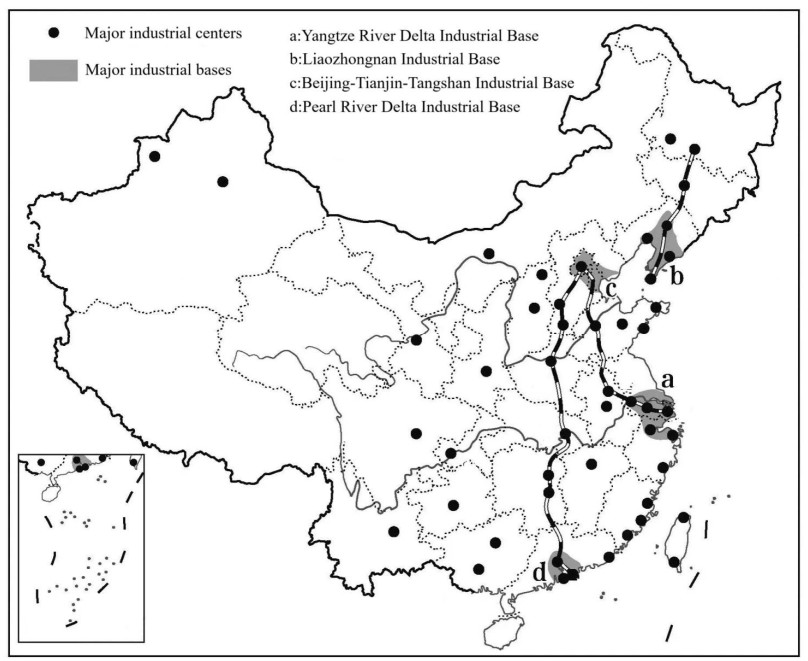
With the rapid development of global industrialization, the surplus and waste heat generated during industrial production processes is becoming increasingly abundant, making the utilization of industrial surplus and waste heat a focal point of current research. The main challenge facing the utilization of industrial surplus and waste heat is the spatial and temporal mismatch between the large amount of industrial waste heat generated during the non-heating season and the heating demand during the heating season. Seasonal energy storage technology enables energy to be stored and transferred over long periods and large areas. The application of this technology in the field of industrial surplus and waste heat utilization can effectively reduce energy waste and greenhouse gas emissions, thereby lowering the costs of industrial production. Here, we provide an overview of the current status of the utilization of surplus and waste heat resources in six industrial scenarios: Thermal power plants, nuclear power plants, steel mills, oil refineries, coal mines, and data centers. The research progress of sensible heat storage (SHS), latent heat storage (LHS), and thermochemical storage (THS) is analyzed. The advantages and disadvantages of different energy storage technologies are discussed. Application cases combining industrial waste heat recovery with seasonal energy storage are enumerated and analyzed. Our aim is to provide a reference for research and practice in related fields.
Citation: Jialin Song, Haoyi Zhang, Yanming Zhang, Zhongjiao Ma, Mingfei He. Research progress on industrial waste heat recycling and seasonal energy storage[J]. AIMS Energy, 2025, 13(1): 147-187. doi: 10.3934/energy.2025006
[1] | John G Rogers . Paper making in a low carbon economy. AIMS Energy, 2018, 6(1): 187-202. doi: 10.3934/energy.2018.1.187 |
[2] | Khadim Ndiaye, Stéphane Ginestet, Martin Cyr . Thermal energy storage based on cementitious materials: A review. AIMS Energy, 2018, 6(1): 97-120. doi: 10.3934/energy.2018.1.97 |
[3] | Faris Elmanakhly, Andre DaCosta, Brittany Berry, Robert Stasko, Michael Fowler, Xiao-Yu Wu . Hydrogen economy transition plan: A case study on Ontario. AIMS Energy, 2021, 9(4): 775-811. doi: 10.3934/energy.2021036 |
[4] | D.M. Reddy Prasad, R. Senthilkumar, Govindarajan Lakshmanarao, Saravanakumar Krishnan, B.S. Naveen Prasad . A critical review on thermal energy storage materials and systems for solar applications. AIMS Energy, 2019, 7(4): 507-526. doi: 10.3934/energy.2019.4.507 |
[5] | Eduardo Enrique Martinez Jorges, António M.N. Quintino, Diogo M.F. Santos . Economic analysis of lithium-ion battery recycling. AIMS Energy, 2023, 11(5): 960-973. doi: 10.3934/energy.2023045 |
[6] | Mojgan Pouralizadeh, Aliraza Amirtaimoori, Rossana Riccardi, Mohsen Vaez-Ghasemi . Supply chain performance evaluation in the presence of undesirable products: A case on power industry. AIMS Energy, 2020, 8(1): 48-80. doi: 10.3934/energy.2020.1.48 |
[7] | Obafemi O. Olatunji, Stephen Akinlabi, Nkosinathi Madushele, Paul A. Adedeji, Ishola Felix . Multilayer perceptron artificial neural network for the prediction of heating value of municipal solid waste. AIMS Energy, 2019, 7(6): 944-956. doi: 10.3934/energy.2019.6.944 |
[8] | Mojgan Pouralizadeh . A DEA model to sustainability improvement of the electricity supply chain in presence dual-role factors and undesirable outputs: A case on the power industry. AIMS Energy, 2020, 8(4): 580-614. doi: 10.3934/energy.2020.4.580 |
[9] | Eman S. Maayah, Hamzeh M. Duwairi, Banan Maayah . Analytical model of solar energy storage using non—Newtonian Fluid in a saturated porous media in fully developed region: carboxymethyl cellulose (CMC) and graphite model. AIMS Energy, 2021, 9(2): 213-237. doi: 10.3934/energy.2021012 |
[10] | Mohamed Hamdi, Hafez A. El Salmawy, Reda Ragab . Optimum configuration of a dispatchable hybrid renewable energy plant using artificial neural networks: Case study of Ras Ghareb, Egypt. AIMS Energy, 2023, 11(1): 171-196. doi: 10.3934/energy.2023010 |
With the rapid development of global industrialization, the surplus and waste heat generated during industrial production processes is becoming increasingly abundant, making the utilization of industrial surplus and waste heat a focal point of current research. The main challenge facing the utilization of industrial surplus and waste heat is the spatial and temporal mismatch between the large amount of industrial waste heat generated during the non-heating season and the heating demand during the heating season. Seasonal energy storage technology enables energy to be stored and transferred over long periods and large areas. The application of this technology in the field of industrial surplus and waste heat utilization can effectively reduce energy waste and greenhouse gas emissions, thereby lowering the costs of industrial production. Here, we provide an overview of the current status of the utilization of surplus and waste heat resources in six industrial scenarios: Thermal power plants, nuclear power plants, steel mills, oil refineries, coal mines, and data centers. The research progress of sensible heat storage (SHS), latent heat storage (LHS), and thermochemical storage (THS) is analyzed. The advantages and disadvantages of different energy storage technologies are discussed. Application cases combining industrial waste heat recovery with seasonal energy storage are enumerated and analyzed. Our aim is to provide a reference for research and practice in related fields.
Abbreviations: ATES: Aquifer thermal energy storage; LHS: Latent heat storage; BF: Base fluid; LP: Low pressure; BORC: Basic organic Rankine cycle; BTES: Borehole Thermal Energy Storage; CFD: Computational Fluid Dynamics; CHP: Combined Heat and Power; CHP-HBP: CHP with High-Back Pressure Steam Turbine; DW: Distilled water; EG: Ethylene glycol; HP: High Pressure; NF: Nanofluid; ORC: Organic Rankine cycle; PCM: Phase-change material; PTES: Pit Thermal Energy Storage; SHS: Sensible heat storage; STES: Seasonal thermal energy storage; THS: Thermochemical heat storage; TTES: Tank thermal energy storage
Nomenclature: r: revenue per kW of deep peak shaving capacity during the valley period, $/kW; t: utilization hours of power peak-shaving equipment during the valley period, h
Heating is an essential energy service for the building and industrial sectors, accounting for one-third of the global total final energy consumption, or nearly 145 exajoules, of which approximately 75% is derived from fossil fuels [1]. Heating accounts for 24% of the global emissions from the energy sector. China's share of global heat consumption is 33%, playing a significant role in shaping global trends; within this, the industrial sector in China accounts for as high as 40% of global heat consumption, while the building sector's heat consumption constitutes about 20% of the global total. With the rapid development of the global economy, the energy demand is growing, and the environmental pollution problem is becoming more and more serious. Since 2010, the urban area has been increasing yearly, and the length of heating pipelines has also increased accordingly. The length of centralized heating networks has grown from less than 100,000 kilometers in 2000 to nearly 500,000 kilometers in 2020 [2]. The required heat for heating has also increased year by year, and the issue of environmental pollution has become increasingly severe. Figure 1 shows the major industrial centers and industrial bases in China, among which the central and southern Liaoning region is the largest heavy industrial base. If the waste heat from industrial processes can be effectively utilized for heating, it will significantly reduce the heating burden in the northern regions of China and achieve sustainable energy utilization [3]. To further harness industrial waste heat, it is necessary to estimate the potential of industrial waste heat. Gui-Bing Hong et al. [4] evaluated a dataset of over 11,000 waste heat emissions across regions in Taiwan. Through a bottom-up analysis, they determined the theoretical waste heat potential in Taiwan to be 89.66 PJ/y, laying the foundation for future utilization. Seasonal energy storage technology is an effective means to address the imbalance between energy supply and demand [5]. By recovering and storing industrial waste heat during the spring, summer, and autumn, it can be released during peak energy demand periods (winter), thereby achieving optimized energy allocation and sustainable utilization [6]. The recovery of industrial waste heat and the technology of seasonal storage provide effective pathways to enhance energy utilization efficiency and to moderate the conflict between energy supply and demand [7]. Integrating these two approaches is expected to facilitate sustainable energy utilization, enhance energy efficiency, and promote the development of green industry [8].
The scientific research community prioritizes the reduction of greenhouse gas emissions from industrial activities to decrease the use of fossil fuels. Green and low-carbon development is a significant direction for the energy development and transformation in today's world [9]. Advancing the clean utilization of fossil energy and fully exploiting and utilizing renewable energy sources is an inevitable path. There are several types of renewable energy, including biomass, wind, and solar energy. However, due to the intermittency of renewable energy sources such as wind and solar energy [10], the issue of mismatch between energy supply and demand has led to a severe phenomenon of curtailed green electricity, particularly in the form of abandoned wind and solar power in our country. To effectively store energy, a proposal has been put forward to convert the generated electricity into valuable chemicals and fuels required by industry. Green hydrogen has always been considered a promising alternative to fossil fuels [11]. Hydrogen has a high energy density, which means that under the same mass condition, hydrogen can store more energy than most batteries. Moreover, hydrogen can be stored for a long time without any significant energy loss, making it highly suitable for long-term energy storage. Hydrogen can be produced through various methods, including electrolysis of water. If renewable energy sources are used to power the electrolysis process, the production of green hydrogen can be achieved, which represents a sustainable means of energy storage. Ajeeb et al. [12] conducted a study comparing two hydrogen production via electrolysis technologies: pressurized alkaline electrolysis and capillary-fed alkaline electrolysis. The environmental impact of a green hydrogen production project with an expected operational life of 20 years and a capacity of 60 MW was assessed using SimaPro. Among the 16 environmental categories studied, including construction, disposal, operation, and power supply, the capillary-fed alkaline electrolysis technology demonstrated a lower potential environmental impact, approximately 17% lower than the pressurized alkaline electrolysis technology when considering the overall impact.
Razi et al. [13] conducted a comparative assessment of various solar hydrogen production technologies using two sets of criteria. The first set included environmental impact and hydrogen production costs. The second set comprised energy and energy efficiency, sustainability indices, and hydrogen production rates. The results indicated that high-temperature energy methods had higher efficiency and hydrogen production rates, while also posing greater environmental harm. Photon and bio-chemical energy routes were more environmentally friendly, but less efficient. Perhaps the compatibility of environmental protection and efficiency could be a direction for future research.
In recent years, environmental protection and the enhancement of energy efficiency have become focal points of global concern [14]. Against this backdrop, the recovery of industrial waste heat as an effective means to improve energy efficiency and reduce environmental pollution has received widespread attention. As shown in Tables 1–3, China's industrial sector possesses a vast amount of waste heat resources, which still have considerable development potential. According to statistics, the exploitable waste heat resources account for approximately 15% to 30% of the total energy consumption.
Industries | Waste heat resources | Waste heat recovery rate |
Thermal power generation | Flue gas, spent steam condensation waste heat | Above 50% |
Iron and steel metallurgy | Slag flushing water, blast furnace exhaust gas, etc. | Above 30% |
Petroleum | Oil production wastewater | 30%~40% |
Chemical industry | Process cooling water, industrial wastewater, exhaust gas, etc. | Above 30% |
Industries | Production volume/10,000 t | Waste heat resources per unit of product/(gce/t) |
Thermal power generation | 100,739 | 571 |
Iron and steel metallurgy | 85,236 | 260 |
Petroleum and chemical | 79,135 | 1,396 |
Industries | Total amount of low-temperature waste heat resources/10,000 tce | Utilizable low-temperature waste heat resources/10,000 tce |
Thermal power generation | 43,906 | 34,833 |
Iron and steel metallurgy | 10,734 | 7,633 |
Petroleum and chemical | 11,573 | 8,370 |
Figure 2 is a schematic diagram of a traditional Combined Heat and Power with High-Back Pressure Steam Turbine (CHP-HBP) system. To improve the flexibility of thermal power plants, peak shaving and valley filling based on heating demand is an inevitable trend. There are four primary methods of peak shaving [15]: The Electric boiler method [16], the direct steam extraction method, the absorption heat pump waste heat recovery method [17], and the electric heat pump waste heat recovery method [18]. Figure 3 shows the relationship between the revenue per kW of the deep peak shaving capacity(r) and the utilization hours of peak-shaving equipment during the valley period for the four peak shaving methods(t). This can be calculated from the figure, using the peak-shaving depth, which is not limited for both the electric boiler method and the waste heat recovery method using electric heat pumps. The maximum peak-shaving depth for direct steam extraction method and the absorption heat pump waste heat recovery method is approximately 20% of the rated power generation output. Wang et al. [19] selected the most favorable method for each power peak-shaving scenario to improve the power peak-shaving capability. The research indicates that the waste heat recovery method using electric heat pumps has a significant peak-shaving capacity, capable of meeting the deep peak-shaving demand for up to 360 hours of continuous duration. Therefore, large-scale, long-term seasonal energy storage projects are needed to store energy during periods of low demand for use during high-demand seasons in the future. Peak shaving and valley filling work is used flatten the load curve by reducing peak loads and shifting them to times of lower demand, thereby reducing the operation of expensive power plants [20].
