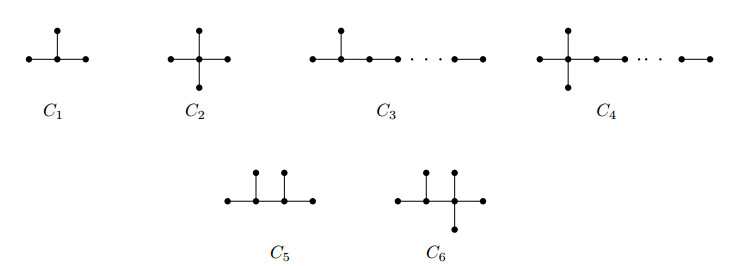
This study evaluates the logistics cost associated with transporting Wood Pellets (WP) and Torrefied Biomass Pellets (TBP) from Aveiro, Portugal's principal WP exporting port, to Northern European destinations. With increasing emphasis on sustainable energy, understanding the cost dynamics between WP and TBP becomes crucial for market competitiveness. Using data sourced from the Argus Biomass Markets report, we compared the energy in gigajoules per ton of both WP and TBP. Torrefaction results in pellets with superior energy and bulk densities, influencing their transportation logistics costs. The main metrics for comparison were cost per energy unit and the implications of energy and bulk densities on transport costs. Preliminary findings indicate that although torrefied pellets undergo more significant mass loss than energy loss, their enhanced energy and bulk densities present logistical advantages. These advantages manifest as more tons per volume unit and heightened energy per ton, which ultimately lead to reduced transportation cost per energy unit. The insights from this analysis provide valuable input for the biofuel sector. By understanding the cost benefits associated with TBP transportation in contrast to WP, stakeholders can make strategic decisions, bolstering the competitiveness of Portuguese biofuel products in the European domain.
Citation: Leonel J. R. Nunes. Potential exportation of wood pellets and torrefied biomass pellets logistics cost analysis: A comparative case study from Portugal[J]. AIMS Energy, 2024, 12(1): 45-61. doi: 10.3934/energy.2024003
[1] | Na Pang . Nonlinear neural networks adaptive control for a class of fractional-order tuberculosis model. Mathematical Biosciences and Engineering, 2023, 20(6): 10464-10478. doi: 10.3934/mbe.2023461 |
[2] | Shanjing Ren . Global stability in a tuberculosis model of imperfect treatment with age-dependent latency and relapse. Mathematical Biosciences and Engineering, 2017, 14(5&6): 1337-1360. doi: 10.3934/mbe.2017069 |
[3] | Georgi Kapitanov . A double age-structured model of the co-infection of tuberculosis and HIV. Mathematical Biosciences and Engineering, 2015, 12(1): 23-40. doi: 10.3934/mbe.2015.12.23 |
[4] | Silvia Martorano Raimundo, Hyun Mo Yang, Ezio Venturino . Theoretical assessment of the relative incidences of sensitive andresistant tuberculosis epidemic in presence of drug treatment. Mathematical Biosciences and Engineering, 2014, 11(4): 971-993. doi: 10.3934/mbe.2014.11.971 |
[5] | Abba B. Gumel, Baojun Song . Existence of multiple-stable equilibria for a multi-drug-resistant model of mycobacterium tuberculosis. Mathematical Biosciences and Engineering, 2008, 5(3): 437-455. doi: 10.3934/mbe.2008.5.437 |
[6] | C. Connell McCluskey . Global stability for an SEI epidemiological model with continuous age-structure in the exposed and infectious classes. Mathematical Biosciences and Engineering, 2012, 9(4): 819-841. doi: 10.3934/mbe.2012.9.819 |
[7] | Tao-Li Kang, Hai-Feng Huo, Hong Xiang . Dynamics and optimal control of tuberculosis model with the combined effects of vaccination, treatment and contaminated environments. Mathematical Biosciences and Engineering, 2024, 21(4): 5308-5334. doi: 10.3934/mbe.2024234 |
[8] | Juan Pablo Aparicio, Carlos Castillo-Chávez . Mathematical modelling of tuberculosis epidemics. Mathematical Biosciences and Engineering, 2009, 6(2): 209-237. doi: 10.3934/mbe.2009.6.209 |
[9] | Xi-Chao Duan, Xue-Zhi Li, Maia Martcheva . Dynamics of an age-structured heroin transmission model with vaccination and treatment. Mathematical Biosciences and Engineering, 2019, 16(1): 397-420. doi: 10.3934/mbe.2019019 |
[10] | Surabhi Pandey, Ezio Venturino . A TB model: Is disease eradication possible in India?. Mathematical Biosciences and Engineering, 2018, 15(1): 233-254. doi: 10.3934/mbe.2018010 |
This study evaluates the logistics cost associated with transporting Wood Pellets (WP) and Torrefied Biomass Pellets (TBP) from Aveiro, Portugal's principal WP exporting port, to Northern European destinations. With increasing emphasis on sustainable energy, understanding the cost dynamics between WP and TBP becomes crucial for market competitiveness. Using data sourced from the Argus Biomass Markets report, we compared the energy in gigajoules per ton of both WP and TBP. Torrefaction results in pellets with superior energy and bulk densities, influencing their transportation logistics costs. The main metrics for comparison were cost per energy unit and the implications of energy and bulk densities on transport costs. Preliminary findings indicate that although torrefied pellets undergo more significant mass loss than energy loss, their enhanced energy and bulk densities present logistical advantages. These advantages manifest as more tons per volume unit and heightened energy per ton, which ultimately lead to reduced transportation cost per energy unit. The insights from this analysis provide valuable input for the biofuel sector. By understanding the cost benefits associated with TBP transportation in contrast to WP, stakeholders can make strategic decisions, bolstering the competitiveness of Portuguese biofuel products in the European domain.
The graphs considered throughout this paper are finite and connected. The graph-theoretical terminology and notation that are used in this study without explaining here can be found in the books [1,2].
A graph invariant is a function f defined on the set of all graphs with the condition that f(G1)=f(G2) whenever G1 and G2 are isomorphic. The real-valued graph invariants are commonly known as topological indices in mathematical chemistry, particularly in chemical graph theory [20].
The Sombor index and the reduced Sombor index abbreviated as SO and SOred, respectively, are the topological indices introduced recently by mathematical chemist Ivan Gutman in his seminal paper [9]. The Sombor index SO has attained attention from many scientific groups all over the world in a very short time, which resulted in many publications; for example, see the review papers [8,15] and associated papers listed therein. The chemical applicability of the indices SO and SOred is also well documented. Redžepović [17] examined the discriminating and predictive ability of the indices SO and SOred on a large class of isomers and found that both of these indices have good discriminating and predictive potential. Deng et al. [7] compared the predictive ability of SO on octane isomers with that of similar kind of existing topological indices and showed that SO has a higher accuracy in predicting physico-chemical properties of the the aforementioned chemical compounds; Liu et al. [13] conducted a similar comparative study for SOred and concluded that SOred outperforms in several cases. Also, it was demonstrated in [14] that boiling points of benzenoid hydrocarbons are highly correlated with SO and SOred. By considering these chemical applications of SO and SOred, it make sense to study further these indices, particularly for molecular graphs (these are graphs of maximum degree at most 4).
In chemical graph theory, molecular trees play an important role because a certain class of chemical compounds can be viewed by using the concept of molecular trees. Thereby, in the present paper, we study the topological indices SO and SOred for molecular trees under certain constraints. Deng et al. [7] determined the trees possessing the maximum and minimum values of SO and SOred among all molecular trees of a given order; see also [5,18] where the same problem regarding SO was solved independently. Let us consider the following problem.
Problem 1. Characterize the trees possessing the maximum and minimum values of SO and SOred among all molecular trees of a given order and with a fixed number of (i) branching vertices (ii) vertices of degree 2.
The minimal part of Problem 1 concerning SO has already been solved in [3] where several other interesting extremal problems were also resolved. The main objective of this study is to give a solution to the maximal part of Problem 1. Detail about the mathematical study of the Sombor index for general trees can be found in [5,6,10,12,19,21,22].
Let V(G) and E(G) denote the set of vertices and edges, respectively, in the graph G. For the vertex v∈V(G), the degree of v is denoted by dG(v) (or simply by dv if only one graph is under consideration). A vertex u∈V(G) is said to be a pendent vertex or a branching vertex if du=1 or du≥3, respectively. The set NG(u) consists of the vertices of the graph G that are adjacent to the vertex u. Let ni(G) denotes the count of vertices having degree i in the graph G. Denote by xi,j(G) the cardinality of the set consisting of the edges connecting the vertex of degree i with the vertex of degree j in the graph G. A graph of order n is also known as an n-vertex graph.
For a graph G, the Sombor index and reduced Sombor index abbreviated as SO and SOred, respectively, are defined [9] as
SO(G)=∑uv∈E(G)√d2u+d2vandSOred(G)=∑uv∈E(G)√(du−1)2+(dv−1)2. |
We start this section with the following elementary result, noted in [16].
Lemma 1. The function f defined as
f(x,y)=√x2+y2−√(x−c)2+y2, |
with 1≤c<x and y>0, is strictly decreasing in y and strictly increasing in x.
For r≥3, each of the vertices u2,u3,⋯,ur−1 of the path P:u1u2⋯ur in a graph is called internal vertex of P. Denote by Pi,j(C) (or simply Pi,j) the path from a branching vertex of degree i to a branching vertex of degree j in a molecular tree C such that all the internal vertices (if exist) of Pi,j have degree 2.
Lemma 2. If the molecular tree C contains a path P4,4:v1v2⋯vs and an edge uw such that du=1 and dw=3 with the condition that v1 lies on the w−vs path, then for the molecular tree C′ obtained from C by deleting the edges v1v2, uw and adding new edges v2w, v1u, the inequalities SO(C)<SO(C′) and SOred(C)<SOred(C′) hold, where C and C′ have the same degree sequence.
Proof. Clearly, the trees C and C′ have the same degree sequence. Also, we note that
SO(C)=SO(C′)+√10−√17+√4+d2v2−√9+d2v2<SO(C′) |
and
SOred(C)=SOred(C′)+2−3+√9+(dv2−1)2−√4+(dv2−1)2<SO(C′). |
Lemma 3. For a molecular tree C, if x1,3(C)>0 such that C contains the paths P3,4:u1u2⋯ut and P′4,3:utut+1⋯us−1us, where t≥2, s≥3, and t<s, then a molecular tree C′ can be obtained with x1,3(C′)<x1,3(C) such that SO(C)<SO(C′) and SOred(C)<SOred(C′), where C and C′ have the same degree sequence.
Proof. Suppose that uv∈E(C) such that du=1 and dv=3. We prove the result by considering two possible cases.
Case I. s≤4.
Note that one of the paths P4,3 and P′4,3 contains exactly one internal vertex and the other contains no internal vertex. Thus, without loss of generality it can be assumed that t=2. If s=3, then we take C′=C−{uv,u1u2,u2u3}+{u1u3,uu2,u2v}, and for s=4, we take C′=C−{u1u2,u3u4,uv}+{u1u4,uu2,u3v}. In either case, we note that both C and C′ have the same degree sequence, x1,3(C′)<x1,3(C), and
SO(C)=SO(C′)+5+√10−3√2−√17<SO(C′) |
SOred(C)=SOred(C′)+√13−1−2√2<SOred(C′), |
as required.
