalls to be incorrect labeling, faults during production, incorrect packing and lack of identification of conditions that compromise safety. This situation leads to loss of consumer trust and costs with withdrawals and destruction of affected products. Most companies are unable to correctly estimate the amount of product that needs to be removed nor have efficient methods to assure an effective recall. Traceability systems can help companies to execute better recalls and so, a good performance indicator is the capacity to reduce capital loss associated to recalls. Another performance indicator is the existence of a systemic information loss. Traceability by itself does not increase the value of a product but helps other systems to identify desirable characteristics, communicate them and their value. Using an automated traceability system can increase the precision of collected data and the capacity to identify a unit. There has been an emergence of industrial standards for traceability that ease information exchange. Traceability is regulated on three levels, national and international laws and regulations and additional certification.
Aiello et al. [42] studied traceability systems as instruments that potentiate economic gains of a company. With the emergence of non-invasive technologies that allow the evaluation of data automatically and in real time, there is a good opportunity to optimize the number of materials to order and when to promote a sale. However, the implementation of these systems often requires costs with external consultants, software acquisition and staff training. As granularity also has a large impact in the cost and practicability of traceability systems, a model to assess the ideal granularity is presented. However, this study is limited to systems supported by RFID, thus limiting its usability.
Germani et al. [43] explained the necessity of adding information about all elements that have an effect in the environmental sustainability as is the case of, among others, energy consumption and chemical debris. This addition is important to traceability systems. Flaws and opportunities to improve the degree of sustainability and efficiency of any given process can be determined by carefully monitoring these types of parameters.
Thakur & Forås [44] explored a system that monitors temperature over time. This system uses EPC and the collected data can be viewed online. It is demonstrated that that the products suffer greater temperature variations than expected.
Hsiao & Huang [45] studied how the information relative to temperature history is transmitted throughout food supply chains. It is concluded that this exchange is easier between producers and consumers than between suppliers and producers. Thus, there is lack of transparency in information exchange. It should be noted that this lack of transparency can easily occur with the history of other parameters. A traceability system can greatly limit this lack of transparency when information exchange is imposed, and its veracity verified by an impartial external authority.
Alonso-Rorís et al. [46] discussed about the necessity of a low-cost traceability system that can be used by several companies and that is also customizable in order to fulfill each company's individual necessities. Such solves one of the main issues associated with these systems, the high cost. This proposal leads to the implementation of flexibility and commonality in information exchange.
Dandage et al. [47] described the Indian food sector, the waste, the fraud, the insecurity. Those concepts are used as justification for the need of food traceability systems. Although the Indian situation is worse than other world regions, those circumstances are observed globally, albeit with different dimensions.
Raak et al. [48] presented the sources of waste of food products. Themes like overproduction, bad logistics, human errors, equipment faults, residues, power outages, among others were approached. Traceability systems can minimize the impact of such circumstances due to quality focused monitoring.
Olsen & Borit [49] presented the necessary components of a traceability system: mechanism to identify resource units, mechanism to identify the transformations applied to those units and mechanism to store information relative to transformations. A traceability system should be able to answer the following questions: how is the identifier associated to the resource units? What is the structure of the identifier? In what context is the identifier unique? How is the information relative to transformations stored? How are the percentages of constituents stored? How is the data relative to each transformation stored? Facts do not exist in a traceability system, only affirmations and means of verification. Such happens because of errors in data collection or preservation.
Matzembacher et al. [50] characterized food supply chains by their inability to connect information, lack of precision and lack of capability in supplying timely fundamental data in case of crisis. Traceability systems are pointed as a solution as they facilitate the determination of deficiencies and speed up the response. The same technological evolution that allows the automation of traceability systems has been accompanied by the evolution in the food processing. This condition means that the technology that allows a closer proximity with the food products is accompanied by technology that reduces that same familiarity. Special attention is given to packaging to increase familiarization, as it is the part of the product containing more information about any characteristic that is not immediately obvious for the consumers who are willing to pay more for more information. Traceability systems can amplify and speed up the process of obtaining that information. By doing that, consumer trust is retained since the transparency between companies and is increased. There are several obstacles to the implementation of traceability systems: lack of awareness about the benefits, being considered as bureaucracy, fear or unwillingness on the part of busyness partners, economic limitations, limits in the available information and lack of standard structure for information sharing. To achieve the biggest benefits, traceability systems should be implemented throughout entire food supply chains, although it is very difficult to achieve due to different companies' structures, rules, and system along the chain.
Ndraha et al. [51] studied temperature abuse in food supply chains. Such happens due to diverse factors as employed practices, equipment limitations and the position of the commodities during storage and distribution. Although these concepts are not a part of this study, the introduction of a traceability system capable of correct monitoring should be able to report information that allows the timely identification and resolution of these issues.
Stranieri et al. [52] analyzed the Italian wine sector, in which have been implemented traceability systems. Thirty-nine companies of the sector were inquired to determine the reasons that led to the adoption of these systems. Some adhered to comply with legal requirements, others to avoid fraudulent activity, social pressure, or voluntary certification. This study demonstrates that companies invest in more complex systems when they believe that traceability systems are valuable tools. When the adoption is made just to comply with legal requirements, enterprises prefer simpler and flexible systems. Voluntary adoption of more complex traceability systems usually means that a reorganization of whole chain takes place. This reorganization stimulates an effective distribution of responsibility between stakeholders and an increase in the transparency of transactions. Even so, companies that adopted more complex systems sometimes have difficulty in determining how to apply and how much to invest.
Óskarsdóttir & Oddsson [13] underlined the difficulty to assure the quality of food commodities as their production often involves many stages and their transport can be on an international level. Traceability systems allows the reduction of product recalls and alimentary crisis, reinforce reputation, protect brands, increase management efficiency, gain competitive edges, improve access to markets, assure consumer trust, reach legislative or complimentary certification objectives, reach consumer expectations, reduce risk and responsibility, reduce operative costs and stocks, better inventory management and provisioning. Several traceability technologies are compiled and recommend which to use based on a decision tree. Still, the biggest challenge to the implementation of traceability systems is the lack of a standard structure for sharing data.
The necessity of traceability systems is clearly demonstrated by the need for regulatory compliance, consumer demand for safety, quality and transparency, corporate necessity to avoid fraudulent activity and inability to efficiently execute a recall. Although recalls may have several causes, being unable to adequately remove unsafe products can have severe consequences as food crisis and their associated impact on society. Thus, traceability systems can increase security and quality, optimize logistics and production, potentiate capital gains, and increase consumer satisfaction. To achieve these results, traceability systems must be able to model the supply chain, the companies using them, and all transformations associated. To have those abilities, it is necessary to identify all batches, whether inputs or outputs, document all operations over batches and communicate all information to an external impartial authority able to scientifically assess the validity of the information. Still, there are several obstacles that restraint the development and deployment of traceability systems. These include, high costs, reduced available information and capacity to operate the systems, reluctance to the implementation by business partners and lack of information sharing structure. To effectively develop and implement comprehensive chain-wide traceability systems, these issues need to be addressed, if not, traceability systems will lose most of their utility and benefits.
Figure 3 includes the keywords concerning the benefits, necessity, requirements, obstacles, and components of traceability systems described in the relevant scientific literature summarized in Table 2.
