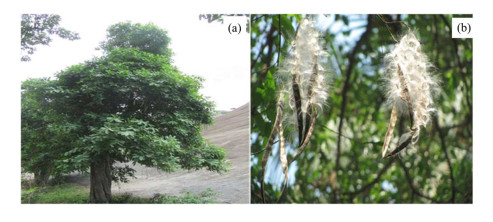
Characterization of new innovative natural seed fibers from seedpods or fruits of various plants has increased popularly in textile, automotive, and construction industries due to various aspects, availability, and biodegradability. In addition, these fibers provide sustainable solutions to support technological innovation in numerous industrial applications. The current research aims to investigate the new lignocellulose fibers extracted from Wrightia tinctoria seedpods. The obtained Wrightia tinctoria seed fibers (WTSFs) were characterized via Scanning electron microscope (SEM), Fourier Transform Infrared-ray (FTIR), X-ray diffraction (XRD), Thermogravimetric analysis (TGA), and Differential scanning calorimetry (DSC) to understand the fibers physicochemical properties. Complete experimental study of natural seed fibers of Wrightia tinctoria found to be a lignocellulose fiber and contains unique characteristics. Surface morphological studies reveal that, WTSFs contain smoother surface which is beneficial to develop a good bond with matrix while making composites. It does not get wet quickly with water due to fatty, wax, mineral matters, and higher lignin content on the fiber surface which means the fiber is soft compared with other natural seed fibers. These unique properties of WTSFs ascertain as a suitable material for polymer fabrication process, which would be favourable to develop good bonding with the matrix for making composites and also useful for insulating composite materials.
Citation: SYED HABIBUNNISA, Ruben Nerella, Srirama Chand Madduru, RajaGopal Reddy S. Physicochemical characterization of lignocellulose fibers obtained from seedpods of Wrightia tinctoria plant[J]. AIMS Materials Science, 2022, 9(1): 135-149. doi: 10.3934/matersci.2022009
[1] | Wisawat Keaswejjareansuk, Xiang Wang, Richard D. Sisson, Jianyu Liang . Electrospinning process control for fiber-structured poly(Bisphenol A-co-Epichlorohydrin) membrane. AIMS Materials Science, 2020, 7(2): 130-143. doi: 10.3934/matersci.2020.2.130 |
[2] | Nursiah Chairunnisa, Ninis Hadi Haryanti, Ratni Nurwidayati, Ade Yuniati Pratiwi, Yudhi Arnandha, Tetti N Manik, Suryajaya, Yoga Saputra, Nur Hazizah . Characteristics of metakaolin-based geopolymers using bemban fiber additives. AIMS Materials Science, 2024, 11(4): 815-832. doi: 10.3934/matersci.2024040 |
[3] | Iketut Suarsana, Igpagus Suryawan, NPG Suardana, Suprapta Winaya, Rudy Soenoko, Budiarsa Suyasa, Wijaya Sunu, Made Rasta . Flexural strength of hybrid composite resin epoxy reinforced stinging nettle fiber with silane chemical treatment. AIMS Materials Science, 2021, 8(2): 185-199. doi: 10.3934/matersci.2021013 |
[4] | Kator Jeff Jomboh, Adele Dzikwi Garkida, Emmanuel Majiyebo Alemaka, Mohammed Kabir Yakubu, Vershima Cephas Alkali, Wilson Uzochukwu Eze, Nuhu Lawal . Properties and applications of natural, synthetic and hybrid fiber reinforced polymer composite: A review. AIMS Materials Science, 2024, 11(4): 774-801. doi: 10.3934/matersci.2024038 |
[5] | Ninis Hadi Haryanti, Suryajaya, Tetti Novalina Manik, Khaipanurani, Adik Bahanawan, Setiawan Khoirul Himmi . Characteristics of water chestnut (Eleocharis dulcis) long fiber reinforced composite modified by NaOH and hot water. AIMS Materials Science, 2024, 11(6): 1199-1219. doi: 10.3934/matersci.2024059 |
[6] | Hendra Suherman, Yovial Mahyoedin, Afdal Zaky, Jarot Raharjo, Talitha Amalia Suherman, Irmayani Irmayani . Investigation of the mechanical properties of bio-composites based on loading kenaf fiber and molding process parameters. AIMS Materials Science, 2024, 11(6): 1165-1178. doi: 10.3934/matersci.2024057 |
[7] | Kiyotaka Obunai, Daisuke Mikami, Tadao Fukuta, Koichi Ozaki . Microstructure and mechanical properties of newly developed SiC-C/C composites under atmospheric conditions. AIMS Materials Science, 2018, 5(3): 494-507. doi: 10.3934/matersci.2018.3.494 |
[8] | Falko Böttger-Hiller, Klaus Nestler, Henning Zeidler, Gunther Glowa, Thomas Lampke . Plasma electrolytic polishing of metalized carbon fibers. AIMS Materials Science, 2016, 3(1): 260-269. doi: 10.3934/matersci.2016.1.260 |
[9] | Mica Grujicic, S. Ramaswami, Jennifer S. Snipes . Use of the Materials Genome Initiative (MGI) approach in the design of improved-performance fiber-reinforced SiC/SiC ceramic-matrix composites (CMCs). AIMS Materials Science, 2016, 3(3): 989-1021. doi: 10.3934/matersci.2016.3.989 |
[10] | João Otávio Donizette Malafatti, Thamara Machado de Oliveira Ruellas, Camila Rodrigues Sciena, Elaine Cristina Paris . PLA/starch biodegradable fibers obtained by the electrospinning method for micronutrient mineral release. AIMS Materials Science, 2023, 10(2): 200-212. doi: 10.3934/matersci.2023011 |
