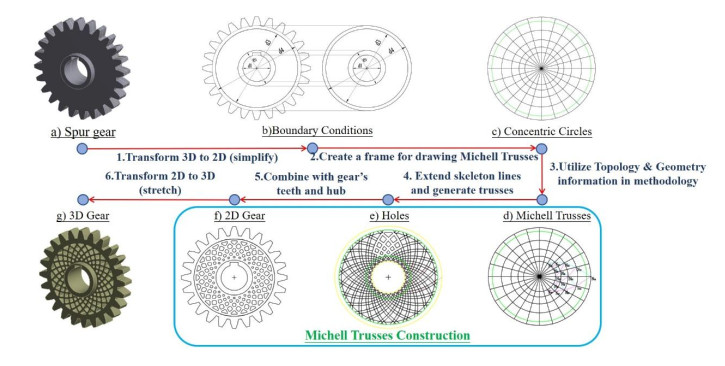
A new method for lightweight gear design based on Michell Trusses Design method was investigated in this research to compare with the traditional Topology Optimization method. A workflow with detailed steps was established using example of constructing Michell Trusses to make lightening holes at the gear's web. In this workflow, Michell Trusses are generated from a set of concentric circles. By solving the equation with the variables of concentric circles (complexity), the optimal orthogonality of trusses can be determined. Real experiments were conducted to compare the two design methods in the aspects of design costs and product mechanical property, including recording the time consumed in each link and detecting the force of failure of gears by a testing platform. The results indicate that this new method can significantly reduce design time while maintain the same power-to-weight ratio as the Topology Optimization design, which potentially provide a new research direction for lightweight structural modeling in mechanical engineering and aviation industry. The experimental product developed in this research demonstrated the promising prospects for real world applications.
Citation: Ganjun Xu, Ning Dai. Michell truss design for lightweight gear bodies[J]. Mathematical Biosciences and Engineering, 2021, 18(2): 1653-1669. doi: 10.3934/mbe.2021085
[1] | Ganjun Xu, Ning Dai, Sukun Tian . Principal stress lines based design method of lightweight and low vibration amplitude gear web. Mathematical Biosciences and Engineering, 2021, 18(6): 7060-7075. doi: 10.3934/mbe.2021351 |
[2] | Shuang Tan, Shangrui Zhao, Jinran Wu . QL-ADIFA: Hybrid optimization using Q-learning and an adaptive logarithmic spiral-levy firefly algorithm. Mathematical Biosciences and Engineering, 2023, 20(8): 13542-13561. doi: 10.3934/mbe.2023604 |
[3] | Zhiqin Zhu, Shaowen Wang, Shuangshuang Gu, Yuanyuan Li, Jiahan Li, Linhong Shuai, Guanqiu Qi . Driver distraction detection based on lightweight networks and tiny object detection. Mathematical Biosciences and Engineering, 2023, 20(10): 18248-18266. doi: 10.3934/mbe.2023811 |
[4] | Zhen Liu, Song Yang, Chen Cheng, Tao Ding, Ruimin Chai . Study on modeling and dynamic performance of a planar flexible parallel manipulator based on finite element method. Mathematical Biosciences and Engineering, 2023, 20(1): 807-836. doi: 10.3934/mbe.2023037 |
[5] | Xiaorui Yang, Yumei Zhang, Xiaojiao Lv, Honghong Yang, Zengguo Sun, Xiaojun Wu . Hybrid multi-strategy chaos somersault foraging chimp optimization algorithm research. Mathematical Biosciences and Engineering, 2023, 20(7): 12263-12297. doi: 10.3934/mbe.2023546 |
[6] | Mazhar Ali Dootio, Abdullah Lakhan, Ali Hassan Sodhro, Tor Morten Groenli, Narmeen Zakaria Bawany, Samrat Kumar . Secure and failure hybrid delay enabled a lightweight RPC and SHDS schemes in Industry 4.0 aware IIoHT enabled fog computing. Mathematical Biosciences and Engineering, 2022, 19(1): 513-536. doi: 10.3934/mbe.2022024 |
[7] | Yijie Zhang, Yuhang Cai . Adaptive dynamic self-learning grey wolf optimization algorithm for solving global optimization problems and engineering problems. Mathematical Biosciences and Engineering, 2024, 21(3): 3910-3943. doi: 10.3934/mbe.2024174 |
[8] | Xiaoyang Zhao, Xinzheng Xu, Hu Chen, Hansang Gu, Zhongnian Li . FAPI-Net: A lightweight interpretable network based on feature augmentation and prototype interpretation. Mathematical Biosciences and Engineering, 2023, 20(4): 6191-6214. doi: 10.3934/mbe.2023267 |
[9] | Qian Wu, Yuyao Pei, Zihao Cheng, Xiaopeng Hu, Changqing Wang . SDS-Net: A lightweight 3D convolutional neural network with multi-branch attention for multimodal brain tumor accurate segmentation. Mathematical Biosciences and Engineering, 2023, 20(9): 17384-17406. doi: 10.3934/mbe.2023773 |
[10] | Yong Zhu, Zhipeng Jiang, Xiaohui Mo, Bo Zhang, Abdullah Al-Dhelaan, Fahad Al-Dhelaan . A study on the design methodology of TAC3 for edge computing. Mathematical Biosciences and Engineering, 2020, 17(5): 4406-4421. doi: 10.3934/mbe.2020243 |
A new method for lightweight gear design based on Michell Trusses Design method was investigated in this research to compare with the traditional Topology Optimization method. A workflow with detailed steps was established using example of constructing Michell Trusses to make lightening holes at the gear's web. In this workflow, Michell Trusses are generated from a set of concentric circles. By solving the equation with the variables of concentric circles (complexity), the optimal orthogonality of trusses can be determined. Real experiments were conducted to compare the two design methods in the aspects of design costs and product mechanical property, including recording the time consumed in each link and detecting the force of failure of gears by a testing platform. The results indicate that this new method can significantly reduce design time while maintain the same power-to-weight ratio as the Topology Optimization design, which potentially provide a new research direction for lightweight structural modeling in mechanical engineering and aviation industry. The experimental product developed in this research demonstrated the promising prospects for real world applications.
