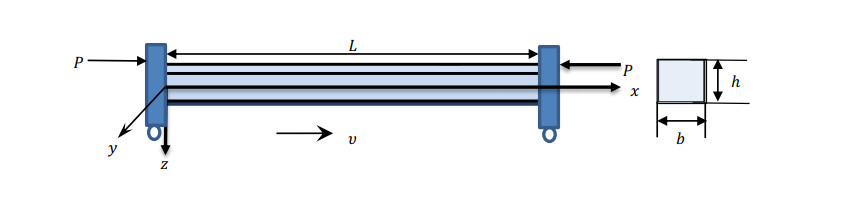
Citation: Yuriy Stoyan, Georgiy Yaskov, Tatiana Romanova, Igor Litvinchev, Sergey Yakovlev, José Manuel Velarde Cantú. Optimized packing multidimensional hyperspheres: a unified approach[J]. Mathematical Biosciences and Engineering, 2020, 17(6): 6601-6630. doi: 10.3934/mbe.2020344
[1] | Yuanyuan Huang, Yiping Hao, Min Wang, Wen Zhou, Zhijun Wu . Optimality and stability of symmetric evolutionary games with applications in genetic selection. Mathematical Biosciences and Engineering, 2015, 12(3): 503-523. doi: 10.3934/mbe.2015.12.503 |
[2] | Jinhan Liu, Lin Zhang . Strain-induced packing transition of Ih Cun@Ag55-n(n = 0, 1, 13, 43) clusters from atomic simulations. Mathematical Biosciences and Engineering, 2020, 17(6): 6390-6400. doi: 10.3934/mbe.2020336 |
[3] | K. Renee Fister, Jennifer Hughes Donnelly . Immunotherapy: An Optimal Control Theory Approach. Mathematical Biosciences and Engineering, 2005, 2(3): 499-510. doi: 10.3934/mbe.2005.2.499 |
[4] | Shuo Wang, Heinz Schättler . Optimal control of a mathematical model for cancer chemotherapy under tumor heterogeneity. Mathematical Biosciences and Engineering, 2016, 13(6): 1223-1240. doi: 10.3934/mbe.2016040 |
[5] | Rong Zheng, Heming Jia, Laith Abualigah, Shuang Wang, Di Wu . An improved remora optimization algorithm with autonomous foraging mechanism for global optimization problems. Mathematical Biosciences and Engineering, 2022, 19(4): 3994-4037. doi: 10.3934/mbe.2022184 |
[6] | YoungSu Yun, Mitsuo Gen, Tserengotov Nomin Erdene . Applying GA-PSO-TLBO approach to engineering optimization problems. Mathematical Biosciences and Engineering, 2023, 20(1): 552-571. doi: 10.3934/mbe.2023025 |
[7] | Zilong Zhuang, Zhiyao Lu, Zizhao Huang, Chengliang Liu, Wei Qin . A novel complex network based dynamic rule selection approach for open shop scheduling problem with release dates. Mathematical Biosciences and Engineering, 2019, 16(5): 4491-4505. doi: 10.3934/mbe.2019224 |
[8] | Andrzej Swierniak, Jaroslaw Smieja . Analysis and Optimization of Drug Resistant an Phase-Specific Cancer. Mathematical Biosciences and Engineering, 2005, 2(3): 657-670. doi: 10.3934/mbe.2005.2.657 |
[9] | Haiquan Wang, Hans-Dietrich Haasis, Menghao Su, Jianhua Wei, Xiaobin Xu, Shengjun Wen, Juntao Li, Wenxuan Yue . Improved artificial bee colony algorithm for air freight station scheduling. Mathematical Biosciences and Engineering, 2022, 19(12): 13007-13027. doi: 10.3934/mbe.2022607 |
[10] | Hongmin Chen, Zhuo Wang, Di Wu, Heming Jia, Changsheng Wen, Honghua Rao, Laith Abualigah . An improved multi-strategy beluga whale optimization for global optimization problems. Mathematical Biosciences and Engineering, 2023, 20(7): 13267-13317. doi: 10.3934/mbe.2023592 |
In recent decades, nano-electromechanical systems (NEMS) technology has significantly progressed [1]. Nanoscale structural materials used in NEMS, like nanobeams, nanoplates, and nanoshells, have better properties, so researchers in this field pay a lot of attention to studying their mechanical and physical properties [2]. Vibration at nanoscales, which is highly size-dependent, is still a mystery despite the existence of well-established classical theories of linear and nonlinear vibration of strings and beams. The resonance of a nanobeam is examined here using nonlocal elastic stress theories in an effort to expand the classical theory of size-dependent nanomechanics [3].
Microstructural engineering problems can be addressed using the standard local theories of continuum mechanics and flexibility from civil, mechanical, and bioengineering engineering fields. The classical-local continuum framework is predicated on the idea that stress and strain are correlated at every point in space and time. Elastic wave spreading, crack propagation, and dislocations are extensively studied in the traditional theory of elasticity. Conventional elastic models, on the other hand, are useless for studying these processes in real-time at the atomic and subatomic scales [4].
The distance between atoms has little effect on classical continuum theory; nonetheless, it becomes significant when the model size is reduced. Several investigators have thus constructed classical continuum mechanics to represent the size effect. These advancements have been dubbed non-classical (higher-order) elasticity theories. So-called nonlocal beams are a subcategory of beam structures that are distinguished by applying the nonlocal elasticity constitutive equation to take into account the small-scale effects. Because of the nanoscale dimensions of their formations, nonlocal beams of this kind are typically referred to as nanobeams in the scientific literature [5]. Several theories that emphasize small-scale influences have been created, including the strain gradient concept [6,7], modified couple stress theory [8,9], couple stress elasticity model [10,11], and nonlocal elasticity theory [12,13,14].
The nonlocal theories are often based on Eringen's nonlocal elasticity theory [12,13,14], which is the most widely used. Based on Eringen's hypothesis of nonlocal elasticity, stress at any situation point affects the entire body. It depends not only on strains at this point but also on strains throughout the body. The formulation of nonlocal Eringen elasticity focuses on the atomic theory of lattice dynamics and some experimental evidence for phonon scattering. As a result, the object's size affects the results of the nonlocal theory, which considers long-range interactions between atoms [12,13,14].
The nonlocal elasticity model has been used to investigate many applications in nano-mechanics, such as lattice propagation of transverse waves, vibration in nanomaterials, deformation mechanics, fracture mechanics, compressive fluids, and others [15]. Due to their mechanical properties, the greatest attention has been paid to nanotubes and nanobeams. Peddiesion et al. [16] initially constructed the nonlocal Euler-Bernoulli (EB) beam equations in order to analyze the static behavior of MEMS cantilever actuators utilizing Eringen's nonlocal differential form. Simultaneously, Wang [17] outlined the conditions under which a Carbon nanotube (CNT) may be described as a beam based on its dimensions. These studies prompted nonlocal differential beam theories on CNTs and nanobeams to analyze their stationary, dynamic, and buckled attitudes and behaviors. Abouelregal and Marin [18] presented a nonlocal thermal model that shows how the nanobeams move and change shape. Eringen's theory of nonlocal elasticity as well as generalized thermoelastic theory is used to derive the equations governing the nonlocal nanobeams. In this paper, the structure of the nanobeam is affected by external harmonic forces and temperature changes caused by the heating of a modified sine wave. A generalized kernel function for memory-based derivatives with two-time lags was proposed by Abouelregal et al. [19,20] as a theoretical model for analyzing the nonlocal heat conduction model. The thermomechanical reaction of spinning size-dependent nanobeams is the focus of the new model. The nonlocal elasticity theories and the extended heat transfer model with phase lags are used in the mathematical formulation. Bian and Qing [21] have created a new framework for the Finite Element Method (FEM) in order to simulate the mechanical interactions of an Euler-Bernoulli beam using a nonlocal and nonlocal two-phase mixed model at the same time. In this work, a fifth-degree polynomial was used for the model function, and the constitutive boundary conditions (CBCs) were treated the same way as the external loads. Scorza et al. [22] introduced a study that aims to extend the two-phase local/nonlocal stress-driven integral system (SDM) to the situation of nanobeams with internal discontinuities. In point of fact, the initial formulation attempts to avoid the existence of any discontinuities in the structure. The thermal buckling of an anisotropic flexible composite beam with a dielectric core and two thin semiconducting surface layers was recently modeled by Zhang et al. [23]. From the kinematic relations for a Timoshenko beam and the concepts of piezoelectricity, flexoelectricity, strain gradient elasticity, and semiconductors, we derive the system of equations and boundary conditions for the beam.