Characterization of new innovative natural seed fibers from seedpods or fruits of various plants has increased popularly in textile, automotive, and construction industries due to various aspects, availability, and biodegradability. In addition, these fibers provide sustainable solutions to support technological innovation in numerous industrial applications. The current research aims to investigate the new lignocellulose fibers extracted from Wrightia tinctoria seedpods. The obtained Wrightia tinctoria seed fibers (WTSFs) were characterized via Scanning electron microscope (SEM), Fourier Transform Infrared-ray (FTIR), X-ray diffraction (XRD), Thermogravimetric analysis (TGA), and Differential scanning calorimetry (DSC) to understand the fibers physicochemical properties. Complete experimental study of natural seed fibers of Wrightia tinctoria found to be a lignocellulose fiber and contains unique characteristics. Surface morphological studies reveal that, WTSFs contain smoother surface which is beneficial to develop a good bond with matrix while making composites. It does not get wet quickly with water due to fatty, wax, mineral matters, and higher lignin content on the fiber surface which means the fiber is soft compared with other natural seed fibers. These unique properties of WTSFs ascertain as a suitable material for polymer fabrication process, which would be favourable to develop good bonding with the matrix for making composites and also useful for insulating composite materials.
Environmental pollution issues have motivated towards extensive investigation on sustainable alternatives to replace materials that mobilize enormous financial resources and acquire high energy costs [1]. Fibers extracted from plants and animals play an essential part in our lifestyle, not only in sustainable attire but also in other textile fields [1,2]. Natural fibers gained significant attention in construction filed for their inherent characteristics viz: low cost, easy availability, good mechanical properties, biodegradable, renewability, and non-abrasive nature [2]. Added to this, natural fibers can accommodate numerous benefits over manmade fibers such as good acoustic property, thermal insulation, low density, low cost and high flexural strength. Owing to this aspect, these natural fibers are tremendously recommended for various building material applications [3]. Native cellulose fibers have successfully shown their qualities while considering them as eco-friendly fiber materials [2,4]. The design of environmentally safe materials developed from natural resources represented a significant challenge in previous decades. However, interest to use fibers from plant origin increased latterly for sustainable construction practices [4]. Natural fibres are composed of cellulose, hemicellulose, lignin, pectins, waxes and water soluble substances [3,5]. The chemical composition and physical characteristics are altered with climatic conditions, age and retting process [3].
Lignocellulose or vegetable fibers are extracts from plants, especially seeds, stems, leaves, and fruits. These include hairs such as kapok and cotton, fiber sheaves, or vessel-sheaves extracted from the dactylic plant and monocyclic plants, respectively (example: hemp, flax, jute, and ramie) [6]. Majority of studies recommended usage of lignocellulose fibers in composites as reinforcement that associates high mechanical performance with less ecological impact [7]. There is an increase in demands from automobiles, textiles, and construction industries for materials with good insulation capacity and thus reduces energy costs for fuel efficiencies [8]. Therefore, natural fibers are eco-friendly materials to replace synthetic fibers [9]. Due to broad accessibility, especially in tropical countries, natural fibers regenerate with less amount and require about 20–40% of the total production energy than synthetic fiber [10]. Natural fiber composites encourage environmental benefits viz: eventual disposal ability, raw fiber material utilization, and represent a possible route to obtain new CO2 fewer materials [11]. Recently, the awareness to develop green composite from biodegradable material has raised in the public [12]. Utilization of bio-composite mitigates the release of carbon footprint and greenhouse gas emissions to the environment, through the reduced release on fossil fuel resource [12]. Scientists and researchers focused on the production of bio-based materials from agriculture waste due mitigation of climate change problems. These are plentiful, renewable, sustainable, and the presence of cellulose compounds can acts as a replacement source for manufactured cellulose derivative products. As well as, it uses as a reinforcing agent in composite materials application. The usage of biomass was considered as an effective approach that contributes the establishment of a sustainable and cleaner environment [13]. New developments in composite materials can mitigate the challenges in aerospace sectors has cascade over to cater less demand in domestic and industrial applications. Different natural fibers offer several advantages over synthetic fibers due to its bio-renewable and environmental-friendly nature. Industries are widely using natural fibres for numerous applications from many resources [14]. Because most of the natural fibers are lignocellulose, these are consider as low-value industrial fibers [15]. These type of renewable natural fibers are considered as cost-effective reinforcing materials [16].
