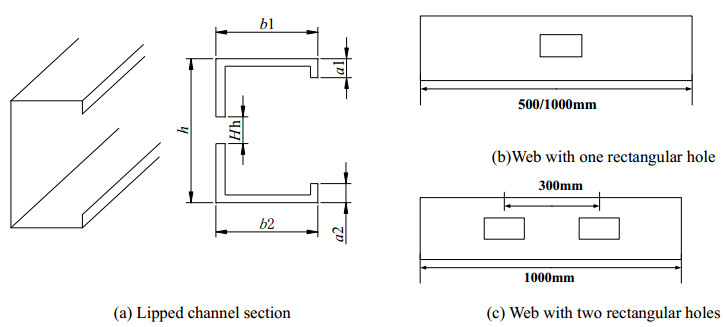
Citation: Roman I. Bogdanov, Yaakov B. Unigovski, Emmanuel M. Gutman, Iliya V. Ryakhovskikh, Roni Z. Shneck. Stress corrosion cracking of pipeline steels in near-neutral pH solutions: the role of mechanochemical and chemomechanical effects[J]. AIMS Materials Science, 2019, 6(6): 1065-1085. doi: 10.3934/matersci.2019.6.1065
[1] | Tran Hong Thai, Nguyen Anh Dai, Pham Tuan Anh . Global dynamics of some system of second-order difference equations. Electronic Research Archive, 2021, 29(6): 4159-4175. doi: 10.3934/era.2021077 |
[2] | Qianhong Zhang, Shirui Zhang, Zhongni Zhang, Fubiao Lin . On three-dimensional system of rational difference equations with second-order. Electronic Research Archive, 2025, 33(4): 2352-2365. doi: 10.3934/era.2025104 |
[3] | Amira Khelifa, Yacine Halim . Global behavior of P-dimensional difference equations system. Electronic Research Archive, 2021, 29(5): 3121-3139. doi: 10.3934/era.2021029 |
[4] | Merve Kara . Investigation of the global dynamics of two exponential-form difference equations systems. Electronic Research Archive, 2023, 31(11): 6697-6724. doi: 10.3934/era.2023338 |
[5] | Meng-Xue Chang, Bang-Sheng Han, Xiao-Ming Fan . Global dynamics of the solution for a bistable reaction diffusion equation with nonlocal effect. Electronic Research Archive, 2021, 29(5): 3017-3030. doi: 10.3934/era.2021024 |
[6] | Feng Wang, Taotao Li . Dynamics of a stochastic epidemic model with information intervention and vertical transmission. Electronic Research Archive, 2024, 32(6): 3700-3727. doi: 10.3934/era.2024168 |
[7] | Bin Wang . Random periodic sequence of globally mean-square exponentially stable discrete-time stochastic genetic regulatory networks with discrete spatial diffusions. Electronic Research Archive, 2023, 31(6): 3097-3122. doi: 10.3934/era.2023157 |
[8] | Najmeddine Attia, Ahmed Ghezal . Global stability and co-balancing numbers in a system of rational difference equations. Electronic Research Archive, 2024, 32(3): 2137-2159. doi: 10.3934/era.2024097 |
[9] | Wedad Albalawi, Fatemah Mofarreh, Osama Moaaz . Dynamics of a general model of nonlinear difference equations and its applications to LPA model. Electronic Research Archive, 2024, 32(11): 6072-6086. doi: 10.3934/era.2024281 |
[10] | Shu Wang, Mengmeng Si, Rong Yang . Dynamics of stochastic 3D Brinkman-Forchheimer equations on unbounded domains. Electronic Research Archive, 2023, 31(2): 904-927. doi: 10.3934/era.2023045 |
The CFS lipped channel sections have been widely used in buildings as walls, floors, and ceilings due to their high strength-to-weight ratio and ease of construction. However, the holes often appear in the web because of the installation of electrical, plumbing, and heating conduits for such lipped channel sections. The occurrence of holes in the web would decrease the cross-section area, stiffness and the constraint for the flange, which makes such sections prone to be distortional buckling.
In the literature, the distortional buckling of CFS members has been investigated by most researchers. Based on the studies conducted by Schafer et al. [1,2] and Yao et al. [3,4], the design methods of distortional buckling were given in the AISI 100-2016 [5] and GB50018 [6], respectively. Meanwhile, some significant work has been reported on the reduction in strength of channel sections having openings covering web crippling by Uzzaman et al. [7,8,9,10] and Lian et al. [11,12,13,14], shear by Pham [15], Pham et al. [16], Keerthan et al. [17,18], and Pham et al [16], the bending of beam by Moen et al. [20] and Zhao et al. [21], and the deep learning-based prediction by using Deep Belief Network by Fang et al. [22,23].
Recently, Chen et al. [24,25,26] reported experimental and numerical studies on the axial strength of single channels and back-to-back channels with edge-stiffened holes and found that the axial strength of channels with edge-stiffened holes was greater than those of plain channels. Meanwhile, some other work has been reported on the strength of channel sections having edge-stiffened hole covering web crippling by Uzzaman et al. [27,28] and moment capacity by Chen et al. [29].
In the literature, limited work has been reported on distortional buckling of CFS channels with holes in the web. The compression tests of 24 short and intermediate CFS lipped channel columns with and without slotted web holes showed that the presence of slotted hole caused a slight decrease in the ultimate capacity [30]. For lipped channel columns with web stiffener, numerical and experimental studies were carried out to analysis the effects of holes on the failure mode and load-carrying capacity by Yao and Wu [31]. The results demonstrated that the holes led the change of bucking mode and decreased the ultimate strength. The effects of holes on the buckling behavior of CFS channels under axial compression were studied by Macdonald et al. [32,33], and it was found that the ultimate failure load of the channels under compression varied greatly with the presence of holes. Zheng and Yu [34] reported the distortional buckling behavior of the CFS channel with web openings by using ANSYS finite element software, and the influence of the transverse and longitudinal hole spacing, the hole size, and the shape of the hole on the distortional buckling.
In order to develop the design method of effective width method and direct strength method for the axially-compressed member with holes, the calculated method of buckling coefficient and elastic buckling capacity for the member with holes has been studied by some researchers. The equivalent modulus method is used to calculate the elastic buckling stress of CFS members with slotted holes by Zhou and Yu [35]. According to finite element analysis, the modified formula of the distortional buckling coefficient for axially-compressed member with circular hole was given by Yao et al. [36]. The simplified methods to predict the local, distortional, and global critical elastic buckling loads of CFS columns with holes were developed based on theoretical and FE analysis [37]. Based on experiments and theoretical analysis, the modified direct strength methods were proposed by Moen and Schafer [38] and Yao and Rasmussen [39] for calculating the distortional buckling capacity of CFS members with web openings under axial compression. In terms of the design standards, the American Iron and Steel Institute (AISI) [5] do not provide sufficient effective width design rules for determining the distortional buckling strength of CFS channels with holes because the reduced effective width method is only suitable to members with relatively small holes in these codes. The direct strength method is given in AISI for determining distortional buckling strength of CFS channels with holes, but the elastic buckling capacity of members with holes need to be calculated by using finite element method or complicated formula. Meanwhile, there is no design provision about distortional buckling for the perforated members in the Chinese code [6].
As mentioned previously literatures, some works considered the distortional buckling behavior and design method of the CFS channels with holes have been reported. Nevertheless, limited work considered the distortional buckling has been reported on columns with large holes under axial compression by using effective width method. Thus, this paper reports 44 new distortional buckling experiments on the axial strength of CFS lipped channels with rectangular holes in the web. A nonlinear elasto-plastic FE model was then developed and validated against the test results in terms of ultimate strength and buckling modes. Using the validated FE model, a parametric study involving 16 models was conducted to investigate the effects of sections, hole size, and number of holes on the axial strength of such columns. The proven FEM was used to develop the distortional buckling coefficient equation of CFS lipped channel section under axial compression considering the effect of holes. Finally, the prediction method of ultimate strength of CFS lipped channels with holes in the web considering distortional buckling was proposed and the design strengths were compared against both the test and FEA results.
This test employed 44 CFS lipped channel sections under axial compression. There were 8 nonperforated members and 36 members with rectangular holes. The definitions of geometric parameters of specimen and the location and spacing of holes are illustrated in Figure 1. Four cross-sections were selected. The nominal thicknesses of the specimens are 0.8 and 1.0 mm. The heights of the rectangular holes are 0.2, 0.4, and 0.6 to the web depth. The ratio of length-to-width (Lh/Hh) of rectangular hole is equal to 2. The length of specimens is 500 and 1000 mm. The hole spacings are 300 mm for members with two rectangular holes. The labeling rule of all specimens is defined in Figure 2. For example, the label "C8008-05-RH21-1" defines the specimen as follows: C indicates the section is a lip channel section column; 8008 means that the nominal height of the web and the nominal thickness of section are 80 and 0.8 mm, respectively; RH21 represents that the section has a rectangular hole and the ratio of the height of the rectangular hole to the height of the web is 0.2; 1 represents the sequence number of the same specimens. The nominal and measured dimensions of all specimens are tabulated in Table 1.
Specimen | Nominal sectional dimension | Measured sectional dimension | initial imperfection Δmax/mm | |||||||||
L/mm | h/mm | b/mm | a/mm | t/mm | L/mm | h/mm | b1/mm | b2/mm | a1/mm | a2/mm | ||
C8008-05-NH-1 | 500 | 80 | 60 | 10 | 0.80 | 499.45 | 76.61 | 58.89 | 59.19 | 10.13 | 10.49 | 1.251 |
C8008-05-NH-2 | 499.55 | 78.77 | 58.93 | 58.88 | 10.17 | 9.85 | 1.124 | |||||
C8008-05-RH21-1 | 499.40 | 79.13 | 58.82 | 59.87 | 10.05 | 10.02 | 0.876 | |||||
C8008-05-RH21-2 | 499.35 | 77.11 | 58.72 | 60.14 | 9.22 | 9.79 | 0.752 | |||||
C8008-05-RH41-1 | 499.15 | 77.20 | 60.11 | 58.88 | 9.59 | 9.42 | 0.641 | |||||
C8008-05-RH41-2 | 499.50 | 79.18 | 59.58 | 59.38 | 10.07 | 9.95 | 0.521 | |||||
C8008-05-RH61-1 | 499.25 | 78.35 | 59.94 | 59.88 | 9.54 | 9.52 | 0.981 | |||||
C8008-05-RH61-2 | 499.35 | 77.69 | 60.26 | 59.29 | 10.32 | 9.46 | 1.141 | |||||
C10010-05-NH-1 | 500 | 100 | 90 | 10 | 1.00 | 474.15 | 99.25 | 90.05 | 89.19 | 9.04 | 8.83 | 0.825 |
C10010-05-NH-2 | 499.55 | 97.97 | 89.13 | 89.14 | 9.56 | 9.98 | 1.028 | |||||
C10010-05-RH21-1 | 499.40 | 97.70 | 90.04 | 89.27 | 9.65 | 9.23 | 1.254 | |||||
C10010-05-RH21-2 | 499.45 | 99.27 | 89.62 | 89.61 | 9.58 | 9.16 | 1.158 | |||||
C10010-05-RH41-1 | 499.50 | 99.37 | 89.58 | 90.02 | 9.32 | 9.24 | 1.345 | |||||
C10010-05-RH41-2 | 499.20 | 98.18 | 89.23 | 88.71 | 9.78 | 9.43 | 1.429 | |||||
C10010-05-RH61-1 | 499.40 | 96.75 | 89.80 | 89.81 | 9.34 | 9.39 | 0.988 | |||||
C10010-05-RH61-2 | 499.20 | 98.21 | 89.44 | 88.78 | 9.64 | 9.49 | 1.024 | |||||
C8008-10-NH-1 | 1000 | 80 | 60 | 10 | 0.8 | 1000.00 | 79.31 | 58.98 | 58.78 | 9.87 | 10.41 | 0.812 |
C8008-10-NH-2 | 1000.20 | 79.57 | 58.89 | 59.06 | 10.26 | 9.76 | 0.988 | |||||
C8008-10-RH21-1 | 999.80 | 79.23 | 59.40 | 59.61 | 10.03 | 9.91 | 0.841 | |||||
C8008-10-RH21-2 | 999.95 | 78.87 | 59.60 | 59.66 | 9.66 | 10.11 | 0.754 | |||||
C8008-10-RH41-1 | 1000.00 | 79.64 | 59.57 | 59.09 | 9.47 | 9.56 | 0.684 | |||||
C8008-10-RH41-2 | 1000.10 | 79.36 | 59.52 | 59.39 | 9.98 | 9.25 | 0.751 | |||||
C8008-10-RH61-1 | 999.90 | 78.50 | 60.12 | 59.54 | 9.80 | 9.60 | 1.042 | |||||
C8008-10-RH61-2 | 1000.10 | 78.58 | 59.78 | 59.36 | 9.81 | 9.93 | 0.985 | |||||
C8008-10-RH22-1 | 999.05 | 78.68 | 59.93 | 59.41 | 9.83 | 9.61 | 1.451 | |||||
C8008-10-RH22-2 | 999.95 | 79.23 | 59.58 | 58.90 | 10.19 | 9.68 | 1.345 | |||||
C8008-10-RH42-1 | 999.85 | 79.55 | 58.79 | 59.70 | 9.51 | 10.10 | 1.231 | |||||
C8008-10-RH42-2 | 1000.00 | 78.78 | 60.17 | 59.49 | 9.65 | 9.50 | 1.012 | |||||
C8008-10-RH62-1 | 999.70 | 79.38 | 59.43 | 59.39 | 9.69 | 9.80 | 0.984 | |||||
C8008-10-RH62-2 | 999.95 | 78.67 | 58.99 | 57.80 | 11.50 | 10.37 | 0.756 | |||||
C10010-10-NH-1 | 1000 | 100 | 90 | 10 | 1 | 999.00 | 98.97 | 88.95 | 88.44 | 9.29 | 9.83 | 0.852 |
C10010-10-NH-2 | 999.00 | 98.45 | 89.72 | 89.08 | 8.75 | 9.76 | 0.734 | |||||
C10010-10-RH21-1 | 1000.00 | 99.83 | 87.83 | 89.02 | 8.92 | 9.38 | 1.102 | |||||
C10010-10-RH21-2 | 999.50 | 99.73 | 88.45 | 89.15 | 9.02 | 9.34 | 1.034 | |||||
C10010-10-RH41-1 | 999.50 | 99.56 | 89.18 | 89.35 | 8.79 | 9.19 | 0.614 | |||||
C10010-10-RH41-2 | 1000.00 | 99.85 | 88.67 | 89.06 | 8.87 | 9.09 | 0.785 | |||||
C10010-10-RH61-1 | 1001.00 | 99.13 | 89.35 | 89.04 | 9.37 | 9.26 | 0.635 | |||||
C10010-10-RH61-2 | 1000.25 | 98.89 | 88.85 | 89.32 | 9.76 | 9.35 | 0.564 | |||||
C10010-10-RH22-1 | 1001.00 | 99.34 | 88.50 | 87.93 | 9.51 | 9.11 | 0.645 | |||||
C10010-10-RH22-2 | 1000.00 | 99.58 | 88.93 | 88.26 | 9.23 | 10.09 | 0.451 | |||||
C10010-10-RH42-1 | 999.90 | 99.18 | 89.34 | 88.51 | 10.15 | 9.29 | 0.845 | |||||
C10010-10-RH42-2 | 1000.00 | 98.92 | 88.75 | 88.74 | 9.23 | 9.23 | 0.684 | |||||
C10010-10-RH62-1 | 1000.00 | 98.41 | 89.34 | 89.01 | 9.91 | 10.06 | 0.945 | |||||
C10010-10-RH62-2 | 1000.00 | 98.50 | 89.65 | 89.11 | 9.89 | 9.27 | 0.863 |
Steel sheets of grade LQ550 with two kinds of thicknesses were selected to manufacture the specimens. 3 tensile coupon tests of steel sheets with different thicknesses were conducted to determine the material properties based on Chinese specification "Tensile tests of metallic materials Part 1: test methods at room temperature" (GB/T228.1-2010) [19]. The stress-strain curves of coupons for every kind of steel plates are shown in Figure 3. The measured average material properties including the static 0.2% proof stress (f0.2), initial Young's modulus (E), ultimate strength (fu), and ultimate strain (εu) are listed in Table 2.
