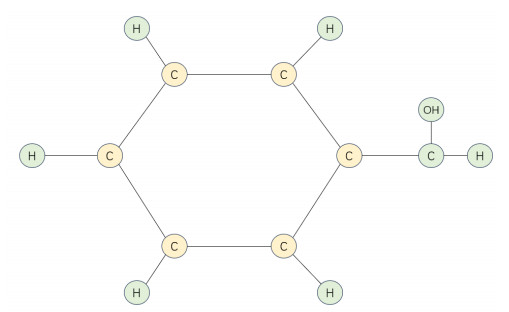
Citation: Daria Wehlage, Robin Böttjer, Timo Grothe, Andrea Ehrmann. Electrospinning water-soluble/insoluble polymer blends[J]. AIMS Materials Science, 2018, 5(2): 190-200. doi: 10.3934/matersci.2018.2.190
[1] | Khaled M. Bataineh, Assem N. AL-Karasneh . Direct solar steam generation inside evacuated tube absorber. AIMS Energy, 2016, 4(6): 921-935. doi: 10.3934/energy.2016.6.921 |
[2] | Sunbong Lee, Shaku Tei, Kunio Yoshikawa . Properties of chicken manure pyrolysis bio-oil blended with diesel and its combustion characteristics in RCEM, Rapid Compression and Expansion Machine. AIMS Energy, 2014, 2(3): 210-218. doi: 10.3934/energy.2014.3.210 |
[3] | Saad S. Alrwashdeh . Investigation of the effect of the injection pressure on the direct-ignition diesel engine performance. AIMS Energy, 2022, 10(2): 340-355. doi: 10.3934/energy.2022018 |
[4] | Xiaoyu Zheng, Dewang Chen, Yusheng Wang, Liping Zhuang . Remaining useful life indirect prediction of lithium-ion batteries using CNN-BiGRU fusion model and TPE optimization. AIMS Energy, 2023, 11(5): 896-917. doi: 10.3934/energy.2023043 |
[5] | Gitsuzo B.S. Tagawa, François Morency, Héloïse Beaugendre . CFD investigation on the maximum lift coefficient degradation of rough airfoils. AIMS Energy, 2021, 9(2): 305-325. doi: 10.3934/energy.2021016 |
[6] | Charalambos Chasos, George Karagiorgis, Chris Christodoulou . Technical and Feasibility Analysis of Gasoline and Natural Gas Fuelled Vehicles. AIMS Energy, 2014, 2(1): 71-88. doi: 10.3934/energy.2014.1.71 |
[7] | Tien Duy Nguyen, Trung Tran Anh, Vinh Tran Quang, Huy Bui Nhat, Vinh Nguyen Duy . An experimental evaluation of engine performance and emissions characteristics of a modified direct injection diesel engine operated in RCCI mode. AIMS Energy, 2020, 8(6): 1069-1087. doi: 10.3934/energy.2020.6.1069 |
[8] | Abdelrahman Kandil, Samir Khaled, Taher Elfakharany . Prediction of the equivalent circulation density using machine learning algorithms based on real-time data. AIMS Energy, 2023, 11(3): 425-453. doi: 10.3934/energy.2023023 |
[9] | Anbazhagan Geetha, S. Usha, J. Santhakumar, Surender Reddy Salkuti . Forecasting of energy consumption rate and battery stress under real-world traffic conditions using ANN model with different learning algorithms. AIMS Energy, 2025, 13(1): 125-146. doi: 10.3934/energy.2025005 |
[10] | Kunzhan Li, Fengyong Li, Baonan Wang, Meijing Shan . False data injection attack sample generation using an adversarial attention-diffusion model in smart grids. AIMS Energy, 2024, 12(6): 1271-1293. doi: 10.3934/energy.2024058 |
Fractional calculus is a branch of mathematics that investigates the properties of arbitrary-order differential and integral operators to address various problems. Fractional differential equations provide a more appropriate model for describing diffusion processes, wave phenomena, and memory effects [1,2,3,4] and possess a diverse array of applications across numerous fields, encompassing stochastic equations, fluid flow, dynamical systems theory, biological and chemical engineering, and other domains[5,6,7,8,9].
Star graph G=(V,E) consists of a finite set of nodes or vertices V(G)={v0,v1,...,vk} and a set of edges E(G)={e1=→v1v0,e2=→v2v0,...,ek=→vkv0} connecting these nodes, where v0 is the joint point and ei is the length of li the edge connecting the nodes vi and v0, i.e., li=|→viv0|.
Graph theory is a mathematical discipline that investigates graphs and networks. It is frequently regarded as a branch of combinatorial mathematics. Graph theory has become widely applied in sociology, traffic management, telecommunications, and other fields[10,11,12].
Differential equations on star graphs can be applied to different fields, such as chemistry, bioengineering, and so on[13,14]. Mehandiratta et al. [15] explored the fractional differential system on star graphs with n+1 nodes and n edges,
{CDα0,xui(x)=fi(x,ui,CDβ0,xui(x)),0<x<li,i=1,2,...,k,ui(0)=0,i=1,2,...,k,ui(li)=uj(lj),i,j=1,2,...,k,i≠j,k∑i=1u′i=0,i=1,2,...,k, |
where CDα0,x,CDβ0,x are the Caputo fractional derivative operator, 1<α≤2, 0<β≤α−1, fi,i=1,2,...,k are continuous functions on C([0,1]×R×R). By a transformation, the equivalent fractional differential system defined on [0,1] is obtained. The author studied a nonlinear Caputo fractional boundary value problem on star graphs and established the existence and uniqueness results by fixed point theory.
Zhang et al. [16] added a function λi(x) on the basis of the reference [15]. In addition, Wang et al. [17] discussed the existence and stability of a fractional differential equation with Hadamard derivative. For more papers on the existence of solutions to fractional differential equations, refer to [18,19,20,21]. By numerically simulating the solution of fractional differential systems, we are able to solve problems more clearly and accurately. However, numerical simulation has been rarely used to describe the solutions of fractional differential systems on graphs [22,23].
The word chemical is used to distinguish chemical graph theory from traditional graph theory, where rigorous mathematical proofs are often preferred to the intuitive grasp of key ideas and theorems. However, graph theory is used to represent the structural features of chemical substances. Here, we introduce a novel modeling of fractional boundary value problems on the benzoic acid graph (Figure 1). The molecular structure of the benzoic acid seven carbon atoms, seven hydrogen atoms, and one oxygen atom. Benzoic acid is mainly used in the preparation of sodium benzoate preservatives, as well as in the synthesis of drugs and dyes. It is also used in the production of mordants, fungicides, and fragrances. Therefore, a thorough understanding of its properties is of utmost importance.
By this structure, we consider atoms of carbon, hydrogen, and oxygen as the vertices of the graph and also the existing chemical bonds between atoms are considered as edges of the graph. To investigate the existence of solutions for our fractional boundary value problems, we label vertices of the benzoic acid graph in the form of labeled vertices by two values, 0 or 1, and the length of each edge is fixed at e (|→ei|=e,i=1,2,...,14) (Figure 2). In this case, we construct a local coordinate system on the benzoic acid graph, and the orientation of each vertex is determined by the orientation of its corresponding edge. The labels of the beginning and ending vertices are taken into account as values 0 and 1, respectively, as we move along any edge.
Motivated by the above work and relevant literature[15,16,17,18,19,20,21,22,23], we discuss a boundary value problem consisting of nonlinear fractional differential equations defined on |→ei|=e,i=1,2,⋯,14 by
HDα1+ri(t)=−ϱαiϕp(fi(s,ri(s),HDβ1+ri(s))),t∈[1,e], |
and the boundary conditions defined at boundary nodes e1,e2,⋯,e14, and
ri(1)=0,ri(e)=rj(e),i,j=1,2,⋯,14,i≠j, |
together with conditions of conjunctions at 0 or 1 with
k∑i=1ϱ−1ir′i(e)=0,i=1,2,⋯,14. |
Overall, we consider the existence and stability of solutions to the following nonlinear boundary value problem on benzoic acid graphs:
{HDα1+ri(t)=−ϱαiϕp(fi(s,ri(s),HDβ1+ri(s))),t∈[1,e],ri(1)=0,i=1,2,⋯,14,ri(e)=rj(e),i,j=1,2,⋯,14,i≠j,k∑i=1ϱ−1ir′i(e)=0,i=1,2,⋯,14, | (1.1) |
where HDα1+,HDβ1+ represent the Hadamard fractional derivative, α∈(1,2],β∈(0,1],fi∈C([1,e]×R×R), ϱi is a real constant, and ϕp(s)=sgn(s)⋅|s|p−1. The existence and Hyers-Ulam stability of the solutions to the system (1.1) are discussed. Moreover, the approximate graphs of the solution are obtained.
It is also noteworthy that solutions obtained from the problem (1.1) can be depicted in various rational applications of organic chemistry. More precisely, any solution on an arbitrary edge can be described as the amount of bond polarity, bond power, bond energy, etc. This paper lies in the integration of fractional differential equations with graph theory, utilizing the formaldehyde graph as a specific case for numerical simulation, and providing an approximate solution graph after iterations.
In this section, for conveniently researching the problem, several properties and lemmas of fractional calculus are given, forming the indispensable premises for obtaining the main conclusions.
Definition 2.1. [2,20] The Hadamard fractional integral of order α, for a function g∈Lp[a,b], 0≤a≤t≤b≤∞, is defined as
HIqa+g(t)=1Γ(α)∫ta(logts)α−1g(s)sds, |
and the Hadamard fractional integral is a particular case of the generalized Hattaf fractional integral introduced in [24].
Definition 2.2. [2,20] Let [a,b]⊂R, δ=tddt and ACnδ[a,b]={g:[a,b]→R:δn−1(g(t))∈AC[a,b]}. The Hadamard derivative of fractional order α for a function g∈ACnδ[a,b] is defined as
HDαa+g(t)=δn(HIn−αa+)(t)=1Γ(n−α)(tddt)n∫ta(logts)n−α−1g(s)sds, |
where n−1<α<n, n=[α]+1, and [α] denotes the integer part of the real number α and log(⋅)=loge(⋅).
Definition 2.3. [25] Completely continuous operator: A bounded linear operator f, acting from a Banach space X into another space Y, that transforms weakly-convergent sequences in X to norm-convergent sequences in Y. Equivalently, an operator f is completely-continuous if it maps every relatively weakly compact subset of X into a relatively compact subset of Y.
Compact operator: An operator A defined on a subset M of a topological vector space X, with values in a topological vector space Y, such that every bounded subset of M is mapped by it into a pre-compact subset of Y. If, in addition, the operator A is continuous on M, then it is called completely continuous on this set. In the case when X and Y are Banach or, more generally, bornological spaces and the operator A:X→Y is linear, the concepts of a compact operator and of a completely-continuous operator are the same.
Lemma 2.4. [20] For y∈ACnδ[a,b], the following result hold
HIα0+(HDα0+)y(t)=y(t)−n−1∑k=0ci(logta)k, |
where ci∈R,i=0,1,⋯,n−1.
Lemma 2.5. [21] For p>2, ∣x∣,∣y∣≤M, we have
∣ϕp(x)−ϕp(y)∣≤(p−1)Mp−2∣x−y∣. |
Lemma 2.6. [4] Let M be a closed convex and nonempty subset of a Banach space X. Let T,S be the operators T−S:M→X such that
(ⅰ) Tx+Sy∈M whenever x,y∈M;
(ⅱ) T is contraction mapping;
(ⅲ) S is completely continuous in M.
Then T+S has at least one fixed point in M.
Proof. For every Z∈S(M), we have T(x)+z:M→M. According to (ⅱ) and the Banach contraction mapping principle, Tx+z=x or z−x=Tx has only one solution in M. For any z,˜z∈S(M), we have
T(t(z))+z=T(z),T(t(˜z))+z=t(˜z). |
So we have
|t(z)−t(˜z)|≤|T(t(z))−T(t(˜z))|+|z−˜z|≤ν|t(z)−t(˜z)|+|z−˜z|,0≤ν<1. |
Thus, |t(z)−t(˜z)|≤11−ν|z−˜z|. It indicates that t∈C(S(M)). Because of S is completely continuous in M, tS is completely continuous. According to the Schauder fixed point theorem, there exists x∗∈M, such that tS(x∗)=x. So we have
T(t(S(x∗)))+S(x∗)=t(S(x∗)),Tx∗+Sx∗=x∗. |
Lemma 2.7. Let hi(t)∈AC([1,e],R),i=1,2,⋯,14; then the solution of the fractional differential equations
{HDα1+ri(t)=−ζi(t),t∈[1,e],ri(1)=0,i=1,2,⋯,14,ri(e)=rj(e),i,j=1,2,⋯,14,i≠j,k∑i=1ϱ−1ir′i(e)=0,i=1,2,⋯,14, | (2.1) |
is given by
ri(t)=−1Γ(α)∫t1(logts)α−1ζi(s)sds +logt[1Γ(α−1)k∑j=1(ϱ−1j∑kj=1ϱ−1j)∫e1(loges)α−2ζj(s)sds −1Γ(α)k∑j=1j≠i(ϱ−1j∑kj=1ϱ−1j)(∫e1(loges)α−1(ζj(s)−ζi(s)s))ds]. | (2.2) |
Proof. By Lemma 2.4, we have
ri(t)=−HIα1+ζi(t)+c(1)i+c(2)ilogt,i=1,2,⋯,14, |
where c(1)i,c(2)i are constants. The boundary condition ri(1)=0 gives c(1)i=0, for i=1,2,⋯,14.