Many researchers have come up with the term "axially moving nanostructures" to describe how axially moving continuums work in many structural applications, such as band saws, printing mechanisms, tubes carrying fluids, etc. [24,25] Since the 1950s, scientists have been studying how materials vibrate when they move in one direction. Through many efforts, the first papers were presented on the vibration of the thread moving along it [26,27]. In recent decades, many research articles have been published about beams, plates, and shells that move in one direction [28,29,30].
The temperature of the body changes as a result of the body's deformation. The temperature of the body changes, and the body deforms when a heat source is applied from outside. Consequently, deformation and temperature affect the body's inner energy. Thermoelasticity looks at how stress, stain, and deformation are linked to heat source and time. The goal is to find a formula that describes how stress, stain, and deformation change over time. According to research, this theory can be applied to various engineering fields and advanced technologies, from acoustics to aeronautical engineering to chemical engineering. It can also be used to check the strength, stiffness, and stability of a structure or system parts and the elastic limit of a structure or machine [31].
The linear theory of linked thermoelasticity was first satisfactorily derived by Biot [32]. Later, Chadwick [33] published both linear and nonlinear formulations of the concept and solved several significant linear dynamic system issues. Coupled thermoelasticity has been expanded to include more types of materials, such as micro elastic materials, electromechanical solids, and viscoelastic solid particles, among others. The conventional uncorrelated thermoelasticity hypothesis predicts two events that are incompatible with physical phenomena. First, this heat transfer theory equation does not include any elastic factors, even though elastic changes create thermal effects. Second, the equation for thermal conductivity is of the parabolic type, which indicates that heat waves will propagate at an infinite rate within the medium. To address this dilemma, several efforts have been made to change the coupled concept of thermal elasticity in order to obtain a wave-type heat transfer formula. Some of the most well-known generalized thermoelastic concepts and theories include the Lord and Shulman (LS) model [34], the Green and Lindsey theory (G-L) [35], as well as the Green and Naghdi (GN) [36,37] theories, which were developed with the help of the energy equation. Also, the dual-phase lag (DPL) model [38,39] was introduced by Tzou.
Non-Fourier transient heat transport in a two-dimensional sub-100 nm metal-oxide-semiconductor field-effect transistor was the subject of research by Ghazanfarian and Shomali [40], who used numerical simulation to examine the phenomenon (MOSFET). Zhou et al. [41] constructed one/two-dimensional (1D/2D) TED models of rings by using the nonlocal dual-phase-lag (DPL) framework and the modified-couple-stress (MCS) concept. In order to represent heat transfer on the nanoscale, the dual-phase-lag (DPL) model is presented together with a tailored normalizing approach. Zhang and He [42] studied the dynamic behavior of a limited thermoelastic rod fixed at both ends and exposed to a moving heat source within the context of the extended thermoelasticity with nonlocal influence and memory-dependent derivative. Laplace transformation and numerical inversion are used to develop and solve the associated governing equations. In [43], Zhang et al. used a two-phase local/nonlocal mixture theory of strain- and stress-driven types to propose predictive models of the free vibration of Euler-Bernoulli beams in a uniformly heated environment. With the help of Hamilton's principle, we are able to derive the equation of motion and the conventional boundary conditions, and the constitutive equation is written in local/nonlocal mixed integral form using a bi-Helmholtz kernel.
Considering the effects of size and heat variations on softening hardness and elastic strengthening patterns in moving nano and nanostructures, the investigation into continuous size-dependent concepts, generalized heat conduction, and mass mechanisms of thermoelastic responses is still lacking, according to the aforementioned overview. To the author's knowledge, no one has ever investigated the thermoelastic resonances in nanobeams under external transversal excitation, non-localization, and thermomechanical influences using the generalized theory of thermoelasticity. The research aims to investigate how the nanoscale and longitudinal speed influence the various beam behaviors.
This work aims to present a governing system of equations that describe nonlocal thermoelastic moving Euler-Bernoulli beams that are excited from the outside in a transverse direction. When considering the nonlocal scale implications in the nanobeam resonances, the novel size-dependent thermoelastic model is based on Eringen's hypothesis of nonlocal elasticity and the DPL heat transfer model. Differential motion equations were also derived from the Euler-Bernoulli nanobeam theory, based on the generalized Hamiltonian concept. The Laplace transform and its inversion are used in the deductive process. The effects of nonlocal phase lags, moving speed, and external excitation will be studied and graphically depicted.
Consider an Euler-Bernoulli nanobeam of length L that has an initial axial tension P at either end. In Figure 1, we have a schematic diagram of a nanobeam moving at a constant horizontal velocity υ. Initially, the body is in equilibrium such that the beam is not restricted in any way, is not subject to any pressure, and maintains the same temperature T0. When the beam is bent around the x -axis, small-amplitude vibrations occur, which allow the deflection to be described using the linear Euler-Bernoulli hypothesis of mechanics. During bending, any plane cross-section initially parallel to the beam axis stays parallel to the reference plane and perpendicular to the plane. This means that the displacements can be expressed as
u=−z∂w∂x, v=0, w(x,y,z,t)=w(x,t), | (2.1) |
where w denotes the transverse displacement.
It is possible to establish the governing equation for nanobeam transverse vibration by employing Hamilton's principle. By applying Newton's second law of motion and the condition of moment equilibrium, one can derive the dynamic equation of motion for the element that is subject to an axial dynamic load P. This equation of motion may be written as [44,45]
∂2M∂x2+m(∂2w∂t2+2υ∂2w∂x∂t+υ2∂2w∂x2)+P∂2w∂x2=0, | (2.2) |
M(x,t) represents the bending moment, m=ρA is mass per unit length, ρ is the density, and A represents the cross-sectional area.
The components of the local stress and strain tensors are given by
τkl=λεmmδkl+μεkl−γδklθ, | (2.3) |
2εkl=∂uk∂xl+∂ul∂xk, | (2.4) |
where uk are the displacement vector components, τkl are the local stress tensor components. Also, θ=T−T0 is the of temperature change, T is the temperature distribution, T0 is the environmental temperature, εkl are the classical Cauchy relations, λ and μ are Lamé's constants, γ=αt(3λ+2μ)=Eαt/(1−2ν), αt is the coefficient of thermal expansion, E denotes Young modulus, ν is Poisson's ratio and δkl is Kronecker delta function. The Lamé constants λ and μ can be expressed as λ=Eν/(1+ν)(1−2ν) and μ=E/2(1+ν).
The dynamic study of the nanostructure is done using a nonlocal stress model. The basic equations of Eringen's nonlocal elasticity theory [12,13,14] incorporate spatial integrals that reflect the weighted averages of the contributions of associated strain tensors at the corresponding location in the body. As a result, the theory employs a spatial integral constitutive correlation to incorporate the small-size scale effect. The integral form of the nonlocal constitutive relation can be represented as follows in nonlocal elasticity theory:
σkl(x)=∫τkl(x′)Kξ(|x−x′|,ξ)dV(x′),∀x∈V, | (2.5) |
where σkl are the nonlocal stress tensor components at any point x, Kξ(|x−x′|,ξ) represents the attenuation function (kernel) which includes nonlocal influences into the constitutive relations, |x−x′| is a distance in Euclidean norm and ξ=(e0a)2 is the nonlocal parameter where a is the intrinsic property length (characteristic internal length) and e0 is a material constant that can be determined from molecular dynamics simulations or by using the dispersive curve of the Born-Karman model of lattice dynamics. Eringen [12,13,14] provided a differential form of constitutive equations by using an appropriate kernel function Kξ in the preceding integral form of the equation can be derived as [46]
σkl−ξ∂2σkl∂x2=τkl. | (2.6) |
According to Eringen's nonlocal elasticity theory, the one-dimensional nonlocal constitutive relation can be written as [47,48]
σx−ξ∂2σx∂x2=−E(z∂2w∂x2+αTθ), | (2.7) |
where σx represents the nonlocal axial stress, E is Young's modulus, αT=αt/(1−2ν) and θ=T−T0 indicates the over-temperature distribution.