Cogeneration plants generate a significant amount of high-temperature waste heat during the electricity generation process. China's cogeneration waste heat recovery and utilization rate stands at approximately 60%, leaving substantial room for improvement in both spatial and temporal coordination. We propose combining industrial waste heat recovery with seasonal thermal storage technology to address the issue of mismatch between supply and demand. Industrial facilities such as steel mills, data centers, and coal mine shafts also produce a significant amount of waste heat, which, if effectively utilized, can contribute to reducing energy consumption.
Seasonal energy storage technology involves utilizing underground heat storage, water body heat storage, and other methods to store surplus energy during off-peak hours (summer) and release it during peak hours (winter), in order to achieve balanced energy utilization. Improved seasonal storage technology helps to reconcile the disparity between energy supply and demand, enhance energy utilization efficiency, and lower energy costs.
Combining waste heat recovery with cross-seasonal storage technology can reduce reliance on fossil fuels and promote the development of renewable energy. Industrial waste heat recovery can effectively mitigate greenhouse gas emissions [21], reduce environmental pollution, and also enhance economic returns. Pello Larrinaga [22] and his colleagues used a case study approach to assess the potential for industrial waste heat recovery in the Basque Autonomous Community (located in northern Spain). Their estimates suggest that there is a significant amount of waste heat available, with 36% of the waste heat having temperatures above 500 ℃. The study highlights that there is a considerable amount of energy being wasted in industries such as steel and petrochemicals, waiting to be recovered. These findings underscore the opportunity for these industries to implement waste heat recovery systems to improve energy efficiency and reduce operational costs. Kristina [23] and her colleagues analyzed 107 industrial heat recovery projects in Sweden. They found that the average operating duration of ongoing collaborations was 18.2 years. For collaborations that had been terminated, the average operating duration was 13.3 years. Two-thirds of the terminated collaborations had lasted beyond the investment payback period, indicating that most of the projects were profitable. This analysis provides valuable insights into the financial viability and longevity of industrial heat recovery projects, suggesting that such initiatives can be a sound investment with long-term benefits for the industry. Moreover, seasonal storage technology contributes to decreased energy consumption and mitigates environmental pollution [24]. Guerra [25] and colleagues have proposed an integrated techno-economic assessment method to explore the cost competitiveness of seasonal energy storage technologies, taking into account factors such as cost, storage duration, and efficiency. The results indicated that for the Western United States power system, pump storage and compressed air energy storage with a discharge time of 1 day are expected to be cost-competitive in the near future. Based on forecasts of future energy costs, storage technologies with longer durations may also become cost-effective. This research is significant because it provides a framework for evaluating the economic viability of different energy storage solutions, which is crucial for the integration of variable renewable energy sources like solar and wind into the grid. By understanding the cost dynamics of storage technologies, policymakers and industry stakeholders can make informed decisions about investments in energy infrastructure that will support a sustainable and resilient energy system. In data centers, waste heat recovery technology can be employed to capture and utilize the heat generated by servers, thereby reducing reliance on traditional energy sources and fostering the advancement of renewable energy. By capturing and utilizing waste heat from coal mine shafts, the energy consumption of coal mine operations can be minimized, leading to a reduction in greenhouse gas emissions. Integrating these two technologies contributes to the establishment of an environmentally friendly, low-carbon, and sustainable energy system, facilitating the realization of sustainable development. By recovering and storing waste heat from the iron and steel plant, it enables optimal energy allocation, reduces energy consumption, and promotes sustainable development within the facility. It can efficiently manage energy supply and demand, lower energy expenses, and enhance economic efficiency for enterprises. In regions characterized by high winter heating demand, the implementation of seasonal storage technology for excess heat can lead to reduced energy costs, as the stored heat can be released during peak heating hours.
The potential for energy conservation and environmental benefits is significant when industrial waste heat recovery is combined with seasonal storage. Here we aim to provide a comprehensive overview of the recent advancements in seasonal energy storage through industrial waste heat recovery, analyze the merits and drawbacks of diverse energy storage technologies, and offer insights into future development directions and application prospects.
Industrial waste heat refers to the thermal energy produced as a byproduct of industrial processes that is not directly utilized. This type of heat typically arises from heat exchange inindustrial equipment and processes, such as combustion, chemical reactions, and equipment operation. Industrial waste heat exists in various forms [26,27], including high-temperature flue gas, cooling water, waste steam, slag, products, and by-products. The harnessing of industrial waste heat involves capturing the thermal energy that is not directly utilized and converting it into usable thermal or electrical energy through appropriate technologies and equipment for applications such as heating, cooling, power generation, and other industrial processes. This not only reduces energy waste and enhances energy utilization efficiency but also mitigates environmental pollution and decreases greenhouse gas emissions. The key to utilizing industrial waste heat lies in the efficient and cost-effective recovery and use of this thermal energy. This typically involves a combination of factors, including the characteristics of the waste heat source, the feasibility of the utilization technology, economic considerations, and compatibility with existing industrial processes. This paper outlines the utilization of waste heat in six industries: Thermal power plants, nuclear power plants, oil refineries, iron and steel plants, coal mines, and data centers.
Thermal power plants, which utilize coal as fuel, generate two forms of waste heat during the power generation process: Flue gas waste heat and exhaust steam waste heat. If not reclaimed, a substantial amount of thermal energy would be wasted. The recovery of this waste heat can enhance the energy efficiency of heating units and reduce the heating burden on the power plant [28].
Flue gas waste heat refers to the substantial amount of thermal energy contained in the flue gas produced by the combustion of coal or gas in a boiler within a thermal power plant. Typically, this heat is released into the atmosphere through a chimney, a process that results in flue gas waste heat. The temperature of the flue gas is usually high, often reaching 140 ℃ or more, and thus it contains a significant amount of recoverable thermal energy [29]. High-temperature flue gas contains dust, acidic gases, and other harmful substances. If emitted directly into the atmosphere, it would cause air pollution, endanger human health, and damage the ecological environment. It also implies a significant waste of thermal energy, which increases the production costs for power plants. Therefore, the recovery of waste heat from high-temperature flue gas is an important measure for thermal power plants to save energy, reduce consumption, and improve energy utilization rates. Additionally, it is a key step in reducing environmental pollution [30].
In terms of directly absorbing the waste heat from flue gas, Li [31] proposed a model for direct contact heat transfer between flue gas and water and experimentally demonstrated that distributing cold water at multiple points in the flue gas path enhances heat transfer efficiency compared to single-point injection. Yan et al. [32] proposed using cooling water and flue gas waste heat for centralized heating and designed two water source heat pump systems for flue gas waste heat recovery, which were compared with the traditional absorption heat pump system. The results indicated that the water source heat pump system is more cost-effective. Kuang et al. [33] demonstrated that lithium bromide absorption heat pumps are more effective than vapor compression heat pumps for recovering low-temperature flue gas waste heat. The single-effect heat pump showed greater operational stability than the double-effect heat pump. Wang et al. [34] used flue gases to heat water to a specific temperature, followed by flash evaporation to produce low-pressure waste heat steam. The research showed that energy utilization could be optimized by retrofitting the system to operate at the lowest feasible waste heat steam pressure. Retrofitting a 1,000 MW unit in this manner is expected to effectively reduce CO2 emissions by 6,333.97 tons annually.
In terms of system improvement, Liu et al. [35] provided a comprehensive overview of current flue gas waste heat recovery technologies and suggested potential avenues for improvement, without detailing specific optimization methods. Feng et al. [36] investigated the use of sintering waste heat to recover low-temperature flue gas from a waste heat boiler. They found that using R236ea in a basic organic Rankine cycle (BORC) can achieve a waste heat recovery efficiency of 65.07%. Li et al. [37] proposed the use of absorption heat pumps to capture low-grade flue gas heat from a coal-fired unit, with the aim of enhancing air preheating to reduce coal consumption and water usage. (as shown in Figure 4) Liu et al. [38] proposed the implementation of a combined cycle system that integrates Thermal Electricity Generation with an Organic Rankine Cycle (ORC) to recover waste heat from the main engine's flue gas. The study indicated that the system's output performance was optimized when the pressure (P) was set at 0.75 MPa. Mubashir et al. [39] achieved a thermal efficiency of 59.21% by integrating an Absorption Refrigeration System with an ORC to utilize waste heat from a 470 ℃ engine for simultaneous electricity generation and refrigeration. The Brayton cycle and ORC were used in a cascaded arrangement to recover heat from the flue gases of the internal combustion engine.
Exhaust steam waste heat refers to the high-temperature and high-pressure steam that expands and performs work within a steam turbine, converting thermal energy into mechanical energy. After this process, the steam retains a certain temperature and pressure and is referred to as exhaust steam. This exhaust steam contains a significant amount of heat. If it is directly released into the atmosphere through a cooling tower or cooling system, it not only results in energy waste but also contributes to environmental pollution [40]. To improve the quality of low-temperature waste heat, An et al. [41] proposed a combined compression and absorption heat pump system, which constructs two cycles capable of significant temperature elevation and high-temperature output. The research showed that both cycles significantly outperformed the R245fa compression cycle in terms of temperature elevation and output temperature. Building on the Co-ah system, Wu et al. [42] added two heat storage tanks for low and high temperatures, along with a set of electric heat pumps, to capture and store the waste heat from the thermal power plant using the low-temperature tank. The stored high-temperature hot water is then used to compensate for heating capacity gaps and maintain heating output stability, achieving significant thermoelectric decoupling and enhancing power generation regulation. Talib et al. [43] integrated an existing system with an ORC to improve the utilization of boiler waste heat by recovering additional energy from the exhaust gases through the ORC. This integration resulted in nearly a 20% increase in the overall thermal efficiency of the plant. Zhang et al. [44] made enhancements to the heat accumulator and heater across two cycles, which significantly improved heat source utilization and net power output compared to the period before the improvements, although there was a slight reduction in thermal efficiency.
Additionally, it can be combined with other forms of waste heat. Kauko et al. [45] used a 1,000 m3 minimum thermal energy storage tank in an industrial area of Mo, Norway, to integrate waste heat from boilers powered by various energy sources, including carbon monoxide gas, electricity, and petroleum. They found a significant reduction in both the total cost of heating and CO2 emissions. Elistratov et al. [46] demonstrated that integrating absorption heat pumps and chillers of various designs and capacities into the thermal circuits of existing and planned thermal power plants can achieve significant reductions in heat losses. Aberkane et al. [47] proposed integrating an ORC system during summer and adding a waste heat reclaimer in winter. The results showed a 16.9% increase in energy efficiency in summer and a 21.59% increase in winter. Sinha et al. [48] found that the integrated waste heat recovery system can mitigate specific heat losses, reduce consumption, and enhance thermal efficiency. The proposed two-stage waste heat recovery system achieved a maximum energy efficiency of 61.639%.
The utilization of waste heat in a cogeneration plant involves the technical process of recovering and converting excess heat into usable thermal energy, which can be used for heating, hot water supply, or other industrial applications. When a cogeneration system is integrated with a power plant [49], the waste heat is effectively reused, thereby increasing the overall efficiency of the facility. This not only improves energy utilization efficiency and reduces energy waste but also helps mitigate environmental pollution, resulting in significant economic and social benefits.
The traditional heat transfer fluidsused in thermal power plants are generally water or oil. The thermal conductivity and heat transfer efficiency of these conventional heat transfer fluids are relatively low, which limits their application effectiveness in fields such as thermal management and cooling systems [50]. To enhance the heat transfer efficiency of heat transfer fluids [51], some scholars have researched the preparation of nanoparticles with high thermal conductivity and their incorporation into the heat transfer fluids. These nanoscale solid particles, when uniformly dispersed in conventional fluids to form a stable suspension, are referred to as Nanofluids (NFs). In the field of thermal convection in NF, numerical simulation research is of great importance [52], encompassing a variety of simulation strategies including the mixture model, the volume of fluid method, the Eulerian model, and the Eulerian-Lagrangian model.
Ajeeb and colleagues [53,54] used various compounds such as SiC and BN to prepare NFs and they found that the electrical conductivity of the NFs was significantly enhanced. Furthermore, they prepared fiveconcentrations of nanoparticle suspensions using Al2O3 and TiO2 as materials, respectively, which served as the base fluids (BFs) flowing within a Compact Plate Heat Exchanger. By comparing viscosity and thermal conductivity through numerical investigations, they analyzed the thermal performance of the NFs. The research indicates that the addition of nanoparticles to the BF can enhance thermal performance, with a 24.6% improvement in heat transfer performance for a concentration of 0.2 vol.% Al2O3, and a 15.3% improvement for the same concentration of TiO2. Ajeeb et al. [55] prepared two concentrations (0.01 and 0.05 vol.%) of Al2O3 NF to study the applicability of NFs in pool boiling systems. A mixture of ethylene glycol (EG) and distilled water (DW) was used as the BF. The critical heat flux, burnout heat flux, and convective heat transfer coefficient were compared. The results revealed a significant improvement in the heat transfer performance of the NFs. When the concentration of the Al2O3 NF was 0.05 vol.%, the critical heat flux increased by 60% and the burnout heat flux increased by 54%.
Due to the enhancement of thermal conductivity, smaller or lighter heat exchangers can be utilized to achieve the same heat exchange effect. Ajeeb et al. [56] prepared five concentrations of Al2O3 and EG/water-based Al nanoparticle solutions ranging from 1.0 to 3.0 vol.%, and conducted a numerical study under a constant heat flux in a microchannel with Reynolds numbers between 400 and 2,000 (laminar flow). The results indicated that the convective heat transfer of both NFs was significantly enhanced and increased with the increasing concentration of nanoparticles. At a nanoparticle concentration of 3.0 vol.%, the maximum enhancement for Al reached 20.3%, while for Al2O3 it was 25.1%.
In recent years, China's installed nuclear power capacity has seen rapid growth [57]. The nation has been committed to the development of nuclear energy as a vital component of clean energy, with the aim of reducing reliance on fossil fuels and mitigating greenhouse gas emissions. Nuclear power plants are often constructed in coastal areas due to their geographical location and the availability of surrounding water resources. In northern China, where water resources are scarce, the waste heat generated by nuclear power plants can be harnessed for preparing hot water and desalinating seawater, addressing water resource challenges. This integrated approach enables the simultaneous provision of heat and water supply (the basic schematic diagram as shown in Figure 5). During winter, the temperature of the spent vapor is approximately 20 to 45 ℃, while the return water from the heat network ranges from 50 to 70 ℃.
Kostarev et al. [59] demonstrated that by implementing heat pumps for low-grade heat utilization in the thermal circuit of the BN-800 power unit, which is equipped with fast neutron reactors, it is possible to reduce steam extraction and generate additional energy at a constant production cost while also minimizing thermal emissions released to the environment. Tai et al. [60] integrated seawater desalination technology with waste heat recovery technology to establish a water-heat cogeneration system for nuclear power waste heat recovery, which can meet the requirements of seawater desalination and hot water heating. The overall thermal efficiency of this system can reach 69%, surpassing that of other heating systems. Li et al. [61] examined three contemporary technologies for nuclear power heat supply and compared them with conventional steam extraction for heat supply. They determined that the large temperature difference long-distance transmission for heat supply and water-heat co-provisioning technology are economically feasible. The investigation revealed that as the transmission distance of the large temperature difference for heat supply increases, the cost differential between it and water-heat co-provisioning also expands. Furthermore, the water-heat co-provisioning technology reduces carbon dioxide emissions by 3.09 million tons, as evidenced by an analysis of the heat supply from the Haiyang nuclear power plant to Yantai. Zhang et al. [62] utilized a fault tree to construct a reliability model for the waste heat discharge system in nuclear power plants, with the optimization of both coolant transfer and heat exchange functions taken into account. The study demonstrated that the optimized scheme led to a substantial enhancement in system reliability.
