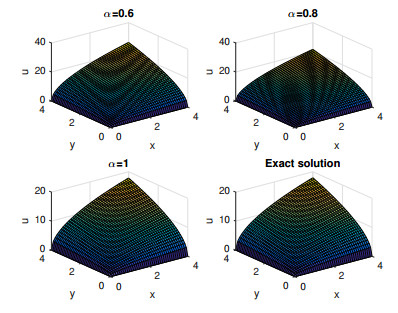
In this paper, food packaging materials and bioplastics applied as materials for food packaging are reviewed. Other possible materials, such as plastics, paper, metal, and glass, are also discussed. The advantages and disadvantages of every material are highlighted. The awareness of sustainability and the depletion of petroleum sources have contributed to the studies or innovations of using green materials, such as starch/polylactide, as food packaging. Bioplastic materials have several weaknesses in terms of their mechanical and barrier properties that have resulted in several studies on composite systems. These weaknesses have been reviewed and analyzed to determine the potential of bioplastic composites for application as food packaging materials.
Citation: Loh Guan Hong, Nor Yuliana Yuhana, Engku Zaharah Engku Zawawi. Review of bioplastics as food packaging materials[J]. AIMS Materials Science, 2021, 8(2): 166-184. doi: 10.3934/matersci.2021012
[1] | Ali Khalouta, Abdelouahab Kadem . A new computational for approximate analytical solutions of nonlinear time-fractional wave-like equations with variable coefficients. AIMS Mathematics, 2020, 5(1): 1-14. doi: 10.3934/math.2020001 |
[2] | D. Priyadarsini, P. K. Sahu, M. Routaray, D. Chalishajar . Numerical treatment for time fractional order phytoplankton-toxic phytoplankton-zooplankton system. AIMS Mathematics, 2024, 9(2): 3349-3368. doi: 10.3934/math.2024164 |
[3] | Muhammad Imran Liaqat, Sina Etemad, Shahram Rezapour, Choonkil Park . A novel analytical Aboodh residual power series method for solving linear and nonlinear time-fractional partial differential equations with variable coefficients. AIMS Mathematics, 2022, 7(9): 16917-16948. doi: 10.3934/math.2022929 |
[4] | Sumbal Ahsan, Rashid Nawaz, Muhammad Akbar, Saleem Abdullah, Kottakkaran Sooppy Nisar, Velusamy Vijayakumar . Numerical solution of system of fuzzy fractional order Volterra integro-differential equation using optimal homotopy asymptotic method. AIMS Mathematics, 2022, 7(7): 13169-13191. doi: 10.3934/math.2022726 |
[5] | M. Ali Akbar, Norhashidah Hj. Mohd. Ali, M. Tarikul Islam . Multiple closed form solutions to some fractional order nonlinear evolution equations in physics and plasma physics. AIMS Mathematics, 2019, 4(3): 397-411. doi: 10.3934/math.2019.3.397 |
[6] | Rahat Zarin, Abdur Raouf, Amir Khan, Aeshah A. Raezah, Usa Wannasingha Humphries . Computational modeling of financial crime population dynamics under different fractional operators. AIMS Mathematics, 2023, 8(9): 20755-20789. doi: 10.3934/math.20231058 |
[7] | Hayman Thabet, Subhash Kendre, James Peters . Travelling wave solutions for fractional Korteweg-de Vries equations via an approximate-analytical method. AIMS Mathematics, 2019, 4(4): 1203-1222. doi: 10.3934/math.2019.4.1203 |
[8] | Omar Barkat, Awatif Muflih Alqahtani . Analytical solutions for fractional Navier–Stokes equation using residual power series with ϕ-Caputo generalized fractional derivative. AIMS Mathematics, 2025, 10(7): 15476-15496. doi: 10.3934/math.2025694 |
[9] | Ahmad Qazza, Rania Saadeh, Emad Salah . Solving fractional partial differential equations via a new scheme. AIMS Mathematics, 2023, 8(3): 5318-5337. doi: 10.3934/math.2023267 |
[10] | Abdul Samad, Imran Siddique, Fahd Jarad . Meshfree numerical integration for some challenging multi-term fractional order PDEs. AIMS Mathematics, 2022, 7(8): 14249-14269. doi: 10.3934/math.2022785 |
In this paper, food packaging materials and bioplastics applied as materials for food packaging are reviewed. Other possible materials, such as plastics, paper, metal, and glass, are also discussed. The advantages and disadvantages of every material are highlighted. The awareness of sustainability and the depletion of petroleum sources have contributed to the studies or innovations of using green materials, such as starch/polylactide, as food packaging. Bioplastic materials have several weaknesses in terms of their mechanical and barrier properties that have resulted in several studies on composite systems. These weaknesses have been reviewed and analyzed to determine the potential of bioplastic composites for application as food packaging materials.
Fractional calculus is a field of applied mathematics that deals with derivatives and integrals of arbitrary orders [6,9,11,17]. Recently, fractional partial differential equations play an important role in interpretation and modeling of many of realism matters appear in applied mathematics and physics including fluid mechanics, electrical circuits, diffusion, damping laws, relaxation processes, optimal control theory, chemistry, biology, and so on [7,13,14,15,16]. Therefore, the search of the solutions for fractional partial differential equations is an important aspect of scientific research.
Many powerful and efficient methods have been proposed to obtain numerical solutions and analytical solutions of fractional partial differential equations. The most commonly used ones are: Adomian decomposition method (ADM) [5], variational iteration method (VIM) [18], new iterative method (NIM) [8], fractional difference method (FDM) [11], reduced differential transform method (RDTM) [1], homotopy analysis method (HAM) [3], homotopy perturbation method (HPM) [4].
The main objective of this paper is to present a new numerical technique called modified generalized Taylor fractional series method (MGTFSM) to obtain the approximate and exact solutions of Caputo time-fractional biological population equation. The proposed algorithm provides the solution in a rapid convergent series which may lead to the solution in a closed form. The main advantage of the proposed method compare with the existing methods is, that method solves the nonlinear problems without using linearization and any other restriction.
Consider the following Caputo time-fractional biological population equation
Dαtu=∂2u2∂x2+∂2u2∂y2+F(u), | (1.1) |
with the initial condition
u(x,y,0)=u0(x,y), | (1.2) |
where Dαt=∂α∂tα is the Caputo fractional derivative operator of order α, 0<α≤1,u=u(x,y,t),(x,y)∈R2,t>0 denotes the population density and F represents the population supply due to birth and death, α is a parameter describing the order of the fractional derivative.
The plan of our paper is as follows: In Section 2, we present some necessary definitions and properties of the fractional calculus theory. In Section 3, we will propose an analysis of the modified generalized Taylor fractional series method (MGTFSM) for solving the Caputo time-fractional biological population equation (1.1) subject to the initial condition (1.2). In Section 4, we present three numerical examples to show the efficiency and effectiveness of this method. In Section 5, we discuss our obtained results represented by figures and tables. These results were verified with Matlab (version R2016a). Section 6, is devoted to the conclusions on the work.