t/mm | f0.2/MPa | fu/MPa | E/MPa | εu/% |
0.80 | 600 | 602 | 2.16 × 105 | 7.19 |
1.00 | 620 | 634 | 2.15 × 105 | 8.92 |
The initial geometric imperfection resulted from forming and transportation has a great influence on the buckling behavior of CFS members. So the initial imperfections of all specimens along the longitudinal direction were measured before test. The interval of longitudinal location measured was 150 mm. The measuring locations of cross-section are illustrated in Figure 4, including the initial local imperfection calculated by locations 1 and 3 and the initial distortional imperfection predicted by locations 2 and 4. The initial local and distortional geometric imperfections of Section C8008 and Section C10010 are depicted in Figure 5. The initial imperfections indicated that the imperfections of the CFS lipped channel columns had no obvious laws along the longitudinal direction. The maximum initial geometric imperfection magnitudes (Δmax) for all specimens are listed in Table 2.
The reaction frame system and a 500 kN hydraulic jack were used to apply axial compression load on all specimens as shown in Figure 6. The upper actuator and lower pedestal were fitted with 250 mm × 200 mm × 8 mm thick steel platen ground flat and parallel. The column specimens put directly on the steel platen as they were compressed. Friction between the column ends and the steel platens were the only lateral forces that restrained the column cross-section under load. A load cell measured the applied compression force on each specimen. The displacement transducers and strain gauges were adopted to capture the displacement, deformation, and stress of the specimens during the loading process as illustrated in Figure 7. For specimens without hole, four position transducers (Figure 7(a)) were used to record the lateral deformations and four strain gauges (Figure 7(b)) were arranged to measure the stress of web. These instrumentations are set at the mid-height of the stud column. At the mid-height of all specimens with hole, four position transducers (Figure 7(c)) and four strain gauges (Figure 7(d)) were positioned. At the web about 50 mm higher the mid-height of specimens with hole, Three position transducers and four strain gauges were employed as depicted in Figure 7(e), (f). A position transducer was set at the upper end plate of the specimens to measure the vertical displacement under axial load for all specimens.
The buckling failure modes of 44 axial compression specimens are shown in Table 3, where L represents local buckling, D represents distorted buckling. Pt, Pa, Pc are the test result, finite element analysis result, and calculated result by using proposed method, respectively.
Specimen | Test buckling mode | FEA buckling mode | Pt/KN | Reduction in capacity /% | Pa/KN | Pc | Pt/Pa | Pt/Pc |
C8008-05-NH-1 | L + D | L + D | 34.38 | 35.44 | 34.04 | 0.97 | 1.01 | |
C8008-05-NH-2 | L + D | L + D | 35.97 | 36.33 | 34.17 | 0.99 | 1.05 | |
C8008-05-RH21-1 | L + D | L + D | 34.55 | 1.78 | 34.9 | 32.48 | 0.99 | 1.06 |
C8008-05-RH21-2 | L + D | L + D | 34.4 | 2.2 | 34.77 | 32.06 | 0.99 | 1.07 |
C8008-05-RH41-1 | L + D | L + D | 33.3 | 5.33 | 33.64 | 30.97 | 0.99 | 1.08 |
C8008-05-RH41-2 | L + D | L + D | 33.91 | 3.6 | 34.1 | 30.29 | 0.99 | 1.12 |
C8008-05-RH61-1 | L + D | L + D | 29.91 | 14.97 | 31.82 | 29.01 | 0.94 | 1.03 |
C8008-05-RH61-2 | L + D | L + D | 29.45 | 16.28 | 31.1 | 28.97 | 0.95 | 1.02 |
C10010-05-NH-1 | D | D | 52.31 | 53.7 | 49.98 | 0.97 | 1.05 | |
C10010-05-NH-2 | D | D | 52.48 | 54.67 | 49.86 | 0.96 | 1.05 | |
C10010-05-RH21-1 | D | D | 51.95 | 0.85 | 53.01 | 48.83 | 0.98 | 1.06 |
C10010-05-RH21-2 | D | D | 51.48 | 1.75 | 52.53 | 48.91 | 0.98 | 1.05 |
C10010-05-RH41-1 | D | D | 51.1 | 2.48 | 53.23 | 48.03 | 0.96 | 1.06 |
C10010-05-RH41-2 | D | D | 50.22 | 4.16 | 51.77 | 48.21 | 0.97 | 1.04 |
C10010-05-RH61-1 | D | D | 46.19 | 11.85 | 49.14 | 42.96 | 0.94 | 1.08 |
C10010-05-RH61-2 | D | D | 44.12 | 15.8 | 45.96 | 43.24 | 0.96 | 1.02 |
C8008-10-NH-1 | L + D | L + D | 27.52 | 28.3 | 26.42 | 0.97 | 1.04 | |
C8008-10-NH-2 | L + D | L + D | 27.85 | 28.3 | 26.4 | 0.98 | 1.05 | |
C8008-10-RH21-1 | L + D | L + D | 27.5 | 0.6 | 28 | 25.87 | 0.98 | 1.06 |
C8008-10-RH21-2 | L + D | L + D | 27.74 | -0.2 | 27.91 | 25.83 | 0.99 | 1.07 |
C8008-10-RH41-1 | L + D | L + D | 26.94 | 2.6 | 26.28 | 24.06 | 1.03 | 1.12 |
C8008-10-RH41-2 | L + D | L + D | 26.33 | 4.8 | 25.99 | 24.15 | 1.01 | 1.09 |
C8008-10-RH61-1 | L + D | L + D | 23.8 | 13.9 | 24.2 | 22.73 | 0.98 | 1.05 |
C8008-10-RH61-2 | L + D | L + D | 23.88 | 13.7 | 23.99 | 22.89 | 1.00 | 1.04 |
C8008-10-RH22-1 | L + D | L + D | 27.6 | 0.25 | 27.25 | 25.53 | 1.01 | 1.08 |
C8008-10-RH22-2 | L + D | L + D | -- | -- | 27.79 | 25.69 | -- | -- |
C8008-10-RH42-1 | L + D | L + D | 26.52 | 4.2 | 26.05 | 23.91 | 1.02 | 1.11 |
C8008-10-RH42-2 | L + D | L + D | -- | -- | 26.5 | 23.6 | -- | -- |
C8008-10-RH62-1 | L + D | L + D | 23.5 | 15.1 | 24.02 | 22.45 | 0.98 | 1.05 |
C8008-10-RH62-2 | L + D | L + D | -- | -- | 23.42 | 22.66 | -- | -- |
C10010-10-NH-1 | L + D | L + D | 41.7 | 41.29 | 41.31 | 1.01 | 1.01 | |
C10010-10-NH-2 | L + D | L + D | 39.6 | 40.58 | 40.73 | 0.98 | 0.97 | |
C10010-10-RH21-1 | L + D | L + D | 40.1 | 1.3 | 40.62 | 39.64 | 0.99 | 1.01 |
C10010-10-RH21-2 | L + D | L + D | 40.95 | -0.74 | 40.65 | 39.68 | 1.01 | 1.03 |
C10010-10-RH41-1 | L + D | L + D | 39.38 | 3.1 | 39.9 | 36.79 | 0.99 | 1.07 |
C10010-10-RH41-2 | L + D | L + D | 39.4 | 3.1 | 39.26 | 36.71 | 1.00 | 1.07 |
C10010-10-RH61-1 | L + D | L + D | 37.3 | 8.2 | 36.51 | 35.52 | 1.02 | 1.05 |
C10010-10-RH61-2 | L + D | L + D | 37.66 | 7.4 | 36.1 | 35.83 | 1.04 | 1.05 |
C10010-10-RH22-1 | L + D | L + D | 40.25 | 0.98 | 39.99 | 39.55 | 1.01 | 1.02 |
C10010-10-RH22-2 | L + D | L + D | -- | -- | 40.52 | 40.15 | -- | -- |
C10010-10-RH42-1 | L + D | L + D | 38.45 | 5.4 | 38.88 | 37.16 | 0.99 | 1.03 |
C10010-10-RH42-2 | L + D | L + D | 38.7 | 4.8 | 38.46 | 37.52 | 1.01 | 1.03 |
C10010-10-RH62-1 | L + D | L + D | 36.8 | 9.5 | 36.36 | 36.08 | 1.01 | 1.02 |
C10010-10-RH62-2 | L + D | L + D | 37.05 | 8.9 | 36.87 | 35.94 | 1.00 | 1.03 |
Average | 0.99 | 1.05 | ||||||
Standard deviation | 0.0005 | 0.0009 | ||||||
Variable coefficient | 0.023 | 0.029 |
It can be found from Table 3, the local buckling occurred firstly for the Section C8008 with the length of 500 mm (Figure 8(a)). With the increase of load, the distortional buckling appeared sequentially (Figure 8(b)). Finally, the specimens failed with the interaction of local and distortional buckling (Figure 8(c)). For Section C10010 with the length of 500 mm, the distortional buckling occurred firstly (Figure 9(a)). Then the deformation of distortional buckling was more and more obvious with the increase of load (Figure 9(b)). The specimens failed with distortional buckling (Figure 9(c)). For Sections C10010 and C8008 with the length of 1000 mm, the local buckling occurred at the web firstly (Figure 10(a)). Then the distortional buckling appeared with the increasing of load (Figure 10(b)). Finally the specimens suffered with interaction of local and distortional buckling (Figure 10(c)).
The comparison on load-strain curves at the plate adjacent to hole (Point 4) for specimen C10010 with the length of 1000 mm and different hole sizes is shown in Figure 11. It can be seen from Figure 11, the strain gradually increases with the increase of the hole size, which indicates that the stress concentration is more obvious with the increase of hole size.