Authors | Important concepts |
Jansen-Vullers et al. [31] | Elements and requirements of traceability systems |
Regattieri et al. [32] | Pillars of traceability systems, consequences of inadequate information exposition, benefits and requirements of efficient traceability systems |
Gessner et al. [33] | Advantages of using IT technology to record information and necessity of traceability systems to avoid alimentary crisis |
Jedermann & Lang [34] | Necessity of quality monitoring traceability systems due to the subjection of products to greater variations than expected |
Donnelly et al. [35] | Necessity of recording information about transformations applied to products |
Chrysochou et al. [36] | Consumers' need for information and impact of that information |
Bosona & Gebresenbet [37] | Increase in supply chain logistic efficiency, main driving forces behind the development of traceability systems, advantages, and obstacles |
Storøy et al. [38] | General principles of traceability systems, review on the state of information exchange and necessity of safety guarantees for information exchange |
Aung & Chang [39] | Necessity of traceability systems due to the impact of food crisis, characterization of traceability systems and benefits of application |
Asioli et al. [40] | Review on the factors that led Italian wine companies to implement traceability systems and cost benefit description |
Dabbene et al. [41] | Causes and consequences of recalls, traceability systems proposed as solution, performance indicators of those systems and levels of regulation |
Aiello et al. [42] | Benefits and obstacles of RFID based traceability systems and model to assess optimal granularity |
Germani et al. [43] | Monitoring elements that have an impact in sustainability can lead to opportunities to process optimization |
Thakur & Forås [44] | Demonstration of variations subjected to products |
Hsiao & Huang [45] | Need for traceability systems to increase transparency in information exchange |
Alonso-Rorís et al. [46] | Necessity for low-cost and adaptable traceability systems |
Dandage et al. [47] | Traceability systems as tools to avoid waste, fraud and insecurity |
Raak et al. [48] | Causes of waste and traceability systems as tools to avoid it |
Olsen & Borit [49] | Essential components of traceability systems and useful questions for performance evaluation |
Matzembacher et al. [50] | Corporate inability to provide useful and timely data for the resolution of food crisis, consumers' willingness to pay for information, advantages, and obstacles of food traceability systems |
Ndraha et al. [51] | Traceability systems as tools to prevent temperature abuse in food supply chains |
Stranieri et al. [52] | Factors leading to the adoption of traceability systems and corporate necessities |
Óskarsdóttir & Oddsson [13] | Necessity of traceability systems to monitor quality and technology capable of being incorporated on a traceability system |
After describing the application of traceability systems in food context and their granularity, as well as it benefits, necessity, requirements, obstacles and components, this last section presents traceability and quality models, their use methods, usable algorithms, and concepts relative to supply chain management.
Hsu et al. [53] presented an algorithm for distribution of food perishables. The study highlights the importance of a good distribution system in the maintenance of nutrients and that sometimes forces a less efficient distribution. The premise of the algorithm is the delivery of the goods in the best quality possible. Due to quality monitoring and consequent quantification, it becomes possible to deliver food commodities in more desirable quality levels, depending on the application.
Heese [54] explored inventory management through the use of wireless sensors. Correctly managing inventory is considered, for the purpose of this study, essential to keep a record of the quality variation. Although not necessary in a traceability system, its inclusion can help reducing the probability of error by keeping a closer watch in the products that are not immediately processed or dispatched.
Xiaofeng et al. [55] developed a model that allows to determine the correct allocation of commodities in order to maximize profit. The authors expanded on models for price variation in the sense that it also considers the entry of materials and not only the exit.
Hu et al. [56] presented a model for a traceability system to use in cases where there is a relatively high probability of contamination. An algorithm was developed that considers the presence of a certain material in each product group.
Wang & Li [57] stated that expiration dates are unable to expose the variations subjected to products. The study underlines the importance of correct monitoring since the quality decay leads to a demand decay. To keep product demand, the use of quality stages and associated discount per stage is proposed. A method to determine the optimum discount of each stage is presented. This model is dependent of specific characteristics of each corporation. Still, it serves as a starting point to a local application capable of automatically applying the discounts.
Grunow & Piramuthu [58] explored expiration dates associated to perishable products. The study states that, often, products still have enough quality for consumption and that expiration dates are conservative estimates. Thus, there is a security margin for the consumption of perishables. Nevertheless, it may cause additional waste. This consequence can be avoided by better monitoring of the properties that influence security and quality. The use of RFID to monitor that properties is presented as solution. Additionally, models are described for the determination of the quality level and to assess the profit from the use of that technology, through the value of the information transmitted to the consumer. Despite being a comprehensive solution, it is limited to RFID, which limits this system's application range. Therefore, there is a necessity for more versatile models that allow the use of several different technologies.
Piramuthu et al. [59] discussed about the utility of traceability systems in the loss reduction in products' recall whose levels of quality and safety are not acceptable for consumption. A model that can determine economic loss reduction was presented. The model does not consider transportation costs, monitoring system, marketing and considers that the quality decay starts after production. Although, it demonstrates the utility of correctly monitoring the quality of perishable products.
Hertog et al. [60] presented a simple generic algorithm to determine product quality. Based on the evaluation of quality, an algorithm was developed that allows to optimize the product distribution. Although the algorithm is computationally demanding, small scale application should not become excessively time consuming. The algorithm is based on the FEFO model, that authors consider an evolution of the FIFO model. This model implies that the transport to the consumer is considered. As other authors, it is underlined the lack of compatibility between existing systems and the enormous obstacle that such condition represents. Figure 4 overviews the concepts related to mathematical models used in traceability systems described in Table 3.
Authors | Important concepts |
Hsu et al. [53] | Algorithm for distribution of perishables based on their deliverance at the highest possible quality |
Heese [54] | Inventory management using wireless sensors |
Xiaofeng et al. [55] | Model for the correct allocation of commodities in order to maximize profit |
Hu et al. [56] | Model for a traceability system usable in high probability of contamination scenarios and algorithm to determine contamination |
Wang & Li [57] | Fixed expiration dates are inefficient to expose variations subjected to products; Algorithm to apply discount according to quality variation to keep demand |
Grunow & Piramuthu [58] | Fixed expiration dates as inefficient means to assess product quality and models to determine quality using RFID and profit analysis |
Piramuthu et al. [59] | Traceability systems as tools to increase recall efficiency and model to determine economic loss reduction due to the use of those systems |
Hertog et al. [60] | Algorithm to evaluate quality decay and to distribute perishables based in FEFO |
Sloof et al. [61] used two methods to model quality. One is through the variation of inherent properties of a perishable commodity that degrade over time. The other is based on the value that the consumers attribute to those properties. However, this value is appreciated differently according to the application and consumer experience. By monitoring and quantifying inherent properties and reporting them, a traceability system provides tangibility to those characteristics. Thus, it becomes possible to attribute a value to them. So, quality can be quantified by the additional value conferred by any given property. This value is highly subjective but due to the self-regulatory nature of markets, it will stabilize over time. That makes the value more predictable, less subjective, and easier to attribute.
Bechini et al. [62] presented a simpler architecture for traceability systems than other authors. A simpler architecture is more advantageous in the short term due to its easy implementation. In the long term a simple framework provides easier implementation as well as allowing for a smoother transition to a fully automated traceability system with minimal loss of autonomy by the companies. Although other traceability systems can correctly operate as they were presented, they are, sometimes, too demanding in their requirements for implementation. In this sense, it is here considered that there is a lack of a single traceability system that eases the transition between the absence of a traceability system to a fully automated and efficient one.
Kelepouris et al. [63] presented a model for a traceability system based on RFID and EPC to be used in the agricultural sector. The authors highlight that companies that deal with perishables food products are of small or medium dimension and usually do not possess the necessary means to implement traceability systems, especially when fine granularity is required. Besides, these companies do not want to risk spending considerable resources in these systems if their benefits are not tangible and well defined.
Bechini et al. [64] modelled how different parts of a food supply chain can relate and exchange information through the introduction of a common communication paradigm. XML was used to obtain information of stakeholders. The elaboration of a model that allows information sharing in a standardized manner is necessary.
van der Vorst et al. [65] explored the concepts of LSFO versus FIFO and simulates its utility in a sliced pineapple supply chain. Although this study focuses on the logistic analysis and the increase of the chain efficiency, some very important concepts were described. Those concepts are the utilization of maximum, minimum, and average values for an effective monitoring of remaining shelf-life. It is advised to slightly alter to maximum, minimum, and real current values in a real-time monitoring case. It is considered these values change eases the efficiency analysis of a given production stage by its closeness to the maximum or minimum values. It also allows a better price scaling through more precision and easier visualization of monitored data.
Zhou et al. [66] analyzed the information sharing between sellers and buyers. In the context of the present study, the information sharing should be left to the seller's consideration but restricting it, at its minimum, to legal requirements. This condition allows to preserve corporate autonomy and flexibility on how to deal with customers.
Olsen & Aschan [67] discussed some benefits of traceability systems as the rationing of logistic information and competitive advantage through improvement of documentation. The application of these systems is dependent of the product, commercial obligations, size of the company and the supply chain it belongs to. To successfully apply a traceability system, it is necessity to develop a model of food supply chains. A methodology is defined to develop those models considering limitations of stakeholders, privacy, and data access. It implies interviewing staff to develop the model. As effective as the developed traceability system may be, its application may be slow since all stakeholders must wait for the interviewing process, information compilation, treatment, and application.