In this section, we present some basic definitions and properties of the fractional calculus theory which are used further in this paper. For more details see, [9,11].
Definition 2.1. A real function u(X,t), X=(x1,x2,...,xn)∈RN,N∈N∗,t∈R+, is considered to be in the space Cμ(RN×R+), μ∈ R, if there exists a real number p>μ, so that u(X,t)=tpv(X,t), where v ∈C(RN×R+), and it is said to be in the space Cnμ if u(n)∈Cμ(RN×R+),n∈N.
Definition 2.2. The Riemann-Liouville fractional integral operator of order α≥0 of u∈Cμ(RN×R+),μ≥−1, is defined as follows
Iαtu(X,t)={1Γ(α)t∫0(t−ξ)α−1u(X,ξ)dξ,α>0,t>ξ>0,u(X,t), α=0, | (2.1) |
where Γ(.) is the well-known Gamma function.
Definition 2.3. The Caputo time-fractional derivative operator of order α>0 of u∈Cn−1(RN×R+),n∈N, is defined as follows
Dαtu(X,t)={1Γ(n−α)t∫0(t−ξ)n−α−1u(n)(X,ξ)dξ,n−1<α<n,u(n)(X,t), α=n. | (2.2) |
For this definition we have the following properties
(1)
Dαt(c)=0, where c is a constant. |
(2)
Dαttβ={Γ(β+1)Γ(β−α+1)tβ−α if β>n−1,0, if β≤n−1. |
Definition 2.3. The Mittag-Leffler function is defined as follows
Eα(z)=∞∑n=0znΓ(nα+1),α∈C,Re(α)>0. | (2.3) |
For α=1, Eα(z) reduces to ez.
Theorem 3.1. Consider the Caputo time-fractional biological population equation of the form (1.1) with the initial condition (1.2).
Then, by MGTFSM the solution of equations (1.1)-(1.2) is given in the form of infinite series which converges rapidly to the exact solution as follows
u(x,y,t)=∞∑i=0ui(x,y)tiαΓ(iα+1),(x,y)∈R2,t∈[0,R), |
where ui(x,y) the coefficients of the series and R is the radius of convergence.
Proof. In order to achieve our goal, we consider the following Caputo time-fractional biological population equation of the form (1.1) with the initial condition (1.2).
Assume that the solution takes the following infinite series form
u(x,y,t)=∞∑i=0ui(x,y)tiαΓ(iα+1). | (3.1) |
Consequently, the approximate solution of equations (1.1)-(1.2), can be written in the form of
un(x,y,t)=n∑i=0ui(x,y)tiαΓ(iα+1)=u0(x,y)+n∑i=1ui(x,y)tiαΓ(iα+1). | (3.2) |
By applying the operator Dαt on equation (3.2), and using the properties (1) and (2), we obtain the formula
Dαtun(x,y,t)=n−1∑i=0ui+1(x,y)tiαΓ(iα+1). | (3.3) |
Next, we substitute both (3.2) and (3.3) in (1.1). Therefore, we have the following recurrence relations
0=n−1∑i=0ui+1(x,y)tiαΓ(iα+1)−∂2∂x2(n∑i=0ui(x,y)tiαΓ(iα+1))2−∂2∂y2(n∑i=0ui(x,y)tiαΓ(iα+1))2−F(n∑i=0ui(x,y)tiαΓ(iα+1)). |
We follow the same analogue used in obtaining the Taylor series coefficients. In particular, to calculate the function un(x,y),n=1,2,3,.., we have to solve the following
D(n−1)αt{G(x,y,t,α,n)}↓t=0=0, |
where
G(x,y,t,α,n)=n−1∑i=0ui+1(x,y)tiαΓ(iα+1)−∂2∂x2(n∑i=0ui(x,y)tiαΓ(iα+1))2−∂2∂y2(n∑i=0ui(x,y)tiαΓ(iα+1))2−F(n∑i=0ui(x,y)tiαΓ(iα+1)). |
Now, we calculate the first terms of the sequence {un(x,y)}N1.
For n=1 we have
G(x,y,t,α,1)=u1(x,y)−∂2∂x2(u0(x,y)+u1(x,y)tαΓ(α+1))2−∂2∂y2(u0(x,y)+u1(x,y)tαΓ(α+1))2−F(u0(x,y)+u1(x,y)tαΓ(α+1)). |
Solving G(x,y,0,α,1)=0, yields
u1(x,y)=∂2∂x2u20(x,y)+∂2∂y2u20(x,y)+F(u0(x,y)). |
For n=2 we have
G(x,y,t,α,2)=u1(x,y)+u2(x,y)tαΓ(α+1)−∂2∂x2(u0(x,y)+u1(x,y)tαΓ(α+1)+u2(x,y)t2αΓ(2α+1))2−∂2∂y2(u0(x,y)+u1(x,y)tαΓ(α+1)+u2(x,y)t2αΓ(2α+1))2−F(u0(x,y)+u1(x,y)tαΓ(α+1)+u2(x,y)t2αΓ(2α+1)). | (3.4) |
Applying Dαt on both sides of equation (3.4) gives
DαtG(x,y,t,α,2)=u2(x,y)−2∂2∂x2[(u0(x,y)+u1(x,y)tαΓ(α+1)+u2(x,y)t2αΓ(2α+1))×(u1(x,y)+u2(x,y)tαΓ(α+1))]−2∂2∂y2[(u0(x,y)+u1(x,y)tαΓ(α+1)+u2(x,y)t2αΓ(2α+1))×(u1(x,y)+u2(x,y)tαΓ(α+1))]−(u1(x,y)+u2(x,y)tαΓ(α+1))×F′(u0(x,y)+u1(x,y)tαΓ(α+1)+u2(x,y)t2αΓ(2α+1)). |
Solving Dαt{G(x,y,t,α,2)}↓t=0=0, yields
u2(x,y)=2∂2∂x2[u0(x,y)u1(x,y)]+2∂2∂y2[u0(x,y)u1(x,y)]+u1(x,y)F′(u0(x,y)). |
To calculate u3(x,y), we consider G(x,y,t,α,3) and we solve
D2αt{G(x,y,t,α,3)}↓t=0=0, |
we have
u3(x,y)=2∂2∂x2[3u1(x,y)u2(x,y)+u0(x,y)u3(x,y)]+2∂2∂y2[3u1(x,y)u2(x,y)+u0(x,y)u3(x,y)]+u2(x,y)F′(u0(x,y))+u21(x,y)F′′(u0(x,y)), |
and so on.
In general, to obtain the coefficient function uk(x,y) we solve
D(k−1)αt{G(x,y,t,α,k)}↓t=0=0. |
Finally, the solution of equations (1.1)-(1.2), can be expressed by
u(x,y,t)=limn→∞un(x,y,t)=limn→∞n∑i=0ui(x,y)tiαΓ(iα+1)=∞∑i=0ui(x,y)tiαΓ(iα+1). |
The proof is complete.
In this section, we test the validity and efficiency of the proposed method to solve three numerical examples of Caputo time-fractional biological population equation.