The bending moment may be calculated using the Euler-Bernoulli beam theory as follows:
M(x,t)=b∫h/2−h/2σxzdz. | (2.8) |
When the of the axial stress σx is multiplied by z and integrated across the cross-section area of the nanobeam, the flexure moment satisfies the following equation:
M(x,t)−ξ∂2M∂x2=−EI(∂2w∂x2+αTMT), | (2.9) |
where I=bh3/12 is the moment of inertia and MT denotes the thermal moment which is obtained by
MT=12h3∫h/2−h/2θ(x,z,t)zdz. | (2.10) |
Equation (2.2) may be substituted into Eq (2.9), yielding the following equation of the flexure moment:
M(x,t)=−ξm(∂2w∂t2+2υ∂2w∂x∂t+υ2∂2w∂x2+Pm∂2w∂x2)−EI(∂2w∂x2+αTMT). | (2.11) |
Equation (2.2) can be represented as a nonlocal partial differential equation with a constant coefficient of the lateral displacement w(x,t) by substituting Eq (2.11) into Eq (2.2):
(1+ξmυ2EI)∂4w∂x4+[(mEI∂2∂t2+2υmEI∂2∂x∂t+PEI∂2∂x2)(ξ∂2∂x2−1)]w−mυ2EI∂2w∂x2+αT∂2MT∂x2=0. | (2.12) |
When ξ=0 is used in the preceding equations, the relevant local equation of motion for moving the Euler-Bernoulli beam is restored.
Tzou [38,39] suggested a dual-phase-lag (DPL) model that ignores the instantaneous interaction of temperature and energy. The DPL model, in particular, provides a straightforward and realistic representation of heat transmission in skin tissues. The DPL model has also been applied to describethe thermal response to laser transmission, thermal shock, and photothermal excitement. Also, this theory is built logically to generate a coherent theory that can logically contain thermal pulse excitation. Tzou's theory is a modified version of the conventional thermoelasticity model in which the Fourier law is substituted with an approximation of the following equation [38]:
→q(x,t+τq)=−K∇θ(x,t+τθ), | (2.13) |
where →q denotes the heat flux vector, and K symbolizes the thermal conductivity. The phase lag of the heat flow is τq, while the temperature gradient's phase lag is τθ.
The modified heat conduction equation for the DPL model may be expressed by using the first-order approximation of the previous equation as
(1+τq∂∂t)→q=−K∇(1+τθ∂∂t)θ. | (2.14) |
The equation for the conservation of energy is written as follows:
CE∂θ∂t+γT0∂e∂t=−∇·→q+Q, | (2.15) |
where CE denotes the specific heat per unit mass at constant strain, e=∇·→u represent the cubical dilatation, →u is the displacement vector, and Q signifies the internal energy generation (heat source).
When Eqs (2.14) and (2.15) are combined, we get the DPL heat conduction model as
(1+τq∂∂t)(ρCE∂θ∂t+γT0∂e∂t−Q)=K(1+τθ∂∂t)∇2θ. | (2.16) |
One can use Eq (2.1) to get the DPL heat equation for the current situation in the absence of a heat generation (Q=0) as
(1+τθ∂∂t)∂2θ∂x2+(1+τθ∂∂t)∂2θ∂z2=(1+τq∂∂t)[ρCEK∂θ∂t−γT0Kz∂∂t(∂2w∂x2)]. | (2.17) |
The DPL model simplifies the traditional Fourier's law when τq=0=τθ. Also, the Lord and Shulman thermoelastic model can be obtained when τθ and τq>0.
Assume that the temperature increment θ(x,z,t) increases sinusoidally (sin(πz/h)) along the thickness direction for an extremely nanobeam. Furthermore, there is no heat movement along the upper and bottom surfaces of the nanobeam, resulting in ∂θ∂z=0 at z=±h2. In this case,
MT=12h3∫h/2−h/2θzdz=12hπ2[θ|h/2−h/2−z∂θ∂z|h/2−h/2]=−12hπ2∫h2−h2∂2θ∂z2zdz. | (2.18) |
Substituting Eq (2.18) into (2.17) leads to
(1+τθ∂∂t)[∂2MT∂x2−π2h2MT]=(1+τq∂∂t)[ρCEK∂MT∂t−βT0π2h24K∂∂t(∂2w∂x2)]. | (2.19) |
To help with the solution, the dimensionless variables listed below are used:
(x′,L′,u′,w′,z′)=ηc(x,L,u,w,z),Θ′=ΘT0,σ′x=σxE,M′T=MTEAh,υ′=υc,M′=−MηcEI,(t′,t′0,τ′q,τ′θ)=ηc2(t,t0,τq,τθ),η=ρCEK,c=√Eρ. | (2.20) |
Applying the dimensionless values from (2.20) to Eqs (2.11)-(2.12) and (2.19), and then suppressing the primes for convenience, we obtain
M(x,t)=ξ(∂2w∂t2+2υ∂2w∂x∂t+υ2∂2w∂x2+P∂2w∂x2)+∂2w∂x2+24T0αThπ2MT. | (2.21) |
(1+ξυ2)∂4w∂x4+12h2[(∂2∂t2+2υ∂2∂x∂t+P∂2∂x2)(ξ∂2∂x2−1)]w−12υ2h2∂2w∂x2+24T0αThπ2∂2MT∂x2=0. | (2.22) |
(1+τθ∂∂t)[∂2MT∂x2−π2h2MT]=(1+τq∂∂t)[∂MT∂t−EαTπ2h24ηK∂3w∂t∂x2]. | (2.23) |
When the two ends of the microbeams are simply supported and kept at a sinusoidal temperature with a pulse width t0 at the first end (x=0) while the second end (x=L) is insulated, the boundary conditions are given by the expression:
w(x,t)=0,M(x,t)=0 at x=0,L, | (2.24) |
θ=θ(z,t)=θ0z sin(πt0t),0≤t≤t0 on x=0, | (2.25) |
∂θ∂x=0 at x=0,L | (2.26) |
Inserting Eqs (2.25) and (2.26) into Eq (2.10) leads to
MT=M0 sin(πt0t), 0≤t≤t0 on x=0, | (2.27) |
∂MT∂x=0 at x=0,L | (2.28) |
Most earlier investigations assumed that the transverse excitation axial force was either non-existent or fixed. Actually, the axial force can change over time. It is supposed that the dimensionless transverse excitation axial tension is a time-dependent function as [1]
P=Ps+PD cos(ωt). | (2.29) |
This equation uses ω to represent the frequency of the load and the terms " Ps " and " PD "to express the static and dynamic components of axial force.
Nonlinear differential equations are notoriously difficult to solve analytically, especially in their closed-form form. Many different numerical and approximation methods have been used in the literature to solve this problem. One can consider the following as initial conditions:
w(x,t)|t=0=0=∂w(x,t)∂t|t=0, MT(x,t)|t=0=0=∂MT(x,t)∂t|t=0. | (3.1) |
When the Laplace transform technique is applied to Eqs (2.7)-(2.13), one obtains the transformed differential equations that are shown below:
−M=(1+ξυ2+ξ−P)d2−wdx2+2υsξd−wdx+ξs2−w+24T0αThπ2−MT, | (3.2) |
d4−wdx4+A3d3−wdx3+A2d2−wdx2+A1d−wdx+A0−w=−B1d2−MTdx2, | (3.3) |
−A4d2−wdx2=(d2dx2−B2)−MT, | (3.4) |
where
A0=12s2h2(1+ξυ2+ξ−P),A1=2υA0s,A2=A0(s2ξ−υ2−−P),A3=2υξA0s,B1=24T0αTπ2h(1+ξυ2+ξ−P),B2=π2h2+s(1+τqs)1+τθs,A4=sγπ2h(1+τqs)24Kη(1+τθs),−P=Pss+sPDs2+ω2. | (3.5) |
By eliminating −w or −Θ from Eqs (3.3) and (3.4), the differential equation governing the functions −w and −Θ may be found.