Thakur et al. [68] presented a method to keep traceability information using the EPCIS framework, using RFID and unique identifiers generated electronically. This framework is used to avoid proprietary systems that lose much utility for their inability to transmit information to others due to lack of compatibility. It records and reports information about the transport of commodities. So, the information about the transformations or mixing is not kept and relies on the next event to describe the product. This is a common issue, and since it is an external traceability framework, the information relative to the processes subjected to commodities is often accumulated on the final identifiers. This condition happens due to lack of a traceability system capable of operating externally and internally.
Karlsen et al. [69] discussed the concept of granularity in a specific case as to better understand how traceability is affected by it. It is possible to use bigger units when the risk of contamination is low and quality control is less strict. The use of Internet based traceability systems significantly facilitates information sharing without compromising the control of each company over its own information and the necessities of its users. The authors reinforced that the knowledge of all costs allows the implementation of a system whose granularity is adequate to the situation.
Bakker et al. [70] highlighted the necessity for inventory management systems to monitor distinct occurrences in distinct locations and accommodate pricing variation induced by quality variation. Inventory management systems should be a part of traceability systems to monitor heterogeneous quality decay of materials or products that are not used or sold immediately.
Verdouw et al. [71] proposed a method to trace an operational map based in the Internet of Things (IoT) perspective on a floricultural supply chain. Although it focusses on a specific application, the inherent concepts used can be applied to other cases with other perishables.
Pahl & Voß [72] highlighted the need to take into account the deterioration of food perishables in their distribution and presents some algorithms to determine that deterioration.
Jedermann et al. [73] underlined the importance of monitoring quality and remaining shelf-life in food supply chains as a method to increase efficiency and reduce waste. Opposes the FIFO model, commonly used, to the FEFO and LSFO models. This last two models are more efficient logistics wise and ensure more gain and less waste but need a more careful and demanding monitoring to be applied. The main difference between the last two models is that the first considers the time-window until the product becomes improper for consumption and the latter considers the time-window until it becomes no longer salable. This distinction is very important as the consumers tend to avoid products nearing their validity. In this sense, the LSFO model is more useful to portray cases where a company produces or distributes, and another sells the commodities to the end consumer.
Badia-Melis et al. [74] presented trends and necessities of food traceability systems. The Critical Tracking Event that relates to all information about the events that manipulate the products is presented. The Food Track & Trace Ontology that is characterized by agents, products, raw materials, used means and methods is also presented. The TraceFood framework is presented. This framework defines a non-proprietary structure for information sharing on an international level. The theme of intelligent traceability focused on quality to reduce waste is discussed. On this topic, FEFO is compared to the common FIFO methodology. Fuzzy Cognitive Maps to determine mixing between inputs are also discussed. The IoT perspective is highlighted as a mean to present consumers with the cumulative history of products, although there is lacking a structure for storing and sharing information.
Qian et al. [75] discussed on the granularity of traceability systems. The finer the granularity more precise will be the information collected and easier it becomes to solve problems. For a traceability system to be efficient, granularity should be such that allows a precise description of the process. A method to determine the optimal granularity of a traceability system based on queries made to entities in the sector is proposed. That value will have to be determined for each case through evaluation of objectives and capabilities of each company.
Óskarsdóttir & Oddsson [13] explored information technologies that can be used in traceability systems. A method was developed to aid the selection of the most appropriate technology considering a company's necessities and objectives. It is introduced the concept of gateways, which in this context consists in monitoring in well-defined points of a process. This concept is very important as it facilitates the implementation of traceability systems and reduces the costs of implementation.
Figure 5 highlights the most relevant concepts described in Table 4.
Authors | Important concepts |
Sloof et al. [61] | Quality modeling through variation of inherent properties and the value that consumers attribute them |
Bechini et al. [62] | Simple architecture for traceability systems |
Kelepouris et al. [63] | Model for agricultural traceability system based on RFID and EPC |
Bechini et al. [64] | Model for information sharing between stakeholders in a supply chain based on XML |
van der Vorst et al. [65] | Comparison of LSFO versus FIFO in a supply chain, use of max., min., and avg. values to determine the quality uncertainty |
Zhou et al. [66] | Review on information sharing between sellers and buyers |
Olsen & Aschan [67] | Benefits of traceability systems and methodology for modeling food supply chains |
Thakur et al. [68] | Framework for traceability using EPCIS and RFID |
Karlsen et al. [69] | Discussion on granularity and its effect on traceability |
Bakker et al. [70] | Necessity of inventory management as a part of traceability systems to monitor heterogeneous quality decay |
Verdouw et al. [71] | Method to virtualize operations based on the IoT perspective |
Pahl & Voß [72] | Algorithms to determine deterioration of perishable food |
Jedermann et al. [73] | FIFO versus FEFO and LSFO |
Badia-Melis et al.[74] | Review on trends and necessities of traceability systems, concept of CTE; FTTO and the TraceFood, FIFO vs FEFO and FCM to determine mixing |
Qian et al. [75] | Methodology to determine optimal granularity |
Óskarsdóttir & Oddsson [13] | Methodology to select the most appropriate technology to incorporate in a traceability system |
Kwok et al. [76] created a software supported by wireless sensors with the objective of ensuring authenticity of a given product. The model of the system and its constituents are presented in detail. Its constitution was limited to product authentication, but it can be considered as a function of a more comprehensive traceability system.
Woo et al. [77] presented an architecture for a wireless sensor and passive RFID based traceability system. Makes use of the ER model but adds a temporal dimension to incorporate quality degradation. This last characteristic is very important as the ER model does not consider the time consumed by each entity or by the relationships between them. Being restricted to the mentioned sensors, the concepts that can be extrapolated to other traceability systems are limited.
Thakur & Hurburgh [78] defined methods for bulk grain internal and supply chain traceability. For supply chain traceability a UML Use Case diagram was elaborated. The UML Use Case diagram indicates the requirements of the traceability system and which stakeholders require it. The requirements were: record of breeding practices, farming practices, handling and storage practices, processing practices, authenticate claims, compliance with food safety regulations, protect integrity of brand name and document chain of custody. Another UML based model was developed to define information exchange. A function modeling methodology for describing manufacturing functions, namely IDEF0 was used for internal traceability. The model inputs were business needs, consumer preferences and regulatory needs, which also served as control for the model. Developing the internal traceability system implies several steps, namely: determination of the traceability plan, implementation of the traceability plan, evaluation of the system performance, system validation and system maintenance. Information exchange between stakeholders can be done using EDI, XML, TCX and a relational database management system. The presented methodology can encompass enterprises from small to big dimension, and although it was developed with the bulk grain supply chain in mind, the inherent concepts leading to its development can be applied to other supply chains.
Saak [79] presented a simple hypothetical case to determine the increase of product value due to the information provided by a traceability system. Some applicability is lost due to the hypothetical basis, but is, nevertheless, a good starting point to real case analysis.
Gaukler et al. [80] explored the benefits of dynamic expiration dates per opposition to fixed ones and uses a real case to demonstrate them. The benefits are the same as those exposed by other authors, such as, increase in efficiency, sustainability and profit and waste reduction. However, the determination of the uncertainty when measuring quality is highlighted as well as the necessity of always considering the quality wherewith a product is acquired and the quality when a product is manipulated. Figure 6 gathers the main concepts related to the simulation models described in Table 5.
Authors | Important concepts |
Kwok et al. [76] | System model and software for wireless sensor-based product authentication |
Woo et al. [77] | Model for sensor-based traceability system using the ER model adding the temporal dimension |
Thakur & Hurburgh [78] | Methods to elaborate internal and external traceability models |
Saak [79] | Increase in product value due to information provided by traceability systems |
Gaukler et al. [80] | Benefits of dynamic expiration dates per opposition to fixed expiration dates |
Food safety, economic gain, better logistics, sustainability, trust, satisfaction are advantages associated with a proper implementation of traceability systems. However, fundamental and recurrent issues exist that can make the implementation of a traceability system rather difficult. Issues as the determination of granularity, mixing, contamination, transformations, tangible benefits, the making of a gapless product history and analysis made from the end user point of view of maximum quality at all times. Granularity should be left to enterprises to decide as it has a big impact on the initial investment. Mixing and contamination can make use of existing algorithms and tools. The issue if transformations can be alleviated by introducing gateways. A cost benefit assessment can be made by comparing the increase in price conferred by traceability information. To create a complete history, a unified traceability model capable to link all elements of the supply chain is necessary. Information loss is inevitable but the transfer of that workload from paper-based systems to autonomous systems can greatly reduce this loss. Additionally, a unifying model also imposes standard practices for traceability which can be beneficial to all as it becomes less confusing to determine what to transmit and how to read the information. Still, this unifying model has be able to maximize the utility of the information and minimize the associated bureaucracy. Maximum quality is not always convenient depending on the end use of a given product, as such, quality should be determined and declared by producers leaving the choice of purchase to the consumer. Inevitably, large data volumes will arise and handling them requires a structure that is insofar non-existent.