We define En to be the absolute error between the exact solution u and the approximate solution un, as follows
En(x,y,t)=|u(x,y,t)−un(x,y,t)|,n=0,1,2,3,... |
Example 4.1. Consider the Caputo time-fractional biological population equation in the form
Dαtu=∂2u2∂x2+∂2u2∂y2+hu, | (4.1) |
with the initial condition
u(x,y,0)=u0(x,y)=√xy. | (4.2) |
By applying the steps involved in the MGTFSM as presented in Section 3, we have the solution of equations (4.1)-(4.2) in the form
u(x,y,t)=∞∑i=0ui(x,y)tiαΓ(iα+1), |
and
ui(x,y)=hi√xy, for i=0,1,2,3,... |
So, the solution of equations (4.1)-(4.2), can be expressed by
u(x,y,t)=√xy(1+htαΓ(α+1)+h2t2αΓ(2α+1)+h3t3αΓ(3α+1)+...)=√xy∞∑i=0(htα)iΓ(iα+1)=√xyEα(htα), | (4.3) |
where Eα(htα) is the Mittag-Leffler function, defined by (2.3).
Taking α=1 in (4.3), we have
u(x,y,t)=√xy(1+ht+(ht)22!+(ht)33!+...)=√xyexp(ht), |
which is an exact solution to the standard form biological population equation [10].
Example 4.2. Consider the Caputo time-fractional biological population equation in the form
Dαtu=∂2u2∂x2+∂2u2∂y2+u, | (4.4) |
with the initial condition
u(x,y,0)=u0(x,y)=√sinxsinhy. | (4.5) |
By applying the steps involved in the MGTFSM as presented in Section 3, we have the solution of equations (4.4)-(4.5) in the form
u(x,y,t)=∞∑i=0ui(x,y)tiαΓ(iα+1), |
and
ui(x,y)=√sinxsinhy, for i=0,1,2,3,... |
So, the solution of equations (4.4)-(4.5), can be expressed by
u(x,y,t)=√sinxsinhy(1+tαΓ(α+1)+t2αΓ(2α+1)+t3αΓ(3α+1)+...)=√sinxsinhy∞∑i=0tiαΓ(iα+1)=√sinxsinhyEα(tα), | (4.6) |
where Eα(tα) is the Mittag-Leffler function, defined by (2.3).
Taking α=1 in (4.6), we have
u(x,y,t)=√sinxsinhy(1+t+t22!+t33!+...)=(√sinxsinhy)exp(t), |
which is an exact solution to the standard form biological population equation [12].
Example 4.3 Consider the Caputo time-fractional biological population equation in the form
Dαtu=∂2u2∂x2+∂2u2∂y2+hu(1−ru), | (4.7) |
with the initial condition
u(x,y,0)=u0(x,y)=exp(√hr8(x+y)). | (4.8) |
By applying the steps involved in the MGTFSM as presented in Section 3, we have the solution of equations (4.7)-(4.8) in the form
u(x,y,t)=∞∑i=0ui(x,y)tiαΓ(iα+1), |
and
ui(x,y)=hiexp(√hr8(x+y)), for i=0,1,2,3,... |
So, the solution of equations (4.7)-(4.8), can be expressed by
u(x,y,t)=exp(√hr8(x+y))(1+htαΓ(α+1)+h2t2αΓ(2α+1)+h3t3αΓ(3α+1)+...)=exp(√hr8(x+y))∞∑i=0(htα)iΓ(iα+1)=exp(√hr8(x+y))Eα(htα), | (4.9) |
where Eα(htα) is the Mittag-Leffler function, defined by (2.3).
Taking α=1 in (4.9), we have
u(x,y,t)=exp(√hr8(x+y))(1+ht+(ht)22!+(ht)33!+...)=exp(√hr8(x+y)+ht), |
which is an exact solution to the standard form biological population equation [2].
In this section the numerical results for Examples 4.1, 4.2 and 4.3 are presented. Figures 1, 3 and 5 represents the surface graph of the exact solution and the approximate solution u6(x,y,t) at α=0.6,0.8,1. Figures 2, 4 and 6 represents the behavior of the exact solution and the approximate solution u6(x,y,t) at α=0.7,0.8,0.9,1. These figures affirm that when the order of the fractional derivative α tends to 1, the approximate solutions obtained by MGTFSM tends continuously to the exact solutions. Tables 1–3 show the absolute errors between the exact solution and the approximate solution u6(x,y,t) at α=1 for different values of x,y and t. These tables clarifies the convergence of the approximate solutions to the exact solutions.
t/x,y | 0.1 | 0.3 | 0.5 | 0.7 |
0.1 | 1.4090×10−10 | 4.2269×10−10 | 7.0449×10−10 | 9.8629×10−10 |
0.3 | 1.0576×10−7 | 3.1727×10−7 | 5.2879×10−7 | 7.4030×10−7 |
0.5 | 2.3354×10−6 | 7.0062×10−6 | 1.1677×10−5 | 1.6348×10−5 |
0.7 | 1.8129×10−5 | 5.4387×10−5 | 9.0645×10−5 | 1.2690×10−4 |
0.9 | 8.4486×10−5 | 2.5346×10−4 | 4.2243×10−4 | 5.9140×10−4 |
t/x,y | 0.1 | 0.3 | 0.5 | 0.7 |
0.1 | 1.4090×10−10 | 4.2268×10−10 | 7.0425×10−10 | 9.8497×10−10 |
0.3 | 1.0576×10−7 | 3.1726×10−7 | 5.2860×10−7 | 7.3932×10−7 |
0.5 | 2.3354×10−6 | 7.0059×10−6 | 1.1673×10−5 | 1.6326×10−5 |
0.7 | 1.8129×10−5 | 5.4385×10−5 | 9.0614×10−5 | 1.2673×10−4 |
0.9 | 8.4486×10−5 | 2.5345×10−4 | 4.2228×10−4 | 5.9061×10−4 |
t/x,y | 0.1 | 0.3 | 0.5 | 0.7 |
0.1 | 1.5572×10−9 | 1.9019×10−9 | 2.3230×10−9 | 2.8373×10−9 |
0.3 | 1.1688×10−6 | 1.4276×10−6 | 1.7436×10−6 | 2.1297×10−6 |
0.5 | 2.5810×10−5 | 3.1525×10−5 | 3.8504×10−5 | 4.7029×10−5 |
0.7 | 2.0036×10−4 | 2.4472×10−4 | 2.9890×10−4 | 3.6507×10−4 |
0.9 | 9.3372×10−4 | 1.1404×10−3 | 1.3929×10−3 | 1.7013×10−3 |
In addition, numerical results have confirmed the theoretical results and high accuracy of the proposed scheme.
Remark 5.1. In this paper, we only apply Six terms to approximate the solutions, if we apply more terms of the approximate solutions, the accuracy of the approximate solutions will be greatly improved.
In this paper, a new numerical technique called modified generalized Taylor fractional series method (MGTFSM) has been successfully applied for solving the Caputo time-fractional biological population equation. The method was applied to three numerical examples. The results show that the MGTFSM is an efficient and easy to use technique for finding approximate and exact solutions for these problems. The obtained approximate solutions using the suggested method is in excellent agreement with the exact solutions. This confirms our belief that the effciency of our technique gives it much wider applicability for general classes of fractional problems.