Figure 12 shows the load-strain curves of the specimen C10010-10-RH21-1 at two cross-sections. For the cross-section which is higher than middle cross-section, it can be seen from Figure 12(a), the strains of all points increases linearly before the load of the specimen reaches 24 kN. The strain changes abruptly after the load exceeds 24 kN which indicates that the local buckling occurs for the web. For the middle cross-section, it can be seen from Figure 12(b), the strain changes abruptly when the load reaches 15 kN which indicates the local buckling occurs at the plate adjacent to hole. The above comparison shows that the presence of hole lets the local buckling occur early.
The comparisons on load-strain curves between the plate adjacent to hole (Point 4) and the position higher 100 mm along the longitudinal direction (Point 1) for the Section C10010 with the length of 1000 mm and different hole sizes are shown in Figure 13. It can be seen from Figure 13, the strain of the plate adjacent to hole is larger than that of the position higher 100 mm along the longitudinal direction because of the stress concentration resulted from the hole. Larger the hole size is, larger the stress concentration is.
The load-carrying capacities of all specimens are shown in Table 3. As can be seen from Table 3, the load-carrying capacities for Sections C8008 and C10010 with the length of 500 mm and hole size Hh/h of 0.2, 0.4 and 0.6 decrease by 2.2, 6.33, 16.28% and 1.75, 4.16, 15.8% compared with the specimens without hole, respectively. The load-carrying capacities for Sections C8008 and C10010 with the length of 1000 mm and hole size Hh/h of 0.2, 0.4 and 0.6 decrease by 0.6, 4.8, 13.9% and 1.3, 3.1, 8.2% compared with the specimens without hole, respectively. It indicates that the load-carrying capacity of the specimen decreases obviously with the increase of the hole size. It indicates that the load-carrying capacity of the specimen decreases obviously with the increase of the hole size. For the specimens with the length of 100 mm and two rectangular holes, the same conclusion can be obtained.
Figure 14 shows the load-axial displacement curves of the Section C10010 with the length of 1000 mm for different hole sizes. It can be seen from Figure 13 that the load-carrying capacity and the ductility of the specimen decrease with the increasing of the hole size.
The finite element program ABAQUS [20] was used to simulate the distortional buckling modes and behavior of the specimens and conduct a further parametric analysis on the CFS lipped channel axially-compressed columns with rectangular holes. The finite element model is shown in Figure 15. The S4R shell element was selected for modeling column and the analytical rigid body element was used for modeling the upper and lower end steel plates of the specimens. The dimensions of the cross sections measured before the tests were used in the FEM. The mesh size of 5 mm × 5 mm was selected to model specimens. The ideal elasto-plastic model based on the material properties obtained from the coupon tests shown in Table 2 was used in FEM. The end constraint conditions of the test plate were all fixed, by constraining the five degrees of freedom of the reference point RP1 at the upper end plate (2 translation degrees of freedom and 3 rotational degree of freedom, releasing UZ degrees of freedom to control displacement) and the six degrees of freedom of the reference point RP2 at the lower end plate. In fact, the fixed end constraint conditions developed in the paper had a few different with the test because a litter movement or rotation can be observed at the failure stage for the specimen ends. But the effect of this error on the buckling mode and the load carrying capacity can be ignored in the finite element analysis. The measured dimensions of specimens (see in Table 1) were all included in the models. The analysis procedure included two phases: Firstly, an eigenvalue buckling analysis was performed to find the most probable elastic buckling mode of the specimen. The measured maximum magnitude of the initial geometric imperfections shown in Table 1 was applied to the first eigen-mode to produce the geometric imperfection of FEM. Secondly, nonlinear analysis considering both material nonlinear and geometric nonlinear was carried out by using the arc-length method to analyze the failure modes and ultimate load-carrying capacity of the specimen.
The buckling failure mode and load-carrying capacities of all specimens obtained from the finite element analysis are shown in Table 3. It can be seen from Table 3 that the buckling modes of the specimens obtained from the finite element analysis are consistent with the experimental buckling mode. The maximum error of the load-carrying capacity between the test and the finite element analysis results is 6%. The mean value and the corresponding coefficient of variation of ratio of the test result and the finite element analysis result are 0.99 and 0.023, respectively. The comparison on load-axial displacement curve and buckling mode of the finite element analysis and test for the specimen C10010-10-RH61-1 are shown in Figures 16 and 17, respectively. By the above-mentioned comparison, the load-carrying capacities, the failure modes, and load-displacement curves obtained from FEA show good agreement with the test results. Therefore, the FEM developed in this study for the axially-compressed members with rectangular hole in the web has been well validated with the tests.
The proven finite element model was used to analysis on the buckling behavior and ultimate load-carrying capacity of Sections SS89 and SS7510 with different hole sizes and lengths which are widely used in engineering. The section dimensions of the columns with holes, the buckling modes and the ultimate load-carrying capacities obtained from the finite element analysis were shown in Table 4, and G represents the overall buckling.
h/mm | b/mm | a/mm | t/mm | fy/MPa | L/mm | Hh/mm | Lh/mm | The number of holes | Hole spacing S/mm | Buckling mode | Pa/kN | Pc/kN | Pa/Pc |
89 | 41 | 13 | 1 | 280 | 1000 | 0 | 0 | 0 | - | L | 36.5 | 34.2 | 1.07 |
89 | 41 | 13 | 1 | 280 | 1000 | 26.7 | 26.7 | 1 | - | L + D | 35.8 | 33.4 | 1.07 |
89 | 41 | 13 | 1 | 280 | 1000 | 44.5 | 44.5 | 1 | - | L + D | 33.9 | 31 | 1.09 |
89 | 41 | 13 | 1 | 280 | 1500 | 62.3 | 62.3 | 1 | - | L+ D | 29.8 | 27.8 | 1.07 |
89 | 41 | 13 | 1 | 280 | 1500 | 0 | 0 | 0 | - | L + G | 34.3 | 31.4 | 1.09 |
89 | 41 | 13 | 1 | 280 | 1500 | 26.7 | 26.7 | 3 | 500 | L + G | 33.2 | 30.8 | 1.08 |
89 | 41 | 13 | 1 | 280 | 1500 | 44.5 | 44.5 | 3 | 500 | L+D+G | 30.8 | 28.4 | 1.08 |
89 | 41 | 13 | 1 | 280 | 1500 | 62.3 | 62.3 | 3 | 500 | L+D+G | 27.5 | 25.2 | 1.09 |
75 | 40 | 8 | 1 | 550 | 1000 | 0 | 0 | 0 | - | L + D | 43.2 | 41 | 1.05 |
75 | 40 | 8 | 1 | 550 | 1000 | 22.5 | 22.5 | 1 | - | L + D | 42.3 | 40.5 | 1.04 |
75 | 40 | 8 | 1 | 550 | 1000 | 37.5 | 37.5 | 1 | - | L + D | 39.7 | 37.8 | 1.05 |
75 | 40 | 8 | 1 | 550 | 1500 | 52.5 | 52.5 | 1 | - | L+D+G | 36.1 | 33.5 | 1.08 |
75 | 40 | 8 | 1 | 550 | 1500 | 0 | 0 | 0 | - | L+D+G | 35.3 | 32.6 | 1.08 |
75 | 40 | 8 | 1 | 550 | 1500 | 22.5 | 22.5 | 3 | 500 | L+D+G | 34.4 | 32.2 | 1.07 |
75 | 40 | 8 | 1 | 550 | 1500 | 37.5 | 37.5 | 3 | 500 | L+D+G | 30.9 | 28.5 | 1.08 |
75 | 40 | 8 | 1 | 550 | 1500 | 52.5 | 52.5 | 3 | 500 | L+D+G | 27.3 | 25.1 | 1.09 |
Mean value | 1.07 | ||||||||||||
Standard deviation | 0.0002 | ||||||||||||
Coefficient of variable | 0.014 |
It can be seen from Table 4 that the ultimate load-carrying capacity gradually decreases with the increase of the hole size. Larger the hole size is, lower the ultimate load-carrying capacity is. For example, the ultimate load-carrying capacity of the Section SS89 with the length of 1000 mm and the hole size Hh/h of 0.7 decreases by 18% compared with that of the Section SS89 with the length of 1000 mm without hole. At the same time, it can be found that the buckling mode of the members with large holes may change from interaction of local and distortional buckling to interaction of local, distortional, and overall buckling due to the reduction of the rotational constraint of the web to the flange and the bending stiffness.
The load-carrying capacity of the axially-compressed member with rectangular holes can be calculated by using effective width method in Chinese code GB50018-2002. The calculation formula is shown in Eq (1):
N=φAef | (1) |
where, φ is the overall buckling coefficient of the axially-compressed member; Ae is the effective area of the cross section, which should be calculated by the effective width of the cross section be. The effective width of the web can be predicted according to the suggested method in reference [21]. The effective width of flange is calculated by using the Eq (2), and the buckling coefficient takes into account the influence of the hole. For single rectangular hole and multi-rectangular holes, k1 = δ1k and k2 = δ2k are used to calculate the buckling stability, respectively. k is the buckling coefficient of flange without hole in the web, while k1 and k2 are buckling coefficients of flange with single hole and multi holes in the web.
{bet=bctbt≤18αρbet=(√21.8αρbt−0.1)bct18αρ<bt<38αρbet=25αρbtbctbt≥38αρ | (2) |
Since the hole in the web reduces the rotational constraint stiffness of web to flange, members with holes in the web are prone to occur distortional buckling than the members without hole. The distortional buckling stress and coefficient decrease because of the presence of hole. The finite element is used to analyze the elastic distortional buckling stress of axially-compressed member with rectangular holes in the web. The analysis parameters include hole size, hole spacing and number of holes.
In order to ensure the occurrence of distortional buckling for the member with rectangular hole, the section dimensions of the member were selected as h = 100 mm, b = 65 mm, a = 10 mm, t = 1.5 mm and l = 1200 mm. The distortional buckling half wavelength of this member was 400 mm. A single rectangular hole was in the middle of the web, and the ratio of hole height to web height (Hh/h) changed from 0.2 to 0.7. The ratio of hole length to hole height (Lh/Hh) was set as 1, 2 and 4, respectively. The comparison between the distortional buckling coefficient of members with holes (ka) and the distortional buckling coefficient of members without holes (k0) is shown in Figure 18. It can be seen from Figure 18 that the distortional buckling coefficient decrease with the increase of Lh/Hh and Hh/h which indicates that Lh/Hh and Hh/h have important effect on the distortional buckling coefficient.
1) A single hole and multiple holes in a distortional buckling half wave
The section of the finite element analysis is the same as the section of the member with single rectangular hole. Three rectangular holes are equally separated from the middle of the member to both ends. The size of the hole Hh/h changes from 0.2 to 0.7, and Lh/Hh is 1 and 2. The hole spacing is 150 mm when holes are set in a distorted buckling half-wave. The hole spacing is equal to the distorted buckling half-wavelength of the member when holes are set in different half-waves. The variation of ka/k0 is shown in Figure 19. It can be seen from Figure 19 that Lh/Hh has a great influence on the distortional buckling coefficient, while the single hole or multiple holes in a distortional buckling half wave have little influence on the distortional buckling coefficient.
2) Effect of hole spacing
When the number of holes is 3, Lh/Hh is equal to 1, the hole spacing changes from 150 to 500 mm, and the hole size Hh/h is 0.3, 0.5 and 0.7, the ratio of the distortional buckling coefficient ka to the distortional buckling coefficient k0 varies with the hole spacing as shown in Figure 20. It can be seen from Figure 20 that ka/k0 changes with hole spacing basically similar. With the increase of hole spacing, ka/k0 increases firstly and then decreases. When the hole spacing reaches 400 mm (half wavelength of distortional buckling), ka/k0 is the minimum. Therefore, the distorted buckling coefficient of the member with holes spacing equaling to the distortional buckling half wavelength can be conservative taken as the distortional buckling coefficient of the cold-formed thin-wall steel channel section with rectangular holes in the web.
1) Axially-compressed member with single rectangular hole in the web
The distortional buckling coefficient of members with holes can be calculated using formula k1 = δ1k, where k is the distortional buckling coefficient of the axially-compressed member without holes, δ1 is the reduction coefficient of distortional buckling coefficient which can be calculated by using formula (3) obtained from above finite element analysis as shown in Figure 17.
δ1={(0.987+0.057(Hhh)−0.202(Hhh)2)(LhHh)−0.07,Hhh≤0.5(0.987+0.057(Hhh)−0.202(Hhh)2)(LhHh)−0.105,Hhh>0.5 | (3) |
2) Axially-compressed member with multiple rectangular holes in the web.
The distortional buckling coefficient of members with holes can be calculated using formula k2 = δ2k, where δ2 is the reduction coefficient of distortional buckling coefficient which can be calculated by using Eq (4) obtained from above finite element analysis as shown in Figures 18 and 19.
