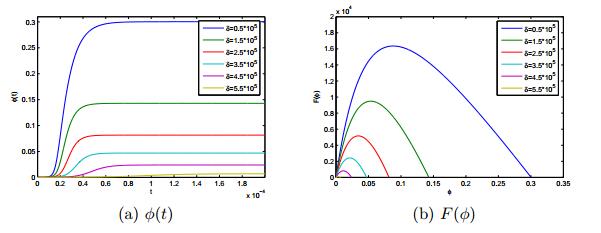
Citation: Shemelis Nigatu Gebremariam, Jorge Mario Marchetti. Biodiesel production technologies: review[J]. AIMS Energy, 2017, 5(3): 425-457. doi: 10.3934/energy.2017.3.425
[1] | Florencia G. Palis, R. M. Lampayan, R.J. Flor, E. Sibayan . A multi-stakeholder partnership for the dissemination of alternate wetting and drying water-saving technology for rice farmers in the Philippines. AIMS Agriculture and Food, 2017, 2(3): 290-309. doi: 10.3934/agrfood.2017.3.290 |
[2] | Theodor Friedrich, Amir Kassam . Food security as a function of Sustainable Intensification of Crop Production. AIMS Agriculture and Food, 2016, 1(2): 227-238. doi: 10.3934/agrfood.2016.2.227 |
[3] | Boris Boincean, Amir Kassam, Gottlieb Basch, Don Reicosky, Emilio Gonzalez, Tony Reynolds, Marina Ilusca, Marin Cebotari, Grigore Rusnac, Vadim Cuzeac, Lidia Bulat, Dorian Pasat, Stanislav Stadnic, Sergiu Gavrilas, Ion Boaghii . Towards Conservation Agriculture systems in Moldova. AIMS Agriculture and Food, 2016, 1(4): 369-386. doi: 10.3934/agrfood.2016.4.369 |
[4] | Isaac Busayo Oluwatayo . Towards assuring food security in South Africa: Smallholder farmers as drivers. AIMS Agriculture and Food, 2019, 4(2): 485-500. doi: 10.3934/agrfood.2019.2.485 |
[5] | Fernando Arias, Maytee Zambrano, Kathia Broce, Carlos Medina, Hazel Pacheco, Yerenis Nunez . Hyperspectral imaging for rice cultivation: Applications, methods and challenges. AIMS Agriculture and Food, 2021, 6(1): 273-307. doi: 10.3934/agrfood.2021018 |
[6] | J.M.A. Duncan, J. Dash, E.L. Tompkins . Observing adaptive capacity in Indian rice production systems. AIMS Agriculture and Food, 2017, 2(2): 165-182. doi: 10.3934/agrfood.2017.2.165 |
[7] | Raulston Derrick Gillette, Norio Sakai, Godfrid Erasme Ibikoule . Role and impact of contract farming under various pricing standards: A case of Guyana's rice sector. AIMS Agriculture and Food, 2024, 9(1): 336-355. doi: 10.3934/agrfood.2024020 |
[8] | Karin Lindsjö, Agnes Anderssonc Djurfeldt, Aida Cuthbert Isinika, Elibariki Msuya . Youths' participation in agricultural intensification in Tanzania. AIMS Agriculture and Food, 2020, 5(4): 681-699. doi: 10.3934/agrfood.2020.4.681 |
[9] | Abbas Ali Chandio, Yuansheng Jiang, Abdul Rehman, Rahman Dunya . The linkage between fertilizer consumption and rice production: Empirical evidence from Pakistan. AIMS Agriculture and Food, 2018, 3(3): 295-305. doi: 10.3934/agrfood.2018.3.295 |
[10] | Deborah Nabuuma, Beatrice Ekesa, Mieke Faber, Xikombiso Mbhenyane . Food security and food sources linked to dietary diversity in rural smallholder farming households in central Uganda. AIMS Agriculture and Food, 2021, 6(2): 644-662. doi: 10.3934/agrfood.2021038 |
Currently it is the digital era where there is a steady flood of information. Such information inundation makes a variety of mass media more important, for example, newspapers, broadcast, social network system media, and public speaking. Before developing mass media, rumors propagated by word of mouth and played a crucial role in communication between people or groups. This process can be understood as a kind of homogenization of information system and social interaction [1]. With the emergence of multimedia and social media, rumors have spread faster and have wide transmissions [5]. However, some harmful and powerful rumor outbreaks arise from such wide transmission via these media [10,14,18]. Moreover, their influence causes multiple effects for a variety of situations rather than the mono effect for localized situations [12].
As a benefit in return for the homogenization, personality is more heavily emphasized and the diversity of people has garnered much attention in our social community. In the microscopic viewpoint of rumor spreading, this variety of characteristics is important. Many researchers already have investigated that the degree of belief is important in rumor spreading [8,16]. From this perspective, we assume that there will be various groups that share the same trust rate. In this paper, we propose an SIR type rumor spreading model with given spreading rate distributions
Next we provide a brief historical review of the rumor spreading model. Starting the pioneering studies by Daley and Kendall [3,4], a lot of researchers have studied rumor spreading and tried to build mathematical models [11,17]. Zanette [23,24] numerically obtained the existence of a critical threshold for a rumor spreading model regarding small-world networks. In [13], the authors derived the mean-field equation of complex heterogeneous networks. For other topological settings, see [7,15]. Most mathematical models for rumor spreading are based on the epidemic model. In [27], the authors considered an SIR type rumor spreading model with forgetting mechanism. See also [6,28] for other models with forgetting mechanisms. In [26], the authors added a hibernator variable to the SIR type rumor spreading model. Similarly, in [20,22], the authors adapted several new variables to construct a more realistic model for the rumor spreading phenomena. In [25], the authors employed the probability that ignorants directly become stiflers when they are aware of a rumor. We refer to papers [2,9,29] for other rumor spreading models.
The paper is organized as follows. In Section 2, we present the trust distribution and its mechanism in the SIR type model. In Section 3, we derive a single equation for the rumor size
Notation: Throughout the paper, we use the following simplified notation:
I(t)=(I1(t),…,IN(t)), ˚I=(˚I1,…,˚IN), ˚In=(˚In1,…,˚InN), n,N∈N. |
Let
There are three groups of populations: ignorants (I), spreaders (S), and stiflers (R). At the first stage, ignorants contact a spreader, realize a rumor, and accept the hearsay. According to the acceptance with rate
˙I=−kλSI,˙S=kλSI−kS(σ1S+σ2R),˙R=kσS(S+R), |
where
As in [25], we assume that spreaders lose their interest in rumors with probability
˙Ii=−kλiSIi, i=1,…,N,˙S=N∑i=1kλiSIi−kσS(S+R)−δS,˙R=kσS(S+R)+δS, | (1) |
subject to initial data
Throughout this paper, we assume that
(1)
(2) The spreading (trust) rate distribution
We will consider a family of initial data
˚T=(N∑j=1˚Ij)+˚S+˚R |
for a fixed total initial population
Next, we define the rumor size, a momentum type quantity of the initial data and rumor outbreak.