The authors are very grateful to the guest editors of this special issue and would like to express their sincere thanks to the referees for the careful and noteworthy reading of the paper and for their constructive comments and suggestions which are improved the paper substantially.
The authors declare that there is no conflict of interest in this paper.
[1] | Molenveld K, Van Den Oever MJA, Bos HL (2015) Biobased Packaging Catalogue, Wageningen: Wageningen UR-Food & Biobased Research. |
[2] | Byun Y, Kim YT (2014) Bioplastics for food packaging: Chemistry and physics, In: Han JH, Innovations in Food Packaging, 2nd Eds., Academic Press, 349-366. |
[3] | Mohanty F, Swain SK (2017) Bionanocomposites for food packaging applications, In: Oprea AE, Grumezescu AM, Nanotechnology Applications in Food: Flavor, Stability, Nutrition, and Safety, Academic Press, 363-379. |
[4] | Sedlacekova Z (2017) Food packaging materials: Comparison of materials used for packaging purposes [Dissertation]. Helsinki Metropolia University of Applied Sciences. |
[5] | Talegaonkar S, Sharma H, Pandey S, et al. (2017) Bionanocomposites: Smart biodegradable packaging material for food preservation, In: Grumezescu AM, Food Packaging, Academic Press, 7: 79-110. |
[6] | Kim YT, Min B, Kim KW (2014) General characteristics of packaging materials for food system, In: Han JH, Innovations in Food Packaging, 2nd Eds., Academic Press, 13-35. |
[7] | Beyer R (2012) Manual on Food Packaging for Small and Medium-Size Enterprises in Samoa, Food and Agriculture Organization of the United Nations Sub-Regional Office for the Pacific Islands. |
[8] | Paine FA, Paine HY (1992) A Handbook of Food Packaging, 2nd Eds. United Kingdom: Springer Science + Business Media Dordrecht. |
[9] |
Keskin G, Kızıl G, Bechelany M, et al. (2017) Potential of polyhydroxyalkanoate (PHA) polymers family as substitutes of petroleum based polymers for packaging applications and solutions brought by their composites to form barrier materials. Pure Appl Chem 28: 1841-1848. doi: 10.1515/pac-2017-0401
![]() |
[10] | Galić K, Barrier packaging materials, 2015. Available from: https://www.newfoodmagazine.com/article/16971/barrier-packaging-materials/. |
[11] |
Marsh K, Bugusu B (2007) Food packaging-roles, materials, and environmental issues. J Food Sci 72: R39-R55. doi: 10.1111/j.1750-3841.2007.00301.x
![]() |
[12] | Gu G, Concept of permeation and barrier materials, 2017. Available from: https://www.packageintegrity.com/single-post/2017/10/02/Concept-of-Permeation-and-Barrier-Materials. |
[13] | Mal J, Food spoilage-rancidity and food chemistry, 2018. Available from: https://foodcrumbles.com/food-spoilage-rancidity-and-food-chemistry/. |
[14] | Marcus JB (2013) Lipids basics: Fats and oils in foods and health: Healthy lipid choices, roles and applications in nutrition, food science and the culinary arts, Culinary Nutrition, Academic Press, 231-277. |
[15] | Leelaphiwat P, Auras RA, Harte JB, et al. (2016) Barrier properties of polymeric packaging materials to major aroma volatiles in herbs, In: Jawaid M, Kenawy El-R, MATEC Web of Conferences, 67: 06100. |
[16] |
Sajilata MG, Savitha K, Singhal RS, et al. (2007) Scalping of flavors in packaged foods. Compr Rev Food Sci F 6: 17-35. doi: 10.1111/j.1541-4337.2007.00014.x
![]() |
[17] |
Zhao C (2018) Food packaging. Johnson Matthey Technol Rev 62: 74-80. doi: 10.1595/205651318X696350
![]() |
[18] | Siracusa V (2012) Food packaging permeability behaviour: A report. Int J Polym Sci 2012: 302029. |
[19] |
Sangroniz A, Zhu JB, Tang XY, et al. (2019) Packaging materials with desired mechanical and barrier properties and full chemical recyclability. Nat Commun 10: 1-7. doi: 10.1038/s41467-019-11525-x
![]() |
[20] |
Fung F, Wang HS, Menon S (2018) Food safety in the 21st century. Biomed J 41: 88-95. doi: 10.1016/j.bj.2018.03.003
![]() |
[21] | Rawat S (2015) Food Spoilage: Microorganisms and their prevention. Asian J Plant Sci Res 5: 47-56. |
[22] | Corrales M, Fernández A, Han JH (2014) Antimicrobial packaging systems, In: Han JH, Innovations in Food Packaging, 2nd Eds., Academic Press, 133-170. |
[23] |
Malhotra B, Keshwani A, Kharkwal H (2015) Antimicrobial food packaging: Potential and pitfalls. Front Microbiol 6: 1-9. doi: 10.3389/fmicb.2015.00611
![]() |
[24] |
Radusin TI, Ristić IS, Pilić BM, et al. (2016) Antimicrobial nanomaterials for food packaging applications. Food Feed Res 43: 119-126. doi: 10.5937/FFR1602119R
![]() |
[25] | Shin J, Selke SEM (2014) Food packaging, In: Clark S, Jung S, Lamsal B, Food Processing: Principles and Applications, 2nd Eds., Singapore: John Wiley & Sons, 249-273. |
[26] | Sinai M, Plastic vs. aluminum vs. glass: Which packaging should you choose, 2017. Available from: https://recyclenation.com/2017/08/plastic-vs-aluminum-vs-glass-which-packaging-should-you-choose/. |
[27] | Hutson A, The pros and cons of 7 types of food packaging explained, 2019. Available from: https://dansensor.com/blog/7-types-of-food-packaging-explained. |
[28] | Weiss D, Your guide to food packaging, 2019. Available from: https://www.newfoodmagazine.com/article/90810/food-packaging-types-importance-trends/. |
[29] | Filtext, Materials for packaging: Advantages and disadvantages, 2019. Available from: https://filtext.es/en/blog/materials-for-packaging-advantages-and-disadvantages. |
[30] | Guern CL, When the mermaids cry: The great plastic tide, 2018. Available from: https://plastic-pollution.org/. |
[31] | Knight L, A brief history of plastics, natural and synthetic, 2014. Available from: https://www.bbc.com/news/magazine-27442625. |