The iron and steel industry in China has traditionally been a significant consumer of energy due to its extensive production and energy-intensive nature. The distribution of steel in China is shown in Figure 6, with the southern region aligned along the Yangtze River, and the northern region primarily concentrated in the Beijing-Tianjin-Tangshan area and Liaoning province, where large steel enterprises dominate. During the production process, steel mills produce high-temperature slag exceeding 1,400 ℃, and the cooling slag flushing water contains a substantial amount of waste heat [63]. If the waste heat from steel mills can be fully recovered and utilized, it would not only reduce the energy costs for enterprises and improve economic efficiency but also decrease environmental pollution.
Woolley [8] proposed a comprehensive program for assessing energy recovery, which demonstrated its broad applicability through empirical case studies. Lin [64] conducted an analysis and exploration of the underemphasized low-temperature waste heat resources in steel mills, identifying three major components of unutilized low-temperature waste heat: Cooling water, flue gas, and spent steam, as shown in Figure 7. Cooling water is recovered directly through a heat exchanger, flue gas is proposed to be contacted with water for heat exchange, and spent steam is reclaimed through a condenser for direct use in heating. Ronggen et al. [65] proposed a novel planning approach for waste heat utilization in the steel industry, capable of generating adaptive optimal solutions. Following a numerical study, this new model predicts minimal deviation from actual performance even under highly uncertain conditions. Besevli et al. [66] employed various combined cycles, including the steam Rankine cycle, to harness waste heat from the annealing furnace of a steel plant. The recovered waste heat is released into the low-temperature oxygen line within the plant, enabling the condenser to operate at lower temperature and pressure compared to conventional systems.
The underutilization of low-temperature waste heat resources, such as condensate, spent steam, and low-pressure steam, is prevalent in refineries during the process production. The temperature of condensate typically ranges from 60 to 100 ℃, and can sometimes be higher, depending on the pressure and purpose of the steam. The temperature and pressure of low-pressure steam, also known as exhaust steam, are relatively low, usually not suitable for driving machinery, and fall within the range of 30 to 60 ℃. The temperature of low-pressure steam generally lies between 100 and 150 ℃.
Zhang et al. [67] utilized low-temperature waste heat, such as condensate, spent steam, and low-pressure steam, for power generation through the ORC. The findings revealed that the adoption of low-temperature waste heat recovery technology led to significant annual energy savings and emission reductions compared to traditional heating methods. The annual net income from power generation was 8.698 million yuan. Mu et al. [68] conducted a study on the impact of flue gas waste heat recovery and pressure drop on energy conservation and carbon reduction in a heating furnace rail heat exchanger. The findings indicated that reducing the pressure drop of flue gas can significantly enhance the utilization of flue gas waste heat and reduce carbon emissions. Wang et al. [69] demonstrated that the largest portion of the system investment cost is attributed to the expense of solar collectors, accounting for approximately 60% in their case study. They also suggested that a significant reduction in cost could be achieved by replacing solar collectors with waste heat.
Coal mine waste heat refers to the residual heat generated during the production process of coal mining, which primarily encompasses activities such as ventilation, drainage, lifting, extraction, and transportation. This thermal energy typically manifests as a low temperature and holds significant potential for utilization [70]. In China, the harnessing of waste heat from coal mines cannot only enhance energy utilization and reduce energy consumption but also mitigate environmental pollution and facilitate green sustainable development. The primary sources of waste heat include the return air from coal mines and the dissipation from mining equipment, with the return air temperature consistently ranging between 15 to 20 ℃.
Bai et al. [71] discovered that employing a spray heat exchange system to recover the waste heat from mine return air results in higher heat exchange efficiency, leading to approximately 75% energy savings compared to traditional electric boiler heating. In the heat exchanger, the heat and mass transfer occurs through the downward spray of water and the upward flow of return air in a counter-current manner. After the exchange, the circulating water is heated by the warm return air and then sent back to the heat pump machine room for utilization (as shown in Figure 8). Zhu et al. [72] upgraded the aging heating system at Huacaotan coal mine and proposed a plan to harness waste heat from the mine for heating purposes. They implemented an air source heat pump system for building heating, a compressor waste heat utilization system for supplying hot water to bathrooms, and a mine return air waste heat utilization system to protect shafts from frost. The operational results demonstrated that this approach can save 16.157 million yuan annually compared to an electric hot water boiler program. Liu et al. [73] conducted continuous "thermal charging" of conventional backfilled workings based on the type of mine heat source. Furthermore, in the presence of high-temperature surrounding rock, the heat recovery rate exceeds 1, and with "thermal charging, " the solid ratio demonstrates significantly improved performance compared to conventional rock thermal storage. Zhai et al. [74] proposed an improvement scheme for a high-flow rate, multi-pipe rows configuration, which significantly enhanced the efficiency of the heat transfer system. The enhancement resulted in a 4.1 ℃ reduction compared to pre-improvement conditions and facilitated further recovery of waste heat from the mine return air. The fresh air outlet temperature increased by 7.8 ℃ leading to an overall 10% increase in heat transfer efficiency.
In recent years, with the advancement of big data, cloud computing, and other technologies, there has been a growing demand for data processing, transmission, storage, and related services, and the scale of data centers is also expanding. The energy consumption of data centers is much higher than that of ordinary commercial buildings. Surveys have shown that data centers use about 3% of the world's electricity, yet they account for nearly 4% of greenhouse gas emissions [75]. Itis worth noting that the energy consumption of data centers far exceeds that of typical commercial buildings, due to their primary heat source being the servers housed within [76]. When operational, the IT equipment, uninterruptible power supply, and auxiliary equipment in the server room generate a significant amount of heat. As a result, it is essential for the server room to maintain a consistent temperature and humidity environment year-round. Therefore, data centers generally employ two types of natural cooling technologies: Air-side and water-side. Due to the heat resistance of the electronic equipment in the data center, the waste heat generated is typically low-grade waste heat below 85 ℃, primarily derived from the hot air (30~40 ℃) within the machine room.
Khosravi et al. [77] conducted a study on two different technologies, heat pumps and heat-only boilers, for recovering waste heat from data centers and LuxTurrim5G smart poles, and utilizing it in a low-temperature district heating network. The research indicates that this technology is both efficient and cost-effective. Wahlroos et al. [78] conducted an analysis of the potential for waste heat utilization in data centers located in the Nordic countries. The primary obstacles to leveraging waste heat include its low quality (e.g., low temperature or unstable heat sources) and high investment costs. This pertains to utilizing low-grade heat for heating purposes in data centers with peak loads. Li et al. [79] proposed a water tank and borehole thermal storage system for short- and long-term thermal energy storage, achieving a 31% reduction in peak load with a storage efficiency exceeding 80%. The borehole thermal energy storage system demonstrated an impressive waste heat utilization rate of 96%.
Chen et al. [80] implemented a waste heat recovery system utilizing a water source heat pump and thermal storage tank. Simulation results showed that the system achieved a thermal energy savings of approximately 46.1% compared to the traditional air-cooled heat pump system, representing an improvement in savings of 64.4% over the traditional water source heat pump. Gai et al. [81] developed two types of heat extraction systems to optimize the simulation of cooling and waste heat recovery. The results indicated that at outdoor wet bulb temperatures between 8~10 ℃, the higher the temperature, the lower the energy consumption in cooling mode. Considering a data center with 9,142 kW heat dissipation in different cities, it was calculated that the waste heat exceeded 10,000,000 kWh. Yang et al. [82] proposed a model predictive control strategy for winter operation aimed at reducing the energy consumption of a data center. They also developed a water source heat pump system for waste heat recovery. The results showed that the control strategy reduced indoor temperature overshoot by 17.54%. Guo et al. [83] integrated a refrigeration system with a soil source heat pump to establish a soil-assisted refrigeration and waste heat recovery system. The experiment demonstrated that it could conserve 4,420 tons of standard coal, resulting in an annual cost savings of approximately 2.21 million yuan. The annual temperature increase of the soil source was approximately 0.03 ℃, effectively achieving thermal equilibrium. Li et al. [84] found that peak load can contribute to 20% of the heating expenses for a campus district heating system in Norway. They found that implementing tank heat storage could reduce the costs associated with peak loads by 15%. Huang et al. [85] developed a novel palmate lobe-shaped finned LHTES device inspired by bionic technology. The new LHTES device demonstrated a 21.0% reduction in charging time and a 38.2% reduction in discharging time compared to the conventional device.
We focused on the comprehensive application of industrial waste heat recovery and seasonal heat storage technology. The waste heat recovery system provides a heat source for the seasonal heat storage system by capturing and utilizing the waste heat generated during industrial processes. This integration not only improves the efficiency of energy utilization but also achieves long-term heat storage through seasonal heat storage. Furthermore, this technological integration reduces dependence on external energy sources, lowers operating costs, and significantly improves the environmental benefits of the system. By optimizing the operational strategies of both components, efficient cyclic utilization of thermal energy can be achieved, offering a sustainable solution for building heating and industrial thermal energy requirements. Thermal storage technology is a widely employed method for utilizing industrial waste heat to achieve seasonal energy storage. This process involves converting waste heat into thermal energy, which is then stored and released during periods of peak energy demand or when traditional energy sources are in short supply. The thermal storage technologies that are widely implemented include sensible heat energy storage (SHS), latent heat storage (LHS), and thermochemical heat storage (THS) [86,87].
The primary objective of developing thermal storage technology is to address the challenge of the energy supply-demand imbalance and to enhance the efficiency of energy utilization. This technology is particularly effective in mitigating the temporal and spatial disparities in energy consumption. Renewable energy sources, such as solar and wind power, do not always generate energy in concert with the timing of demand [88]. For instance, solar energy is most abundantly produced during daylight hours, yet energy demand persists throughout the night. Thermal energy storage technology enables the capture and storage of excess thermal energy generated during the day, which can subsequently be released to meet demand during the night.
Additionally, while some regions may possess an abundance of thermal energy resources, others may not. Thermal storage technology facilitates the transfer of thermal energy between different locations, enabling spatial redistribution of energy. Many industrial processes generate significant amounts of waste heat, which, if not captured, is lost to the environment as unused energy. By storing this waste heat or surplus energy for future use in power generation or heating, thermal storage technology significantly improves energy efficiency [89]. The output of renewable energy sources is often variable and dependent on factors such as weather conditions, which can lead to instability in energy supply. Thermal storage technology serves as a crucial buffer, balancing supply and demand to ensure a more stable energy supply. Consequently, thermal storage technology plays a vital role in promoting the sustainable development of energy systems, achieving efficient energy use, and supporting the broader adoption of clean energy sources.
SHS involves using the change in material temperature to directly store and release thermal energy. It primarily includes Aquifer Thermal Energy Storage (ATES), Borehole Thermal Energy Storage (BTES), and Pit Thermal Energy Storage (PTES) technologies. The Water Pit thermal storage system is the most reliable and widely applied seasonal energy storage system [90]. Thermal energy storage is a promising technology that can bridge the intermittency gap of solar energy. Thermal energy storage systems accumulate excess thermal energy generated by intermittent energy sources and supply the required heat on demand at the necessary time and location. Therefore, thermal energy storage systems provide a solution to the temporal mismatch between energy demand and supply.
As a natural underground reservoir composed of strata with high water content and porosity, surrounded by upper and lower impermeable layers, such a structure renders it an ideal site for seasonal thermal energy storage (STES). ATES technology is the most cost-effective among sensible heat storage technologies and offers the advantage of high capacity. However, it necessitates favorable geological conditions and typically achieves a storage temperature of only 40~50 ℃, thereby limiting its range of application [91]. ATES technology operates based on the principle that during the warm season, solar energy is used to heat low-temperature water in cold wells, which is then injected into hot wells for heat storage. In the cold season, hot water is extracted from the hot wells to serve as a low-temperature heat source for the heat pump system to supply warmth, and the low-temperature water, after being pumped for heat, is reinjected into the cold wells [92]. The schematic is shown in Figure 9.
The assessment of ATES performance heavily relies on sophisticated Computational Fluid Dynamics (CFD) models for simulation and analysis. For instance, Yapparova et al.'s study [94] highlighted that a greater distance between the hot water wells and the cold water wells leads to improved thermal energy storage effectiveness. Additionally, an increase in thermal energy storage temperature results in decreased thermal energy storage efficiency. Oh et al. [95] explored a technique for integrating residual energy from photovoltaic systems with storage in an aquifer. Practical cases demonstrated that storing heat for 6 hours during the night can result in a reduction of more than 60% in daytime power consumption. Sifnaios et al. [96] conducted an analysis on the high flexibility of TES storage, demonstrating its potential to increase PV capacity by 35% and expedite the achievement of carbon neutrality. However, in comparison with TTES, PTES systems offer greater advantages due to lower system costs and higher utilization of renewable energy. It is also crucial to understand how to ensure the profitability of the system.
A buried pipe is a facility that utilizes underground space for heat exchange. The construction process commences with the drilling of holes to a specific depth below the ground, followed by the installation of multiple vertically positioned U-tubes in these holes, forming what are known as drilled heat exchangers. Heat is then transferred through these exchangers via the circulation of heat carriers (usually water). The optimal depth of the borehole is determined by factors such as the heat transfer properties of the ground, the natural temperature of the subsurface, the level of the water table, the distribution of heat loads, and the distance to other heat storage systems [97]. One of the configurations for non-heating and heating seasons as shown in Figures 10 and 11. In some buried pipe systems, horizontally placed heat exchangers can be utilized, making these systems relatively inexpensive to construct and more cost-effective than vertical borehole systems due to the shallow drilling depth [98]. The performance of underground pipe systems is significantly impacted by climate change, leading to potential high heat losses and increased drilling costs during installation, as well as higher initial expenses.