Hence,
ri(t)=−HIα1+ζi(t)+c(2)ilogt =−1Γ(α)∫t1(logts)α−1ζ(s)sds+c(2)ilogt,i=1,2,⋯,14. | (2.3) |
Also
r′i(t)=−1Γ(α−1)∫t11t(logts)α−2ζ(s)sds+1tc(2)i. |
Now, the boundary conditions ri(e)=rj(e) and k∑i=1ϱ−1ir′i(e)=0 implies that c(2)i must satisfy
−1Γ(α)∫e1(loges)α−1ζi(s)sds+c(2)i=−1Γ(α)∫e1(loges)α−1ζj(s)sds+c(2)j, | (2.4) |
−k∑i=1ϱ−1i(1Γ(α−1)∫e1(loges)α−2ζi(s)sds−c(2)i)=0. | (2.5) |
On solving above Eqs (2.4) and (2.5), we have
−k∑j=1ϱ−1j(1Γ(α−1)∫e1(loges)α−2ζj(s)sds)+λ−1ic(2)i=−k∑j=1j≠iϱ−1j[1Γ(α)∫e1(loges)α−1ζj(s)sds−1Γ(α)∫e1(loges)α−1ζi(s)sds+c(2)i], |
which implies
k∑j=1ϱ−1jc(2)i=−k∑j=1ϱ−1j1Γ(α−1)∫e1(loges)α−2ζj(s)sds+k∑j=1j≠iϱ−1j1Γ(α)∫e1(loges)α−1(ζj(s)−ζi(s)s)ds. |
Hence, we get
c(2)i=−1Γ(α−1)k∑j=1(ϱ−1j∑kj=1ϱ−1j)∫e1(loges)α−2ζj(s)sds +1Γ(α)k∑j=1j≠i(ϱ−1j∑kj=1ϱ−1j)(∫e1(loges)α−1(ζj(s)−ζi(s)s))ds. | (2.6) |
Hence, inserting the values of c(2)i, we get the solution (2.2). This completes the proof.
In this section, we discuss the existence and uniqueness of solutions of system (1.1) by using fixed point theory.
We define the space X={r:r∈C([1,e],R),HDβ1+r∈C([1,e],R)} with the norm
‖r‖X=‖r‖+‖HDβ1+u‖=supt∈[1,e]|r(t)|+supt∈[1,e]|HDβ1+r(t)|. |
Then, (X,‖.‖X) is a Banach space, and accordingly, the product space (Xk=X1×X2⋯×X14,‖.‖Xk) is a Banach space with norm
‖r‖Xk=‖(r1,r2,⋯,r14)‖X=k∑i=1‖ri‖X,(r1,r2,⋯,rk)∈Xk. |
In view of Lemma 2.7, we define the operator T:Xk→Xk by
T(r1,r2,⋯,rk)(t):=(T1(r1,r2,⋯,rk)(t),⋯,Tk(r1,r2,⋯,rk)(t)), |
where
Ti(r1,r2,⋯,rk)(t)=−ϱαiΓ(α)∫t1(logts)α−1ϕp(gi(s,ri(s),HDβ1+ri(s)))ds+logtΓ(α−1)k∑j=1(ϱ−1j∑kj=1ϱ−1j)ϱαj∫e1(loges)α−2ϕp(gj(s,rj(s),HDβ1+rj(s)))ds−logtΓ(α)k∑j=1j≠i(ϱ−1j∑kj=1ϱ−1j)ϱαj∫e1(loges)α−1ϕp(gj(s,rj(s),HDβ1+rj(s)))ds+logtΓ(α)k∑j=1j≠i(ϱ−1j∑kj=1ϱ−1j)ϱαi∫e1(loges)α−1ϕp(gi(s,ri(s),HDβ1+ri(s)))ds, | (3.1) |
where ϕp(fi(s,ri(s),HDβ1+ri(s))s)=ϕp(gi(s,ri(s),HDβ1+ri(s))).
Assume that the following conditions hold:
(H1) gi:[1,e]×R×R→R,i=1,2,⋯,14 be continuous functions, and there exists nonnegative functions li(t)∈C[1,e] such that
|gi(t,x,y)−gi(t,x1,y1)|≤ui(t)(|x−x1|+|y−y1|), |
where t∈[1,e],(x,y),(x1,y1)∈R2;
(H2) ιi=supt∈[1,e]|ui(t)|,i=1,2,⋯,14;
(H3) There exists Qi>0, such that
|gi(t,x,y)|≤Qi,t∈[1,e],(x,y)∈R×R,i=1,2,⋯,14; |
(H4)sup1≤t≤e∣gi(t,0,0)∣=κ<∞,i=1,2,...,14.
For computational convenience, we also set the following quantities:
χi=e(p−1)Qp−2i(ϱαi+ϱα−βi) ×[1Γ(α)+2Γ(α+1)+1Γ(α−β+1)+1Γ(α)Γ(2−β)+1Γ(α+1)Γ(2−β)] +ek∑j=1j≠i(ϱαj+ϱα−βj)(p−1)Qp−2j ×[1Γ(α)+1Γ(α+1)+1Γ(α)Γ(2−β)+1Γ(α+1)Γ(2−β)], | (3.2) |
Υi=e(p−1)Qp−2i(ϱαi+ϱα−βi) ×[1Γ(α)+1Γ(α+1)+1Γ(α)Γ(2−β)+1Γ(α+1)Γ(2−β)] +ek∑j=1j≠i(ϱαj+ϱα−βj)(p−1)Qp−2j ×[1Γ(α)+1Γ(α+1)+1Γ(α)Γ(2−β)+1Γ(α+1)Γ(2−β)]. | (3.3) |
Theorem 3.1. Assume that (H1) and (H2) hold; then the fractional differential system (1.1) has a unique solution on [1,e] if
(k∑i=1χi)(k∑i=1ιi)<1, |
where χi,i=1,2,⋯,14 are given by Eq (3.2).
Proof. Let u=(r1,r2,⋯,r14),v=(v1,v2,⋯,v14)∈Xk,t∈[1,e], we have
|Tir(t)−Tiv(t)|≤ϱαiΓ(α)∫t1(logts)α−1|ϕp(gi(s,ri(s),HDβ1+ri(s))−ϕp(gi(s,vi(s),HDβ1+vi(s))|ds+logtΓ(α−1)k∑j=1(ϱ−1j∑kj=1ϱ−1j)ϱαj∫e1(loges)α−2[|ϕp(gj(s,rj(s),HDβ1+rj(s))−ϕp(gj(s,vj(s),HDβ1+vj(s))|ds]+logtΓ(α)k∑j=1j≠i(ϱ−1j∑kj=1ϱ−1j)ϱαj∫e1(loges)α−1[|ϕp(gj(s,rj(s),HDβ1+rj(s))−ϕp(gj(s,vj(s),HDβ1+vj(s))|ds]+logtΓ(α)k∑j=1j≠i(ϱ−1j∑kj=1ϱ−1j)ϱαi∫e1(loges)α−1[|ϕp(gi(s,ri(s),HDβ1+ri(s))−ϕp(gi(s,vi(s),HDβ1+vi(s))|ds]. |
Using Lemma 2.5, (H1) and (H2), t∈[1,e] and (ϱ−1j∑kj=1ϱ−1j)<1 for j=1,2,⋯,k, we obtain
|Tir(t)−Tiv(t)|≤eϱαiΓ(α+1)(p−1)Qp−2iιi‖ri−vi‖+eϱα−βiΓ(α+1)(p−1)Qp−2iιi‖HDβ1+ri−HDβ1+vi‖+e(p−1)Qp−2jk∑j=1(ϱαjΓ(α)ιj‖rj−vj‖+ϱα−βjΓ(α)ιj‖HDβ1+rj−HDβ1+vj‖)+e(p−1)Qp−2jk∑j=1j≠i(ϱαjΓ(α+1)ιj‖rj−vj‖+ϱα−βjΓ(α+1)ιj‖HDβ1+rj−HDβ1+vj‖)+eϱαiΓ(α+1)(p−1)Qp−2iιi‖ri−vi‖+eϱα−βiΓ(α+1)(p−1)Qp−2iιi‖HDβ1+ri−HDβ1+vi‖≤2e(ϱαi+ϱα−βi)Γ(α+1)(p−1)Qp−2iιi(‖ri−vi‖+‖HDβ1+ri−HDβ1+vi‖)+ek∑j=1ϱαj+ϱα−βjΓ(α)(p−1)Qp−2jιj(‖rj−vj‖+‖HDβ1+rj−HDβ1+vj‖)+ek∑j=1j≠iϱαj+ϱα−βjΓ(α+1)(p−1)Qp−2jιj(‖rj−vj‖+‖HDβ1+rj−HDβ1+vj‖)=e(1Γ(α)+2Γ(α+1))(ϱαi+ϱα−βi)(p−1)Qp−2iιi(‖ri−vi‖+‖HDβ1+ri−HDβ1+vi‖)+e(1Γ(α)+1Γ(α+1))k∑j=1j≠i(ϱαj+ϱα−βj)(p−1)Qp−2jιj(‖rj−vj‖+‖HDβ1+rj−HDβ1+vj‖). |
Hence,
‖Tir(t)−Tiv(t)‖ ≤e(1Γ(α)+2Γ(α+1))(ϱαi+ϱα−βi)(p−1)Qp−2iιi(‖ri−vi‖+‖HDβ1+ri−HDβ1+vi‖) +e(1Γ(α)+1Γ(α+1))k∑j=1j≠i(ϱαj+ϱα−βj)(p−1)Qp−2jιj(‖rj−vj‖+‖HDβ1+rj−HDβ1+vj‖). | (3.4) |
By the formula in reference[3],
HDβ1+(logts)β−1=Γ(β)Γ(β−α)(logts)β−α−1,β>1, |
we have
|HDβ1+Tir(t)−HDβ1+Tiv(t)|≤ϱαiΓ(α−β)∫t1(logts)α−β−1|ϕp(gi(s,ri(s),HDβ1+ri(s))−ϕp(gi(s,vi(s),HDβ1+vi(s))|ds+(logt)1−βΓ(α−1)Γ(2−β)k∑j=1(ϱ−1j∑kj=1ϱ−1j)ϱαj∫e1(loges)α−2[|ϕp(gj(s,rj(s),HDβ1+rj(s))−ϕp(gj(s,vj(s),HDβ1+vj(s))|ds]+(logt)1−βΓ(α)Γ(2−β)k∑j=1j≠i(ϱ−1j∑kj=1ϱ−1j)ϱαj∫e1(loges)α−1[|ϕp(gj(s,rj(s),HDβ1+rj(s))−ϕp(gj(s,vj(s),HDβ1+vj(s))|ds]+(logt)1−βΓ(α)Γ(2−β)k∑j=1j≠i(ϱ−1j∑kj=1ϱ−1j)ϱαi∫e1(loges)α−1[|ϕp(gi(s,ri(s),HDβ1+ri(s))−ϕp(gi(s,vi(s),HDβ1+vi(s))|ds]. |
Using Lemma 2.5, (H1) and (H2), Γ(2−β)≤1 and (ϱ−1j∑kj=1ϱ−1j)<1 for j=1,2,⋯,k, we obtain
|HDβ1+Tir(t)−HDβ1+Tiv(t)|≤eϱαiΓ(α−β+1)(p−1)Qp−2iιi‖ri−vi‖+eϱαiΓ(α+1)Γ(2−β)(p−1)Qp−2iιi‖ri−vi‖+eϱα−βiΓ(α−β+1)(p−1)Qp−2iιi‖HDβ1+ri−HDβ1+vi‖+eϱα−βiΓ(α+1)Γ(2−β)(p−1)Qp−2iιi‖HDβ1+ri−HDβ1+vi‖+e(p−1)Qp−2jk∑j=1(ϱαiΓ(α)Γ(2−β)ιj‖rj−vj‖+ϱα−βiΓ(α)Γ(2−β)ιj‖HDβ1+rj−HDβ1+vj‖)+e(p−1)Qp−2jk∑j=1j≠i(λαjΓ(α+1)ιj‖rj−vj‖+ϱα−βjΓ(α+1)ιj‖HDβ1+rj−HDβ1+vj‖)≤e(ϱαi+ϱα−βi)Γ(α−β+1)(p−1)Qp−2iιi(‖ri−vi‖+‖HDβ1+ri−HDβ1+vi‖)+ek∑j=1ϱαj+ϱα−βjΓ(α)Γ(2−β)(p−1)Qp−2jιj(‖rj−vj‖+‖HDβ1+rj−HDβ1+vj‖)+ek∑j=1j≠iϱαj+ϱα−βjΓ(α+1)Γ(2−β)(p−1)Qp−2jιj(‖rj−vj‖+‖HDβ1+rj−HDβ1+vj‖)+e(ϱαi+ϱα−βi)Γ(α+1)Γ(2−β)(p−1)Qp−2iιi(‖ri−vi‖+‖HDβ1+ri−HDβ1+vi‖). |
Hence,
‖HDβ1+Tir(t)−HDβ1+Tiv(t)‖ ≤e(1Γ(α−β+1)+1(Γ(α)Γ(2−β)+1Γ(α+1)Γ(2−β)) ×(ϱαi+ϱα−βi)(p−1)Qp−2iιi(‖ri−vi‖+‖HDβ1+ri−HDβ1+vi‖) +e(1Γ(α)Γ(2−β)+1Γ(α+1)Γ(2−β))k∑j=1j≠i(ϱαj+ϱα−βj) ×(p−1)Qp−2jιj(‖rj−vj‖+‖HDβ1+rj−HDβ1+vj‖). | (3.5) |
From (3.4) and (3.5), we have
‖Tir(t)−Tiv(t)‖+‖HDβ1+Tir(t)−HDβ1+Tiv(t)‖≤e(1Γ(α)+2Γ(α+1)+1Γ(α−β+1)+1(Γ(α)Γ(2−β)+1Γ(α+1)Γ(2−β))×(ϱαi+ϱα−βi)(p−1)Qp−2iιi(‖ri−vi‖+‖HDβ1+ri−HDβ1+vi‖)+e(1Γ(α)+1Γ(α+1)+1Γ(α)Γ(2−β)+1Γ(α+1)Γ(2−β))k∑j=1j≠i(ϱαj+ϱα−βj)×(p−1)Qp−2jιj(‖rj−vj‖+‖HDβ1+rj−HDβ1+vj‖). |
Hence,
‖Tir(t)−Tiv(t)‖X ≤e(p−1)[(1Γ(α)+2Γ(α+1)+1Γ(α−β+1)+1Γ(α)Γ(2−β)+1Γ(α+1)Γ(2−β)) ×Qp−2i(ϱαi+ϱα−βi)+(1Γ(α)+1Γ(α+1)+1Γ(α)Γ(2−β)+1Γ(α+1)Γ(2−β)) ×Qp−2jk∑j=1j≠i(ϱαj+ϱα−βj)](k∑i=1ιi)(‖rj−vj‖+‖HDβ1+rj−HDβ1+vj‖) =χi(k∑i=1ιi)‖r−v‖Xk, | (3.6) |
where χi,i=1,2,⋯,k are given by (3.2).