Definition 2.1. [19,25,26]For a solution
ϕ(t)=∫t0S(τ)dτ. |
Definition 2.2. Let
M1(˚I)=N∑i=1λi˚Ii |
and total population with initial
T(t)=(N∑i=1Ii(t))+S(t)+R(t). |
Definition 2.3. Let
ϕ∞(˚I,˚S):=limt→∞ϕ(t). |
Definition 2.4. For a given initial data
˚In→˚I, ˚Sn→0 as n→∞ |
and
˚Sn>0, ˚Rn=0 for n∈N. |
We additionally assume that the total populations are the same:
˚T=(N∑i=1˚Ii)+˚S+˚R=(N∑i=1˚Ini)+˚Sn+˚Rn=˚Tn. |
We say that a rumor outbreak occurs if the following limit exists
ϕe(˚I)=limn→∞ϕ∞(˚In,˚Sn) |
and
Remark 1. (1) In [13,15,25], the authors define that the rumor outbreak occurs if
lim˚R→0R(∞)>0. |
This is essentially equivalent to Definition 2.4. We use
(2) The rumor spreading begins with one spreader. Therefore,
The following is the main theorem of this paper.
Theorem 2.5. Let
We assume that each
˚T=(N∑k=1˚Ink)+˚Sn=N∑i=1˚Ii. |
Then, there exists the following limit of steady states:
ϕe=ϕe(˚I)=lim˚Sn→0,˚In→˚Iϕ∞(˚In,˚Sn), |
where
Furthermore, if
Remark 2. An equivalent condition of occurring a rumor outbreak is
kM1(˚I)>δ. |
In this section, we derive a single equation for
Lemma 3.1. Let
Ii(t)=˚Iie−kλiϕ(t), i=1,…,N, | (2) |
where
Proof. From the first equation of system (1), we have
ddtlogIi(t)=−kλiS(t), i=1,…,N. |
Integrating the above relation gives
logIi(t)=log˚Ii−∫t0kλiS(τ)dτ, i=1,…,N. |
For the population density of
Ii(t)=˚Iie−∫t0kλiS(τ)dτ, i=1,…,N. |
Clearly, we have
Lemma 3.2. Let
T(t)=˚T, for any t>0. | (3) |
Proof. Note that the summation of all equations in system (1) yields
(N∑i=1˙Ii)+˙S+˙R=0. |
Integrating the above equation leads to
T(t)=(N∑i=1Ii(t))+S(t)+R(t)=(N∑i=1˚Ii)+˚S+˚R=˚T. |
Remark 3. By the conservation property (3) in Lemma 3.2 and the formula in (2), we easily obtain the following formula for
S(t)=˚T−N∑i=1Ii(t)−R(t)=˚T−N∑i=1˚Iie−kλiϕ(t)−R(t). | (4) |
Lemma 3.3. Let
R(t)=R(ϕ(t))=˚R+kσ˚Tϕ(t)−kσ∑λi≠0˚Ii1−e−kλiϕ(t)kλi−kσ∑λi=0˚Iiϕ(t)+δϕ(t). |
Proof. The third equation in system (1) gives us that
R(t)−˚R=∫t0˙R(τ)dτ=∫t0[kσS(τ)(S(τ)+R(τ))+δS(τ)]dτ. |
From (4) and the definition of
R(t)−˚R=kσ∫t0S(τ)[S(τ)+R(τ)]dτ+δϕ(t)=kσ∫t0S(τ)(˚T−N∑i=1Ii(τ))dτ+δϕ(t)=kσ∫t0ϕ′(τ)(˚T−N∑i=1˚Iie−kλiϕ(τ))dτ+δϕ(t)=kσ˚T∫t0ϕ′(τ)dτ−∑λi≠0kσ∫t0ϕ′(τ)˚Iie−kλiϕ(τ)dτ−∑λi=0kσ∫t0ϕ′(τ)˚Iie−kλiϕ(τ)dτ+δϕ(t)=K1+K2+K3+K4. |
We directly have
K1=kσ˚Tϕ(t) and K4=δϕ(t). |
For
K2=−∑λi≠0kσ∫t0ϕ′(τ)e−kλiϕ(τ)dτ=−∑λi≠0kσ∫ϕ(t)ϕ(0)e−kλiηdη=−∑λi≠0kσe−kλiϕ(0)−e−kλiϕ(t)kλi=−∑λi≠0kσ1−e−kλiϕ(t)kλi. |
Similarly, we have
K3=−∑λi=0kσ∫t0ϕ′(τ)e−kλiϕ(τ)dτ=−∑λi=0kσ∫t0ϕ′(τ)dτ=−∑λi=0kσ(ϕ(t)−ϕ(0))=−∑λi=0kσϕ(t). |
Therefore, the above elementary calculations yield
R(t)−˚R=kσ˚Tϕ(t)−kσ∑λi≠0˚Ii1−e−kλiϕ(t)kλi−kσ∑λi=0˚Iiϕ(t)+δϕ(t). |
The formula (4) of
dϕ(t)dt=S(t)=˚T−N∑i=1˚Iie−kλiϕ(t)−R(t). |
By the result in Lemma 3.3, we derive a single decoupled equation for
dϕ(t)dt=˚T−N∑i=1˚Iie−kλiϕ(t)−˚R−kσ˚Tϕ(t)+kσ∑λi≠0˚Ii1−e−kλiϕ(t)kλi+kσ∑λi=0˚Iiϕ(t)−δϕ(t). |
For simplicity, we define