[32] | OECD Environment Directorate (2010) Materials case study 4: Plastics. OECD Global Forum on Environment Focusing on Sustainable Materials Management. |
[33] | de Moura IG, de Sá AV, Sofia A, et al. (2017) Bioplastics from agro-wastes for food packaging applications. In: Grumezescu AM, Food Packaging, Academic Press, 7: 223-263. |
[34] | Types of plastic food packaging and safety: A close-up look, 2019. Available from: https://www.chemicalsafetyfacts.org/types-plastic-food-packaging-safety-close-look/. |
[35] | Khanam PN, AlMaadeed MAA (2015) Processing and characterization of polyethylene-based composites. Adv Manuf Polym Compos Sci 1: 63-79. |
[36] | Allahvaisi S (2012) Polypropylene in the industry of food packaging, In: Dogan F, Polypropylene, Croatia: InTech, 1-20. |
[37] | Kirwan MJ, Plant S, Strawbridge JW (2011) Plastics in food packaging, In: Coles R, Kirwan M, Food and Beverage Packaging Technology, 2nd Eds., Blackwell Publishing, 157-212. |
[38] | Cort S de, Godts F, Moreau A (2017) Packaging materials 1: Polyethylene terephthalate (PET) for food packaging applications, ILSI Europe Report Series, ILSI Europe, 2017: 1-24. |
[39] | Yadav A, Mangaraj S, Singh R, et al. (2018) Biopolymers as packaging material in food and allied industry. Int J Chem Stud 6: 2411-2418. |
[40] |
Spiridon I, Ursu RG, Spiridon IAC (2015) New polylactic acid composites for packaging applications: Mechanical properties, thermal behavior, and antimicrobial activity. Int J Polym Anal Ch 20: 681-692. doi: 10.1080/1023666X.2015.1081131
![]() |
[41] |
Süfer Ö, Oz AT, Celebi Sezer Y (2017) Poly(lactic acid) films in food packaging systems. Food Sci Nutr Technol 2: 1-5. doi: 10.23880/FSNT-16000131
![]() |
[42] |
Singh N, Hui D, Singh R, et al. (2017) Recycling of plastic solid waste: A state of art review and future applications. Compos Part B-Eng 115: 409-422. doi: 10.1016/j.compositesb.2016.09.013
![]() |
[43] | Han JH (2014) A review of food packaging technologies and innovations, In: Han JH, Innovations in Food Packaging, 2nd Eds. Academic Press, 1-12. |
[44] | European Bioplastics, Applications for bioplastics, 2019. Available from: https://www.european-bioplastics.org/market/applications-sectors/. |
[45] | Dammer L, Partanan A (2016) The EU Ecolabel and bio-based products. Bioplastics Mag 11: 44-46. |
[46] | European Bioplastics, What are bioplastics? 2019. Available from: https://www.european-bioplastics.org/bioplastics/. |
[47] | Van Den Oever M, Molenveld K, Van Der Zee M, et al. (2017) Bio-based and Biodegradable Plastics-Facts and Figures: Focus on Food Packaging in the Netherlands, Netherlands: Wageningen Food & Biobased Research. |
[48] | Niaounakis M (2015) Definitions of terms and types of biopolymers, Biopolymers: Applications and Trends, Oxford: William Andrew Publishing, 1-90. |
[49] | Green Dot Bioplastic, A straightforward explanation of biodegradable vs. compostable vs. oxo-degradable plastics, 2020. Available from: https://www.greendotbioplastics.com/biodegradable-vs-compostable-vs-oxo-degradable-plastics-a-straightforward-explanation/. |
[50] |
Nitayaphat W, Jiratumnukul N, Charuchinda S, et al. (2019) Mechanical properties of chitosan/bamboo charcoal composite films made with normal and surface oxidized charcoal. Carbohydr Polym 78: 444-448. doi: 10.1016/j.carbpol.2009.04.027
![]() |
[51] |
Papageorgiou GZ (2018) Thinking green: Sustainable polymers from renewable resources. Polymers 10: 952. doi: 10.3390/polym10090952
![]() |
[52] |
Castro-Galiano E, Auras RA, Selke SEM, et al. (2018) Poly(lactic acid) nanocomposites. Polymers 10: 202. doi: 10.3390/polym10020202
![]() |
[53] |
Karina M, Syampurwadi A, Satoto R, et al. (2017) Physical and mechanical properties of recycled PP composites reinforced with rice straw lignin. BioResources 12: 5801-5811. doi: 10.15376/biores.12.3.5801-5811
![]() |
[54] |
Siracusa V, Blanco I (2020) Bio-polyethylene (Bio-PE), bio-polypropylene (Bio-PP) and bio-poly(ethylene terephthalate) (Bio-PET): Recent developments in bio-based polymers analogous to petroleum-deived ones for packaging and engineering applications. Polymers 12: 1641. doi: 10.3390/polym12081641
![]() |
[55] | Pillai CKS (2010) Challenges for natural monomers and polymers: Novel design strategies and engineering to develop advanced polymers. Des Monomers Polym 3: 87-121. |
[56] | Siracusa V (2019) Microbial degradation of synthetic biopolymers waste. Polymers 11:1-18. |
[57] |
Lamberti FM, Román-Ramírez LA, Wood J (2020) Recycling of bioplastics: Routes and benefits. J Polym Environ 28: 2551-2571. doi: 10.1007/s10924-020-01795-8
![]() |
[58] | Chauvin S, Bio-based polymers: what is the future? 2017. Avaliable from: https://www.linkedin.com/pulse/bio-based-polymers-what-future-sophie-chauvin-1/. |
[59] |
Jiménez-Rosado M, Rubio-Valle JF, Perez-Puyana V, et al. (2020) Use of heat treatment for the development of protein-based bioplastics. Sustain Chem Pharm 18: 100341. doi: 10.1016/j.scp.2020.100341
![]() |
[60] |
Jiménez-Rosado M, Bouroudian E, Perez-Puyana V, et al. (2020) Evaluation of different strengthening methods in the mechanical and functional properties of soy protein-based bioplastics. J Clean Prod 262: 121517. doi: 10.1016/j.jclepro.2020.121517
![]() |
[61] |
Chakravartula SSN, Soccio M, Lotti N, et al. (2019) Characterization of composite edible films based on pectin/alginate/whey protein concentrate. Materials 12: 2454. doi: 10.3390/ma12152454
![]() |
[62] | Huang Y, Mei L, Chen X, et al. (2018) Recent developments in food packaging based on nanomaterials. Nanomaterials 8: 1-29. |