δ2={(0.98+0.069(Hhh)−0.363(Hhh)2)(LhHh)−0.105,Hhh≤0.4(0.98+0.069(Hhh)−0.363(Hhh)2)(LhHh)−0.16,Hhh>0.4 | (4) |
The load-carrying capacities of specimens were calculated by using the suggested reduction coefficient of distortional buckling coefficient as shown in Table 3. The mean value and the coefficient of variation of the ratio of test and calculated capacity Pt/Pc were 1.05 and 0.029, respectively. The load-carrying capacities were calculated by using the suggested reduction coefficient of distortional buckling coefficient for the common Sections SS89 and SS7510 as shown in Table 4. The mean and the coefficient of variation of the ratio of Pa/Pc of the finite element analysis and the calculated results are 1.07 and 0.014, respectively. The results show that the proposed method is safe and reliable to calculate the load-carrying capacity of the lipped channel section with holes in the web under axial compression.
1) Forty-four CFS lipped channel sections with and without rectangular holes in the web were conducted under axial compression. The specimens displayed distortional buckling or interaction of distortional and local buckling. The load-carrying capacity of specimens with holes was lower than that of specimens without holes. The load-carrying capacities of specimens gradually decreased with the increase of the size of holes.
2) The finite element program ABAQUS was used to simulate the buckling modes and ultimate capacities of test specimens. The analysis results were in good agreement with the test results. The compared results show that the finite element model is feasible to analyze the distortional buckling behavior and load-carrying capacity of the axially-compressed member with holes in the web. The proven finite element model was used to analyze the distortional buckling behavior of the common cross-sections used in engineering. The analysis results show that the load-carrying capacity decreases with the increase of the hole size and the buckling mode would be affected by the hole.
3) The elastic distortional buckling behavior and buckling coefficient of CFS lipped channel section with holes under axial compression was analyzed by using finite element. Based on the finite element analysis results, a reduction method for the distortional buckling coefficient of axially-compressed members with rectangular holes in the web was developed.
4) Based on the reduction formulas of distortion buckling coefficient and effective width method, the load-carrying capacities of axially-compressed members with rectangular holes in the web were calculated. The comparison between the experimental results and the finite element analysis results shows that the developed calculation method has great accuracy and applicability.
The author declares that there is no conflict of interest regarding the publication of this paper.
This research was funded by National Natural Science Foundation Projects of China, grant number 51868049, Natural Science Foundation Projects of Jiangxi Province in China, grant number 20181BAB206040, and Department of Education Science and Technology Projects of Jiangxi Province in China, grant number GJJ180932 and GJJ170983.
[1] | National Energy Board (1996) Public inquiry concerning stress corrosion cracking on Canadian oil and gas pipelines: report of the inquiry. MH-2-95, Canada. |
[2] | Canadian Energy Pipeline Association (1996) Submission to the National Energy Board. Proceeding MH-2-95, 2. |
[3] | Gareev AG, Ivanov IA, Abdullin IG, et al. (1997) Prognozirovaniye Korrozionno-Mekhanicheskikh Razrusheniy Magistral'nykh Truboprovodov (Prediction of Corrosion/Mechanical Damage to Main Pipelines), Moscow: Gazprom IRZ, 1-170. (in Russian) |
[4] | Parkins R (2000) A review on SCC of high-pressure pipelines. NACE-International Corrosion Conference Series, 00363. |
[5] | Arabey AB, Knoshinski Z (2006) Korrozionnoe Rastreskivanie Pod Napryazheniem Trub Magistral'nykh Gazoprovodov. Atlas (Stress Corrosion Cracking of Main Gas Pipelines. Atlas), Moscow: Nauka, 1-106. (in Russian) |
[6] | King F (2010) Stress corrosion cracking of carbon steel used fuel containers in a Canadian deep geological repository in sedimentary rock. TR-2010-21, Nuclear Waste Management Organization, 34. |
[7] |
Meresht ES, Farahani TS, Neshati J (2011) Failure analysis of stress corrosion cracking occurred in a gas transmission steel pipeline. Eng Fail Anal 18: 963-970. doi: 10.1016/j.engfailanal.2010.11.014
![]() |
[8] | Cheng YF (2013) Stress Corrosion Cracking of Pipelines, Hoboken: John Wiley & Sons, 257. |
[9] | Alimov SV, Arabey AB, Ryakhovskih IV, et al. (2015) The concept of diagnosis and repair gas mains in regions with high susceptibility to stress corrosion cracking. Nat Gas Indust 724: 10-15. (in Russian) |
[10] |
Gamboa E (2015) Inclined stress corrosion cracks in steel pipelines. Corros Eng Sci Technol 50: 191-195. doi: 10.1179/1743278215Y.0000000006
![]() |
[11] |
Chen W (2016) An overview of near-neutral pH stress corrosion cracking in pipelines and mitigation strategies for its initiation and growth. Corrosion 72: 962-977. doi: 10.5006/1967
![]() |
[12] | Canadian Energy Pipeline Association (CEPA) (2015) Recommended Practices for Managing Near-neutral pH Stress Corrosion Cracking 3rd Edition, 158. Avaliable from: https://www.cepa.com/wp-content/uploads/2016/11/Stress-Corrosion-Cracking_3rdEdition_CEPA_FINAL.pdf |
[13] | Malkin AI, Marshakov AI, Arabei AB (2009) Processes of crack initiation and propagation on the steels of main pipelines. Part I: modern understanding of the mechanisms of stress corrosion cracking of pipeline steels in aqueous media. Corros Mater Prot 10: 1-16. |
[14] |
Parkins RN, Blanchard WK, Delanty BS (1994) Transgranular stress corrosion cracking of high-pressure pipelines in contact with solutions of near neutral pH. Corrosion 50: 394-408. doi: 10.5006/1.3294348
![]() |
[15] | Ryakhovskikh IV, Bogdanov RI, Arabey AB (2019) Regularities of pipelines stress corrosion cracking. 14th Pipeline Technology Conference, 1-13. |
[16] | Ryakhovskikh IV, Bogdanov RI, Rodionova IG et al. (2018) Regularities of stress corrosion cracking of pipe steels. 9th Eurasian Scientific and Practical Conference "Strength of Heterogeneous Structures-PROST 2018", 191. (in Russian) |
[17] | Gutman EM (1967) A transl. of Fiziko-khimicheskaya mekhanika materialov, Academy of Sciences of the Ukrainian SSR. Sov Mat Sci 3: 190-196, 304-310, 401-409. |
[18] | Gutman EM (1974) Mechanochemistry of Metals and Corrosion Prevention, Moscow: Metallurgy, 231. (in Russian) |
[19] | Gutman EM (1994) Mechanochemistry of Solid Surfaces, New Jersey-London-Singapore: World Scientific, 332. |
[20] | Gutman EM (1998) Mechanochemistry of Materials, Cambridge: Cambridge Interscience, 205. |
[21] |
Gutman EM (1994) Surface placticity modification using electrolytic etching. Surf Coat Tech 67: 133-136. doi: 10.1016/S0257-8972(05)80037-4
![]() |
[22] | Ostwald W (1917) Grundriss der allgemeinen Chemie, 5 Eds., Dresden: Steinkopff. |
[23] | Heinicke G (1984) Tribochemistry, Berlin: Academie-Verlag. |
[24] | Boldyrev VV (1983) Experimental methods in mechanochemistry of inorganic solids, In: Herman H, Treatise on Materials Science and Technology, New York: Academic Press, 19: 185-223. |
[25] | Butyagin PY (1989) Active States in Mechanochemical Reactions, Glasgow: Harwood Academic Publishers. |
[26] | Tkacova K (1989) Mechanical Activation of Minerals, Amsterdam: Elsevier. |
[27] |
Suryanarayana C (2001) Mechanical alloying and milling. Prog Mater Sci 46: 1-184. doi: 10.1016/S0079-6425(99)00010-9
![]() |
[28] | Baláž P (2008) Mechanochemistry in Nanoscience and Minerals Engineering, Berlin: Springer-Verlag, 413. |
[29] |
Xu LY, Cheng YF (2013) Development of a finite element model for simulation and prediction of mechano-electrochemical effect of pipeline corrosion. Corros Sci 73: 150-160. doi: 10.1016/j.corsci.2013.04.004
![]() |
[30] |
Xu LY, Cheng YF (2012) An experimental investigation of corrosion of X100 pipeline steel under uniaxial elastic stress in a near-neutral pH solution. Corros Sci 59:103-109. doi: 10.1016/j.corsci.2012.02.022
![]() |
[31] |
Xu LY, Cheng YF (2012) Corrosion of X100 pipeline steel under plastic strain in a neutral pH bicarbonate solution. Corros Sci 64: 145-152. doi: 10.1016/j.corsci.2012.07.012
![]() |
[32] |
Xu LY, Cheng YF (2017) A finite element based model for prediction of corrosion defect growth on pipelines. Int J Pres Ves Pip 153: 70-79. doi: 10.1016/j.ijpvp.2017.05.002
![]() |
[33] | Oura K, Lifshits VG, Saranin AA, et al. (2003) Surface Science-An Introduction, New York: Springer-Verlag, 440. |
[34] | Gutman EM, Fourie JT (1977) Surface Effects in Crystal Plasticity, Netherlands: Springer, 17: 737. |
[35] | Cottrell AH, Bilby BA (1949) Dislocation theory of yielding and strain ageing of iron. Proc Phys Soc Sec A 62: 49-62. |
[36] | Dieter GE (2000) Mechanical behavior under tensile and compressive loads, In: Medlin A, Mechanical Testing and Evaluation, ASM International, 8: 237-262. |
[37] |
Guo XH, Lu BT, Luo JL (2006) Responce of surface mechanical properties to electrochemical dissolution determined by in situ nanoindentation technique. Electrochem Commun 8: 1092-1098. doi: 10.1016/j.elecom.2006.04.020