Conventional lignocellulose fibers like coir, sisal, hemp, ramie, jute, etc., have been studied and well reported previously [17,18]. The present scenario demands utilization of easily available more natural plant fiber and their wastes with proper treatment as reinforcements in polymer composites [19]. Still, some vegetable fibers/lignocellulose fibers remain unutilized and these are gone as natural wastes [20]. One of such hitherto uninvestigated lignocellulose fibers are Wrightia tinctoria seed fibers (WTSFs) obtained from Wrightia tinctoria plant [20,21]. A potential seed fiber that has not been extensively explored. There are a limited number of studies reported on WTSFs. Hence, this seed fiber chooses to tap out of its physical, chemical, and thermal properties in the current study to exploit potential textile applications, industry sector, and as insulation material.
Wrightia tinctoria (Roxb.) R. Br. is belonging to the Apocynaceae family and is known as "Indrajau". It is distributed throughout the world and is extensively available in India. It is a small deciduous tree grows from 4–14 m with a light grey, smooth scaly bar [21]. It is native to India and Burma, generally found in Southeast Asia, and Australia, located in moist deciduous forests. It is a naturally grown drought and pest resistant tree of Indian origin and is well known for its medicinal values [22]. It was named by the scottish physician and botanist William Wright (1740–1827). Wrightiatinctoria commonly known as Ankuduchettu, Chittiankudu, Veppalai, Dudhi, Vettupala, Ivory wood, and Sweet indrajau. The seedpods contain floss or fibers, which uses for stuffing cushions. Based on the above literature, the current research deals with the extraction of new natural WTSFs to understand the physicochemical, thermal properties, and characterization process. The overview of Wrightia tinctoria plant and seedpods are appear in Figure 1.
Wrightia tinctoria material is collected from Guvvala cheruvu village, Seshachalam biosphere reserve forest area near kadapa to Rayachoti way, Southern part of India. Guvvalacheruvu village is located in Ramapuram Tehsil of YSR district in Andhra Pradesh, India. It is situated 10 km away from sub-district headquarter Ramapuram and 25 km away from district headquarter Kadapa. As per 2009 stats, Guvvalacheruvu village is also a gram panchayat.
The total geographical area of village is 351 hm2. Guvvalacheruvu has a total population of 1795 peoples. There are about 379 h in Guvvalacheruvu village. Kadapa is nearest town to Guvvalacheruvu which is approximately 25 km away, as shown in Figure 2.
Wrightia tinctoria seedpods are collected from Guvvalacheruvu reserve forest, Kadapa district, Andhra Pradesh, India. The herbarium specimen was deposited near at Yogi Vemana University, Kadapa, Andhra Pradesh. These are allowed to decay by exposing it to sunlight until the seedpods break and open or break the seedpods manually by applying an external force, thereby exposing the seed fibers. These WTSFs are used as raw material in the characterization process obtained from the fully matured fruit or seedpods assortment. The seed gets separated from the seedpods through the plugging process. Seed is linear, pointed at ends as 1.2–1.8 cm long and in light yellowish-grey colour crowned with a tuft of white silky hairs, which separates from the seeds. Proper care was taken such that the fibers were collected in air-tight polyethylene bags immediately before they dispersed in the air. Later stored fibers are utilized to carry out physical, chemical, and thermal analysis to identify their properties. The plant's dry fiber or floss yield is approximately in and around 1–3 kg/year. Figure 3 shows the extraction process of WTSFs. WTSF based composite products can be used in industrial sectors for low-density lightweight and nonwoven medical applications, technical applications, textile production after the delignification process [21,22].
Extracted fibers were chopped into small pieces with the help scissor and ground into powder form by using mortar and pestle as shown in Figure 4. After the grounded powder was stored to conduct tests such as XRD and FTIR analysis on it. Around 2–6 mg powder was used for each analysis. The fibers characterization process includes as follows.
Length: The fiber length analysis using advanced instruments was not possible due to its brittle nature. Hence, fiber length is calculated manually using a calibrated steel scale [22].
Diameter: The fiber diameter can be measured using Scanning Electron Microscopy (SEM). The dimension was found to be in the particular range of 100–50 μm with mean values.
