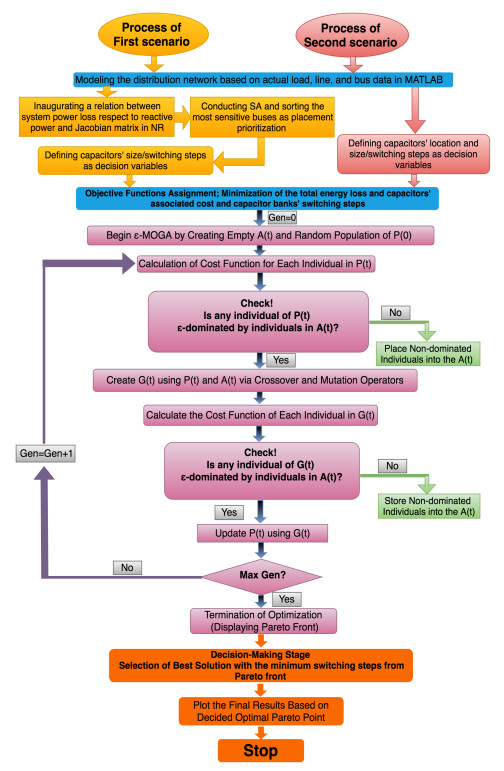
Powders of the system (1–x)Bi0.5Na0.5TiO3–xBiFeO3 (x = 0, 0.02, 0.08, 0.10) are synthesized by the combustion reaction method. The crystal structure and the particle size of Bi0.5Na0.5TiO3 are modified by the incorporation of BiFeO3, as can be seen from the infrared spectroscopy and X-ray diffraction results. The inclusion of iron and the increase in the molar percentage of bismuth in the BNT matrix generate new bonds with a different force constant. The structural analysis showed that the addition of BFO to the BNT does not induce any structural phase transition, preserving the rhombohedral symmetry of the Bi0.5Na0.5TiO3 system. The electrical measurements show that the incorporation of iron increases the conductivity of the system generated by an increase in the concentration of oxygen vacancies; alternatively, the addition of 10% of BiFeO3 generates ferrimagnetic behavior reflected in the magnetic hysteresis curves obtained at room temperature.
Citation: Wolfgang Zúñiga-Mera, Sonia Gaona Jurado, Alejandra Isabel Guerrero Duymovic, Claudia Fernanda Villaquirán Raigoza, José Eduardo García. Effect of the incorporation of BiFeO3 on the structural, electrical and magnetic properties of the lead-free Bi0.5Na0.5TiO3[J]. AIMS Materials Science, 2021, 8(5): 792-808. doi: 10.3934/matersci.2021048
[1] | Minh Y Nguyen . Optimal voltage controls of distribution systems with OLTC and shunt capacitors by modified particle swarm optimization: A case study. AIMS Energy, 2019, 7(6): 883-900. doi: 10.3934/energy.2019.6.883 |
[2] | Essam A. Al-Ammar, Ghazi A. Ghazi, Wonsuk Ko, Hamsakutty Vettikalladi . Temperature impact assessment on multi-objective DGs and SCBs placement in distorted radial distribution systems. AIMS Energy, 2020, 8(2): 320-338. doi: 10.3934/energy.2020.2.320 |
[3] | Abdul Matin Ibrahimi, K Narayanan, Mohammed Elsayed Lotfy, Mir Sayed Shah Danish, Mikaeel Ahmadi, Tomonobu Senjyu . Transients outrush current analysis and mitigation: A Case study of Afghanistan North East power system. AIMS Energy, 2019, 7(4): 493-506. doi: 10.3934/energy.2019.4.493 |
[4] | Akash Talwariya, Pushpendra Singh, Mohan Lal Kolhe, Jalpa H. Jobanputra . Fuzzy logic controller and game theory based distributed energy resources allocation. AIMS Energy, 2020, 8(3): 474-492. doi: 10.3934/energy.2020.3.474 |
[5] | Md Mashud Hyder, Kaushik Mahata . Reconfiguration of distribution system using a binary programming model. AIMS Energy, 2016, 4(3): 461-480. doi: 10.3934/energy.2016.3.461 |
[6] | Bitian Wu . Day ahead scheduling model of wind power system based on fuzzy stochastic chance constraints—considering source-load dual-side uncertainty case. AIMS Energy, 2025, 13(3): 471-492. doi: 10.3934/energy.2025018 |
[7] | Santosh Kumar Sharma, D. K. Palwalia, Vivek Shrivastava . Distributed generation integration optimization using fuzzy logic controller. AIMS Energy, 2019, 7(3): 337-348. doi: 10.3934/energy.2019.3.337 |
[8] | Anbazhagan Geetha, S. Usha, J. Santhakumar, Surender Reddy Salkuti . Forecasting of energy consumption rate and battery stress under real-world traffic conditions using ANN model with different learning algorithms. AIMS Energy, 2025, 13(1): 125-146. doi: 10.3934/energy.2025005 |
[9] | Amandeep Gill, Pushpendra Singh, Jalpa H. Jobanputra, Mohan Lal Kolhe . Placement analysis of combined renewable and conventional distributed energy resources within a radial distribution network. AIMS Energy, 2022, 10(6): 1216-1229. doi: 10.3934/energy.2022057 |
[10] | Abdollah Kavousi-Fard, Amin Khodaei . Multi-objective optimal operation of smart reconfigurable distribution grids. AIMS Energy, 2016, 4(2): 206-221. doi: 10.3934/energy.2016.2.206 |
Powders of the system (1–x)Bi0.5Na0.5TiO3–xBiFeO3 (x = 0, 0.02, 0.08, 0.10) are synthesized by the combustion reaction method. The crystal structure and the particle size of Bi0.5Na0.5TiO3 are modified by the incorporation of BiFeO3, as can be seen from the infrared spectroscopy and X-ray diffraction results. The inclusion of iron and the increase in the molar percentage of bismuth in the BNT matrix generate new bonds with a different force constant. The structural analysis showed that the addition of BFO to the BNT does not induce any structural phase transition, preserving the rhombohedral symmetry of the Bi0.5Na0.5TiO3 system. The electrical measurements show that the incorporation of iron increases the conductivity of the system generated by an increase in the concentration of oxygen vacancies; alternatively, the addition of 10% of BiFeO3 generates ferrimagnetic behavior reflected in the magnetic hysteresis curves obtained at room temperature.
Indeed, capacitors due to their capacitive characteristics are used as reactive power compensation devices in distribution networks. Compensation of the reactive power in distribution networks results in line-current reduction from the generation side to the distribution system which deduces the power system losses. If the reactive power supply, considers in the generation side only, all electrical parts of the network such as transformers, transmission and distribution lines, protection switching devices, and many other control units must be increased by size.
The capacitors can adjust the power system performance by reducing the reactive power demand in the network which results in reduction of line-carrying current. It also decreases the power loss in distribution lines, transformer stations, and transmission lines significantly. Also, it affects the voltage profile positively, and by reduction of reactive power, the current will decrease on transformers, lines, and equipment that consequently increases the capacity of distribution networks, the lifetime of the power system equipment as well as delay on their replacement.
Variations in demand load and power factor at consumption points are significant characteristics for capacitor banks to justify the supplied reactive power. For this reason, usually, two types of capacitor banks are considered in power system networks. The fixed type capacitor is the simplest form to supply a fixed amount of reactive power in the network. Usually, it can provide the base reactive power which does not fluctuate by variation of reactive power and the load.
As the reactive power supplied by capacitors neutralizes the extra inductive reactive power, it is not economically and technically recommended to provide a large amount of reactive power throughout the day and night. For instance, during the light load, reactive power neutralization is no longer needed since, it causes the voltage profile of the network to be raised unexpectedly.