Case II. s>4.
If t=2 or t=s−1, the result is proved in a fully analogous way as in Case I. In what follows, suppose that 2<t<s−2. When s=5 then (t=3 and) we take C′=C−{u2u3,u4u5,uv}+{u2u5,u3u,u4v}, and otherwise (that is, if s≥6 then) we take C′=C−{u2u3,ut−1ut,us−1us,uv}+{u2us,uut,us−1u3,ut−1v}. In either case, we observe that both C and C′ have the same degree sequence, x1,3(C′)<x1,3(C), and
SO(C)=SO(C′)+√10+2√5−√13−√17<SO(C′), |
SOred(C)=SOred(C′)+√10−1−√5<SOred(C′), |
as desired.
Lemma 4. Let C be a molecular tree with xy,uv,wz∈E(C), where the vertices x, y, u, v, w, z are chosen in such a way that du=1, dx=3=dy, dv=dw=dz=4, and w lies on one of the three paths v−z, x−z, y−z paths, and that x1,3(C)=0. If NC(z)={w,z1,z2,z3} and C′=C−{xy,z1z,z2z,z3z,uv}+{xu,uy,z1u,z2u,z3v} then SO(C)<SO(C′) and SOred(C)<SOred(C′), where C and C′ have the same degree sequence.
Proof. It can be easily observed that C and C′ have the same degree sequence. Also, after elementary calculations, we arrive at SO(C)=SO(C′)+7√2−10<SO(C′) and SOred(C)=SOred(C′)+5√2−2√13<0.
Lemma 5. Let C be a molecular tree with uv,z′w,wz∈E(C), where the vertices u,v,w,z,z′∈V(C) are chosen in such a way that dw=2 and min{du,dv,dz,dz′}≥3 provided that du+dv>dz+dz′. If C′=C−{uv,z′w,wz}+{z′z,uw,wv}, then SO(C)<SO(C′) and SOred(C)<SOred(C′), where C and C′ have the same degree sequence.
Proof. We observe that both the trees C and C′ have the same degree sequence and
SO(C)=SO(C′)+√d2u+d2v+√4+d2z′+√4+d2z−√4+d2v−√4+d2u−√d2z+d2z′=SO(C′)+I1 |
and
SOred(C)=SOred(C′)+√(du−1)2+(dv−1)2+√1+(dz′−1)2+√1+(dz−1)2−√1+(du−1)2−√1+(dv−1)2−√(dz−1)2+(dz′−1)2=SOred(C′)+I2, |
where
I1=√d2u+d2v+√4+d2z′+√4+d2z−√4+d2v−√4+d2u−√d2z+d2z′ |
and
I2=√(du−1)2+(dv−1)2+√1+(dz′−1)2+√1+(dz−1)2−√1+(du−1)2 −√1+(dv−1)2−√(dz−1)2+(dz′−1)2. |
To complete the proof, it is enough to show that I1<0 and I2<0. Recall that du+dv∈{7,8} and hence we consider two cases accordingly.
ⅰ) If du+dv=8 then du=4=dv and hence dz+dz′∈{6,7}, and therefore we get I1<0 and I2<0
ⅱ) If du+dv=7 then du=3 and dv=4 (or du=4 and dv=3) and hence dz=3=dz′ and thence we have I1<0 and I2<0.
Lemma 6. Let C be a molecular tree with uv,vw,xy∈E(C), where the vertices u,v,w,x,y are chosen in such a way that du=2=dv, dw≥2, and min{dx,dy}≥3. If C′=C−{uv,vw,xy}+{uw,xv,vy} then SO(C)<SO(C′) and SOred(C)<SOred(C′), where C and C′ have the same degree sequence.
Proof. Clearly, the degree sequences of C and C′ is the same. Since dx,dy∈{3,4}, we have
SO(C)=SO(C′)+2√2+√d2x+d2y−√4+d2x−√4+d2y<SO(C′) |
and
SOred(C)=SOred(C′)+√2+√(dx−1)2+(dy−1)2 −√1+(dx−1)2−√1+(dy−1)2<SOred(C′). |
For n≥4, denote by Cn,nb the collection of all n-vertex molecular trees with nb branching vertices, where nb≤12(n−2). As the path Pn is the unique graph in Cn,0, where SO(Pn)=2√2(n−3)+2√5 and SOred(Pn)=√2(n−3)+2, and C1 (depicted in Figure 1) is the unique graph in C4,1 (whose (reduced) Sombor index value is given in Table 1), in rest of the investigation we assume that n>4 and nb≥1. We also define the sub-classes Cp and C∗q of Cn,nb as follows:
Cp={C∈Cn,nb:n2(C)=0,n3(C)≥0}, | (4.1) |
C∗q={C∈Cn,nb:n3(C)=0,n2(C)≥0}. | (4.2) |
SO(Ci) | SOred(Ci) | |
C1 | 3√10 | 6 |
C2 | 4√17 | 12 |
C3 | 2√2(n−5)+2√10+√13+√5 | √2(n−5)+5+√5 |
C4 | 2√2(n−6)+3(√17+√5) | √2(n−6)+10+√10 |
C5 | 4√10+3√2 | 2√2+8 |
C6 | 2√10+3√17+5 | √13+13 |
Lemma 7. If Cb is a molecular tree with the maximum Sombor index (respectively, reduced Sombor index) over the class Cn,nb, then either Cb∈Cp or Cb∈C∗q.
Proof. Contrarily, assume that Cb∈Cn,nb∖(Cp∪C∗q). There must be vertices u and v in Cb with du=3 and dv=2. Let Nu(Cb)={u1,u2,u3} and Nv(Cb)={v1,v2}, where v2 and u3 lie on the u−v path. If uv∈E(C) then we take v2=u and u3=v, and also it possible that u3=v2. If C′ is the tree deduced from C by dropping the edges uu1, uu2 and adding two new edges vu1, vu2 in C, then C′∈Cn,nb and (by keeping in mind Lemma 1, we have)
SO(Cb)=SO(C′)+3∑i=1√9+d2ui+2∑j=1√4+d2vj−√1+d2u3−2∑i=1√16+d2ui−2∑j=1√16+d2vj<SO(C′)+√9+d2u3−√1+d2u3+2∑j=1(√4+d2vj−√16+d2vj)≤SO(C′)+2∑j=1(√4+d2vj−√16+d2vj)+√13−√5≤SO(C′)+3√5+√13−8√2<SO(C′), |
which is contradicting our assumption concerning the choice of Cb.
Similarly, we have
SOred(Cb)=SOred(C′)+3∑i=1√4+(dui−1)2+2∑j=1√1+(dvj−1)2−√(du3−1)2−2∑i=1√9+(dui−1)2−2∑j=1√9+(dvj−1)2<SOred(C′)+√4+(du3−1)2−√(du3−1)2+2∑j=1√1+(dvj−1)2−2∑j=1√9+(dvj−1)2≤SOred(C′)+2∑j=1√1+(dvj−1)2−2∑j=1√9+(dvj−1)2+√5−1≤SOred(C′)+√5+2√10−6√2−1<SOred(C′), |
a contradiction.
Lemma 8. For nb>1, if Cb is the tree with the maximum Sombor index (respectively reduced Sombor index) in the class Cn,nb, then x1,2(Cb)=0.
Proof. Contrariwise, assume that there is a path P:v1v2⋯vt in Cb, where t≥3 such that dv1=1, dvt>2 and dvj=2 for all 2≤j≤t−1. Since n2(Cb)≥1, by Lemma 7 we must have dvt=4. Also, at least one of the neighbors of vt different from vt−1 is non-pendent because nb>1. Take w∈NCb(vt)∖{vt−1} such that dw≥2. As n3(Cb)=0 by Lemma 7, we have dw∈{2,4}. If C′=Cb−{v1v2,vt−1v1,uw}+{v1vt,uv2,vt−1w}, then we have C′∈Cn,nb and
SO(Cb)=SO(C′)+√5−√17+√16+d2w−√4+d2w<SO(C′), |
and
SOred(Cb)=SOred(C′)+1−3+√9+(dw−1)2−√1+(dw−1)2<SOred(C′). |
a contradiction.
For a non-trivial molecular tree C of order n, the following identities hold:
n=n1(C)+n2(C)+n3(C)+n4(C), | (4.3) |
n1(C)+2n2(C)+3n3(C)+4n4(C)=2(n−1), | (4.4) |
nb=n3(C)+n4(C). | (4.5) |
The results in the following lemma directly follows from Eqs (4.3)–(4.5).
Lemma 9. For a molecular tree C∈Cn,nb, the following statements hold:
(i) If C∈Cp, then n1(C)=n−nb, n3(C)=3nb−n+2 and n4(C)=n−2nb−2.
(ii) If C∈C∗q, then n1(C)=2nb+2, n2(C)=n−3nb−2 and n4(C)=nb.
(iii) C∈Cp∩C∗q if and only if nb=n−23.
Lemma 10. For a molecular tree C with the maximum Sombor index (respectively reduced Sombor index) over the class Cn,nb, n2(C)≥1 if and only if 0≤nb<n−23 or n≥3nb+3.
Proof. If n2(C)≥1, then n3(C)=0 by Lemma 7 and hence C∈C∗q; now, by using the result n2(C)=n−3nb−2 of Lemma 9 it is deduced that nb<n−23 or n≥3nb+3.
Conversely, suppose that 0≤nb<n−23 or n≥3nb+3 with nb≥0. Contrarily, assume that n2(C)=0. From Eqs (4.3)–(4.5), it follows that 2nb+n4(C)=n−2, which together with the assumption n≥3nb+3 implies that n4(C)≥nb+1, which is a contradiction.
Note that C2 and C3 with n=5 (see Figure 1) are the only molecular trees in C5,1, and it can be easily observed that SO(C2)>SO(C3) (respectively SOred(C2)>SOred(C3)); see Table 1. For n≥5, we define the the following sub-classes of Cn,nb:
B0={C∈C∗q: nb=1 and x1,2(C)=1},
B1={C∈C∗q: 1<nb<n−14 and x1,2(C)=0=x4,4(C)},
B2={C∈C∗q: n−14≤nb<n−23 and x1,2(C)=0=x2,2(C)},
B3={C∈Cp: n−23<nb≤3n−78 and x1,3(C)=0=x3,3(C)},
B4={C∈Cp: 3n−78<nb≤2n−65 and x1,3(C)=0=x4,4(C) and x3,3≠0},
B5={C∈Cp: 2n−65<nb≤n−22 and x4,4=0 and x3,3=n3(C)−1},
where Cp and C∗q are defined in (4.1) and (4.2). For a molecular tree C, we have
∑1≤j≤4;j≠ixi,j(C)+2xi,i(C)=i⋅niwherei=1,2,3,4. | (4.6) |
Theorem 1. If n≥6 and C∈Cn,1, then
i) SO(C)≤2√2(n−6)+3√5+3√17,
ii) SOred(C)≤√2(n−6)+10+√10.
The equalities occur if and only if C≅B0.
Proof. Let n>5 and C1∈Cn,1 be a molecular tree with the maximum Sombor index (respectively reduced Sombor index). Let v be the unique branching vertex of C1.