From the above Eq (3.6), it follows that
‖Tr−Tv)‖Xk=k∑i=1‖Tir−Tiv‖X≤(k∑i=1χi)(k∑i=1ιi)‖r−v‖Xk. |
Since
(k∑i=1χi)(k∑i=1ιi)<1, |
we obtain that T is a contraction map. According to Banach's contraction principle, the original system (1.1) has a unique solution on [1,e].
Theorem 3.2. Assume that (H1) and (H2) hold; then system (2.1) has at least one solution on [1,e] if
(k∑i=1Υi)(k∑i=1ιi)<1, |
where Υi,i=1,2,⋯,14 are given by Eq (3.3).
By Theorem 3.1, T is defined under the consideration of Krasnoselskii's fixed point theorem as follows:
Tμ=ϖ1μ+ϖ2μ, |
where
ϖ1μ=−ϱαiΓ(α)∫t1(logts)α−1ϕp(gi(s,ri(s),HDβ1+ri(s)))ds,ϖ2μ=logtΓ(α−1)k∑j=1(ϱ−1j∑kj=1ϱ−1j)ϱαj∫e1(loges)α−2ϕp(gj(s,rj(s),HDβ1+rj(s)))ds−logtΓ(α)k∑j=1j≠i(ϱ−1j∑kj=1ϱ−1j)ϱαj∫e1(loges)α−1ϕp(gj(s,rj(s),HDβ1+rj(s)))ds+logtΓ(α)k∑j=1j≠i(ϱ−1j∑kj=1ϱ−1j)ϱαi∫e1(loges)α−1ϕp(gi(s,ri(s),HDβ1+ri(s)))ds. |
Proof. For any δ=(δ1,δ2,⋯,δ14)(t), μ=(μ1,μ2,⋯,μ14)(t)∈Xk, we have
|ϖ2δ(t)−ϖ2μ(t)|≤logtΓ(α−1)k∑j=1(ϱ−1j∑kj=1ϱ−1j)ϱαj∫e1(loges)α−2[|ϕp(gi(s,δi(s),HDβ1+δi(s))−ϕp(gi(s,μi(s),HDβ1+μi(s))|ds]+logtΓ(α)k∑j=1j≠i(ϱ−1j∑kj=1ϱ−1j)ϱαj∫e1(loges)α−1[|ϕp(gj(s,δj(s),HDβ1+δj(s))−ϕp(gj(s,μj(s),HDβ1+μj(s))|ds]+logtΓ(α)k∑j=1j≠i(ϱ−1j∑kj=1ϱ−1j)ϱαi∫e1(loges)α−1[|ϕp(gi(s,δi(s),HDβ1+δi(s))−ϕp(gi(s,μi(s),HDβ1+μi(s))|ds], |
which implies that
\begin{eqnarray*} &&\|\varpi_{2}\delta(t)-\varpi_{2}\mu(t)\| \\& \leq& e(p-1)Q_{j}^{p-2} \sum\limits_{j = 1}^{k}\left(\frac{\varrho_{j}^{\alpha}}{\Gamma(\alpha)}u_{j}(t)\|\delta_{j}-\mu_{j}\| +\frac{\varrho_{j}^{\alpha-\beta}}{\Gamma(\alpha)}u_{j}(t)\left\|{}^{H}D^{\beta}_{1^{+}}\delta_{j}-{}^{H}D^{\beta}_{1^{+}}\mu_{j}\right\|\right) \\ &&+e(p-1)Q_{j}^{p-2} \sum\limits_{\substack{j = 1\\ j\neq i}}^{k}\left(\frac{\varrho_{j}^{\alpha}}{\Gamma(\alpha+1)}u_{j}(t)\|\delta_{j}-\mu_{j}\| +\frac{\varrho_{j}^{\alpha-\beta}}{\Gamma(\alpha+1)}u_{j}(t)\left\| {}^{H}D^{\beta}_{1^{+}}\delta_{j}-{}^{H}D^{\beta}_{1^{+}}\mu_{j}\right\|\right)\\ &&+\frac{e\varrho_{i}^{\alpha}}{\Gamma(\alpha+1)}(p-1)Q_{i}^{p-2}u_{i}(t)\|\delta_{i}-\mu_{i}\| +\frac{e\varrho_{i}^{\alpha-\beta}}{\Gamma(\alpha+1)}(p-1)Q_{i}^{p-2}u_{i}(t)\left\| {}^{H}D^{\beta}_{1^{+}}\delta_{i}-{}^{H}D^{\beta}_{1^{+}}\mu_{i}\right\| \\ &\leq& \frac{e(\varrho_{i}^{\alpha}+\varrho_{i}^{\alpha-\beta})}{\Gamma(\alpha+1)}(p-1)Q_{i}^{p-2}u_{i}(t)\Big(\|\delta_{i}-\mu_{i}\| +\left\|{}^{H}D^{\beta}_{1^{+}}\delta_{i}-{}^{H}D^{\beta}_{1^{+}}\mu_{i}\right\|\Big) \\ &&+e \sum\limits_{j = 1}^{k}\frac{\varrho_{j}^{\alpha}+\varrho_{j}^{\alpha-\beta}}{\Gamma(\alpha)} (p-1)Q_{j}^{p-2}u_{j}(t)\left(\|\delta_{j}-\mu_{j}\| +\left\|{}^{H}D^{\beta}_{1^{+}}\delta_{j}-{}^{H}D^{\beta}_{1^{+}}\mu_{j}\right\|\right) \\ &&+e \sum\limits_{\substack{j = 1\\ j\neq i}}^{k}\frac{\varrho_{j}^{\alpha}+\varrho_{j}^{\alpha-\beta}}{\Gamma(\alpha+1)} (p-1)Q_{j}^{p-2}u_{j}(t)\left(\|\delta_{j}-\mu_{j}\| +\left\|{}^{H}D^{\beta}_{1^{+}}\delta_{j}-{}^{H}D^{\beta}_{1^{+}}\mu_{j}\right\|\right) \\ & = &e\Big(\frac{1}{\Gamma(\alpha)}+\frac{1}{\Gamma(\alpha+1)}\left)(\varrho_{i}^{\alpha}+\varrho_{i}^{\alpha-\beta}) (p-1)Q_{i}^{p-2}u_{i}(t)\Big(\|\delta_{i}-\mu_{i}\|+\left\|{}^{H}D^{\beta}_{1^{+}}\delta_{i}-{}^{H}D^{\beta}_{1^{+}}\mu_{i}\right\|\right) \\ &&+e\Big(\frac{1}{\Gamma(\alpha)}+\frac{1}{\Gamma(\alpha+1)}\Big) \sum\limits_{\substack{j = 1\\ j\neq i}}^{k}(\varrho_{j}^{\alpha}+\varrho_{j}^{\alpha-\beta})(p-1)Q_{j}^{p-2}u_{j}(t) \left(\|\delta_{j}-\mu_{j}\|+\left\|{}^{H}D^{\beta}_{1^{+}}\delta_{j}-{}^{H}D^{\beta}_{1^{+}}\mu_{j}\right\|\right). \end{eqnarray*} |
In a similar way, we get
\begin{eqnarray*} &&|{}^{H}D^{\beta}_{1^{+}}\varpi_{2}\delta(t)-{}^{H}D^{\beta}_{1^{+}}\varpi_{2}\mu(t)| \\& \leq& \frac{e\varrho_{i}^{\alpha}}{\Gamma(\alpha+1)\Gamma(2-\beta)}(p-1)Q_{i}^{p-2}u_{i}(t)\|\delta_{i}-\mu_{i}\|\\ &&+\frac{e\varrho_{i}^{\alpha-\beta}}{\Gamma(\alpha+1)\Gamma(2-\beta)}(p-1)Q_{i}^{p-2}u_{i}(t)\left\| {}^{H}D^{\beta}_{1^{+}}\delta_{i}-{}^{H}D^{\beta}_{1^{+}}\mu_{i}\right\|\\ &&+e(p-1)Q_{j}^{p-2} \sum\limits_{j = 1}^{k}\left(\frac{\varrho_{i}^{\alpha}} {\Gamma(\alpha)\Gamma(2-\beta)}u_{j}(t)\|\delta_{j}-\mu_{j}\| +\frac{\varrho_{i}^{\alpha-\beta}}{\Gamma(\alpha)\Gamma(2-\beta)}u_{j}(t) \left\|{}^{H}D^{\beta}_{1^{+}}\delta_{j}-{}^{H}D^{\beta}_{1^{+}}\mu_{j}\right\|\right) \\ &&+e(p-1)Q_{j}^{p-2} \sum\limits_{\substack{j = 1\\ j\neq i}}^{k}\left(\frac{\varrho_{j}^{\alpha}}{\Gamma(\alpha+1)}u_{j}(t)\|\delta_{j}-\mu_{j}\| +\frac{\varrho_{j}^{\alpha-\beta}}{\Gamma(\alpha+1)}u_{j}(t)\left\| {}^{H}D^{\beta}_{1^{+}}\delta_{j}-{}^{H}D^{\beta}_{1^{+}}\mu_{j}\right\|\right) \\ &\leq& e \sum\limits_{j = 1}^{k}\frac{\varrho_{j}^{\alpha}+\varrho_{j}^{\alpha-\beta}} {\Gamma(\alpha)\Gamma(2-\beta)}(p-1)Q_{j}^{p-2}u_{j}(t)\left(\|\delta_{j}-\mu_{j}\| +\left\|{}^{H}D^{\beta}_{1^{+}}\delta_{j}-{}^{H}D^{\beta}_{1^{+}}\mu_{j}\right\|\right) \\ &&+e \sum\limits_{\substack{j = 1\\ j\neq i}}^{k}\frac{\varrho_{j}^{\alpha}+\varrho_{j}^{\alpha-\beta}}{\Gamma(\alpha+1)\Gamma(2-\beta)} (p-1)Q_{j}^{p-2}u_{j}(t)\left(\|\delta_{j}-\mu_{j}\| +\left\|{}^{H}D^{\beta}_{1^{+}}\delta_{j}-{}^{H}D^{\beta}_{1^{+}}\mu_{j}\right\|\right) \\ &&+\frac{e(\lambda_{i}^{\alpha}+\lambda_{i}^{\alpha-\beta})}{\Gamma(\alpha+1)\Gamma(2-\beta)} (p-1)Q_{i}^{p-2}u_{j}(t)\left(\|\delta_{i}-\mu_{i}\| +\left\|{}^{H}D^{\beta}_{1^{+}}\delta_{i}-{}^{H}D^{\beta}_{1^{+}}\mu_{i}\right\|\right). \end{eqnarray*} |
Then,
\begin{eqnarray} &&\|\varpi_{2}\delta(t)-\varpi_{2}\mu(t)\|_{X} \ \\ &\leq& e(p-1)\Bigg[\Big(\frac{1}{\Gamma(\alpha)}+\frac{1}{\Gamma(\alpha+1)}+\frac{1}{\Gamma(\alpha)\Gamma(2-\beta)} +\frac{1}{\Gamma(\alpha+1)\Gamma(2-\beta)}\Big) Q_{i}^{p-2}\big(\varrho_{i}^{\alpha}+\varrho_{i}^{\alpha-\beta}\big)\ \\ &&+\Big(\frac{1}{\Gamma(\alpha)}+\frac{1}{\Gamma(\alpha+1)} +\frac{1}{\Gamma(\alpha)\Gamma(2-\beta)}+\frac{1}{\Gamma(\alpha+1)\Gamma(2-\beta)}\Big) Q_{j}^{p-2} \sum\limits_{\substack{j = 1\\ j\neq i}}^{k}\big(\varrho_{j}^{\alpha}+\varrho_{j}^{\alpha-\beta}\big)\Bigg] \ \\ &&\times \left( \sum\limits_{i = 1}^{k}\iota_{i}\Bigg)\Bigg(\|\delta_{j}-\mu_{j}\| +\left\|{}^{H}D^{\beta}_{1^{+}}\delta_{j}-{}^{H}D^{\beta}_{1^{+}}\mu_{j}\right\|\right) \ \\ & = &\Upsilon_{i}\left( \sum\limits_{i = 1}^{k}\omega_{i}\right)\|\delta-\mu\|_{X^{k}}. \end{eqnarray} | (3.7) |
Hence,
\begin{eqnarray} \|\varpi_{2}\delta(t)-\varpi_{2}\mu(t)\|_{X^{k}}& = & \sum\limits_{i = 1}^{k}\|\varpi_{2}\delta-\varpi_{2}\mu\|_{X} \ \\ &\leq&\Bigg( \sum\limits_{i = 1}^{k}\Upsilon_{i}\Bigg) \Bigg( \sum\limits_{i = 1}^{k}\iota_{i}\Bigg)\|\delta-\mu\|_{X^{k}}. \end{eqnarray} | (3.8) |
It follows from \Bigg(\sum\limits_{i = 1}^{k}\Upsilon_{i}\Bigg)\Bigg(\sum\limits_{i = 1}^{k}\iota_{i}\Bigg) < 1 that \varpi_{2} is a contraction operator. In addition, we shall prove that \varpi_{1} is continuous and compact. For any \delta = (\delta_{1}, \delta_{2}, \cdots, \delta_{14})(t)\in X^{k} , we have