This review aids to clear the main flaws and benefits of current traceability systems, along with detailing the necessary concepts and requirements. The analysis presented aims to help SME's by presenting models, methodologies and technologies that allow for a lower initial investment and allow for better product placement and marketing. Following the principles here described, an open-source traceability focused on safety and quality is to be developed in Part Ⅱ of this study. This system will be based on HACCP flowcharts to define gateways for quality evaluation and will encompass external verification and product history maintenance. This strategy can reduce the initial cost, limiting it to the acquisition of technology. SMEs can benefit from such a system by the tighter quality control involved and possible future integration of any tools supposed valuable. The system will be developed specifically for SMEs and thus it will not require mature IT capabilities.
All authors declare no conflicts of interest in this paper.
This study is within the activities of project PrunusPós—Otimização de processos de armazenamento, conservação em frio, embalamento ativo e/ou inteligente, e rastreabilidade da qualidade alimentar no póscolheita de produtos frutícolas (Optimization of processes of storage, cold conservation, active and/or intelligent packaging, and traceability of food quality in the postharvest of fruit products), Operation n.º PDR2020-101-031695 (Partner), Consortium n.º 87, Initiative n.º 175 promoted by PDR2020 and co-financed by FEADER under the Portugal 2020 initiative.
[1] |
Karlsen KM, Dreyer B, Olsen P, et al. (2013) Literature review: Does a common theoretical framework to implement food traceability exist? Food Control 32: 409-417. doi: 10.1016/j.foodcont.2012.12.011
![]() |
[2] |
Moe T (1998) Perspectives on traceability in food manufacture. Trends Food Sci Technol 9: 211-214. doi: 10.1016/S0924-2244(98)00037-5
![]() |
[3] | ISO (1994) ISO Standard 8402: 1994-Quality management and quality assurance-Vocabulary. International Organization for Standardization (ISO). |
[4] | ISO (2015) ISO Standard 9000: 2015-Quality management systems-Fundamentals and vocabulary. International Organization for Standardization (ISO). |
[5] | ISO (2007) ISO Standard 22005: 2007-Traceability in the feed and food chain-General principles and basic requirements for system design and implementation. International Organization for Standardization (ISO). |
[6] | Joint FAO/WHO Codex Alimentarius Commission (2013) Codex alimentarius: Cereals, pulses, legumes and vegetable proteins. 21st ed. Rome: World Health Organization: Food and Agriculture Organization of the United Nations (WHO/FAO). |
[7] |
Olsen P, Borit M (2013) How to define traceability. Trends Food Sci Technol 29: 142-150. doi: 10.1016/j.tifs.2012.10.003
![]() |
[8] |
Charlebois S, Sterling B, Haratifar S, et al. (2014) Comparison of global food traceability regulations and requirements. Compr Rev Food Sci Food Saf 13: 1104-1123. doi: 10.1111/1541-4337.12101
![]() |
[9] |
Lupien JR (2005) Food quality and safety: Traceability and labeling. Crit Rev Food Sci Nutr 45: 119-123. doi: 10.1080/10408690490911774
![]() |
[10] |
Souali K, Rahmaoui O, Ouzzif M (2017) An overview of traceability: Towards a general multi-domain model. Adv Sci Technol Eng Syst J 2: 356-361. doi: 10.25046/aj020345
![]() |
[11] |
Walker GS (2017) Food authentication and traceability: An Asian and Australian perspective. Food Control 72: 168-172. doi: 10.1016/j.foodcont.2016.01.028
![]() |
[12] | Opara LU (2003) Traceability in agriculture and food supply chain: A review of basic concepts, technological implications, and future prospects. Food Agric Environ 1: 101-106. |
[13] |
Óskarsdóttir K, Oddsson GV (2019) Towards a decision support framework for technologies used in cold supply chain traceability. J Food Eng 240: 153-159. doi: 10.1016/j.jfoodeng.2018.07.013
![]() |
[14] |
Beulens AJM, Broens DF, Folstar P, et al. (2005) Food safety and transparency in food chains and networks. Relationships and challenges. Food Control 16: 481-486. doi: 10.1016/j.foodcont.2003.10.010
![]() |
[15] |
Bollen AF, Riden CP, Cox NR (2007) Agricultural supply system traceability, Part Ⅰ: Role of packing procedures and effects of fruit mixing. Biosyst Eng 98: 391-400. doi: 10.1016/j.biosystemseng.2007.07.011
![]() |
[16] |
Skoglund T, Dejmek P (2007) Fuzzy traceability: A process simulation derived extension of the traceability concept in continuous food processing. Food Bioprod. Process 85: 354-359. doi: 10.1205/fbp07044
![]() |
[17] |
Frosch S, Randrup M, Thorup-Frederiksen M (2008) Opportunities for the herring industry to optimize operations through information recording, effective traceability systems, and use of advanced data analysis. J Aquat Food Prod Technol 17: 387-403. doi: 10.1080/10498850802369179
![]() |
[18] |
Wang L, Kwok SK, Ip WH (2010) A radio frequency identification and sensor-based system for the transportation of food. J Food Eng 101: 120-129. doi: 10.1016/j.jfoodeng.2010.06.020
![]() |
[19] |
Li M, Qian JP, Yang XT, et al. (2010) A PDA-based record-keeping and decision-support system for traceability in cucumber production. Comput Electron Agric 70: 69-77. doi: 10.1016/j.compag.2009.09.009
![]() |
[20] |
Thakur M, Martens BJ, Hurburgh CR (2011) Data modeling to facilitate internal traceability at a grain elevator. Comput Electron Agric 75: 327-336. doi: 10.1016/j.compag.2010.12.010
![]() |
[21] |
Karlsen KM, Sørensen CF, Forås F, et al. (2011) Critical criteria when implementing electronic chain traceability in a fish supply chain. Food Control 22: 1339-1347. doi: 10.1016/j.foodcont.2011.02.010
![]() |
[22] |
Borit M., Olsen P (2012) Evaluation framework for regulatory requirements related to data recording and traceability designed to prevent illegal, unreported and unregulated fishing. Mar Policy 36: 96-102. doi: 10.1016/j.marpol.2011.03.012
![]() |
[23] |
Huang F, Zhang S, Zhao H (2012) Design and application of quality traceability system based on RFID technology for red jujubes. IFIP Adv Inf Commun Technol 368: 371-380. doi: 10.1007/978-3-642-27281-3_43
![]() |
[24] | Pizzuti T, Mirabelli G, Gómez-González F, et al. (2012) Modeling of an agro-food traceability system : The case of the frozen vegetables. Proceedings of the 2012 International Conference on Industrial Engineering and Operations Management, 1065-1074. |
[25] |
Lavelli V (2013) High-warranty traceability system in the poultry meat supply chain: A medium sized enterprise case study. Food Control 33: 148-156. doi: 10.1016/j.foodcont.2013.02.022
![]() |
[26] |
Hu J, Zhang X, Moga LM, et al. (2013) Modeling and implementation of the vegetable supply chain traceability system. Food Control 30: 341-353. doi: 10.1016/j.foodcont.2012.06.037
![]() |
[27] |
Trebar M, Lotrič M, Fonda I, et al. (2013) RFID data loggers in fish supply chain traceability. Int J Antennas Propag 2013(3-4): 1-9. doi: 10.1155/2013/875973
![]() |
[28] |
Parreño-Marchante A, Alvarez-Melcon A, Trebar M, et al. (2014) Advanced traceability system in aquaculture supply chain. J Food Eng 122: 99-109. doi: 10.1016/j.jfoodeng.2013.09.007
![]() |
[29] |
Liu F, Wang Y, Jia Y, et al. (2015) The egg traceability system based on the video capture and wireless networking technology. Int J Sens Networks 17: 211-216. doi: 10.1504/IJSNET.2015.069582
![]() |
[30] |
Wang X, Fu D, Fruk G, et al. (2018) Improving quality control and transparency in honey peach export chain by a multi-sensors-managed traceability system. Food Control 88: 169-180. doi: 10.1016/j.foodcont.2018.01.008
![]() |
[31] |
Jansen-Vullers MH, Van Dorp CS, Beulens AJM (2003) Managing traceability information in manufacture. Int J Inf Manage 23: 395-413. doi: 10.1016/S0268-4012(03)00066-5
![]() |
[32] |