Density: WTSFs apparent density (±0.4%) at 25.0 ±0.4 ℃ is determined by a pycnometer bottle of 25 mL capacity, where xylene was taken as the immersion liquid. This Specific gravity bottle also determines the density of xylene at 25 ℃ (±0.2 ℃) as 0.86 g/mL.
Specific Gravity: WTSFs fibers are chopped into small pieces and ground into powder form by mortar pestle. Specific gravity test was conducted on Wrightia tinctoria seed fiber powder [23].
Moisture Content: The average moisture content of WTSFs was determined by weighing the sample before and after drying for 24 h at 105 ℃ by using following Eq 1 [24]:
(1) |
Where WO is original weight of sample, and WD is dried weight of sample.
Surface Morphology: WTSFs Surfaces visualized by SEM of Vega-3, Tescan with an accelerated voltage of 30 kV and, an accessible vacuum level of 1.5 × 10−3 Pa [13].
It is a primary method to examine the sample crystallinity from diffraction peaks of cellulose crystals. Although all materials give X-ray scatters and represent the amorphous parts of the sample [20]. It measures the presence of cellulose, hemicelluloses, and lignin content with certain diffractograms. These are similar to amorphous cellulose, which raises a broad, unspecific peak. In that, amorphous scatters show as a softly rising and decreasing background [21]. The type of cellulose that exists in all plants is cellulose Iβ, which is monoclinic. Crystallinity Index (CI) is estimated by following Eq 2 [22]:
(2) |
Where H24.47 height of the peak at 2θ = 24.47, it assigns by crystalline fractions. H18.39 is the diffracted intensity at 2θ = 18.39 and it assigns to amorphous fractions. The Crystallite Size (CS) of WTSFs is finalize by following Eq 3 [25]. Here, K = 0.89 (Scherrer's constant), β is full-width at half-maximum, and the λ is X-ray wavelength.
(3) |
This analysis performs on WTSFs to study the structural and chemical information of fiber materials. The FTIR spectrum represents the well-defined peaks for origin attribution to a particular intensity range [26]. WTSFs samples were chopped into small fiber particles by using scissors. Later it was grounded into fine powder form, with the help of mortar and pestle. A sample of around 2 g will be considered for the analysis [27]. The FTIR spectra record intensity with wave numbers ranges from 400 to 4000 cm−1 resolution with an average of 45 scans. Each spectrum contains a regime in transmittance modes as a function of wave numbers [27].
Most of the natural fibers are less thermal and therefore the WTSFs were analysed to find out the thermal stability nature. The degraded temperature of lignocellulose fibers depends on their molecular weight, polymer morphology, and crystalline nature [28]. There are mainly two types of techniques used for the analysis, which are as follows. One is Differential scanning calorimetry. It is a thermo analytical method that represents, differences in the amount of heat required to increase the temperature of a sample and reference is measured as a function of temperature [28]. The other is Thermogravimetric analysis. This type of analysis examines the mass changes as a function of temperature (in scanning mode) or as a function of time (in an isothermal way). It measures the changes in physical and chemical properties of materials, as a function of time with constant temperature and mass loss [29].
The WTSFs is a light yellow-grey brittle, light white filamentous fibre that is neither soluble in water nor in NaOH. Raw fiber length with an accuracy of ±3.0% was measured manually by taking average values of 30 samples. Usage of advanced instruments makes it impossible to get correct fiber lengths due to breaking problems while feeding this brittle raw fiber into this equipment. A scale ruler was used to measure the length of fibers, as shown in Figure 5. The staple lengths of WTSFs were measured manually and the average of WTSF was measured as value is 5.32 cm. The short fiber percentage was high, and there are broader variations in fiber lengths.
An average of around 30 randomly chosen readings were taken to compute the mean fiber diameter with ±1.5% accuracies. The diameter of WTSFs observed by SEM as shown in Figure 6. The mean diameter of WTSFs is obtained as 20.58 μm under 50 μm magnification and 27.328 μm at 100 μm magnification.
The density of WTSFs is 800 kg/m3 which is less than Sansvieria Cylindrical (915 kg/m3), Sansevieria ehrenbergii (887 kg/m3), and Acacia arabica (1028 kg/m3). It is determined by a pycnometer bottle of 25 mL capacity, as shown in Figure 7. It is smaller than the density of native cellulose 1500–1800 kg/m3.
The average specific gravity of Wrightia tinctoria seed fiber powder is SWTSFP = 1.349 [24]. The average moisture content of WTSFs material was determined by weighing the sample before and after drying for 24 h at 105 ℃ obtained to be 7.69% [23].