[a6d6dx6+a5d5dx5+a3d4dx4+a3d3dx3+a2d2dx2+a1ddx+a0]{−w,−Θ}, | (3.6) |
where
a5=A3,a4=A2−B1A4, a3=A1−B2A3,a2=A0−B2A2,a1=−B2A1,a0=−B2A0. | (3.7) |
The solution to the Eq (3.6) may be written as
{−w,−MT}=∑6i=1{Ci,C′i}emix, | (3.8) |
where Ci and C′i are the integral constants and the parameters mi(i=1,2,...,6) are the roots of the equation
m6+a5m5+a4m4+a3m3+a2m2+a2m+a0=0. | (3.9) |
The compatibility between Eqs (3.8) and (3.4) gives
C′i=βiCi, βi=−A4m2im2i−B2. | (3.10) |
Substituting Eq (3.8) into Eq (2.1) after applying the Laplace transform, we get the displacement ˉu as follows:
ˉu=∑6i=1miCiemix. | (3.11) |
The bending moment −M given in Eq (3.2) with the help of Eq (3.8), takes the form
−M(x,t)=∑6i=1(υ2ξm2i+m2i+2υsξmi+ξs2+24T0αThπ2βi)Ciemix. | (3.12) |
The boundary conditions (2.24), (2.27) and (2.28) are as follows when the Laplace transformation
−w(x,s)|x=0,L=0,d−w(x,s)dx|x=0,L=0,−Θ(x,s)|x=0=πt0π2+t20s2=ˉG(s),d−Θ(x,s)dx|x=L=0. | (3.13) |
Substituting Eq (3.8) into the boundary mentioned above conditions yields six linear equations in matrix form as
∑6i=1emiLCi=0,∑6i=1miCi=0,∑6i=1miemiLCi=0,∑6i=1Ci=0,∑6i=1βiCi=ˉG(s),∑6i=1βimiemiLCi=0. | (3.14) |
The unknown parameters Ci(i=1,2,...,6) are obtained from the solution of the preceding system of linear equations. This concludes the solution to the issue in the domain of the Laplace transform.
To calculate the studied physical domains such as bending moment distributions, temperature, displacement, and pressure in the beam, the Laplace domains must be reversed to the time domain. However, these solutions are too complex to be directly inverted; therefore, no direct analytic solutions can be obtained. Consequently, the Riemann-sum approximation approach is employed to generate numerical results. In this approach, any function −f(x,t) in the Laplace domain may be inverted into the time domain as [38]
f(x,t)=eωtt[12Re[ˉF(x,ω)]+Re∑Nφ=0(ˉF(x,ω+iφπt)(−1)n)]. | (4.1) |
The influence of many elements, including the nanobeam's flexural stiffness, axial speed, phase delays, the static and dynamic parts of its axial force, and its vibration properties, was investigated using numerical computations. The non-dimensional investigated variables in the nanobeam are obtained by computational Laplace inversion using the Riemann-sum approximation stated in Eq (4.1). This study uses a silicon beam to examine the thermoelastic interaction behavior. The following are the physical values related to silicon [18,20]:
E=169GPa,ρ=2330kg/m3,CE=713J/(kgK),T0=293K, |
αT=2.59×10−6K−1,ν=0.22,K=156W/(mK). |
The numerical values of the studied non-dimensional domains were calculated, and graphs were generated using the dimensional physical values mentioned above. Based on the dimensionless values of the physical quantities, the beam lengths of L=10h=1, b=h/2, z=h/6, and t=0.12 are considered. The distributions of the thermal moment MT, Lateral vibration w, bending moment M, and axial displacement u domains are graphically represented for the x, and z directions by inverting Laplace transforms using Eq (4.1). The following three cases are numerically calculated and discussed.
Calculations were made to determine the numeric data of the non-dimensional research fields under investigation, and graphs were constructed based on the previous physical values. The dimensions of the nanobeam are considered to be L=10h=1, b=h/2, and t=0.12. By transposing the Laplace transforms with the help of Eq (4.1), the patterns of the thermal moment MT, lateral vibration w, bending moment M, and axial deformation u domains have been graphically displayed for the x axis at z=h/6. The following important situations are analyzed using figures and then highlighted.
The so-called nonlocal beams are a subcategory of beam structures characterized by applying the constitutive equation of nonlocal elasticity in order to account for small-scale influences. In published studies, these types of nonlocal beams are often called "nanobeams" because their structures lie on nanoscale dimensions. Due to its inherent length-free construction, the conventional continuum mechanics technique is not applicable at the nano-length scale. The small-scale effects and long-distance behavior in nanomechanical systems cannot be ignored the way they can be ignored in macroscopic mechanical systems.
Experiments on their mechanical characteristics have indicated a size effect that is not observable at the macroscale. This impact becomes more pronounced when the dimensions of the nanoscale structure approach those of the microstructure. Therefore, studying the size influence on the dynamic responses of axially moving nanoscale beams employing suitable models is essential to designing such structural systems.
In this section, a nonlocal continuum model will be used to figure out how nanobeams behave differently depending on their size. The effect of the dimensionless nonlocal factor ξ on the lateral vibration w amplitude, the thermal moment of inertia MT, displacement u, and bending moment M for a range of different values will be examined. These different effects are illustrated by introducing Figures (2)-(6). It can be seen that the local thermoelastic model is represented by the value ξ=0, while the other values (ξ=0.001 and 0.003) are represented by the nonlocal thermoelastic theory. In this case, it is assumed that the pulse width parameter (t0=0.1) and the delay phase coefficients τq=0.2 and τθ=0.15 remain constant. Also, the dimensionless transfer velocity of the nanobeam is also assumed to be constant (υ=1.2).
Figure 2 depicts the variations in thermal deflection w. The graphic depicts the lateral deflection pattern w, which always begins at zero (i.e., vanishes) and satisfies the problem's boundary condition at the edges x=0 and L. We also discovered that the deflection w reaches its maximum value at a specific distance from the nanobeam edge and then decreases as the distance x increases. As depicted, increasing the value of the nonlocal factor decreases the wave propagation rate of the lateral deflection w and causes it to vanish more rapidly. Compared with the results produced by standard vibration theory, the nonlocal effect results in more intense vibration signals.
In Figure 3, we can see the effect of changing the nonlocal factor ξ on the thermal moment MT of a moving nanobeam while it is subjected to a time-varying external axial force. The thermal moment MT is shown to be relatively insensitive to variations in the nonlocal parameter (see Figure 3). Observably, the nonlocal parameter appears to have minimal effect on the nanobeam's thermal moment. Moreover, moving away from the heat source in the direction of the spread of the heat wave causes the thermal moment MT to drop significantly as the distance x grows (see Figure 4).
Contrary to the expectations of standard continuum models, actual findings have shown that size effects have a major impact on the physical properties and mechanical responses of NEMS at the nanoscale [49,50]. The influence of the small scale on lattice dynamics depends on the crystal structure and the sort of material science being examined [51]. Unlike discrete microscopic or molecular dynamical simulations, which require much computer work, this continuum theory can be used to model submicron or nanoscale structures [52].
Figure 4 shows the variations in axial displacement u over the interval x∈[0,1] at a very short time t=0.12, for nonlocal moduli ξ=0, 0.001, and 0.003. As can be seen in the graph, the displacement u begins with negative values and grows in amplitude as the beam length increases. It is clear that as the nonlocal factor ξ is increased, the displacement u grows in the interval x∈[0,0.4] and shrinks in the region x∈[0.4,1]. Additionally, the graph clearly shows that the split between local and nonlocal thermoelastic concepts persists.
Figure 5 depicts how the bending moment changes as a function of the nonlocal component, which is dimensionless. Figure 5 shows that the nanobeam's bending moment varies as a function of distance from its ends, starting at zero at, and increasing steadily to a maximum some distance from the beam's ends before decreasing back to zeroat. As seen in Figure 5, the bending moment is highly sensitive to variations in the nonlocal constant.
Figure 6 depicts how the temperature changes θ along the longitudinal direction as a function of the nonlocal factor ξ. As can be seen, the non-dimensional temperature θ increases to its highest value at x=0 fluctuate along the longitudinal axis, then declines to zero at the end of the nanobeam resonator. The postulated thermal boundary conditions are consistent with this pattern. The non-dimensional temperature increases when the nonlocal factor's value increases.
Once again, it is clear that Eringen's nonlocal theory of elasticity predicts a larger bending moment than the local theory of elasticity. In other words, the nonlocal effects soften the structures, making them more adaptable. Mechanical qualities at the micro and nanoscale should be considered during the construction and design of MEMS and NEMS devices.
The results shown in Figures 2-6 demonstrate that the elastic field is more significantly affected by changes in the small-scale parameter value than the temperature profile. Minor changes in the lateral deflection, coupled with temperature field changes in the extended coupled thermoelasticity of the DPL theory, cause the temperature field's small alterations.
High-velocity cars and trucks, spacecraft antennas, and advanced robotic manipulators can benefit from axially-moving nanoscale beams exceptional mechanical and physical features. Recently, researchers have explored the subject of studying the resonance of an axially moving beam under the influence of an external force. Researchers have examined various practical applications, such as a transmission system, medical nanorobots, power cutting tools, tape cutting tools, and magnetic disks.