It is well known that Additive Manufacturing (AM) can provide an exclusive design scheme for parts based on their characteristics. It can realize the macroscopic structural design in topology, and also make full use of the design domain brought by the changes on multiple scales or the spatial gradient, which greatly improves the product performance [1]. Therefore it applies to a wide range of industries, including medical engineering [2], automotive [3], aerospace [4] and civil engineering [5]. However, it is always necessary to provide a suitable design tool especially for a complex part design, which is considered a major obstacle for the implementation of AM [6]. There are four mainstream AM design methods to generate lightweight structure: reinforcing shells with protruding rib design, lattice structure design, integrated structure design, and complex-shaped Topology Optimization (TO) structure design.
TO is recognized as one of the most promising techniques in the design of aircraft and aerospace structure [7]. Technical difficulties in the development of aeronautics and aerospace structural engineering promote rapid progress in TO theories. Currently, the research on TO of continuum structures focused on Homogenization method, Solid Isotropic Material with Penalization (SIMP), Evolutionary Structural Optimization (ESO) and Level Set method. However, there are two problems in the implementation of the above methods: (a) overwhelmingly huge amount of computation in FEA (dimensional disaster); (b) time-consuming manual process of reconstructing models with computer-aided design (CAD) tools. Therefore, TO may not be applicable to all part design, and the approach to directly forward-design the structure needs to be further explored.
Michell structures reveal the truss-like characteristics in TO, and its optimal trusses under load and boundary conditions are generated by analytical method [8]. Michell's Truss, characterized by the minimal weight and the maximum stiffness, have significantly influenced the contemporary architectural forms as well as the structural design concepts in modern civil engineering. When applying Michell Truss Design (MTD) method in lightweight design, it is not difficult to find that MTD method is an analytical method with huge mathematical calculation cost, which requires designers having strong ability to solve equations and matrix calculation. Therefore, it is the reason why this directly forward design is lack of literatures reported in practical engineering applications.
In this research, a new method was presented to create Michell Trusses from a set of concentric circles, which is a kind of analytical method with diagrams based on basic parameters of gears. By solving the equation with the variables of concentric circles (complexity), the optimal orthogonality of trusses can be determined. Compared with the traditional method, this new method is more efficient and cost effective to construct Michell Trusses. Lightweight gear bodies were designed using the new method and experiments were conducted to compare with the TO design in the aspects of design costs and product mechanical property. The results indicate that this new method can significantly reduce design time while maintain the same power-to-weight ratio as the TO design, which potentially provide a new idea or research direction for lightweight structural modeling in mechanical engineering and aviation industry.
Due to its friendly-to-manufacture property, AM has been extensively applied to solving complex engineering design problems with a wide range of industrial applications. Meanwhile, several design methods for AM have been promoted rapid progress, such as TO, Michell Trusses Design and Lightweight Design. However, each of these methods have some problems which make it difficult to be implemented. In this section, a review of relative research of these methods are summarized as below.