![]() |
[38] |
Gutman EM, Unigovski Ya, Shneck R, et al. (2016) Electrochemically enhanced surface plasticity of steels. Appl Surf Sci 388: 49-56. doi: 10.1016/j.apsusc.2016.04.071
![]() |
[39] | Zhu RK, Lu BT, Luo JL, et al. (2013) Effect of cold work on surface reactivity and nano-hardness of alloy 800 in corroding environment. Appl Surf Sci 270: 733-762. |
[40] |
Revie RW, Uhlig H (1974) Effect of applied potential and surface dissolution on the creep behavior of copper. Acta Metall 22: 619-627. doi: 10.1016/0001-6160(74)90159-X
![]() |
[41] | Olive JM, Sarrazin C (1993) Effect of anodic dissolution on creep rate of austenitic stainless steel, Corrosion-Deformation Interactions, In: Magnin T, Gras JM, France: Les Editions de Phyisque, 153-162. |
[42] |
Unigovski Ya, Keren Z, Eliezer A, et al. (2005) Creep behavior of pure magnesium and Mg-Al alloys in active environments. Mater Sci Eng A 398: 188-197. doi: 10.1016/j.msea.2005.03.017
![]() |
[43] | Unigovski Ya, Gutman EM (2011) Corrosion creep and fatigue behavior of Mg alloys, Corrosion of Magnesium Alloys, In: Song GL, Oxford-Cambridge-Philadelphia-New Delhi: Woodhead Publishing, 365-402. |
[44] |
Hoar TP, West JM (1962) Mechano-chemical anodic dissolution of austenitic stainless steel in hot chloride solution. Proc R Soc London Ser A 268: 304-315. doi: 10.1098/rspa.1962.0142
![]() |
[45] |
Raicheff RG, Damjanovic A, Bockris JO'M (1967) Dependence of the velocity of the anodic dissolution of iron on its yield rate under tension. J Chem Phys 47: 2198-99. doi: 10.1063/1.1712258
![]() |
[46] |
Despic AR, Raicheff RG, Bockris JO'M (1968) Mechanism of the acceleration of the electrodic dissolution of metals during yielding under stress. J Chem Phys 49: 926-938. doi: 10.1063/1.1670162
![]() |
[47] |
Scully JC (1975) Stress corrosion crack propagation: A constant charge criterion. Corros Sci 15: 207-224. doi: 10.1016/S0010-938X(75)80017-5
![]() |
[48] |
Andresen PL, Ford FP (1988) Life prediction by mechanistic modeling and system monitoring of environmental cracking of iron and nickel alloys in aqueous systems. Mater Sci Eng A 103: 167-184. doi: 10.1016/0025-5416(88)90564-2
![]() |
[49] |
Parkins RN (1988) Localized corrosion and crack initiation. Mater Sci Eng A 103: 143-156. doi: 10.1016/0025-5416(88)90562-9
![]() |
[50] |
Saito K, Kunya J (2001) Mechanochemical model to predict SCC growth of stainless steel in high temperature water. Corros Sci 43: 1751-1766. doi: 10.1016/S0010-938X(00)00173-6
![]() |
[51] |
Gutman EM (2007) An inconsistency in "film rupture model" of stress corrosion cracking. Corros Sci 49: 2289-2302. doi: 10.1016/j.corsci.2006.10.023
![]() |
[52] |
Hall JR, MM (2009) Critique of the Ford-Andresen film rupture model for aqueous stress corrosion cracking. Corros Sci 51: 1103-1106. doi: 10.1016/j.corsci.2009.02.022
![]() |
[53] |
Chen W, King F, Vokes E (2002) Characteristics of near-neutral-pH stress corrosion cracks in an X-65 pipeline. Corrosion 58: 267-275. doi: 10.5006/1.3279878
![]() |
[54] | Chen W (2017) Modeling and prediction of stress corrosion cracking of pipeline steels, In: El-Sherik AM, Trends in Oil and Gas Corrosion Research and Technologies Production and Transmission, France: Woodhead Publishing, 707-748. |
[55] | Ryakhovskikh IV (2013) A complex technique of research of corrosion-mechanical properties of low-carbon low-alloyed pipe steels and an assessment of their firmness against SCC [PhD's thesis]. National Research Nuclear University MEPhI, Moscow, 155. (in Russian) |
[56] |
Wang SH, Chen W, King F, et al. (2002) Precyclic-loading-induced stress corrosion cracking of pipeline steels in a near-neutral-pH soil environment. Corrosion 58: 526. doi: 10.5006/1.3277644
![]() |
[57] |
Chu R, Chen W, Wang SH, et al. (2004) Microstructure dependence of stress corrosion cracking initiation in X65 pipeline steel exposed to a near-neutral pH soil environment. Corrosion 60: 275. doi: 10.5006/1.3287732
![]() |
[58] | Viktorovich RI, Esiev TS, Kohtev SA (2012) Improving methods of estimating the propensity of pipeline steels to stress corrosion cracking. Phys Chem Mater Processing 4: 88-93. (in Russian) |
[59] |
Cui Z, Liu Z, Wang L, et al. (2016) Effect of plastic deformation on the electrochemical and stress corrosion cracking behavior of X70 steel in near-neutral pH environment. Mater Sci Eng A 677: 259-273. doi: 10.1016/j.msea.2016.09.033
![]() |
[60] |
Wang Y, Zhao W, Ai H, et al (2011) Effects of strain on the corrosion behavior of X80 steel. Corros Sci 53: 2761-2766. doi: 10.1016/j.corsci.2011.05.011
![]() |
[61] | Talbot DEJ, Talbot JDR (1997) Corrosion science and technology, 1 Ed., Materials Science & Technology, New York: CRC-Press, 406. |
[62] |
Wang Y, Wharton JA, Shenoi RA (2016) Mechano-electrochemical modelling of corroded steel structures. Eng Struct 128: 1-14. doi: 10.1016/j.engstruct.2016.09.015
![]() |
[63] | Ren RK, Zhang S, Pang XL, et al. (2012) A novel observation of the interaction between the macroelastic stress and electrochemical corrosion of low carbon steel in 3.5 wt% NaCl solution. Electrochim Acta 85: 283-294. |
[64] |
Wu T, Yan M, Xu J, et al. (2016) Mechano-chemical effect of pipeline steel in microbiological corrosion. Corros Sci 108: 160-168. doi: 10.1016/j.corsci.2016.03.011
![]() |
[65] |
Zhao W, Zou Y, Xia DX, et al. (2015) Effects of anodic protection on SCC behavior of X80 pipeline steel in high-pH carbonate-bicarbonate solution. Arch Metall Mater 60: 1009-1013. doi: 10.1515/amm-2015-0251
![]() |
[66] |
Lu BT, Luo JL, Norton PR (2010) Environmentally assisted cracking mechanism of pipeline steel in near-neutral pH groundwater. Corros Sci 52: 1787-1795. doi: 10.1016/j.corsci.2010.02.020
![]() |
[67] |
Liu ZY, Wang XZ, Du CW, et al. (2016) Effect of hydrogen-induced plasticity on the stress corrosion cracking of X70 pipeline steel in simulated soil environments. Mater Sci Eng A 658: 348-354 doi: 10.1016/j.msea.2016.02.019
![]() |
[68] | Bueno AHS, Castro BB, Ponciano JAC (2008) Assessment of stress corrosion cracking and hydrogen embrittlement susceptibility of buried pipeline steels, In: Shipilov SA, Jones RH, Olive J-M, et al., Environment-Induced Cracking of Materials, 2 Eds., Elsevier, 2: 313-322. |
[69] | Perlovich YA, Ryakhovskikh IV, Isaenkova MG, et al. (2017) Correlation between the resistance to stress corrosion cracking of steel tubes of gas pipelines with their layerwise texture inhomogeneity. KnE Mater Sci 179-186. |
[70] | Arabey AB, Esiyev TS, Ryakhovskikh IV, et al. (2012) Influence of features of the pipe production technology on resistance to stress corrosion cracking during the operation of main gas pipelines. The Gas Industry, 2: 52-54. (in Russian) |
[71] | Beavers JA, Johnson JT, Sutherby RL (2000) Materials factors influencing the initiation of near-neutral pH SCC on underground pipelines. 2000 International Pipeline Conference 2: 979-998. |
[72] | Fang BY, Han EH, Wang JQ, et al. (2013) Stress corrosion cracking of X-70 pipeline steel in near neutral pH solution subjected to constant load and cyclic load testing. Corros Eng Sci Techn 42: 123-129. |
[73] |
Jia YZ, Wang JQ, Han EH, et al. (2011) Stress corrosion cracking of X80 pipeline steel in near-neutral pH environment under constant load tests with and without preload. J Mater Sci Techn 27: 1039-1046. doi: 10.1016/S1005-0302(11)60184-9
![]() |
[74] | Masoumi M, Abreu H (2015) Textural analysis through thickness of API X70 steel after hot rolling and post heat treatment. The Brazilian Materials & Mining Association, 52: 1-10. |
[75] | Pyshmintsev I, Gervasyev A, Petrov RH, et al. (2012) Crystallographic texture as a factor enabling ductile fracture arrest in high strength pipeline steel. Mater Sci Forum 702-703: 770-773. |
[76] | Lyakishev NP, Kantor ММ, Voronin VN et al. (2005) The study of the metal structure of gas pipelines after their long operation. Metally 1: 3-16. (In Russian) |
[77] |
Lu BT, Luo JL, Norton PR (2010) Environmentally assisted cracking mechanism of pipeline steel in near-neutral pH groundwater. Corros Sci 52: 1787-1795. doi: 10.1016/j.corsci.2010.02.020
![]() |
[78] | Elboujdaini M, Wang YZ, Revie RW, et al (2000) Stress corrosion crack initiation processes: pitting and microcrack coalescence. NACE-International Corrosion Conference Series, 00379. |
[79] |
Lu BT, Luo JL, Norton PR, et al. (2009) Effects of dissolved hydrogen and elastic and plastic deformation on active dissolution of pipeline steel in anaerobic groundwater of near-neutral pH. Acta Mater 57: 41-49. doi: 10.1016/j.actamat.2008.08.035
![]() |
[80] |
Tang X, Cheng YF (2011) Quantitative characterization by micro-electrochemical measurements of the synergism of hydrogen, stress and dissolution on near-neutral pH stress corrosion cracking of pipelines. Corros Sci 53: 2927-2933. doi: 10.1016/j.corsci.2011.05.032
![]() |
[81] |
Marshakov AI, Ignatenko VE, Bogdanov RI, et al. (2014) Effect of electrolyte composition on crack growth rate in pipeline steel. Corros Sci 83: 209-216. doi: 10.1016/j.corsci.2014.02.012
![]() |
[82] |
Egbewande A, Chen W, Eadie R, et al. (2014) Transgranular crack growth in the pipeline steels exposed to near-neutral pH soil aqueous solutions: discontinuous crack growth mechanism. Corros Sci 83: 343-354. doi: 10.1016/j.corsci.2014.02.032