In the second scenario, the effects of the vibrational heat pulse on the distribution of the thermal bending moment of the nanobeam are studied. As well as deformation caused by turbulence and bending moment change in addition to stress when changing the axial velocities of the beam. In this case, three different velocity values (υ=1.2, 1.3 and 1.4) will be taken into account if the values of the nonlocal index and the values of the phase lag factors τq and τθ are held constant. In Figures 7-11, the effect of the axial velocity of the beam on the longitudinal vibration response of the fine beams is shown. It is also shown that the different field curves inside the beam are very sensitive to the axial velocity. It can be revealed by looking at the field curves that the amplitudes of thermal and mechanical waves increase with the increase in the axial speed with which the bite is moving. In addition, it is observed in the period x∈[0,0.4], the amounts of distortion decrease with increasing rate while increasing in the region x∈[0.4,1]. With the axial speed of the nanobeam impact, the thermal bending moment is less than it would be without it. As a result, it is clear that the beam's axial velocity significantly impacts the safety design of nanobeams. It is found that the velocity parameter does not have a significant effect on the temperature change.
The axially moving continuum types are paper sheets, drive shafts, fiber textile products, oil and gas pipelines, and various wire and structural steel processing technologies such as straightening lines. Excitations caused by continuously moving materials are what ultimately lead to failure and poor quality. As a consequence of this, the investigation of these vibrations is of utmost significance in the system design. Additionally, good agreement is found between the present results and the documented literature when analyzing the local results of the traveling Euler-Bernoulli nanobeam described in references [53,54]. That being said, the validity of the present findings can be independently confirmed. Thermomechanical disturbances can arise in the nanobeam if it experiences a considerable transverse deformation in the orthogonal direction to the rate [55]. In this way, noise that isn't expected might be introduced, which can reduce the structure's usefulness in some contexts, cause wear and tear on the system, and lower quality overall. During production, these things must be considered to ensure that the nanostructure is not overworked and loses its performance.
Engineers must ensure that axially moving nano-systems do not become unstable and that excessive vibrations are eliminated. System velocity is key in determining axial motion continuation's dynamic response and stability. Different instability mechanisms, such as divergence and flutter, manifest at different system velocities.
When studying and making new NEMS or MEMS systems, it is very important to study the thermodynamic stability of micro or nanostructures when exposed to time-dependent transverse external excitation. In this subsection, we will explore the effect of static (Ps), dynamic (PDcos(ωt)), and amplitude external transverse excitation (P=Ps+PDcos(ωt)) on the responses of the domains considered. The impact of various kinds of external transverse stimulation on all investigated physical fields is depicted in Figures 12-16.
In this case, the values of components of axial force, Ps=0.8 and PD=0.6 are considered, while the angular frequency ω of the employed transverse excitement remains constant (ω=0.3). It is assumed that the nonlocal factor ξ=0.001, the speed of axial motion υ=1.2, the pulse width t0=0.1 and also the parameters τq and τθ stay unchanged in this scenario. The figures show that the behavior of different domains inside the nanobeam is very sensitive to the strength of the axial tension. This effect also depends on the type of this external induction, whether it is static, dynamic, or both. In different cases, the curves of the studied fields exhibit the same behavior with different amounts. From these curves, it is also clear that the static axial external transverse excitation increases the magnitudes of various fields while the dynamic transverse excitation decreases the size of these fields.
This work investigated thermoelastic vibrations in a nanobeam moving axially at a constant speed and subjected to an axial transverse dynamic force. We obtain the linear motion equations by applying Hamilton's principle to the Euler-Bernoulli beam hypothesis. In addition, the thermal part of the problem was addressed by including a two-phase delay in the modified thermoelastic framework (DPL model). An effective method for finding solutions was provided, and it involved using the Laplace transform and a numerical inversion strategy. The influence of several factors, including phase delays, axial translation velocity, nonlocal parameters, statics, and dynamics of the transverse excitation, on the system's response, was examined. The following are the most important conclusions that can be drawn from this investigation:
1) The nonlocal parameter significantly influences all the minimum and maximum values of the different domains. Larger nonlocal parameter values result in an undamped system. In other words, nonlocal effects "soften" the structures, making them more adaptable.
2) Mechanical and thermal vibration studies on such nano-systems are critical to ensuring system integrity and stability. It can also be used to simulate the mechanical properties of basic elements in AMEMS and ANEMS.
3) The presence of a constant motion velocity of the nanobeam leads to large phase shifts in the transverse dynamic profiles, but the effect of the thermal change is negligible. Also, if the velocity increases, the phase gap between the variables of deformation and bending torque should decrease.
4) Unlike conventional models, the two-phase thermoelastic model predicts that waves can only move at a specific speed. This means that the theory of thermal expansion proposed in this article is more in line with how matter works as well as physical phenomena.
5) The behavior of different domains inside the nanobeam is very sensitive to the strength of the axial tension. This effect also depends on the type of this external induction, whether it is static, dynamic, or both.
The current work with axially moving nanobeams has many uses in many areas of science and engineering, such as making and designing some moving structures, civil, structural, and aerospace engineering, and systems engineering. Also, the current study covers systems like belt conveyors, clinical nanorobots, control saws, tape cutting tools, magnetic media, and many others.
The authors extend their appreciation to the Deputyship for Research & Innovation, Ministry of Education, Saudi Arabia for funding this research work through the project number (QU-IF-05-03-26925). The authors also thank to Qassim University for technical support.
The authors declare no conflicts of interest.
[1] | T. Cremer, M. Cremer, Chromosome territories, Cold Spring Harbor Perspect. Biol., 2 (2010), 1-22. |
[2] | A. Raj, Y. Chen, The wiring economy principle: connectivity determines anatomy in the human brain, PLoS ONE, 6 (2011), 1-11. |