F(ϕ)=F(ϕ,˚I,˚S,˚R,˚T):=˚T−N∑i=1˚Iie−kλiϕ−˚R−kσ˚Tϕ+kσ∑λi≠0˚Ii1−e−kλiϕkλi+kσ∑λi=0˚Iiϕ(t)−δϕ. | (5) |
Then,
˙ϕ(t)=F(ϕ(t)). | (6) |
In this section, we use the steady state analysis to obtain the threshold phenomena for asymptotic behavior of the solution to system (1). To obtain the asymptotic behavior of solutions to (6), we first consider a steady state
F(ϕ)=0, | (7) |
where
G(ϕ)=G(ϕ,˚I,˚S,˚R,˚T)=˚T−N∑i=1˚Iie−kλiϕ−˚R+kσ∑λi≠0˚Ii1−e−kλiϕkλi | (8) |
and
H(ϕ)=H(ϕ,˚I,˚S,˚R,˚T)=(δ+kσ˚T−kσ∑λi=0˚Ii)ϕ. | (9) |
Then, we divide
H(ϕ)=G(ϕ). |
Lemma 4.1. Let
G(0)=˚S, and limϕ→∞G(ϕ)<∞, if ˚R=0. |
Proof. By the definition of
For the next result, we take the limit such that
limϕ→∞G(ϕ)=limϕ→∞(˚T−N∑i=1˚Iie−kλiϕ−˚R+kσ∑λi≠0˚Ii1−e−kλiϕkλi)=limϕ→∞(˚T−∑λi≠0˚Iie−kλiϕ−∑λi=0˚Ii−˚R+kσ∑λi≠0˚Ii1−e−kλiϕkλi)=˚T−∑λi=0˚Ii−˚R+kσ∑λi≠0˚Iikλi. |
Therefore, we have
kσ∑λi≠0˚Iikλi<∞. |
Therefore, we conclude that
Lemma 4.2. Assume that
dGdϕ=∑λi≠0(kλi˚Iie−kλiϕ+kσ˚Iie−kλiϕ)>0. |
Proof. Note that the derivative of
dGdϕ=−ddϕN∑i=1˚Iie−kλiϕ+kσ∑λi≠0˚Iie−kλiϕ. |
We can calculate the first term in the above as
ddϕN∑i=1˚Iie−kλiϕ=ddϕ∑λi≠0˚Iie−kλiϕ+ddϕ∑λi=0˚Iie−kλiϕ=ddϕ∑λi≠0˚Iie−kλiϕ+ddϕ∑λi=0˚Ii=−∑λi≠0kλi˚Iie−kλiϕ. |
Thus, if at least one non-zero
dGdϕ=∑λi≠0kλi˚Iie−kλiϕ+kσ∑λi≠0˚Iie−kλiϕ>0. |
Lemma 4.3. Let
Proof. Note that
δ+kσ˚T−kσ∑λi=0˚Ii=δ+kσ(N∑i=1˚Ii+˚S+˚R)−kσ∑λi=0˚Ii=δ+kσ(∑λi≠0˚Ii+˚S+˚R). |
Therefore,
Proposition 1. Let
Then there is a final rumor size
ϕ∞(˚I,˚S):=limt→∞ϕ(t), |
where
F(ϕ∞(˚I,˚S))=0. |
Proof. This follows from an elementary result of ordinary differential equations. Note that for given initial data
F(0)=G(0)−H(0)=˚S>0, |
and
limϕ→∞F(ϕ)=G(ϕ)−H(ϕ)=−∞. |
By the intermediate value theorem, there is at least one positive solution
For a fixed
Proposition 2. Let
The equation
Proof. We have, by Lemma 4.1 and 4.3,
G(0)=˚S=0, limϕ→∞G(ϕ)<∞ |
and
H(0)=0, limϕ→∞H(ϕ)=∞. |
It follows that
limϕ→∞F(ϕ)=−∞. | (10) |
Lemma 4.2 implies that the derivative of
dGdϕ=∑λi≠0kλi˚Iie−kλiϕ+kσ∑λi≠0˚Iie−kλiϕ>0. |
Moreover, if
dHdϕ(ϕ,˚I,˚S,˚R,˚T)=δ+kσ˚T−kσ∑λi=0˚Ii. |
Therefore,
dFdϕ=dGdϕ−dHdϕ=∑λi≠0kλi˚Iie−kλiϕ+kσ∑λi≠0˚Iie−kλiϕ−(δ+kσ˚T−kσ∑λi=0˚Ii). | (11) |
So,
dFdϕ(0)=dGdϕ(0)−dHdϕ(0)=∑λi≠0kλi˚Ii+kσ∑λi≠0˚Ii−(δ+kσ˚T−kσ∑λi=0˚Ii)=∑λi≠0kλi˚Ii−δ=kM1−δ. |
This yields
kM1>δ⇒dFdϕ(0)>0, | (12) |
and the continuity of
F(ϕϵ)>0. |
Thus, the intermediate value theorem and (10) show that
In order to complete the proof of this proposition, it suffices to verify that the equation has a unique solution
We now assume that
dFdϕ=∑λi≠0kλi˚Iie−kλiϕ+kσ∑λi≠0˚Iie−kλiϕ−(δ+kσ˚T−kσ∑λi=0˚Ii)=∑λi≠0kλi˚Iie−kλiϕ+kσ∑λi≠0˚Iie−kλiϕ−(δ+kσ˚T−kσ∑λi=0˚Iie−kλiϕ)=N∑i=1kλi˚Iie−kλiϕ+kσN∑i=1˚Iie−kλiϕ−δ−kσ˚T. |
Since we assume that
dFdϕ≤N∑i=1kλi˚Iie−kλiϕ+kσN∑i=1˚Iie−kλiϕ−N∑i=1kλi˚Ii−kσN∑i=1˚Ii=N∑i=1kλi˚Ii(e−kλiϕ−1)+kσN∑i=1˚Ii(e−kλiϕ−1). |
This implies that
dFdϕ<0 if ϕ>0, and dFdϕ≤0 if ϕ=0. |
The fact in (10) with
F(ϕ)<0 for ϕ>0. |
Therefore, we complete the proof.
We are now ready to prove the main theorem.