The second type of capacitor bank is the automatic/switch-able capacitor bank which is made up of a combination of capacitor steps connected in parallel and can be automatically switched to different tap upon the condition of various parameters of the system. In such type of capacitors, an integrated power factor controller controls reactive power supply by switching on and off of all or part of the capacitor bank [1].
The distribution networks usually consist of several types of load demand; residential, industrial, and commercial which sometimes covers all sorts together and requires a variable electricity supply. For such fluctuating load demand in the network, utilizing automatic capacitor banks is preferable. However, controlling and managing their effective operation is the point of interest that has to enable and satisfy both; utility managers and electricity end-users for higher profit and power quality, respectively beside several other benefits.
The optimal capacitor allocations considering their appropriate sizing and placement have been considered in distribution networks vastly for a long time. Many research works consider capacitor allocation in distribution systems. Both fixed and automatic capacitors are found in literature to be applied in distribution networks using a variety of methodologies. In previous studies, researchers have discussed and addressed optimal reactive power allocation and optimal selection of capacitors in the distribution networks considering various criteria such as cost and effective utilization of such compensators. Going back to decades before the earliest research and investigation considering numerical and heuristic optimization is found in [2,3] for instances.
A methodology using NSGA-Ⅱ is proposed in [4] to determine number, locations, control, and size of fixed and switchable capacitor banks in distribution networks contaminated by harmonics in three different load level. The net present value (NPV), voltage deviation, and total harmonic distortion (THD) of voltage are the three objective functions, they considered. The same algorithm is proposed in [5] considering power loss and THD as the objective function for fixed capacitor allocation. A decision-making support technique in terms of switching transients is applied to determine the best solution from the obtained Pareto. They have found their proposed methodology to be satisfactory and consistent with previous methods.
Optimal capacitor placement is solved using a hybrid CODEQ method in the distribution network to overcome the previous drawback of parameters selection in differential evolution (DE). The performance of the proposed method over conventional CODEQ method, DE, simulated annealing (SA), and ant system (AS) is tested and shown in [6].
Authors in [7], considered allocation of capacitors in radial distribution networks using cuckoo search algorithm (CSA) to minimize the system operation cost and improving voltage profile. Their methodology is applied in 69-bus and 118-bus IEEE test distribution networks and resulted in the reduction of power loss and annual energy consumption in both systems. Two-stage procedure for optimal location and size of the capacitors applied in [8]. In their proposed first stage, loss sensitivity analysis using two loss sensitivity indices (LSIs) was applied to find the most suitable candidate locations for capacitor placement which can reduce the search space for the optimization process. In their second stage, ant colony optimization (ACO) algorithm proposed and utilized for the optimal location and size based on the minimization of energy loss and capacitor cost as the objective functions. Reference [9] introduced an exciting methodology for the simultaneous planning of vehicle charging station (CS) and capacitors in electric distribution networks. They observed the best results for improving power loss and voltage profile in their proposed real distribution network. Optimal placement of capacitor banks to distribution transformers (TRs) for the power loss reduction is offered in [10] where the problem modeled as maximizing the net present value (NPV) of the capacitor installation project. It was formulated as a mixed integer programming (MIP) model based on the explicit formula for direct calculation of the power loss. They have implemented their proposed method to a portion of Macau MV distribution network which resulted in significant improvement of the system. In the same way studies in [11,12,13,14] expressed different algorithms and methods such as genetic algorithm (GA) and sensitivity analysis in radial distribution networks for power quality improvement as well as maintaining the minimum cost of capacitor installation.
The authors in [15] propose an optimal allocation of capacitors along with distributed generations (DGs) and dispersed energy storage devices. They used a hybrid procedure based on GA and sequential quadratic programming (SQP) algorithm on 18-bus medium voltage (MV) balanced 3-phase network.
Reliability and economic-based capacitor allocation is studied in [16] utilizing simulated annealing (SA) as an optimization tool. The capacitor allocation problem is considered and studied only for three conditions as light, medium, and peak load levels. Then at each load level, the average load is applied for the capacitor allocation.
In the same manner, simultaneous allocation of DG and capacitor is addressed in [17] using single-objective GA considering limited load level into three load categories.
MINLP is another useful method which applied in many research studies. It is also the right approach for solving such optimization problems having continuous, and discrete variables [18,19].
In this study, those variables that are integers, use a lower bound of 1, and an upper bound of the number of different values that are valid for those integer position/decision variables. Then inside the objective function, an x value is considered for indexing into the vector of discrete values and the results reflexed simply into the calculations. What was found from literature and in previous studies that although fixed/automatic capacitors were widely used for optimizing the cost, power loss, THD, and voltage improvement and adopting various methodologies but still many drawbacks should be pointed out for better and proper implementation. In previous studies, little attention is paid to the time-dependent nature of distribution networks and the importance of automatic capacitors' switching steps in which minimizing capacitor switching will affect the lifetime of devices directly. In this study, a novel Pareto based epsilon multi-objective optimization is put forward for the first time to allocate the two types of capacitors optimally in the real distribution network. Capacitor switching steps and operational cost of energy loss and capacitor installation as the two significant objective functions are considered in this optimization.
In summary, the following points are addressed in this paper and further illustration is made.
● Utilizing Pareto based real optimization method which has not been considered for optimal capacitor allocation in distribution networks so far.
● Optimization considering the 24-hour real-time load flow analysis.
● Confirming the proposed methodologies performance with its application on the complex real distribution network, under capacity expansion planning.
● Simultaneous allocation of fixed and automatic capacitors' optimal operation.
● Time-variant load dependent switching operation and its minimization to improve the lifetime of devices as well as operational cost.
● Developing and deploying two different scenarios and their comparison for suitable selection.
● Applying the optimization using the hybrid methodology of sensitivity analysis and epsilon-MOGA as the first scenario for optimal placement and sizing.
● Applying the optimization using only epsilon-MOGA for both sizing and placement under the second scenario.
● Computing the annual saving by energy capacity release in distribution network.
The introduction part of the paper is considered in the first section, and the remainder of the paper is organized as follows. Section-2, expresses the related problem formulations for sensitivity analysis, objective functions and constraints. The methodology along with the theory of ϵ-MOGA is expressed in Section-3 and ends with introducing the real distribution model in Kabul city as the case study in this paper. Simulations and results are presented and discussed in Section-4 which is followed by concluding remarks in Section-5.
In this study, two scenarios are conducted for both fixed type and automatic capacitor allocation in a real distribution network. In the first scenario, a two-step method is put forward to proceed with the optimization.
Accordingly, in its first step, a sensitivity analysis method coordinating with the Jacobian matrix of the Newton-Raphson load flow analysis is utilized for determination of the most sensitive buses to power loss considering the reactive power. These buses are sorted based on their sensitivity order. After selection of the most sensitive buses, the results are the input to the second step, which is a multi-objective optimization approach yielding to the best and faster convergence. It determines the most optimal solutions in terms of the optimal non-dominated Pareto points.
In the second scenario, both optimal placement and sizing are conducted based on applying multi-objective optimization utilizing ϵ-MOGA. The decision variables are the location and size of the fixed capacitors and hourly switching steps of automatic capacitor banks.
Cost of energy loss and capacitors is the first objective function and the second objective function is considered to be the minimization of the capacitor's switching steps.
A sensitivity analysis is conducted based on a systematic methodology to eliminate and reduce the search space for optimal allocation of the capacitor banks. On the other hand, locations with the most or maximum impact on the power loss of the system with respect to their reactive power will be chosen.
The total power loss of the network including real and reactive power loss in complex form is mathematically expressed as (1), and the real part for total power loss of the network is formulated in (2).
Ploss+Qloss=VI∗=VY∗V∗ | (2.1) |
PL=n∑i=1n∑j=1|Vi||Vj||Yij|cos(δi−δj−αij) | (2.2) |
As shown in (2), there is no relation between power loss of the system PL and the nodal reactive power Q, so a relation for applying sensitivity of the power loss respect to reactive power is needed. For this reason, the derivative of system loss with respect to reactive power is expanded as following equations.