Yang et al. [99] demonstrated that utilizing phase change materials with low transition temperatures in summer and high transition temperatures in winter for backfilling can enhance the heat exchange efficiency of underground heat exchangers. Guo et al. [100] injected 33,458.6 GJ of thermal energy into a 500,000 m3 borehole, resulting in an average soil temperature increase of approximately 25 ℃. The findings indicated that BTES has the potential to enhance the flexibility, resilience, and energy efficiency of heat supply networks. The research team led by Xu et al. [101] implemented a 500,000 m3 borehole thermal storage system to capture waste heat from an on-site solar thermal power plant and a copper plant. The efficacy of the BTES model was assessed. The findings indicated that employing a timed combination control operation strategy makes the system more advantageous in terms of reducing carbon dioxide emissions compared to area control and overall control. Zhang et al. [102] observed that increasing the spacing between boreholes can mitigate thermal disturbances and enhance heat extraction capacity. Sun et al. [103] observed that the distribution of drilled holes downstream of advection can effectively reduce heat accumulation. Shi et al. [104] conducted a comparison of the thermal conductivity of the ground across six geological structures, revealing that the thickest layer of clay, measuring 60 m, exhibited the lowest thermal conductivity. The heat transfer rate between a vertically bored heat exchanger and its surrounding ground varies depending on the length of the borehole. Guo et al. [105] introduced a semi-analytical solution known as the "MVQ solution". The findings indicated that, in terms of mean absolute percentage error for average well wall temperature, the MVQ solution demonstrates a 48% improvement in accuracy compared to the conventional solution.
In the early stages, thermal storage technology primarily existed in the form of Tank Thermal Energy Storage (TTES) [107], which was categorized into above-ground, semi-buried, and fully buried types. The fundamental principle behind this technology is the use of water's specific heat capacity to store and release thermal energy. Under non-adiabatic conditions, the issue of heat loss in TTES is quite pronounced. Moreover, with the development of the social economy and the growth of energy demand, the required capacity of water tanks continues to increase, leading to a rise in construction cost. TTES is gradually evolving towards large bodies of water thermal storage systems to cope with the growing demand for thermal energy. This process reflects significant advances in the scale, efficiency, and application areas of thermal storage technology.
PTES operates by storing heated water in a large excavated basin with an insulated cover, or in an artificial storage container constructed of reinforced concrete/stainless steel below or near the surface (also known as an in-ground tank). The sides and bottom of the basin are typically lined with a polymer material [108]. Compared to ATES and BTES, PTES is less susceptible to hydrogeological conditions, but it comes with a higher cost [109]. The heat source for seasonal heat storage is predominantly solar energy; therefore, this section mainly refers to solar seasonal heat storage projects. Figure 12 is a schematic diagram of a solar seasonal heat storage engineering system. The geometric shapes of STES water bodies mainly include four types: Cylindrical, inverted conical, square, and inverted pyramid. The sectional view of an inverted prismatic type thermal storage water body as shown in Figure 13.
In terms of control strategy and prediction, Li et al. [111] conducted an analysis of the impact of control strategies on the thermal collection performance and entropy efficiency of the system, demonstrating that flow control results in a 10% higher solar energy collection efficiency compared to temperature control. Tafuni et al. [112] conducted a study on a dual-media thermal storage system comprised of gravel and water, which was analyzed based on the hourly heating demand and weather data. The findings indicated that the storage system effectively mitigated greenhouse environmental impacts. He et al. [113] examined the heat transfer process of the insulated floating cover in PTES and found that the significant heat loss was attributed to the direct contact between the insulated top cover and the soil. Michele et al. [114] proposed a tool for minimizing prediction errors, enabling the calculation of storage heat loss and determination of the optimal insulation thickness. When applied to the REPLICATE project, this model calculated an optimal hot water tank volume of 3,800 m3 and a solar field area of 1,000 m2. The biogas power generation technology in Europe, which involves managing substantial quantities of digestate for 120~180 days, bears similarities to seasonal water storage. Balsari et al. [115] developed and implemented a cover system for digestate storage tanks, which was experimentally demonstrated to effectively store recovered biogas, thereby preventing 1,260 tons of carbon dioxide emissions per year and increasing methane production by 3%.
In terms of heat transfer studies in water bodies, Bai et al. [116,117,118] conducted three studies. In the first study, they investigated the impact of geometry on factors such as the thermal capacity of heating water pits, revealing that a decrease in sidewall area and an increase in sidewall slope both lead to higher efficiency in water storage within the pit. Additionally, water pits with smaller slopes exhibited a more rapid increase in thermal stratification. In the second study, they focused on heat storage conditions and thermal stratification phenomena in underground water pits. The experimental data and simulation results from a 3,000 m3 underground water pit in Huangdi City, China were analyzed. The heat storage efficiency was determined to be 62%, with most heat loss occurring at the sidewalls of the pit, accounting for 57%. Additionally, an investigation into the heat stratification effect in hot water storage tanks revealed that natural convection primarily occurs in the upper part of the cylindrical tank. The shape of the tank had a significant impact on thermal stratification, with the cylindrical tank having a height to diameter ratio of 1:1 exhibiting the highest energy efficiency, exergy efficiency, and lowest entropy yield. Chang et al. [108] conducted a study on the transient natural convection phenomenon in an underground seasonal thermal water storage system. Their findings revealed that heat loss from the water body led to a reduction in water temperature near the wall surface, resulting in sidewall flow; as a result, thermal storage efficiency decreased rapidly from 100% to 83.19% within the initial 5 minutes and then stabilized after approximately 40 minutes.
Regarding the mixing of hot and cold water bodies in the water pits, there are proposals to separate hot and cold tanks and conduct research on hot and cold layering theory. Li et al. [119] observed that, during simultaneous charging and discharging, water mixing in the tanks is more pronounced at the onset of water use, with the thermocline layer initially thickening before thinning. Throughout the water usage period, the rate of change in thermocline thickness remains minimal. Chang et al. [120] discovered that variations in inlet velocity and temperature result in fluctuations in outlet temperature. Specifically, an increase in inlet velocity leads to higher velocities within the thermocline region, while an increase in inlet temperature corresponds to a decrease in the frequency of oscillations within the thermocline region. Wang et al. [121] experimentally observed that as the storage and exothermic temperatures increase, so does the exothermic efficiency. Furthermore, with an increasing number of consecutive storage and exothermic cycles, the thickness of the inclined thermocline layer grows, leading to a decrease in the effective utilization rate of the storage tank. Falcoz et al. [122] conducted a study on the impact of fluid distribution on storage in a filled bed thermocline. The findings indicated that the overall storage performance was unaffected by fluid distribution, and that radial temperature exhibited the most uniformity.
Additionally, a variety of energy storage technologies exist, including underground geotechnical energy storage. Subsurface geotechnical energy storage technologies harness industrial waste heat to warm underground formations and store thermal energy within them. Erasmus et al. [123] utilized a campus photovoltaic-diesel generator to demonstrate the feasibility of storing waste heat from microgrids using a bedrock Thermal Energy Storage (TES) system, and showed that the thermal energy can be effectively utilized through two strategies: Deferrable and non-deferrable.
The technology of phase change material (PCM) energy storage involves the absorption or release of a significant amount of heat during the transformation of the phase change material between solid, liquid, and gas states [124]. Various methods such as melting/solidification, evaporation/condensation, sublimation/condensation, or other types of phase changes under specific constant temperature conditions are employed in thermal energy storage technology. In comparison to SHS, phase change latent heat offers greater capacity, higher energy density, constant storage temperature (nearly isothermal during charging and discharging), and improved chemical stability and safety. Researchers have also investigated the use of PCMs for thermal energy storage in buildings [125] to meet the thermal comfort requirements of residents. The utilization of PCM in battery thermal management systems [126] represents an effective passive method for thermal regulation, offering low operational costs and consistent temperature control. PCMs are considered a primary focus within the realm of phase change thermal storage technology. They can be classified into inorganic materials, organic materials, composite materials, and graphite-based materials based on type [127]. The thermophysical properties of some PCMs are shown in Table 4.
The technology of phase change heat storage using hydrated salt offers the benefits of high heat storage density and low cost. Liu et al. [143] utilized sodium acetate trihydrate as the heat storage material and employed cylindrical PCM to fill the bed phase change heat storage device. The experimental findings indicated that an increase in the heat storage temperature and flow rate could expedite the filling process. Li et al. [144] conducted preparation and analysis of the ternary mixed molten salt NaNO3-LiNO3-NaCl. The experimental findings indicated a 45.3 ℃ reduction in the phase transition temperature of NaNO3-LiNO3-NaCl compared to pure NaNO3, demonstrating higher thermal decomposition temperature and improved thermal stability. Revising the sentence: "Exploring high-performance PCMs [145] is of great significance in advancing technology. The thermal conductivity of PCMs [146] plays a crucial role. Improved sentence: Enhancing the thermal conductivity of PCMs involves elucidating the phonon scattering mechanism in PCMs and expanding the pathways for thermal conductivity. Due to the intricate electrochemical reactions occurring at various temperatures, lithium-ion batteries [147] exhibit sensitivity to temperature fluctuations and possess a relatively limited operational temperature range. Heyhat et al. [148] conducted simulations on the melting process of nano-PCMs within porous media and demonstrated that compositions of porous PCMs are more effective. The utilization of porous PCMs lowers the average battery temperature but has a detrimental impact on the battery's thermal management system. Jilte et al. [149] devised the arrangement of cells, primary containers, and secondary containers. The results demonstrated that the 7 × 7 × 1 arrangement exhibited superior cooling performance.
Type | PCM | Phase transition temperature (℃) |
Density (kg/m³) |
Thermal conductivity [W/(m·K)] |
Latent heat of change (kJ/kg) |
Inorganic materials | CaCl2·6H2O [128] | 29.9 | 1710 | 0.57 | 190.0 |
Paraffinic | ParaffinRT4 [129] | 2.0~4.0 | 880(s)/770(l) | 0.20 | 180.0 |
Paraffin [130] | 21.0 | 850 | 0.20 | ||
ParaffinC21H44 [131] | 40.0 | 800 | 0.14 | 220.0 | |
ParaffinRT-44HC [132] | 43.0 | 860(s)/760(l) | 0.20 | 255.0 | |
Paraffin(p-116) [133] | 44.0 | 817 | 0.16 | 226.0 | |
Paraffin [134] | 53.5 | 810(s)/790(l) | 0.21 | 266.0 | |
Organic Materials | Orthoanisic acid [135] | 31.6 | 878 | \ | 155.4 |
Polyethylene Glycol | 52.0~66.0 | \ | \ | \ | |
6000 [136] | 0 | \ | \ | \ | |
Stearic Acid [133] | 58.1 | 965 | 0.29 | 169.0 | |
Composite phase change materials | 35%Lauric Acid/65%Anacardic Acid [137] | 19.8 | \ | 0.14 | 133.2 |
60%Anacardic Acid/24%lauric acid/10%SiO2/6%EG [135] | \ | \ | 0.53 | 109.2 | |
339%dodecanoic acid/412%tetradecanol/201%cetyl alcohol/5%EG [138] | 26.1 | \ | \ | 172.2 | |
80%Paraffin/20%EG [139] | 27.3 | \ | 9.80 | 156.6 | |
FAC/epoxyalkane [140] | 33.9~35.8 | \ | 0.48~0.53 | 211.7 | |
SAT/AC complex [141] | 47.8 | \ | \ | 219.8 | |
SAT/KCI complex [142] | 47.8 | \ | \ | 242.0 | |
In the table, '/' represents 'No Data Available.' |
THS involves the conversion of industrial waste heat into chemical energy through thermo-chemical reactions, thereby enabling energy storage. The thermal storage system utilizes a heat storage medium to store and release heat through reversible chemical adsorption or chemical reaction. THS is an emerging technology still in the research and development stage, yet it holds significant potential. In comparison to sensible and latent heat technologies, THS systems offer higher energy storage density, longer duration of energy storage, and minimal heat loss throughout the entire process.
Chang et al. [150] integrated hydrogen storage with THS by proposing a sandwich reactor, which offers the advantage of a larger heat transfer area and reduced heat transfer thermal resistance, resulting in enhanced rates of heat transfer and hydrogen storage. Xu et al. [151] developed a composite adsorption cooling system to achieve efficient cooling and dehumidification by utilizing waste heat from fuel cells. The results demonstrated that the overall efficiency of this composite system in recovering fuel cell waste heat was 67.3%. Funayama et al. [152] utilized molten salt as a heat transfer medium for loading composites into a bed reactor. Their results demonstrated that integrating THS with a thermocline of molten salt can enhance the system's thermocline temperature and provide greater flexibility in variable discharge. Li et al. [153] proposed the direct extraction of flue gas from a thermal power generating unit to heat molten salt for thermal storage. Simulations indicated that this approach could result in a 10% reduction in peak temperature within thermal generating units. Lu et al. [154] integrated a packed bed with anisotropic heat transfer into a molten salt thermocline storage system, resulting in significantly enhanced effective discharge time and efficiency. Adsorption heat storage [155] is a form of chemical heat storage that utilizes the desorption/adsorption process of adsorbent and adsorbent mass to absorb/release a significant amount of thermal energy for energy storage and release. The heat storage density can reach as high as 800 to 2,600 kJ/kg, and it is categorized into hydrated salt system and ammonia complex system.
All energy storage technologies have their own set of advantages and drawbacks. Moving forward, the advancement of energy storage technology will focus on achieving high energy density, low cost, extended lifespan, and environmental sustainability. The research progress in industrial waste heat storage technology encompasses a range of energy storage methods, enhancing not only the efficiency of energy storage but also enabling the efficient utilization of heat energy. These research findings offer crucial technical support for achieving sustainable energy usage.
In this chapter, multiple instances of seasonal energy storage systems will be presented to illustrate their practical applicability and advantages. These systems harness renewable solar energy to achieve a seasonal energy balance by storing surplus energy and releasing it as needed [156,157].
The Institute of Electrical Engineering, Chinese Academy of Sciences (IEE, CAS) has established a 3,000 m3 hot water storage facility in Zhangjiakou for the Huangdicheng town (as shown in Figure 14). The solar heating system is comprised of three sub-systems [158]: The solar collection sub-system, the UWPS sub-system, and the heating sub-system (Figure 15).
The key system components comprise a heliostat field, a tower receiver, an underground hot water storage pit, and a buffer tank. Throughout the non-heating season, the heliostat field and tower receiver are responsible for capturing solar energy, converting it into thermal energy, and transferring it to the hot water storage pit for thermal energy storage. During the heating season, thermal energy stored in the hot water storage pit is released and supplied to customers for heating and hot water. A buffer tank is utilized for heating during this period, and when its temperature falls too low, seasonal hot water storage is employed for combined heating purposes. The hot water from the hot water storage system is utilized to transfer heat to the buffer tank via plate heat exchange, enabling heating of a 3,000 square meter energy-efficient building. This project eliminates the need for a gas boiler heating system.
The Tibet Langkazi project, similar to the Yellow Emperor City project, features a total collector area of 24,300 square meters, a thermal storage pool capacity of 15,000 cubic meters, and an initial phase indoor heating area of 82,600 square meters (as shown in Figure 16).
During winter, as the ground temperature decreases and geothermal energy supply diminishes, stored thermal energy will be extracted and utilized for heating through the heat exchange system, ensuring stable winter heating. After 5 months of data measurement, the solar energy guarantee rate has consistently reached 100% (as shown in Figure 17).