[63] | Rezic I, Haramina T (2017) Metal nanoparticles and carbon nanotubes-perfect antimicrobial nano-fillers in polymer-based food packaging materials, In: Grumezescu, Food Packaging, Academic Press, 7: 497-532. |
[64] |
Wahyuningtiyas NE, Suryanto H (2018) Properties of cassava starch based bioplastic reinforced by nanoclay. JMEST 2: 20-26. doi: 10.17977/um016v2i12018p020
![]() |
[65] |
López O V, Castillo LA, García MA, et al. (2014) Food packaging bags based on thermoplastic corn starch reinforced with talc nanoparticles. Food Hydrocolloid 43: 18-24. doi: 10.1016/j.foodhyd.2014.04.021
![]() |
[66] |
Souza VGL, Fernando AL (2016) Nanoparticles in food packaging: Biodegradability and potential migration to food-A review. Food Packaging Shelf 8: 63-70. doi: 10.1016/j.fpsl.2016.04.001
![]() |
[67] |
Vilarinho F, Sanches-silva A, Vaz MF, et al. (2017) Nanocellulose: A benefit for green food packaging. Crit Rev Food Sci Nutr 58: 1526-1537. doi: 10.1080/10408398.2016.1270254
![]() |
[68] |
Fathilah WFW, Othaman R (2019) Electrospun cellulose fibres and applications. Sains Malays 48: 1459-1472. doi: 10.17576/jsm-2019-4807-15
![]() |
[69] |
Azeredo HMC, Rosa MF, Mattoso LHC (2017) Nanocellulose in bio-based food packaging applications. Ind Crop Prod 97: 664-671. doi: 10.1016/j.indcrop.2016.03.013
![]() |
[70] |
Xu X, Liu F, Jiang L, et al. (2013) Cellulose nanocrystals vs. cellulose nanofibrils: A comparative study on their microstructures and effects as polymer reinforcing agents. ACS Appl Mater Interfaces 5: 2999-3009. doi: 10.1021/am302624t
![]() |
[71] |
Zhao H, Li J, Zhu K (2018) Bacterial cellulose production from waste products and fermentation conditions optimization. IOP Conf Ser Mater Sci Eng 394: 022041. doi: 10.1088/1757-899X/394/2/022041
![]() |
[72] |
Azeredo HMC, Barud H, Farinas CS, et al. (2019) Bacterial cellulose as a raw material for food and food packaging applications. Front Sustain Food Syst 3: 1-14. doi: 10.3389/fsufs.2019.00001
![]() |
[73] |
Rahmad D, Kasim A (2017) Provision of micro-nano bacterial cellulose as bio plastic filler by sonication method. IOP Conf Ser Mater Sci Eng 223: 012040. doi: 10.1088/1757-899X/223/1/012040
![]() |
[74] | Sulaiman NN, Rahman NA, Esa F (2019) Monitoring production of bacterial cellulose by Acetobacter xylinum 0416 with fuzzy logic via simulation. J Kejuruter SI 1: 21-26. |
[75] |
Carbone M, Donia DT, Sabbatella G, et al. (2016) Silver nanoparticles in polymeric matrices for fresh food packaging. J King Saud Univ Sci 28: 273-279. doi: 10.1016/j.jksus.2016.05.004
![]() |
[76] | Tavakoli H, Rastegar H, Taherian M, et al. (2017) The effect of nano-silver packaging in increasing the shelf life of nuts: An in vitro model. Ital J Food Saf 6: 6874. |
[77] |
Swaroop C, Shukla M (2018) Nano-magnesium oxide reinforced polylactic acid biofilms for food packaging applications. Int J Biol Macromol 113: 729-736. doi: 10.1016/j.ijbiomac.2018.02.156
![]() |
[78] |
Tang Z, Lv B (2014) MgO Nanoparticles as antibacterial agent: Preparation and activity. Brazilian J Chem Eng 31: 591-601. doi: 10.1590/0104-6632.20140313s00002813
![]() |
[79] | Bioplastics NEWS, Polylactic acid or polylactide (PLA), 2019. Available from: https://bioplasticsnews.com/polylactic-acid-or-polylactide-pla/. |
[80] | Voznyak Y, Morawiec J, Galeski A (2018) Ductility of polylactide composites reinforced with polyhydroxyalkanoates nanofibers, AIP Conference Proceedings, AIP Publishing, 1981: 0200078. |
[81] |
Genovese L, Soccio M, Lotti N, et al. (2017) Design of biobased PLLA triblock copolymers for sustainable food packaging: Thermo-mechanical properties, gas barrier ability and compostability. Eur Polym J 95: 289-303. doi: 10.1016/j.eurpolymj.2017.08.001
![]() |
[82] | Byun Y, Kim YT (2014) Utilization of bioplastics for food packaging industry, In: Han JH, Innovations in Food Packaging, 2nd Eds., Academic Press, 367-388. |
[83] | Zhang Y, Rempel C, Mclaren D (2014) Thermoplastic starch, In: Han JH, Innovations in Food Packaging, 4th Eds., Academic Press, 389-410. |
[84] |
Sun Q, Xi T, Li Y, et al. (2014) Characterization of corn starch films reinforced with CaCO3 nanoparticles. Plos One 9: e106727. doi: 10.1371/journal.pone.0106727
![]() |
[85] | Gilfillan WN (2015) Developing starch-based polymer composites [Dissertation]. Queensland University of Technology (QUT). |
[86] |
Mannina G, Presti D, Montiel-jarillo G, et al. (2019) Bioplastic recovery from wastewater: A new protocol for polyhydroxyalkanoates (PHA) extraction from mixed microbial cultures. Bioresour Technol 282: 361-369. doi: 10.1016/j.biortech.2019.03.037
![]() |
[87] | Mohammadi M, Ghaffari-Moghaddam M (2015) Recovery and extraction of polyhydroxyalkanoates (PHAs), In: Roy I, Visakh PM, Polyhydroxyalkanoate (PHA) Based Blends, Composites and Nanocomposites, Royal Society of Chemistry, 47-65. |
[88] | Luyt AS, Malik SS (2019) Can biodegradable plastics solve plastic solid waste accumulation? In: Al-Salem, Plastics to Energy: Fuel, Chemicals, and Sustainability Implications, New York: William Andrew Publishing, 403-423. |
[89] |
Vandi L, Chan CM, Werker A, et al. (2018) Wood-PHA composites: Mapping opportunities. Polymers 10: 1-15. doi: 10.3390/polym10070751
![]() |
[90] | Gumel AM, Annuar MSM (2015) Nanocomposites of polyhydroxyalkanoates (PHAs), In: Roy I, Visakh PM, Polyhydroxyalkanoate (PHA) Based Blends, Composites and Nanocomposites, Royal Society of Chemistry, 98-118. |
[91] |
Valentini F, Dorigato A, Rigotti A, et al. (2019) Polyhydroxyalkanoates/fibrillated nanocellulose composites for additive manufacturing. J Polym Environ 27: 1333-1341. doi: 10.1007/s10924-019-01429-8
![]() |