∂PL∂Q=(∂PL∂V)(∂V∂Q) | (2.3) |
∂PL∂Vi=2n∑j=1VjYijcosαijcos(δi−δj) | (2.4) |
∂PL∂δi=−2n∑j=1VjYijcosαijsin(δi−δj) | (2.5) |
Likewise, the relation between system power loss and Jacobian matrix is obtained as below.
[∂PL∂δ∂PL∂V]=[J][∂PL∂P∂PL∂Q] | (2.6) |
where, J=[∂P∂δ∂P∂V∂Q∂δ∂Q∂V]
[∂PL∂P∂PL∂Q]=[J]−1[∂PL∂δ∂PL∂V] | (2.7) |
where, J−1=[JI1JI2 JI3JI4]
Hence,
[∂PL∂Q]=[JI3JI4][∂PL∂δ∂PL∂V] | (2.8) |
where, JI3 and JI4 are ∂δ∂Q and ∂V∂Q, respectively which are defined to be sub matrix of inverse of Jacobian matrix in Newton-Raphson (NR) power flow analysis.
Consequently, all the buses are assessed and evaluated according to the derived equation for sensitivity and the most sensitive buses are selected as candidates for capacitor placement.
After finding the loss sensitivity with respect to nodal reactive power, the voltage and reactive power of each bus is considered to be observed if it is within predetermined maximum and minimum limit. The procedure is followed to update the sensitive buses or in another words, the selected bus from sorted maximum sensitivity buses is automatically being removed or selected based on the defined criteria. The procedure continues until it reaches the assigned number of locations. In this study, based on the possible availability, twenty locations are considered in the real 162-bus distribution network model.
One important and major tool for determining current flow, voltage difference, and losses in the network for comparison of base case condition or before placement of capacitor banks and the network condition with various scenarios of capacitor allocation, is the load-flow analysis.
In this study, as discussed in previous section NR due to its well-known accuracy and best convergence for complex and non-radial networks is used to perform the analysis. Due to the well-known NR method and its well introduction in many power system analysis textbooks [20,21], further details are skipped in this paper.
Objective functions are the most important part of the optimization formulations. It should be carefully selected based on their priority and effectiveness which can maximize or minimize a parameter of the system. In this study, a multi-objective optimization is conducted and the two objective functions are the total cost and capacitor banks' switching, respectively to be minimized.
The first objective function is to minimize the total cost associated with annual energy loss, peak power loss, equipment and lines, and all involving cost of both fixed and automatic capacitor banks. In other words, the total cost is computed anent to the revenue cost, cost of capacitors, power plants, and related equipment in a year. The second objective function is minimization of the capacitor banks' switching steps, where the less switching steps during its operation, the more the lifetime of the devices are enhanced. The mathematical formulation for the two objective functions are expressed in the following equations.
ℵ1=κEn∑i=1PiTi+κPP0+κRSpeak+CB.Cost | (2.9) |
ℵ2=∑20φ=1∑24ψ=1|CBφ(ψ)−CBφ(ψ+1)|α | (2.10) |
The first objective function is developed involving five different terms which represent the total cost. Each term is discussed separately in the following subsections.
For the second objective function, φ, ψ, CBφ(ψ), CBφ(ψ+1) and α are the number of capacitor banks, time in hour, output of capacitor bank in first step, output of capacitor bank in second step at hour plus one and constant for converting reactive power to switching steps, respectively.
For each kWh of energy supply, a specific cost is calculated based on fuel and electricity supply cost which are standard values for different countries. The mathematical formulation for the cost of energy loss (CEL) is shown in the equation below.
PEnergyloss=n∑i=1PiTi | (2.11) |
where, n is number of the load levels, Pi is the power loss at any load level i with a time duration Ti.
CostEnergyloss=κE.PEnergyloss | (2.12) |
where, κE is in kWh representing cost of energy.
Construction of power plants usually depends on peak demand the peak time. Increasing the number of electricity consumers and thus growth in consumption, leads to constructing new power plants. Therefore, decreasing the power loss in peak time results in postponing the construction of the new power plants.
Usually, cost of construction for new power plant is evaluated based on kW cost and its lifetime. For instance, if every kW of a power plant is A$, its lifetime is n year, and the return on investment (ROI) is B%, then the yearly cost of peak power for each kW is obtained from the below equation.
CostPeak(1kW)=κP=A.(1+B)n×B(1+B)n −1 | (2.13) |
Hence, by determining the cost of each kW for yearly peak power, cost of annual peak power is easily calculated from the below equation.
Costpeak(P0kW)=κP×P0 | (2.14) |
where P0 represents the yearly peak power.
In a distribution network, the equipment and lines have their rating values in kVA. By an increase in the number of consumers, the consumption reaches to the rated operating value which requires renovation to change and replace the lines and equipment.
By compensating the reactive power, the total power carrying into lines and equipment decrease and thus postponing their construction and renovation. The economic factor is applied on several studies such in [22] and helps to extract cost components accordingly.
For calculating the cost of each kVA for the construction of the new equipment and lines, its mathematical formulation is shown below.
Costequip(1kVA)=κR=C.(1+D)m×D(1+D)m −1 | (2.15) |
So, when the yearly line and equipment cost for one kVA is determined, total cost for one-year construction of lines and equipment is obtainable from below equation.
Costequip(SkVA)=κR×Speak | (2.16) |
where C is cost of equipment and lines, D is its ROI, m is their lifetime, and Speak represents the yearly peak kVA.
The cost of capacitor banks including capital, installation, and maintenance is formulated into two parts for the fixed and automatic types. This term is mathematically formulated and presented in the following equation.
CB.Cost=κfL∑k=1CBfix(k)+κaL∑k=1CBaut(k) | (2.17) |
where κf, CBfix(k), κa, and CBaut(k) are price of the fixed capacitor bank in kvar/fanxiexian_myfh, size of the fixed capacitor bank, price of the automatic capacitor bank in kvar/fanxiexian_myfh, and maximum size of automatic capacitor bank, respectively.
The constraints for this study consist of the power flow constraint, voltage condition constraint, current condition constraint, and the maximum reactive power compensation into the network.
Power balance is given by non-linear power flow equations which state that the sum of complex power flows at each bus in the distribution system injected into a bus minus the power flows extracted from the bus should equal zero. Equations formulated as follows:
Pi−Pj−n∑j=1|Vi||Vj||Yij|cos(δi−δj−αij)=0 | (2.18) |
Qi−Qj−n∑j=1|Vi||Vj||Yij|sin(δi−δj−αij)=0 | (2.19) |
The maximum and minimum operational limit on the bus voltage magnitude and phase angle are expressed below:
|Vmini|≤|Vi|≤|Vmaxi| | (2.20) |
δmini≤|δi|≤δmaxi | (2.21) |
The thermal limit of all the transmission lines should not be violated; hence the line flow is constrained to be less than the line thermal limit for both directions of current flow as given below:
Iij≤Imaxij | (2.22) |
Iji≤Imaxji | (2.23) |
where Imaxij is the maximum current flow allowed along each branch ij.
There should be a constraint for reactive power compensation to not exceed the maximum limit as the following equation.
M∑i=1Qc≤Qmax | (2.24) |
where M is the number of candidate buses for capacitor placement, Qc is the amount of reactive power compensated in bus i, and Qmax is the maximum compensation limit based on available reactive power in the network.
Optimal time-based operational planning of large-scale distribution network involving power flow analysis is complex and often time-consuming. This is because there are additional constraints based on the grids steady state operating condition and more decision variables are involved which increases the possible convergence time. A robust evolutionary optimization tool that has been found capable of handling complex non-linear optimization problems involving NR load-flow analysis is employed in this work. ϵ-MOGA can perform the optimization task and reach the best compromise solution at better computational time than most of the other existing optimization tools [23].