The proof of the main theorem. Let
˚In→˚I, ˚Sn→0. | (13) |
We denote
F(ϕ,˚Sn)=F(ϕ,˚In,˚Sn,˚Rn,˚T) and F∞(ϕ)=F(ϕ,˚I,˚S,˚R,˚T). |
First, assume that
F∞(0)=0 and ddϕF∞(ϕ)|ϕ=0>0. |
Note that (11) implies that
∂F∂ϕ(ϕ,˚In,˚Sn,˚Rn,˚T)=∑λi≠0kλi˚Inie−kλiϕ+kσ∑λi≠0˚Inie−kλiϕ−(δ+kσ˚T−kσ∑λi=0˚Ini)=∑λi≠0kλi˚Inie−kλiϕ+kσ∑λi≠0˚Inie−kλiϕ−(δ+kσ˚T−kσ∑λi=0˚Inie−kλiϕ)=N∑i=1kλi˚Inie−kλiϕ+kσN∑i=1˚Inie−kλiϕ−δ−kσ˚T=N∑i=1kλi˚Ini(e−kλiϕ−1)+N∑i=1kλi˚Ini+kσN∑i=1˚Inie−kλiϕ−δ−kσ((N∑i=1˚Ini)+˚Sn). |
Therefore,
∂F∂ϕ(ϕ,˚In,˚Sn,˚Rn,˚T)=N∑i=1kλi˚Ini(e−kλiϕ−1)+kσN∑i=1˚Ini(e−kλiϕ−1)−kσ˚Sn+kM1(˚In)−δ. |
By (13), there is
kM1(˚In)−δ>12(kM1(˚I)−δ) |
and
kσ˚Sn≤14(kM1(˚I)−δ). |
Since
|N∑i=1kλi˚Ini(e−kλiϕ−1)+kσN∑i=1˚Ini(e−kλiϕ−1)|≤14(kM1(˚I)−δ). |
Thus, there are constants
∂F∂ϕ(ϕ,˚In,˚Sn,˚Rn,˚T)>0. | (14) |
In order to prove convergence, we consider differentiable functions
I(1/n)=˚In, S(1/n)=˚Sn, R(1/n)=˚Rn, n∈N, |
and
˚T=(N∑i=1Ii(s))+S(s)+R(s). |
We denote
We now prove that
For
For the last part, we assume that
Let
limn→∞F(ϕnn,˚Inn,˚Snn,˚Rnn,˚T)=F(ϕn∞,˚I,0,0,˚T). |
Therefore, by Proposition 2,
limn→∞ϕn=0. |
In this section, we numerically provide the solutions to system (1) with respect to several
For the numerical simulations, we used the fourth-order Runge-Kutta method with the following parameters:
λ1=1, λ2=2, λ3=3, σ=0.2, k=10. |
We take sufficiently large initial data
˚I1=˚I2=˚I3=9999, ˚S=3, ˚R=0. |
To see the threshold phenomena for
Note that in Proposition 1, we rigorously obtained that the final size of the rumor
In Figure 2, we plotted the densities of the spreaders (S) and the stiflers (R) with respect to several
In Figure 3, we plotted
From our analytic results, we can expect that the threshold occurs when
In this paper, we consider the rumor spreading model with the trust rate distribution. The model consists of several ignorants with trust rates
[1] | EIA UEIA (2016) International energy outlook 20016 With Projections to 2040. Washington, DC 20585: U.S Energy Information Adminstration, Office of Energy Analysis, Department of Energy. |
[2] |
Shafiee S, Topal E (2009) When will fossil fuel reserves be diminished? Energ Policy 37: 181–189. doi: 10.1016/j.enpol.2008.08.016
![]() |
[3] | IEA (2015) Medium term renewable energy market report 2015, Executive Summary: Market analysis and Forcasts to 2020. International Energy Agency. |
[4] | Birol F (2014) world energy outlook 2013–2035. Rotterdam: International Energy Agency, IEA. |
[5] |
Ahmad A, Yasin NM, Derek C, et al. (2011) Microalgae as a sustainable energy source for biodiesel production: a review. Renew Sust Energ Rev 15: 584–593. doi: 10.1016/j.rser.2010.09.018
![]() |
[6] |
Janaun J, Ellis N (2010) Perspectives on biodiesel as a sustainable fuel. Renew Sust Energ Rev 14: 1312–1320. doi: 10.1016/j.rser.2009.12.011
![]() |
[7] |
Kafuku G, Mbarawa M (2010) Biodiesel production from Croton megalocarpus oil and its process optimization. Fuel 89: 2556–2560. doi: 10.1016/j.fuel.2010.03.039
![]() |
[8] |
Satyanarayana M, Muraleedharan C (2011) A comparative study of vegetable oil methyl esters (biodiesels). Energy 36: 2129–2137. doi: 10.1016/j.energy.2010.09.050
![]() |
[9] |
Shahid EMJ, Younis (2011) Production of biodiesel: a technical review. Renew Sust Energ Rev 15: 4732–4745. doi: 10.1016/j.rser.2011.07.079
![]() |
[10] |
Carraretto C, Macor A, Mirandola A, et al. (2004) Biodiesel as alternative fuel: experimental analysis and energetic evaluations. Energy 29: 2195–2211. doi: 10.1016/j.energy.2004.03.042
![]() |
[11] |
Fazal M, Haseeb A, Masjuki H (2011) Biodiesel feasibility study: an evaluation of material compatibility; performance; emission and engine durability. Renew Sust Energ Rev 15: 1314–1324. doi: 10.1016/j.rser.2010.10.004
![]() |
[12] |
Silitonga A, Atabani A, Mahlia T, et al. (2011) A review on prospect of Jatropha curcas for biodiesel in Indonesia. Renew Sust Energ Rev 15: 3733–3756. doi: 10.1016/j.rser.2011.07.011
![]() |
[13] |
Marulanda VF (2012) Biodiesel production by supercritical methanol transesterification: process simulation and potential environmental impact assessment. J Clean Prod 33: 109–116. doi: 10.1016/j.jclepro.2012.04.022
![]() |
[14] | Shin HY, Lee SH, Ryu JH, et al. (2012) Biodiesel production from waste lard using supercritical methanol. The J of Supercriti Fluids 61: 134–138. |
[15] |
Glisic SB, Pajnik JM, Orlović AM (2016) Process and techno-economic analysis of green diesel production from waste vegetable oil and the comparison with ester type biodiesel production. Appl Energ 170: 176–185. doi: 10.1016/j.apenergy.2016.02.102
![]() |
[16] |
Kusdiana D, Saka S (2004) Effects of water on biodiesel fuel production by supercritical methanol treatment. Bioresource Technol 91: 289–295. doi: 10.1016/S0960-8524(03)00201-3
![]() |
[17] |
Meher L, Sagar DV, Naik S (2006) Technical aspects of biodiesel production by transesterification-a review. Renew Sust Energ Rev 10: 248–268. doi: 10.1016/j.rser.2004.09.002
![]() |
[18] |
Koh MY, Mohd. Ghazi TI (2011) A review of biodiesel production from Jatropha curcas L. oil. Renew Sust Energ Rev 15: 2240–2251. doi: 10.1016/j.rser.2011.02.013
![]() |
[19] |
Leung DY, Wu X, Leung M (2010) A review on biodiesel production using catalyzed transesterification. Appl energ 87: 1083–1095. doi: 10.1016/j.apenergy.2009.10.006
![]() |
[20] |
Czernik S, Bridgwater AV (2004) Overview of Applications of Biomass Fast Pyrolysis Oil. Energ Fuels 18: 590–598. doi: 10.1021/ef034067u