\begin{eqnarray*} \|\varpi_{1}\delta(t)\| &\leq&\frac{\varrho_{i}^{\alpha}}{\Gamma(\alpha)}\int_{1}^{t}\Big(\log\frac{t}{s}\Big)^{\alpha-1} \left|\phi_{p}\left(g_{i}\big(s,\delta_{i}(s),{}^{H}D^{\beta}_{1^{+}}\delta_{i}(s)\big)\right)\right|ds\\ &\leq&\frac{\varrho_{i}^{\alpha}}{\Gamma(\alpha)}\int_{1}^{t}\Big(\log\frac{t}{s}\Big)^{\alpha-1} \left|\phi_{p}\left(g_{i}\big(s,\delta_{i}(s),{}^{H}D^{\beta}_{1^{+}}\delta_{i}(s)\big)\right)-\phi_{p}(g_{i}(s,0,0))\right|ds \\ &&+\frac{\varrho_{i}^{\alpha}}{\Gamma(\alpha)}\int_{1}^{t}\Big(\log\frac{t}{s}\Big)^{\alpha-1} \Big|\phi_{p}(g_{i}(s,0,0))\Big|ds \\ &\leq&\frac{e\varrho_{i}^{\alpha}}{\Gamma(\alpha+1)}(p-1)Q_{i}^{p-2}\iota_{i} \Big(\|\delta_{i}\|+\left\|{}^{H}D^{\beta}_{1^{+}}\delta_{i}\right\|\Big) +\frac{e\varrho_{i}^{\alpha}}{\Gamma(\alpha+1)}|\phi_{p}(\kappa)| \\ & = &\frac{e\varrho_{i}^{\alpha}}{\Gamma(\alpha+1)}(p-1)Q_{i}^{p-2}\iota_{i}\|\delta_{i}\|_{X} +\frac{e\varrho_{i}^{\alpha}}{\Gamma(\alpha+1)}|\phi_{p}(\kappa)|. \end{eqnarray*} |
Then,
\begin{eqnarray*} \|{}^{H}D^{\beta}_{1^{+}}\varpi_{1}\delta(t)\| &\leq&\frac{\varrho_{i}^{\alpha}}{\Gamma(\alpha-\beta)}\int_{1}^{t}\big(\log\frac{t}{s}\Big)^{\alpha-\beta-1} \left|\phi_{p}\left(g_{i}\big(s,\delta_{i}(s),{}^{H}D^{\beta}_{1^{+}}\delta_{i}(s)\right)\right|ds\\ &\leq&\frac{\varrho_{i}^{\alpha}}{\Gamma(\alpha-\beta)}\int_{1}^{t}\Big(\log\frac{t}{s}\Big)^{\alpha-\beta-1} \left|\phi_{p}\left(g_{i}\big(s,\delta_{i}(s),{}^{H}D^{\beta}_{1^{+}}\delta_{i}(s)\big)\right)-\phi_{p}(g_{i}(s,0,0))\right|ds \\ &&+\frac{\varrho_{i}^{\alpha}}{\Gamma(\alpha-\beta)}\int_{1}^{t}\Big(\log\frac{t}{s}\Big)^{\alpha-\beta-1} \Big|\phi_{p}(g_{i}(s,0,0))\Big|ds \\ &\leq&\frac{e\varrho_{i}^{\alpha}}{\Gamma(\alpha-\beta+1)}(p-1)Q_{i}^{p-2}\iota_{i} \Big(\|\delta_{i}\|+\left\|{}^{H}D^{\beta}_{1^{+}}\delta_{i}\right\|\Big) +\frac{e\varrho_{i}^{\alpha}}{\Gamma(\alpha-\beta+1)}|\phi_{p}(\kappa)| \\ & = &\frac{e\varrho_{i}^{\alpha}}{\Gamma(\alpha+1)}(p-1)Q_{i}^{p-2}\iota_{i}\|\delta_{i}\|_{X} +\frac{e\lambda_{i}^{\alpha}}{\Gamma(\alpha-\beta+1)}|\phi_{p}(\kappa)|, \end{eqnarray*} |
which implies
\begin{eqnarray} \|\varpi_{1}\delta(t)\|_{X}\leq\left(\frac{1}{\Gamma(\alpha+1)}+\frac{1}{\Gamma(\alpha-\beta+1)}\right) \left((p-1)Q_{i}^{p-2}\iota_{i}\|\delta_{i}\|_{X}+|\phi_{p}(\kappa)|\right). \end{eqnarray} | (3.9) |
Hence,
\begin{eqnarray} \|\varpi_{1}\delta(t)\|_{X^{k}}\leq\left(\frac{1}{\Gamma(\alpha+1)}+\frac{1}{\Gamma(\alpha-\beta+1)}\right) \times\left( \sum\limits_{i = 1}^{k}(p-1)Q_{i}^{p-2}\iota_{i}\|\delta_{i}\|_{X} + \sum\limits_{i = 1}^{k}|\phi_{p}(\kappa)|\right) < \infty. \end{eqnarray} | (3.10) |
This shows that \varpi_{1} is bounded. In addition, we will prove that \varpi_{1} is equi-continuous. Let t_{1} , t_{2}\in[1, e] ; we have
\begin{eqnarray} |\varpi_{1}\delta(t_{2})-\varpi_{1}\delta(t_{1})| \ &\leq& \frac{\varrho_{i}^{\alpha}}{\Gamma(\alpha)}\int_{1}^{t_{1}}\Bigg (\Big(\log\frac{t_{2}}{s}\Big)^{\alpha-1}-\Big(\log\frac{t_{1}}{s}\Big)^{\alpha-1}\Bigg) \left|\phi_{p}\left(g_{i}\big(s,\delta_{i}(s),{}^{H}D^{\beta}_{1^{+}}\delta_{i}(s)\big)\right)\right|ds \notag\ \\ &&+ \frac{\varrho_{i}^{\alpha}}{\Gamma(\alpha)}\int_{t_{1}}^{t_{2}} \Big(\log\frac{t_{2}}{s}\Big)^{\alpha-1} \left|\phi_{p}\left(g_{i}\big(s,\delta_{i}(s),{}^{H}D^{\beta}_{1^{+}}\delta_{i}(s)\big)\right)\right|ds \ \\ &\leq&\frac{e\varrho_{i}^{\alpha}\phi_{p}(Q_{i})}{\Gamma(\alpha+1)}((\log t_{2})^{\alpha}-(\log t_{1})^{\alpha}) +\frac{\varrho_{i}^{\alpha}\phi_{p}(Q_{i})}{\Gamma(\alpha)}\int_{t_{1}}^{t_{2}} \Big(\log\frac{t_{2}}{s}\Big)^{\alpha-1}ds, \end{eqnarray} | (3.11) |
and
\begin{eqnarray} &&\left|{}^{H}D^{\beta}_{1^{+}}\varpi_{1}\delta(t_{2})-{}^{H}D^{\beta}_{1^{+}}\varpi_{1}\delta(t_{1})\right|\ \\ & \leq& \frac{\varrho_{i}^{\alpha}}{\Gamma(\alpha-\beta)}\int_{1}^{t_{1}}\Bigg (\Big(\log\frac{t_{2}}{s}\Big)^{\alpha-\beta-1}-\Big(\log\frac{t_{1}}{s}\Big)^{\alpha-\beta-1}\Bigg) \left|\phi_{p}\left(g_{i}\big(s,\delta_{i}(s),{}^{H}D^{\beta}_{1^{+}}\delta_{i}(s)\big)\right)\right|ds \ \\ &&+ \frac{\varrho_{i}^{\alpha}}{\Gamma(\alpha-\beta)}\int_{t_{1}}^{t_{2}} \Big(\log\frac{t_{2}}{s}\Big)^{\alpha-\beta-1} \left|\phi_{p}\left(g_{i}\big(s,\delta_{i}(s),{}^{H}D^{\beta}_{1^{+}}\delta_{i}(s)\big)\right)\right|ds \ \\ &\leq& \frac{e\varrho_{i}^{\alpha}\phi_{p}(Q_{i})}{\Gamma(\alpha-\beta+1)}((\log t_{2})^{\alpha-\beta}-(\log t_{1})^{\alpha-\beta})+\frac{\lambda_{i}^{\alpha}\phi_{p}(Q_{i})}{\Gamma(\alpha-\beta+1)}\int_{t_{1}}^{t_{2}} \Big(\log\frac{t_{2}}{s}\Big)^{\alpha-\beta-1}ds. \end{eqnarray} | (3.12) |
Therefore, from (3.10) and (3.12), we obtain
\begin{eqnarray} \|\varpi_{1}\delta(t_{2})-\varpi_{1}\delta(t_{1})\|_{X} &\leq&\frac{e\varrho_{i}^{\alpha}\phi_{p}(Q_{i})}{\Gamma(\alpha-\beta+1)}((\log t_{2})^{\alpha-\beta}-(\log t_{1})^{\alpha-\beta})+\frac{\varrho_{i}^{\alpha}\phi_{p}(Q_{i})}{\Gamma(\alpha-\beta+1)}\int_{t_{1}}^{t_{2}} \Big(\log\frac{t_{2}}{s}\Big)^{\alpha-\beta-1}ds \\ &&+\frac{e\varrho_{i}^{\alpha}\phi_{p}(Q_{i})}{\Gamma(\alpha+1)}((\log t_{2})^{\alpha}-(\log t_{1})^{\alpha}) +\frac{\varrho_{i}^{\alpha}\phi_{p}(Q_{i})}{\Gamma(\alpha)}\int_{t_{1}}^{t_{2}} \Big(\log\frac{t_{2}}{s}\Big)^{\alpha-1}ds. \end{eqnarray} | (3.13) |
This indicates that \|\varpi_{1}\delta(t_{2})-\varpi_{1}\delta(t_{1})\|_{X}\rightarrow0 , as t_{2}\rightarrow t_{1} .Thus, \|\varpi_{1}\delta(t_{2})-\varpi_{1}\delta(t_{1})\|_{X^{^{k}}}\rightarrow0 , as t_{2}\rightarrow t_{1} . By the Arzela-Ascoli theorem, we obtain that \omega_{1} is completely continuous. According to Lemma 2.6, system (2.1) has at least one solution on [1, e] , which denotes that the original system (1.1) has at least one solution on [1, e] .
Let \varepsilon_{i} > 0 . Consider the following inequality
\begin{equation} \left|{}^{H}D^{\alpha}_{1^+}r_{i}(t)-\varrho_{i}^{\alpha} \phi_{p}\left({f}_{i}\big(t,r_{i}(t),{}^{H}D^{\beta}_{1^+}r_{i}(t)\big)\right)\right| \leq\varepsilon_{i},\; t\in [1,e]. \end{equation} | (4.1) |
Definition 4.1. [16] The fractional differential system (1.1) is called Hyers-Ulam stable if there is a constant c_{f_{1}, f_{2}, ..., f_{k}} > 0 such that for each \varepsilon = \varepsilon(\varepsilon_{1}, \varepsilon_{2}, ..., \varepsilon_{k}) > 0 and for each solution r = (r_{1}, r_{2}, ..., r_{k})\in X^{k} of the inequality (4.1), there exists a solution \bar{r} = (\bar{r}_{1}, \bar{r}_{2}, ..., \bar{r}_{k})\in X^{k} of (1.1) with
\|r-\bar{r}\|_{X^{k}}\leq c_{f_{1}, f_{2},..., f_{k}}\varepsilon, \; t\in[1,e]. |
Definition 4.2. [16] The fractional differential system (1.1) is called generalized Hyers-Ulam stable if there exists-function \psi_{f_{1}, f_{2}, ..., f_{k}}\in \mathbb C(\mathbb R^{+}, \mathbb R^{+}) with \psi_{f_{1}, f_{2}, ..., f_{k}}(0) = 0 such that for each \varepsilon = \varepsilon(\varepsilon_{1}, \varepsilon_{2}, ..., \varepsilon_{k}) > 0 , and for each solution r = (r_{1}, r_{2}, ..., r_{k})\in X^{k} of the inequality (4.1), there exists a solution \bar{r} = (\bar{r}_{1}, \bar{r}_{2}, ..., \bar{r}_{k})\in X^{k} of (1.1) with
\|r-\bar{r}\|_{X}\leq \psi_{f_{1}, f_{2},..., f_{k}}(\varepsilon), \; t\in[1,e]. |
Remark 4.3. Let function r = (r_{1}, r_{2}, \cdots, r_{k})\in X^k, \; k = 1, 2, \cdots, 14 , be the solution of system (4.1). If there are functions \varphi_{i}:[1, e]\rightarrow \mathbb R^+ dependent on u_{i} respectively, then
(ⅰ) |\varphi_{i}(t)|\leq\varepsilon_{i} , t\in [1, e] , i = 1, 2, \cdots, 14;
(ⅱ) ^{H}D^{\alpha}_{1^+}r_{i}(t) = \varrho_{i}^{\alpha}\phi_{p}\left({f}_{i}\big(t, r_{i}(t), ^{H}D^{\beta}_{1^+}r_{i}(t)\big)\right) +\varphi_{i}(t), t\in [1, e], i = 1, 2, ..., 14.