[3] | M. Rivera-Alba, S. N. Vitaladevuni, Y. Mishchenko, Z. Lu, S. Takemura, L. Scheffer, et al., Wiring economy and volume exclusion determine neuronal placement in the drosophila brain, Curr. Biol., 21 (2011), 2000-2005. |
[4] | Y. Karklin, E. P. Simoncelli, Efficient coding of natural images with a population of noisy Linear-Nonlinear neurons, Advances in neural information processing systems, 2011. |
[5] |
J. Wang, Packing of unequal spheres and automated radiosurgical treatment planning, J. Comb. Optim., 3 (1999), 453-463. doi: 10.1023/A:1009831621621
![]() |
[6] |
A. Sutou, Y. Day, Global optimization approach to unequal sphere packing problems in 3D, J. Optim. Theory Appl., 114 (2002), 671-694. doi: 10.1023/A:1016083231326
![]() |
[7] |
A. S. Shirokanev, D. V. Kirsh, N. Yu. Ilyasova, A. V. Kupriyanov, Investigation of algorithms for coagulate arrangement in fundus images, Comput. Opt., 42 (2018), 712-721. doi: 10.18287/2412-6179-2018-42-4-712-721
![]() |
[8] | K. Sugihara, M. Sawai, H. Sano, D. Kim, D, Kim, Disk packing for the estimation of the size of a wire bundle, Jpn. J. Ind. Appl. Math., 21 (2004), 259-278. |
[9] |
K. A. Dowsland, M. Gilbert, G. Kendall, A local search approach to a circle cutting problem arising in the motor cycle industry, J. Oper. Res. Soc., 58 (2007), 429-438. doi: 10.1057/palgrave.jors.2602170
![]() |
[10] |
Y. Cui, D. Xu, Strips minimization in two-dimensional cutting stock of circular items, Comput. Oper. Res., 37 (2010), 621-629. doi: 10.1016/j.cor.2009.06.005
![]() |
[11] | I. Yanchevskyi, R. Lachmayer, I. Mozgova, R. B. Lippert, G. Yaskov, T. Romanova, et al., Circular packing for support-free structures, EUDL, 2020 (2020), 1-10. |
[12] | T. Romanova, Y. Stoyan, A. Pankratov, I. Litvinchev, K. Avramov, M. Chernobryvko, et al., Optimal layout of ellipses and its application for additive manufacturing, Int. J. Prod. Res., 2019 (2019), 1-16. |
[13] |
T. Romanova, Y. Stoyan, A. Pankratov, I. Litvinchev, I. Yanchevsky, I. Mozgova, Optimal Packing in Additive Manufacturing, IFAC-PapersOnLine, 52 (2019), 2758-2763. doi: 10.1016/j.ifacol.2019.11.625
![]() |
[14] |
G. E. Mueller, Numerically packing spheres in cylinders, Powder Technol., 159 (2005), 105-110. doi: 10.1016/j.powtec.2005.06.002
![]() |
[15] |
S. S. Halkarni, A. Sridharan, S. V. Prabhu, Experimental investigation on effect of random packing with uniform sized spheres inside concentric tube heat exchangers on heat transfer coefficient and using water as working medium, Int. J. Therm. Sci., 133 (2018), 341-356. doi: 10.1016/j.ijthermalsci.2018.05.023
![]() |
[16] |
L. Burtseva, A. Pestryakov, R. Romero, B. Valdez, V. Petranovskii, Some aspects of computer approaches to simulation of bimodal sphere packing in material engineering, Adv. Mater. Res., 1040 (2014), 585-591. doi: 10.4028/www.scientific.net/AMR.1040.585
![]() |
[17] |
D. Frenkel, Computer simulation of hard-core models for liquid crystals, Mol. Phys., 60 (1987), 1-20. doi: 10.1080/00268978700100011
![]() |
[18] | S. Yamada, J. Kanno, M. Miyauchi, Multi-sized sphere packing in containers: optimization formula for obtaining the highest density with two different sized spheres, Inf. Media Technol., 6 (2011), 493-500. |
[19] | Z. Duriagina, I. Lemishka, I. Litvinchev, J. A. Marmolejo, A. Pankratov, T. Romanova, et al., Optimized filling of a given cuboid with spherical powders for additive manufacturing, J. Oper. Res. Soc. China, (2020). |
[20] |
A. J. Otaru, A. R. Kennedy, The permeability of virtual macroporous structures generated by sphere packing models: Comparison with analytical models, Scr. Mater., 124 (2016), 30-33. doi: 10.1016/j.scriptamat.2016.06.037
![]() |
[21] | S. Flaischlen, G. D. Wehinger, Synthetic packed-bed generation for CFD simulations: Blender vs. STAR-CCM+, ChemEngineering, 3 (2019), 1-22. |
[22] |
C. R. A. Abreu, R. Macias-Salinas, F. W. Tavares, M. Castier, A Monte Carlo simulation of the packing and segregation of spheres in cylinders, Braz. J. Chem. Eng., 16 (1999), 395-405. doi: 10.1590/S0104-66321999000400008
![]() |
[23] | J. H. Conway, N. J. A. Sloane, Sphere packings, lattices and groups, Springer-Verlag, New York, 2013. |
[24] |
D. Cullina, N. Kiyavash, Generalized sphere-packing bounds on the size of codes for combinatorial channels, IEEE Trans. Inf. Theory, 62 (2016), 4454-4465. doi: 10.1109/TIT.2016.2565578
![]() |
[25] |
L. Fejes, Ü ber einem geometrischen Satz (German), Math. Z., 46 (1940), 83-85. doi: 10.1007/BF01181430
![]() |
[26] |
T. C. Hales, A proof of the Kepler conjecture, Ann. Math., 162 (2005), 1065-1185. doi: 10.4007/annals.2005.162.1065
![]() |
[27] |
M. S. Viazovska, The sphere packing problem in dimension 8, Ann. Math., 185 (2017), 991-1015. doi: 10.4007/annals.2017.185.3.7
![]() |
[28] | Z. Z. Zeng, W. Q. Huang, R. C. Xu, Z. H. Fu, An algorithm to packing unequal spheres in a larger sphere, Adv. Mater. Res., 546-547 (2012), 1464-1469. |
[29] |
M. Hifi, L. Yousef, A local search-based method for sphere packing problems, Eur. J. Oper. Res., 274 (2019), 482-500. doi: 10.1016/j.ejor.2018.10.016
![]() |
[30] |
A. A. Kovalenko, T. E. Romanova, P. I. Stetsyuk, Balance layout problem for 3D-objects: mathematical model and solution methods, Cybern. Syst. Anal., 51 (2015), 556-565. doi: 10.1007/s10559-015-9746-5
![]() |
[31] | T. Romanova, I. Litvinchev, I. Grebennik, A. Kovalenko, I. Urniaieva, S. Shekhovtsov, Packing convex 3D objects with special geometric and balancing conditions, in Intelligent Computing and Optimization, ICO 2019. Advances in Intelligent Systems and Computing, Springer, Cham, 2020. |
[32] |
P. I. Stetsyuk, T. E. Romanova, G. Scheithauer, On the global minimum in a balanced circular packing problem, Optim. Lett., 10 (2016), 1347-1360. doi: 10.1007/s11590-015-0937-9
![]() |
[33] | Y. Stoyan, T. Romanova, A. Pankratov, A. Kovalenko, P. Stetsyuk, Balance layout problems: mathematical modeling and nonlinear optimization, in Space Engineering. Springer Optimization and Its Applications (eds. G. Fasano, J. Pintér), Springer, Cham, 2016,369-400. |
[34] |
I. V. Grebennik, A. A. Kovalenko, T. E. Romanova, I. A. Urniaieva, S. B. Shekhovtsov, Combinatorial configurations in balance layout optimization problems, Cybern. Syst. Anal., 54 (2018), 221-231. doi: 10.1007/s10559-018-0023-2
![]() |
[35] |
N. Chernov, Y. Stoyan, T. Romanova, Mathematical model and efficient algorithms for object packing problem, Comput. Geom., 43 (2010), 535-553. doi: 10.1016/j.comgeo.2009.12.003
![]() |
[36] |
B. Chazelle, H. Edelsbrunner, L. J. Guibas, The complexity of cutting complexes, Discrete Comput. Geom., 4 (1989), 139-181. doi: 10.1007/BF02187720
![]() |
[37] |
G. Wä scher, H. Hauß ner, H. Schumann, An improved typology of cutting and packing problems, Eur. J. Oper. Res., 183 (2007), 1109-1130. doi: 10.1016/j.ejor.2005.12.047
![]() |
[38] |
L. J. P. Araújo, E. Ö zcan, J. A. D. Atkin, M. Baumers, Analysis of irregular three-dimensional packing problems in additive manufacturing: a new taxonomy and dataset, Int. J. Prod. Res., 57 (2019), 5920-5934. doi: 10.1080/00207543.2018.1534016
![]() |
[39] | J. L. Lagrange, Recherches d'arithmétique, (French), Nouv. Mém. Acad. Roy. Soc. Belles Lettres, 1773 (1773), 265-312. |
[40] | C. F. Gauss, Untersuchungen über die Eigenschaften der positiven ternä ren quadratischen Formen von Ludwig August Seber, (in German), J. Reine Angew. Math., 20 (1840), 312-320. |
[41] | Y. G. Stoyan, Mathematical methods for geometric design, Advances in CAD/CAM, Proceedings of PROLAMAT'82, Leningrad, Amsterdam, 1982, 67-86. |