Xu [160] and his team established a living laboratory in Chifeng City, China, which includes three subsystems: An industrial waste heat recovery system, a solar thermal energy system, and a borehole thermal energy storage system. This laboratory integrates a 500,000 cubic meter borehole thermal energy storage system, an on-site solar thermal power plant, and the waste heat from a copper factory. The collector area of this system reaches 1,004 m2, comprising 468 boreholes, each extending to a depth of 80 m. This setup is capable of providing a heating power of 7.5 MW, serving a building area of 150,000 m2. The system is designed with a storage temperature of 50 ℃, and it achieves an annual heat storage capacity of 20,000 GJ. As shown in Figure 18, this project is a successful case of combining waste heat recovery from a copper factory with STES, which is of great significance for controlling CO2 emissions and researching STES.
Guo et al. [161] integrated simulation and experimentation to calibrate the soil's thermal properties, thereby assessing the long-term energy and exergy performance of the system. By constructing a simulation model, the system was simulated for a period of 10 years, predicting that the cyclic energy efficiency of the studied system would be 83.1%, and the exergy efficiency would be 40.7%. The research indicates that the main cause of exergy loss is the internal heat transfer process within the BTES. The total drilling length has the most significant impact, followed by the circulation flow rate and the spacing between boreholes. In order to maximize the utilization of renewable energy and industrial waste heat, Fang Guo and colleagues [162] have introduced and discussed the design concepts, control strategies, and optimization methods.
The PTES in Marstal, constructed in 2012, has a capacity of 75,000 m3 and can store approximately 6,000 MWh. It is powered by a solar collector field consisting of 15,000 m2 of flat plate collectors and supplies heat to around 1,600 consumers (as shown in Figure 19).
The average supply temperature is 73 ℃, while the return temperature hovers around 40 ℃. The system undergoes charging via the solar collector field in spring and summer, and discharging in fall and winter.
Addressing the issue of underutilization of a large amount of industrial waste heat, we provide a comprehensive review of the research progress related to industrial waste heat recovery systems and seasonal energy storage systems. The basic principles and applications of key technologies for waste heat recovery in industrial sectors such as thermal power plants, nuclear power plants, steel mills, data centers, oil refineries, and coal mines are presented. Industrial waste heat recovery systems represent a promising approach to energy utilization that can effectively improve energy efficiency and reduce carbon emissions. This technology faces several challenges, including the research and optimization of heat storage materials and the design and control of recovery systems to improve thermal recovery efficiency. In response to the mismatch in time, space, and temperature (grade) in the utilization of low-grade industrial waste heat in summer, the construction of large-scale heat storage bodies to store waste heat can form a clean heating mode and reduce carbon emissions for winter heating. Therefore, we introduce three types of heat storage methods: SHS, LHS, and THS, and discuss three heat storage methods, including ATES, BTES, and PTES. Finally, four case studies of seasonal heat storage systems in underground water bodies are presented to provide a reference for future research.
The authors declare they have not used Artificial Intelligence (AI) tools in the creation of this article.
We are grateful for the financial support of National Key R & D Program of China (NO2022YFC3802404).
All authors declare no conflicts of interest in this paper.
Jialin Song (First Author): Conceptualization, Methodology, Funding acquisition, Project administration; Haoyi Zhang: Investigation, Data curation, Writing-original draft; Mingfei He: Formal curation, Resources; Yanming Zhang: Supervision, Validation; Zhongjiao Ma (Corresponding Author): Visualization, Writing—review & editing.
[1] |
Eslamizadeh S, Ghorbani A, Costa RCBF, et al. (2022) Industrial community energy systems: Simulating the role of financial incentives and societal attributes. Front Environ Sci 10: 924509. https://doi.org/10.3389/fenvs.2022.924509 doi: 10.3389/fenvs.2022.924509
![]() |
[2] | Gül T, Jiang Y, Delmastro C, et al. (2024) The future of heat pumps in China, Beijing. Int Energy Agency, Tsinghua University Press, 15–30. Available from: https://www.iea.org/reports/the-future-of-heat-pumps-in-china. |
[3] |
Pelda J, Stelter F, Holler S (2020) Potential of integrating industrial waste heat and solar thermal energy into district heating networks in Germany. Energy 203: 117812. https://doi.org/10.1016/j.energy.2020.117812 doi: 10.1016/j.energy.2020.117812
![]() |
[4] |
Hong GB, Pan TC, Chan DYL, et al. (2020) Bottom-up analysis of industrial waste heat potential in Taiwan. Energy 198: 117393. https://doi.org/10.1016/j.energy.2020.117393 doi: 10.1016/j.energy.2020.117393
![]() |
[5] |
Dahash A, Ochs F, Janetti MB, et al. (2019) Advances in seasonal thermal energy storage for solar district heating applications: A critical review on large-scale hot-water tank and pit thermal energy storage systems. Appl Energy 239: 296–315. https://doi.org/10.1016/j.apenergy.2019.01.189 doi: 10.1016/j.apenergy.2019.01.189
![]() |
[6] |
Alkhalidi A, Al Khatba H, Khawaja MK (2021) Utilization of buildings' foundations for a seasonal thermal energy storage medium to meet space and water heat demands. Int J Photoenergy 2021: 6668079. https://doi.org/10.1155/2021/6668079 doi: 10.1155/2021/6668079
![]() |
[7] |
Woolley E, Luo Y, Simeone A (2018) Industrial waste heat recovery: A systematic approach. Sustainable Energy Technol Assess 29: 50–59. https://doi.org/10.1016/j.seta.2018.07.001 doi: 10.1016/j.seta.2018.07.001
![]() |
[8] |
Slimani H, Baba YF, Ousaleh HA, et al. (2023) Horizontal thermal energy storage system for Moroccan steel and iron industry waste heat recovery: Numerical and economic study. J Clean Prod 393: 136176. https://doi.org/10.1016/j.jclepro.2023.136176 doi: 10.1016/j.jclepro.2023.136176
![]() |
[9] |
Ajeeb W, Costa Neto R, Baptista P (2024) Life cycle assessment of green hydrogen production through electrolysis: A literature review. Sustainable Energy Technol Assess 69: 103923. https://doi.org/10.1016/j.seta.2024.103923 doi: 10.1016/j.seta.2024.103923
![]() |
[10] |
Yan J, Mo Y, Zhao CY, et al. (2024) Preparation and parameter optimization of thermochemical heat storage materials with high cyclic stability. Sol Energy Mater Sol Cells 268: 112749. https://doi.org/10.1016/j.solmat.2024.112749 doi: 10.1016/j.solmat.2024.112749
![]() |
[11] |
Thomas JM, Edwards PP, Dobson PJ, et al. (2020) Decarbonising energy: The developing international activity in hydrogen technologies and fuel cells. J Energy Chem 51: 405–415. https://doi.org/10.1016/j.jechem.2020.03.087 doi: 10.1016/j.jechem.2020.03.087
![]() |
[12] |
Ajeeb W, Baptista P, Neto RC (2024) Life cycle analysis of hydrogen production by different alkaline electrolyser technologies sourced with renewable energy. Energy Conv Manage 316: 118840. https://doi.org/10.1016/j.enconman.2024.118840 doi: 10.1016/j.enconman.2024.118840
![]() |
[13] |
Razi F, Dincer I (2020) A critical evaluation of potential routes of solar hydrogen production for sustainable development. J Clean Prod 264: 21582. https://doi.org/10.1016/j.jclepro.2020.121582 doi: 10.1016/j.jclepro.2020.121582
![]() |
[14] |
Al-Janabi A, Al-Azri N (2020) Effect of recovering the industrial waste heat in Oman on energy and environment. Energy Rep 6: 526–531.https://doi.org/10.1016/j.egyr.2020.11.203 doi: 10.1016/j.egyr.2020.11.203
![]() |
[15] |
Wang X, Wu Y, Fu L (2023) Evaluation of combined heat and power plants with electricity regulation. Appl Therm Eng 227: 120364. https://doi.org/10.1016/j.applthermaleng.2023.120364 doi: 10.1016/j.applthermaleng.2023.120364
![]() |
[16] |
Liu B, Li J, Zhang S, et al. (2020) Economic dispatch of combined heat and power energy systems using electric boiler to accommodate wind power. IEEE Access 8: 41288–41297. https://doi.org/10.1109/ACCESS.2020.2968583 doi: 10.1109/ACCESS.2020.2968583
![]() |
[17] |
Xu ZY, Mao HC, Liu DS, et al. (2018) Waste heat recovery of power plant with large scale serial absorption heat pumps. Energy 165: 1097–1105 https://doi.org/10.1016/j.energy.2018.10.052 doi: 10.1016/j.energy.2018.10.052
![]() |
[18] |
Zhang YJ, Ge ZH, Yang YX, et al. (2023) Carbon reduction and flexibility enhancement of the CHP-based cascade heating system with integrated electric heat pump. Energy Conv Manage 280: 116801. https://doi.org/10.1016/j.enconman.2023.116801 doi: 10.1016/j.enconman.2023.116801
![]() |
[19] |
Wang X, Wu Y, Fu L (2023) Configuration method for combined heat and power plants with flexible electricity regulation. Energy Build 287: 112966. https://doi.org/10.1016/j.enbuild.2023.112966 doi: 10.1016/j.enbuild.2023.112966
![]() |
[20] |
Abdelfattah AI, Shaaban MF, Osman AH, et al. (2023) Optimal management of seasonal pumped hydro storage system for peak shaving. Sustainability 15: 51111973. https://doi.org/10.3390/su151511973 doi: 10.3390/su151511973
![]() |
[21] |
Larrinaga P, Campos-Celador A, Legarreta J, et al. (2021) Evaluation of the theoretical, technical and economic potential of industrial waste heat recovery in the Basque Country. J Clean Prod 312: 127494. https://doi.org/10.1016/j.jclepro.2021.127494 doi: 10.1016/j.jclepro.2021.127494
![]() |
[22] |
Kumar S, Thakur J, Gardumi F (2022) Techno-economic modelling and optimisation of excess heat and cold recovery for industries: A review. Renewable Sustainable Energy Rev 168: 112811. https://doi.org/10.1016/j.rser.2022.112811 doi: 10.1016/j.rser.2022.112811
![]() |
[23] |
Lygnerud K, Werner S (2018) Risk assessment of industrial excess heat recovery in district heating systems. Energy 151: 430–441. https://doi.org/10.1016/j.energy.2018.03.047 doi: 10.1016/j.energy.2018.03.047
![]() |
[24] |
Liu L, Zhu N, Zhao J (2016) Thermal equilibrium research of solar seasonal storage system coupling with ground-source heat pump. Energy 99: 83–90. https://doi.org/10.1016/j.energy.2016.01.053 doi: 10.1016/j.energy.2016.01.053
![]() |
[25] |
Guerra OJ, Zhang JZ, Eichman J, et al. (2020) The value of seasonal energy storage technologies for the integration of wind and solar power. Energy Environ Sci 13: 1909–1922. https://doi.org/10.1039/D0EE00771D doi: 10.1039/D0EE00771D
![]() |
[26] |
Marenco-Porto CA, Fierro JJ, Nieto-Londono C, et al. (2023) Potential savings in the cement industry using waste heat recovery technologies. Energy 279: 127810. https://doi.org/10.1016/j.energy.2023.127810 doi: 10.1016/j.energy.2023.127810
![]() |
[27] |
Mitri FB, Ponce G, Anderson KR (2023) Compost waste heat to power organic rankine cycle design and analysis. J Energy Resour Technol 145: 4062288. https://doi.org/10.1115/1.4062288 doi: 10.1115/1.4062288
![]() |
[28] |
Zhang HS, Liu YF, Liu XG, et al. (2020) Energy and exergy analysis of a new cogeneration system based on an organic Rankine cycle and absorption heat pump in the coal-fired power plant. Energy Conv Manage 223: 113293. https://doi.org/10.1016/j.enconman.2020.113293 doi: 10.1016/j.enconman.2020.113293
![]() |
[29] |
Ma Y, Gao E, Zhang X, et al. (2024) Parametric analysis and design optimization of a fully open absorption heat pump for heat and water recovery of flue gas. Appl Energy 375: 124144. https://doi.org/10.1016/j.apenergy.2024.124144 doi: 10.1016/j.apenergy.2024.124144
![]() |
[30] |
Fu BR, Hsieh JC, Cheng SM, et al. (2024) Thermoeconomic analysis of a novel cogeneration system for cascade recovery of waste heat from exhaust flue gases. Appl Therm Eng 247: 123034. https://doi.org/10.1016/j.applthermaleng.2024.123034 doi: 10.1016/j.applthermaleng.2024.123034
![]() |
[31] |
Li F, Lin DM, Fu L, et al. (2019) Application of absorption heat pump and direct-contact total heat exchanger to advanced-recovery flue-gas waste heat for gas boiler. Sci Technol Built Environ 25: 149–155. https://doi.org/10.1080/23744731.2018.1506676 doi: 10.1080/23744731.2018.1506676
![]() |
[32] |
Yan LF, Wang W, Song BT, et al. (2023) Design of waste heat recovery system for a gas-fired thermal power plant in Beijing. HVAC 53: 127–132. https://doi.org/10.19991/j.hvac1971.2023.09.19 doi: 10.19991/j.hvac1971.2023.09.19
![]() |
[33] |
Kuang SY, Fang L, Xie Y, et al. (2023) Application analysis of core equipment for waste heat recovery of low temperature flue gas. HVAC 53: 121–126. https://doi.org/10.19991/j.hvac1971.2023.02.19 doi: 10.19991/j.hvac1971.2023.02.19
![]() |
[34] |