Remark 4.4. It is worth noting that Hyers-Ulam stability is different from asymptotic stability, which means that the system can gradually return to equilibrium after being disturbed. If the Lyapunov function satisfies certain conditions, the system is asymptotically stable. This stability emphasizes the behavior of the system over a long period of time, that is, as time goes on, the state of the system will return to the equilibrium state, while the error of Hyers-Ulam stability is bounded (proportional to the size of the disturbance).
Lemma 4.5. Suppose r = (r_{1}, r_{2}, ..., r_{k})\in X^k is the solution of inequality (4.1). Then, the following inequality holds:
\begin{eqnarray*} |r_{i}(t)-r_{i}^{*}(t)|&\leq& \varepsilon_{i}e\Big(\frac{1}{\Gamma(\alpha)}+\frac{2}{\Gamma(\alpha+1)}\Big)+\varepsilon_{j}e \sum\limits_{\substack{j = 1\\ j\neq i}}^{k}\Big(\frac{1}{\Gamma(\alpha)}+\frac{1}{\Gamma(\alpha+1)}\Big),\\ |{}^{H}D^{\beta}_{1^{+}}r_{i}(t)-{}^{H}D^{\beta}_{1^{+}}r_{i}^{*}(t)| &\leq& \varepsilon_{j}e \sum\limits_{\substack{j = 1\\ j\neq i}}^{k}\Big(\frac{1}{\Gamma(\alpha)\Gamma(2-\beta)}+\frac{1}{\Gamma(\alpha+1)\Gamma(2-\beta)}\Big) \\ &&+\varepsilon_{i}e\Big(\frac{1}{\Gamma(\alpha-\beta+1)}+\frac{1}{\Gamma(\alpha)\Gamma(2-\beta)} +\frac{1}{\Gamma(\alpha+1)\Gamma(2-\beta)}\Big), \end{eqnarray*} |
where
\begin{align*} r_{i}^{*}(t) = &\frac{1}{\Gamma(\alpha)}\int_{1}^{t}\Big(\log\frac{t}{s}\Big)^{\alpha-1} z_{i}(s)ds \notag\ -\frac{\log t}{\Gamma(\alpha-1)} \sum\limits_{j = 1}^{k}\Bigg(\frac{\lambda_{j}^{-1}}{\sum\nolimits_{j = 1}^{k}\lambda_{j}^{-1}}\Bigg) \int_{1}^{e}\Big(\log\frac{e}{s}\Big)^{\alpha-2} z_{j}(s)ds \notag\ \\ &+\frac{\log t}{\Gamma(\alpha)} \sum\limits_{\substack{j = 1\\ j\neq i}}^{k}\Bigg(\frac{\lambda_{j}^{-1}}{\sum\nolimits_{j = 1}^{k}\lambda_{j}^{-1}}\Bigg) \int_{1}^{e}\Big(\log\frac{e}{s}\Big)^{\alpha-1}z_{j}(s)ds \notag\ -\frac{\log t}{\Gamma(\alpha)} \sum\limits_{\substack{j = 1\\ j\neq i}}^{k}\Bigg(\frac{\lambda_{j}^{-1}}{\sum\nolimits_{j = 1}^{k}\lambda_{j}^{-1}}\Bigg) \int_{1}^{e}\Big(\log\frac{e}{s}\Big)^{\alpha-1}z_{i}(s)ds,\\ {}^{H}D^{\beta}_{1^{+}}r_{i}^{*}(t) = & \frac{1}{\Gamma(\alpha-\beta)}\int_{1}^{t}\big(\log\frac{t}{s}\big)^{\alpha-\beta-1} z_{i}(s)ds \\ &-\frac{(\log t)^{1-\beta}}{\Gamma(\alpha-1)\Gamma(2-\beta)} \sum\limits_{j = 1}^{k} \Bigg(\frac{\lambda_{j}^{-1}}{\sum\nolimits_{j = 1}^{k}\lambda_{j}^{-1}}\Bigg) \int_{1}^{e}\Big(\log\frac{e}{s}\Big)^{\alpha-2}z_{j}(s)ds \\ &+\frac{(\log t)^{1-\beta}}{\Gamma(\alpha)\Gamma(2-\beta)} \sum\limits_{\substack{j = 1\\ j\neq i}}^{k}\Bigg(\frac{\lambda_{j}^{-1}}{\sum\nolimits_{j = 1}^{k}\lambda_{j}^{-1}}\Bigg) \int_{1}^{e}\Big(\log\frac{e}{s}\Big)^{\alpha-1} z_{j}(s)ds \\ &-\frac{(\log t)^{1-\beta}}{\Gamma(\alpha)\Gamma(2-\beta)} \sum\limits_{\substack{j = 1\\ j\neq i}}^{k}\Bigg(\frac{\lambda_{j}^{-1}}{\sum\nolimits_{j = 1}^{k}\lambda_{j}^{-1}}\Bigg) \int_{1}^{e}\Big(\log\frac{e}{s}\Big)^{\alpha-1} z_{i}(s)ds, \end{align*} |
and here
z_{i}(s) = \frac{h_{i}(s)}{s},\; h_{i}(s) = \varrho_{i}^{\alpha}f_{i}\big(s,r_{i}(s),{}^{H}D^{\beta}_{1^{+}}r_{i}(s)\big),\; i = 1,2,\cdots,14. |
Proof. From Remark 4.3, we have
\begin{eqnarray} \left\{\begin{array}{l} {}^{H}D^{\alpha}_{1^{+}} r_{i}(t) = \varrho_{i}^{\alpha}\phi_{p}\left(f_{i}\big(s,r_{i}(s),{}^{H}D^{\beta}_{1^{+}}r_{i}(s)\big)\right)+\varphi_{i}(t),\; t \in [1,e], \\ r_{i}(1) = 0,\; i = 1,2,\cdots,14,\\ r_{i}(e) = r_{j}(e),\; i,j = 1,2,\cdots,14,\; i\neq j,\\ \sum\limits_{i = 1}^{k}\varrho_{i}^{-1}r'_{i}(e) = 0,\; i = 1,2,\cdots,14. \end{array}\right. \end{eqnarray} | (4.2) |
By Lemma 2.7, the solution of (4.2) can be given in the following form:
\begin{eqnarray*} r_{i}(t)& = &\frac{1}{\Gamma(\alpha)}\int_{1}^{t}\Big(\log\frac{t}{s}\Big)^{\alpha-1} \left(z_{i}(s)+\frac{\varphi_{i}(s)}{s}\right)ds \notag\ \\ &&-\frac{\log t}{\Gamma(\alpha-1)} \sum\limits_{j = 1}^{k}\Bigg(\frac{\lambda_{j}^{-1}}{\sum\nolimits_{j = 1}^{k}\lambda_{j}^{-1}}\Bigg) \int_{1}^{e}\Big(\log\frac{e}{s}\Big)^{\alpha-2} \left(z_{j}(s)+\frac{\varphi_{j}(s)}{s}\right)ds \notag\ \\ &&+\frac{\log t}{\Gamma(\alpha)} \sum\limits_{\substack{j = 1\\ j\neq i}}^{k}\Bigg(\frac{\lambda_{j}^{-1}}{\sum\nolimits_{j = 1}^{k}\lambda_{j}^{-1}}\Bigg) \int_{1}^{e}\Big(\log\frac{e}{s}\Big)^{\alpha-1}\left(z_{j}(s)+\frac{\varphi_{j}(s)}{s}\right)ds \notag\ \\ &&-\frac{\log t}{\Gamma(\alpha)} \sum\limits_{\substack{j = 1\\ j\neq i}}^{k}\Bigg(\frac{\lambda_{j}^{-1}}{\sum\nolimits_{j = 1}^{k}\lambda_{j}^{-1}}\Bigg) \int_{1}^{e}\Big(\log\frac{e}{s}\Big)^{\alpha-1}\left(z_{i}(s)+\frac{\varphi_{i}(s)}{s}\right)ds, \end{eqnarray*} |
and
\begin{eqnarray*} {}^{H}D^{\beta}_{1^{+}}r_{i}(t)& = & \frac{1}{\Gamma(\alpha-\beta)}\int_{1}^{t}\big(\log\frac{t}{s}\big)^{\alpha-\beta-1} \left(z_{i}(s)+\frac{\varphi_{i}(s)}{s}\right)ds \\ &&-\frac{(\log t)^{1-\beta}}{\Gamma(\alpha-1)\Gamma(2-\beta)} \sum\limits_{j = 1}^{k} \Bigg(\frac{\lambda_{j}^{-1}}{\sum\nolimits_{j = 1}^{k}\lambda_{j}^{-1}}\Bigg) \int_{1}^{e}\Big(\log\frac{e}{s}\Big)^{\alpha-2}\left(z_{j}(s)+\frac{\varphi_{j}(s)}{s}\right)ds \\ &&+\frac{(\log t)^{1-\beta}}{\Gamma(\alpha)\Gamma(2-\beta)} \sum\limits_{\substack{j = 1\\ j\neq i}}^{k}\Bigg(\frac{\lambda_{j}^{-1}}{\sum\nolimits_{j = 1}^{k}\lambda_{j}^{-1}}\Bigg) \int_{1}^{e}\Big(\log\frac{e}{s}\Big)^{\alpha-1} \left(z_{j}(s)+\frac{\varphi_{j}(s)}{s}\right)ds \\ &&-\frac{(\log t)^{1-\beta}}{\Gamma(\alpha)\Gamma(2-\beta)} \sum\limits_{\substack{j = 1\\ j\neq i}}^{k}\Bigg(\frac{\lambda_{j}^{-1}}{\sum\nolimits_{j = 1}^{k}\lambda_{j}^{-1}}\Bigg) \int_{1}^{e}\Big(\log\frac{e}{s}\Big)^{\alpha-1} \left(z_{i}(s)+\frac{\varphi_{i}(s)}{s}\right)ds. \end{eqnarray*} |
Then, we deduce that
\begin{eqnarray*} |r_{i}(t)-r_{i}^{*}(t)|&\leq& \varepsilon_{i}\frac{2e}{\Gamma(\alpha+1)} + \sum\limits_{j = 1}^{k}\varepsilon_{j}\frac{e}{\Gamma(\alpha)} + \sum\limits_{\substack{j = 1\\ j\neq i}}^{k}\varepsilon_{j}\frac{e}{\Gamma(\alpha+1)} \\ & = &\varepsilon_{i}e\Big(\frac{1}{\Gamma(\alpha)}+\frac{2}{\Gamma(\alpha+1)}\Big)+\varepsilon_{j}e \sum\limits_{\substack{j = 1\\ j\neq i}}^{k}\Big(\frac{1}{\Gamma(\alpha)}+\frac{1}{\Gamma(\alpha+1)}\Big) \end{eqnarray*} |
and
\begin{eqnarray*} |{}^{H}D^{\beta}_{1^{+}}r_{i}(t)-{}^{H}D^{\beta}_{1^{+}}r_{i}^{*}(t)| &\leq&\varepsilon_{i}\frac{e}{\Gamma(\alpha-\beta+1)}+\varepsilon_{j}\frac{e}{\Gamma(\alpha+1)\Gamma(2-\beta)} \\ &&+\varepsilon_{j} \sum\limits_{j = 1}^{k}\frac{e}{\Gamma(\alpha)\Gamma(2-\beta)} +\varepsilon_{i} \sum\limits_{\substack{j = 1\\ j\neq i}}^{k}\frac{e}{\Gamma(\alpha+1)\Gamma(2-\beta)} \\ & = &\varepsilon_{j}e \sum\limits_{\substack{j = 1\\ j\neq i}}^{k}\Big(\frac{1}{\Gamma(\alpha)\Gamma(2-\beta)}+\frac{1}{\Gamma(\alpha+1)\Gamma(2-\beta)}\Big) \\ &&+\varepsilon_{i}e\Big(\frac{1}{\Gamma(\alpha-\beta+1)}+\frac{1}{\Gamma(\alpha)\Gamma(2-\beta)} +\frac{1}{\Gamma(\alpha+1)\Gamma(2-\beta)}\Big). \end{eqnarray*} |
Theorem 4.6. Assume that Theorem 3.1 hold; then the fractional differential system (1.1) is Hyers-Ulam stable if the eigenvalues of matrix A are in the open unit disc. There exists |\lambda| < 1 for \lambda\in \mathbb C with det(\lambda I-A) = 0 , where
A = \begin{pmatrix} \theta_{1}(\varrho_{1}^{\alpha}+\varrho_{1}^{\alpha-\beta})(p-1)Q_{1}^{p-2}u_{1} & \theta_{2}(\varrho_{2}^{\alpha}+\varrho_{2}^{\alpha-\beta})(p-1)Q_{2}^{p-2}u_{2} & \cdots & \theta_{2}(\varrho_{12}^{\alpha}+\varrho_{12}^{\alpha-\beta})(p-1)Q_{12}^{p-2}u_{14} \\ \theta_{2}(\varrho_{1}^{\alpha}+\varrho_{1}^{\alpha-\beta})(p-1)Q_{1}^{p-2}u_{1} & \theta_{1}(\varrho_{2}^{\alpha}+\varrho_{2}^{\alpha-\beta})(p-1)Q_{2}^{p-2}u_{2} & \cdots & \theta_{2}(\varrho_{12}^{\alpha}+\varrho_{12}^{\alpha-\beta})(p-1)Q_{12}^{p-2}u_{14} \\ \vdots & \vdots & \ddots & \vdots\\ \theta_{2}(\varrho_{1}^{\alpha}+\varrho_{1}^{\alpha-\beta})(p-1)Q_{1}^{p-2}u_{1} & \theta_{2}(\varrho_{2}^{\alpha}+\varrho_{2}^{\alpha-\beta})(p-1)Q_{2}^{p-2}u_{2} & \cdots & \theta_{1}(\varrho_{12}^{\alpha}+\varrho_{12}^{\alpha-\beta})(p-1)Q_{12}^{p-2}u_{14} \end{pmatrix}. |