Claim 1. dv=4.
Contrariwise, suppose that dv=3. The constraint n>5 ensures that there is a vertex u of degree 2 in C1 which is adjacent to a pendent vertex, say w. Let C′ be the new tree obtained from C1 by deleting the edge uw and adding the new edge vw. Certainly, we have C′∈Cn,1.
Note that
SO(C1)=SO(C′)+∑z∈NC1(v)√9+d2z+ξ−∑z∈NC1(v)√16+d2z−√17<SO(C′), |
and
SOred(C1)=SOred(C′)+∑z∈NC1(v)√4+(dz−1)2+η−∑z∈NC1(v)√9+(dz−1)2−3.<SOred(C′), |
which leads to the contradiction to our assumption concerning C1, where
ξ={√5 if uv∈V(C1),√8 if uv∉V(C1),andη={1 if uv∈V(C1),√2 if uv∉V(C1). |
Claim 2. The vertex v has exactly one non pendent neighbor.
Since n≥6, the vertex v has at least one non pendent neighbor. Contrarily assume that P1:v1v2⋯vrv and P2:w1w2⋯wsv are two paths in C1 with dv1=1=dw1 and dvi=2=dwj for 2≤i≤r and 2≤j≤s. If C′=C1−{v2v1,vrv}+{v1v,vrw1}, then we have C′∈Cn,1 and
SO(C1)=SO(C′)+√4+d2v−√1+d2v+√5−√8<SO(C′), |
and
SOred(C1)=SOred(C′)+√1+(dv−1)2−√(dv−1)2+1−√2<SOred(C′), |
a contradiction (where dv=4 by Claim 1).
Now, the desired result follows from Claims 1 and 2.
Theorem 2. If C∈Cn,nb and 1<nb<n−14, then
(i) SO(C)≤2√2(n−1)+2√17(nb+1)+4√5(nb−1)−8√2nb,
(ii) SOred(C)≤√2(n−4nb−1)+2√10(nb−1)+6(nb+1),
and the equalities occur if and only if C≅B1.
Proof. Denote by Cb the molecular tree with the maximum Sombor index (respectively reduced Sombor index) in the class Cn,nb, for 1<nb<n−14. Since nb<n−14<n−23, Lemma 10 ensures that n2(Cb)>0, which together with Lemma 7 implies that Cb∈C∗q, and hence by Lemma 9(b) one has n1(Cb)=2nb+2, n2(Cb)=n−3nb−2 and n4(Cb)=nb. Because of the constraint nb>1, Lemma 8 guaranties that
x1,2(Cb)=0, | (4.7) |
plugging it into (4.6) for i=1, we get
x1,4(Cb)=n1(Cb)=2nb+2. | (4.8) |
Since nb<n−14 or 4nb<n−1 which gives n4(Cb)−1=nb−1<n−3nb−2=n2(Cb) and therefore
n4(Cb)≤n2(Cb). | (4.9) |
We claim that x2,2(Cb)≠0. Contrarily, assume that x2,2(Cb)=0. Then, (4.6) with i=2 gives
x2,4(Cb)=2n2(Cb). | (4.10) |
Equations (4.3) and (4.4) implies that
n1(Cb)−2n4(Cb)=2 | (4.11) |
Also, (4.6) with i=4 yields
2x4,4(Cb)=4n4(Cb)−x1,4(Cb)−x2,4(Cb) | (4.12) |
Using (4.8)–(4.11) in (4.12), we have
2x4,4(Cb)=4n4(Cb)−n1(Cb)−2n2(Cb)≤4n4(Cb)−n1(Cb)−2n4(Cb)=−2, |
a contradiction. Hence, the claim x2,2(Cb)≠0 is true.
We also claim that
x4,4(Cb)=0. | (4.13) |
Suppose to the contrary that x4,4(Cb)≠0. Take xy∈E(Cb) such that dx=dy=4. Since x2,2(Cb)≠0, take uv,vw∈E(Cb) such that du=dv=2 and dw≥2. If C′ is the tree obtained by applying the transformation mentioned in the statement of Lemma 6, then Lemma 6 guaranties that SO(Cb)<SO(C′) and SOred(Cb)<SOred(C′), which is a contradiction to the definition of Cb. Therefore, x4,4(Cb)=0.
Now, by using Eqs (4.6)–(4.8) and (4.13), we get x2,4(Cb)=2nb−2 and x2,2(Cb)=n−4nb−1. Hence, SO(Cb)=2√2(n−1)+2√17(nb+1)+4√5(nb−1)−8√2nb and SOred(Cb)=√2(n−4nb−1)+2√10(nb−1)+6(nb+1), which completes the proof.
Theorem 3. If C∈Cn,nb such that n−14≤nb<n−23, then
i) SO(C)≤4√5(n−3nb−2)−4√2(n−4nb−1)+2√17(nb+1),
ii) SOred(C)≤2√10(n−3nb−2)−3√2(n−4nb−1)+6(nb+1),
and the equalities occur if and only if C≅B2.
Proof. Denote by Cb the molecular tree with the maximum Sombor index (respectively reduced Sombor index) from the class Cn,nb for n−14≤nb<n−23. By Lemma 10, the inequality n2(Cb)>0 holds for nb<n−23 and ultimately we have Cb∈C∗q or n3(Cb)=0 because of Lemma 7. The equations n1(Cb)=2nb+2, n2(Cb)=n−3nb−2 and n4(Cb)=nb follow from (b) part of Lemma 9, and (4.7) and (4.8) hold by Lemma 8. Also, the inequality n2(Cb)≤n4(Cb)−1 is obtained from n−14≤nb. By using the method used in the proof of Theorem 2, we get x2,2(Cb)=0, x2,4(Cb)=2n2(Cb)=2n−6nb−4 and x4,4(Cb)=nb−1−n2(Cb)=4nb−n+1. Hence, Cb≅B2 or SO(Cb)=4√5(n−3nb−2)−4√2(n−4nb−1)+2√17(nb+1) and SOred(Cb)=2√10(n−3nb−2)−3√2(n−4nb−1)+6(nb+1), which completes the proof.
Theorem 4. Let C∈Cn,nb be the molecular tree such that nb=n−23, then
i) SO(C)=2√173(n+1)+4√23(n−5),
ii) SOred(C)=2(n+1)+√2(n−5).
Proof. The part (c) of Lemma 9 ensures that C∈Cp∩C∗q, which implies that n3(C)=0=n2(C). Thus, x1,4(C)=n−nb=23(n+1) and x4,4(C)=nb−1=13(n−5).
Theorem 5. If C∈Cn,nb such that n−23<nb≤3n−78, then
i) SO(C)≤√17(n−nb)+5(9nb−3n+6)+4√2(3n−8nb−7),
ii) SOred(C)≤3(n−nb)+√13(9nb−3n+6)+3√2(3n−8nb−7),
and the equalities occur if and only if C≅B3.
Proof. Denote by Cb the molecular tree with the maximum Sombor index (respectively reduced Sombor index) in the class Cn,nb, for n−23<nb≤3n−78. By Lemma 10, we have n2(Cb)=0 (as n−23<nb), which implies that Cb∈Cp. Also, Lemma 9(a) guaranties that n1(Cb)=n−nb, n3(Cb)=3nb−n+2 and n4(Cb)=n−2nb−2. Now, the inequality nb≤3n−78 can be written as 6nb−2n+5<n−2nb−2, which leads us to the fact that 2n3(Cb)+1≤n4(Cb). Using Lemmas 2–4 and keeping in mind the fact n4(Cb)≥2n3(Cb)+1, we have
x1,3(Cb)=0 | (4.14) |
and
x1,4(Cb)=n−nb. | (4.15) |
Now, using Lemmas 2–4 and Eqs (4.6), (4.14) and (4.15), we have x3,3(Cb)=0, x3,4(Cb)=3n3(Cb)=9nb−3n+6, x4,4(Cb)=n4(Cb)−2n3(Cb)−1=3n−8nb−7. Hence, SO(Cb)=√17(n−nb)+5(9nb−3n+6)+4√2(3n−8nb−7), and SOred(Cb)=3(n−nb)+√13(9nb−3n+6)+3√2(3n−8nb−7). This completes the proof.
Theorem 6. If C∈Cn,nb such that 3n−78<nb≤2n−65, then
i) SO(C)≤√17(n−nb)+3√2(8nb−3n+7)+5(3n−7nb−8),
ii) SOred(C)≤3(n−nb)+2√2(8nb−3n+7)+√13(3n−7nb−8),
and the equalities occur if and only if C≅B4.
Proof. Denote by Cb the molecular tree with the maximum Sombor index (respectively reduced Sombor index) from the class Cn,nb for 3n−78<nb≤2n−65. By using Lemma 10 it is easy to check that n2(Cb)=0 as n−23<3n−78<nb, which implies that Cb∈Cp and further (a) part of Lemma 9 concludes that n1(Cb)=n−nb, n3(Cb)=3nb−n+2 and n4(Cb)=n−2nb−2. Note that nb≤2n−65 can be easily written as 3nb−n+4≤n−2nb−2, which leads us to the fact n3(Cb)+2≤n4(Cb).
From Lemmas 2–4 it is clear that we have to place the vertices as described in the proof of Theorem 5. Keeping in mind the fact 2n3(Cb)+1>n4(Cb)≥n3(Cb)+2 and Eqs (4.6), (4.14) and (4.15), we have x3,3(Cb)=2n3(Cb)+1−n4(Cb)=8nb−3n+7, x3,4(Cb)=n3(Cb)+2+2(n4(Cb)−(n3(Cb)+2))=3n−7nb−8 and x4,4(Cb)=0. Hence, SO(Cb)=√17(n−nb)+3√2(8nb−3n+7)+5(3n−7nb−8) and SOred(Cb)=3(n−nb)+2√2(8nb−3n+7)+√13(3n−7nb−8), which completes the proof.
Theorem 7. If C∈Cn,nb such that 2n−65<nb≤n−22, then
i) SO(C)≤(5+3√17)(n−2nb−2)−√10(2n−5nb−6)−3√2(n−3nb−1),
ii) SOred(C)≤(5n−8nb−6)+√13(n−2nb−2)−2√2(n−3nb−1),
and the equalities occur if and only if Cb≅B5.
Proof. Denote by Cb the molecular tree with the maximum Sombor index (respectively reduced Sombor index) from the class Cn,nb for 2n−65<nb≤n−22. By using Lemma 10 it is easy to check that n2(Cb)=0 as n−23<2n−65<nb, which implies that Cb∈Cp and further (a) part of Lemma 9 concludes that n1(Cb)=n−nb, n3(C)=3nb−n+2 and n4(Cb)=n−2nb−2. Note that nb>2n−65 can be easily written as 3nb−n+4>n−2nb−2, which leads us to the fact n3(Cb)+2>n4(Cb). From Lemmas 2–4 it is clear that we have to place the vertices of degree 4 between the pendent vertices and the vertices of degree 3. The fact n3(Cb)+2>n4(Cb) gives the result
x1,4(Cb)=3n4(Cb)=3n−6nb−6, | (4.16) |
and
x1,3(Cb)=5nb−2n+6. | (4.17) |
Now, using (4.6), (4.16) and (4.17), we have x3,3(Cb)=n3(Cb)−1=3nb−n+1, x3,4(Cb)=n4(Cb)=n−2nb−2 and x4,4(Cb)=0. Hence, SO(Cb)=(5+3√17)(n−2nb−2)−√10(2n−5nb−6)−3√2(n−3nb−1) and SOred(Cb)=(5n−8nb−6)+√13(n−2nb−2)−2√2(n−3nb−1), which completes the proof.