![]() |
[21] |
Ma F, Hanna MA (1999) Biodiesel production: a review. Bioresource Technol 70: 1–15. doi: 10.1016/S0960-8524(99)00025-5
![]() |
[22] | Mahanta P, Shrivastava A (2004) Technology development of bio-diesel as an energy alternative. Available from: http://newagepublishers.com/samplechapter/001305.pdf. |
[23] |
Abbaszaadeh A, Ghobadian B, Omidkhah MR, et al. (2012) Current biodiesel production technologies: A comparative review. Energ Convers Manage 63: 138–148. doi: 10.1016/j.enconman.2012.02.027
![]() |
[24] |
French R, Czernik S (2010) Catalytic pyrolysis of biomass for biofuels production. Fuel Process Technol 91: 25–32. doi: 10.1016/j.fuproc.2009.08.011
![]() |
[25] |
Singh SS, Dipti (2010) Biodiesel production through the use of different sources and characterization of oils and their esters as the substitute of diesel: a review. Renew Sust Energ Rev 14: 200–216. doi: 10.1016/j.rser.2009.07.017
![]() |
[26] |
Ranganathan SV, Narasimhan SL, Muthukumar K (2008) An overview of enzymatic production of biodiesel. Bioresource Technol 99: 3975– 3981. doi: 10.1016/j.biortech.2007.04.060
![]() |
[27] | Slomkowski S, Alemán JV, Gilbert RG, et al. (2011) Terminology of polymers and polymerization processes in dispersed systems (IUPAC Recommendations 2011). Pure Appl Chem 83: 2229–2259. |
[28] |
Chiaramonti D, Bonini M, Fratini E, et al. (2003) Development of emulsions from biomass pyrolysis liquid and diesel and their use in engines-Part 1 : emulsion production. Biomass Bioenerg 25: 85– 99. doi: 10.1016/S0961-9534(02)00183-6
![]() |
[29] |
Schwab A, Bagby M, Freedman B (1987) Preparation and properties of diesel fuels from vegetable oils. Fuel 66: 1372–1378. doi: 10.1016/0016-2361(87)90184-0
![]() |
[30] |
Srivastava A, Prasad R (2000) Triglycerides-based diesel fuels. Renew Sust Energ Rev 4: 111–133. doi: 10.1016/S1364-0321(99)00013-1
![]() |
[31] | Bart JCJ, Palmeri N, Cavallaro S (2010) 14-Sustainability and use of biodiesel. Biodiesel Sci Technol 4: 625–712. |
[32] | Pairiawi W (2010) Biodiesel production from Jatropha curcas: A review. Sci Res Essays 5: 1796–1808. |
[33] |
Bilgin A, Durgun O, Sahin Z (2002) The Effects of Diesel-Ethanol Blends on Diesel Engine Performance. Energ Source 24: 431–440. doi: 10.1080/00908310252889933
![]() |
[34] | Lokanatham RPRK (2013) Extraction and Use of Non-Edible Oils in Bio-Diesel Preparation with Performance and Emission Analysis on C.I. Engine. Int Eng Res Develop 6: 35–45. |
[35] | Gerhard Knothe JVG, Jürgen Krahl (2005) The Biodiesel Handbook; Gerhard Knothe JVG, Jürgen Krahl, editor: AOCS Press, Champaign, Illinois. |
[36] | Zhang Y, Dube M, McLean D, et al. (2003) Biodiesel production from waste cooking oil: 1. Process design and technological assessment. Bioresource Technol 89: 1–16. |
[37] |
Park JY, Wang ZM, Kim DK, et al. (2010) Effects of water on the esterification of free fatty acids by acid catalysts. Renew Energ 35: 614–618. doi: 10.1016/j.renene.2009.08.007
![]() |
[38] |
Zheng S, Kates M, Dube M, et al. (2006) Acid-catalyzed production of biodiesel from waste frying oil. Biomass Bioenerg 30: 267–272. doi: 10.1016/j.biombioe.2005.10.004
![]() |
[39] |
Soriano Jr NU, Venditti R, Argyropoulos DS (2009) Biodiesel synthesis via homogeneous Lewis acid-catalyzed transesterification. Fuel 88: 560–565. doi: 10.1016/j.fuel.2008.10.013
![]() |
[40] |
Marchetti J, Miguel V, Errazu A (2008) Techno-economic study of different alternatives for biodiesel production. Fuel Process Technol 89: 740–748. doi: 10.1016/j.fuproc.2008.01.007
![]() |
[41] |
Miao X, Li R, Yao H (2009) Effective acid-catalyzed transesterification for biodiesel production. Energ Convers Manage 50: 2680–2684. doi: 10.1016/j.enconman.2009.06.021
![]() |
[42] |
Ganesan D, Rajendran A, Thangavelu V (2009) An overview on the recent advances in the transesterification of vegetable oils for biodiesel production using chemical and biocatalysts. Rev Environ Sci Bio 8: 367. doi: 10.1007/s11157-009-9176-9
![]() |
[43] |
Farag HA, El-Maghraby A, Taha NA (2011) Optimization of factors affecting esterification of mixed oil with high percentage of free fatty acid. Fuel Process Technol 92: 507–510. doi: 10.1016/j.fuproc.2010.11.004
![]() |
[44] |
Guan G, Kusakabe K, Sakurai N, et al. (2009) Transesterification of vegetable oil to biodiesel fuel using acid catalysts in the presence of dimethyl ether. Fuel 88: 81–86. doi: 10.1016/j.fuel.2008.07.021
![]() |
[45] |
Kulkarni MG, Gopinath R, Meher LC, et al. (2006) Solid acid catalyzed biodiesel production by simultaneous esterification and transesterification. Green Chem 8: 1056–1062. doi: 10.1039/b605713f
![]() |
[46] |
Marchetti J, Miguel V, Errazu A (2007) Possible methods for biodiesel production. Renew Sust Energ Rev 11: 1300–1311. doi: 10.1016/j.rser.2005.08.006
![]() |
[47] |
Díaz GC, Tapanes NdlCO, Câmara LDT, et al. (2014) Glycerol conversion in the experimental study of catalytic hydrolysis of triglycerides for fatty acids production using Ni or Pd on Al2O3 or SiO2. Renew Energ 64: 113–122. doi: 10.1016/j.renene.2013.11.006
![]() |
[48] |
Demirbas A (2009) Progress and recent trends in biodiesel fuels. Energ Convers Manage 50: 14–34. doi: 10.1016/j.enconman.2008.09.001
![]() |
[49] |
Fadhil AB, Ali LH (2013) Alkaline-catalyzed transesterification of Silurus triostegus Heckel fish oil: Optimization of transesterification parameters. Renew Energ 60: 481–488. doi: 10.1016/j.renene.2013.04.018