[42] |
S. J. Wright, Coordinate descent algorithms, Math. Program., 151 (2015), 3-34. doi: 10.1007/s10107-015-0892-3
![]() |
[43] |
W. Q. Huang, Y. Li, H. Akeb, C. M. Li, Greedy algorithms for packing unequal circles into a rectangular container, J. Oper. Res. Soc., 56 (2005), 539-548. doi: 10.1057/palgrave.jors.2601836
![]() |
[44] | E. G. Birgin, J. M. Gentil, New and improved results for packing identical unitary radius circles within triangles, rectangles and strips, Comput. Oper. Res., 37 (2010), 1318-1327. |
[45] |
S. I. Galiev, M. S. Lisafina, Linear models for the approximate solution of the problem of packing equal circles into a given domain, Eur. J. Oper. Res., 230 (2013), 505-514. doi: 10.1016/j.ejor.2013.04.050
![]() |
[46] | I. Litvinchev, L. Infante, E. L. Ozuna, Approximate circle packing in a rectangular container: integer programming formulations and valid inequalities, in Computational Logistics, ICCL 2014, LNCS (eds. R. G. González-Ramírez, et al.), 2014, 47-60. |
[47] |
I. Litvinchev, L. Infante, L. Ozuna, Packing circular like objects in a rectangular container, J. Comput. Syst. Sci. Int., 54 (2015), 259-267. doi: 10.1134/S1064230715020070
![]() |
[48] |
Y. G. Stoyan, M. V. Zlotnik, A. M. Chugay, Solving an optimization packing problem of circles and non-convex polygons with rotations into a multiply connected region, J. Oper. Res. Soc., 63 (2012), 379-391. doi: 10.1057/jors.2011.41
![]() |
[49] |
Y. Stoyan, G. Yaskov, Packing equal circles into a circle with circular prohibited areas, Int. J. Comput. Math., 89 (2012), 1355-1369. doi: 10.1080/00207160.2012.685468
![]() |
[50] | X. Zhuang, L. Yan, L. Chen, Packing equal circles in a damaged square, in 2015 International Joint Conference on Neural Networks (IJCNN), Killarney, 2015, 1-6. |
[51] |
C. O. López, J. E. Beasley, Packing a fixed number of identical circles in a circular container with circular prohibited areas, Optim. Lett., 13 (2019), 1449-1468. doi: 10.1007/s11590-018-1351-x
![]() |
[52] |
H. Akeb, M. Hifi, Algorithms for the circular two-dimensional open dimension problem, Int. Trans. Oper. Res., 15 (2008), 685-704. doi: 10.1111/j.1475-3995.2008.00655.x
![]() |
[53] |
H. Akeb, M. Hifi, S. Negre, An augmented beam search-based algorithm for the circular open dimension problem, Comput. Ind. Eng., 61 (2011), 373-381. doi: 10.1016/j.cie.2011.02.009
![]() |
[54] | M. Hifi, R. M'Hallah, A literature review on circle and sphere packing problems: models and methodologies, Adv. Oper. Res., 2009 (2009). |
[55] | E. Specht, www.packomania.com, 2018. Available from: http://packomania.com. |
[56] | I. Kepleri, S. C. Maiest, Mathematici Strena Seu De Niue Sexangula (Latin), Apud Godefridum Tampach, 2014. |
[57] |
E. G. Birgin, F. N. C. Sobral, Minimizing the object dimensions in circle and sphere packing problems, Comput. Oper. Res., 35 (2008), 2357-2375. doi: 10.1016/j.cor.2006.11.002
![]() |
[58] |
T. Kubach, A. Bortfeldt, T. Tilli, H. Gehring, Greedy algorithms for packing unequal spheres into a cuboidal strip or a cuboid, Asia Pac. J. Oper. Res., 28 (2011), 739-753. doi: 10.1142/S0217595911003326
![]() |
[59] | J. Liu, Y. Yao, Yu. Zheng, H. Geng, G. Zhou, An effective hybrid algorithm for the circles and spheres packing problems, Combinatorial Optimization and Applications Lecture Notes in Computer Science, COCOA, 2009,135-144. |
[60] |
Y. G. Stoyan, G. Scheithauer, G. N. Yaskov, Packing unequal Spheres into Various Containers, Cybern. Syst. Anal., 52 (2016), 419-426. doi: 10.1007/s10559-016-9842-1
![]() |
[61] |
Y. Stoyan, G. Yaskov, Packing unequal circles into a strip of minimal length with a jump algorithm, Optim. Lett., 8 (2014), 949-970. doi: 10.1007/s11590-013-0646-1
![]() |
[62] | A. Kazakov, A. Lempert, T. Thanh Ta, On the algorithm for equal balls packing into a multi-connected set, Proceeding of the VIth International Workshop Critical Infrastructures: Contingency Management, Intelligent, Agent-Based, Cloud Computing and Cyber Security (IWCI 2019), 2019. |
[63] | L. Martínez, R. Andrade, E. G. Birgin, J. M. Martínez, Packmol: A package for building initial configurations for molecular dynamics simulations, J. Comput. Chem., 30 (2009), 2157-2164. |
[64] | J. M. Martínez, L. Martínez, Packing optimization for automated generation of complex system's initial configurations for molecular dynamics and docking, J. Comput. Chem., 24 (2003), 819-825. |
[65] | Institute of Chemistry and Institute of Mathematics, University of Campinas, Institute of Mathematics and Statistics, University of São Paulo, PACKMOL, Initial configurations for Molecular Dynamics Simulations by packing optimization, 2020. Available from: http://m3g.iqm.unicamp.br/packmol/home.shtml. |
[66] | L. Burtseva, B. Valdez Salas, F. Werner, V. Petranovskii, Packing of monosized spheres in a cylindrical container: models and approaches, Rev. Mex. Fís., 61 (2015), 20-27. |
[67] |
L. Burtseva, B. Valdez Salas, R. Romero, F. Werner, Recent advances on modelling of structures of multi-component mixtures using a sphere packing approach, Int. J. Nanotechnol., 13 (2016), 44-59. doi: 10.1504/IJNT.2016.074522
![]() |
[68] | S. C. Agapie, P. A. Whitlock, Random packing of hyperspheres and Marsaglia's parking lot test, Monte Carlo Methods Appl., 16 (2010), 197-209. |
[69] | W. S. Jodrey, E. M. Tory, Computer simulation of close random packing of equal spheres, Phys. Rev. A., 32 (1985), 2347-2351. |
[70] | D. P. Fraser, Setting up random configurations, Inf. Q. Comput. Simul. Condens. Phases, 19 (1985), 53-59. |
[71] |
S. Torquato, O. U. Uche, F. H. Stillinger, Random sequential addition of hard spheres in high Euclidean dimensions, Phys. Rev. E, 74 (2006), 061308. doi: 10.1103/PhysRevE.74.061308
![]() |
[72] | М. Skoge, A. Donev, F. H. Stillinger, S. Torquato, Packing hyperspheres in high-dimensional Euclidean spaces, Phys. Rev. E, 4 (2006), 041127. |
[73] |
B. D. Lubachevsky, F. H. Stillinger, Geometric properties of random disk packings, J. Stat. Phys., 60 (1990), 561-583. doi: 10.1007/BF01025983
![]() |
[74] | P. Morse, M. Clusel, E. Corwin, Polydisperse sphere packing in high dimensions, a search for an upper critical dimension, APS March Meeting 2012, Boston, Massachusetts, 2012. |
[75] |
Y. Stoyan, G. Yaskov, Packing congruent hyperspheres into a hypersphere, J. Global Optim., 52 (2012), 855-868. doi: 10.1007/s10898-011-9716-z
![]() |
[76] | G. N. Yaskov, Packing non-equal hyperspheres into a hypersphere of minimal radius, J. Mech. Eng., 17 (2014), 48-53. |
[77] |
G. Scheithauer, Y. G. Stoyan, T. Y. Romanova, Mathematical Modeling of Interactions of Primary Geometric 3D Objects, Cybern. Syst. Anal., 41 (2005), 332-342. doi: 10.1007/s10559-005-0067-y
![]() |
[78] |
A. Wä chter, L. T. Biegler, On the implementation of a primal-dual interior point filter line search algorithm for large-scale nonlinear programming, Math. Program., 106 (2006), 25-57. doi: 10.1007/s10107-004-0559-y
![]() |
[79] | Y. Stoyan, G. Scheithauer, G. Yaskov, Packing of various radii solid spheres into a parallelepiped, Cent. Eur. J. Oper. Res., 11 (2003), 389-407. |
[80] | G. М. Yaskov, Optimization problems of packing hyperspheres: mathematical models, methods, applications, The thesis for the degree of Doctor of Technical Sciences in speciality 01.05.02 Mathematical modeling and computational methods, A. Podgorny Institute for Mechanical Engineering Problems, Ukraine, 2019. |