Denote by C∗n,q the class of all n-vertex molecular trees, where q is the number of vertices of degree 2. Next, we are going to obtain the upper bounds for the molecular trees with respect to Sombor index and reduced Sombor index from the collection of molecular trees C∗n,q for 0≤q≤n−2. It is obvious that the path graph Pn is the unique graph for q=n−2, and there does not exist any graph corresponding to the value q=n−3 in the collection C∗n,q. Hence, we proceed with the assumption that 0≤q≤n−4.
Lemma 11. If the molecular tree C∈C∗n,q is the tree with the maximum Sombor index (respectively reduced Somber index), then n3(C)≤2.
Proof. Suppose contrarily that n3(C)>2, and there are vertices u,w and z of degree 3 such that w is located on the unique u−z path. Consider Nz(C)={z1,z2,z3} with the assumption that the vertex z3 lies on the u−z path in C (z3 may coincide with w). Now, a tree C′ can be obtained from the collection C∗n,q such as C′=C−{zz1,zz2}+{uz1,wz2}, which gives the following result:
SO(C)=SO(C′)+∑x∈NC(u)√d2x+9+∑y∈NC(w)√d2y+9+3∑i=1√d2zi+9−∑x∈NC(u)√d2x+16−∑y∈NC(w)√d2y+16−2∑i=1√d2zi+16−√d2z3+1<SO(C′)+∑x∈NC(u)√d2x+9+3∑i=1√d2zi+9−∑x∈NC(u)√d2x+16−2∑i=1√d2zi+16−√d2z3+1≤SO(C′)+5(5)−20√2+√10−√2<SO(C′), |
a contradiction for the chosen C.
Similarly
SOred(C)=SOred(C′)+∑x∈NC(u)√(dx−1)2+4+∑y∈NC(w)√(dy−1)2+4+3∑i=1√(dzi−1)2+4−∑x∈NC(u)√(dx−1)2+9−∑y∈NC(w)√(dy−1)2+9−2∑i=1√(dzi−1)2+9−√(dz3−1)2<SOred(C′)+5√13−15√2+2<SOred(C′), |
which also leads to a contradiction.
Lemma 12. If C∈C∗n,q, then
i) n3(C)=0 if and only if n−q−2≡0 (mod 3), n4(C)=n−q−23 and n1(C)=23(n−q+1),
ii) n3(C)=1 if and only if n−q−1≡0 (mod 3), n4(C)=n−q−43 and n1(C)=23(n−q−1)+1,
iii) n3(C)=2 if and only if n−q≡0 (mod 3), n4(C)=n−q−63 and n1(C)=23(n−q).
Proof. The following equation can be drawn by using Eqs (4.3) and (4.4):
n1(C)=n3(C)+2n4(C)+2. | (4.18) |
Now, using Eqs (4.3) and (4.18), we get
n−q−2−2n3(C)=3n4(C) | (4.19) |
or
n−q−2−2n3(C)≡0(mod3). | (4.20) |
By solving the Eqs (4.4) and (4.18) for the values of n1(C) and n4(C), we get
n1(C)=2n−2q+2−n3(C)3, | (4.21) |
and
n4(C)=n−q−2−2n3(C)3. | (4.22) |
The required results are directly followed by Eqs (4.20)–(4.22).
Lemma 13. If C∈C∗n,q is the tree with the maximum Sombor index (respectively reduced Somber index) with n−4≤q≤n−5, then x1,2(C)≤1.
Proof. Note that there is a unique branching vertex (say) u in C with the fact that du=3 if q=n−4, and du=4 if q=n−5. Let us assume that, for l,m≥3, there are paths u1u2⋯ulu and u′1u′2⋯u′mu in C such that dui=2=du′j for all 2≤i≤l and 2≤j≤m, and du1=1=du′1. If a tree C′ in the class C∗n,q is chosen as C′=C−{ul−1ul}+{ul−1u′1}, then
SO(C)=SO(C′)+√4+d2u−√1+d2u+√5−2√2, |
and
SOred(C)=SOred(C′)+√1+(du−1)2−√(du−1)2+1−√2, |
by using the fact du=3 or du=4 in the above mentioned results it can easily be checked that SO(C)<SO(C′) and SOred(C)<SOred(C′), which is a contradiction.
Lemma 14. If C∈C∗n,q is the tree with the maximum Sombor index (respectively reduced Somber index) such that q≤n−6, then x1,2(C)=0.
Proof. The results can be proved by using the same process as done in Lemma 8.
Note that C∗4,0 and C∗5,0 contain unique trees C1 and C2, respectively, with the Sombor and reduced Sombor index values given in Table 1. Further more, by using Lemma 13 it can be observed that C5 and C6 are the molecular trees with maximum (reduced) Somber index values (given in Table 1) among the graphs in C∗6,0 and C∗7,0, respectively. Among all the molecular trees C∗n,q, where q≥1, If we consider C3={C∈C∗n,q:x1,3(C)=2,x1,2(C)=1,x2,3(C)=1,x2,2(C)=n−5} and C4={C∈C∗n,q:x1,4(C)=3,x1,2(C)=1,x2,4(C)=1,x2,2(C)=n−6} (given in Figure 1), the following result is observed:
Theorem 8. For the molecular tree C∈C∗n,q, where n≥5, the following results hold:
a) If C∈C∗n,n−4∖C3, then SO(C)<SO(C3).
b) If C∈C∗n,n−5∖C4, then SO(C)<SO(C4).
Proof. Using Lemma 13, it can be concluded that C3 among the class C∗n,n−4 and C4 among C∗n,n−5, respectively, contain the maximum (reduced) Sombor index value (given in Table 1), which completes the proof.
Consider the following subsets of C∗n,q:
Q0={C∈C∗n,q: q<n−5 and n3(C)=0 such that x1,4(C)=23(n−q+1) and x2,2(C)=0 whenever x4,4(C)≠0},
Q1={C∈C∗n,q: q<n−5 and n3(C)=1 such that x1,2(C)=0 and x1,3(C)≠0 implies that there does not exist P4,4 in C moreover if x2,j(C)≠0 for 2≤j≤3, then x4,4(C)=0},
Q2={C∈C∗n,q: n3(C)=2 such that x1,2(C)=0, x1,3(C)≠0 ⇒ P4,4=0 and P3,3≠0, and whenever x1,3(C)=0 along with P3,3≠0, then P4,4=0, furthermore x2,i(C)≠0 ⇒ xj,k=0, where 2≤i≤3 and 3≤j,k≤4}.
Theorem 9. Let C∈C∗n,q for q<n−5 such that n3(C)=0. Then
SO(C)≤{2√173(n−q+1)+4√23(n−4q−5)+4√5qifq<n−54,2√173(n−q+1)+4√53(n−q−5)−2√23(n−4q−5)ifq≥n−54. |
And
SOred(C)≤{√2(n−4q−5)+2(n−q+1)+2√10qifq<n−54,2(n−q+1)+2√103(n−q−5)−√23(n−4q−5)ifq≥n−54. |
Equalities hold if and only if C∈Q0.
Proof. Denote by Cq0 the molecular tree having maximum Sombor index (or reduced Sombor index) among the collection C∗n,q such that n3(Cq0)=0. By using Lemma 12 it follows that n−q−2≡0 (mod 3), n4(Cq0)=n−q−23 and n1(Cq0)=23(n−q+1). The vertices of degree 2 are to be placed according to the conditions proved in Lemmas 6 and 14, that is all the pendent vertices are to be attached to the vertices of degree 4 i.e., Lemma 14 concludes that
x1,2(Cq0)=0, | (4.23) |
which implies that
x1,4(Cq0)=23(n−q+1). | (4.24) |
Further more, the vertices of degree 2 are to be placed between the vertices of degree 4 in such a way that if there is an edge connecting the vertices of degree 4, then no two vertices of degree 2 are adjacent. The above discussion leads us to the fact that Cq0∈Q0. Now the following two cases arise here:
Case I. n2(Cq0)<n4(Cq0)−1 or q<n−54.
In this case, Lemma 6 implies that
x2,2(Cq0)=0. | (4.25) |
By using (4.6), (4.23)–(4.25), we have x2,4(Cq0)=2q and x4,4(Cq0)=n−4q−53. Hence, SO(Cq0)=2√173(n−q+1)+4√23(n−4q−5)+4√5q and SOred(Cq0)=√2(n−4q−5)+2(n−q+1)+2√10q.
Case II. n2(Cq0)≥n4(Cq0)−1 or q≥n−54.
In this case, by Lemma 6, we have
x4,4(Cq0)=0. | (4.26) |
Using (4.6), (4.23)–(4.26), we get x2,2(Cq0)=4q−n+53 and x2,4(Cq0)=2(n4(Cq0)−1)=23(n−q−5). Hence, SO(Cq0)=2√173(n−q+1)+4√53(n−q−5)−2√23(n−4q−5) and SOred(Cq0)=2(n−q+1)+2√103(n−q−5)−√23(n−4q−5), which completes the proof.
Theorem 10. Let C∈C∗n,q such that n3(C)=1. Then
SO(C)≤{2√10+3√17+5ifq=0andn=7,2√2(q−1)+2√5+2√10+3√17+√13ifq=n−7≥1,6√17+√10(√10+1)ifq=0andn=10,6√17+5+2√5+√13+√10ifq=1andn=11,2√2(q−2)+6√17+4√5+2√13+√10ifq≥2andn−q=10,(2√5−5)q+9√17+15ifq≤2andn−q=13,(2√2)(q−3)+9√17+3(2√5+√13)ifq>2andn−q=13,√173(2n−2q+1)+4√5q+4√23(n−4q−13)+15ifq<n−134,√173(2n−2q+1)+2√53(n+2q−13)+√133(4q−n+13)+53(n−4q−4)ifn−134≤q<n−43,√173(2n−2q+1)+2√23(4q−n+4)+2√53(2n−2q−15)+3√13ifq≥n−43. |
And
SOred(C)≤{√13(√13+1)ifq=0andn=7,√2(q−1)+√10+√5+13ifq=n−7≥1,20+2√13ifq=0andn=10,20+√13+√10+√5ifq=1andn=11,√2(q−2)+20+2√10+2√5ifq≥2andn−q=10,√13(3−q)+27+√10qifq≤2andn−q=13,√2(q−3)+27+3(√5+√10)ifq>2andn−q=13,(2n−2q+1)+2√10q+√2(n−4q−13)+3√13ifq<n−134,(2n−2q+1)+√103(n+2q−13)+√53(4q−n+13)+√133(n−4q−4)ifn−134≤q<n−43,(2n−2q+1)+√23(4q−n+4)+√103(2n−2q−15)+3√13ifq≥n−43. |
Equalities hold if and only if C∈Q1.