Proposed methodologies are summarized in steps and are demonstrated in Figure 1. The flowchart is developed for both scenarios, and after obtaining Pareto fronts, decision-making is made considering the minimum switching steps operation of capacitor banks for each method. The theory and concept of the proposed algorithm is expressed in the following subsection.
ϵ-MOGA is a multi-objective evolutionary optimization tool that is based on elitist population selection using the concept of ϵ-dominance sorting. The ϵ-dominance feature of the algorithm controls the storing of the superior solutions in the archive A(t). The integral action of ϵ-MOGA involves an ϵ-Pareto set which is the point at which the A(t) converges quickly along the Pareto front G(Θp) which reduces the required computational time [24]. In order to achieve this, a fixed number of boxes, nBoxi based on the length of decision vectors are obtained for the objective functions. The width ϵi of each nBoxi is calculated as given below for each dimension i∈[1.....n] [24,25,26].
where,ϵi=(Gmaxi−Gmini)nBoxi,Gmaxi=maxGi(ϑ),Gmini=minGi(ϑ)andϑ∈{Θ∗pϵ} | (3.1) |
In this optimisation method each box is occupied by one solution in the archive A(t) which helps maintaining a good diversity G(Θ∗pϵ) among solutions. The following equation clarify the idea behind ϵ-dominance and Boxi(ϑ) in solution space ϑ∈D accordingly.
Boxi(ϑ)=Gi(ϑ)−GminiGmaxi−Gmini×(nBoxi)∀i∈[1.....n] | (3.2) |
A solution ϑ1 with value G(ϑ1) ϵ-dominates the solution ϑ2 with value G(ϑ2), is represented by ϑ1≺ϵϑ2, if (27) holds for box(ϑ)={box1(ϑ),...,boxs(ϑ)}.
[Box(ϑ1)≺Box(ϑ2)]∨[Box(ϑ1)=Box(ϑ2)andϑ1≺ϑ2] | (3.3) |
Hence, a set Θ∗pϵ⊆Θp is ϵ-Pareto, if and only if
ϑ1,ϑ2ϵΘ∗pϵ,ϑ1≠ϑ2,Box(ϑ1)≠Box(ϑ2)∧Box(ϑ1)≻ϵBox(ϑ2) | (3.4) |
Consequently, ϵ-dominated solutions updates the archive A(t) without shared boxes. If there are two non-dominated solutions existing in a box, the solution nearer to the center of box is preferred by encouragement of a smart distribution. In summary, there are three forms of populations discussed in this algorithm so far and are defined below:
1- P(t) having population size of NP, is the main population and deploy during each iteration.
2- A(t) as an archive stores the ϵ-Pareto set, Θ∗pϵ with NA as its population size. The highest level of ϵ-Pareto set as its maximum limit is obtained using the following equation. The maximum number of boxes is expressed as nBoxmax.
|Θ∗pϵ|≤∏si=1(nBoxi+1)nBoxmax+1 | (3.5) |
3- G(t) which has an even number of population, is considered as auxiliary population. The output of mutation and crossover operators over P(t) and A(t).
The major steps of the proposed optimization algorithm are comprehensively expressed as following [27,28,29]:
Step1. the algorithm is started by creation of empty population as A(t).
Step2. Creating random values of P(0) as initial population using Np individuals and D as search space.
Step3. Objective function evaluation according to input of each individual in P(t).
Step4. Updating archive elements in A(t) using individual in P(t) considering following points:
a. Finding non-dominated individuals in P(t) to determine ΘND.
b. The limits Gmaxi and Gmini of Pareto front are calculated from G(ϑ), ∀ϑ∈ΘND.
c. A(t) updates by introducing new ε-non-dominated individuals which dominate the existing individual in A(t).
Step5. Creation of G(t) as auxiliary population following the below points:
a. Selection of two different individuals, ϑp from P(t), and ϑA from A(t).
b. Generating a random number as μ∈[0...1].
c. If probability of crossover/mutation μ>Pc/m, is less than generated random number in sub step b, an extended linear recombination technique utilized to perform the crossover.
d. If the case is opposite to sub step c, a mutation performs using Gaussian distribution and then the created population will be added to G(t). This process is repeated Np/2 times till G(t) saturates.
Step6. Evaluation of objective functions for every individual in G(t)again.
Step7. Updating A(t) from G(t) considering locations in objective space.
Step8. P(t) modifies if and only if the elements in G(t) dominates the elements in p(t).
Step9. ϵ-Pareto set, Θ∗pϵ are developed by individuals in archive considering Pareto front smart distribution.
The proposed methodologies are applied to a complex real distribution system located in the most congested part of Kabul city, the capital of Afghanistan. The distribution network has 20 kV medium voltage level as well as including 162 buses and 165 distribution lines [30,31]. Typically, in Afghanistan power system, the local or imported electricity is transmitted to substations and from the substations to the junction stations in which electricity distributes to the load buses or transformer stations in medium voltage.
Further, in the low voltage side, the electricity goes from transformer stations to the single phase and three phase low voltage distribution loads. Figure 2 depicts the distribution network under study which consists of all types of load. In this study, the proposed methodology is applied on this real distribution network is applicable to all complex, radial, or meshed distribution networks.
After implementing the steps at the proposed methodologies and obtaining optimal Pareto solutions, an optimal point based on decision-making criterion of the minimum switching steps for all the capacitor banks is selected in each scenario and this point considered as one of the optimal results. Based on decided Pareto set at that point, the results for capacitor banks operation, the voltage of the network, power loss, and other economic parameters for the first and second scenario are achieved and appropriately illustrated.
Furthermore, voltage and power loss in the base case before optimization are extended and illustrated for comparison with the optimal results.
In the first scenario, after conducting the sensitivity analysis, twenty locations are determined for the allocation of fixed and automatic capacitor banks. The result of the sensitivity analysis for placement is utilized in the second step, conducting ϵ-MOGA and the Pareto front for both scenarios are shown in Figures 3 and 4.
Optimum reactive power supply for each capacitor bank is demonstrated in Figures 5 and 6. It shows the optimal daily operation of the capacitor banks in which their locations are the output of the sensitivity analysis.
Switching steps and size for the automatic and fixed type of the capacitor banks are the results of applying proposed multi-objective optimization. Figure 9a shows all the capacitor banks' switching steps on a daily basis. Despite assigning a wider range of operation for switching steps in optimization constraint, less switching steps with a maximum of three steps are effectively allocated.
Also, Table 1 details each capacitor banks optimal location, size, status, configuration, and number of switching per day. The size for the fixed CB and automatic CB is specified as well.
CBs | Optimum Location Sensitivity | Fix CB | Auto CB | Configuration of Auto-switching | No of Switching Per Day |
CB1 | 4 | 600 | 150 | On/Off | 8 |
CB2 | 33 | 450 | 300 | 3-Tap | 7 |
CB3 | 160 | 600 | 150 | On/Off | 12 |
CB4 | 161 | 450 | 300 | 3-Tap | 12 |
CB5 | 162 | 450 | 300 | 3-Tap | 7 |
CB6 | 34 | 600 | 150 | On/Off | 12 |
CB7 | 159 | 450 | 300 | 3-Tap | 10 |
CB8 | 134 | 450 | 300 | 3-Tap | 13 |
CB9 | 118 | 450 | 300 | 3-Tap | 4 |
CB10 | 107 | 450 | 300 | 3-Tap | 12 |
CB11 | 59 | 600 | 150 | On/Off | 13 |
CB12 | 49 | 450 | 300 | 3-Tap | 12 |
CB13 | 128 | 450 | 300 | 3-Tap | 7 |
CB14 | 64 | 450 | 300 | 3-Tap | 14 |
CB15 | 8 | 450 | 300 | 3-Tap | 14 |
CB16 | 42 | 450 | 300 | 3-Tap | 12 |
CB17 | 37 | 450 | 300 | 3-Tap | 17 |
CB18 | 79 | 450 | 300 | 3-Tap | 13 |
CB19 | 90 | 450 | 300 | 3-Tap | 11 |
CB20 | 67 | 450 | 300 | 3-Tap | 10 |
The details of the optimal sizing and placement for each CB along with their operation behaviour is indicated in Table 2. For the second scenario, simultaneous placement and sizing of the capacitor banks are performed using ϵ-MOGA. Based on the obtained Pareto, the optimal operation of capacitor banks and their switching steps are demonstrated in Figures 7 and 8 and Figure 9b, respectively.