WTSFs surfaces were visualized by SEM of Tescan Vega-3 with an accelerated voltage of 30 kV and attainable vacuum levels of 1.50 × 10−3 Pa. Fiber samples were coated with a thin gold layer, to avoid accumulations of electrical charges while observing the readings. The SEM examination depicted those fibers contain a hollow structure and a large lumen with a thin fiber wall which is filled with air [29], as shown in Figure 8. WTSFs are single-celled seed fibers like kapok, poplar, balsa, and cotton different than other natural fibers like wool, hemp, jute, etc [30].
This is a structural analysis technique, based on the diffractions of X-ray samples. XRD analysis allows to determine the micro and polycrystalline phases of materials. The spectrum contains two prominent peaks, the first Bragg peak height is observed at 2θ = 21.8°, it corresponds to crystallography phase of cellulose-I and the second is one observed at 2θ = 14.93°, it corresponds to the presence of amorphous fraction of cellulose IV; both peaks exhibit monoclinic structures. Although, FTIR analysis shows a characteristics band for cellulose Iβ. These results indicate the type of cellulose present in fibers i.e., cellulose Iβ with a crystalline index of 68.82 %, which offers a high value among all fibers [18,31]. These peaks are more evident one to identify the presence of amorphous materials. Fiber encloses with huge amorphous cellulose and contains lignin, hemicelluloses, pectin [31]. Crystalline size was estimated as 2.55 nm, which is lesser than Perotis indica (15 nm), Furcraea foetida (28.36 nm), and flax (2.8 nm) [26]. X-ray spectrum of WTSFs as shown in Figure 9.
This analysis performs on WTSFs, to study the organic and inorganic components present in materials. FTIR analysis of the WTSTs carries a Cary 630 FTIR with Diamond ATR, Agilent Technologies spectrometer (USA). The below Figure 10 illustrates the FTIR Spectrum of WTF, a total of 12 are peaks observed. The bands at 3400 cm−1 and 896.749 cm−1 attributed to cellulose [31]. Bands at 2920.52 cm−1 attributed to waxes present in WTSFs and 1740 cm−1 to 1590 cm−1 are attributes to lignin. The bands at 1735.525 cm−1 and 1233.345 cm−1 attributed to the C = O group of a stretch to hemicelluloses [31], as shown in Table 1. Furthermore band at 1594.516 cm−1 attributes to the lignin. The peaks at 1369.829 cm−1 proved the presence of alcohols and ester groups.
Wave number range (cm−1) |
Intensity | Origin | Origin Attribution |
3338.62 | Broad and very strong | Hydrogen bond O‑H group | Intra and intermolecular hydroxyl (‑OH) bond of cellulose |
2920.52 | Medium | Stretching in ‑CH2− | Methylene groups, wax |
1735.525 | Medium | C = O Stretching | Esters and amide |
1420.694 | Weak | CO Stretching | Aromatic groups |
1369.82 | Medium | Stretching in CH2 and CH | In-plane bending vibrations of CH2 and CH groups of cellulose |
1319.78 | Weak | – | Alcohols, carboxylic groups, esters |
1233.345 | Sharp and medium | CO group Stretching | Hemicelluloses |
896.749 | Medium | Attributed to CH deformation |
Amorphous region of cellulose |
Thermal studies analyzed by TGA and DSC identified higher heat resistance of WTSFs, as most of the natural fibers are less resistance to heat. The thermal behaviour of WTSFs is studied through DSC and TGA curves as shown in Figures 11 and 12.
The DSC thermograms of conditioned (25 ℃) raw fiber samples are recorded using equipment (EXSTAR DSC7020, Hitachi HTG, Japan). The instrument maintains a special heating rate of 10 ℃/min from room temperature to 250 ℃ in a nitrogen atmosphere. Sample used for this analysis was around 2 mg. DSC shows a broad endothermic peak (78 ℃) that extended up to 126 ℃. However, it degrades exothermically beyond 150 ℃. A small endothermic peak is observed at 285 ℃ in raw fiber; it is more credible and attributes to melting and volatilization of fatty and wax substances which are available in fibers [20,21]. DSC spectra of WTSFs can be seen in Figure 11. The fiber degrades upto 350 ℃ and finally it undergoes charrel nature. In the final analysis serial endothermic and exothermic absorption bands after 400 ℃ temperature represents the liquefaction and gasification takes place at the end of fiber decomposition process [32].
Thermograms of WTSFs samples are recorded at 25 ℃ on thermal analyzer (STA 7200, Hitachi HTG, Japan). Thermal analysis was carried on WTSFs at a specific heating rate of 10 ℃/min from room temperature to 460 ℃, both in static air and nitrogen atmosphere. Sample used for this analysis was around 10–20 mg. Figure 12 shows the TGA spectra of WTSFs. The TG traces of the WTF shows two-step degradation up to 400 ℃. The mass loss occurs up to 100 ℃ due to evaporation of moisture content. Fiber sample shows a particular percentage of residue at 450 ℃ due to charring. The first step degradation occurs at 215 ℃. The mass loss observed in raw fiber is due to the appearance of fatty, wax, and other mineral matters [20,21].