Proof. If Cq1 denotes the molecular tree having maximum Sombor index (or reduced Sombor index) among the collection C∗n,q, where n3(Cq1)=1, then by using Lemma 12 we have n−q−1≡0 (mod 3), n1(Cq1)=2n−2q+13, n4(Cq1)=n−q−43. Note that Lemmas 2, 14 and 5 show that Cq1∈Q1. This implies that
x1,2(Cq1)=0, | (4.27) |
and the vertices of degree 4 are to be placed in the three neighbors of the vertex of degree 3 in such a way that if a pendent vertex is present in Cq1 which is adjacent to the vertex of degree 3, then there must not exists a P4,4 path in Cq1. The following cases are possible:
Case 1. n4(Cq1)=1
Subcase 1.1. q=0.
In this case n=7, x2,j(Cq1)=0 for all 1≤j≤4, x3,4(Cq1)=1, x1,3(Cq1)=2 and x1,4(Cq1)=3. The graph here is C6 given in Figure 1 with (reduced) Sombor index value given in Table 1.
Subcase 1.2. q>0.
This holds for n≥8, by keeping in mind the Lemmas 5 and 6, and using the results in Eqs (4.6) and (4.27), we have x3,4(Cq1)=0, x2,3(Cq1)=1=x2,4(Cq1), x1,3(Cq1)=2, x1,4(Cq1)=3 and x2,2(Cq1)=q−1. Hence, SO(Cq1)=2√2(q−1)+2√5+2√10+3√17+√13 and SOred=√2(q−1)+√10+√5+13.
Case 2. n4(Cq1)=2.
Subcase 2.1. q=0 In this case we have n=10, where Lemma 2 shows that
x3,4(Cq1)=2. | (4.28) |
By using Eqs (4.6), (4.27) and (4.28), we have x1,3(Cq1)=1 and x1,4(Cq1)=6, which gives SO(Cq1)=6√17+√10(√10+1) and SOred(Cq1)=20+2√13.
Subcase 2.2. q=1
Here n=11, By using Eqs (4.6), (4.27), we have x1,3(Cq1)=1, x1,4(Cq1)=6 and x3,4(Cq1)=1=x2,3(Cq1)=x2,4(Cq1), which gives SO(Cq1)=6√17+5+2√5+√13+√10 and SOred(Cq1)=20+√13+√10+√5.
Subcase 2.3. q≥2
This holds for n≥12, and by keeping in mind the Lemmas 5, 6 and the results in Eqs (4.6) and (4.27), we have x1,3(Cq1)=1, x1,4(Cq1)=6, x2,4(Cq1)=2=x2,3(Cq1) and x2,2(Cq1)=q−2. Hence, SO(Cq1)=2√2(q−2)+6√17+4√5+2√13+√10 and SOred(Cq1)=√2(q−2)+20+2√10+2√5.
Case 3. n4(Cq1)=3
Lemma 2 gives
x1,3(Cq1)=0. | (4.29) |
Subcase 3.1. q≤2
Again Lemmas 5, 6 and the Eqs (4.6), (4.27) and (4.29) imply that, x1,4(Cq1)=9, x2,3(Cq1)=x2,4(Cq1)=q, x2,2(Cq1)=0=x4,4(Cq1) and x3,4(Cq1)=3−q. Hence, SO(Cq1)=(2√5−5)q+9√17+15 and SOred(Cq1)=√13(3−q)+27+√10q.
Subcase 3.2. q>2
Here x1,4(Cq1)=9, x2,3(Cq1)=x2,4(Cq1)=3, x2,2(Cq1)=q−3 and x3,4(Cq1)=0 are obtained by using Lemmas 5, 6 and the Eqs (4.6), (4.27) and (4.29). Hence, SO(Cq1)=(2√2)(q−3)+9√17+3(2√5+√13) and SOred(Cq1)=√2(q−3)+27+3(√5+√10).
Case 4. n4(Cq1)>3
Subcase 4.1. q<n−134
It is easy to check that q<n−134 implies that q<n4(Cq1)−3 or q<x4,4(Cq1). Lemmas 5, 6 and the Eqs (4.6), (4.27) and (4.29) follow the results x2,2(Cq1)=0=x2,3(Cq1), x2,4(Cq1)=q, x3,4(Cq1)=3, x1,4(Cq1)=2n−2q+13 and x4,4(Cq1)=n−4q−133. Hence, SO(Cq1)=√173(2n−2q+1)+4√5q+4√23(n−4q−13)+15 and SOred(Cq1)=(2n−2q+1)+2√10q+√2(n−4q−13)+3√13.
Subcase 4.2. n−134≤q<n−43
It gives n4(Cq1)−3≤q<n4, which implies that
x4,4(Cq1)=0, | (4.30) |
by keeping in mind the Lemmas 5, 6 and using the Eqs (4.27), (4.29) and (4.30) in (4.6), we have x2,2(Cq1)=0, x2,3(Cq1)=4q−n+133, x2,4(Cq1)=n+2q−133, x1,4(Cq1)=2n−2q+13 and x3,4(Cq1)=n−4q−43. Hence, SO(Cq1)=√173(2n−2q+1)+2√53(n+2q−13)+√133(4q−n+13)+53(n−4q−4) and SOred(Cq1)=(2n−2q+1)+√103(n+2q−13)+√53(4q−n+13)+√133(n−4q−4).
Subcase 4.3. q≥n−43
This imply that q≥n4(C), and Lemmas 5 and 6 conclude that
x3,4(Cq1)=0, | (4.31) |
and using the Eqs (4.27), (4.29)–(4.31) in (4.6), we have x1,4(Cq1)=2n−2q+13, x2,2(Cq1)=4q−n+43, x2,3(Cq1)=3 and x2,4(Cq1)=2n−2q−153. Hence, SO(Cq1)=√173(2n−2q+1)+2√23(4q−n+4)+2√53(2n−2q−15)+3√13 and SOred(Cq1)=(2n−2q+1)+√23(4q−n+4)+√103(2n−2q−15)+3√13.
Theorem 11. Let C∈C∗n,q, where n3(C)=2. Then
SO(C)≤{4√10+3√2ifn−q=6andq=0,2√2(q−1)+4√10+2√13ifn−q=6andq>0,√10(18−n+q)3+(3√17+5)(n−q−6)3+3√2if9≤n−q≤15andq=0,√103(18−n+q)+√17(n−q−6)+(√13+2√5−5)q+3√2+15if9≤n−q≤15and1≤q≤n−64,√103(18−n+q)+(3√17+2√5)3(n−q−6)+√133(n−q)+2√23(4q−n+3)if9≤n−q≤15andq>n−64,2√173(n−q)+(√13+2√5)q+5(4−q)+3√2ifn−q=18and1≤q≤4,2√173(n−q)+6√13+8√5+2√2(q−5)ifn−q=18andq>4,2√173(n−q)+(√13+2√5)q+5(6−q)ifn−q=21and0≤q≤6,2√173(n−q)+6(√13+2√5)+2√2(q−6)ifn−q=21andq>6,2√173(n−q)+4√5q+4√2(n−4q−21)3+30ifn−q>21andq≤n−214,2√173(n−q)+√13(4q−n+21)3+2√5(n+2q−21)3+5(n−4q−3)3ifn−q>21andn−214<q≤n−34,2√173(n−q)+2√2(4q−n+3)3+4√5(n−q−12)3+6√13ifn−q>21andq>n−34. |
And
SOred(C)≤{8+2√2ifn−q=6andq=0,√2(q−1)+8+2√5ifn−q=6andq>0,2(18−n+q)3+(9+√13)(n−q−6)3+2√2if9≤n−q≤15andq=0,2(18−n+q)3+3(n−q−6)3+(√5+√10−√13)q+2√2+3√13if9≤n−q≤15and1≤q≤n−64,2(18−n+q)3+(9+√10)(n−q−6)3+√53(n−q)+√23(4q−n+3)if9≤n−q≤15andq>n−64,2(n−q)+(√5+√10)q+√13(4−q)+2√2ifn−q=18and1≤q≤4,2(n−q)+6√5+4√10+√2(q−5)ifn−q=18andq>4,2(n−q)+(√5+√10)q+√13(6−q)ifn−q=21and0≤q≤6,2(n−q)+6(√5+√10)+√2(q−6)ifn−q=21andq>6,2(n−q)+2√10q+√2(n−4q−21)+6√13ifn−q>21andq≤n−214,2(n−q)+2√10q+√5(4q−n+21)3+√10(n+2q−21)3+√13(n−4q−3)3ifn−q>21andn−214<q≤n−34,2(n−q)+6√5+√2(4q−n+3)3+2√10(n−q−12)3ifn−q>21andq>n−34. |
Equalities hold if and only if C∈Q2.
Proof. Let Cq2 denotes the molecular tree with maximum (reduced) Sombor index value among the class C∗n,q, where n3(Cq2)=2. By Lemma 12, n−q≡0 (mod 3), n1(Cq2)=2n−2q3 and n4(Cq2)=n−q−63. By Lemma 14 it holds that
x1,2(Cq2)=0, | (4.32) |
and Lemmas 2–6 provide the consequence Cq2∈Q2. We consider the following cases:
Case 1. n4(Cq2)=0 or n−q=6
Subcase 1.1. q=0
Here, using Eq (4.6), we have x1,3(Cq2)=4 and x3,3(Cq2)=1, which give SO(Cq2)=4√10+3√2 and SOred(Cq2)=8+2√2.
Subcase 1.2. q>0
By using (4.32) in (4.6), it is easy to get x1,3(Cq2)=4, x2,2(Cq2)=q−1, x2,3(Cq2)=2 and x3,3(Cq2)=0, which give SO(Cq2)=2√2(q−1)+4√10+2√13 and SOred(Cq2)=√2(q−1)+8+2√5.
Case 2. 1≤n4(Cq2)≤3 or 9≤n−q≤15
By using Lemmas 2–4 and Eq (4.32), we have
x1,3(Cq2)=4−n4(Cq2)=18−n+q3, | (4.33) |
x1,4(Cq2)=n1(Cq2)−x1,3(Cq2)=n−q−6. | (4.34) |
and
x4,4(Cq2)=0. | (4.35) |
Subcase 2.1. q=0
Using Eqs (4.32)–(4.35) in (4.6), we have x3,3(Cq2)=1 and x3,4(Cq2)=n−q−63, which give SO(Cq2)=√103(18−n+q)+(√17+53)(n−q−6)+3√2 and SOred(Cq2)=2(18−n+q)3+(9+√13)(n−q−6)3+2√2.
Subcase 2.2. 1≤q≤n−64
This case holds for q≤n4(Cq2), so by using Lemmas 5, 6 and the Eqs (4.32)–(4.35) in (4.6), we have x3,3(Cq2)=1, x3,4(Cq2)=3−q, x2,3(Cq2)=q=x2,4(Cq2) and x2,2(Cq2)=0, which give SO(Cq2)=√103(18−n+q)+√17(n−q−6)+(√13+2√5−5)q+3√2+15 and SOred(Cq2)=2(18−n+q)3+3(n−q−6)3+(√5+√10−√13)q+2√2+3√13.