Proof. Let r = (r_{1}, r_{2}, ..., r_{14})\in X^k, \; k = 1, 2, \cdots14, be the solution of the inequality given by
\begin{equation*} \left|{}^{H}D^{\alpha}_{1^+}r_{i}(t)-\varrho_{i}^{\alpha}\phi_{p}\left( {f}_{i}\big(t,r_{i}(t),{}^{H}D^{\beta}_{1^+}r_{i}(t)\big)\right)\right| \leq\varepsilon_{i},\; t\in [1,e], \end{equation*} |
and \bar{r} = (\bar{r}_{1}, \bar{r}_{2}, ..., \bar{r}_{14})\in X^k be the solution of the following system:
\begin{eqnarray} \left\{\begin{array}{l} ^{H}D^{\alpha}_{1^{+}} \bar{r}_{i}(t) = \varrho_{i}^{\alpha}\phi_{p}\left(f_{i}\big(s,\bar{r}_{i}(s),{}^{H}D^{\beta}_{1^{+}}\bar{r}_{i}(s)\big)\right),\; t \in [1,e], \\ \bar{r}_{i}(1) = 0,\; i = 1,2,\cdots,14,\\ \bar{r}_{i}(e) = \bar{r}_{j}(e),\; i,j = 1,2,\cdots,14,\; i\neq j,\\ \sum\limits_{i = 1}^{k}\varrho_{i}^{-1}\bar{r}'_{i}(e) = 0,\; i = 1,2,\cdots,14. \end{array}\right. \end{eqnarray} | (4.3) |
By Lemma 2.7, the solution of (4.3) can be given in the following form:
\begin{eqnarray*} \bar{r}_{i}(t) & = &\frac{\varrho_{i}^{\alpha}}{\Gamma(\alpha)}\int_{1}^{t}\Big(\log\frac{t}{s}\Big)^{\alpha-1} \phi_{p}\left(g_{i}\big(s,\bar{r}_{i}(s),{}^{H}D^{\beta}_{1^{+}}\bar{r}_{i}(s)\big)\right)ds \\ &&-\frac{\log t}{\Gamma(\alpha-1)} \sum\limits_{j = 1}^{k}\Bigg(\frac{\varrho_{j}^{-1}}{\sum\nolimits_{j = 1}^{k}\varrho_{j}^{-1}}\Bigg) \varrho_{j}^{\alpha}\int_{1}^{e}\Big(\log\frac{e}{s}\Big)^{\alpha-2} \phi_{p}\left(g_{j}\big(s,\bar{r}_{j}(s),{}^{H}D^{\beta}_{1^{+}}\bar{r}_{j}(s)\big)\right)ds \\ &&+\frac{\log t}{\Gamma(\alpha)} \sum\limits_{\substack{j = 1\\ j\neq i}}^{k}\Bigg(\frac{\varrho_{j}^{-1}}{\sum\nolimits_{j = 1}^{k}\varrho_{j}^{-1}}\Bigg)\varrho_{j}^{\alpha} \int_{1}^{e}\Big(\log\frac{e}{s}\Big)^{\alpha-1} \phi_{p}\left(g_{j}\big(s,\bar{r}_{j}(s),{}^{H}D^{\beta}_{1^{+}}\bar{r}_{j}(s)\big)\right)ds \\ &&-\frac{\log t}{\Gamma(\alpha)} \sum\limits_{\substack{j = 1\\ j\neq i}}^{k}\Bigg(\frac{\varrho_{j}^{-1}}{\sum\nolimits_{j = 1}^{k}\varrho_{j}^{-1}}\Bigg)\varrho_{i}^{\alpha} \int_{1}^{e}\Big(\log\frac{e}{s}\Big)^{\alpha-1} \phi_{p}\left(g_{i}\big(s,\bar{r}_{i}(s),{}^{H}D^{\beta}_{1^{+}}\bar{r}_{i}(s)\big)\right)ds. \end{eqnarray*} |
Now, by Lemma 4.5, for t\in[1, e] , we can get
\begin{eqnarray*} |r_{i}(t)-\bar{r}_{i}(t)| &\leq& |r_{i}(t)-r_{i}^{*}(t)|+|r_{i}^{*}(t)-\bar{r}_{i}(t)|\\ &\leq& \varepsilon_{i}e\Big(\frac{1}{\Gamma(\alpha)}+\frac{2}{\Gamma(\alpha+1)}\Big)+\varepsilon_{j}e \sum\limits_{\substack{j = 1\\ j\neq i}}^{k}\Big(\frac{1}{\Gamma(\alpha)}+\frac{1}{\Gamma(\alpha+1)}\Big)\\ &&+e\Big(\frac{1}{\Gamma(\alpha)}+\frac{2}{\Gamma(\alpha+1)}\Big) (\varrho_{i}^{\alpha}+\varrho_{i}^{\alpha-\beta})(p-1)Q_{i}^{p-2}u_{i}(t) \left(\|r_{i}-\bar{r}_{i}\|+\left\|{}^{H}D^{\beta}_{1^{+}}r_{i}-{}^{H}D^{\beta}_{1^{+}}\bar{r}_{i}\right\|\right) \\ &&+e\Big(\frac{1}{\Gamma(\alpha)}+\frac{1}{\Gamma(\alpha+1)}\Big) \sum\limits_{\substack{j = 1\\ j\neq i}}^{k} (\varrho_{j}^{\alpha}+\varrho_{j}^{\alpha-\beta})(p-1)Q_{i}^{p-2}u_{j}(t) \left(\|r_{j}-\bar{r}_{j}\|+\left\|{}^{H}D^{\beta}_{1^{+}}r_{j}-{}^{H}D^{\beta}_{1^{+}}\bar{r}_{j}\right\|\right) \end{eqnarray*} |
and
\begin{eqnarray*} \left|{}^{H}D^{\beta}_{1^+}r_{i}(t)-{}^{H}D^{\beta}_{1^+}\bar{r}_{i}(t)\right| &\leq& \left|{}^{H}D^{\beta}_{1^+}r_{i}(t)-{}^{H}D^{\beta}_{1^+}r_{i}^{*}(t)\right| +\left|{}^{H}D^{\beta}_{1^+}r_{i}^{*}(t)-{}^{H}D^{\beta}_{1^+}\bar{r}_{i}(t)\right|\\ &\leq&\varepsilon_{j}e \sum\limits_{\substack{j = 1\\ j\neq i}}^{k}\Big(\frac{1}{\Gamma(\alpha)\Gamma(2-\beta)}+\frac{1}{\Gamma(\alpha+1)\Gamma(2-\beta)}\Big) \\ &&+\varepsilon_{i}e\Big(\frac{1}{\Gamma(\alpha-\beta+1)}+\frac{1}{\Gamma(\alpha)\Gamma(2-\beta)} +\frac{1}{\Gamma(\alpha+1)\Gamma(2-\beta)}\Big)\\ &&+e\Big(\frac{1}{\Gamma(\alpha-\beta+1)}+\frac{1}{(\Gamma(\alpha)\Gamma(2-\beta)} +\frac{1}{\Gamma(\alpha+1)\Gamma(2-\beta)}\Big)\notag\ \\ &&\times(\varrho_{i}^{\alpha}+\varrho_{i}^{\alpha-\beta})(p-1)Q_{i}^{p-2}u_{i}(t) \left(\|r_{i}-\bar{r}_{i}\|+\left\|{}^{H}D^{\beta}_{1^{+}}r_{i}-{}^{H}D^{\beta}_{1^{+}}\bar{r}_{i}\right\|\right)\notag\ \\ &&+e\Big(\frac{1}{\Gamma(\alpha)\Gamma(2-\beta)}+\frac{1}{\Gamma(\alpha+1)\Gamma(2-\beta)}\Big) \sum\limits_{\substack{j = 1\\ j\neq i}}^{k}(\varrho_{j}^{\alpha}+\varrho_{j}^{\alpha-\beta})\notag\ \\ &&\times (p-1)Q_{i}^{p-2}u_{j}(t)\left(\|r_{j}-\bar{r}_{j}\|+\left\|{}^{H}D^{\beta}_{1^{+}}r_{j}-{}^{H}D^{\beta}_{1^{+}}\bar{r}_{j}\right\|\right). \end{eqnarray*} |
Hence, we have
\begin{eqnarray*} \|r_{i}-\bar{r}_{i}\|_{X} & = &\|r_{i}-\bar{r}_{i}\|+\left\|{}^{H}D^{\beta}_{1^+}r_{i}(t)-{}^{H}D^{\beta}_{1^+}\bar{r}_{i}(t)\right\|\\ &\leq& e\left(\frac{\alpha+2}{\Gamma(\alpha+1)}+\frac{1}{\Gamma(\alpha-\beta+1)}+\frac{\alpha+1}{\Gamma(\alpha+1)\Gamma(2-\beta)}\right) \varepsilon_{i} \\ &&+e \sum\limits_{\substack{j = 1\\ j\neq i}}^{k}\left(\frac{\alpha+1}{\Gamma(\alpha+1)}+\frac{\alpha+1}{\Gamma(\alpha+1)\Gamma(2-\beta)}\right)\varepsilon_{j} \\ &&+e\left(\frac{\alpha+2}{\Gamma(\alpha+1)}+\frac{1}{\Gamma(\alpha-\beta+1)}+\frac{\alpha+1}{\Gamma(\alpha+1)\Gamma(2-\beta)}\right)\\ &&\times(\varrho_{i}^{\alpha}+\varrho_{i}^{\alpha-\beta})(p-1)Q_{i}^{p-2}u_{i}(t) (\|r_{i}-\bar{r}_{i}\|_{X} \\ &&+e \sum\limits_{\substack{j = 1\\ j\neq i}}^{k}\left(\frac{\alpha+1}{\Gamma(\alpha+1)}+\frac{\alpha+1}{\Gamma(\alpha+1)\Gamma(2-\beta)}\right) (\varrho_{j}^{\alpha}+\varrho_{j}^{\alpha-\beta})(p-1)Q_{i}^{p-2}u_{j}(t) \|r_{j}-\bar{r}_{j}\|_{X} \\ & = &\theta_{1}\varepsilon_{i}+ \sum\limits_{\substack{j = 1\\ j\neq i}}^{k}\theta_{2}\varepsilon_{i}+\theta_{1}(\varrho_{i}^{\alpha}+\varrho_{i}^{\alpha-\beta})(p-1)Q_{i}^{p-2}u_{i}(t) \|r_{i}-\bar{r}_{i}\|_{X} \\ &&+ \sum\limits_{\substack{j = 1\\ j\neq i}}^{k}\theta_{2}(\varrho_{j}^{\alpha}+\varrho_{j}^{\alpha-\beta})(p-1)Q_{i}^{p-2}u_{j}(t) \|r_{j}-\bar{r}_{j}\|_{X}, \end{eqnarray*} |
where
\begin{eqnarray*} &&\theta_{1} = e\left(\frac{\alpha+2}{\Gamma(\alpha+1)} +\frac{1}{\Gamma(\alpha-\beta+1)}+\frac{\alpha+1}{\Gamma(\alpha+1)\Gamma(2-\beta)}\right),\\ &&\theta_{2} = e\left(\frac{\alpha+1}{\Gamma(\alpha+1)}+\frac{\alpha+1}{\Gamma(\alpha+1)\Gamma(2-\beta)}\right). \end{eqnarray*} |
Then we have
\begin{eqnarray*} &&(\|r_{1}-\bar{r}_{1}\|_{X}, \|r_{2}-\bar{r}_{2}\|_{X},..., \|r_{14}-\bar{r}_{14}\|_{X})^{T}\\ &\leq& B(\varepsilon_{1}, \varepsilon_{2},..., \varepsilon_{12})^{T} + A(\|r_{1}-\bar{r}_{1}\|_{X}, \|r_{2}-\bar{r}_{2}\|_{X},..., \|r_{14}-\bar{r}_{14}\|_{X})^{T}, \end{eqnarray*} |
where
B_{14\times 14} = \begin{pmatrix} \theta_{1} & \theta_{2} & \cdots & \theta_{2}\\ \theta_{2} & \theta_{1} & \cdots & \theta_{2}\\ \vdots & \vdots & \ddots & \vdots\\ \theta_{2} & \theta_{2} & \cdots & \theta_{1} \end{pmatrix}. |
Then, we can get
\begin{eqnarray*} (\|r_{1}-\bar{r}_{1}\|_{X}, \|r_{2}-\bar{r}_{2}\|_{X},..., \|r_{14}-\bar{r}_{14}\|_{X})^{T} \leq (I-A)^{-1}B(\varepsilon_{1}, \varepsilon_{2},..., \varepsilon_{14})^{T}. \end{eqnarray*} |
Let
H = (I-A)^{-1}B = \begin{pmatrix} h_{1,1} & h_{1,2} & \cdots & h_{1,14}\\ h_{2,1} & h_{2,2} & \cdots & h_{2,14}\\ \vdots & \vdots & \ddots & \vdots\\ h_{14,1} & h_{14,2} & \cdots & h_{14,14} \end{pmatrix}. |
Obviously, h_{i, j} > 0, \; i, j = 1, 2, \cdots, 14 . Set \varepsilon = max\{\varepsilon_{1}, \varepsilon_{2}, ..., \varepsilon_{14} \} , then we can get
\begin{equation} \|r-\bar{r}\|_{X^{k}}\leq \big(\sum\limits_{\substack{j = 1}}^{k} \sum\limits_{\substack{i = 1}}^{k}h_{i,j}\big)\varepsilon. \end{equation} | (4.4) |
Thus, we have derived that system (1.1) is Hyers-Ulam stable.