Regattieri A, Gamberi M, Manzini R (2007) Traceability of food products: General framework and experimental evidence. J Food Eng 81: 347-356. doi: 10.1016/j.jfoodeng.2006.10.032
![]() |
[33] |
Gessner GH, Volonino L, Fish LA (2007) One-up, one-back ERM in the food supply chain. Inf Syst Manag 24: 213-222. doi: 10.1080/10580530701404561
![]() |
[34] | Jedermann R, Lang W (2007) Semi-passive RFID and beyond: steps towards automated quality tracing in the food chain. Int J Radio Freq Identif Technol Appl 1: 247-259. |
[35] |
Donnelly KAM, Karlsen KM, Olsen P (2009) The importance of transformations for traceability-A case study of lamb and lamb products. Meat Sci 83: 68-73. doi: 10.1016/j.meatsci.2009.04.006
![]() |
[36] |
Chrysochou P, Chryssochoidis G, Kehagia O (2009) Traceability information carriers. The technology backgrounds and consumers' perceptions of the technological solutions. Appetite 53: 322-331. doi: 10.1016/j.appet.2009.07.011
![]() |
[37] |
Bosona T, Gebresenbet G (2013) Food traceability as an integral part of logistics management in food and agricultural supply chain. Food Control 33: 32-48. doi: 10.1016/j.foodcont.2013.02.004
![]() |
[38] |
Storoy J, Thakur M, Olsen P (2013) The Trace Food Framework-Principles and guidelines for implementing traceability in food value chains. J Food Eng 115: 41-48. doi: 10.1016/j.jfoodeng.2012.09.018
![]() |
[39] |
Aung MM, Chang YS (2014) Traceability in a food supply chain: Safety and quality perspectives. Food Control 39: 172-184. doi: 10.1016/j.foodcont.2013.11.007
![]() |
[40] |
Asioli D, Boecker A, Canavari M (2014) On the linkages between traceability levels and expected and actual traceability costs and benefits in the Italian fishery supply chain. Food Control 46: 10-17. doi: 10.1016/j.foodcont.2014.04.048
![]() |
[41] |
Dabbene F, Gay P, Tortia C (2014) Traceability issues in food supply chain management: A review. Biosyst Eng 120: 65-80. doi: 10.1016/j.biosystemseng.2013.09.006
![]() |
[42] |
Aiello G, Enea M, Muriana C (2015) The expected value of the traceability information. Eur J Oper Res 244: 176-186. doi: 10.1016/j.ejor.2015.01.028
![]() |
[43] |
Germani M, Mandolini M, Marconi M, et al. (2015) A system to increase the sustainability and traceability of supply chains. Procedia CIRP 29: 227-232. doi: 10.1016/j.procir.2015.02.199
![]() |
[44] |
Thakur M, Forås E (2015) EPCIS based online temperature monitoring and traceability in a cold meat chain. Comput. Electron Agric 117: 22-30. doi: 10.1016/j.compag.2015.07.006
![]() |
[45] |
Hsiao HI, Huang KL (2016) Time-temperature transparency in the cold chain. Food Control 64: 181-188. doi: 10.1016/j.foodcont.2015.12.020
![]() |
[46] |
Alonso-Rorís VM, Álvarez-Sabucedo L, Santos-Gago JM, et al. (2016) Towards a cost-effective and reusable traceability system. A semantic approach. Comput Ind 83: 1-11. doi: 10.1016/j.compind.2016.08.003
![]() |
[47] |
Dandage K, Badia-Melis R, Ruiz-García L (2017) Indian perspective in food traceability: A review. Food Control 71: 217-227. doi: 10.1016/j.foodcont.2016.07.005
![]() |
[48] |
Raak N, Symmank C, Zahn S, et al. (2017) Processing- and product-related causes for food waste and implications for the food supply chain. Waste Manag 61: 461-472. doi: 10.1016/j.wasman.2016.12.027
![]() |
[49] |
Olsen P, Borit M (2018) The components of a food traceability system. Trends Food Sci Technol 77: 143-149. doi: 10.1016/j.tifs.2018.05.004
![]() |
[50] |
Matzembacher DE, do Carmo Stangherlin I, Slongo LA, et al. (2018) An integration of traceability elements and their impact in consumer's trust. Food Control 92: 420-429. doi: 10.1016/j.foodcont.2018.05.014
![]() |
[51] |
Ndraha N, Hsiao HI, Vlajic J, et al. (2018) Time-temperature abuse in the food cold chain: Review of issues, challenges, and recommendations. Food Control 89: 12-21. doi: 10.1016/j.foodcont.2018.01.027
![]() |
[52] |
Stranieri S, Cavaliere A, Banterle A (2018) The determinants of voluntary traceability standards. The case of the wine sector. Wine Econ Policy 7: 45-53. doi: 10.1016/j.wep.2018.02.001
![]() |
[53] |
Hsu CI, Hung SF, Li HC (2007) Vehicle routing problem with time-windows for perishable food delivery. J Food Eng 80: 465-475. doi: 10.1016/j.jfoodeng.2006.05.029
![]() |
[54] | Heese HS (2007) Inventory Record Inaccuracy, Double Marginalization, and RFID Adoption. Prod Oper Manag 16: 542-553. |
[55] |
Xiaofeng L, Tang O, Huang P (2008) Dynamic pricing and ordering decision for the perishable food of the supermarket using RFID technology. Asia Pacific J Mark Logist 20: 7-22. doi: 10.1108/13555850810844841
![]() |
[56] | Hu Z, Jian Z, Shen P, et al.(2009) Modeling method of traceability system based on information flow in meat food supply chain. WSEAS Trans Inf Sci Appl 6: 1094-1103. |
[57] |
Wang X, Li D (2012) A dynamic product quality evaluation based pricing model for perishable food supply chains. Omega 40: 906-917. doi: 10.1016/j.omega.2012.02.001
![]() |
[58] |
Grunow M, Piramuthu S (2013) RFID in highly perishable food supply chains - Remaining shelf life to supplant expiry date? Int J Prod Econ 146: 717-727. doi: 10.1016/j.ijpe.2013.08.028
![]() |
[59] |
Piramuthu S, Farahani P, Grunow M (2013) RFID-generated traceability for contaminated product recall in perishable food supply networks. Eur J Oper Res 225: 253-262. doi: 10.1016/j.ejor.2012.09.024
![]() |
[60] | Hertog MLATM, Uysal I, Verlinden BM, et al. (2014) Shelf life modelling for first-expired-first-out warehouse management. Philos Trans R Soc A: 1-15. |
[61] |
Sloof M, Tijskens P, Wilkinson EC (1996) Concepts for modelling the quality of perishable products. Trends Food Sci Technol 7: 165-171. doi: 10.1016/0924-2244(96)81257-X
![]() |
[62] | Bechini A, Cimino MGCA, Lazzerini B, et al. (2006) A General framework for food traceability. 2005 Symposium on Applications and the Internet Workshops (SAINT 2005 Workshops), 366-369. |
[63] |
Kelepouris T, Pramatari K, Doukidis G (2007) RFID-enabled traceability in the food supply chain. Ind Manag Data Syst 107: 183-200. doi: 10.1108/02635570710723804
![]() |
[64] |
Bechini A, Cimino MGCA, Marcelloni F, et al. (2007) Patterns and technologies for enabling supply chain traceability through collaborative e-business. Inf Softw Technol 50: 342-359. doi: 10.1016/j.infsof.2007.02.017
![]() |
[65] |
Jvan der Vorst JGAJ, Tromp SO, van der Zee DJ (2009) Simulation modelling for food supply chain redesign; Integrated decision making on product quality, sustainability and logistics. Int J Prod Res 47: 6611-6631. doi: 10.1080/00207540802356747
![]() |
[66] |
Zhou W, Kapoor G, Piramuthu S (2009) RFID-enabled item-level product information revelation. Eur J Inf Syst 18: 570-577. doi: 10.1057/ejis.2009.45
![]() |
[67] |
Olsen P, Aschan M (2010) Reference method for analyzing material flow, information flow and information loss in food supply chains. Trends Food Sci Technol 21: 313-320. doi: 10.1016/j.tifs.2010.03.002
![]() |
[68] |
Thakur M, Sørensen CF, Bjørnson FO, et al. (2011) Managing food traceability information using EPCIS framework. J Food Eng 103: 417-433. doi: 10.1016/j.jfoodeng.2010.11.012
![]() |
[69] |
Karlsen KM, Dreyer B, Olsen P, et al. (2012) Granularity and its role in implementation of seafood traceability. J Food Eng 112: 78-85. doi: 10.1016/j.jfoodeng.2012.03.025
![]() |
[70] |
Bakker M, Riezebos J, Teunter RH (2012) Review of inventory systems with deterioration since 2001. Eur J Oper Res 221: 275-284. doi: 10.1016/j.ejor.2012.03.004
![]() |
[71] |
Verdouw CN, Beulens AJM, van der Vorst JGAJ (2013) Virtualisation of floricultural supply chains: A review from an internet of things perspective. Comput Electron Agric 99: 60-175. doi: 10.1016/j.compag.2013.09.006
![]() |
[72] |
Pahl J, Voß S (2014) Integrating deterioration and lifetime constraints in production and supply chain planning: A survey. Eur J Oper Res 238: 654-674. doi: 10.1016/j.ejor.2014.01.060
![]() |