The present study reveals the physicochemical, crystalline, thermal characteristics, and surface morphology of WTSFs. FTIR analysis demonstrate the presence of chemical groups in WTSFs. The predicted chemical nature of WTSFs was relatively closed to existed new lignocellulose fibers. To authenticate the presence of components in lignocellulose fiber, FTIR analysis was familiarized to identify the functional groups. The relatively large amount of cellulose (73.62%) shows the favourable properties to natural lignocellulose fibers. The crystallinity index value of WTSFs is 68.82%, and the crystalline size is 2.55 nm, this indicates the occurrence of a high amount of crystalline cellulose. The density of WTSFs was 800 kg/m3, relatively smaller than other lignocellulose fibers. The thermal analysis showed that WTSF had a hollow structure with thin fiber walls and large lumens, specifically capable to withstand high temperatures. Therefore, these fibers are helpful for potential development as absorbent and insulating materials without sacrificing ecological considerations. This research work proposes a chance to use WTSFs for various applications as a reinforcement while preparing composite materials. WTSF is the most stable thermal tolerance in among all other natural fibers to withstand extreme temperature. Therefore, this fiber is suggested as suitable material for the polymer fabrication process and also useful for insulating purpose.
Finally, this study advances the opportunity to employ the WTSFs for various applications, such as reinforcements in composite structures.
The authors are thankful to the "Centre of Excellence for Advanced Materials, Manufacturing, Processing and Characterization" of Vignan's Foundation for Science, Technology & Research (Deemed to be University) for permitting us to do SEM, XRD, DSC and TG/DTA analyses on materials and also thanking for providing financial support, lab facilities for this research work.
The authors are declaring that, there is no conflict on manuscript to submitting and publishing.
[1] |
Eltahir HA, Xu W, Lu X, et al. (2020) Prospect and potential of adansonia digitata L.(baobab) bast fiber in composite materials reinforced with natural fibers. Part 1: fiber characterization. J Nat Fibers 18: 2197-2207. https://doi.org/10.1080/15440478.2020.172423. doi: 10.1080/15440478.2020.172423
![]() |
[2] |
Gurukarthik BB, Prince WD, SenthamaraiKannan P, et al. (2019) Study on characterization and physicochemical properties of new natural fiber from Phaseolus vulgaris. J Nat Fibers 16: 1035-1042. https://doi.org/10.1080/15440478.2018.144831. doi: 10.1080/15440478.2018.144831
![]() |
[3] |
Asim M, Jawaid M, Abdan K, et al. (2016) Effect of alkali and silane treatments on mechanical and fibre-matrix bond strength of kenaf and pineapple leaf fibres. J Bionic Eng 13: 426-435. https://doi.org/10.1016/S1672-6529(16)60315-3 doi: 10.1016/S1672-6529(16)60315-3
![]() |
[4] |
Baskaran PG, Kathiresan M, Senthamaraikannan P, et al. (2018) Characterization of new natural cellulosic fiber from the bark of Dichrostachys Cinerea. J Nat Fibers 15: 62-68. https://doi.org/10.1080/15440478.2017.1304314 doi: 10.1080/15440478.2017.1304314
![]() |
[5] |
Sanjay MR, Arpitha GR, Naik LL, et al. (2016) Applications of natural fibers and its composites: An overview. Nat Resour 7: 108-114. http://dx.doi.org/10.4236/nr.2016.73011 doi: 10.4236/nr.2016.73011
![]() |
[6] |
Habert G, Roussel N (2009) Study of two concrete mix-design strategies to reach carbon mitigation objectives. Cement Concrete Comp 31: 397-402. https://doi.org/10.1016/j.cemconcomp.2009.04.001 doi: 10.1016/j.cemconcomp.2009.04.001
![]() |
[7] |
Hasan KMF, Horváth PG, Alpár T (2021) Lignocellulosic fiber cement compatibility: A state of the art review. J Nat Fibers 18: 1-26. https://doi.org/10.1080/15440478.2021.1875380 doi: 10.1080/15440478.2021.1875380
![]() |
[8] |