CBs | Optimum Location ϵ-MOGA | Fix CB | Auto CB | Configuration of Auto-switching | No of Switching Per Day |
CB1 | 65 | 450 | 300 | 3-Tap | 6 |
CB2 | 113 | 450 | 300 | 3-Tap | 7 |
CB3 | 78 | 450 | 300 | 3-Tap | 8 |
CB4 | 90 | 450 | 300 | 3-Tap | 11 |
CB5 | 59 | 450 | 300 | 3-Tap | 11 |
CB6 | 58 | 450 | 300 | 3-Tap | 10 |
CB7 | 86 | 450 | 300 | 3-Tap | 13 |
CB8 | 87 | 450 | 300 | 3-Tap | 15 |
CB9 | 98 | 450 | 300 | 3-Tap | 10 |
CB10 | 66 | 450 | 300 | 3-Tap | 16 |
CB11 | 93 | 450 | 300 | 3-Tap | 13 |
CB12 | 99 | 450 | 300 | 3-Tap | 12 |
CB13 | 70 | 450 | 300 | 3-Tap | 10 |
CB14 | 72 | 450 | 300 | 3-Tap | 4 |
CB15 | 97 | 450 | 300 | 3-Tap | 8 |
CB16 | 71 | 450 | 300 | 3-Tap | 12 |
CB17 | 79 | 450 | 300 | 3-Tap | 9 |
CB18 | 80 | 450 | 300 | 3-Tap | 19 |
CB19 | 73 | 450 | 300 | 3-Tap | 13 |
CB20 | 82 | 450 | 300 | 3-Tap | 14 |
Figure 10 clearly shows the better justification of the voltage profile due to more efficient reactive power compensation.
Furthermore, referring to the Figure 11a which represents the reactive load duration curve before and after optimization, it signifies that the first scenario outperforms the second methodology by more compensation of the reactive power. Table 3, is summarizing the comparison of the optimisation with the base case. Total loss of the network decreased from 117 MWh to 104.97 and 109.31 MWh.
Scenario | Total Loss [MWh] | Minimum Voltage (Mean) | CB Daily Switching | Annual Energy Capacity Release [MWh] | Total Annual Operational Cost [USD] | Annual Saving [USD] |
Base case | 117.74 | 0.9026 | 0 | 0 | 1.103 × 107 | 0 |
First Scenario | 104.97 | 0.9075 | 220 | 4.07 × 103 | 1.074 × 107 | 2.81 × 105 |
Second Scenario | 109.31 | 0.9131 | 221 | 3.20 × 103 | 1.086 × 107 | 1.70 × 105 |
Obtaining significant amount of annual energy capacity release leads to decrease total operational cost in both scenario. in addition, the annual saving of 2.81 × 105 and 1.7 × 105 are achievable in the first and second scenario.
Also, the hourly mean voltage and energy loss before and after optimization of the two scenarios are comparatively plotted and graphically illustrated in Figure 11b, c, respectively. The hourly mean voltage is improved to 0.9075 and 0.9131 in the first and second scenario from 0.9026 in the base case, respectively. However, the hybrid methodology in the first scenario outperforms the simultaneous allocation method in terms of power loss reduction as demonstrated.
Finally, It is worth mentioning that the computation time as an essential factor to evaluate the optimization methodology particularly for the proposed problem of allocating fixed and switching capacitors is described as follow.
In the first scenario, due to conducting sensitivity analysis for site selection and thus limiting the decision variables to size and switching of capacitors only the optimization performs faster. In the meantime, the second scenario with additional decision variables for site selection and wider search space dimension applies less efficient. In concluding the first scenario with limiting search space utilizing sensitivity analysis and 8.5 hours elapsed time outperforms the second scenario taking 12.3 hours. However, the time also depends on optimal coding as well as hardware robustness.
In this study, the optimal allocation of the automatic and fixed capacitor banks in a real distribution network is proposed and deployed. The two essential factors; minimization of the total cost and switching steps of the capacitor banks in terms of the objective functions are considered in this technical analysis. The optimizations are conducted utilizing two methods. The first method with its two-step mechanism for placement and sizing separately demonstrated better results whereas the second method with lower complexity using only ϵ-MOGA also had good performance. The performance and results of the proposed algorithm for its first-time utilization in sizing and placement in a distribution network indicated its effectiveness and superiority in such complex and extensive distribution network. Based on the decisioned Pareto points, the optimal operation for capacitor banks size and switching are obtained successfully which shows significant improvement not only power quality in terms of voltage profile and power loss, but financially profitable by gaining considerable annual saving as well as energy capacity release.
The authors declare that there is no conflict of interest.
[1] |
Fruth V, Mitoseriu L, Berger D, et al. (2007) Preparation and characterization of BiFeO3 ceramic. Prog Solid State Ch 35: 193–202. doi: 10.1016/j.progsolidstchem.2007.01.019
![]() |
[2] |
Chengang X, Dunmin L, Kwok KW (2008) Structure, electrical properties and depolarization temperature of (Bi0.5Na0.5)TiO3–BaTiO3 lead-free piezoelectric ceramics. Solid State Sci 10: 934–940. doi: 10.1016/j.solidstatesciences.2007.11.003
![]() |
[3] |
Hagiyev MS, Ismaizade IH, Abiyev AK (1984) Pyroelectric properties of (Na½Bi½)TiO3 ceramics. Ferroelectrics 56: 215–217. doi: 10.1080/00150198408221371
![]() |
[4] |
Suchanicz J, Nowakowska-Malczyk M, Kania A, et al. (2021). Effects of electric field poling on structural, thermal, vibrational, dielectric and ferroelectric properties of Na0.5Bi0.5TiO3 single crystals. J Alloy Compd 854: 157227. doi: 10.1016/j.jallcom.2020.157227
![]() |
[5] |
Chen M, Xu Q, Kim BH, et al. (2008) Structure and electrical properties of (Na0.5Bi0.5)1–xBaxTiO3 piezoelectric ceramics. J Eur Ceram Soc 28: 843–849. doi: 10.1016/j.jeurceramsoc.2007.08.007
![]() |
[6] |
Wang G, Zhongming F, Murakami S, et al. (2019) Origin of the large electrostrain in BiFeO3–BaTiO3 based lead-free ceramics. J Mater Chem A 7: 21254–21263. doi: 10.1039/C9TA07904A
![]() |
[7] |