Remark 4.7. Making \psi_{f_{1}, f_{2}, ..., f_{k}}(\varepsilon) in (4.4). We have \psi_{f_{1}, f_{2}, ..., f_{k}}(0) = 0 . Then by Definition 4.2, we deduce that the fractional differential system (1.1) is generalized Hyers-Ulam stable.
The benzoic acid graph we studied in the system (1.1) can be extended to other types of graphs. For example, star graphs and chord bipartite graphs provide a theoretical basis for physics, computer networks, and other fields. Here we only discuss the fractional differential system on the star graphs (i = 1, 2, 3). We discuss the solution of a fractional differential equation on a formaldehyde graph, and the approximate graphs of solutions are presented by using iterative methods and numerical simulation.
Example 5.1. Consider the following fractional differential equation:
\begin{eqnarray} \left\{\begin{array}{l} {}^{H}D_{1^{+}}^{\frac{7}{4}} r_{1}(t)+(\frac{1}{3})^{\frac{7}{4}}\phi_{3}\left(1+\frac{t}{5(t+3)^{5}}\left(sin(r_{1}(t)+ \frac{|{}^{H}D_{1^{+}}^{\frac{3}{4}} r_{1}(t)|}{1+|{}^{H}D_{1^{+}}^{\frac{3}{4}} r_{1}(t)|}\right)\right) = 0, \\ {}^{H}D_{1^{+}}^{\frac{7}{4}} r_{2}(t)+(\frac{1}{2})^{\frac{7}{4}}\phi_{3}\left(1+\frac{t}{(t+2)^{7}}\left(sin(r_{2}(t)+ \frac{|{}^{H}D_{1^{+}}^{\frac{3}{4}} r_{2}(t)|}{1+|{}^{H}D_{1^{+}}^{\frac{3}{4}} r_{2}(t)|}\right)\right) = 0,\\ {}^{H}D_{1^{+}}^{\frac{7}{4}} r_{3}(t)+(\frac{2}{3})^{\frac{7}{4}}\phi_{3}\left(1+\frac{t}{1000}|arcsin(r_{3}(t))|+ \frac{t|{}^{H}D_{1^{+}}^{\frac{3}{4}} r_{3}(t)|}{1000(1+|{}^{H}D_{1^{+}}^{\frac{3}{4}} r_{3}(t)|)}\right) = 0,\\ r_{1}(1) = r_{2}(1) = r_{3}(1) = 0,\\ r_{1}(e) = r_{2}(e) = r_{3}(e),\\ (\frac{1}{3})^{-1}r'_{1}(e)+(\frac{1}{2})^{-1}r'_{2}(e)+(\frac{2}{3})^{-1}r'_{3}(e) = 0, \end{array}\right. \end{eqnarray} | (5.1) |
corresponding to the system (1.1), we obtain
\alpha = \frac{7}{4},\; \beta = \frac{3}{4},\; k = 3,\; \varrho_{1} = \frac{1}{3},\; \varrho_{2} = \frac{1}{2},\; \varrho_{3} = \frac{2}{3}. |
Figure 3 (The structure of formaldehyde) is from reference[22]. Coordinate systems with r_{1}, \; r_{2}, and r_{3} are established, respectively, on the formaldehyde graph with 3 edges (Figure 4).
For t\in [1, e],
\begin{eqnarray*} g_{1}\big(t,r_{1}(t),{}^{H}D^{\beta}_{1^{+}}r_{1}(t)\big)& = &1+\frac{1}{5(t+3)^{2}}\left(sin(r_{1}(t)+ \frac{|{}^{H}D_{1^{+}}^{\frac{3}{4}} r_{1}(t)|}{1+|{}^{H}D_{1^{+}}^{\frac{3}{4}} r_{1}(t)|}\right),\\ g_{2}\big(t,r_{2}(t),{}^{H}D^{\beta}_{1^{+}}r_{2}(t)\big)& = &1+\frac{1}{(t+2)^{7}}\left(sin(r_{2}(t)+ \frac{|{}^{H}D_{1^{+}}^{\frac{3}{4}} r_{2}(t)|}{1+|{}^{H}D_{1^{+}}^{\frac{3}{4}} r_{2}(t)|}\right),\\ g_{3}\big(t,r_{3}(t),{}^{H}D^{\beta}_{1^{+}}r_{3}(t)\big)& = &1+\frac{t}{1000}|arcsin(r_{3}(t))|+ \frac{t|{}^{H}D_{1^{+}}^{\frac{3}{4}} r_{3}(t)|}{1000(1+|{}^{H}D_{1^{+}}^{\frac{3}{4}} r_{3}(t)|)}. \end{eqnarray*} |
For any x, \; y, \; x_{1}, \; y_{1} , it is clear that
g_{1}(t,x,y)-g_{1}(t,x_{1},y_{1})\leq\frac{1}{5(t+3)^{2}}(|x-x_{1}|+|y-y_{1}|), |
g_{2}(t,x,y)-g_{2}(t,x_{2},y_{2})\leq\frac{1}{(t+2)^{7}}(|x-x_{2}|+|y-y_{2}|), |
g_{3}(t,x,y)-g_{3}(t,x_{3},y_{3})\leq \frac{t}{1000}(|x-x_{3}|+|y-y_{3}|). |
So we get
u_{1} = \sup\limits_{t\in[1,e]}|u_{1}(t)| = \frac{1}{5120}, u_{2} = \sup\limits_{t\in[1,e]}|u_{2}(t)| = \frac{1}{2187}, u_{3} = \sup\limits_{t\in[1,e]}|u_{3}(t)| = \frac{e}{1000}, |
\chi_{1} = 51.9811, \chi_{2} = 54.7872, \chi_{3} = 58.0208, |
and
(\chi_{1}+\chi_{2}+\chi_{3})(u_{1}+u_{2}+u_{3}) = 0.5555 < 1. |
Therefore, by Theorem 3.1, system (5.1) has a unique solution on [1, e] .
Meanwhile,
\theta_{1} = 14.1839,\; \; \; \; \theta_{2} = 9.7755, |
A = \begin{pmatrix} 2.6581e-03 & 7.134e-03 & 6.1901e-02\\ 1.832e-03 & 1.0351e-02 & 6.1901e-02\\ 1.832e-03 & 7.134e-03 & 8.9816e-02 \end{pmatrix}. |
Let
det(\lambda I-A) = (\lambda-0.0964)(\lambda-0.0011)(\lambda-0.0054) = 0, |
so we have
\lambda_{1} = 0.0964 < 1, \; \; \; \lambda_{2} = 0.0011 < 1, \; \; \; \lambda_{3} = 0.0054 < 1. |
It follows from Theorem 4.6 that system (5.1) is Hyer-Ulams stable, and by Remark 4.4, it will be generalized Hyer-Ulams stable.
Ultimately, the iterative process curve and approximate solution to the fractional differential system (5.1) are carried out by using the iterative method and numerical simulation. Let u_{i, 0} = 0 , the iteration sequence is as follows:
\begin{eqnarray*} r_{1,n+1}(t)& = & -\frac{(\frac{1}{3})^{\frac{7}{4}}}{\Gamma{(\frac{7}{4})}} \int_{1}^{t}\left(\log \frac{t}{s}\right)^{\frac{3}{4}}\phi_{3}\left(1+\frac{1}{5(t+3)^{2}} \left(sin(r_{1,n}(t)) + \frac{|{}^{H}D_{1^+}^{\frac{3}{4}}r_{1,n}(t)|} {1+|{}^{H}D_{1^+}^{\frac{3}{4}}r_{1,n}(t)|}\right)\right) ds\\ &&- \frac{(\frac{1}{3})^{\frac{7}{4}}(\frac{1}{2})^{-1}(\log t)} {\bigg((\frac{1}{3})^{-1}+(\frac{1}{2})^{-1} +(\frac{2}{3})^{-1}\bigg)\Gamma(\frac{7}{4})} \int_{1}^{e}(1-\log s)^{\frac{3}{4}}\phi_{3}\Bigg(1+\frac{1}{(t+2)^7} \Bigg(sin|r_{2,n}(t)|\\ &&+ \frac{|{}^{H}D^{\frac{3}{4}}_{1^+}r_{2,n}(t)|}{1+|{}^{H}D^{\frac{3}{4}}_{1^+}r_{2,n}(t)|}\Bigg)\Bigg)ds - \frac{(\frac{1}{3})^{\frac{7}{4}}(\frac{1}{2})^{-1}(\log t)} {\bigg((\frac{1}{3})^{-1}+(\frac{1}{2})^{-1} +(\frac{2}{3})^{-1}\bigg)\Gamma(\frac{7}{4})}\int_{1}^{e}(1-\log s)^{\frac{3}{4}}\\ &&\times\phi_{3}\left(\Bigg(1+0.001t |arcsin(r_{3,n}(t))| + \frac{t |{}^{H}D^{\frac{3}{4}}_{1^+}r_{3,n}(t)|} {1000+1000 |{}^{H}D^{\frac{3}{4}}_{1^+}r_{3,n}(t)|}\Bigg)\right) ds\\ &&+ \frac{(\frac{1}{2})^{-1}(\frac{1}{3})^{\frac{7}{4}}(\log t)} {\bigg((\frac{1}{3})^{-1}+(\frac{1}{2})^{-1} +(\frac{2}{3})^{-1}\bigg)\Gamma(\frac{7}{4})} \int_{1}^{e}(1-\log s)^{\frac{3}{4}} \phi_{3}\Bigg(1+\frac{1}{5(t+3)^{2}} \Bigg(sin(r_{1,n}(t))\\ &&+ \frac{|{}^{H}D_{1^+}^{\frac{3}{4}}r_{1,n}(t)|} {1+|{}^{H}D_{1^+}^{\frac{3}{4}}r_{1,n}(t)|}\Bigg)\Bigg)ds +\frac{(\frac{1}{3})^{\frac{7}{4}}(\frac{2}{3})^{-1}(\log t)} {\bigg((\frac{1}{3})^{-1}+(\frac{1}{2})^{-1} +(\frac{2}{3})^{-1}\bigg)\Gamma(\frac{7}{4})}\int_{1}^{e}(1-\log s)^{\frac{3}{4}}\\ &&\times \phi_{3}\Bigg(1+\frac{1}{5(t+3)^{2}} \Bigg(sin(r_{1,n}(t)) + \frac{|{}^{H}D_{1^+}^{\frac{3}{4}}r_{1,n}(t)|} {1+|{}^{H}D_{1^+}^{\frac{3}{4}}r_{1,n}(t)|}\Bigg)\Bigg) ds\\ &&+ \frac{(\frac{1}{3})^{\frac{7}{4}}(\frac{1}{3})^{-1}(\log t)} {\bigg((\frac{1}{3})^{-1}+(\frac{1}{2})^{-1} +(\frac{2}{3})^{-1}\bigg)}\frac{1}{\Gamma(\frac{3}{4})}\int_{1}^{e}(1-\log s)^{-\frac{1}{2}} \phi_{3}\Bigg(1+\frac{1}{5(t+3)^{2}}\\ &&\times\Bigg(sin(r_{1,n}(t)) +\frac{|{}^{H}D_{1^+}^{\frac{3}{4}}r_{1,n}(t)|} {1+|{}^{H}D_{1^+}^{\frac{3}{4}}r_{1,n}(t)|}\Bigg)\Bigg)ds +\frac{(\frac{1}{2})^{\frac{5}{2}}(\frac{1}{2})^{-1}(\log t)} {\bigg((\frac{1}{4})^{-1}+(\frac{1}{2})^{-1} +(\frac{2}{3})^{-1}\bigg)\Gamma(\frac{3}{4})}\\ &&\times\int_{1}^{e}(1-\log s)^{-\frac{1}{2}}\phi_{3}\Bigg(1+\frac{1}{(t+2)^7}\Bigg(sin|r_{2,n}(t)| +\frac{|D^{\frac{3}{4}}_{1^+}r_{2,n}(t)|}{1+ |D^{\frac{3}{4}}_{1^+}r_{2,n}(t)|}\Bigg)\Bigg)ds\\ &&+ \frac{(\frac{2}{3})^{\frac{7}{4}}(\frac{2}{3})^{-1}(\log t)} {\bigg((\frac{1}{3})^{-1}+(\frac{1}{2})^{-1} +(\frac{2}{3})^{-1}\bigg)\Gamma(\frac{3}{2})}\int_{1}^{e}(1-\log s)^{-\frac{1}{2}} \phi_{3}\Bigg(1+0.003t \\ &&\times|arcsin(r_{3,n}(t))|+ \frac{t|{}^{H}D^{\frac{3}{4}}_{1^+}r_{3,n}(t)|} {1000+1000|{}^{H}D^{\frac{3}{4}}_{1^+}r_{3,n}(t)|}\Bigg)\Bigg)ds. \end{eqnarray*} |
The iterative sequence of r_{2, n+1} and r_{3, n+1} is similar to r_{1, n+1} . After several iterations, the approximate solution of fractional differential system (5.1) can be obtained by using the numerical simulation. Figure 5 is the approximate graph of the solution of \overrightarrow{r_{1}r_{0}} after iterations. Figure 6 is the approximate graph of the solution of \overrightarrow{r_{2}r_{0}} after iterations. Figure 7 is the approximate graph of the solution of \overrightarrow{r_{3}r_{0}} after iterations.