Subcase 2.3. q>n−64
This holds for q>n4(Cq2), and again by keeping in mind the results used in Subcase 2.2, we may easily get x3,3(Cq2)=0=x3,4(Cq2), x2,3(Cq2)=n−q3, x2,4(Cq2)=n−q−63 and x2,2(Cq2)=4q−n+33. Hence, SO(Cq2)=√103(18−n+q)+(3√17+2√5)3(n−q−6)+√133(n−q)+2√23(4q−n+3) and SOred(Cq2)=2(18−n+q)3+(9+√10)(n−q−6)3+√53(n−q)+√23(4q−n+3).
Case 3. n−q=18 or n4(Cq2)=4
In this case, Lemmas 2–4 and Eq. (4.32) show that (4.35) holds and
x1,3(Cq2)=0, | (4.36) |
also
x1,4(Cq2)=2n−2q3. | (4.37) |
Consider the following possibilities:
Subcase 3.1. 0≤q≤4
Keeping in mind Lemmas 5 and 6, also using the Eqs (4.6), (4.32) and (4.35)–(4.37), we have x2,2(Cq2)=0, x2,3(Cq2)=q=x2,4(Cq2), x3,3(Cq2)=1 and x3,4(Cq2)=4−q. Hence, SO(Cq2)=2√173(n−q)+(√13+2√5)q+5(4−q)+3√2 and SOred(Cq2)=2(n−q)+(√5+√10)q+√13(4−q)+2√2.
Subcase 3.2. q>4
Taking into account the facts used in Subcase 3.1, we may check that x2,2(Cq2)=q−5, x2,3(Cq2)=6, x2,4(Cq2)=4 and x3,3(Cq2)=0=x3,4(Cq2). Hence, SO(Cq2)=2√173(n−q)+6√13+8√5+2√2(q−5) and SOred(Cq2)=2(n−q)+6√5+4√10+√2(q−5).
Case 4. n−q>18 or n4(Cq2)>4
Lemmas 2–4 imply that (4.36) and (4.37) hold and
x3,3(Cq2)=0. | (4.38) |
Subcase 4.1. n−q=21 and 0≤q≤6
Note that (4.35) holds in this case, further more Lemmas 5, 6 and the Eqs (4.6), (4.32), (4.35) and (4.36)–(4.38), we have x2,2(Cq2)=0, x2,3(Cq2)=q=x2,4(Cq2) and x3,4(Cq2)=6−q. Hence, SO(Cq2)=2√173(n−q)+(√13+2√5)q+5(6−q) and SOred(Cq2)=2(n−q)+(√5+√10)q+√13(6−q).
Subcase 4.2. n−q=21 and q>6
Taking into account the facts used in Subcase 3.1, we have x2,2(Cq2)=q−6, x2,3(Cq2)=6=x2,4(Cq2) and x3,4(Cq2)=0. Hence, SO(Cq2)=2√173(n−q)+6(√13+2√5)+2√2(q−6) and SOred(Cq2)=2(n−q)+6(√5+√10)+√2(q−6).
Subcase 4.3. n−q>21 and q≤n−214
This case implies that q≤n4(Cq2)−5 for which x2,3(Cq2)=0 by Lemma 5. Now using Lemma 6 and Eqs (4.6), (4.32) and (4.36)–(4.38), we have x2,2(Cq2)=0, x2,4(Cq2)=2q, x4,4(Cq2)=n−4q−213 and x3,4(Cq2)=6. Hence, SO(Cq2)=2√173(n−q)+4√5q+4√2(n−4q−21)3+30 and SOred(Cq2)=2(n−q)+2√10q+√2(n−4q−21)+6√13.
Subcase 4.4. n−q>21 and n−214<q≤n−34
(4.35) holds in this case and also using (4.6), (4.32) and (4.36)–(4.38), we have x2,2(Cq2)=0, x2,3(Cq2)=4q−n+213, x2,4(Cq2)=n+2q−213 and x3,4(Cq2)=n−4q−33. Hence, SO(Cq2)=2√173(n−q)+√13(4q−n+21)3+2√5(n+2q−21)3+5(n−4q−3)3 and SOred(Cq2)=2(n−q)+2√10q+√5(4q−n+21)3+√10(n+2q−21)3+√13(n−4q−3)3.
Subcase 4.5. n−q>21 and q>n−34
Again using Lemmas 5, 6 and the Eqs (4.6), (4.32), (4.35) and (4.36)–(4.38), we have x2,2(Cq2)=4q−n+33, x2,3(Cq2)=6, x2,4(Cq2)=2(n−q−12)3 and x3,4(Cq2)=0. Hence, SO(Cq2)=2√173(n−q)+2√2(4q−n+3)3+4√5(n−q−12)3+6√13 and SOred(Cq2)=2(n−q)+6√5+√2(4q−n+3)3+2√10(n−q−12)3.
In this paper, an extremal chemical-graph-theoretical problem concerning the Sombor index and the reduced Sombor index is addressed. Particularly, the problem of characterizing trees possessing the maximum values of the aforementioned two indices from the class of all molecular trees of a given order and with a fixed number of (i) branching vertices (ii) vertices of degree 2, is solved in this paper. A solution to the minimal version of this problem regarding the Sombor index was reported in [3]. It is believed that the minimal version of the problem under consideration regarding the reduced Sombor index is not difficult and can be solved by using the technique used in [3]; nevertheless, it still seems to be interesting to find such a solution. Solving Problem 1 for the multiplicative and exponential versions of the Sombor and reduced Sombor indices (for example, see [11]) is another possible direction for a future work concerning the present study.
The authors have no conflict of interest.
[1] | Yang T, Percival RV (2009) The emergence of global environmental law. Ecol Law Q 36: 615–664. |
[2] |
Fang JY, Zhu JL, Wang SP, et al. (2011) Global warming, human-induced carbon emissions, and their uncertainties. Sci China Earth Sci 54: 1458–1468. https://doi.org/10.1007/s11430-011-4292-0 doi: 10.1007/s11430-011-4292-0
![]() |
[3] |
Wu W, Chou SC, Viswanathan K (2023) Optimal dispatching of smart hybrid energy systems for addressing a low-carbon community. Energies 16: 3698. https://doi.org/10.3390/en16093698 doi: 10.3390/en16093698
![]() |
[4] |
Omer AM (2008) Energy, environment and sustainable development. Renewable Sustainable Energy Rev 12: 2265–2300. https://doi.org/10.1016/j.rser.2007.05.001 doi: 10.1016/j.rser.2007.05.001
![]() |
[5] |
Thompson WR (2001) Identifying rivals and rivalries in world politics. Int Stud Quart 45: 557–586. https://doi.org/10.1111/0020-8833.00214 doi: 10.1111/0020-8833.00214
![]() |
[6] |
Ferreira S, Monteiro E, Brito P, et al. (2017) Biomass resources in Portugal: Current status and prospects. Renewable Sustainable Energy Rev 78: 1221–1235. https://doi.org/10.1016/j.rser.2017.03.140 doi: 10.1016/j.rser.2017.03.140
![]() |
[7] | Torres PJF, Ekonomou L, Karampelas P (2016) The correlation between renewable generation and electricity demand: A case study of Portugal. In: Karampelas, P., Ekonomou, L., Electricity Distribution. Energy Systems. Springer, Berlin, Heidelberg, 119–151. https://doi.org/10.1007/978-3-662-49434-9_5 |
[8] |
Khatiwada D, Vasudevan RA, Santos BH (2022) Decarbonization of natural gas systems in the EU—Costs, barriers, and constraints of hydrogen production with a case study in Portugal. Renewable Sustainable Energy Rev 168: 112775. https://doi.org/10.1016/j.rser.2022.112775 doi: 10.1016/j.rser.2022.112775
![]() |
[9] |
Bhutto AW, Bazmi AA, Zahedi G (2011) Greener energy: Issues and challenges for Pakistan—Biomass energy prospective. Renewable Sustainable Energy Rev 15: 3207–3219. https://doi.org/10.1016/j.rser.2011.04.015 doi: 10.1016/j.rser.2011.04.015
![]() |
[10] |
Gustavsson L, Börjesson P, Johansson B, et al. (1995) Reducing CO2 emissions by substituting biomass for fossil fuels. Energy 20: 1097–1113. https://doi.org/10.1016/0360-5442(95)00065-O doi: 10.1016/0360-5442(95)00065-O
![]() |
[11] |
Demirbas A (2005) Potential applications of renewable energy sources, biomass combustion problems in boiler power systems and combustion related environmental issues. Prog Energy Combust Sci 31: 171–192. https://doi.org/10.1016/j.pecs.2005.02.002 doi: 10.1016/j.pecs.2005.02.002
![]() |
[12] |
Crutzen PJ, Andreae MO (1990) Biomass burning in the tropics: Impact on atmospheric chemistry and biogeochemical cycles. Science 250: 1669–1678. https://doi.org/10.1126/science.250.4988.1669 doi: 10.1126/science.250.4988.1669
![]() |
[13] |
Mousa E, Wang C, Riesbeck J, et al. (2016) Biomass applications in iron and steel industry: An overview of challenges and opportunities. Renewable Sustainable Energy Rev 65: 1247–1266. https://doi.org/10.1016/j.rser.2016.07.061 doi: 10.1016/j.rser.2016.07.061
![]() |
[14] |
Klein-Marcuschamer D, Simmons BA, Blanch HW (2011) Techno-economic analysis of a lignocellulosic ethanol biorefinery with ionic liquid pre-treatment. Biofuels Bioprod Biorefin 5: 562–569. https://doi.org/10.1002/bbb.303 doi: 10.1002/bbb.303
![]() |
[15] | Godina R, Nunes LJR, Santos FMBC, et al. (2018) Logistics cost analysis between wood pellets and torrefied biomass pellets: The case of Portugal. 2018 7th International Conference on Industrial Technology and Management (ICITM), IEEE, 284–287. https://doi.org/10.1109/ICITM.2018.8333962 |
[16] |
Hakkila P (2006) Factors driving the development of forest energy in Finland. Biomass Bioenergy 30: 281–288. https://doi.org/10.1016/j.biombioe.2005.07.003 doi: 10.1016/j.biombioe.2005.07.003
![]() |
[17] |
Su Y, Hiltunen P, Syri S, et al. (2022) Decarbonization strategies of Helsinki metropolitan area district heat companies. Renewable Sustainable Energy Rev 160: 112274. https://doi.org/10.1016/j.rser.2022.112274 doi: 10.1016/j.rser.2022.112274
![]() |
[18] |
Moya R, Tenorio C, Oporto G (2019) Short rotation wood crops in Latin American: A review on status and potential uses as biofuel. Energies 12: 705. https://doi.org/10.3390/en12040705 doi: 10.3390/en12040705
![]() |
[19] |
Heinimö J, Junginger M (2009) Production and trading of biomass for energy–An overview of the global status. Biomass Bioenergy 33: 1310–1320. https://doi.org/10.1016/j.biombioe.2009.05.017 doi: 10.1016/j.biombioe.2009.05.017
![]() |
[20] |
Bilgen S, Kaygusuz K, Sari A (2004) Renewable energy for a clean and sustainable future. Energy Sources 26: 1119–1129. https://doi.org/10.1080/00908310490441421 doi: 10.1080/00908310490441421
![]() |
[21] |
Bórawski P, Bełdycka-Bórawska A, Szymańska EJ, et al. (2019) Development of renewable energy sources market and biofuels in the European Union. J Cleaner Prod 228: 467–484. https://doi.org/10.1016/j.jclepro.2019.04.242 doi: 10.1016/j.jclepro.2019.04.242
![]() |
[22] |
Sikkema R, Steiner M, Junginger M, et al. (2011) The European wood pellet markets: Current status and prospects for 2020. Biofuels Bioprod Biorefin 5: 250–278. https://doi.org/10.1002/bbb.277 doi: 10.1002/bbb.277
![]() |
[23] |
Olugbade TO, Ojo OT (2020) Biomass torrefaction for the production of high-grade solid biofuels: A review. Bioenergy Res 13: 999–1015. https://doi.org/10.1007/s12155-020-10138-3 doi: 10.1007/s12155-020-10138-3