[73] | Jedermann R, Nicometo M, Uysal I, et al. (2014) Reducing food losses by intelligent food logistics Reducing food losses by intelligent food logistics. Philos Trans R Soc, Series A: 1-20. |
[74] |
Badia-Melis R, Mishra P, Ruiz-García L (2015) Food traceability: New trends and recent advances. A review. Food Control 57: 393-401. doi: 10.1016/j.foodcont.2015.05.005
![]() |
[75] |
Qian J, Fan B, Wu X, et al. (2017) Comprehensive and quantifiable granularity: A novel model to measure agro-food traceability. Food Control 74: 98-106. doi: 10.1016/j.foodcont.2016.11.034
![]() |
[76] | Kwok SK, Tsang AHC, Ting JSL, et al. (2008) An intelligent RFID-based electronic anti-counterfeit system (InRECS) for the manufacturing industry. IFAC 41: 5482-5487. |
[77] |
Woo SH, Choi JY, Kwak C, et al. (2009) An active product state tracking architecture in logistics sensor networks. Comput Ind 60: 149-160. doi: 10.1016/j.compind.2008.12.001
![]() |
[78] |
Thakur M, Hurburgh CR (2009) Framework for implementing traceability system in the bulk grain supply chain. J Food Eng 95: 617-626. doi: 10.1016/j.jfoodeng.2009.06.028
![]() |
[79] |
Saak AE (2016) Traceability and reputation in supply chains. Int J Prod Econ 177: 149-162. doi: 10.1016/j.ijpe.2016.04.008
![]() |
[80] |
Gaukler G, Ketzenberg M, Salin V (2017) Establishing dynamic expiration dates for perishables: An application of RFID and sensor technology. Int J Prod Econ 193: 617-632. doi: 10.1016/j.ijpe.2017.07.019
![]() |
1. | Agapi Dima, Eleni Arvaniti, Chrysostomos Stylios, Dimitrios Kafetzopoulos, Dimitris Skalkos, Adapting Open Innovation Practices for the Creation of a Traceability System in a Meat-Producing Industry in Northwest Greece, 2022, 14, 2071-1050, 5111, 10.3390/su14095111 | |
2. | Nainsi Gupta, Gunjan Soni, Sameer Mittal, Indrajit Mukherjee, Bharti Ramtiyal, Devesh Kumar, Evaluating Traceability Technology Adoption in Food Supply Chain: A Game Theoretic Approach, 2023, 15, 2071-1050, 898, 10.3390/su15020898 | |
3. | Martim L. Aguiar, Pedro D. Gaspar, Pedro D. Silva, Luísa C. Domingues, David M. Silva, Real-Time Temperature and Humidity Measurements during the Short-Range Distribution of Perishable Food Products as a Tool for Supply-Chain Energy Improvements, 2022, 10, 2227-9717, 2286, 10.3390/pr10112286 | |
4. | Carlos M Fernandez, Joel Alves, Pedro Dinis Gaspar, Tânia M Lima, Pedro D Silva, Innovative processes in smart packaging. A systematic review, 2023, 103, 0022-5142, 986, 10.1002/jsfa.11863 | |
5. | Pranav Vyas, Dharmendra Patel, 2022, Blockchain based applications' future challenges in food traceability, 978-1-6654-7886-1, 1, 10.1109/IRTM54583.2022.9791625 | |
6. | Charles B. Herron, Laura J. Garner, Aftab Siddique, Tung-Shi Huang, Jesse C. Campbell, Shashank Rao, Amit Morey, Building “First Expire, First Out” models to predict food losses at retail due to cold chain disruption in the last mile, 2022, 6, 2571-581X, 10.3389/fsufs.2022.1018807 | |
7. | Tsiqatun Nasyiah, Ilyas Masudin, Fien Zulfikarijah, Devika Kannan, Aniek Rumijati, Rahmad Wijaya, Explaining Sustainable Performance With SEM–FsQCA: The Role of Traceability Systems, Knowledge Management, Halal SCM Practices, and Spiritual Leadership in Small–Medium Enterprises (SMEs), 2024, 71, 0018-9391, 5691, 10.1109/TEM.2024.3365660 | |
8. | Camila C. Kersten, Jaqueline Mastrocola Carneiro Kerber, Jailson dos Santos Silva, Marina Bouzon, Lucila Maria de Souza Campos, Traceability in the agri-food supply chain: a new perspective under the Circular Economy approach, 2024, 34, 1980-5411, 10.1590/0103-6513.20240009 | |
9. | Xiaofeng Wang, Xiaoming Bi, 2024, Application of BIM Algorithm and Block Chain Technology in the Construction of Agricultural Safety Traceability System, 979-8-3503-8295-2, 1, 10.1109/ICDCOT61034.2024.10515791 | |
10. | Mohammad Rifat Ahmmad Rashid, Mahamudul Hasan, Md Ariful Islam, Syeda Tasfia Tasnim, Rawnak Jahan Taifa, Sraboni Mahbub, Nafees Mansoor, Md Sawkat Ali, Taskeed Jabid, Maheen Islam, Mohammad Manzurul Islam, Transforming agri-food value chains in Bangladesh: A practical application of blockchain for traceability and fair pricing, 2024, 10, 24058440, e40091, 10.1016/j.heliyon.2024.e40091 | |
11. | Linhai Wu, Zhiyuan Ling, Jingxiang Zhang, Xiaoting Dai, Xiujuan Chen, Safe Food Supply Chain as Health Network: An Evolutionary Game Analysis of Behavior Strategy for Quality Investment, 2024, 61, 0046-9580, 10.1177/00469580241244728 | |
12. | Pedro Fernandes, Pedro D. Gaspar, Pedro D. Silva, Peltier Cell Integration in Packaging Design for Minimizing Energy Consumption and Temperature Variation during Refrigerated Transport, 2023, 7, 2411-9660, 88, 10.3390/designs7040088 | |
13. | Priyanka Vern, Anupama Panghal, Rahul S Mor, Vikas Kumar, Sandeep Jagtap, Blockchain-based traceability framework for agri-food supply chain: a proof-of-concept, 2024, 1936-9735, 10.1007/s12063-024-00529-6 | |
14. | Aries Susanty, Nia Budi Puspitasari, Zainal Fanani Rosyada, Muhamad Aria Pratama, Edi Kurniawan, Design of blockchain-based halal traceability system applications for halal chicken meat-based food supply chain, 2024, 16, 2511-2104, 1449, 10.1007/s41870-023-01650-8 | |
15. | Zaryab Shafi, Vinay Kumar Pandey, Rahul Singh, Sarvesh Rustagi, Carbon dots-nanosensors: Advancement in food traceability for a sustainable environmental development, 2024, 165, 09567135, 110693, 10.1016/j.foodcont.2024.110693 | |
16. | P B Purwandoko, K B Seminar, C Litaay, A Triyono, N K I Mayasti, Analysis and Design of Internal Traceability System for Rice Processing Industry, 2023, 1168, 1755-1307, 012050, 10.1088/1755-1315/1168/1/012050 | |
17. | Valentina Maria Merlino, Simone Blanc, Stefano Massaglia, Innovation in agriculture and the agri-food chain: Some insights, 2023, 8, 2471-2086, 550, 10.3934/agrfood.2023029 | |
18. | Guangjie Lv, Caixia Song, Pengmin Xu, Zhiguo Qi, Heyu Song, Yi Liu, Blockchain-Based Traceability for Agricultural Products: A Systematic Literature Review, 2023, 13, 2077-0472, 1757, 10.3390/agriculture13091757 | |
19. | Angelo Corallo, Martina De Giovanni, Maria Elena Latino, Marta Menegoli, Fulvio Signore, 2023, A Case Study to Evaluate the Diffusion of Technological Traceability Systems: Exploratory Insights from South Italy Agri-food Companies, 978-1-6654-7583-9, 84, 10.1109/AIBT57480.2023.00023 | |
20. | João Laia Antunes, Pedro Dinho Silva, Pedro Dinis Gaspar, Thermal Behavior of Alveoli with Phase Change Materials in Fruit Packaging, 2025, 15, 2076-3417, 1924, 10.3390/app15041924 | |
21. | Mati Ullah Khan, Pengfei Yu, Yuyin Wu, Zhiwei Chen, Ling Kong, Anum Farid, Jiaqi Cui, Jun Yang, Comprehensive review of enzymes (protease, lipase) in milk: Impact on storage quality, detection methods, and control strategies, 2025, 24, 1541-4337, 10.1111/1541-4337.70164 | |
22. | R. Shreeja, S. Kayalvizhi, S. Ahamed Ali, B. Padmavathi, 2025, Chapter 41, 978-981-96-0923-9, 527, 10.1007/978-981-96-0924-6_41 | |
23. | Marina Balaic, Samo Bobek, Vujica Lazović, Simona Sternad Zabukovšek, 2025, 13, 9789612990107, 271, 10.18690/um.epf.7.2025.13 |
Authors | Products | Granularity | Important concepts |
Beulens et al. [14] | Eggs | Undisclosed | Shared quality standards, shared information infrastructure, prototype traceability system in a SME supply chain |
Bollen et al. [15] | Apples | Output packages linked to input bins | Mixing causes traceability information loss, model to determine and minimize mixing |
Skoglund & Dejmek [16] | Milk | Output packages linked to input silos | Fuzzy traceability, batch virtualization, mixing algorithm |
Frosch et al. [17] | Fish | Output lots liked to fishing vessels | Measures to improve a manual traceability system scenario |
Wang et al. [18] | Undisclosed | Containers | Traceability as a tool to improve distribution and minimize capital loss and waste |