[92] | Nova-Institue, Biobased polybutylene succinate (PBS)-An attractive polymer for biopolymer compounds, 2015. Available from: https://renewable-carbon.eu/publications/product/biobased-polybutylene-succinate-pbs-an-attractive-polymer-for-biopolymer-compounds-%E2%88%92-full-version/. |
[93] |
Puchalski M, Szparaga G, Biela T, et al. (2018) Molecular and supramolecular changes in polybutylene succinate (PBS) and polybutylene succinate adipate (PBSA) copolymer during degradation in various environmental conditions. Polymers 10: 1-12. doi: 10.3390/polym10030251
![]() |
[94] | Polymer Properties Database, Polybutylene succinate (PBS), 2018. Available from: https://polymerdatabase.com/Polymer Brands/PBS.html. |
[95] |
Budtri N, Aekrum S, Lertsiriyothin W (2017) The compatibility of polylactides and polybutylene succinate in PLA blends based on thermal, mechanical, and rheological properties. Orient J Chem 33: 2766-2775. doi: 10.13005/ojc/330609
![]() |
[96] |
Monika Pal AK, Bhasney SM, Bhagabati P, et al. (2018) Effect of dicumyl peroxide on a poly(lactic acid) (PLA)/poly(butylene succinate) (PBS)/functionalized chitosan-based nanobiocomposite for packaging: A reactive extrusion study. ACS Omega 3: 13298-13312. doi: 10.1021/acsomega.8b00907
![]() |
[97] |
Deng Y, Thomas NL (2015) Blending poly(butylene succinate) with poly(lactic acid): Ductility and phase inversion effects. Eur Polym J 17: 534-546. doi: 10.1016/j.eurpolymj.2015.08.029
![]() |
[98] |
Fortunati E, Puglia D, Iannoni A, et al. (2017) Processing conditions, thermal and mechanical responses of stretchable poly(lactic acid)/poly(butylene succinate) films. Materials 10: 1-17. doi: 10.3390/ma10070809
![]() |
[99] | Su S, Kopitzky R, Tolga S, et al. (2019) Polylactide (PLA) and its blends with poly(butylene succinate) (PBS): A brief review. Polymers 11: 1-21. |
[100] |
Soccio M, Dominici F, Quattrosoldi S, et al. (2020) PBS-based green copolymer as an efficient compatibilizer in thermoplastic inedible wheat flour/poly(butylene succinate) blends. Biomacromolecules 21: 3254-3269. doi: 10.1021/acs.biomac.0c00701
![]() |
[101] |
Quattrosoldia S, Soccioa M, Gazzanob M, et al. (2020) Fully biobased, elastomeric and compostable random copolyesters of poly(butylene succinate) containing Pripol 1009 moieties: Structure-property relationship. Polym Degrad Stab 178: 109189. doi: 10.1016/j.polymdegradstab.2020.109189
![]() |
[102] | Souza AF, Vilela C, Fonseca AC, et al. (2015) Biobased polyesters and other polymers from 2, 5-furandicarboxylic acid: a tribute to furan excellency. Polym Chem 33: 5961-5983. |
[103] | Holladay JE, White JF, Bozell JJ, et al. (2007) Results of screening for potential candidates from biorefinery lignin, Top Value-Added Chemicals from Biomass. Richland, WA, USA: Pacific Northwest National Lab. |
[104] |
Sajid M, Zhao X, Liu D (2018) Production of 2, 5-furandicarboxylic acid (FDCA) from 5-hydroxymethylfurfural (HMF): Recent progress focusing on the chemical-catalytic routes. Green Chem 24: 5427-5453. doi: 10.1039/C8GC02680G
![]() |
[105] | Bicerano & Associates Consulting, A plant-based renewable alternative to PET, 2019. Available from: https://www.polymerexpert.biz/blog/134-a-plant-based-renewable-alternative-to-pet. |
[106] |
Terzopoulou Z, Papadopoulos L, Zamboulis A, et al. (2020) Tuning the properties of furandicarboxylic acid-based polyesters with copolymerization: A review. Polymers 12: 1209. doi: 10.3390/polym12061209
![]() |
[107] |
Guidotti G, Soccio M, García-Gutiérrez MC, et al. (2019) Evidence of a 2D-ordered structure in biobased poly(pentamethylene furanoate) responsible for its outstanding barrier and mechanical properties. ACS Sustain Chem Eng 7: 17863-17871. doi: 10.1021/acssuschemeng.9b04407
![]() |
[108] |
Wojcieszak R, Itabaiana I (2020) Engineering the future: Perspectives in the 2, 5-furandicarboxylic acid synthesis. Catal Today 354: 211-217. doi: 10.1016/j.cattod.2019.05.071
![]() |
[109] |
Geyer R, Jambeck JR, Law KL (2017) Production, use, and fate of all plastics ever made. Sci Adv 3: 25-29. doi: 10.1126/sciadv.1700782
![]() |
[110] | Parker L, A whopping 91% of plastic isn't recycled, 2018. Available from: https://www.nationalgeographic.com/news/2017/07/plastic-produced-recycling-waste-ocean-trash-debris-environment/. |
[111] | Ritchie H, Roser M, Plastic Pollution, 2018. Available from: https://ourworldindata.org/plastic-pollution. |
[112] | Balasegaram M, Human Writes: Malaysia rated one of the world's worst for plastic pollution, 2019. Available from: https://www.thestar.com.my/lifestyle/living/2019/01/27/plastic-waste-malaysia/. |
[113] | Greenpeace Malaysia, The recycling myth: Malaysia and the broken global recycling system, 2018. Available from: https://www.greenpeace.org/static/planet4-southeastasia-stateless/2019/04/7c9f822c-7c9f822c-the-recycling-myth-malaysia-and-the-broken-global-recycling-system.pdf. |
[114] | Bendix A, Staggering photos show one small town covered in 19000 tons of plastic waste, 2019. Available from: https://www.businessinsider.my/malaysia-town-plastic-waste-china-photos-2019-2?r=US&IR=T. |
[115] | Singh S, Yeo: 139 illegal plastic recycling premises shut down nationwide, 2019. Available from: https://www.thestar.com.my/news/nation/2019/02/25/yeo-139-illegal-plastic-recycling-premises-shut-down-nationwide/. |
[116] |
Verma R, Vinoda KS, Papireddy M, et al. (2016) Toxic pollutants from plastic waste-A review. Procedia Environ Sci 35: 701-708. doi: 10.1016/j.proenv.2016.07.069
![]() |
[117] | Ananthalakshmi A, Chow E, Swamped with plastic waste: Malaysia struggles as global scrap piles up-Reuters, 2018. Available from: https://www.reuters.com/article/us-malaysia-waste/swamped-with-plastic-waste-malaysia-struggles-as-global-scrap-piles-up-idUSKCN1MZ0P4. |