![]() |
[24] |
Tumuluru JS, Wright CT, Hess JR, et al. (2011) A review of biomass densification systems to develop uniform feedstock commodities for bioenergy application. Biofuels Bioprod Biorefin 5: 683–707. https://doi.org/10.1002/bbb.324 doi: 10.1002/bbb.324
![]() |
[25] |
Taipabu MI, Viswanathan K, Chen HT, et al. (2023) Green solvent production of ethyl lactate via process intensification. J Taiwan Inst Chem Eng 146: 104876. https://doi.org/10.1016/j.jtice.2023.104876 doi: 10.1016/j.jtice.2023.104876
![]() |
[26] | Nunes LJR, Matias JCO, Catalão JPS (2016) Torrefied biomass pellets: An alternative fuel for coal power plants. 2016 13th International Conference on the European Energy Market (EEM), IEEE. https://doi.org/10.1109/EEM.2016.7521316 |
[27] |
Tursi A (2019) A review on biomass: Importance, chemistry, classification, and conversion. Biofuel Res J 6: 962–979. https://doi.org/10.18331/BRJ2019.6.2.3 doi: 10.18331/BRJ2019.6.2.3
![]() |
[28] | Tumuluru JS, Wright CT, Boardman RD, et al. (2011) A review on biomass classification and composition, co-firing issues and pretreatment methods. 2011 Louisville, Kentucky, August 7–10, 2011. https://doi.org/10.13031/2013.37191 |
[29] |
Proskurina S, Heinimö J, Schipfer F, et al. (2017) Biomass for industrial applications: The role of torrefaction. Renewable Energy 111: 265–274. https://doi.org/10.1016/j.renene.2017.04.015 doi: 10.1016/j.renene.2017.04.015
![]() |
[30] |
Thrän D, Witt J, Schaubach K, et al. (2016) Moving torrefaction towards market introduction—Technical improvements and economic-environmental assessment along the overall torrefaction supply chain through the SECTOR project. Biomass Bioenergy 89: 184–200. https://doi.org/10.1016/j.biombioe.2016.03.004 doi: 10.1016/j.biombioe.2016.03.004
![]() |
[31] |
Uslu A, Faaij APC, Bergman PCA (2008) Pre-treatment technologies, and their effect on international bioenergy supply chain logistics. Techno-economic evaluation of torrefaction, fast pyrolysis and pelletisation. Energy 33: 1206–1223. https://doi.org/10.1016/j.energy.2008.03.007 doi: 10.1016/j.energy.2008.03.007
![]() |
[32] |
Ciolkosz D, Wallace R (2011) A review of torrefaction for bioenergy feedstock production. Biofuels Bioprod Biorefin 5: 317–329. https://doi.org/10.1002/bbb.275 doi: 10.1002/bbb.275
![]() |
[33] |
Taipabu MI, Viswanathan K, Wu W (2023) Process design and optimization of green processes for the production of hydrogen and urea from glycerol. Int J Hydrogen Energy 48: 24212–24241. https://doi.org/10.1016/j.ijhydene.2023.03.163 doi: 10.1016/j.ijhydene.2023.03.163
![]() |
[34] |
Meisterling K, Samaras C, Schweizer V (2009) Decisions to reduce greenhouse gases from agriculture and product transport: LCA case study of organic and conventional wheat. J Cleaner Prod 17: 222–230. https://doi.org/10.1016/j.jclepro.2008.04.009 doi: 10.1016/j.jclepro.2008.04.009
![]() |
[35] | Litman T (2009) Transportation cost and benefit analysis. Victoria Transp Policy Inst 31: 1–19. |
[36] |
Psaraftis HN, Kontovas CA (2013) Speed models for energy-efficient maritime transportation: A taxonomy and survey. Transport Res C-Emer 26: 331–351. https://doi.org/10.1016/j.trc.2012.09.012 doi: 10.1016/j.trc.2012.09.012
![]() |
[37] |
Gasparatos A, Doll CNH, Esteban M, et al. (2017) Renewable energy and biodiversity: Implications for transitioning to a green economy. Renewable Sustainable Energy Rev 70: 161–184. https://doi.org/10.1016/j.rser.2016.08.030 doi: 10.1016/j.rser.2016.08.030
![]() |
[38] |
Ekins P (1999) European environmental taxes and charges: Recent experience, issues and trends. Ecol Econ 31: 39–62. https://doi.org/10.1016/S0921-8009(99)00051-8 doi: 10.1016/S0921-8009(99)00051-8
![]() |
[39] |
Wu W, Taipabu MI, Chang WC, et al. (2022) Economic dispatch of torrefied biomass polygeneration systems considering power/SNG grid demands. Renewable Energy 196: 707–719. https://doi.org/10.1016/j.renene.2022.07.007 doi: 10.1016/j.renene.2022.07.007
![]() |
[40] |
Jones-Lee MW (1990) The value of transport safety. Oxford Rev Econ Pol 6: 39–60. https://doi.org/10.1093/oxrep/6.2.39 doi: 10.1093/oxrep/6.2.39
![]() |
[41] |
Searcy E, Flynn P, Ghafoori E, et al. (2007) The relative cost of biomass energy transport. Appl Bioche Biotechnol 137: 639–652. https://doi.org/10.1007/s12010-007-9085-8 doi: 10.1007/s12010-007-9085-8
![]() |
[42] |
Abbas T, Costen PG, Lockwood FC (1996) Solid fuel utilization: From coal to biomass. Symp (Int) Combust 26: 3041–3058. https://doi.org/10.1016/S0082-0784(96)80148-2 doi: 10.1016/S0082-0784(96)80148-2
![]() |
[43] |
Bajwa DS, Peterson T, Sharma N, et al. (2018) A review of densified solid biomass for energy production. Renewable Sustainable Energy Rev 96: 296–305. https://doi.org/10.1016/j.rser.2018.07.040 doi: 10.1016/j.rser.2018.07.040
![]() |
[44] |
Shahi C, Upadhyay TP, Pulkki R, et al. (2011) Integrated model for power generation from biomass gasification: A market readiness analysis for northwestern Ontario. For Chron 87: 48–53. https://doi.org/10.5558/tfc87048-1 doi: 10.5558/tfc87048-1
![]() |
[45] |
Herran DS, Nakata T (2012) Design of decentralized energy systems for rural electrification in developing countries considering regional disparity. Appl Energy 91: 130–145. https://doi.org/10.1016/j.apenergy.2011.09.022 doi: 10.1016/j.apenergy.2011.09.022
![]() |
[46] |
Sharma HB, Sarmah AK, Dubey B (2020) Hydrothermal carbonization of renewable waste biomass for solid biofuel production: A discussion on process mechanism, the influence of process parameters, environmental performance and fuel properties of hydrochar. Renewable Sustainable Energy Rev 123: 109761. https://doi.org/10.1016/j.rser.2020.109761 doi: 10.1016/j.rser.2020.109761
![]() |
[47] |
Kambo HS, Dutta A (2014) Strength, storage, and combustion characteristics of densified lignocellulosic biomass produced via torrefaction and hydrothermal carbonization. Appl Energy 135: 182–191. https://doi.org/10.1016/j.apenergy.2014.08.094 doi: 10.1016/j.apenergy.2014.08.094
![]() |
[48] |
Daskin MS (1985) Logistics: An overview of the state of the art and perspectives on future research. Transp Res Part A Gen 19: 383–398. https://doi.org/10.1016/0191-2607(85)90036-6 doi: 10.1016/0191-2607(85)90036-6
![]() |
[49] |
Saidur R, Abdelaziz EA, Demirbas A, et al. (2011) A review on biomass as a fuel for boilers. Renewable Sustainable Energy Rev 15: 2262–2289. https://doi.org/10.1016/j.rser.2011.02.015 doi: 10.1016/j.rser.2011.02.015
![]() |
[50] |
Thomas DJ, Griffin PM (1996) Coordinated supply chain management. Eur J Oper Res 94: 1–15. https://doi.org/10.1016/0377-2217(96)00098-7 doi: 10.1016/0377-2217(96)00098-7
![]() |
[51] | Van Thuijl E, Roos CJ, Beurskens LWM (2003) An overview of biofuel technologies, markets and policies in Europe. Energy Research Centre of the Netherlands, ECN Policy Studies Report: ECN-C--03-008. Available from: https://imedea.uib-csic.es/master/cambioglobal/Modulo_Ⅱ_cod101602/Biofuels%20in%20Europe.pdf. |
[52] |
Beagle E, Belmont E (2019) Comparative life cycle assessment of biomass utilization for electricity generation in the European Union and the United States. Energy Policy 128: 267–275. https://doi.org/10.1016/j.enpol.2019.01.006 doi: 10.1016/j.enpol.2019.01.006
![]() |
[53] |
Thomson H, Liddell C (2015) The suitability of wood pellet heating for domestic households: A review of literature. Renewable Sustainable Energy Rev 42: 1362–1369. https://doi.org/10.1016/j.rser.2014.11.009 doi: 10.1016/j.rser.2014.11.009
![]() |
[54] |
Yun H, Clift R, Bi X (2020) Process simulation, techno-economic evaluation and market analysis of supply chains for torrefied wood pellets from British Columbia: Impacts of plant configuration and distance to market. Renewable Sustainable Energy Rev 127: 109745. https://doi.org/10.1016/j.rser.2020.109745 doi: 10.1016/j.rser.2020.109745
![]() |
[55] | Searcy E, Hess JR, Tumuluru JS, et al. (2014) Optimization of biomass transport and logistics. In: Junginger, M., Goh, C., Faaij, A., International Bioenergy Trade, Springer, Dordrecht, 103–123. https://doi.org/10.1007/978-94-007-6982-3_5 |
[56] |
Forsberg G (2000) Biomass energy transport: Analysis of bioenergy transport chains using life cycle inventory method. Biomass Bioenergy 19: 17–30. https://doi.org/10.1016/S0961-9534(00)00020-9 doi: 10.1016/S0961-9534(00)00020-9
![]() |
[57] |
Dujmović M, Šafran B, Jug M, et al. (2022) Biomass pelletizing process: A review. Drvna Ind 73: 99–106. https://doi.org/10.5552/drvind.2022.2139 doi: 10.5552/drvind.2022.2139
![]() |
[58] |
Nunes LJR, Causer TP, Ciolkosz D (2020) Biomass for energy: A review on supply chain management models. Renewable Sustainable Energy Rev 120: 109658. https://doi.org/10.1016/j.rser.2019.109658 doi: 10.1016/j.rser.2019.109658
![]() |
[59] |
Rane SB, Thakker SV (2020) Green procurement process model based on blockchain—IoT integrated architecture for a sustainable business. Manage Environ Qual 31: 741–763. https://doi.org/10.1108/MEQ-06-2019-0136 doi: 10.1108/MEQ-06-2019-0136
![]() |
[60] |