[81] |
J. Gondzio, HOPDM (version 2.12) - a fast LP solver based on a primal-dual interior point method, Eur. J. Oper. Res., 85 (1995), 221-225. doi: 10.1016/0377-2217(95)00163-K
![]() |
[82] |
C. Meszaros, On numerical issues of interior point methods, SIAM J. Matrix Anal. Appl., 30 (2008), 223-235. doi: 10.1137/050633354
![]() |
[83] |
M. Tawarmalani, N. V. Sahinidis, A polyhedral branch-and-cut approach to global optimization, Math. Program., 103 (2005), 225-249. doi: 10.1007/s10107-005-0581-8
![]() |
[84] | S. V. Yakovlev, The method of artificial dilation in problems of optimal packing of geometric objects, Cybern. Syst. Anal., 53 (2017), 725-731. |
[85] |
Y. G. Stoyan, S. V. Yakovlev, Configuration space of geometric objects, Cybern. Syst. Anal., 54 (2018), 716-726. doi: 10.1007/s10559-018-0073-5
![]() |
[86] | Y. Stoyan, T. Romanova, G. Scheithauer, A. Krivulya, Covering a polygonal region by rectangles, Comput. Optim. Appl., 48 (3), (2011), 675-695. |
[87] |
T. Romanova, I. Litvinchev, A. Pankratov, Packing ellipsoids in an optimized cylinder, Eur. J. Oper. Res., 285 (2020), 429-443. doi: 10.1016/j.ejor.2020.01.051
![]() |
[88] | A. Pankratov, T. Romanova, I. Litvinchev, J. A. Marmolejo-Saucedo, An optimized covering spheroids by spheres, Appl. Sci., 10 (2020), 1846. |
[89] |
I. Litvinchev, Decomposition-aggregation method for convex programming problems, Optimization, 22 (1991), 47-56. doi: 10.1080/02331939108843642
![]() |
[90] |
I. Litvinchev, S. Rangel, Localization of the optimal solution and aposteriori bounds for aggregation, Comput. Oper. Res., 26 (1999), 967-988. doi: 10.1016/S0305-0548(99)00027-1
![]() |
[91] |
I. Litvinchev, Refinement of lagrangian bounds in optimization problems, Comput. Math. Math. Phys., 47 (2007), 1101-1107. doi: 10.1134/S0965542507070032
![]() |
[92] | I. Litvinchev, L. Ozuna, Lagrangian bounds and a heuristic for the two-stage capacitated facility location problem, Int. J. Energy Optim. Eng., 1 (2012), 59-71 |
1. | Yuriy Stoyan, Georgiy Yaskov, Optimized packing unequal spheres into a multiconnected domain: mixed-integer non-linear programming approach, 2021, 6, 2379-9927, 94, 10.1080/23799927.2020.1861105 | |
2. | T. Romanova, G. Yaskov, A. Chugay, Y. Stoian, Optimized Layout of Spherical Objects in a Polyhedral Domain, 2020, 2707-451X, 39, 10.34229/2707-451X.20.4.3 | |
3. | Xiangjing Lai, Jin-Kao Hao, Dong Yue, Zhipeng Lü, Zhang-Hua Fu, Iterated dynamic thresholding search for packing equal circles into a circular container, 2022, 299, 03772217, 137, 10.1016/j.ejor.2021.08.044 | |
4. | Y. G. Stoyan, T. E. Romanova, O. V. Pankratov, P. I. Stetsyuk, Y. E. Stoian, Sparse Balanced Layout of Spherical Voids in Three-Dimensional Domains, 2021, 57, 1060-0396, 542, 10.1007/s10559-021-00379-1 | |
5. | Y. G. Stoyan, T. E. Romanova, O. V. Pankratov, P. I. Stetsyuk, S. V. Maximov, Sparse Balanced Layout of Ellipsoids*, 2021, 57, 1060-0396, 864, 10.1007/s10559-021-00412-3 | |
6. | Tatiana Romanova, Georgiy Yaskov, Igor Litvinchev, Igor Yanchevskyi, Yurii Stoian, Pandian Vasant, 2022, 9780323897853, 331, 10.1016/B978-0-323-89785-3.00008-6 | |
7. | Mykola Gil, Volodymyr Patsuk, 2023, Chapter 4, 978-3-031-20140-0, 35, 10.1007/978-3-031-20141-7_4 | |
8. | Dmitriy Kritskiy, Olha Pohudina, Mykhailo Kovalevskyi, Yevgen Tsegelnyk, Volodymyr Kombarov, 2022, Chapter 72, 978-3-030-94258-8, 924, 10.1007/978-3-030-94259-5_72 | |
9. | Josef Kallrath, 2021, Chapter 15, 978-3-030-73236-3, 495, 10.1007/978-3-030-73237-0_15 | |
10. | Yaskov G, Chugay A, Romanova T, Shekhovtsov S, Modern method of topology optimization of products in additive production, 2022, 27, 27101673, 301, 10.15407/jai2022.01.301 | |
11. | Tatiana Romanova, Georgiy Yaskov, Igor Litvinchev, Petro Stetsyuk, Andrii Chuhai, Sergiy Shekhovtsov, 2023, Chapter 3, 978-3-031-20140-0, 25, 10.1007/978-3-031-20141-7_3 | |
12. | Xiangjing Lai, Jin-Kao Hao, Renbin Xiao, Fred Glover, Perturbation-Based Thresholding Search for Packing Equal Circles and Spheres, 2023, 1091-9856, 10.1287/ijoc.2023.1290 | |
13. | Eduardo Basurto, Peter Gurin, Eckard Specht, Gerardo Odriozola, Searching for the maximal packing fraction of hard disks confined by a circular cavity through replica exchange/event-chain Monte Carlo, 2024, 161, 0021-9606, 10.1063/5.0219006 | |
14. | Chuhai A, Yaskova Y, Dubinskyi V, An intelligent decision support system for solving optimized geometric design problems, 2022, 27, 27101673, 29, 10.15407/jai2022.02.029 | |
15. | Igor Litvinchev, Andrii Chuhai, Sergey Shekhovtsov, Tatiana Romanova, Georgiy Yaskov, 2024, Chapter 5, 978-3-031-34749-8, 63, 10.1007/978-3-031-34750-4_5 | |
16. | Xiangjing Lai, Zhenheng Lin, Jin-Kao Hao, Qinghua Wu, An Efficient Optimization Model and Tabu Search–Based Global Optimization Approach for the Continuous p-Dispersion Problem, 2024, 1091-9856, 10.1287/ijoc.2023.0089 | |
17. | Tatiana Romanova, Anna Grebinyk, Alexander Pankratov, Yuri Stoyan, Alina Nechyporenko, Yuriy Prylutskyy, Igor Grebennik, Marcus Frohme, 2024, Chapter 15, 978-3-031-34749-8, 257, 10.1007/978-3-031-34750-4_15 | |
18. | Andreas Fischer, Igor Litvinchev, Tetyana Romanova, Petro Stetsyuk, Georgiy Yaskov, Packing spheres with quasi-containment conditions, 2024, 90, 0925-5001, 671, 10.1007/s10898-024-01412-1 | |
19. | Zoia Duriagina, Ihor Lemishka, Oleksandr Ovchynnykov, Vladimir Yefanov, Piotr Klimczyk, O. Voznyak, The influence of the structure and properties of powder heat-resistant alloys on the features of 3D printing of products from them, 2024, 390, 2261-236X, 04004, 10.1051/matecconf/202439004004 | |
20. | Jianrong Zhou, Shuo Ren, Kun He, Yanli Liu, Chu-Min Li, An efficient solution space exploring and descent method for packing equal spheres in a sphere, 2024, 164, 03050548, 106522, 10.1016/j.cor.2023.106522 | |
21. | Mao Chen, Yajing Yang, Zeyu Zeng, Xiangyang Tang, Xicheng Peng, Sannuya Liu, A filtered beam search based heuristic algorithm for packing unit circles into a circular container, 2024, 166, 03050548, 106636, 10.1016/j.cor.2024.106636 | |
22. | Jianrong Zhou, Kun He, Jiongzhi Zheng, Chu-Min Li, Geometric batch optimization for packing equal circles in a circle on large scale, 2024, 250, 09574174, 123952, 10.1016/j.eswa.2024.123952 | |
23. | Andreas Fischer, Igor Litvinchev, Tetyana Romanova, Petro Stetsyuk, Georgiy Yaskov, Quasi-Packing Different Spheres with Ratio Conditions in a Spherical Container, 2023, 11, 2227-7390, 2033, 10.3390/math11092033 | |
24. | Georgiy Yaskov, Yuriy Stoyan, Tetyana Romanova, Igor Litvinchev, Andrii Chuhai, Nilolay Gil’, 2024, Chapter 35, 978-3-031-73323-9, 361, 10.1007/978-3-031-73324-6_35 | |
25. | Dong Liu, Lijun Kong, Jinghui Song, Yiming Zhou, Predictive models for overall health of hydroelectric equipment based on multi-measurement point output, 2025, 34, 2191-026X, 10.1515/jisys-2024-0364 | |
26. | Xiangjing Lai, Jin-Kao Hao, Dong Yue, Yangming Zhou, A heuristic algorithm with multi-scale perturbations for point arrangement and equal circle packing in a convex container, 2025, 03050548, 107099, 10.1016/j.cor.2025.107099 | |
27. | Zeki Oralhan, Burcu Oralhan, Quantum Snowflake Algorithm (QSA): A Snowflake-Inspired, Quantum-Driven Metaheuristic for Large-Scale Continuous and Discrete Optimization with Application to the Traveling Salesman Problem, 2025, 15, 2076-3417, 5117, 10.3390/app15095117 |