![]() |
[83] |
Chen W, Kania R, Worthingham R, et al. (2009) Transgranular crack growth in the pipeline steels exposed to near-neutral pH soil aqueous solutions: the role of hydrogen. Acta Mater 57: 6200-6214. doi: 10.1016/j.actamat.2009.08.047
![]() |
[84] |
Asher SL, Singh PM (2009) Role of stress in transgranular stress corrosion cracking of transmission pipelines in near-neutral pH environments. Corrosion 65: 79-87. doi: 10.5006/1.3319122
![]() |
[85] |
Lu BT, Luo JL, Norton PR (2010) Environmentally assisted cracking mechanism of pipeline steel in near-neutral pH groundwater. Corros Sci 52: 1787-1795. doi: 10.1016/j.corsci.2010.02.020
![]() |
[86] |
Wang R (2009) Effects of hydrogen on the fracture toughness of a X70 pipeline steel. Corros Sci 51: 2803-2810. doi: 10.1016/j.corsci.2009.07.013
![]() |
[87] |
Kang Y, Chen W, Kania R, et al. (2011) Simulation of crack growth during hydrostatic testing of pipeline steel in near-neutral pH environment. Corros Sci 53: 968-975. doi: 10.1016/j.corsci.2010.11.029
![]() |
[88] |
Chu WY, Hsiao CM, Li SQ (1979) Hydrogen induced delayed plasticity and cracking. Scr Metall 13: 1063-1068. doi: 10.1016/0036-9748(79)90204-7
![]() |
[89] |
Robertson IM, Birnbaum HK (1986) An HVEM study of hydrogen effects on the deformation and fracture of nickel. Acta metall 34: 353-366. doi: 10.1016/0001-6160(86)90071-4
![]() |
[90] |
Rozenak P, Robertson IM, Birnbaum HK (1990) HVEM studies of the effects of hydrogen on the deformation and fracture of AISI type 316 austenitic stainless steel. Acta Metall Mater 38: 2031-2040. doi: 10.1016/0956-7151(90)90070-W
![]() |
[91] |
Delafosse D, Magnin T (2001) Hydrogen induced plasticity in stress corrosion cracking of engineering systems. Eng Fract Mech 68: 693-729. doi: 10.1016/S0013-7944(00)00121-1
![]() |
[92] | Lu BT, Luo JL (2008) A mechanistic study on near-neutral pH stress corrosion cracking of pipeline steel, In: Shipilov SA, Jones RH, Olive J-M, et al., Environment-Induced Cracking of Materials, Elsevier, 2: 243-253. |
[93] | Lynch SP (2008) Towards understanding the mechanisms and kinetics of environmentally assisted cracking, In: Shipilov SA, Jones RH, Olive J-M, et al., Environment-Induced Cracking of Materials, Elsevier, 1: 167. |
[94] | Kishore R (2009) Effect of hydrogen on the creep behavior of Zr-2.5% Nb alloy at 723K. J Nucl Mater 385: 591-594. |
[95] |
Barnoush A, Zamanzade M, Vehoff H (2010) Direct observation of hydrogen-enhanced plasticity in super duplex stainless steel by means of in situ electrochemical methods. Scr Mater 62: 242-245. doi: 10.1016/j.scriptamat.2009.11.007
![]() |
[96] |
Dmytrakh IM, Leshchak RL, Syrotyuk AM, et al. (2017) Effect of hydrogen concentration on fatigue crack growth behaviour in pipeline steel. Int J Hydrogen Energ 42: 6401-6408. doi: 10.1016/j.ijhydene.2016.11.193
![]() |
[97] | Delafosse D, Bayle B, Bosch C (2008) The roles of crack-tip plasticity, anodic dissolution and hydrogen in SCC of mild and C-Mn steels. In: Shipilov SA, Jones RH, Olive J-M, et al., Environment-Induced Cracking of Metals, Elsevier, 2: 267-278. |
[98] | Been J, King F, Sutherby RL (2008) Environmentally assisted cracking of pipeline steels in near-neutral pH environments. In: Shipilov SA, Jones RH, Olive J-M, et al., Environment-Induced Cracking of Metals, Elsevier, 2: 221-230. |
[99] |
Niu L, Cheng YF (2007) Corrosion behavior of X-70 pipe steel in near-neutral pH solution. Appl Surf Sci 253: 8626-8631. doi: 10.1016/j.apsusc.2007.04.066
![]() |
[100] |
Flis J, Zakroczymski T (1992) Enhanced hydrogen entry in iron at low anodic and low cathodic polarizations in neutral and alkaline solutions. Corrosion 48: 530-539. doi: 10.5006/1.3315970
![]() |
[101] | King F, Jack T, Chen W, et al. (2000) Mechanistic studies of initiation and early stage crack growth for near-neutral pH SCC on pipelines. NACE-International Corrosion Conference Series, 00361. |
[102] |
Li MC, Cheng YF (2007) Mechanistic investigation of hydrogen-enhanced anodic dissolution of X-70 pipe steel and its implication on near-neutral pH SCC of pipelines. Electrochim Acta 52: 8111-8117. doi: 10.1016/j.electacta.2007.07.015
![]() |
[103] |
Qiao L, Mao X (1995) Thermodynamic analysis on the role of hydrogen in anodic stress corrosion cracking. Acta Metall Mater 43: 4001-4006. doi: 10.1016/0956-7151(95)00090-I
![]() |
[104] |
Qiao LJ, Luo JL, Mao X (1997) The role of hydrogen in the process of stress corrosion cracking of pipeline steels in dilute carbonate-bicarbonate solution. J Mater Sci Lett 16: 516-520. doi: 10.1023/A:1018541116291
![]() |
[105] |
Mao SX, Li M (1998) Mechanics and thermodynamics on the stress and hydrogen interaction in crack tip stress corrosion: experiment and theory. J Mech Phys Solids 46:1125-1137. doi: 10.1016/S0022-5096(97)00054-9
![]() |
[106] |
Gu B, Luo J, Mao X (1999) Hydrogen-facilitated anodic dissolution-type stress corrosion cracking of pipeline steels in near-neutral pH solution. Corrosion 55: 96-106. doi: 10.5006/1.3283971
![]() |
[107] |
Marshakov AI, Maleeva МА, Rybkina AA et al. (2010) Effect of atomic hydrogen on the anodic dissolution of iron in a weakly acidic sulfate electrolyte. Prot Met Phys Chem 46: 40-49. doi: 10.1134/S2070205110010053
![]() |
[108] | Ignatenko VE, Marshakov AI, Marichev VA, et al. (2000) Effect of cathodic polarization on the corrosion cracking rate in pipe steels. Prot Met Phys Chem 36: 111-117. |
[109] | Mikhailovsky YuN, Marshakov AI, Ignatenko VE et al. (2000) Estimation of the probability of hydrogen embrittlement of steel gas pipelines in the action areas of cathode stations. Prot Met Phys Chem 36: 140-145. |
[110] |
Ignatenko VE, Kuznetsov YuI, Arabei AB, et al. (2013) Application of SSRT to estimate the effect of corrosive medium on the liability of X70 pipe steel to stress corrosion cracking. Int J Corros Scale Inhib 2: 318-336. doi: 10.17675/2305-6894-2013-2-4-318-336
![]() |
[111] | Bogdanov RI (2013) Regularities of stress corrosion cracking of a X70 pipe steel in near-neutral pH ground electrolytes [PhD's thesis]. A.N. Frumkina RAS, Moscow, 201. (in Russian) |
[112] |
Marshakov AI, Ignatenko VE, Bogdanov RI, et al. (2014) Effect of electrolyte composition on crack growth rate in pipeline steel. Corros Sci 83: 209-216. doi: 10.1016/j.corsci.2014.02.012
![]() |
[113] |
Arabey AB, Bogdanov RI, Ignatenko VE, et al. (2011) Effect of corrosion medium composition on rate of crack growth in X70 pipeline steel. Prot Met Phys Chem 47: 236-244. doi: 10.1134/S2070205111020031
![]() |
[114] | Bogdanov RI, Marshakov AI, Ignatenko VE (2011) Effect of solution composition on crack growth rate in X70 pipeline steel under static and cyclic loading. Corros Mater Prot 11: 30-38 (In Russian) |
[115] | Ryakhovskikh IV, Bogdanov RI, Esiev TS, et al. (2014) Stress corrosion cracking of pipeline steel in near-neutral pH environment. Materials Science and Technology Conference and Exhibition, 2: 807-814. |
[116] |
Bogdanov RI, Marshakov AI, Ignatenko VE, et al. (2017) Effect of hydrogen peroxide on crack growth rate in X70 pipeline steel in weak acid solution. Corros Eng Sci Techn 52: 294-301. doi: 10.1080/1478422X.2016.1277315
![]() |
[117] | Yang Y, Cheng YF (2016) Stress enhanced corrosion at the tip of near-neutral pH stress corrosion cracks on pipelines. Corrosion 72: 1035-1043. |
[118] |
Tang X, Cheng YF (2009) Micro-electrochemical characterization of the effect of applied stress on local anodic dissolution behavior of pipeline steel under near-neutral pH condition. Electrochim Acta 54: 1499-1505. doi: 10.1016/j.electacta.2008.09.037
![]() |
[119] | Malkin AI, Marshakov AI, Ignatenko VE, et al. (2010) Processes of crack initiation and propagation on the steels of main pipelines. Part II. The kinetics of crack growth and environmental effects on SCC of pipeline steels in aqueous media. Corros Mater Prot 2: 1-11. |
[120] | Zhao W, Xin R, He Z, et al. (2012) Contribution of anodic dissolution to the corrosion fatigue crack propagation of X80 steel in 3.5 wt% NaCl solution. Corros Sci 63: 387-392. |
[121] |
Cui ZY, Liu ZY, Wang XZ, et al. (2016) Crack growth behaviour and crack tip chemistry of X70 pipeline steel in near-neutral pH environment. Corros Eng Sci Techn 51: 352-357. doi: 10.1080/1478422X.2015.1110963
![]() |
1. | Xueli Chen, Jiafu Su, Dynamical Systems of Differential Equations Based on Information Technology: Effects of Integral Step Size on Bifurcation and Chaos Control of Discrete Hindmarsh–Rose Models, 2022, 2022, 1875-905X, 1, 10.1155/2022/1425403 | |
2. | Abdul Qadeer Khan, Leonid Shaikhet, Global Dynamics of a Nonsymmetric System of Difference Equations, 2022, 2022, 1563-5147, 1, 10.1155/2022/4435613 | |
3. | Leonid Shaikhet, Stability of the Exponential Type System of Stochastic Difference Equations, 2023, 11, 2227-7390, 3975, 10.3390/math11183975 | |
4. | Sevda Atpinar, Yasin Yazlik, Qualitative behavior of exponential type of fuzzy difference equations system, 2023, 69, 1598-5865, 4135, 10.1007/s12190-023-01919-y | |
5. | Merve Kara, Investigation of the global dynamics of two exponential-form difference equations systems, 2023, 31, 2688-1594, 6697, 10.3934/era.2023338 | |