Pividal P, Rocha AM (2020) Thermal behavior of bi-layered needle-punched nonwovens produced from 100% raw kapok fibers. J Text Inst 112: 928-935. https://doi.org/10.1080/00405000.2020.1786209 doi: 10.1080/00405000.2020.1786209
![]() |
[9] |
Oduor EO, Ciera L, Adolkar V, et al. (2021) Physical characterization of eri silk fibers produced in Kenya. J Nat Fibers 18: 59-70. https://doi.org/10.1080/15440478.2019.1612306 doi: 10.1080/15440478.2019.1612306
![]() |
[10] |
Madhu P, Sanjay MR, Senthamaraikannan P, et al. (2019) A review on synthesis and characterization of commercially available natural fibers: Part II. J Nat Fibers 16: 25-36. https://doi.org/10.1080/15440478.2017.1379045 doi: 10.1080/15440478.2017.1379045
![]() |
[11] |
Fiore V, Di Bella G, Valenza A (2019) Effect of sheep wool fibers on thermal insulation and mechanical properties of cement-based composites. J Nat Fibers 17: 1532-1543. https://doi.org/10.1080/15440478.2019.1584075 doi: 10.1080/15440478.2019.1584075
![]() |
[12] |
Alothman OY, Kian LK, Saba N, et al. (2021) Cellulose nanocrystal extracted from date palm fibre: Morphological, structural and thermal properties. Ind Crops Prod 159: 113075. https://doi.org/10.1016/j.indcrop.2020.113075 doi: 10.1016/j.indcrop.2020.113075
![]() |
[13] |
Jawaid M, Kian LK, Fouad H, et al. (2021) Morphological, structural, and thermal analysis of three part of Conocarpus cellulosic fibres. J Mater Res Technol 10: 24-33. https://doi.org/10.1016/j.jmrt.2020.11.108 doi: 10.1016/j.jmrt.2020.11.108
![]() |
[14] |
Asim M, Abdan K, Jawaid M, et al. (2015) A review on pineapple leaves fibre and its composites. Int J Polym Sci 2015:1-16. http://dx.doi.org/10.1155/2015/950567 doi: 10.1155/2015/950567
![]() |
[15] |
Hamdaoui O, Limam O, Ibos L, et al. (2021) Thermal and mechanical properties of hardened cement paste reinforced with Posidonia-Oceanica natural fibers. Constr Build Mater 269: 121339. https://doi.org/10.1016/j.conbuildmat.2020.121339 doi: 10.1016/j.conbuildmat.2020.121339
![]() |
[16] |
Nadlene R, Sapuan SM, Jawaid M, et al. (2016) A review on roselle fiber and its composites. J Nat Fibers 13: 10-41. https://doi.org/10.1080/15440478.2014.984052 doi: 10.1080/15440478.2014.984052
![]() |
[17] |
Loganathan TM, Sultan MTH, Ahsan Q, et al. (2021) Comparative study of mechanical properties of chemically treated and untreated cyrtostachys renda fibers. J Nat Fibers 19: 1-16. https://doi.org/10.1080/15440478.2021.1902900 doi: 10.1080/15440478.2021.1902900
![]() |
[18] | Petroudy SRD (2017) Physical and mechanical properties of natural fiber, In: Fan Mizi, Feng Fu, Advanced High Strength Natural Fibre Composites in Construction, London: Woodhead Publishing, 59-83. https://doi.org/10.1016/B978-0-08-100411-1.00003-0 |
[19] |
Kumar R, Hynes NRJ, Senthamaraikannan P, et al. (2018) Physicochemical and thermal properties of ceiba pentandra bark fiber. J Nat Fibers 15: 822-829. https://doi.org/10.1080/15440478.2017.1369208 doi: 10.1080/15440478.2017.1369208
![]() |
[20] |
Subramanian K, Kumar PS, Jeyapal P, et al. (2005) Characterization of ligno-cellulosic seed fibre from Wrightia Tinctoria plant for textile applications-an exploratory investigation. Eur Polym J 41: 853-861. https://doi.org/10.1016/j.eurpolymj.2004.10.037 doi: 10.1016/j.eurpolymj.2004.10.037
![]() |
[21] |
Mothilal B, Prakash C, Ramakrishnan G (2019) Design and development of non-woven medical product from Wrightia tinctoria fiber. J Nat Fibers 16: 576-588. https://doi.org/10.1080/15440478.2018.1430649 doi: 10.1080/15440478.2018.1430649
![]() |
[22] | Grace Annapoorani S, Divya S (2017) Investigating the characterization of fiber extracted from Wrightia tinctoria (Roxb.) R. BR. Int J Appl Res 3: 731-736. |
[23] | Bureau of Indian Standards (1980) Methods of test for soils, Part 3: Determination of specific gravity, New Delhi: India Government. IS 2720-3-1 |
[24] | Bureau of Indian Standards (1973) Methods of test for soils-Part 2: Determination of water content, New Delhi: India Government. IS 2720-2 |