Wang D, Wang M, Liu F (2015) Sol-gel synthesis of Nd-doped BiFeO3 multiferroic and its characterization. Ceram Int 41: 8768–8772. doi: 10.1016/j.ceramint.2015.03.100
![]() |
[8] |
Li ZJ, Hou ZL, Song WL, et al. (2016) Mg-substitution for promoting magnetic and ferroelectric properties of BiFeO3 multiferroic nanoparticles. Mater Lett 175: 207–211. doi: 10.1016/j.matlet.2016.04.016
![]() |
[9] |
Cheng S, Zhang BP, Zhao L, et al. (2019) Enhanced insulating and piezoelectric properties of BiFeO3–BaTiO3–Bi0.5Na0.5TiO3 ceramics with high Curie temperature. J Am Ceram Soc 102: 7355–7365. doi: 10.1111/jace.16602
![]() |
[10] |
Dorcet V, Marchet P, Trolliard G (2007) Structural and dielectric studies of the Na0.5Bi0.5TiO3–BiFeO3 system. J Eur Ceram Soc 27: 4371–4374. doi: 10.1016/j.jeurceramsoc.2007.02.173
![]() |
[11] |
Wu J, Wang J (2009) Multiferroic behaviour and orientation dependence of lead-free (1–x)BiFeO3–x(Bi0.50Na0.50)TiO3 thin films. J Phys D Appl Phys 42: 195405. doi: 10.1088/0022-3727/42/19/195405
![]() |
[12] |
Hieno A, Sakamoto W, Moriya M, et al. (2011) Synthesis of BiFeO3–Bi0.5Na0.5TiO3 thin films by chemical solution deposition and their properties. Jpn J Appl Phys 50: 09NB04. doi: 10.7567/JJAP.50.09NB04
![]() |
[13] |
Ji WJ, Chen YB, Zhang ST, et al. (2012) Microstructure and electric properties of lead-free 0.8Bi1/2Na1/2TiO3–0.2Bi1/2K1/2TiO3 ceramics. Ceram Int 38: 1683–1686. doi: 10.1016/j.ceramint.2011.09.061
![]() |
[14] |
Kim C Y, Sekino T, Niihara K (2003) Synthesis of bismuth sodium titanate nanosized powders by solution/sol-gel process. J Am Ceram Soc 86: 1464–1467. doi: 10.1111/j.1151-2916.2003.tb03497.x
![]() |
[15] |
Ma YJ, Cho JH, Lee YH, et al. (2006) Hydrothermal synthesis of (Bi1/2Na1/2)TiO3 piezoelectric ceramics. Mater Chem Phys 98: 5–8. doi: 10.1016/j.matchemphys.2004.09.045
![]() |
[16] |
Van Hal HAM, Groen WA, Maassen S, et al. (2001) Mechanochemical synthesis of BaTiO3, Bi0.5Na0.5TiO3 and Ba2NaNb5O15 dielectric ceramics. J Am Ceram Soc 21: 1689–1692. doi: 10.1016/S0955-2219(01)00095-4
![]() |
[17] |
Patil KC, Aruna ST, Ekambaram S (1997) Combustion synthesis. Curr Opin Solid St M 2: 158–165. doi: 10.1016/S1359-0286(97)80060-5
![]() |
[18] | Fityk 0.9.2 a curve fitting and data analysis program, 2010. Available from: http://www.unipress.waw.pl/fityk/.Marcin Wojdyr. |
[19] | Larson AC, Von Dreele RB (2004) General Structure Analysis System (GSAS), Los Alamos National Laboratory Report LAUR 86-748. |
[20] | Cullity BD, Stock SR (2001) Elements of X-ray Diffraction, 3 Eds., New York: Prentice Hall Publication. |
[21] |
Rietveld HM (1967) Line profiles of neutron powder-diffraction peaks for structure refinement. Acta Crystallogr 22: 151–152. doi: 10.1107/S0365110X67000234
![]() |
[22] |
Warren BE, Averbach BL (1950) The effect of cold-work distortion on X-ray patterns. J Appl Phys 21: 595–599. doi: 10.1063/1.1699713
![]() |
[23] | Suryanarayana C, Norton MG (1998) Part I Basics, X-ray Diffraction: A Practical Approach, New York: Plenum Press. |
[24] | Xavier E (2004) Introduction to the behavior of ceramic pastes (in Spanish). Available from: https://www.scienceopen.com/document?vid=178d6249-68f8-445a-b6b6-19140255a435. |
[25] | Moreno R (2005) Rheology of ceramic suspensions. Available from: http://boletines.secv.es/upload/20070111131337.contenido_adicional_45[1].pdf. |
[26] | Nakamoto K (2008) Infrared and Raman Spectra of Inorganic and Coordination Compounds: Part A: Theory and Applications in Inorganic Chemistry, 6 Eds., John Wiley & Sons. |
[27] |
Chen Z, He X (2010) Low-temperature preparation of nanoplated bismuth titanate microspheres by a sol-gel-hydrothermal method. J Alloy Compd 497: 312–315. doi: 10.1016/j.jallcom.2010.03.053
![]() |
[28] |
Li JB, Wang H, Hou YD, et al. (2004) Low-temperature preparation of Na0.5Bi0.5TiO3 nano whiskers by a sol-gel-hydrothermal method. Nanotechnology 15: 777–780. doi: 10.1088/0957-4484/15/7/010
![]() |
[29] |
Ng CY, Razak KA (2011) Properties of praseodymium-doped bismuth potassium titanate (Bi0.5K0.5TiO3) synthesised using the soft combustion technique. J Alloy Compd 509: 942–947. doi: 10.1016/j.jallcom.2010.09.136
![]() |
[30] | Ardelean I, Cora S, Ioncu V (2006) Structural investigation of CuO–Bi2O3–B2O3 glasses by FT-IR, Raman and UV-VIS spectroscopies. Optoelectron Adv M 8: 1843–1847. |
[31] |
Ardelean I, Cora S, Rusu D (2008) EPR and FT-IR spectroscopic studies of Bi2O3–B2O3–CuO glasses. Physica B 403: 3682–3685. doi: 10.1016/j.physb.2008.06.016
![]() |
[32] |
Bhushan B, Basumallick A, Bandopadhyay SK, et al. (2009) Effect of alkaline earth metal doping on thermal, optical, magnetic and dielectric properties of BiFeO3 nanoparticles. J Phys D Appl Phys 42: 065004–065011. doi: 10.1088/0022-3727/42/6/065004
![]() |
[33] | Ramadevudu G (2011) FTIR and some physical properties of alkaline earth borate glasses containing heavy metal oxides. Int J Eng Sci Technol 3: 6998–7005. |
[34] |
Gurmeet L, Verma N (2014) Synthesis and characterization of BiFeO3 nanowires and their applications in dye-sensitized solar cells. Mat Sci Semicon Proc 21: 206–211. doi: 10.1016/j.mssp.2013.11.029
![]() |
[35] | Chiang YM, Birnie DP, Kingery V (1997) Physical Ceramics-Principles for Ceramic Science and Engineering, John Wiley & Sons. |
[36] | Karthik T, Rao TD, Srinivas A, et al. (2012) A-site cation disorder and Size variance effects on the physical properties of multiferroic Bi0.9RE0.1FeO3 ceramics (RE = Gd3+, Tb3+, Dy3+). arXiv: 1206.5606. Available from: https://arXiv.org/abs/1206.5606. |
[37] |
Reddy R, Rao R, Viswanath R (1989) Correlation between electronegativity differences and bond energies. J Am Chem Soc 111: 2914–2915. doi: 10.1021/ja00190a028
![]() |
[38] |