Li et al. [19] | Cucumbers | Terrain lot | Traceability as tool to aid production and comply with regulations |
Thakur et al. [20] | Grain | Shipment to customer | Implementation of traceability in a heavy mixing scenario, quality evaluation |
Karlsen et al. [21] | Fish | Several tested | Impact of granularity in usefulness and cost of a traceability system |
Borit & Olsen [22] | Fish | Dependent on the records of activity | Traceability as a tool to enforce regulations and quality |
Huang et al. [23] | Red jujubes | Final product batch | Consumer access to traceability information, traceability system composed by several different subsystems |
Pizzuti et al. [24] | Frozen vegetables | Dependent of the company | Model for frozen vegetables, supply chain traceability |
Lavelli [25] | Poultry meat | Final product lot | Fuzzy traceability as a tool to comply with regulations |
Hu et al. [26] | Vegetables | Variable, depend on stakeholder | Supply chain traceability |
Trebar et al. [27] | Fish | Box | Supply chain traceability based on wireless sensors |
Parreño-Marchante et al. [28] | Fish | Box | Application of a traceability system in two SME's |
Liu et al. [29] | Eggs | Dependent on the stakeholder | Real time traceability system in a Chinese egg supply chain |
Wang et al. [30] | Peach | Undisclosed | Sensor based supply chain traceability system |
Authors | Important concepts |
Jansen-Vullers et al. [31] | Elements and requirements of traceability systems |
Regattieri et al. [32] | Pillars of traceability systems, consequences of inadequate information exposition, benefits and requirements of efficient traceability systems |
Gessner et al. [33] | Advantages of using IT technology to record information and necessity of traceability systems to avoid alimentary crisis |
Jedermann & Lang [34] | Necessity of quality monitoring traceability systems due to the subjection of products to greater variations than expected |
Donnelly et al. [35] | Necessity of recording information about transformations applied to products |
Chrysochou et al. [36] | Consumers' need for information and impact of that information |
Bosona & Gebresenbet [37] | Increase in supply chain logistic efficiency, main driving forces behind the development of traceability systems, advantages, and obstacles |
Storøy et al. [38] | General principles of traceability systems, review on the state of information exchange and necessity of safety guarantees for information exchange |
Aung & Chang [39] | Necessity of traceability systems due to the impact of food crisis, characterization of traceability systems and benefits of application |
Asioli et al. [40] | Review on the factors that led Italian wine companies to implement traceability systems and cost benefit description |
Dabbene et al. [41] | Causes and consequences of recalls, traceability systems proposed as solution, performance indicators of those systems and levels of regulation |
Aiello et al. [42] | Benefits and obstacles of RFID based traceability systems and model to assess optimal granularity |
Germani et al. [43] | Monitoring elements that have an impact in sustainability can lead to opportunities to process optimization |
Thakur & Forås [44] | Demonstration of variations subjected to products |
Hsiao & Huang [45] | Need for traceability systems to increase transparency in information exchange |
Alonso-Rorís et al. [46] | Necessity for low-cost and adaptable traceability systems |
Dandage et al. [47] | Traceability systems as tools to avoid waste, fraud and insecurity |
Raak et al. [48] | Causes of waste and traceability systems as tools to avoid it |
Olsen & Borit [49] | Essential components of traceability systems and useful questions for performance evaluation |
Matzembacher et al. [50] | Corporate inability to provide useful and timely data for the resolution of food crisis, consumers' willingness to pay for information, advantages, and obstacles of food traceability systems |
Ndraha et al. [51] | Traceability systems as tools to prevent temperature abuse in food supply chains |
Stranieri et al. [52] | Factors leading to the adoption of traceability systems and corporate necessities |
Óskarsdóttir & Oddsson [13] | Necessity of traceability systems to monitor quality and technology capable of being incorporated on a traceability system |
Authors | Important concepts |
Hsu et al. [53] | Algorithm for distribution of perishables based on their deliverance at the highest possible quality |
Heese [54] | Inventory management using wireless sensors |
Xiaofeng et al. [55] | Model for the correct allocation of commodities in order to maximize profit |
Hu et al. [56] | Model for a traceability system usable in high probability of contamination scenarios and algorithm to determine contamination |
Wang & Li [57] | Fixed expiration dates are inefficient to expose variations subjected to products; Algorithm to apply discount according to quality variation to keep demand |
Grunow & Piramuthu [58] | Fixed expiration dates as inefficient means to assess product quality and models to determine quality using RFID and profit analysis |
Piramuthu et al. [59] | Traceability systems as tools to increase recall efficiency and model to determine economic loss reduction due to the use of those systems |
Hertog et al. [60] | Algorithm to evaluate quality decay and to distribute perishables based in FEFO |
Authors | Important concepts |
Sloof et al. [61] | Quality modeling through variation of inherent properties and the value that consumers attribute them |
Bechini et al. [62] | Simple architecture for traceability systems |
Kelepouris et al. [63] | Model for agricultural traceability system based on RFID and EPC |
Bechini et al. [64] | Model for information sharing between stakeholders in a supply chain based on XML |
van der Vorst et al. [65] | Comparison of LSFO versus FIFO in a supply chain, use of max., min., and avg. values to determine the quality uncertainty |
Zhou et al. [66] | Review on information sharing between sellers and buyers |
Olsen & Aschan [67] | Benefits of traceability systems and methodology for modeling food supply chains |
Thakur et al. [68] | Framework for traceability using EPCIS and RFID |
Karlsen et al. [69] | Discussion on granularity and its effect on traceability |
Bakker et al. [70] | Necessity of inventory management as a part of traceability systems to monitor heterogeneous quality decay |
Verdouw et al. [71] | Method to virtualize operations based on the IoT perspective |
Pahl & Voß [72] | Algorithms to determine deterioration of perishable food |
Jedermann et al. [73] | FIFO versus FEFO and LSFO |
Badia-Melis et al.[74] | Review on trends and necessities of traceability systems, concept of CTE; FTTO and the TraceFood, FIFO vs FEFO and FCM to determine mixing |
Qian et al. [75] | Methodology to determine optimal granularity |
Óskarsdóttir & Oddsson [13] | Methodology to select the most appropriate technology to incorporate in a traceability system |
Authors | Important concepts |
Kwok et al. [76] | System model and software for wireless sensor-based product authentication |
Woo et al. [77] | Model for sensor-based traceability system using the ER model adding the temporal dimension |
Thakur & Hurburgh [78] | Methods to elaborate internal and external traceability models |
Saak [79] | Increase in product value due to information provided by traceability systems |
Gaukler et al. [80] | Benefits of dynamic expiration dates per opposition to fixed expiration dates |
Authors | Products | Granularity | Important concepts |
Beulens et al. [14] | Eggs | Undisclosed | Shared quality standards, shared information infrastructure, prototype traceability system in a SME supply chain |
Bollen et al. [15] | Apples | Output packages linked to input bins | Mixing causes traceability information loss, model to determine and minimize mixing |