![]() |
[50] |
Atadashi IM, Aroua MK, Abdul Aziz AR, et al. (2013) The effects of catalysts in biodiesel production: A review. J Ind Eng Chem 19: 14–26. doi: 10.1016/j.jiec.2012.07.009
![]() |
[51] |
Leung D, Guo Y (2006) Transesterification of neat and used frying oil: optimization for biodiesel production. Fuel Process Technol 87: 883–890. doi: 10.1016/j.fuproc.2006.06.003
![]() |
[52] |
Dias JM, Alvim-Ferraz MCM, Almeida MF (2008) Comparison of the performance of different homogeneous alkali catalysts during transesterification of waste and virgin oils and evaluation of biodiesel quality. Fuel 87: 3572–3578. doi: 10.1016/j.fuel.2008.06.014
![]() |
[53] | Boyce ABMSHaAN (2009) Biodiesel Production from Waste Sunflower Cooking Oil as an Environmental Recycling Process and Renewable Energy. Bulgarian J Agricul Sci 15: 312–317. |
[54] |
Meher L, Dharmagadda VS, Naik S (2006) Optimization of alkali-catalyzed transesterification of Pongamia pinnata oil for production of biodiesel. Bioresource technol 97: 1392–1397. doi: 10.1016/j.biortech.2005.07.003
![]() |
[55] | Ojolo S, Ogunsina B, Adelaja A, et al. (2011) Study of an effective technique for the production of biodiesel from jatropha oil. JETEAS 2: 79–86. |
[56] |
Barnwal B, Sharma M (2005) Prospects of biodiesel production from vegetable oils in India. Renew Sust Energ Rev 9: 363–378. doi: 10.1016/j.rser.2004.05.007
![]() |
[57] |
Sinha S, Agarwal AK, Garg S (2008) Biodiesel development from rice bran oil: Transesterification process optimization and fuel characterization. Energ Convers Manage 49: 1248–1257. doi: 10.1016/j.enconman.2007.08.010
![]() |
[58] | Ouanji F, Kacimi M, Ziyad M, et al. (2016) Production of biodiesel at small-scale (10 L) for local power generation. Int J Hydrogen Energ 42: 8914–8921. |
[59] | Ojolo SJ OBS, Adelaja AO, Ogbonnaya M (2011) Study of an effective technique for the production of biodeseal. JETEAS 2: 79–86. |
[60] |
Keera ST, El Sabagh SM, Taman AR (2011) Transesterification of vegetable oil to biodiesel fuel using alkaline catalyst. Fuel 90: 42–47. doi: 10.1016/j.fuel.2010.07.046
![]() |
[61] |
Uzun BB, Kılıç M, Özbay N, et al. (2012) Biodiesel production from waste frying oils: Optimization of reaction parameters and determination of fuel properties. Energy 44: 347–351. doi: 10.1016/j.energy.2012.06.024
![]() |
[62] |
Chung K-H, Kim J, Lee K-Y (2009) Biodiesel production by transesterification of duck tallow with methanol on alkali catalysts. Biomass Bioenerg 33: 155–158. doi: 10.1016/j.biombioe.2008.04.014
![]() |
[63] |
Chen KS, Lin YC, Hsu KH, et al. (2012) Improving biodiesel yields from waste cooking oil by using sodium methoxide and a microwave heating system. Energy 38: 151–156. doi: 10.1016/j.energy.2011.12.020
![]() |
[64] |
Brito JQA, Silva CS, Almeida JS, et al. (2012) Ultrasound-assisted synthesis of ethyl esters from soybean oil via homogeneous catalysis. Fuel Process Technol 95: 33–36. doi: 10.1016/j.fuproc.2011.11.007
![]() |
[65] |
Karavalakis G, Anastopoulos G, Stournas S (2011) Tetramethylguanidine as an efficient catalyst for transesterification of waste frying oils. Appl Energy 88: 3645–3650. doi: 10.1016/j.apenergy.2011.03.050
![]() |
[66] | Jagadale SSJLM (2012) Review of various reaction parameters and other factors affecting on production of chicken fat based biodiesel. IJMER 2: 407–411. |
[67] |
Baskar G, Aiswarya R (2016) Trends in catalytic production of biodiesel from various feedstocks. Renew Sust Energ Rev 57: 496–504. doi: 10.1016/j.rser.2015.12.101
![]() |
[68] |
Dell'Anna MM, Capodiferro VF, Mali M, et al. (2016) Esterification, transesterification and hydrogenation reactions of polyunsaturated compounds catalyzed by a recyclable polymer supported palladium catalyst. J Organomet Chem 818: 106–114. doi: 10.1016/j.jorganchem.2016.06.001
![]() |
[69] |
Borges ME, Díaz L (2012) Recent developments on heterogeneous catalysts for biodiesel production by oil esterification and transesterification reactions: A review. Renew Sust Energ Rev 16: 2839–2849. doi: 10.1016/j.rser.2012.01.071
![]() |
[70] |
Bournay L, Casanave D, Delfort B, et al. (2005) New heterogeneous process for biodiesel production: A way to improve the quality and the value of the crude glycerin produced by biodiesel plants. Catal Today 106: 190–192. doi: 10.1016/j.cattod.2005.07.181
![]() |
[71] |
Furuta S, Matsuhashi H, Arata K (2006) Biodiesel fuel production with solid amorphous-zirconia catalysis in fixed bed reactor. Biomass Bioenerg 30: 870–873. doi: 10.1016/j.biombioe.2005.10.010
![]() |
[72] |
Zhu H, Wu Z, Chen Y, et al. (2006) Preparation of Biodiesel Catalyzed by Solid Super Base of Calcium Oxide and Its Refining Process. Chinese J Catal 27: 391–396. doi: 10.1016/S1872-2067(06)60024-7
![]() |
[73] |
Sánchez M, Avhad MR, Marchetti JM, et al. (2016) Enhancement of the jojobyl alcohols and biodiesel production using a renewable catalyst in a pressurized reactor. Energ Convers Manage 126: 1047–1053. doi: 10.1016/j.enconman.2016.08.047
![]() |
[74] |
Avhad MR, Sánchez M, Bouaid A, et al. (2016) Modeling chemical kinetics of avocado oil ethanolysis catalyzed by solid glycerol-enriched calcium oxide. Energ Convers Manage 126: 1168–1177. doi: 10.1016/j.enconman.2016.07.060
![]() |
[75] |
Melero JA, Iglesias J, Morales G (2009) Heterogeneous acid catalysts for biodiesel production: current status and future challenges. Green Chem 11: 1285–1308. doi: 10.1039/b902086a
![]() |