Wang R, Du X, Shi Y, et al. (2023) An ejector and flashbox-integrated approach to flue gas waste heat recovery: A novel systematic study. Energies 16: 16227607. https://doi.org/10.3390/en16227607 doi: 10.3390/en16227607
![]() |
[35] |
Liu YL (2023) Practical analysis of flue gas waste heat utilisation technology in boiler tail of thermal power plant. Mod Ind Econ Inform 13: 305–307. https://doi.org/10.16525/j.cnki.14-1362/n.2023.10.101 doi: 10.16525/j.cnki.14-1362/n.2023.10.101
![]() |
[36] |
Feng J, Cheng X, Yan Y, et al. (2023) Thermodynamic and thermo-economic analysis, performance comparison and parameter optimization of basic and regenerative organic Rankine cycles for waste heat recovery. Case Stud Therm Eng 52: 103816. https://doi.org/10.1016/j.csite.2023.103816 doi: 10.1016/j.csite.2023.103816
![]() |
[37] |
Li Y, Chen X, Jiang S, et al. (2023) Thermodynamics of cascaded waste heat utilization from flue gas and circulating cooling water. J Therm Sci 32: 2166–2178. https://doi.org/10.1007/s11630-023-1886-8 doi: 10.1007/s11630-023-1886-8
![]() |
[38] |
Liu C, Li H, Yu S, et al. (2023) Analysis of main engine various waste heat cascade recovery systems under different evaporation pressure. Int J Exergy 40: 263–281. https://doi.org/10.1504/IJEX.2023.129797 doi: 10.1504/IJEX.2023.129797
![]() |
[39] |
Mubashir W, Adnan M, Zaman M, et al. (2023) Thermo-economic evaluation of supercritical CO2 Brayton cycle integrated with absorption refrigeration system and organic Rankine cycle for waste heat recovery. Therm Sci Eng Prog 44: 102073. https://doi.org/10.1016/j.tsep.2023.102073 doi: 10.1016/j.tsep.2023.102073
![]() |
[40] |
Wu SY, Wu YL, Bai JY, et al. (2021) Research on recovering waste heat from exhaust steam in cogeneration system by heat pump. Clean Coal Technol 27: 323–327. https://doi.org/10.13226/j.issn.1006-6772.21032404 doi: 10.13226/j.issn.1006-6772.21032404
![]() |
[41] |
An MY, Zhao XR, Xu ZY, et al. (2021) A hybrid compression-absorption high temperature heat pump cycles for industrial waste heat recovery. J Shanghai Jiaotong Univ 55: 434–443. https://doi.org/10.16183/j.cnki.jsjtu.2020.023 doi: 10.16183/j.cnki.jsjtu.2020.023
![]() |
[42] |
Wu YT, Yin SY, Fu L, et al. (2018) "Cogeneration Synergy" to improve CHP flexibility. District Heating, 32–38. https://doi.org/10.16641/j.cnki.cn11-3241/tk.2018.01.006 doi: 10.16641/j.cnki.cn11-3241/tk.2018.01.006
![]() |
[43] |
Talib R, Khan Z, Khurram S, et al. (2023) Energy efficiency enhancement of a thermal power plant by novel heat integration of internal combustion engine, boiler, and organic Rankine cycle. Asia Pac J Chem Eng 13: 3013. https://doi.org/10.1002/apj.3013 doi: 10.1002/apj.3013
![]() |
[44] |
Zhang L, Zhao C, Sun E, et al. (2023) Energy, exergy and economic (3E) study on waste heat utilization of gas turbine by improved recompression cycle and partial cooling cycle. Energy Sources Part A 45: 4127–4145. https://doi.org/10.1080/15567036.2023.2202626 doi: 10.1080/15567036.2023.2202626
![]() |
[45] |
Kauko H, Rohde D, Knudsen BR, et al. (2020) Potential of thermal energy storage for a district heating system utilizing industrial waste heat. Energies 13: 13153923. https://doi.org/10.3390/en13153923 doi: 10.3390/en13153923
![]() |
[46] |
Elistratov SL, Mironova NV (2023) Absorption thermal transformers for heat recycling at thermal power plants. Thermophys Aeromech 30: 381–386. https://doi.org/10.1134/S0869864323020191 doi: 10.1134/S0869864323020191
![]() |
[47] |
Aberkane S, Semmari H, Filali A, et al. (2023) Thermo-economic assessment of upgrading a basic gas turbine power plant into CHP plant. Int J Exergy 40: 429–450. https://doi.org/10.1504/IJEX.2023.130368 doi: 10.1504/IJEX.2023.130368
![]() |
[48] |
Sinha AA, Choudhary T, Ansari MZ, et al. (2023) Waste heat recovery and exergy-based comparison of a conventional and a novel fuel cell integrated gas turbine hybrid configuration. Sustainable Energy Technol Assess 57: 103256. https://doi.org/10.1016/j.seta.2023.103256 doi: 10.1016/j.seta.2023.103256
![]() |
[49] |
Singh N, Chakrabarti T, Chakrabarti P, et al. (2023) Analysis of heuristic optimization technique solutions for combined heat-power economic load dispatch. Appl Sci Basel 13: 10380. https://doi.org/10.3390/app131810380 doi: 10.3390/app131810380
![]() |
[50] |
Pathak SK, Kumar R, Goel V, et al. (2022) Recent advancements in thermal performance of nano-fluids charged heat pipes used for thermal management applications: A comprehensive review. Appl Therm Eng 216: 119023. https://doi.org/10.1016/j.applthermaleng.2022.119023 doi: 10.1016/j.applthermaleng.2022.119023
![]() |
[51] |
Gupta M, Singh V, Kumar R, et al. (2017) A review on thermophysical properties of nanofluids and heat transfer applications. Renewable Sustainable Energy Rev 74: 638–670. https://doi.org/10.1016/j.rser.2017.02.073 doi: 10.1016/j.rser.2017.02.073
![]() |
[52] | Ajeeb W, Zhang JZ, Wu Z, et al. (2022) Numerical development of the thermal convection characteristics of nanofluids. in: Murshed SMS, editor. Fundam Transp Prop Nanofluids, R Soc Chem, 365–366. https://doi.org/10.1039/9781839166457-00335 |
[53] |
Ajeeb W, Murshed SMS (2023) Characterization of thermophysical and electrical properties of SiC and BN nanofluids. Energies 16: 3768. https://doi.org/10.3390/en16093768 doi: 10.3390/en16093768
![]() |
[54] |
Ajeeb W, Murshed SMS (2022) Comparisons of numerical and experimental investigations of the thermal performance of Al2O3 and TiO2 nanofluids in a compact plate heat exchanger. Nanomaterials (Basel) 12: 3634. https://doi.org/10.3390/nano12203634 doi: 10.3390/nano12203634
![]() |
[55] |
Ajeeb W, Murshed SMS (2023) Pool boiling heat transfer characteristics of new and recycled alumina nanofluids. Nanomaterials (Basel) 13: 1040. https://doi.org/10.3390/nano13061040 doi: 10.3390/nano13061040
![]() |
[56] | Ajeeb W, Murshed SMS (2023) Numerical study of convective heat transfer performance, entropy generation and energy efficiency of Al and Al2O3 nanofluids in minichannel. J Nanofluids 12: 18–28. Available from: https://www.ingentaconnect.com/contentone/asp/jon/2023/00000012/00000001/art00002. |
[57] |
Moriarty P (2021) Global nuclear energy: An uncertain future. AIMS Energy 9: 1027–1042. https://doi.org/10.3934/energy.2021047 doi: 10.3934/energy.2021047
![]() |
[58] | Tai CM (2022) Analysis of the water-heat combined supply system based on waste heat utilization of nuclear power units. https://doi.org/10.27273/d.cnki.gsajc.2022.000655 |
[59] |
Kostarev VS, Tashlykov OL, Klimova VA (2019) The increasing of the energy efficiency of nuclear power plants with fast neutron reactors by utilizing waste heat using heat pumps. IOP Conf Ser Mater Sci Eng 552: 012022. https://doi.org/10.1088/1757-899X/552/1/012022 doi: 10.1088/1757-899X/552/1/012022
![]() |
[60] |
Tai CM, Tian GS, Lei WJ (2022) A water-heat combined supply system based on waste heat from a coastal nuclear power plant in northern China. Appl Therm Eng 200: 117684. https://doi.org/10.1016/j.applthermaleng.2021.117684 doi: 10.1016/j.applthermaleng.2021.117684
![]() |
[61] | Li YH, Wang X, Li ZY, et al. (2022) Using waste heat from nuclear power plants to achieve zero-carbon heating. Energy China 44: 48–55. Available from: https://qikan.cqvip.com/Qikan/Article/Detail?id=7107732180&from=Qikan_Search_Index. |
[62] |
Zhang DL, You WH, Pan XL, et al. (2022) Reliability modeling and analysis of residual heat removal system in pressurized water reactor nuclear power plant. Nuc Phys Rev 39: 266–271. https://doi.org/10.11804/NuclPhysRev.39.2021084 doi: 10.11804/NuclPhysRev.39.2021084
![]() |
[63] |
Inayat A (2023) Current progress of process integration for waste heat recovery in steel and iron industries. Fuel 338: 127237. https://doi.org/10.1016/j.fuel.2022.127237 doi: 10.1016/j.fuel.2022.127237
![]() |
[64] | Lin JH (2021) Study on utilization of low-grade waste heat potential in steel plant for heating. https://doi.org/10.27139/d.cnki.ghbdu.2021.000031 |
[65] |
Wang R, Zhang W, Yang S, et al. (2023) A novel approach for utilizing waste heat resources in the steel industry. Front Energy Res 11: 1257344. https://doi.org/10.3389/fenrg.2023.1257344 doi: 10.3389/fenrg.2023.1257344
![]() |
[66] |
Besevli B, Kayabasi E, Akroot A, et al. (2024) Technoeconomic analysis of oxygen-supported combined systems for recovering waste heat in an iron-steel facility. Appl Sci Basel 14: 2563. https://doi.org/10.3390/app14062563 doi: 10.3390/app14062563
![]() |
[67] | Zhang MQ, He J, Ma RY, et al. (2020) Organic Rankine cycle power generation using low temperature waste heat in oil refineries and its benefit analysis. Pet Process Petrochem 51: 92–95. Available from: https://qikan.cqvip.com/Qikan/Article/Detail?id=7103372460&from=Qikan_Search_Index. |
[68] |
Mu LB, Wang SL, Lu JH, et al. (2023) Effect of flue gas condensing waste heat recovery and its pressure drop on energy saving and carbon reduction for refinery heating furnace. Energy 279: 128081. https://doi.org/10.1016/j.energy.2023.128081 doi: 10.1016/j.energy.2023.128081
![]() |
[69] |
Wang J, Kang LX, Liu YZ, et al. (2023) A multi-period design method for the steam and power systems coupling solar thermal energy and waste heat recovery in refineries. J Clean Prod 416: 137934. https://doi.org/10.1016/j.jclepro.2023.137934 doi: 10.1016/j.jclepro.2023.137934
![]() |
[70] |
Pallarés J, Herce C, Bartolomé C, et al. (2017) Investigation on co-firing of coal mine waste residues in pulverized coal combustion systems. Energy 140: 58–68. https://doi.org/10.1016/j.energy.2017.07.174 doi: 10.1016/j.energy.2017.07.174
![]() |
[71] | Bai YB (2022) Optimization and application of spray heat exchange system for waste heat utilization of mine return air. https://doi.org/10.27517/d.cnki.gzkju.2022.001662 |
[72] | Zhu J, Wei XF, Fang X, et al. (2023) Application of heating system based on utilization of various waste heat resources. Coal Eng 55: 45–48. Available from: https://qikan.cqvip.com/Qikan/Article/Detail?id=7111076411&from=Qikan_Search_Index. |
[73] |
Liu H, Zhang J, Rodriguez-Dono A, et al. (2023) Utilization of mine waste heat in phase change rechargeable battery. Appl Therm Eng 233: 121136. https://doi.org/10.1016/j.applthermaleng.2023.121136 doi: 10.1016/j.applthermaleng.2023.121136
![]() |
[74] |
Zhai Y, Zhao X, Xue G, et al. (2023) Study on heat transfer performance and parameter improvement of gravity-assisted heat pipe heat transfer unit for waste heat recovery from mine return air. Energies 16: 6148. https://doi.org/10.3390/en16176148 doi: 10.3390/en16176148
![]() |
[75] |
Zhang C, Luo H, Wang Z (2022) An economic analysis of waste heat recovery and utilization in data centers considering environmental benefits. Sustainable Prod Consum 31: 127–138. https://doi.org/10.1016/j.spc.2022.02.006 doi: 10.1016/j.spc.2022.02.006
![]() |
[76] |
Yuan X, Liang Y, Hu X, et al. (2023) Waste heat recoveries in data centers: A review. Renewable Sustainable Energy Rev 188: 113777. https://doi.org/10.1016/j.rser.2023.113777 doi: 10.1016/j.rser.2023.113777
![]() |
[77] |
Khosravi A, Laukkanen T, Vuorinen V, et al. (2021) Waste heat recovery from a data centre and 5G smart poles for low-temperature district heating network. Energy 218: 119468. https://doi.org/10.1016/j.energy.2020.119468 doi: 10.1016/j.energy.2020.119468
![]() |
[78] |
Wahlroos M, Pärssinen M, Rinne S, et al. (2018) Future views on waste heat utilization—Case of data centers in Northern Europe. Renewable Sustainable Energy Rev 82: 1749–1764. https://doi.org/10.1016/j.rser.2017.10.058 doi: 10.1016/j.rser.2017.10.058
![]() |
[79] |
Li H, Hou J, Hong T, et al. (2021) Energy, economic, and environmental analysis of integration of thermal energy storage into district heating systems using waste heat from data centres. Energy 219: 119582. https://doi.org/10.1016/j.energy.2020.119582 doi: 10.1016/j.energy.2020.119582
![]() |
[80] |
Chen SY, Zhang Q, Zhou SK, et al. (2023) Simulation on performance of waste heat recovery system with lake water in data centers: A case study of Dongjiang lake data center park. Sci Technol Eng 23: 9502–9508. https://doi.org/10.12404/j.issn.1671-1815.2023.23.22.09502 doi: 10.12404/j.issn.1671-1815.2023.23.22.09502
![]() |
[81] | Gai XT (2023) Research on waste heat recovery and utilization of data center based on heat pump technology. https://doi.org/10.27140/d.cnki.ghbbu.2023.000598 |
[82] | Yang JT (2023) Energy-saving optimization control of data center refrigeration and waste heat recovery system. Available from: https://webvpn.sjzu.edu.cn/https/77726476706e69737468656265737421fbf952d2243e635930068cb8/kcms2/article/abstract?v=nKttgsEmyDdbVgcKxtrbVXsQZn6YBbwB497BG1PsBwSwIPBoNY2-_c3UQUWSCN4G6X3NNjcw4y0q5ZVidr-vo9tw9dah06W8T90P2C6GTsNL5A_r9Q_tLMCBaocvLxEkkfgJiZtQixi5I7-2GkKh-d55R6XJ83R1RODDDLK8D8tw1PpR6WWg71PBys1rnMAn2_uuJSXtL2c=&uniplatform=NZKPT&language=CHS. |
[83] | Guo XY (2023) Research on soil auxiliary cooling and waste heat recovery heating technology for cold land data center. Available from: https://d.wanfangdata.com.cn/thesis/D03370499. |
[84] |