6. | Hashem Althagafi, Ahmed Ghezal, Global Stability of a System of Fuzzy Difference Equations of Higher-Order, 2024, 1598-5865, 10.1007/s12190-024-02302-1 | |
7. | Leonid Shaikhet, About stability of equilibria of one system of stochastic delay differential equations with exponential nonlinearity, 2025, 2351-6046, 1, 10.15559/25-VMSTA274 | |
8. | Merve Kara, Yasin Yazlik, Global dynamics of the system of difference equations , 2025, 75, 0139-9918, 339, 10.1515/ms-2025-0026 |
Specimen | Nominal sectional dimension | Measured sectional dimension | initial imperfection Δmax/mm | |||||||||
L/mm | h/mm | b/mm | a/mm | t/mm | L/mm | h/mm | b1/mm | b2/mm | a1/mm | a2/mm | ||
C8008-05-NH-1 | 500 | 80 | 60 | 10 | 0.80 | 499.45 | 76.61 | 58.89 | 59.19 | 10.13 | 10.49 | 1.251 |
C8008-05-NH-2 | 499.55 | 78.77 | 58.93 | 58.88 | 10.17 | 9.85 | 1.124 | |||||
C8008-05-RH21-1 | 499.40 | 79.13 | 58.82 | 59.87 | 10.05 | 10.02 | 0.876 | |||||
C8008-05-RH21-2 | 499.35 | 77.11 | 58.72 | 60.14 | 9.22 | 9.79 | 0.752 | |||||
C8008-05-RH41-1 | 499.15 | 77.20 | 60.11 | 58.88 | 9.59 | 9.42 | 0.641 | |||||
C8008-05-RH41-2 | 499.50 | 79.18 | 59.58 | 59.38 | 10.07 | 9.95 | 0.521 | |||||
C8008-05-RH61-1 | 499.25 | 78.35 | 59.94 | 59.88 | 9.54 | 9.52 | 0.981 | |||||
C8008-05-RH61-2 | 499.35 | 77.69 | 60.26 | 59.29 | 10.32 | 9.46 | 1.141 | |||||
C10010-05-NH-1 | 500 | 100 | 90 | 10 | 1.00 | 474.15 | 99.25 | 90.05 | 89.19 | 9.04 | 8.83 | 0.825 |
C10010-05-NH-2 | 499.55 | 97.97 | 89.13 | 89.14 | 9.56 | 9.98 | 1.028 | |||||
C10010-05-RH21-1 | 499.40 | 97.70 | 90.04 | 89.27 | 9.65 | 9.23 | 1.254 | |||||
C10010-05-RH21-2 | 499.45 | 99.27 | 89.62 | 89.61 | 9.58 | 9.16 | 1.158 | |||||
C10010-05-RH41-1 | 499.50 | 99.37 | 89.58 | 90.02 | 9.32 | 9.24 | 1.345 | |||||
C10010-05-RH41-2 | 499.20 | 98.18 | 89.23 | 88.71 | 9.78 | 9.43 | 1.429 | |||||
C10010-05-RH61-1 | 499.40 | 96.75 | 89.80 | 89.81 | 9.34 | 9.39 | 0.988 | |||||
C10010-05-RH61-2 | 499.20 | 98.21 | 89.44 | 88.78 | 9.64 | 9.49 | 1.024 | |||||
C8008-10-NH-1 | 1000 | 80 | 60 | 10 | 0.8 | 1000.00 | 79.31 | 58.98 | 58.78 | 9.87 | 10.41 | 0.812 |
C8008-10-NH-2 | 1000.20 | 79.57 | 58.89 | 59.06 | 10.26 | 9.76 | 0.988 | |||||
C8008-10-RH21-1 | 999.80 | 79.23 | 59.40 | 59.61 | 10.03 | 9.91 | 0.841 | |||||
C8008-10-RH21-2 | 999.95 | 78.87 | 59.60 | 59.66 | 9.66 | 10.11 | 0.754 | |||||
C8008-10-RH41-1 | 1000.00 | 79.64 | 59.57 | 59.09 | 9.47 | 9.56 | 0.684 | |||||
C8008-10-RH41-2 | 1000.10 | 79.36 | 59.52 | 59.39 | 9.98 | 9.25 | 0.751 | |||||
C8008-10-RH61-1 | 999.90 | 78.50 | 60.12 | 59.54 | 9.80 | 9.60 | 1.042 | |||||
C8008-10-RH61-2 | 1000.10 | 78.58 | 59.78 | 59.36 | 9.81 | 9.93 | 0.985 | |||||
C8008-10-RH22-1 | 999.05 | 78.68 | 59.93 | 59.41 | 9.83 | 9.61 | 1.451 | |||||
C8008-10-RH22-2 | 999.95 | 79.23 | 59.58 | 58.90 | 10.19 | 9.68 | 1.345 | |||||
C8008-10-RH42-1 | 999.85 | 79.55 | 58.79 | 59.70 | 9.51 | 10.10 | 1.231 | |||||
C8008-10-RH42-2 | 1000.00 | 78.78 | 60.17 | 59.49 | 9.65 | 9.50 | 1.012 | |||||
C8008-10-RH62-1 | 999.70 | 79.38 | 59.43 | 59.39 | 9.69 | 9.80 | 0.984 | |||||
C8008-10-RH62-2 | 999.95 | 78.67 | 58.99 | 57.80 | 11.50 | 10.37 | 0.756 | |||||
C10010-10-NH-1 | 1000 | 100 | 90 | 10 | 1 | 999.00 | 98.97 | 88.95 | 88.44 | 9.29 | 9.83 | 0.852 |
C10010-10-NH-2 | 999.00 | 98.45 | 89.72 | 89.08 | 8.75 | 9.76 | 0.734 | |||||
C10010-10-RH21-1 | 1000.00 | 99.83 | 87.83 | 89.02 | 8.92 | 9.38 | 1.102 | |||||
C10010-10-RH21-2 | 999.50 | 99.73 | 88.45 | 89.15 | 9.02 | 9.34 | 1.034 | |||||
C10010-10-RH41-1 | 999.50 | 99.56 | 89.18 | 89.35 | 8.79 | 9.19 | 0.614 | |||||
C10010-10-RH41-2 | 1000.00 | 99.85 | 88.67 | 89.06 | 8.87 | 9.09 | 0.785 | |||||
C10010-10-RH61-1 | 1001.00 | 99.13 | 89.35 | 89.04 | 9.37 | 9.26 | 0.635 | |||||
C10010-10-RH61-2 | 1000.25 | 98.89 | 88.85 | 89.32 | 9.76 | 9.35 | 0.564 | |||||
C10010-10-RH22-1 | 1001.00 | 99.34 | 88.50 | 87.93 | 9.51 | 9.11 | 0.645 | |||||
C10010-10-RH22-2 | 1000.00 | 99.58 | 88.93 | 88.26 | 9.23 | 10.09 | 0.451 | |||||
C10010-10-RH42-1 | 999.90 | 99.18 | 89.34 | 88.51 | 10.15 | 9.29 | 0.845 | |||||
C10010-10-RH42-2 | 1000.00 | 98.92 | 88.75 | 88.74 | 9.23 | 9.23 | 0.684 | |||||
C10010-10-RH62-1 | 1000.00 | 98.41 | 89.34 | 89.01 | 9.91 | 10.06 | 0.945 | |||||
C10010-10-RH62-2 | 1000.00 | 98.50 | 89.65 | 89.11 | 9.89 | 9.27 | 0.863 |
t/mm | f0.2/MPa | fu/MPa | E/MPa | εu/% |
0.80 | 600 | 602 | 2.16 × 105 | 7.19 |
1.00 | 620 | 634 | 2.15 × 105 | 8.92 |
Specimen | Test buckling mode | FEA buckling mode | Pt/KN | Reduction in capacity /% | Pa/KN | Pc | Pt/Pa | Pt/Pc |
C8008-05-NH-1 | L + D | L + D | 34.38 | 35.44 | 34.04 | 0.97 | 1.01 | |
C8008-05-NH-2 | L + D | L + D | 35.97 | 36.33 | 34.17 | 0.99 | 1.05 | |
C8008-05-RH21-1 | L + D | L + D | 34.55 | 1.78 | 34.9 | 32.48 | 0.99 | 1.06 |
C8008-05-RH21-2 | L + D | L + D | 34.4 | 2.2 | 34.77 | 32.06 | 0.99 | 1.07 |
C8008-05-RH41-1 | L + D | L + D | 33.3 | 5.33 | 33.64 | 30.97 | 0.99 | 1.08 |
C8008-05-RH41-2 | L + D | L + D | 33.91 | 3.6 | 34.1 | 30.29 | 0.99 | 1.12 |
C8008-05-RH61-1 | L + D | L + D | 29.91 | 14.97 | 31.82 | 29.01 | 0.94 | 1.03 |
C8008-05-RH61-2 | L + D | L + D | 29.45 | 16.28 | 31.1 | 28.97 | 0.95 | 1.02 |
C10010-05-NH-1 | D | D | 52.31 | 53.7 | 49.98 | 0.97 | 1.05 | |
C10010-05-NH-2 | D | D | 52.48 | 54.67 | 49.86 | 0.96 | 1.05 | |
C10010-05-RH21-1 | D | D | 51.95 | 0.85 | 53.01 | 48.83 | 0.98 | 1.06 |
C10010-05-RH21-2 | D | D | 51.48 | 1.75 | 52.53 | 48.91 | 0.98 | 1.05 |
C10010-05-RH41-1 | D | D | 51.1 | 2.48 | 53.23 | 48.03 | 0.96 | 1.06 |
C10010-05-RH41-2 | D | D | 50.22 | 4.16 | 51.77 | 48.21 | 0.97 | 1.04 |
C10010-05-RH61-1 | D | D | 46.19 | 11.85 | 49.14 | 42.96 | 0.94 | 1.08 |
C10010-05-RH61-2 | D | D | 44.12 | 15.8 | 45.96 | 43.24 | 0.96 | 1.02 |
C8008-10-NH-1 | L + D | L + D | 27.52 | 28.3 | 26.42 | 0.97 | 1.04 | |
C8008-10-NH-2 | L + D | L + D | 27.85 | 28.3 | 26.4 | 0.98 | 1.05 | |
C8008-10-RH21-1 | L + D | L + D | 27.5 | 0.6 | 28 | 25.87 | 0.98 | 1.06 |
C8008-10-RH21-2 | L + D | L + D | 27.74 | -0.2 | 27.91 | 25.83 | 0.99 | 1.07 |
C8008-10-RH41-1 | L + D | L + D | 26.94 | 2.6 | 26.28 | 24.06 | 1.03 | 1.12 |
C8008-10-RH41-2 | L + D | L + D | 26.33 | 4.8 | 25.99 | 24.15 | 1.01 | 1.09 |
C8008-10-RH61-1 | L + D | L + D | 23.8 | 13.9 | 24.2 | 22.73 | 0.98 | 1.05 |
C8008-10-RH61-2 | L + D | L + D | 23.88 | 13.7 | 23.99 | 22.89 | 1.00 | 1.04 |
C8008-10-RH22-1 | L + D | L + D | 27.6 | 0.25 | 27.25 | 25.53 | 1.01 | 1.08 |
C8008-10-RH22-2 | L + D | L + D | -- | -- | 27.79 | 25.69 | -- | -- |
C8008-10-RH42-1 | L + D | L + D | 26.52 | 4.2 | 26.05 | 23.91 | 1.02 | 1.11 |
C8008-10-RH42-2 | L + D | L + D | -- | -- | 26.5 | 23.6 | -- | -- |
C8008-10-RH62-1 | L + D | L + D | 23.5 | 15.1 | 24.02 | 22.45 | 0.98 | 1.05 |
C8008-10-RH62-2 | L + D | L + D | -- | -- | 23.42 | 22.66 | -- | -- |
C10010-10-NH-1 | L + D | L + D | 41.7 | 41.29 | 41.31 | 1.01 | 1.01 | |
C10010-10-NH-2 | L + D | L + D | 39.6 | 40.58 | 40.73 | 0.98 | 0.97 | |
C10010-10-RH21-1 | L + D | L + D | 40.1 | 1.3 | 40.62 | 39.64 | 0.99 | 1.01 |
C10010-10-RH21-2 | L + D | L + D | 40.95 | -0.74 | 40.65 | 39.68 | 1.01 | 1.03 |
C10010-10-RH41-1 | L + D | L + D | 39.38 | 3.1 | 39.9 | 36.79 | 0.99 | 1.07 |
C10010-10-RH41-2 | L + D | L + D | 39.4 | 3.1 | 39.26 | 36.71 | 1.00 | 1.07 |
C10010-10-RH61-1 | L + D | L + D | 37.3 | 8.2 | 36.51 | 35.52 | 1.02 | 1.05 |
C10010-10-RH61-2 | L + D | L + D | 37.66 | 7.4 | 36.1 | 35.83 | 1.04 | 1.05 |
C10010-10-RH22-1 | L + D | L + D | 40.25 | 0.98 | 39.99 | 39.55 | 1.01 | 1.02 |
C10010-10-RH22-2 | L + D | L + D | -- | -- | 40.52 | 40.15 | -- | -- |
C10010-10-RH42-1 | L + D | L + D | 38.45 | 5.4 | 38.88 | 37.16 | 0.99 | 1.03 |
C10010-10-RH42-2 | L + D | L + D | 38.7 | 4.8 | 38.46 | 37.52 | 1.01 | 1.03 |
C10010-10-RH62-1 | L + D | L + D | 36.8 | 9.5 | 36.36 | 36.08 | 1.01 | 1.02 |
C10010-10-RH62-2 | L + D | L + D | 37.05 | 8.9 | 36.87 | 35.94 | 1.00 | 1.03 |
Average | 0.99 | 1.05 | ||||||
Standard deviation | 0.0005 | 0.0009 | ||||||
Variable coefficient | 0.023 | 0.029 |
h/mm | b/mm | a/mm | t/mm | fy/MPa | L/mm | Hh/mm | Lh/mm | The number of holes | Hole spacing S/mm | Buckling mode | Pa/kN | Pc/kN | Pa/Pc |
89 | 41 | 13 | 1 | 280 | 1000 | 0 | 0 | 0 | - | L | 36.5 | 34.2 | 1.07 |
89 | 41 | 13 | 1 | 280 | 1000 | 26.7 | 26.7 | 1 | - | L + D | 35.8 | 33.4 | 1.07 |
89 | 41 | 13 | 1 | 280 | 1000 | 44.5 | 44.5 | 1 | - | L + D | 33.9 | 31 | 1.09 |
89 | 41 | 13 | 1 | 280 | 1500 | 62.3 | 62.3 | 1 | - | L+ D | 29.8 | 27.8 | 1.07 |
89 | 41 | 13 | 1 | 280 | 1500 | 0 | 0 | 0 | - | L + G | 34.3 | 31.4 | 1.09 |
89 | 41 | 13 | 1 | 280 | 1500 | 26.7 | 26.7 | 3 | 500 | L + G | 33.2 | 30.8 | 1.08 |
89 | 41 | 13 | 1 | 280 | 1500 | 44.5 | 44.5 | 3 | 500 | L+D+G | 30.8 | 28.4 | 1.08 |
89 | 41 | 13 | 1 | 280 | 1500 | 62.3 | 62.3 | 3 | 500 | L+D+G | 27.5 | 25.2 | 1.09 |
75 | 40 | 8 | 1 | 550 | 1000 | 0 | 0 | 0 | - | L + D | 43.2 | 41 | 1.05 |
75 | 40 | 8 | 1 | 550 | 1000 | 22.5 | 22.5 | 1 | - | L + D | 42.3 | 40.5 | 1.04 |
75 | 40 | 8 | 1 | 550 | 1000 | 37.5 | 37.5 | 1 | - | L + D | 39.7 | 37.8 | 1.05 |
75 | 40 | 8 | 1 | 550 | 1500 | 52.5 | 52.5 | 1 | - | L+D+G | 36.1 | 33.5 | 1.08 |
75 | 40 | 8 | 1 | 550 | 1500 | 0 | 0 | 0 | - | L+D+G | 35.3 | 32.6 | 1.08 |
75 | 40 | 8 | 1 | 550 | 1500 | 22.5 | 22.5 | 3 | 500 | L+D+G | 34.4 | 32.2 | 1.07 |