[76] |
Peng BX, Shu Q, Wang JF, et al. (2008) Biodiesel production from waste oil feedstocks by solid acid catalysis. Process Saf Environ 86: 441–447. doi: 10.1016/j.psep.2008.05.003
![]() |
[77] |
Melero JA, Bautista LF, Morales G, et al. (2009) Biodiesel production with heterogeneous sulfonic acid-functionalized mesostructured catalysts. Energ Fuel 23: 539–547. doi: 10.1021/ef8005756
![]() |
[78] |
Devanesan M, Viruthagiri T, Sugumar N (2007) Transesterification of Jatropha oil using immobilized Pseudomonas fluorescens. Afr J Biotechnol 6: 2497–2501. doi: 10.5897/AJB2007.000-2396
![]() |
[79] |
Bajaj A, Lohan P, Jha PN, et al. (2010) Biodiesel production through lipase catalyzed transesterification: an overview. J Mol Catal B Enzym 62: 9–14. doi: 10.1016/j.molcatb.2009.09.018
![]() |
[80] |
Ban K, Kaieda M, Matsumoto T, et al. (2001) Whole cell biocatalyst for biodiesel fuel production utilizing Rhizopus oryzae cells immobilized within biomass support particles. Biochem Eng J 8: 39–43. doi: 10.1016/S1369-703X(00)00133-9
![]() |
[81] | Guang Jin TJB (2010) Whole-cell biocatalysts for producing biodiesel from waste greases. Illinois State University Normal, Illinois. |
[82] | Meryam Sardar RA (2015) Enzyme Immobilization: an overview on nanoparticles as immobilization matrix. Anal Biochem 4: 178. |
[83] |
Ansari SA, Husain Q (2012) Potential applications of enzymes immobilized on/in nano materials: A review. Biotechnol Adv 30: 512–523. doi: 10.1016/j.biotechadv.2011.09.005
![]() |
[84] |
Du W, Xu Y, Liu D, et al. (2004) Comparative study on lipase-catalyzed transformation of soybean oil for biodiesel production with different acyl acceptors. J Mol Catal B Enzym 30: 125–129. doi: 10.1016/j.molcatb.2004.04.004
![]() |
[85] |
Yomi Watanabea YS, Akio Sugiharaa, Hideo Nodab, Hideki Fukudac, and Yoshio Tominagaa (2000) Continuous Production of Biodiesel Fuel from Vegetable Oil Using Immobilized Candida antarctica Lipase. J Am Oil Chem Soc 77: 355–360. doi: 10.1007/s11746-000-0058-9
![]() |
[86] |
Li L, Du W, Liu D, et al. (2006) Lipase-catalyzed transesterification of rapeseed oils for biodiesel production with a novel organic solvent as the reaction medium. J Mol Catal B Enzym 43: 58–62. doi: 10.1016/j.molcatb.2006.06.012
![]() |
[87] |
Shah S, Sharma S, Gupta MN (2004) Biodiesel Preparation by Lipase-Catalyzed Transesterification of Jatropha Oil. Energ Fuel 18: 154–159. doi: 10.1021/ef030075z
![]() |
[88] |
Ha SH, Lan MN, Lee SH, et al. (2007) Lipase-catalyzed biodiesel production from soybean oil in ionic liquids. Enzyme Microb Tech 41: 480–483. doi: 10.1016/j.enzmictec.2007.03.017
![]() |
[89] |
Du W, Xu YY, Liu DH, et al. (2005) Study on acyl migration in immobilized lipozyme TL-catalyzed transesterification of soybean oil for biodiesel production. J Mol Catal B Enzym 37: 68–71. doi: 10.1016/j.molcatb.2005.09.008
![]() |
[90] |
Shah S, Gupta MN (2007) Lipase catalyzed preparation of biodiesel from Jatropha oil in a solvent free system. Process Biochem 42: 409–414. doi: 10.1016/j.procbio.2006.09.024
![]() |
[91] |
Sharma N, Ojha H, Bharadwaj A, et al. (2015) Preparation and catalytic applications of nanomaterials: a review. RSC Adv 5: 53381–53403. doi: 10.1039/C5RA06778B
![]() |
[92] |
Wen L, Wang Y, Lu D, et al. (2010) Preparation of KF/CaO nanocatalyst and its application in biodiesel production from Chinese tallow seed oil. Fuel 89: 2267–2271. doi: 10.1016/j.fuel.2010.01.028
![]() |
[93] |
Chaturvedi S, Dave PN, Shah NK (2012) Applications of nano-catalyst in new era. J Saudi Chem Soc 16: 307–325. doi: 10.1016/j.jscs.2011.01.015
![]() |
[94] | Sidra HSG, Tariq Mahmood3, Umar Nawaz, et al. (2016) Biodiesel Production by using CaO-Al2O3 Nano Catalyst. Int J Eng Res Sci 2: 2395–6992. |
[95] | Sivakumar P, Sankaranarayanan S, Renganathan S, et al. (2013) Studies on sono-chemical biodiesel production using smoke deposited nano mgo catalyst. Bull Chem React Eng Cataly 8: 89–96. |
[96] | Mookan RSM, Senthilkumar HV, Ravichandran B, et al. (2014) Transesterification of castor oil using nano-sized iron catalyst for the production of biodiesel. J Chem Pharm Sci 2: 108–112. |
[97] | Mookan RKA, Sundaresan M, Velan P (2014) Biodiesel production from pongamia pinnata oil using synthesized iron nanocatalyst. Int J ChemTech Res 6: 4511–4516. |
[98] | Gupta J, Agarwal M (2016) Preparation and characterizaton of CaO nanoparticle for biodiesel production. 2nd International Conference on Emerging Technologies. Jaipur, 302017, India: American Institute of Physics. |
[99] |
Hu S, Guan Y, Wang Y, et al. (2011) Nano-magnetic catalyst KF/CaO–Fe3O4 for biodiesel production. Appl Energ 88: 2685–2690. doi: 10.1016/j.apenergy.2011.02.012
![]() |
[100] |
Tahvildari K, Anaraki YN, Fazaeli R, et al. (2015) The study of CaO and MgO heterogenic nano-catalyst coupling on transesterification reaction efficacy in the production of biodiesel from recycled cooking oil. J Environ Health Sci Eng 13: 73–81. doi: 10.1186/s40201-015-0226-7
![]() |
[101] | Earle MJ, Plechkova NV, Seddon KR (2009) Green synthesis of biodiesel using ionic liquids. Pure Appl Chem 81: 2045–2057. |
[102] |
Gamba M, Lapis AA, Dupont J (2008) Supported ionic liquid enzymatic catalysis for the production of biodiesel. Adv Synth Catal 350: 160–164. doi: 10.1002/adsc.200700303
![]() |
[103] |
Ren Q, Zuo T, Pan J, et al. (2014) Preparation of biodiesel from soybean catalyzed by basic ionic liquids [Hnmm]OH. Materials 7: 8012–8023. doi: 10.3390/ma7128012