Li H, Hou J, Ding Y, et al. (2021) Techno-economic analysis of implementing thermal storage for peak load shaving in a campus district heating system with waste heat from the data centre. E3S Web Conf 246: 9003. https://doi.org/10.1051/e3sconf/202124609003 doi: 10.1051/e3sconf/202124609003
![]() |
[85] |
Huang Y, Deng Z, Chen Y, et al. (2023) Performance investigation of a biomimetic latent heat thermal energy storage device for waste heat recovery in data centers. Appl Energy 335: 1210745. https://doi.org/10.1016/j.apenergy.2023.1210745 doi: 10.1016/j.apenergy.2023.1210745
![]() |
[86] | Zheng YC, Shan CL, Zhang JB (2024) Current research status and development prospects of long duration energy storage system. Southern Energy Constr 11: 93–101. Available from: https://www.energychina.press/cn/article/doi/10.16516/j.ceec.2024.2.09. |
[87] |
Ding LW, Chen D, Lv HK, et al. (2024) Performance through Ni-Al doping enhancement mechanism of calcium-based thermochemical energy storage cyclic. Proc CSEE, 1–8. https://doi.org/10.13334/j.0258-8013.pcsee.231909 doi: 10.13334/j.0258-8013.pcsee.231909
![]() |
[88] |
Solomon AA, Child M, Caldera U, et al. (2020) Exploiting wind-solar resource complementarity to reduce energy storage need. AIMS Energy 8: 749–770. https://doi.org/10.3934/energy.2020.5.749 doi: 10.3934/energy.2020.5.749
![]() |
[89] |
Renaldi R, Friedrich D (2019) Techno-economic analysis of a solar district heating system with seasonal thermal storage in the UK. Appl Energy 236: 388–400. https://doi.org/10.1016/j.apenergy.2019.01.019 doi: 10.1016/j.apenergy.2019.01.019
![]() |
[90] |
Prasadi DMR, Senthilkumar R, Lakshmanarao G, et al. (2019) A critical review on thermal energy storage materials and systems for solar applications. AIMS Energy 7: 507–526. https://doi.org/10.3934/energy.2019.4.507 doi: 10.3934/energy.2019.4.507
![]() |
[91] |
Gao L, Zhao J, An Q, et al. (2019) Thermal performance of medium-to-high-temperature aquifer thermal energy storage systems. Appl Therm Eng 146: 898–909. https://doi.org/10.1016/j.applthermaleng.2018.11.060 doi: 10.1016/j.applthermaleng.2018.11.060
![]() |
[92] |
Ganguly S, Mohan Kumar MS, Date A, et al. (2017) Numerical investigation of temperature distribution and thermal performance while charging-discharging thermal energy in aquifer. Appl Therm Eng 115: 756–773. https://doi.org/10.1016/j.applthermaleng.2017.01.041 doi: 10.1016/j.applthermaleng.2017.01.041
![]() |
[93] |
Li S, Wang GS, Zhou MM, et al. (2024) Thermal performance of an aquifer thermal energy storage system: Insights from novel multilateral wells. Energy 294: 131915. https://doi.org/10.1016/j.energy.2023.131915 doi: 10.1016/j.energy.2023.131915
![]() |
[94] |
Yapparova A, Matthäi S, Driesner T (2014) Realistic simulation of an aquifer thermal energy storage: Effects of injection temperature, well placement and groundwater flow. Energy 76: 1011–1018. https://doi.org/10.1016/j.energy.2014.09.018 doi: 10.1016/j.energy.2014.09.018
![]() |
[95] |
Oh J, Sumiyoshi D, Nishioka M, et al. (2021) Efficient operation method of aquifer thermal energy storage system using demand response. Energies 14: 3129. https://doi.org/10.3390/en14113129 doi: 10.3390/en14113129
![]() |
[96] |
Sifnaios I, Sneum DM, Jensen AR, et al. (2023) The impact of large-scale thermal energy storage in the energy system. Appl Energy 349: 121663. https://doi.org/10.1016/j.apenergy.2023.121663 doi: 10.1016/j.apenergy.2023.121663
![]() |
[97] |
Lund H, Østergaard PA, Chang M, et al. (2018) The status of 4th generation district heating: Research and results. Energy 164: 147–159. https://doi.org/10.1007/s12273-020-0671-9 doi: 10.1007/s12273-020-0671-9
![]() |
[98] |
Morchio S, Fossa M (2020) On the ground thermal conductivity estimation with coaxial borehole heat exchangers according to different undisturbed ground temperature profiles. Appl Therm Eng 173: 115198. https://doi.org/10.1016/j.applthermaleng.2020.115198 doi: 10.1016/j.applthermaleng.2020.115198
![]() |
[99] |
Yang WB, Xu R, Yang BB, et al. (2019) Experimental and numerical investigations on the thermal performance of a borehole ground heat exchanger with PCM backfill. Energy 174: 216–235. https://doi.org/10.1016/j.energy.2019.02.172 doi: 10.1016/j.energy.2019.02.172
![]() |
[100] |
Guo F, Zhu XY, Zhang JY, et al. (2020) Large-scale living laboratory of seasonal borehole thermal energy storage system for urban district heating. Appl Energy 264: 114763. https://doi.org/10.1016/j.apenergy.2020.114763 doi: 10.1016/j.apenergy.2020.114763
![]() |
[101] |
Xu L, Guo F, Hoes P-J, et al. (2021) Investigating energy performance of large-scale seasonal storage in the district heating system of chifeng city: Measurements and model-based analysis of operation strategies. Energy Build 247: 1113. https://doi.org/10.1016/j.enbuild.2021.111113 doi: 10.1016/j.enbuild.2021.111113
![]() |
[102] |
Zhang FF, Fang L, Zhu K, et al. (2022) Long-term dynamic heat transfer analysis for the borehole spacing planning of multiple deep borehole heat exchanger. Case Stud Therm Eng 38: 102373. https://doi.org/10.1016/j.csit.2022.102373 doi: 10.1016/j.csit.2022.102373
![]() |
[103] |
Sun ZC, He ZX, Yu MZ (2021) Research on heat transfer characteristics and borehole field layout of ground heat exchangers to alleviate thermal accumulation with groundwater advection. Thermal Sci 25: 2781–2794. https://doi.org/10.1007/s12273-020-0671-9 doi: 10.1007/s12273-020-0671-9
![]() |
[104] |
Shi ZG, Zhang CX, Cai C, et al. (2024) Comparative analysis of ground thermal conductivity and thermal resistance of borehole heat exchanger in different geological layered sequence. J Build Eng 84: 108541. https://doi.org/10.1016/j.jobe.2024.108541 doi: 10.1016/j.jobe.2024.108541
![]() |
[105] |
Guo Y, Huang G, Liu W (2023) A new semi-analytical solution addressing varying heat transfer rates for U-shaped vertical borehole heat exchangers in multilayered ground. Energy 274: 127373. https://doi.org/10.1016/j.energy.2023.127373 doi: 10.1016/j.energy.2023.127373
![]() |
[106] | Li XX (2021) Research on dynamic characteristic and control strategy of solar heating system with seasonal thermal energy storage. Available from: https://apps.wanfangdata.com.cn/thesis/article:D02425573. |
[107] |
Novo AV, Bayon JR, Castro-Fresno D, et al. (2010) Review of seasonal heat storage in large basins: Water tanks and gravel-water pits. Appl Energy 87: 390–397. https://doi.org/10.1016/j.apenergy.2009.06.033 doi: 10.1016/j.apenergy.2009.06.033
![]() |
[108] |
Chang C, Wu Z, Navarro H, et al. (2017) Comparative study of the transient natural convection in an underground water pit thermal storage. Appl Energy 208: 1162–1173. https://doi.org/10.1016/j.apenergy.2017.09.036 doi: 10.1016/j.apenergy.2017.09.036
![]() |
[109] |
Yang T, Liu W, Kramer GJ, et al. (2021) Seasonal thermal energy storage: A techno-economic literature review. Renewable Sustainable Energy Rev 139: 110732. https://doi.org/10.1016/j.rser.2021.110732 doi: 10.1016/j.rser.2021.110732
![]() |
[110] | Zhao SS (2023) Study on economic analysis method of a heating system with a water pit for solar seasonal thermal energy storage. Available from: https://webvpn.sjzu.edu.cn/https/77726476706e69737468656265737421fbf952d2243e635930068cb8/kcms2/article/abstract?v=nKttgsEmyDca_XVxgMPI3VhDmHGQ0xIWwZIRwRKUAkHXe1U6CZaPExDoBUU5DLlxFFXePx_YximTPigrrfU66pT7rJEVaFWVgYfw3eTQoThJgap__c2Z74QVOGSz66VFjfs9XEpr2UIm-rk1eqywONfgJT7fhFGjzEq2-ZkMyQbV9MCwidmmlDH9Zt_pVlqRE1VBq8hWaJo=&uniplatform=NZKPT&language=CHS. |
[111] |
Li X, Wang Z, Li J, et al. (2019) Comparison of control strategies for a solar heating system with underground pit seasonal storage in the non-heating season. J Energy Storage 26: 100963. https://doi.org/10.1016/j.est.2019.100963 doi: 10.1016/j.est.2019.100963
![]() |
[112] |
Tafuni A, Giannotta A, Mersch M, et al. (2023) Thermo-economic analysis of a low-cost greenhouse thermal solar plant with seasonal energy storage. Energy Conv Manage 288: 117123. https://doi.org/10.1016/j.enconman.2023.117123 doi: 10.1016/j.enconman.2023.117123
![]() |
[113] |
He M, Wang Z, Zhang J, et al. (2022) Study on heat transfer process of insulated floating cover of water pit for solar seasonal thermal storage. Energy Rep 8: 1396–1404. https://doi.org/10.1016/j.egyr.2022.09060 doi: 10.1016/j.egyr.2022.09060
![]() |
[114] |
Salvestroni M, Pierucci G, Pourreza A, et al. (2021) Design of a solar district heating system with seasonal storage in Italy. Appl Therm Eng 197: 117438. https://doi.org/10.1016/j.applthermaleng.2021.117438 doi: 10.1016/j.applthermaleng.2021.117438
![]() |
[115] |
Balsari P, Dinuccio E, Gioelli F (2013) A floating coverage system for digestate liquid fraction storage. Biores Technol 134: 285–289. https://doi.org/10.1016/j.biortech.2013.02.021 doi: 10.1016/j.biortech.2013.02.021
![]() |
[116] |
Bai Y, Wang Z, Fan J, et al. (2020) Numerical and experimental study of an underground water pit for seasonal heat storage. Renewable Energy 150: 487–508. https://doi.org/10.1016/j.renene.2019.12.080 doi: 10.1016/j.renene.2019.12.080
![]() |
[117] |
Bai Y, Yang M, Wang Z, et al. (2019) Thermal stratification in a cylindrical tank due to heat losses while in standby mode. Sol Energy 185: 222–234. https://doi.org/10.1016/j.solener.2018.12.063 doi: 10.1016/j.solener.2018.12.063
![]() |
[118] |
Bai Y, Yang M, Fan J, et al. (2020) Influence of geometry on the thermal performance of water pit seasonal heat storages for solar district heating. Build Simul 14: 579–599. https://doi.org/10.1007/s12273-020-0671-9 doi: 10.1007/s12273-020-0671-9
![]() |
[119] |
Li Q, Lin W, Huang X, et al. (2022) Thermocline dynamics in a thermally stratified water tank under different operation modes. Appl Therm Eng 212: 118560. https://doi.org/10.1016/j.applthermaleng.2022.118560 doi: 10.1016/j.applthermaleng.2022.118560
![]() |
[120] |
Chang Z, Li X, Falcoz Q, et al. (2022) Quasi-analytical study of dynamic performance of the thermocline heat storage system under time-varying inlet flow and temperature environment. Sol Energy 244: 264–278. https://doi.org/10.1016/j.jsolener.2022.08024 doi: 10.1016/j.jsolener.2022.08024
![]() |
[121] | Wang XH, He ZY, Xu C, et al. (2019) Dynamic simulations on simultaneous charging/discharging process of water thermocline storage tank. Proc CSEE 39: 5989–5998. Available from: https://epjournal.csee.org.cn/zgdjgcxb/article/doi/10.13334/j.0258-8013.pcsee.190027. |
[122] |
Falcoz Q, Vannerem S, Neveu P (2022) Experimental investigation of the impact of fluid distribution on thermocline storage performance. J Energy Storage 52: 104864. https://doi.org/10.1016/j.est.2022.104864 doi: 10.1016/j.est.2022.104864
![]() |
[123] |
Erasmus S, Maritz J (2023) A carbon reduction and waste heat utilization strategy for generators in scalable PV-Diesel generator campus microgrids. Energies 16: 6749. https://doi.org/10.3390/en16186749 doi: 10.3390/en16186749
![]() |
[124] | Feng GH, Zhu YH, Huang KL, et al. (2016) Heat storage and release performance simulation and multiple factors analysis in phase change energy storage tank. J Shenyang Jianzhu Univ Nat Sci 32: 675–683. Available from: https://qikan.cqvip.com/Qikan/Article/Detail?id=669645697&from=Qikan_Search_Index. |
[125] |
Faraj K, Khaled M, Faraj J, et al. (2020) Phase change material thermal energy storage systems for cooling applications in buildings: A review. Renewable Sustainable Energy Rev 119: 10957. https://doi.org/10.1016/j.rser.2019.10957 doi: 10.1016/j.rser.2019.10957
![]() |
[126] |
Luo J, Zou DQ, Wang YS, et al. (2022) Battery thermal management systems (BTMs) based on phase change material (PCM): A comprehensive review. Chem Eng J 430: 132741. https://doi.org/10.1016/j.cej.2021.132741 doi: 10.1016/j.cej.2021.132741
![]() |
[127] | Yang G, Xiao X, Wang YF (2024) Research progress of compression heat pump coupled with heat storage of phase change materials. J Refrig, 1–15 Available from: https://qikan.cqvip.com/Qikan/Article/Detail?id=7200116584&from=Qikan_Search_Index. |
[128] | Liu X, Wu JH, Xian T, et al. (2019) Preparation and properties of CaCl2·6H2O/expanded graphite composite phase change materials. J Zhejiang Univ Eng Sci 53: 1291–1297. Available from: https://qikan.cqvip.com/Qikan/Article/Detail?id=7002235920&from=Qikan_Search_Index. |
[129] |
Mselle BD, Zsembinszki G, Verez D, et al. (2022) Experimental assessment of the influence of the design on the performance of novel evaporators with latent energy storage ability. Appl Sci Basel 12: 1813. https://doi.org/10.3390/app12041813 doi: 10.3390/app12041813
![]() |
[130] |
Zhou GB, Zhang YP, Zhang QL, et al. (2007) Performance of a hybrid heating system with thermal storage using shape-stabilized phase-change material plates. Appl Energy 84: 1068–1077. https://doi.org/10.1016/j.apenergy.2006.09.015 doi: 10.1016/j.apenergy.2006.09.015
![]() |
[131] |
Sharma A, Tyagi VV, Chen CR, et al. (2009) Review on thermal energy storage with phase change materials and applications. Renewable Sustainable Energy Rev 13: 318–345. https://doi.org/10.1016/j.rser.2007.10.005 doi: 10.1016/j.rser.2007.10.005