Jones GO, Thomas PA (2002) Investigation of the structure and phase transitions in the novel A-site substituted distorted perovskite compound Na0.5Bi0.5TiO3. Acta Crystallogr B 58: 168–178. doi: 10.1107/S0108768101020845
![]() |
[39] | Oxford Cryosystems, Crystallographica Search-Match, Version 2, 1, 1, 1. Available from: http://www.crystallographica.co.uk. |
[40] |
Kumar MM, Srinivas A, Suryanarayana SV (2000) Structure property relations in BiFeO3/BaTiO3 solid solutions. J Appl Phys 87: 855–862. doi: 10.1063/1.371953
![]() |
[41] |
Bhalla AS, Guo R, Roy R (2000) The perovskite structure-a review of its role in ceramic science and technology. Mater Res Innov 4: 3–26. doi: 10.1007/s100190000062
![]() |
[42] | Kayser GP (2014) New double perovskites obtained under extreme conditions of pressure and temperature [Doctoral Dissertation]. University Complutense of Madrid, Spain. |
[43] |
Wang D, Angel RJ (2011) Octahedral tilts, symmetry-adapted displacive modes and polyhedral volume ratios in perovskite structures. Acta Crystallogr B 67: 302–314. doi: 10.1107/S0108768111018313
![]() |
[44] | Rao KS, Rajulu KCV, Tilak B, et al. (2010) Effect of Ba2+ in BNT ceramics on dielectric and conductivity properties. Nat Sci 2: 357–367. |
[45] |
Lee WC, Huang CY, Tsao LK, et al. (2009) Chemical composition and tolerance factor at the morphotropic phase boundary in (Bi0.5Na0.5)TiO3-based piezoelectric ceramics. J Eur Ceram Soc 29: 1443–1448. doi: 10.1016/j.jeurceramsoc.2008.08.028
![]() |
[46] |
Ramana EV, Suryanarayana SV, Bhima ST (2010) Synthesis and magnetoelectric studies on Na0.5Bi0.5TiO3–BiFeO3 solid solution ceramics. Solid State Sci 12: 956–962. doi: 10.1016/j.solidstatesciences.2010.02.009
![]() |
[47] |
Shannon RD (1976) Revised effective ionic radii and systematic studies of interatomic distances in halides and chalcogenides. Acta Crystallogr A 32: 751–767. doi: 10.1107/S0567739476001551
![]() |
[48] |
Shahmoradi Y, Souri D (2019) Growth of silver nanoparticles within the tellurovanadate amorphous matrix: Optical band gap and band tailing properties, beside the Williamson–Hall estimation of crystallite size and lattice strain. Ceram Int 5: 7857–7864. doi: 10.1016/j.ceramint.2019.01.094
![]() |
[49] | Izumi F, Ikeda T (2014) Implementation of the Williamson–Hall and Halder–Wagner Methods into RIETAN-FP, Nagoya Institute of Technology, 3: 33–38. |
[50] | Patle LB, Labhane PK, Huse VR, et al. (2015) Structural analysis of Cu doped TiO2 nanoparticles using Williamson–Hall method. IJSRSET 1: 66–70. |
[51] | Suryanarayana C, Norton MG (1998) Determination of crystallite size and lattice strain, X-ray Diffraction: A Practical Approach, New York: Plenum Press. |
[52] |
Thompson P, Cox DE, Hastings JB (1987) Rietveld refinement of Debye–Scherrer synchrotron X-ray data from Al2O3. J Appl Crystallogr 20: 79–83. doi: 10.1107/S0021889887087090
![]() |
[53] |
Ramana E, Mahajan A, Graca M, et al. (2014) Ferroelectric and magnetic properties of magnetoelectric (Na0.5Bi0.5)TiO3–BiFeO3 synthesized by acetic acid assisted sol-gel method. J Eur Ceram Soc 34: 4201–4211. doi: 10.1016/j.jeurceramsoc.2014.06.027
![]() |
[54] |
Dorcet V, Marchet P, Peña O, et al. (2009) Properties of the solid solution (1—x)Na0.5Bi0.5TiO3–(x)BiFeO3. J Magn Magn Mater 321: 1762–1766. doi: 10.1016/j.jmmm.2009.02.014
![]() |
[55] |
Yao J, Ge W, Luo L, et al. (2010) Hierarchical domains in Na1/2Bi1/2TiO3 single crystals: Ferroelectric phase transformations within the geometrical restrictions of a ferroelastic inheritance. Appl Phys Lett 96: 222905. doi: 10.1063/1.3443717
![]() |
[56] |
Lee JH, Lee GJ, Pham TL, et al. (2020) Suppression of dielectric loss at high temperature in (Bi1/2Na1/2)TiO3 ceramic by controlling A-site cation deficiency and heat treatment. J Sens Sci Technol 29: 7–13. doi: 10.5369/JSST.2019.29.1.7
![]() |
[57] |
Dorcet V, Trolliard G, Boullay P (2008) Reinvestigation of phase transitions in Na0.5Bi0.5TiO3 by TEM. Part I: First order rhombohedral to orthorhombic phase transition. Chem Mater 20: 5061–5073. doi: 10.1021/cm8004634
![]() |
[58] |
He H, Lu X, Li M, et al. (2020) Thermal and compositional driven relaxor ferroelectric behaviors of lead-free Bi0.5Na0.5TiO3–SrTiO3 Ceramics. J Mater Chem C 7: 2411–2418. doi: 10.1039/C9TC04864B
![]() |
[59] |
Li W, Chen K, Yao Y, et al. (2004) Correlation among oxygen vacancies in bismuth titanate ferroelectric ceramics. Appl Phys Lett 85: 4717–4719. doi: 10.1063/1.1823583
![]() |
1. | Mikaeel Ahmadi, Mir Sayed Shah Danish, Tomonobu Senjyu, Habibullah Fedayee, Najib Rahman Sabory, Atsushi Yona, 2021, Chapter 4, 978-981-15-7178-7, 47, 10.1007/978-981-15-7179-4_4 | |
2. | Mohamad Nur Hidayat Mat, Nor Zelawati Asmuin, Md Faisal Md Basir, Mohammad Reza Safaei, Mohd Shareduwan Mohd Kasihmuddin, Taufiq Khairi Ahmad Khairuddin, Marjan Godarzi, Optimizing nozzle convergent angle using central composite design on the particle velocity and acoustic power level for single-hose dry ice blasting nozzle, 2020, 1388-6150, 10.1007/s10973-020-10083-5 | |
3. | Mikaeel Ahmadi, Oludamilare Bode Adewuyi, Mir Sayed Shah Danish, Paras Mandal, Atsushi Yona, Tomonobu Senjyu, Optimum coordination of centralized and distributed renewable power generation incorporating battery storage system into the electric distribution network, 2021, 125, 01420615, 106458, 10.1016/j.ijepes.2020.106458 | |
4. | Mazdak Ebadi, Mohammad Bayat, Hossain Asadi, Evaluating maximum permissible feeder current in capacitive compensated harmonic polluted networks introducing Apparent RMS Current Ratio Index (ACRI), 2020, 187, 03787796, 106511, 10.1016/j.epsr.2020.106511 | |
5. | Pramod Kumar, Nagendra Kumar Swarnkar, Ahmed Ali, Om Prakash Mahela, Baseem Khan, Divya Anand, Julien Brito Ballester, Transmission Network Loss Reduction and Voltage Profile Improvement Using Network Restructuring and Optimal DG Placement, 2023, 15, 2071-1050, 976, 10.3390/su15020976 | |