Using the idea of star graphs, several scholars have studied the solutions of fractional differential equations. They chose to utilize star graphs since their method required a central node connected to nearby vertices through interconnections, but there are no edges between the nodes.
The purpose of this study was to extend the technique's applicability by introducing the concept of a benzoic acid graph, a fundamental molecule in chemistry with the formula C_{7}H_{6}O_{2} . In this manner, we explored a network in which the vertices were either labeled with 0 or 1, and the structure of the chemical molecule benzoic acid was shown to have an effect on this network. To study whether or not there were solutions to the offered boundary value problems within the context of the Caputo fractional derivative with p -Laplacian operators, we used the fixed-point theorems developed by Krasnoselskii. Meanwhile, the Hyers-Ulam stability has been considered. In conclusion, an example was given to illustrate the significance of the findings obtained from this research line.
The following open problems are presented for the consideration of readers interested in this topic: At present, the research prospects of fractional boundary value problems and their numerical solutions on graphs are very broad, which can be extended to other graphs, such as chord bipartite graphs. The follow-up research process, especially the research on chemical graph theory, has a certain practical significance. This is because such research does not need chemical reagents and experimental equipment. In the absence of experimental conditions and reagents, the molecular structure is studied, and the same results are obtained under experimental conditions. Although the differential equation on the benzoic acid graph is studied in this paper, the molecular structure is not studied by the topological index in the research process. It can be tried later to provide a theoretical basis for the study of reverse engineering and provide new ideas for the study of mathematics, chemistry, and other fields.
Yunzhe Zhang: Writing-original draft, formal analysis, investigation; Youhui Su: Supervision, writing-review, editing and project administration; Yongzhen Yu: Resources, editing. All authors have read and approved the final version of the manuscript for publication.
The authors declare they have not used Artificial Intelligence (AI) tools in the creation of this article.
This work is supported by the Xuzhou Science and Technology Plan Project (KC23058) and the Natural Science Research Project of Jiangsu Colleges and Universities (22KJB110026).
The author declares no conflicts of interest.
[1] | Nakajima T, Kajiwara K, McIntyre JE (1994) Advanced Fiber Spinning Technology, Woodhead Publishing. |
[2] |
Li D, Xia Y (2004) Electrospinning of Nanofibers: Reinventing the Wheel? Adv Mater 16: 1151–1170. doi: 10.1002/adma.200400719
![]() |
[3] |
Subbiah T, Bhat GS, Tock RW, et al. (2005) Electrospinning of Nanofibers. J Appl Polym Sci 96: 557–569. doi: 10.1002/app.21481
![]() |
[4] |
Greiner A, Wendorff JH (2007) Electrospinning: A Fascinating Method for the Preparation of Ultrathin Fibers. Angew Chem Int Edit 46: 5670–5703. doi: 10.1002/anie.200604646
![]() |
[5] |
Lackowski M, Krupa A, Jaworek A (2011) Nonwoven Filtration Mat Production by Electrospinning Method. J Phys Conf Ser 301: 012013. doi: 10.1088/1742-6596/301/1/012013
![]() |
[6] | Filatov Y, Budyka A, Kirichenko V (2007) Electrospinning of Micro- and Nanofibers: Fundamentals and Applications in Separation and Filtration Processes, Moscow: Begell House Inc. |
[7] |
Lemma SM, Esposito A, Mason M, et al. (2015) Removal of bacteria and yeast in water and beer by nylon nanofibrous membranes. J Food Eng 157: 1–6. doi: 10.1016/j.jfoodeng.2015.02.005
![]() |
[8] |
Wang X, Kim YG, Drew C, et al. (2004) Electrostatic Assembly of Conjugated Polymer Thin Layers on Electrospun Nanofibrous Membranes for Biosensors. Nano Lett 4: 331–334. doi: 10.1021/nl034885z
![]() |
[9] |
Ashammakhi N, Ndreu A, Yang Y, et al. (2012) Nanofiber-based scaffolds for tissue engineering. Eur J Plast Surg 35: 135–149. doi: 10.1007/s00238-008-0217-3
![]() |
[10] |
Schnell E, Klinkhammer K, Balzer S, et al. (2007) Guidance of glial cell migration and axonal growth on electrospun nanofibers of poly-epsilon-caprolactone and a collagen/polyepsilon-caprolactone blend. Biomaterials 28: 3012–3025. doi: 10.1016/j.biomaterials.2007.03.009
![]() |
[11] |
Klinkhammer K, Seiler N, Grafahrend D, et al. (2009) Deposition of electrospun fibers on reactive substrates for in vitro investigations. Tissue Eng Part C 15: 77–85. doi: 10.1089/ten.tec.2008.0324
![]() |
[12] |
Großerhode C, Wehlage D, Grothe T, et al. (2017) Investigation of microalgae growth on electrospun nanofiber mats. AIMS Bioeng 4: 376–385. doi: 10.3934/bioeng.2017.3.376
![]() |
[13] |
Natu MV, de Sousa HC, Gil MH (2011) Electrospun Drug-Eluting Fibers for Biomedical Applications, In: Zilberman M, Active Implants and Scaffolds for Tissue Regeneration. Studies in Mechanobiology, Tissue Engineering and Biomaterials, Berlin, Heidelberg: Springer, 8: 57–85. doi: 10.1007/8415_2010_56
![]() |
[14] |
Pan JF, Liu NH, Sun H, et al. (2014) Preparation and Characterization of Electrospun PLCL/Poloxamer Nanofibers and Dextran/Gelatin Hydrogels for Skin Tissue Engineering. PLoS One 9: e112885. doi: 10.1371/journal.pone.0112885
![]() |
[15] |
Gu JY, Liu NH, Yang XR, et al. (2014) Adiposed-derived stem cells seeded on PLCL/P123 eletrospun nanofibrous scaffold enhance wound healing. Biomed Mater 9: 035012. doi: 10.1088/1748-6041/9/3/035012
![]() |
[16] |
Maslakci NN, Ulusoy S, Uygun E, et al. (2017) Ibuprofen and acetylsalicylic acid loaded electrospun PVP-dextran nanofiber mats for biomedical applications. Polym Bull 74: 3283–3299. doi: 10.1007/s00289-016-1897-7
![]() |
[17] |
Kumar YS, Unnithan AR, Sen D, et al. (2015) Microgravity biosynthesized penicillin loaded electrospun polyurethane-dextran nanofibrous mats for biomedical applications. Colloid Surface A 477: 77–83. doi: 10.1016/j.colsurfa.2015.01.065
![]() |
[18] |
Rzayev ZMO, Bunyatova U, Simsek M (2017) Multifunctional colloidal nanofiber composites including dextran and folic acid as electro-active platforms. Carbohyd Polym 166: 83–92. doi: 10.1016/j.carbpol.2017.02.100
![]() |
[19] |
Deitzel JM, Kleinmeyer J, Harris D, et al. (2001) The Effect of Processing Variables on the Morphology of Electrospun Nanofibers and Textiles. Polymer 42: 261–272. doi: 10.1016/S0032-3861(00)00250-0
![]() |
[20] | Grothe T, Brikmann J, Meissner H, et al. (2017) Influence of Solution and Spinning Parameters on Nanofiber Mat Creation of Poly(ethylene oxide) by Needleless Electrospinning. Mater Sci 23: 342–349. |
[21] |
Grimmelsmann N, Grothe T, Homburg SV, et al. (2017) Electrospinning and stabilization of chitosan nanofiber mats. IOP Conf Ser Mater Sci Eng 254: 102006. doi: 10.1088/1757-899X/254/10/102006
![]() |
[22] | Böttjer R, Grothe T, Ehrmann A (2018) Functional Nanofiber Mats for Medical and Biotechnological Applications, In: Kyosev Y, Mahltig B, Schwarz-Pfeiffer A, Narrow and Smart Textiles, Springer International Publishing. |
[23] |
Panthi G, Park SJ, Chae SH, et al. (2017) Immobilization of Ag3PO4 nanoparticles on electrospun PAN nanofibers via surface oximation: Bifunctional composite membrane with enhanced photocatalytic and antimicrobial activities. J Ind Eng Chem 45: 277–286. doi: 10.1016/j.jiec.2016.09.035
![]() |
[24] |
Neisiany RE, Lee JKY, Khorasani SN, et al. (2017) Self-healing and interfacially toughened carbon fibre-epoxy composites based on electrospun core-shell nanofibers. J Appl Polym Sci 134: 44956. doi: 10.1002/app.44956
![]() |
[25] |
Kim GH, Park SH, Birajdar MS, et al. (2017) Core/shell structured carbon nanofiber/platinum nanoparticle hybrid web as a counter electrode for dye-sensitized solar cell. J Ind Eng Chem 52: 211–217. doi: 10.1016/j.jiec.2017.03.046
![]() |
[26] |
Guo JY, Niu QJ, Yuan YC, et al. (2017) Electrospun core-shell nanofibers derived Fe-S/N doped carbon material for oxygen reduction reaction. Appl Surf Sci 416: 118–123. doi: 10.1016/j.apsusc.2017.04.135
![]() |
[27] | Sabantina L, Mirasol JR, Cordero T, et al. (2018) Investigation of Needleless Electrospun PAN Nanofiber Mats. AIP Conf Proc, In press. |
[28] |
Liu C, Lafdi K (2017) Fabrication and characterization of carbon nanofibers from polyacrylonitrile/pitch blends. J Appl Polym Sci 134: 45388. doi: 10.1002/app.45388
![]() |
[29] |
Ju YW, Oh GY (2017) Behavior of toluene adsorption on activated carbon nanofibers prepared by electrospinning of a polyacrylonitrile-cellulose acetate blending solution. Korean J Chem Eng 34: 2731–2737. doi: 10.1007/s11814-017-0171-5
![]() |
[30] | Liu YW, Peng XX, Cao Q, et al. (2017) Gel Polymer Electrolyte Based on Poly(vinylidene fluoride)/Thermoplastic Polyurethane/Polyacrylonitrile by the Electrospinning Technique. J Phys Chem C 35: 19140–19146. |
[31] | Böttjer R, Grothe T, Wehlage D, et al. (2018) Electrospraying poloxamer/(bio-)polymer blends using a needleless electrospinning machine. J Text Fib Mater 1: 2515221117743079. |
[32] | Grothe T, Grimmelsmann N, Homburg SV, et al. (2017) Green Electrospinning of Nanofiber Mats from Biopolymers for Medical and Biotechnological Applications, In: Mahltig B, Textiles: Advances in Research and Applications, Nova Science Publishers. |
[33] | Fuchs S, Hartmann J, Mazur P, et al. (2017) Electrospinning of Biopolymers and Biopolymer Blends. J Chem Pharm Sci 10: 1–3. |
1. | Okorie Ekwe Agwu, Saad Alatefi, Reda Abdel Azim, Ahmad Alkouh, Applications of artificial intelligence algorithms in artificial lift systems: A critical review, 2024, 97, 09555986, 102613, 10.1016/j.flowmeasinst.2024.102613 | |
2. | Okorie Ekwe Agwu, Ahmad Alkouh, Saad Alatefi, Reda Abdel Azim, Razaq Ferhadi, Utilization of machine learning for the estimation of production rates in wells operated by electrical submersible pumps, 2024, 14, 2190-0558, 1205, 10.1007/s13202-024-01761-3 | |
3. | Onyebuchi Ivan Nwanwe, Nkemakolam Chinedu Izuwa, Nnaemeka Princewill Ohia, Anthony Kerunwa, Nnaemeka Uwaezuoke, Determining optimal controls placed on injection/production wells during waterflooding in heterogeneous oil reservoirs using artificial neural network models and multi-objective genetic algorithm, 2024, 1420-0597, 10.1007/s10596-024-10300-2 | |
4. | Daniel Chuquin-Vasco, Dennise Chicaiza-Sagal, Cristina Calderón-Tapia, Nelson Chuquin-Vasco, Juan Chuquin-Vasco, Lidia Castro-Cepeda, Forecasting mixture composition in the extractive distillation of n-hexane and ethyl acetate with n-methyl-2-pyrrolidone through ANN for a preliminary energy assessment, 2024, 12, 2333-8334, 439, 10.3934/energy.2024020 | |
5. | Mariea Marcu, Approximation methods used to build the gas-lift performance curve based on reduced datasets: a comprehensive statistical comparison, 2024, 1091-6466, 1, 10.1080/10916466.2024.2404625 | |
6. | Sungil Kim, Tea-Woo Kim, Suryeom Jo, Artificial intelligence in geoenergy: bridging petroleum engineering and future-oriented applications, 2025, 15, 2190-0558, 10.1007/s13202-025-01939-3 | |
7. | James O. Arukhe, Ammal F. Anazi, 2025, Predicting Gas Lift Equipment Failure with Deep Learning Techniques, 10.4043/35605-MS |