![]() |
[104] |
Dupont J, Suarez PA, Meneghetti MR, et al. (2009) Catalytic production of biodiesel and diesel-like hydrocarbons from triglycerides. Energ Environ Sci 2: 1258–1265. doi: 10.1039/b910806h
![]() |
[105] | Andreani L, Rocha JD (2012) Use of ionic liquids in biodiesel production: a review. Braz J Chem Eng 29: 1–13. |
[106] | Guo W, Leng Y, Ji G, et al. (2014) Ionic liquids-catalyzed transesterification of soybean oil under ultrasound irradiation. International Conference on Materials for Renewable Energy and Environment. IEEE, 295–297. |
[107] |
Wu Q, Chen H, Han M, et al. (2007) Transesterification of cottonseed oil catalyzed by brønsted acidic ionic liquids. Ind Eng Chem Res 46: 7955–7960. doi: 10.1021/ie070678o
![]() |
[108] |
Fan P, Xing S, Wang J, et al. (2017) Sulfonated imidazolium ionic liquid-catalyzed transesterification for biodiesel synthesis. Fuel 188: 483–488. doi: 10.1016/j.fuel.2016.10.068
![]() |
[109] |
Marchetti J, Errazu A (2008) Technoeconomic study of supercritical biodiesel production plant. Energ Convers Manage 49: 2160–2164. doi: 10.1016/j.enconman.2008.02.002
![]() |
[110] |
van Kasteren JMN, Nisworo AP (2007) A process model to estimate the cost of industrial scale biodiesel production from waste cooking oil by supercritical transesterification. Resour Conserv Recy 50: 442–458. doi: 10.1016/j.resconrec.2006.07.005
![]() |
[111] |
Atabani AE, Silitonga AS, Badruddin IA, et al. (2012) A comprehensive review on biodiesel as an alternative energy resource and its characteristics. Renew Sust Energ Rev 16: 2070–2093. doi: 10.1016/j.rser.2012.01.003
![]() |
[112] |
Kiss FE, Micic RD, Tomić MD, et al. (2014) Supercritical transesterification: Impact of different types of alcohol on biodiesel yield and LCA results. J Supercrit Fluid 86: 23–32. doi: 10.1016/j.supflu.2013.11.015
![]() |
[113] |
Kusdiana D, Saka S (2001) Kinetics of transesterification in rapeseed oil to biodiesel fuel as treated in supercritical methanol. Fuel 80: 693–698. doi: 10.1016/S0016-2361(00)00140-X
![]() |
[114] |
Bunyakiat K, Makmee S, Sawangkeaw R, et al. (2006) Continuous Production of Biodiesel via Transesterification from Vegetable Oils in Supercritical Methanol. Energ Fuel 20: 812–817. doi: 10.1021/ef050329b
![]() |
[115] |
Micic RD, Tomić MD, Kiss FE, et al. (2014) Influence of reaction conditions and type of alcohol on biodiesel yields and process economics of supercritical transesterification. Energ Convers Manage 86: 717–726. doi: 10.1016/j.enconman.2014.06.052
![]() |
[116] |
Hawash S, Kamal N, Zaher F, et al. (2009) Biodiesel fuel from Jatropha oil via non-catalytic supercritical methanol transesterification. Fuel 88: 579–582. doi: 10.1016/j.fuel.2008.09.007
![]() |
[117] |
Demirbas A (2007) Biodiesel from sunflower oil in supercritical methanol with calcium oxide. Energ Convers Manage 48: 937–941. doi: 10.1016/j.enconman.2006.08.004
![]() |
[118] |
Song ES, Lim JW, Lee HS, et al. (2008) Transesterification of RBD palm oil using supercritical methanol. J Supercrit Fluid 44: 356–363. doi: 10.1016/j.supflu.2007.09.010
![]() |
[119] |
Santana A, Maçaira J, Larrayoz MA (2012) Continuous production of biodiesel using supercritical fluids: A comparative study between methanol and ethanol. Fuel Process Technol 102: 110–115. doi: 10.1016/j.fuproc.2012.04.014
![]() |
[120] |
Lam MK, Lee KT, Mohamed AR (2010) Homogeneous, heterogeneous and enzymatic catalysis for transesterification of high free fatty acid oil (waste cooking oil) to biodiesel: A review. Biotechnol Adv 28: 500–518. doi: 10.1016/j.biotechadv.2010.03.002
![]() |
1. | Carlos Ballester, Camilla Vote, John Hornbuckle, Thavone Inthavong, Vanndy Lim, Chantha Oeurng, Wendy Quayle, Vang Seng, Pheng Sengxua, Vorachith Sihathep, Veasna Touch, Philip Eberbach, Effects of Frequency of Irrigation on Dry-Season Furrow-Irrigated Maize and Peanut Production in the Rice-Growing Lowlands of the Lower Mekong Basin, 2019, 9, 2077-0472, 128, 10.3390/agriculture9060128 | |
2. | Hao Yuan Chan, Sarina Abdul Halim-Lim, Tai Boon Tan, Nitty Hirawaty Kamarulzaman, Adi Ainurzaman Jamaludin, Wan Abd Al Qadr Imad Wan-Mohtar, Exploring the Drivers and the Interventions towards Sustainable Food Security in the Food Supply Chain, 2020, 12, 2071-1050, 7890, 10.3390/su12197890 | |
3. | Abha Mishra, Jan Willem Ketelaar, Norman Uphoff, Max Whitten, Food security and climate-smart agriculture in the lower Mekong basin of Southeast Asia: evaluating impacts of system of rice intensification with special reference to rainfed agriculture, 2021, 1473-5903, 1, 10.1080/14735903.2020.1866852 | |
4. | Thi Bui, Huu Tran, Hossein Azadi, Philippe Lebailly, Improving the Technical Efficiency of Sengcu Rice Producers through Better Financial Management and Sustainable Farming Practices in Mountainous Areas of Vietnam, 2018, 10, 2071-1050, 2279, 10.3390/su10072279 | |
5. | Muhammad Shahbaz Farooq, Hira Fatima, Obaid Ur Rehman, Muhammad Yousuf, Rabia Kalsoom, Sajid Fiaz, Muhammad Ramzan Khan, Muhammad Uzair, Shuhao Huo, Major challenges in widespread adaptation of aerobic rice system and potential opportunities for future sustainability, 2023, 159, 02546299, 231, 10.1016/j.sajb.2023.06.017 | |
6. | Yun-Ho Lee, Seong-Woo Cho, Tae-Young Hwang, On-Farm Assessment of the System of Rice Intensification (SRI) Under Rainfed Lowland Fields of Southern Cambodia, 2024, 36, 1225-8504, 63, 10.12719/KSIA.2024.36.1.63 |