6. | Amandeep Gill, Pushpendra Singh, Jalpa H. Jobanputra, Mohan Lal Kolhe, Placement analysis of combined renewable and conventional distributed energy resources within a radial distribution network, 2022, 10, 2333-8334, 1216, 10.3934/energy.2022057 | |
7. | Evan S. Jones, Nicholas Jewell, Yuan Liao, Dan M. Ionel, Optimal Capacitor Placement and Rating for Large-Scale Utility Power Distribution Systems Employing Load-Tap-Changing Transformer Control, 2023, 11, 2169-3536, 19324, 10.1109/ACCESS.2023.3244572 | |
8. | Shaikh Sohail Mohiyodin, Rajesh Maharudra Patil, Dr MS Nagaraj, Northern goshawk optimization for optimal reactive power compensation in photovoltaic low-voltage radial distribution networks, 2024, 5, 26664127, 206, 10.1016/j.susoc.2024.07.002 | |
9. | Zeeshan Aslam, Nadeem Javaid, Muhammad Umar Javed, Muhammad Aslam, Abdulaziz Aldegheishem, Nabil Alrajeh, A new clustering-based semi-supervised method to restrict the users from anomalous electricity consumption: supporting urbanization, 2024, 106, 0948-7921, 6431, 10.1007/s00202-024-02362-3 | |
10. | Sourav Mondal, Mala De, A graph theory-based solution method for capacitor bank and voltage regulator allocation problems in an unbalanced distribution system, 2024, 45, 0143-0750, 10.1080/01430750.2024.2304727 | |
11. | Alexey Mikhaylov, 2024, Chapter 3, 978-3-031-53573-4, 69, 10.1007/978-3-031-53574-1_3 | |
12. | Mohammad Hamid Ahadi, 2024, Chapter 4, 978-3-031-53573-4, 87, 10.1007/978-3-031-53574-1_4 |
CBs | Optimum Location Sensitivity | Fix CB | Auto CB | Configuration of Auto-switching | No of Switching Per Day |
CB1 | 4 | 600 | 150 | On/Off | 8 |
CB2 | 33 | 450 | 300 | 3-Tap | 7 |
CB3 | 160 | 600 | 150 | On/Off | 12 |
CB4 | 161 | 450 | 300 | 3-Tap | 12 |
CB5 | 162 | 450 | 300 | 3-Tap | 7 |
CB6 | 34 | 600 | 150 | On/Off | 12 |
CB7 | 159 | 450 | 300 | 3-Tap | 10 |
CB8 | 134 | 450 | 300 | 3-Tap | 13 |
CB9 | 118 | 450 | 300 | 3-Tap | 4 |
CB10 | 107 | 450 | 300 | 3-Tap | 12 |
CB11 | 59 | 600 | 150 | On/Off | 13 |
CB12 | 49 | 450 | 300 | 3-Tap | 12 |
CB13 | 128 | 450 | 300 | 3-Tap | 7 |
CB14 | 64 | 450 | 300 | 3-Tap | 14 |
CB15 | 8 | 450 | 300 | 3-Tap | 14 |
CB16 | 42 | 450 | 300 | 3-Tap | 12 |
CB17 | 37 | 450 | 300 | 3-Tap | 17 |
CB18 | 79 | 450 | 300 | 3-Tap | 13 |
CB19 | 90 | 450 | 300 | 3-Tap | 11 |
CB20 | 67 | 450 | 300 | 3-Tap | 10 |
CBs | Optimum Location ϵ-MOGA | Fix CB | Auto CB | Configuration of Auto-switching | No of Switching Per Day |
CB1 | 65 | 450 | 300 | 3-Tap | 6 |
CB2 | 113 | 450 | 300 | 3-Tap | 7 |
CB3 | 78 | 450 | 300 | 3-Tap | 8 |
CB4 | 90 | 450 | 300 | 3-Tap | 11 |
CB5 | 59 | 450 | 300 | 3-Tap | 11 |
CB6 | 58 | 450 | 300 | 3-Tap | 10 |
CB7 | 86 | 450 | 300 | 3-Tap | 13 |
CB8 | 87 | 450 | 300 | 3-Tap | 15 |
CB9 | 98 | 450 | 300 | 3-Tap | 10 |
CB10 | 66 | 450 | 300 | 3-Tap | 16 |
CB11 | 93 | 450 | 300 | 3-Tap | 13 |
CB12 | 99 | 450 | 300 | 3-Tap | 12 |
CB13 | 70 | 450 | 300 | 3-Tap | 10 |
CB14 | 72 | 450 | 300 | 3-Tap | 4 |
CB15 | 97 | 450 | 300 | 3-Tap | 8 |
CB16 | 71 | 450 | 300 | 3-Tap | 12 |
CB17 | 79 | 450 | 300 | 3-Tap | 9 |
CB18 | 80 | 450 | 300 | 3-Tap | 19 |
CB19 | 73 | 450 | 300 | 3-Tap | 13 |
CB20 | 82 | 450 | 300 | 3-Tap | 14 |
Scenario | Total Loss [MWh] | Minimum Voltage (Mean) | CB Daily Switching | Annual Energy Capacity Release [MWh] | Total Annual Operational Cost [USD] | Annual Saving [USD] |
Base case | 117.74 | 0.9026 | 0 | 0 | 1.103 × 107 | 0 |
First Scenario | 104.97 | 0.9075 | 220 | 4.07 × 103 | 1.074 × 107 | 2.81 × 105 |
Second Scenario | 109.31 | 0.9131 | 221 | 3.20 × 103 | 1.086 × 107 | 1.70 × 105 |
CBs | Optimum Location Sensitivity | Fix CB | Auto CB | Configuration of Auto-switching | No of Switching Per Day |
CB1 | 4 | 600 | 150 | On/Off | 8 |
CB2 | 33 | 450 | 300 | 3-Tap | 7 |
CB3 | 160 | 600 | 150 | On/Off | 12 |
CB4 | 161 | 450 | 300 | 3-Tap | 12 |
CB5 | 162 | 450 | 300 | 3-Tap | 7 |
CB6 | 34 | 600 | 150 | On/Off | 12 |
CB7 | 159 | 450 | 300 | 3-Tap | 10 |
CB8 | 134 | 450 | 300 | 3-Tap | 13 |
CB9 | 118 | 450 | 300 | 3-Tap | 4 |
CB10 | 107 | 450 | 300 | 3-Tap | 12 |
CB11 | 59 | 600 | 150 | On/Off | 13 |
CB12 | 49 | 450 | 300 | 3-Tap | 12 |
CB13 | 128 | 450 | 300 | 3-Tap | 7 |
CB14 | 64 | 450 | 300 | 3-Tap | 14 |
CB15 | 8 | 450 | 300 | 3-Tap | 14 |
CB16 | 42 | 450 | 300 | 3-Tap | 12 |
CB17 | 37 | 450 | 300 | 3-Tap | 17 |
CB18 | 79 | 450 | 300 | 3-Tap | 13 |
CB19 | 90 | 450 | 300 | 3-Tap | 11 |
CB20 | 67 | 450 | 300 | 3-Tap | 10 |
CBs | Optimum Location ϵ-MOGA | Fix CB | Auto CB | Configuration of Auto-switching | No of Switching Per Day |
CB1 | 65 | 450 | 300 | 3-Tap | 6 |
CB2 | 113 | 450 | 300 | 3-Tap | 7 |
CB3 | 78 | 450 | 300 | 3-Tap | 8 |
CB4 | 90 | 450 | 300 | 3-Tap | 11 |
CB5 | 59 | 450 | 300 | 3-Tap | 11 |
CB6 | 58 | 450 | 300 | 3-Tap | 10 |
CB7 | 86 | 450 | 300 | 3-Tap | 13 |
CB8 | 87 | 450 | 300 | 3-Tap | 15 |
CB9 | 98 | 450 | 300 | 3-Tap | 10 |
CB10 | 66 | 450 | 300 | 3-Tap | 16 |
CB11 | 93 | 450 | 300 | 3-Tap | 13 |
CB12 | 99 | 450 | 300 | 3-Tap | 12 |
CB13 | 70 | 450 | 300 | 3-Tap | 10 |
CB14 | 72 | 450 | 300 | 3-Tap | 4 |
CB15 | 97 | 450 | 300 | 3-Tap | 8 |
CB16 | 71 | 450 | 300 | 3-Tap | 12 |
CB17 | 79 | 450 | 300 | 3-Tap | 9 |
CB18 | 80 | 450 | 300 | 3-Tap | 19 |
CB19 | 73 | 450 | 300 | 3-Tap | 13 |
CB20 | 82 | 450 | 300 | 3-Tap | 14 |
Scenario | Total Loss [MWh] | Minimum Voltage (Mean) | CB Daily Switching | Annual Energy Capacity Release [MWh] | Total Annual Operational Cost [USD] | Annual Saving [USD] |
Base case | 117.74 | 0.9026 | 0 | 0 | 1.103 × 107 | 0 |
First Scenario | 104.97 | 0.9075 | 220 | 4.07 × 103 | 1.074 × 107 | 2.81 × 105 |
Second Scenario | 109.31 | 0.9131 | 221 | 3.20 × 103 | 1.086 × 107 | 1.70 × 105 |