Skoglund & Dejmek [16] | Milk | Output packages linked to input silos | Fuzzy traceability, batch virtualization, mixing algorithm |
Frosch et al. [17] | Fish | Output lots liked to fishing vessels | Measures to improve a manual traceability system scenario |
Wang et al. [18] | Undisclosed | Containers | Traceability as a tool to improve distribution and minimize capital loss and waste |
Li et al. [19] | Cucumbers | Terrain lot | Traceability as tool to aid production and comply with regulations |
Thakur et al. [20] | Grain | Shipment to customer | Implementation of traceability in a heavy mixing scenario, quality evaluation |
Karlsen et al. [21] | Fish | Several tested | Impact of granularity in usefulness and cost of a traceability system |
Borit & Olsen [22] | Fish | Dependent on the records of activity | Traceability as a tool to enforce regulations and quality |
Huang et al. [23] | Red jujubes | Final product batch | Consumer access to traceability information, traceability system composed by several different subsystems |
Pizzuti et al. [24] | Frozen vegetables | Dependent of the company | Model for frozen vegetables, supply chain traceability |
Lavelli [25] | Poultry meat | Final product lot | Fuzzy traceability as a tool to comply with regulations |
Hu et al. [26] | Vegetables | Variable, depend on stakeholder | Supply chain traceability |
Trebar et al. [27] | Fish | Box | Supply chain traceability based on wireless sensors |
Parreño-Marchante et al. [28] | Fish | Box | Application of a traceability system in two SME's |
Liu et al. [29] | Eggs | Dependent on the stakeholder | Real time traceability system in a Chinese egg supply chain |
Wang et al. [30] | Peach | Undisclosed | Sensor based supply chain traceability system |
Authors | Important concepts |
Jansen-Vullers et al. [31] | Elements and requirements of traceability systems |
Regattieri et al. [32] | Pillars of traceability systems, consequences of inadequate information exposition, benefits and requirements of efficient traceability systems |
Gessner et al. [33] | Advantages of using IT technology to record information and necessity of traceability systems to avoid alimentary crisis |
Jedermann & Lang [34] | Necessity of quality monitoring traceability systems due to the subjection of products to greater variations than expected |
Donnelly et al. [35] | Necessity of recording information about transformations applied to products |
Chrysochou et al. [36] | Consumers' need for information and impact of that information |
Bosona & Gebresenbet [37] | Increase in supply chain logistic efficiency, main driving forces behind the development of traceability systems, advantages, and obstacles |
Storøy et al. [38] | General principles of traceability systems, review on the state of information exchange and necessity of safety guarantees for information exchange |
Aung & Chang [39] | Necessity of traceability systems due to the impact of food crisis, characterization of traceability systems and benefits of application |
Asioli et al. [40] | Review on the factors that led Italian wine companies to implement traceability systems and cost benefit description |
Dabbene et al. [41] | Causes and consequences of recalls, traceability systems proposed as solution, performance indicators of those systems and levels of regulation |
Aiello et al. [42] | Benefits and obstacles of RFID based traceability systems and model to assess optimal granularity |
Germani et al. [43] | Monitoring elements that have an impact in sustainability can lead to opportunities to process optimization |
Thakur & Forås [44] | Demonstration of variations subjected to products |
Hsiao & Huang [45] | Need for traceability systems to increase transparency in information exchange |
Alonso-Rorís et al. [46] | Necessity for low-cost and adaptable traceability systems |
Dandage et al. [47] | Traceability systems as tools to avoid waste, fraud and insecurity |
Raak et al. [48] | Causes of waste and traceability systems as tools to avoid it |
Olsen & Borit [49] | Essential components of traceability systems and useful questions for performance evaluation |
Matzembacher et al. [50] | Corporate inability to provide useful and timely data for the resolution of food crisis, consumers' willingness to pay for information, advantages, and obstacles of food traceability systems |
Ndraha et al. [51] | Traceability systems as tools to prevent temperature abuse in food supply chains |
Stranieri et al. [52] | Factors leading to the adoption of traceability systems and corporate necessities |
Óskarsdóttir & Oddsson [13] | Necessity of traceability systems to monitor quality and technology capable of being incorporated on a traceability system |
Authors | Important concepts |
Hsu et al. [53] | Algorithm for distribution of perishables based on their deliverance at the highest possible quality |
Heese [54] | Inventory management using wireless sensors |
Xiaofeng et al. [55] | Model for the correct allocation of commodities in order to maximize profit |
Hu et al. [56] | Model for a traceability system usable in high probability of contamination scenarios and algorithm to determine contamination |
Wang & Li [57] | Fixed expiration dates are inefficient to expose variations subjected to products; Algorithm to apply discount according to quality variation to keep demand |
Grunow & Piramuthu [58] | Fixed expiration dates as inefficient means to assess product quality and models to determine quality using RFID and profit analysis |
Piramuthu et al. [59] | Traceability systems as tools to increase recall efficiency and model to determine economic loss reduction due to the use of those systems |
Hertog et al. [60] | Algorithm to evaluate quality decay and to distribute perishables based in FEFO |
Authors | Important concepts |
Sloof et al. [61] | Quality modeling through variation of inherent properties and the value that consumers attribute them |
Bechini et al. [62] | Simple architecture for traceability systems |
Kelepouris et al. [63] | Model for agricultural traceability system based on RFID and EPC |
Bechini et al. [64] | Model for information sharing between stakeholders in a supply chain based on XML |
van der Vorst et al. [65] | Comparison of LSFO versus FIFO in a supply chain, use of max., min., and avg. values to determine the quality uncertainty |
Zhou et al. [66] | Review on information sharing between sellers and buyers |
Olsen & Aschan [67] | Benefits of traceability systems and methodology for modeling food supply chains |
Thakur et al. [68] | Framework for traceability using EPCIS and RFID |
Karlsen et al. [69] | Discussion on granularity and its effect on traceability |
Bakker et al. [70] | Necessity of inventory management as a part of traceability systems to monitor heterogeneous quality decay |
Verdouw et al. [71] | Method to virtualize operations based on the IoT perspective |
Pahl & Voß [72] | Algorithms to determine deterioration of perishable food |
Jedermann et al. [73] | FIFO versus FEFO and LSFO |
Badia-Melis et al.[74] | Review on trends and necessities of traceability systems, concept of CTE; FTTO and the TraceFood, FIFO vs FEFO and FCM to determine mixing |
Qian et al. [75] | Methodology to determine optimal granularity |
Óskarsdóttir & Oddsson [13] | Methodology to select the most appropriate technology to incorporate in a traceability system |
Authors | Important concepts |
Kwok et al. [76] | System model and software for wireless sensor-based product authentication |
Woo et al. [77] | Model for sensor-based traceability system using the ER model adding the temporal dimension |
Thakur & Hurburgh [78] | Methods to elaborate internal and external traceability models |
Saak [79] | Increase in product value due to information provided by traceability systems |
Gaukler et al. [80] | Benefits of dynamic expiration dates per opposition to fixed expiration dates |