![]() |
[132] |
Zou DQ, Ma XF, Liu XS, et al. (2017) Experimental research of an air-source heat pump water heater using water-PCM for heat storage. Appl Energy 206: 784–792. https://doi.org/10.1016/j.apenergy.2017.08.209 doi: 10.1016/j.apenergy.2017.08.209
![]() |
[133] |
Bansal NK, Buddhi D (1992) An analytical study of a latent heat storage system in a cylinder. Energy Conv Manage 33: 235–242. https://doi.org/10.1016/0196-8904(92)90113-B doi: 10.1016/0196-8904(92)90113-B
![]() |
[134] |
Mettawee EBS, Assassa GMR (2006) Experimental study of a compact PCM solar collector. Energy 31: 2958–2968. https://doi.org/10.1016/j.energy.2005.11.019 doi: 10.1016/j.energy.2005.11.019
![]() |
[135] |
Li XL, Tong C, Lin DM, et al. (2016) Research on U-tube heat exchanger with shape-stabilized phase change backfill material. Proc Eng 146: 640–647. https://doi.org/10.1016/j.proeng.2016.06.420 doi: 10.1016/j.proeng.2016.06.420
![]() |
[136] |
Sadeghi G, Mehrali M, Shahi M, et al. (2022) Progress of experimental studies on compact integrated solar collector-storage retrofits adopting phase change materials. Sol Energy 237: 62–95. https://doi.org/10.1016/j.solener.2022.03.070 doi: 10.1016/j.solener.2022.03.070
![]() |
[137] |
Long Z, Jiankai D, Yiqiang J, et al. (2014) A novel defrosting method using heat energy dissipated by the compressor of an air source heat pump. Appl Energy 133: 101–111. https://doi.org/10.1016/j.apenergy.2014.07.039 doi: 10.1016/j.apenergy.2014.07.039
![]() |
[138] |
Zheng CX, You SJ, Zhang H, et al. (2020) Defrosting performance improvement of air-source heat pump combined refrigerant direct-condensation radiant floor heating system with phase change material. Energies 13: 4594. https://doi.org/10.3390/en13184594 doi: 10.3390/en13184594
![]() |
[139] | Hu XD, Gao XN, Li DL, et al. (2013) Performance of paraffin/expanded graphite composite phase change materials. CIESC J 64: 3831–3837. Available from: https://hgxb.cip.com.cn/CN/10.3969/j.issn.0438-1157.2013.10.047. |
[140] |
Leong KY, Rahman MRA, Gurunathan BA (2019) Nano-enhanced phase change materials: A review of thermo-physical properties, applications and challenges. J Energy Storage 21: 18–31. https://doi.org/10.1016/j.est.2018.11.008 doi: 10.1016/j.est.2018.11.008
![]() |
[141] |
Jin X, Wu FP, Xu T, et al. (2021) Experimental investigation of the novel melting point modified Phase-Change material for heat pump latent heat thermal energy storage application. Energy 216: 119191. https://doi.org/10.1016/j.energy.2020.119191 doi: 10.1016/j.energy.2020.119191
![]() |
[142] |
Li MQ, Lin ZQ, Sun YJ, et al. (2020) Preparation and characterizations of a novel temperature-tuned phase change material based on sodium acetate trihydrate for improved performance of heat pump systems. Renewable Energy 157: 670–677. https://doi.org/10.1016/j.renene.2020.05061 doi: 10.1016/j.renene.2020.05061
![]() |
[143] |
Liu YH, Wang L, Zhang S, et al. (2024) Experimental study on heat storage and discharge characteristics of packed bed based on hydrated salt using cylindrical encapsulation units. Energy Storage Sci Technol, 1–10. https://doi.org/10.1019799/jcnki2095-4239.2024.0187 doi: 10.1019799/jcnki2095-4239.2024.0187
![]() |
[144] |
Li Y, Zhou S, Wang S, et al. (2023) Preparation and thermal properties of a novel ternary molten salt/expanded graphite thermal storage material. J Energy Storage 74: 109273. https://doi.org/10.1016/j.est.2023.109273 doi: 10.1016/j.est.2023.109273
![]() |
[145] |
Wu SF, Yan T, Kuai ZH, et al. (2020) Thermal conductivity enhancement on phase change materials for thermal energy storage: A review. Energy Storage Mater 25: 251–295. https://doi.org/10.1016/j.ensm.2019.10.010 doi: 10.1016/j.ensm.2019.10.010
![]() |
[146] |
Yuan KJ, Shi JM, Aftab W, et al. (2020) Engineering the thermal conductivity of functional phase-change materials for heat energy conversion, storage, and utilization. Adv Funct Mater 30: 1904228. https://doi.org/10.1002/adfm.201904228 doi: 10.1002/adfm.201904228
![]() |
[147] |
Lyu PZ, Liu XJ, Qu J, et al. (2020) Recent advances of thermal safety of lithium-ion battery for energy storage. Energy Storage Mater 31: 195–220. https://doi.org/10.1016/j.est.2020.06.042 doi: 10.1016/j.est.2020.06.042
![]() |
[148] |
Heyhat MM, Mousavi S, Siavashi M (2020) Battery thermal management with thermal energy storage composites of PCM, metal foam, fin and nanoparticle. J Energy Storage 28: 101235. https://doi.org/10.1016/j.est.2020.101235 doi: 10.1016/j.est.2020.101235
![]() |
[149] |
Jilte R, Afzal A, Panchal S (2021) A novel battery thermal management system using nano-enhanced phase change materials. Energy 219: 119564. https://doi.org/10.1016/j.energy.2020.119564 doi: 10.1016/j.energy.2020.119564
![]() |
[150] | Chang H, Tao YB (2024) Performance study of metal hydride hydrogen storage based on thermochemical heat storage. J Eng Thermophys 45: 500–505. Available from: https://qikan.cqvip.com/Qikan/Article/Detail?id=7111555829&from=Qikan_Search_Index. |
[151] | Xu J, Pan QW, Zhang W, et al. (2024) Experimental study on a hybrid adsorption refrigeration system powered by low grade heat from fuel cells. J Eng Thermophys 45: 1–6. Available from: https://qikan.cqvip.com/Qikan/Article/Detail?id=7111465508&from=Qikan_Search_Index. |
[152] |
Funayama S, Kato T, Tamano S, et al. (2024) Thermal energy storage with flexible discharge performance based on molten-salt thermocline and thermochemical energy storage. Appl Therm Eng 238: 121947. https://doi.org/10.1016/j.applthermaleng.2023.121947 doi: 10.1016/j.applthermaleng.2023.121947
![]() |
[153] |
Li L, Li WY, Ma JL (2023) Research on coordinated control strategy of power response rate of thermal power plant with high temperature molten salt heat storage. Int J Heat Technol 41: 55–62. https://doi.org/10.1018280/ijht410106 doi: 10.1018280/ijht410106
![]() |
[154] |
Lu JF, Ding J, Wang WL, et al. (2024) Anisotropic heat characteristics and analysis of molten salt thermocline storage system. J Energy Storage 84: 110773. https://doi.org/10.1016/j.est.2024.110773 doi: 10.1016/j.est.2024.110773
![]() |
[155] | Yan T, Wang WH, Wang RZ (2018) Present status and progress of research on chemical adsorption heat storage. Mater Rep 32: 4107–4115. Available from: https://qikan.cqvip.com/Qikan/Article/Detail?id=7000962317&from=Qikan_Search_Index. |
[156] |
Ganzer C, Pratama YW, Mac Dowell N (2022) The role and value of inter-seasonal grid-scale energy storage in net zero electricity systems. Int J Greenhouse Gas Control 120: 103740. https://doi.org/10.1016/j.ijggc.2022.103740 doi: 10.1016/j.ijggc.2022.103740
![]() |
[157] |
Ye AQ, Guan BW, Liu XH, et al. (2023) Using solar energy to achieve near-zero energy buildings in Tibetan Plateau. Renewable Energy 218: 119347. https://doi.org/10.1016/j.renene.2023.119347 doi: 10.1016/j.renene.2023.119347
![]() |
[158] | He M, Wang Z, Yuan G, et al. (2021) A technical introduction of water pit for long-term seasonal solar thermal energy storage. Renewable Energy 368: 68–70. Available from: https://qikan.cqvip.com/Qikan/Article/Detail?id=7106076587. |
[159] |
Wang M, Zhang XY, Li BJ, et al. (2022) Discussion on the application of solar district heating technologies in Tibet. Build Sci 38: 1–6. https://doi.org/10.13614/j.cnki.11-1962/tu.2022.10.01 doi: 10.13614/j.cnki.11-1962/tu.2022.10.01
![]() |
[160] |
Xu L, Guo F, Hoes P-J, et al. (2021) Investigating energy performance of large-scale seasonal storage in the district heating system of chifeng city: Measurements and model-based analysis of operation strategies. Energy Build 247: 111113. https://doi.org/10.1016/j.enbuild.2021.111113 doi: 10.1016/j.enbuild.2021.111113
![]() |
[161] |
Guo F, Yang X (2021) Long-term performance simulation and sensitivity analysis of a large-scale seasonal borehole thermal energy storage system for industrial waste heat and solar energy. Energy Build 236:10768. https://doi.org/10.1016/j.enbuild.2021.110768 doi: 10.1016/j.enbuild.2021.110768
![]() |
[162] |
Guo F, Yang X, Xu L, et al. (2017) A central solar-industrial waste heat heating system with large scale borehole thermal storage. Proc Eng 205: 1584–1591. https://doi.org/10.1016/j.proeng.2017.10.274 doi: 10.1016/j.proeng.2017.10.274
![]() |
[163] |
Sifnaios I, Jensen AR, Furbo S, et al. (2022) Performance comparison of two water pit thermal energy storage (PTES) systems using energy, exergy, and stratification indicators. J Energy Storage 52: 104947. https://doi.org/10.1016/j.est.2022.104947 doi: 10.1016/j.est.2022.104947
![]() |
Industries | Waste heat resources | Waste heat recovery rate |
Thermal power generation | Flue gas, spent steam condensation waste heat | Above 50% |
Iron and steel metallurgy | Slag flushing water, blast furnace exhaust gas, etc. | Above 30% |
Petroleum | Oil production wastewater | 30%~40% |
Chemical industry | Process cooling water, industrial wastewater, exhaust gas, etc. | Above 30% |
Industries | Production volume/10,000 t | Waste heat resources per unit of product/(gce/t) |
Thermal power generation | 100,739 | 571 |
Iron and steel metallurgy | 85,236 | 260 |
Petroleum and chemical | 79,135 | 1,396 |
Industries | Total amount of low-temperature waste heat resources/10,000 tce | Utilizable low-temperature waste heat resources/10,000 tce |
Thermal power generation | 43,906 | 34,833 |
Iron and steel metallurgy | 10,734 | 7,633 |
Petroleum and chemical | 11,573 | 8,370 |
Type | PCM | Phase transition temperature (℃) |
Density (kg/m³) |
Thermal conductivity [W/(m·K)] |
Latent heat of change (kJ/kg) |
Inorganic materials | CaCl2·6H2O [128] | 29.9 | 1710 | 0.57 | 190.0 |
Paraffinic | ParaffinRT4 [129] | 2.0~4.0 | 880(s)/770(l) | 0.20 | 180.0 |
Paraffin [130] | 21.0 | 850 | 0.20 | ||
ParaffinC21H44 [131] | 40.0 | 800 | 0.14 | 220.0 | |
ParaffinRT-44HC [132] | 43.0 | 860(s)/760(l) | 0.20 | 255.0 | |
Paraffin(p-116) [133] | 44.0 | 817 | 0.16 | 226.0 | |
Paraffin [134] | 53.5 | 810(s)/790(l) | 0.21 | 266.0 | |
Organic Materials | Orthoanisic acid [135] | 31.6 | 878 | \ | 155.4 |
Polyethylene Glycol | 52.0~66.0 | \ | \ | \ | |
6000 [136] | 0 | \ | \ | \ | |
Stearic Acid [133] | 58.1 | 965 | 0.29 | 169.0 | |
Composite phase change materials | 35%Lauric Acid/65%Anacardic Acid [137] | 19.8 | \ | 0.14 | 133.2 |
60%Anacardic Acid/24%lauric acid/10%SiO2/6%EG [135] | \ | \ | 0.53 | 109.2 | |
339%dodecanoic acid/412%tetradecanol/201%cetyl alcohol/5%EG [138] | 26.1 | \ | \ | 172.2 | |
80%Paraffin/20%EG [139] | 27.3 | \ | 9.80 | 156.6 | |
FAC/epoxyalkane [140] | 33.9~35.8 | \ | 0.48~0.53 | 211.7 | |
SAT/AC complex [141] | 47.8 | \ | \ | 219.8 | |
SAT/KCI complex [142] | 47.8 | \ | \ | 242.0 | |
In the table, '/' represents 'No Data Available.' |
Industries | Waste heat resources | Waste heat recovery rate |
Thermal power generation | Flue gas, spent steam condensation waste heat | Above 50% |
Iron and steel metallurgy | Slag flushing water, blast furnace exhaust gas, etc. | Above 30% |
Petroleum | Oil production wastewater | 30%~40% |
Chemical industry | Process cooling water, industrial wastewater, exhaust gas, etc. | Above 30% |
Industries | Production volume/10,000 t | Waste heat resources per unit of product/(gce/t) |
Thermal power generation | 100,739 | 571 |
Iron and steel metallurgy | 85,236 | 260 |
Petroleum and chemical | 79,135 | 1,396 |
Industries | Total amount of low-temperature waste heat resources/10,000 tce | Utilizable low-temperature waste heat resources/10,000 tce |
Thermal power generation | 43,906 | 34,833 |
Iron and steel metallurgy | 10,734 | 7,633 |
Petroleum and chemical | 11,573 | 8,370 |
Type | PCM | Phase transition temperature (℃) |
Density (kg/m³) |
Thermal conductivity [W/(m·K)] |
Latent heat of change (kJ/kg) |
Inorganic materials | CaCl2·6H2O [128] | 29.9 | 1710 | 0.57 | 190.0 |
Paraffinic | ParaffinRT4 [129] | 2.0~4.0 | 880(s)/770(l) | 0.20 | 180.0 |
Paraffin [130] | 21.0 | 850 | 0.20 | ||
ParaffinC21H44 [131] | 40.0 | 800 | 0.14 | 220.0 | |
ParaffinRT-44HC [132] | 43.0 | 860(s)/760(l) | 0.20 | 255.0 | |
Paraffin(p-116) [133] | 44.0 | 817 | 0.16 | 226.0 | |
Paraffin [134] | 53.5 | 810(s)/790(l) | 0.21 | 266.0 | |
Organic Materials | Orthoanisic acid [135] | 31.6 | 878 | \ | 155.4 |
Polyethylene Glycol | 52.0~66.0 | \ | \ | \ | |
6000 [136] | 0 | \ | \ | \ | |
Stearic Acid [133] | 58.1 | 965 | 0.29 | 169.0 | |
Composite phase change materials | 35%Lauric Acid/65%Anacardic Acid [137] | 19.8 | \ | 0.14 | 133.2 |
60%Anacardic Acid/24%lauric acid/10%SiO2/6%EG [135] | \ | \ | 0.53 | 109.2 | |
339%dodecanoic acid/412%tetradecanol/201%cetyl alcohol/5%EG [138] | 26.1 | \ | \ | 172.2 | |
80%Paraffin/20%EG [139] | 27.3 | \ | 9.80 | 156.6 | |
FAC/epoxyalkane [140] | 33.9~35.8 | \ | 0.48~0.53 | 211.7 | |
SAT/AC complex [141] | 47.8 | \ | \ | 219.8 | |
SAT/KCI complex [142] | 47.8 | \ | \ | 242.0 | |
In the table, '/' represents 'No Data Available.' |