75 | 40 | 8 | 1 | 550 | 1500 | 37.5 | 37.5 | 3 | 500 | L+D+G | 30.9 | 28.5 | 1.08 |
75 | 40 | 8 | 1 | 550 | 1500 | 52.5 | 52.5 | 3 | 500 | L+D+G | 27.3 | 25.1 | 1.09 |
Mean value | 1.07 | ||||||||||||
Standard deviation | 0.0002 | ||||||||||||
Coefficient of variable | 0.014 |
Specimen | Nominal sectional dimension | Measured sectional dimension | initial imperfection Δmax/mm | |||||||||
L/mm | h/mm | b/mm | a/mm | t/mm | L/mm | h/mm | b1/mm | b2/mm | a1/mm | a2/mm | ||
C8008-05-NH-1 | 500 | 80 | 60 | 10 | 0.80 | 499.45 | 76.61 | 58.89 | 59.19 | 10.13 | 10.49 | 1.251 |
C8008-05-NH-2 | 499.55 | 78.77 | 58.93 | 58.88 | 10.17 | 9.85 | 1.124 | |||||
C8008-05-RH21-1 | 499.40 | 79.13 | 58.82 | 59.87 | 10.05 | 10.02 | 0.876 | |||||
C8008-05-RH21-2 | 499.35 | 77.11 | 58.72 | 60.14 | 9.22 | 9.79 | 0.752 | |||||
C8008-05-RH41-1 | 499.15 | 77.20 | 60.11 | 58.88 | 9.59 | 9.42 | 0.641 | |||||
C8008-05-RH41-2 | 499.50 | 79.18 | 59.58 | 59.38 | 10.07 | 9.95 | 0.521 | |||||
C8008-05-RH61-1 | 499.25 | 78.35 | 59.94 | 59.88 | 9.54 | 9.52 | 0.981 | |||||
C8008-05-RH61-2 | 499.35 | 77.69 | 60.26 | 59.29 | 10.32 | 9.46 | 1.141 | |||||
C10010-05-NH-1 | 500 | 100 | 90 | 10 | 1.00 | 474.15 | 99.25 | 90.05 | 89.19 | 9.04 | 8.83 | 0.825 |
C10010-05-NH-2 | 499.55 | 97.97 | 89.13 | 89.14 | 9.56 | 9.98 | 1.028 | |||||
C10010-05-RH21-1 | 499.40 | 97.70 | 90.04 | 89.27 | 9.65 | 9.23 | 1.254 | |||||
C10010-05-RH21-2 | 499.45 | 99.27 | 89.62 | 89.61 | 9.58 | 9.16 | 1.158 | |||||
C10010-05-RH41-1 | 499.50 | 99.37 | 89.58 | 90.02 | 9.32 | 9.24 | 1.345 | |||||
C10010-05-RH41-2 | 499.20 | 98.18 | 89.23 | 88.71 | 9.78 | 9.43 | 1.429 | |||||
C10010-05-RH61-1 | 499.40 | 96.75 | 89.80 | 89.81 | 9.34 | 9.39 | 0.988 | |||||
C10010-05-RH61-2 | 499.20 | 98.21 | 89.44 | 88.78 | 9.64 | 9.49 | 1.024 | |||||
C8008-10-NH-1 | 1000 | 80 | 60 | 10 | 0.8 | 1000.00 | 79.31 | 58.98 | 58.78 | 9.87 | 10.41 | 0.812 |
C8008-10-NH-2 | 1000.20 | 79.57 | 58.89 | 59.06 | 10.26 | 9.76 | 0.988 | |||||
C8008-10-RH21-1 | 999.80 | 79.23 | 59.40 | 59.61 | 10.03 | 9.91 | 0.841 | |||||
C8008-10-RH21-2 | 999.95 | 78.87 | 59.60 | 59.66 | 9.66 | 10.11 | 0.754 | |||||
C8008-10-RH41-1 | 1000.00 | 79.64 | 59.57 | 59.09 | 9.47 | 9.56 | 0.684 | |||||
C8008-10-RH41-2 | 1000.10 | 79.36 | 59.52 | 59.39 | 9.98 | 9.25 | 0.751 | |||||
C8008-10-RH61-1 | 999.90 | 78.50 | 60.12 | 59.54 | 9.80 | 9.60 | 1.042 | |||||
C8008-10-RH61-2 | 1000.10 | 78.58 | 59.78 | 59.36 | 9.81 | 9.93 | 0.985 | |||||
C8008-10-RH22-1 | 999.05 | 78.68 | 59.93 | 59.41 | 9.83 | 9.61 | 1.451 | |||||
C8008-10-RH22-2 | 999.95 | 79.23 | 59.58 | 58.90 | 10.19 | 9.68 | 1.345 | |||||
C8008-10-RH42-1 | 999.85 | 79.55 | 58.79 | 59.70 | 9.51 | 10.10 | 1.231 | |||||
C8008-10-RH42-2 | 1000.00 | 78.78 | 60.17 | 59.49 | 9.65 | 9.50 | 1.012 | |||||
C8008-10-RH62-1 | 999.70 | 79.38 | 59.43 | 59.39 | 9.69 | 9.80 | 0.984 | |||||
C8008-10-RH62-2 | 999.95 | 78.67 | 58.99 | 57.80 | 11.50 | 10.37 | 0.756 | |||||
C10010-10-NH-1 | 1000 | 100 | 90 | 10 | 1 | 999.00 | 98.97 | 88.95 | 88.44 | 9.29 | 9.83 | 0.852 |
C10010-10-NH-2 | 999.00 | 98.45 | 89.72 | 89.08 | 8.75 | 9.76 | 0.734 | |||||
C10010-10-RH21-1 | 1000.00 | 99.83 | 87.83 | 89.02 | 8.92 | 9.38 | 1.102 | |||||
C10010-10-RH21-2 | 999.50 | 99.73 | 88.45 | 89.15 | 9.02 | 9.34 | 1.034 | |||||
C10010-10-RH41-1 | 999.50 | 99.56 | 89.18 | 89.35 | 8.79 | 9.19 | 0.614 | |||||
C10010-10-RH41-2 | 1000.00 | 99.85 | 88.67 | 89.06 | 8.87 | 9.09 | 0.785 | |||||
C10010-10-RH61-1 | 1001.00 | 99.13 | 89.35 | 89.04 | 9.37 | 9.26 | 0.635 | |||||
C10010-10-RH61-2 | 1000.25 | 98.89 | 88.85 | 89.32 | 9.76 | 9.35 | 0.564 | |||||
C10010-10-RH22-1 | 1001.00 | 99.34 | 88.50 | 87.93 | 9.51 | 9.11 | 0.645 | |||||
C10010-10-RH22-2 | 1000.00 | 99.58 | 88.93 | 88.26 | 9.23 | 10.09 | 0.451 | |||||
C10010-10-RH42-1 | 999.90 | 99.18 | 89.34 | 88.51 | 10.15 | 9.29 | 0.845 | |||||
C10010-10-RH42-2 | 1000.00 | 98.92 | 88.75 | 88.74 | 9.23 | 9.23 | 0.684 | |||||
C10010-10-RH62-1 | 1000.00 | 98.41 | 89.34 | 89.01 | 9.91 | 10.06 | 0.945 | |||||
C10010-10-RH62-2 | 1000.00 | 98.50 | 89.65 | 89.11 | 9.89 | 9.27 | 0.863 |
t/mm | f0.2/MPa | fu/MPa | E/MPa | εu/% |
0.80 | 600 | 602 | 2.16 × 105 | 7.19 |
1.00 | 620 | 634 | 2.15 × 105 | 8.92 |
Specimen | Test buckling mode | FEA buckling mode | Pt/KN | Reduction in capacity /% | Pa/KN | Pc | Pt/Pa | Pt/Pc |
C8008-05-NH-1 | L + D | L + D | 34.38 | 35.44 | 34.04 | 0.97 | 1.01 | |
C8008-05-NH-2 | L + D | L + D | 35.97 | 36.33 | 34.17 | 0.99 | 1.05 | |
C8008-05-RH21-1 | L + D | L + D | 34.55 | 1.78 | 34.9 | 32.48 | 0.99 | 1.06 |
C8008-05-RH21-2 | L + D | L + D | 34.4 | 2.2 | 34.77 | 32.06 | 0.99 | 1.07 |
C8008-05-RH41-1 | L + D | L + D | 33.3 | 5.33 | 33.64 | 30.97 | 0.99 | 1.08 |
C8008-05-RH41-2 | L + D | L + D | 33.91 | 3.6 | 34.1 | 30.29 | 0.99 | 1.12 |
C8008-05-RH61-1 | L + D | L + D | 29.91 | 14.97 | 31.82 | 29.01 | 0.94 | 1.03 |
C8008-05-RH61-2 | L + D | L + D | 29.45 | 16.28 | 31.1 | 28.97 | 0.95 | 1.02 |
C10010-05-NH-1 | D | D | 52.31 | 53.7 | 49.98 | 0.97 | 1.05 | |
C10010-05-NH-2 | D | D | 52.48 | 54.67 | 49.86 | 0.96 | 1.05 | |
C10010-05-RH21-1 | D | D | 51.95 | 0.85 | 53.01 | 48.83 | 0.98 | 1.06 |
C10010-05-RH21-2 | D | D | 51.48 | 1.75 | 52.53 | 48.91 | 0.98 | 1.05 |
C10010-05-RH41-1 | D | D | 51.1 | 2.48 | 53.23 | 48.03 | 0.96 | 1.06 |
C10010-05-RH41-2 | D | D | 50.22 | 4.16 | 51.77 | 48.21 | 0.97 | 1.04 |
C10010-05-RH61-1 | D | D | 46.19 | 11.85 | 49.14 | 42.96 | 0.94 | 1.08 |
C10010-05-RH61-2 | D | D | 44.12 | 15.8 | 45.96 | 43.24 | 0.96 | 1.02 |
C8008-10-NH-1 | L + D | L + D | 27.52 | 28.3 | 26.42 | 0.97 | 1.04 | |
C8008-10-NH-2 | L + D | L + D | 27.85 | 28.3 | 26.4 | 0.98 | 1.05 | |
C8008-10-RH21-1 | L + D | L + D | 27.5 | 0.6 | 28 | 25.87 | 0.98 | 1.06 |
C8008-10-RH21-2 | L + D | L + D | 27.74 | -0.2 | 27.91 | 25.83 | 0.99 | 1.07 |
C8008-10-RH41-1 | L + D | L + D | 26.94 | 2.6 | 26.28 | 24.06 | 1.03 | 1.12 |
C8008-10-RH41-2 | L + D | L + D | 26.33 | 4.8 | 25.99 | 24.15 | 1.01 | 1.09 |
C8008-10-RH61-1 | L + D | L + D | 23.8 | 13.9 | 24.2 | 22.73 | 0.98 | 1.05 |
C8008-10-RH61-2 | L + D | L + D | 23.88 | 13.7 | 23.99 | 22.89 | 1.00 | 1.04 |
C8008-10-RH22-1 | L + D | L + D | 27.6 | 0.25 | 27.25 | 25.53 | 1.01 | 1.08 |
C8008-10-RH22-2 | L + D | L + D | -- | -- | 27.79 | 25.69 | -- | -- |
C8008-10-RH42-1 | L + D | L + D | 26.52 | 4.2 | 26.05 | 23.91 | 1.02 | 1.11 |
C8008-10-RH42-2 | L + D | L + D | -- | -- | 26.5 | 23.6 | -- | -- |
C8008-10-RH62-1 | L + D | L + D | 23.5 | 15.1 | 24.02 | 22.45 | 0.98 | 1.05 |
C8008-10-RH62-2 | L + D | L + D | -- | -- | 23.42 | 22.66 | -- | -- |
C10010-10-NH-1 | L + D | L + D | 41.7 | 41.29 | 41.31 | 1.01 | 1.01 | |
C10010-10-NH-2 | L + D | L + D | 39.6 | 40.58 | 40.73 | 0.98 | 0.97 | |
C10010-10-RH21-1 | L + D | L + D | 40.1 | 1.3 | 40.62 | 39.64 | 0.99 | 1.01 |
C10010-10-RH21-2 | L + D | L + D | 40.95 | -0.74 | 40.65 | 39.68 | 1.01 | 1.03 |
C10010-10-RH41-1 | L + D | L + D | 39.38 | 3.1 | 39.9 | 36.79 | 0.99 | 1.07 |
C10010-10-RH41-2 | L + D | L + D | 39.4 | 3.1 | 39.26 | 36.71 | 1.00 | 1.07 |
C10010-10-RH61-1 | L + D | L + D | 37.3 | 8.2 | 36.51 | 35.52 | 1.02 | 1.05 |
C10010-10-RH61-2 | L + D | L + D | 37.66 | 7.4 | 36.1 | 35.83 | 1.04 | 1.05 |
C10010-10-RH22-1 | L + D | L + D | 40.25 | 0.98 | 39.99 | 39.55 | 1.01 | 1.02 |
C10010-10-RH22-2 | L + D | L + D | -- | -- | 40.52 | 40.15 | -- | -- |
C10010-10-RH42-1 | L + D | L + D | 38.45 | 5.4 | 38.88 | 37.16 | 0.99 | 1.03 |
C10010-10-RH42-2 | L + D | L + D | 38.7 | 4.8 | 38.46 | 37.52 | 1.01 | 1.03 |
C10010-10-RH62-1 | L + D | L + D | 36.8 | 9.5 | 36.36 | 36.08 | 1.01 | 1.02 |
C10010-10-RH62-2 | L + D | L + D | 37.05 | 8.9 | 36.87 | 35.94 | 1.00 | 1.03 |
Average | 0.99 | 1.05 | ||||||
Standard deviation | 0.0005 | 0.0009 | ||||||
Variable coefficient | 0.023 | 0.029 |
h/mm | b/mm | a/mm | t/mm | fy/MPa | L/mm | Hh/mm | Lh/mm | The number of holes | Hole spacing S/mm | Buckling mode | Pa/kN | Pc/kN | Pa/Pc |
89 | 41 | 13 | 1 | 280 | 1000 | 0 | 0 | 0 | - | L | 36.5 | 34.2 | 1.07 |
89 | 41 | 13 | 1 | 280 | 1000 | 26.7 | 26.7 | 1 | - | L + D | 35.8 | 33.4 | 1.07 |
89 | 41 | 13 | 1 | 280 | 1000 | 44.5 | 44.5 | 1 | - | L + D | 33.9 | 31 | 1.09 |
89 | 41 | 13 | 1 | 280 | 1500 | 62.3 | 62.3 | 1 | - | L+ D | 29.8 | 27.8 | 1.07 |
89 | 41 | 13 | 1 | 280 | 1500 | 0 | 0 | 0 | - | L + G | 34.3 | 31.4 | 1.09 |
89 | 41 | 13 | 1 | 280 | 1500 | 26.7 | 26.7 | 3 | 500 | L + G | 33.2 | 30.8 | 1.08 |
89 | 41 | 13 | 1 | 280 | 1500 | 44.5 | 44.5 | 3 | 500 | L+D+G | 30.8 | 28.4 | 1.08 |
89 | 41 | 13 | 1 | 280 | 1500 | 62.3 | 62.3 | 3 | 500 | L+D+G | 27.5 | 25.2 | 1.09 |
75 | 40 | 8 | 1 | 550 | 1000 | 0 | 0 | 0 | - | L + D | 43.2 | 41 | 1.05 |
75 | 40 | 8 | 1 | 550 | 1000 | 22.5 | 22.5 | 1 | - | L + D | 42.3 | 40.5 | 1.04 |
75 | 40 | 8 | 1 | 550 | 1000 | 37.5 | 37.5 | 1 | - | L + D | 39.7 | 37.8 | 1.05 |
75 | 40 | 8 | 1 | 550 | 1500 | 52.5 | 52.5 | 1 | - | L+D+G | 36.1 | 33.5 | 1.08 |
75 | 40 | 8 | 1 | 550 | 1500 | 0 | 0 | 0 | - | L+D+G | 35.3 | 32.6 | 1.08 |
75 | 40 | 8 | 1 | 550 | 1500 | 22.5 | 22.5 | 3 | 500 | L+D+G | 34.4 | 32.2 | 1.07 |
75 | 40 | 8 | 1 | 550 | 1500 | 37.5 | 37.5 | 3 | 500 | L+D+G | 30.9 | 28.5 | 1.08 |
75 | 40 | 8 | 1 | 550 | 1500 | 52.5 | 52.5 | 3 | 500 | L+D+G | 27.3 | 25.1 | 1.09 |
Mean value | 1.07 | ||||||||||||
Standard deviation | 0.0002 | ||||||||||||
Coefficient of variable | 0.014 |