[118] |
Carus M, Chinthapalli R, Skoczinski P, et al. (2019) Bio-based building blocks and polymers-global capacities, production and trends 2018-2023. Ind Biotechnol 15: 237-241. doi: 10.1089/ind.2019.29179.rch
![]() |
[119] | European Bioplastics (2018) Bioplastics market data 2018: Global production capacities of bioplastics 2018-2023. Available from: https://www.european-bioplastics.org/wp-content/uploads/2016/02/Report_Bioplastics-Market-Data_2018.pdf. |
[120] |
Duque-Acevedo M, Belmonte-Ureña LJ, Cortés-García FJ, et al. (2020) Agricultural waste: Review of the evolution, approaches and perspectives on alternative uses. Glob Ecol Conserv 22: e00902. doi: 10.1016/j.gecco.2020.e00902
![]() |
[121] | Barrett A, Turning agro waste into bioplastics, 2019. Available from: https://bioplasticsnews.com/2019/07/31/turning-agro-waste-into-bioplastics/. |
[122] | European Bioplastics, How much agricultural area is used for bioplastics?, 2020. Available from: https://www.european-bioplastics.org/avada_faq/how-much-agricultural-area-is-used-for-bioplastics/. |
[123] |
Maraveas C (2020) Production of sustainable and biodegradable polymers from agricultural waste. Polymers 12: 1127. doi: 10.3390/polym12051127
![]() |
[124] | Samer M (2019) Bioplastics production from agricultural crop residues. Agric Eng Int CIGR J 21: 190-194. |
[125] |
Mostafa NA, Farag AA, Abo-dief HM, et al. (2015) Production of biodegradable plastic from agricultural wastes. Arab J Chem 11: 546-553. doi: 10.1016/j.arabjc.2015.04.008
![]() |
[126] | Ramamoorthy P, Karthikeyan M (2020) Bioplastics from Agricultural Wastes. Available from: https://papers.ssrn.com/sol3/papers.cfm?abstract_id=3564039. |
[127] | Seaweed-based packaging, 2019. Available from: https://rethink-plastic.com/brand/evoware/. |
1. | Gbenga O. Ojo, Nazim I. Mahmudov, Aboodh Transform Iterative Method for Spatial Diffusion of a Biological Population with Fractional-Order, 2021, 9, 2227-7390, 155, 10.3390/math9020155 | |
2. | Mehmet Giyas Sakar, Onur Saldır, A New Reproducing Kernel Approach for Nonlinear Fractional Three-Point Boundary Value Problems, 2020, 4, 2504-3110, 53, 10.3390/fractalfract4040053 | |
3. | Nasir Ali, Rashid Nawaz, Laiq Zada, Abir Mouldi, Souhail Mohamed Bouzgarrou, Ndolane Sene, Taza Gul, Analytical Approximate Solution of the Fractional Order Biological Population Model by Using Natural Transform, 2022, 2022, 1687-4129, 1, 10.1155/2022/6703086 | |
4. | Ali Khalouta, Abdelouahab Kadem, Numerical Comparison of FNVIM and FNHPM for Solving a Certain Type of Nonlinear Caputo Time-Fractional Partial Differential Equations, 2020, 34, 2391-4238, 203, 10.2478/amsil-2020-0008 | |
5. | Nazek A. Obeidat, Daniel E. Bentil, Convergence analysis of the fractional decomposition method with applications to time‐fractional biological population models, 2023, 39, 0749-159X, 696, 10.1002/num.22916 | |
6. | Md Nur Alam, Onur Alp Ilhan, Jalil Manafian, Muhammad Imran Asjad, Hadi Rezazadeh, Haci Mehmet Baskonus, Jorge E. Macias-Diaz, New Results of Some of the Conformable Models Arising in Dynamical Systems, 2022, 2022, 1687-9139, 1, 10.1155/2022/7753879 | |
7. | Yeliz Karaca, Dumitru Baleanu, 2022, 9780323900324, 149, 10.1016/B978-0-323-90032-4.00006-7 | |
8. | Ayşe Ata, Mehmet Giyas Sakar, Onur Saldır, Mehmet Şenol, Finite and Infinite Dimensional Reproducing Kernel Hilbert Space Approach for Bagley–Torvik Equation, 2025, 11, 2349-5103, 10.1007/s40819-024-01828-z |
t/x,y | 0.1 | 0.3 | 0.5 | 0.7 |
0.1 | 1.4090×10−10 | 4.2269×10−10 | 7.0449×10−10 | 9.8629×10−10 |
0.3 | 1.0576×10−7 | 3.1727×10−7 | 5.2879×10−7 | 7.4030×10−7 |
0.5 | 2.3354×10−6 | 7.0062×10−6 | 1.1677×10−5 | 1.6348×10−5 |
0.7 | 1.8129×10−5 | 5.4387×10−5 | 9.0645×10−5 | 1.2690×10−4 |
0.9 | 8.4486×10−5 | 2.5346×10−4 | 4.2243×10−4 | 5.9140×10−4 |
t/x,y | 0.1 | 0.3 | 0.5 | 0.7 |
0.1 | 1.4090×10−10 | 4.2268×10−10 | 7.0425×10−10 | 9.8497×10−10 |
0.3 | 1.0576×10−7 | 3.1726×10−7 | 5.2860×10−7 | 7.3932×10−7 |
0.5 | 2.3354×10−6 | 7.0059×10−6 | 1.1673×10−5 | 1.6326×10−5 |
0.7 | 1.8129×10−5 | 5.4385×10−5 | 9.0614×10−5 | 1.2673×10−4 |
0.9 | 8.4486×10−5 | 2.5345×10−4 | 4.2228×10−4 | 5.9061×10−4 |
t/x,y | 0.1 | 0.3 | 0.5 | 0.7 |
0.1 | 1.5572×10−9 | 1.9019×10−9 | 2.3230×10−9 | 2.8373×10−9 |
0.3 | 1.1688×10−6 | 1.4276×10−6 | 1.7436×10−6 | 2.1297×10−6 |
0.5 | 2.5810×10−5 | 3.1525×10−5 | 3.8504×10−5 | 4.7029×10−5 |
0.7 | 2.0036×10−4 | 2.4472×10−4 | 2.9890×10−4 | 3.6507×10−4 |
0.9 | 9.3372×10−4 | 1.1404×10−3 | 1.3929×10−3 | 1.7013×10−3 |
t/x,y | 0.1 | 0.3 | 0.5 | 0.7 |
0.1 | 1.4090×10−10 | 4.2269×10−10 | 7.0449×10−10 | 9.8629×10−10 |
0.3 | 1.0576×10−7 | 3.1727×10−7 | 5.2879×10−7 | 7.4030×10−7 |
0.5 | 2.3354×10−6 | 7.0062×10−6 | 1.1677×10−5 | 1.6348×10−5 |
0.7 | 1.8129×10−5 | 5.4387×10−5 | 9.0645×10−5 | 1.2690×10−4 |
0.9 | 8.4486×10−5 | 2.5346×10−4 | 4.2243×10−4 | 5.9140×10−4 |
t/x,y | 0.1 | 0.3 | 0.5 | 0.7 |
0.1 | 1.4090×10−10 | 4.2268×10−10 | 7.0425×10−10 | 9.8497×10−10 |
0.3 | 1.0576×10−7 | 3.1726×10−7 | 5.2860×10−7 | 7.3932×10−7 |
0.5 | 2.3354×10−6 | 7.0059×10−6 | 1.1673×10−5 | 1.6326×10−5 |
0.7 | 1.8129×10−5 | 5.4385×10−5 | 9.0614×10−5 | 1.2673×10−4 |
0.9 | 8.4486×10−5 | 2.5345×10−4 | 4.2228×10−4 | 5.9061×10−4 |
t/x,y | 0.1 | 0.3 | 0.5 | 0.7 |
0.1 | 1.5572×10−9 | 1.9019×10−9 | 2.3230×10−9 | 2.8373×10−9 |
0.3 | 1.1688×10−6 | 1.4276×10−6 | 1.7436×10−6 | 2.1297×10−6 |
0.5 | 2.5810×10−5 | 3.1525×10−5 | 3.8504×10−5 | 4.7029×10−5 |
0.7 | 2.0036×10−4 | 2.4472×10−4 | 2.9890×10−4 | 3.6507×10−4 |
0.9 | 9.3372×10−4 | 1.1404×10−3 | 1.3929×10−3 | 1.7013×10−3 |