Varjani S, Shah AV, Vyas S, et al. (2021) Processes and prospects on valorizing solid waste for the production of valuable products employing bio-routes: A systematic review. Chemosphere 282: 130954. https://doi.org/10.1016/j.chemosphere.2021.130954 doi: 10.1016/j.chemosphere.2021.130954
![]() |
[61] |
Moro A, Helmers E (2017) A new hybrid method for reducing the gap between WTW and LCA in the carbon footprint assessment of electric vehicles. Int J Life Cycle Assess 22: 4–14. https://doi.org/10.1007/s11367-015-0954-z doi: 10.1007/s11367-015-0954-z
![]() |
[62] |
Lauf S, Haase D, Kleinschmit B (2014) Linkages between ecosystem services provisioning, urban growth and shrinkage—A modeling approach assessing ecosystem service trade-offs. Ecol Indic 42: 73–94. https://doi.org/10.1016/j.ecolind.2014.01.028 doi: 10.1016/j.ecolind.2014.01.028
![]() |
[63] |
Nunes LJR, Casau M, Ferreira Dias M (2021) Portuguese wood pellets market: Organization, production and consumption analysis. Resources 10: 130. https://doi.org/10.3390/resources10120130 doi: 10.3390/resources10120130
![]() |
[64] |
Tabor DP, Roch LM, Saikin SK, et al. (2018) Accelerating the discovery of materials for clean energy in the era of smart automation. Nat Rev Mater 3: 5–20. https://doi.org/10.1038/s41578-018-0005-z doi: 10.1038/s41578-018-0005-z
![]() |
[65] |
Garai A, Chowdhury S, Sarkar B, et al. (2021) Cost-effective subsidy policy for growers and biofuels-plants in closed-loop supply chain of herbs and herbal medicines: An interactive bi-objective optimization in T-environment. Appl Soft Comput 100: 106949. https://doi.org/10.1016/j.asoc.2020.106949 doi: 10.1016/j.asoc.2020.106949
![]() |
[66] |
Sarkar M, Sarkar B (2020) How does an industry reduce waste and consumed energy within a multi-stage smart sustainable biofuel production system? J Cleaner Prod 262: 121200. https://doi.org/10.1016/j.jclepro.2020.121200 doi: 10.1016/j.jclepro.2020.121200
![]() |
[67] |
Johansson TB, Turkenburg W (2004) Policies for renewable energy in the European Union and its member states: An overview. Energy Sustainable Dev 8: 5–24. https://doi.org/10.1016/S0973-0826(08)60387-7 doi: 10.1016/S0973-0826(08)60387-7
![]() |
[68] |
Chandel SS, Sharma A, Marwaha BM (2016) Review of energy efficiency initiatives and regulations for residential buildings in India. Renewable Sustainable Energy Rev 54: 1443–1458. https://doi.org/10.1016/j.rser.2015.10.060 doi: 10.1016/j.rser.2015.10.060
![]() |
[69] |
Izadian A, Girrens N, Khayyer P (2013) Renewable energy policies: A brief review of the latest US and EU policies. IEEE Ind Electron Mag 7: 21–34. https://doi.org/10.1109/MIE.2013.2269701 doi: 10.1109/MIE.2013.2269701
![]() |
[70] | Metcalf GE (2008) Tax policy financing for alternative energy equipment. J Equip Lease Financ 26: 1–7. Available from: https://www.store.leasefoundation.org/cvweb/Portals/ELFA-LEASE/Documents/Products/Metcalf_article.pdf |
[71] |
Singh R, Setiawan AD (2013) Biomass energy policies and strategies: Harvesting potential in India and Indonesia. Renewable Sustainable Energy Rev 22: 332–345. https://doi.org/10.1016/j.rser.2013.01.043 doi: 10.1016/j.rser.2013.01.043
![]() |
[72] |
Viana H, Cohen WB, Lopes D, et al. (2010) Assessment of forest biomass for use as energy. GIS-based analysis of geographical availability and locations of wood-fired power plants in Portugal. Appl Energy 87: 2551–2560. https://doi.org/10.1016/j.apenergy.2010.02.007 doi: 10.1016/j.apenergy.2010.02.007
![]() |
[73] |
Enes T, Aranha J, Fonseca T, et al. (2019) Thermal properties of residual agroforestry biomass of northern portugal. Energies 12: 1418. https://doi.org/10.3390/en12081418 doi: 10.3390/en12081418
![]() |
[74] |
Monjardino J, Dias L, Fortes P, et al. (2021) Carbon neutrality pathways effects on air pollutant emissions: The Portuguese case. Atmosphere 12: 324. https://doi.org/10.3390/atmos12030324 doi: 10.3390/atmos12030324
![]() |
[75] |
Pinto LC, Sousa S, Valente M (2022) Forest bioenergy as a land and wildfire management tool: Economic valuation under different informational contexts. Energy Policy 161: 112765. https://doi.org/10.1016/j.enpol.2021.112765 doi: 10.1016/j.enpol.2021.112765
![]() |
[76] |
Skulska I, Duarte I, Rego FC, et al. (2020) Relationships between wildfires, management modalities of community areas, and ownership types in pine forests of mainland Portugal. Small-Scale For 19: 231–251. https://doi.org/10.1007/s11842-020-09445-6 doi: 10.1007/s11842-020-09445-6
![]() |
[77] |
Novais A, Canadas MJ (2010) Understanding the management logic of private forest owners: A new approach. For Policy Econ 12: 173–180. https://doi.org/10.1016/j.forpol.2009.09.010 doi: 10.1016/j.forpol.2009.09.010
![]() |
[78] |
Feliciano D, Bouriaud L, Brahic E, et al. (2017) Understanding private forest owners' conceptualisation of forest management: Evidence from a survey in seven European countries. J Rural Stud 54: 162–176. https://doi.org/10.1016/j.jrurstud.2017.06.016 doi: 10.1016/j.jrurstud.2017.06.016
![]() |
[79] |
Martins F, Moura P, de Almeida AT (2022) The role of electrification in the decarbonization of the energy sector in Portugal. Energies 15: 1759. https://doi.org/10.3390/en15051759 doi: 10.3390/en15051759
![]() |
[80] | Faria C, Nunes LJR, Azevedo SG (2016) Portugal as a producer of biomass fuels for power production: An analysis of logistics costs associated to wood pellets exportation. 2016 51st International Universities Power Engineering Conference (UPEC), IEEE. https://doi.org/10.1109/UPEC.2016.8113991 |
[81] |
Monteiro E, Mantha V, Rouboa A (2012) Portuguese pellets market: Analysis of the production and utilization constrains. Energy Policy 42: 129–135. https://doi.org/10.1016/j.enpol.2011.11.056 doi: 10.1016/j.enpol.2011.11.056
![]() |
[82] |
Proskurina S, Junginger M, Heinimö J, et al. (2019) Global biomass trade for energy—Part 2: Production and trade streams of wood pellets, liquid biofuels, charcoal, industrial roundwood and emerging energy biomass. Biofuels Bioprod Biorefin 13: 371–387. https://doi.org/10.1002/bbb.1858 doi: 10.1002/bbb.1858
![]() |
[83] |
Nunes LJR, Matias JCO, Catalao JPS (2016) Wood pellets as a sustainable energy alternative in Portugal. Renewable Energy 85: 1011–1016. https://doi.org/10.1016/j.renene.2015.07.065 doi: 10.1016/j.renene.2015.07.065
![]() |
[84] |
Sirous R, da Silva FJN, da Cruz Tarelho LA, et al. (2020) Mixed biomass pelleting potential for Portugal, step forward to circular use of biomass residues. Energy Rep 6: 940–945. https://doi.org/10.1016/j.egyr.2020.01.002 doi: 10.1016/j.egyr.2020.01.002
![]() |
[85] | Lins C, Williamson LE, Leitner S, et al. (2014) The first decade: 2004–2014: 10 years of renewable energy progress. Renewable Energy Policy Network for the 21st Century. Available from: http://hdl.handle.net/10453/117208. |
[86] |
Van der Stelt MJC, Gerhauser H, Kiel JHA, et al. (2011) Biomass upgrading by torrefaction for the production of biofuels: A review. Biomass Bioenergy 35: 3748–3762. https://doi.org/10.1016/j.biombioe.2011.06.023 doi: 10.1016/j.biombioe.2011.06.023
![]() |
[87] |
Nunes LJR, Matias JCO (2020) Biomass torrefaction as a key driver for the sustainable development and decarbonization of energy production. Sustainability 12: 922. https://doi.org/10.3390/su12030922 doi: 10.3390/su12030922
![]() |
[88] |
Nunes LJR (2020) A case study about biomass torrefaction on an industrial scale: Solutions to problems related to self-heating, difficulties in pelletizing, and excessive wear of production equipment. Appl Sci 10: 2546. https://doi.org/10.3390/app10072546 doi: 10.3390/app10072546
![]() |
[89] |
Ribeiro JMC, Godina R, Matias JCO, et al. (2018) Future perspectives of biomass torrefaction: Review of the current state-of-the-art and research development. Sustainability 10: 2323. https://doi.org/10.3390/su10072323 doi: 10.3390/su10072323
![]() |
[90] |
Malico I, Pereira RN, Gonçalves AC, et al. (2019) Current status and future perspectives for energy production from solid biomass in the European industry. Renewable Sustainable Energy Rev 112: 960–977. https://doi.org/10.1016/j.rser.2019.06.022 doi: 10.1016/j.rser.2019.06.022
![]() |
[91] |
Nunes LJR, Matias JCO, Catalão JPS (2014) A review on torrefied biomass pellets as a sustainable alternative to coal in power generation. Renewable Sustainable Energy Rev 40: 153–160. https://doi.org/10.1016/j.rser.2014.07.181 doi: 10.1016/j.rser.2014.07.181
![]() |
[92] |
Viswanathan K, Abbas S, Wu W (2022) Syngas analysis by hybrid modeling of sewage sludge gasification in downdraft reactor: Validation and optimization. Waste Manage 144: 132–143. https://doi.org/10.1016/j.wasman.2022.03.018 doi: 10.1016/j.wasman.2022.03.018
![]() |
1. | Na Pang, Nonlinear neural networks adaptive control for a class of fractional-order tuberculosis model, 2023, 20, 1551-0018, 10464, 10.3934/mbe.2023461 |
SO(Ci) | SOred(Ci) | |
C1 | 3√10 | 6 |
C2 | 4√17 | 12 |
C3 | 2√2(n−5)+2√10+√13+√5 | √2(n−5)+5+√5 |
C4 | 2√2(n−6)+3(√17+√5) | √2(n−6)+10+√10 |
C5 | 4√10+3√2 | 2√2+8 |
C6 | 2√10+3√17+5 | √13+13 |