[25] | Segal L, Creely JJ, Martin Jr AE, et al. (1959) An empirical method for estimating the degree of crystallinity of native cellulose using the X-ray diffractometer. Text Res J 29: 786-794. https://doi.org/10.1177%2F004051755902901003 |
[26] |
Manimaran P, Senthamaraikannan P, Murugananthan K, et al.(2018) Physicochemical properties of new cellulosic fibers from Azadirachta indica plant. J Nat Fibers 15: 29-38. https://doi.org/10.1080/15440478.2017.1302388 doi: 10.1080/15440478.2017.1302388
![]() |
[27] |
Purnawati R, Febrianto F, Wistara I, et al. (2018) Physical and chemical properties of kapok (Ceiba Pentandra) and balsa (Ochroma Pyramidale) fibers. J Korean Wood Sci Technol 46: 393-401. https://doi.org/10.5658/WOOD.2018.46.4.393 doi: 10.5658/WOOD.2018.46.4.393
![]() |
[28] |
Sathishkumar TP, Navaneethakrishnan P, Shankar S, et al. (2013) Characterization of new cellulose sansevieria ehrenbergii fibers for polymer composites. Compos Interfac 20: 575-593. https://doi.org/10.1080/15685543.2013.816652 doi: 10.1080/15685543.2013.816652
![]() |
[29] |
Saravanakumar SS, Kumaravel A, Nagarajan T, et al. (2013) Characterization of a novel natural cellulosic fiber from Prosopis juliflora bark. Carbohydr Polym 92: 1928-1933. https://doi.org/10.1016/j.carbpol.2012.11.064 doi: 10.1016/j.carbpol.2012.11.064
![]() |
[30] |
Rashid B, Leman Z, Jawaid M, et al. (2016) Physicochemical and thermal properties of lignocellulosic fiber from sugar palm fibers: Effect of treatment. Cellulose 23: 2905-2916. https://doi.org/10.1007/s10570-016-1005-z doi: 10.1007/s10570-016-1005-z
![]() |
[31] |
Prithiviraj M, Muralikannan R, Senthamaraikannan P, et al. (2016) Characterization of new natural cellulosic fiber from the Perotis indica plant. Int J Polym Anal Ch 21: 669-674. https://doi.org/10.1080/1023666X.2016.1202466 doi: 10.1080/1023666X.2016.1202466
![]() |
[32] | Jawaid M, Kian LK, Fouad H, et al. (2021) New cellulosic fibers from Washingtonia tree agro-wastes: Structural, morphological, and thermal properties. 2021: 1-11. https://doi.org/10.1080/15440478.2021.1875374 |
1. | Habibunnisa Syed, Ruben Nerella, Sri Rama chand Madduru, Raja Gopal Reddy S, Utilization of wrightia tinctoria nano seed fibers as a reinforcement in the preparation of epoxy-based composites, 2022, 2300-5599, 5, 10.32933/ActaInnovations.45.1 | |
2. | L. Natrayan, Raviteja Surakasi, S. Kaliappan, G. Muthu, Prabhu Paramasivam, Kirubanandan Shanmugam, Effectiveness of natural dye adsorption on ILSS and optical properties of bio synthesised TiO2 nano particles and reinforced with flax seed fiber/epoxy based hybrid composites, 2024, 6, 3004-9261, 10.1007/s42452-024-05758-9 |
Wave number range (cm−1) |
Intensity | Origin | Origin Attribution |
3338.62 | Broad and very strong | Hydrogen bond O‑H group | Intra and intermolecular hydroxyl (‑OH) bond of cellulose |
2920.52 | Medium | Stretching in ‑CH2− | Methylene groups, wax |
1735.525 | Medium | C = O Stretching | Esters and amide |
1420.694 | Weak | CO Stretching | Aromatic groups |
1369.82 | Medium | Stretching in CH2 and CH | In-plane bending vibrations of CH2 and CH groups of cellulose |
1319.78 | Weak | – | Alcohols, carboxylic groups, esters |
1233.345 | Sharp and medium | CO group Stretching | Hemicelluloses |
896.749 | Medium | Attributed to CH deformation |
Amorphous region of cellulose |
Wave number range (cm−1) |
Intensity | Origin | Origin Attribution |
3338.62 | Broad and very strong | Hydrogen bond O‑H group | Intra and intermolecular hydroxyl (‑OH) bond of cellulose |
2920.52 | Medium | Stretching in ‑CH2− | Methylene groups, wax |
1735.525 | Medium | C = O Stretching | Esters and amide |
1420.694 | Weak | CO Stretching | Aromatic groups |
1369.82 | Medium | Stretching in CH2 and CH | In-plane bending vibrations of CH2 and CH groups of cellulose |
1319.78 | Weak | – | Alcohols, carboxylic groups, esters |
1233.345 | Sharp and medium | CO group Stretching | Hemicelluloses |
896.749 | Medium | Attributed to CH deformation |
Amorphous region of cellulose |