TO: As a freeform material distribution scheme, TO enables the creation, merging and splitting of the interior solids and voids during the structural evolution, therefore, a much larger design space can be explored [1]. A typical example of Topology Optimization solution is the leading edge droop nose ribs for Airbus 380, which achieved structural weight saving design meeting all mechanical performance requirements [9]. A typical Topology Optimization design of an aircraft pylon, which satisfied stiffness, strength and weight requirements [10]. Unfortunately, two major challenges have limited the applicability of TO in applications: overwhelmingly huge computational expense and subsequent detailed post-processing. Zhang et al. [11] indicated that a TO problem often involves a large number of design variables to guarantee sufficient expressive power. In addition, many TO problems require a large number of expensive FEA model simulations, which cannot be parallelized. Niels et al. [12] indicated that TO is an iterative and sequential procedure, which is not straightforward to be parallelized. Joe et al. [13] indicated that a typical large-scale TO problem may involve hundreds or even thousands of design iterations, and for each iteration, the physical response needs to be solved to compute the gradient information through sensitivity analysis. Anton et al. [14] indicated that large-scale TO problem always involves millions of design variables, the associated computational cost is highly prohibitive and will be larger and larger in the future since the problem are becoming more complex with more details. Additionally, the resulting optimal design from TO often needs subsequent detailed post-processing. Otherwise, it is impossible to be applied directly in engineering practice because its material layout includes holes of arbitrary and complex shapes, zigzag boundary, grayscale images and many tiny features, etc. Zhang et al. [15] indicated that most engineering applications require simple geometric feature and smooth boundary, especially for manufacturing. For the reasons above, designers have to consider whether TO is the only effective solution to solve the problems.
Michell Trusses Design method: MTD method is widely used in Civil and mechanical engineering, which illustrates the structure of the optimal force transmission path and inspires designers to adopt truss-like strategy to interpret the resulting conceptual design. Kwok et al. [7] indicated that studies usually solve the principal stress lines to predict the locations of possible cracks based on Michell Truss Theory and set reinforcement bars at those locations. Gao et al. [16] indicated that reinforcement will work more effectively in tensile and the overall structural stiffness can be improved, which has been successfully applied to the layout optimization design of support frames for high-rise buildings and long-span bridges. Krog et al. [9] proposed a way of interpreting regions with high density of material as structural truss and regions with low density of material as voids, the TO designs can be interpreted as truss-like structures. Based on truss-like approach it is easy to construct the parameterized optimization model. Zhou et al. [17] indicated if the positions of the nodes and the cross sectional areas of the members are optimized, the final optimal truss structures are established. The above examples show that MTD method has been successfully applied into some engineering applications and it is worthy being explored in other applications.
Lightweight gear design: With the constant improvement of helicopters' flight speed and load capacity, reducing weight and improving power-to-weight ratio are the goals pursued by high-performance helicopter transmission system. Upon reducing the weight of models through structural lightweight design, the weight and energy consumption of the helicopters can be effectively reduced, and the endurance and maneuverability can be improved. As one of the crucial parts in the mechanical power transmissions of helicopters, the lightweight design method of gear has gradually become the research focus of scholars worldwide. With the increasing demands on less weight, higher speed, and improved running conditions, Robert et al. [18] brought composite spur gears into fabrication. The composite material serves as the web of the gear between the gear teeth and a metallic hub for mounting to the torque-applying shaft. Compared with an initially all-metallic aerospace quality spur gear, the composite gears were found to be 20% lighter. Ramadani et al. [19] proposed a lightweight gear whose solid gear body was replaced by a lattice structure with optimal layout through TO and it was found to be 58.8% lighter, compared with the original solid gear body. Nowadays, lightweight modeling of gears based on MTD method is a research frontier with a lack of technical theories and has not been reported in literatures. Research presented in this paper aims to fill this gap.
The design workflow is shown in Figure 1. The goal is to reduce the weight of gears is to design Michell Truss while maintain maximum stiffness of the gear bodies. This method is divided into 6 steps: (a) obtain the boundary parameters of the gear; (b) create a frame for drawing Michell Trusses; (c) utilize topology and geometry information in Michell Truss method to generate skeleton lines; (d) extend skeleton lines and generate trusses; (e) combine the holes with the gear features (teeth, hub and keyway) into a new sketch; (f) stretch the drawing to generate the 3D model.
The detailed description for generating holes is shown in Figure 2. This process is divided into 4 steps: (a) offset the skeleton lines to both sides, and generate a truss with width; (b) array the truss around the center by Z times; (c) remove extra lines and keep the holes; (d) array the holes around the center by Z times.
In this process, several parameters related to design should be paid more close attention:
(I) Michell Trusses are generated by arraying around the center and the times z in arraying is exactly the number of teeth z of the gear.
(II) The width of Michell Trusses is obtained by offsetting the skeleton lines to both sides by w, which is related to the modulus m of the gear.
(III) In order to improve the mechanical properties of gear, chamfering the holes can effectively reduce the stress concentration.
The Michell Truss is to be restricted in a group of concentric circles. The way to construct the Michell Truss is to connect the Michell Truss nodes into the Michell Truss, where the nodes of Michell Truss are geometry information and the connection order of Michell Truss nodes is topology information.
Figure 3(a) shows 4 Michell Trusses, M1,M2,M3,M4, which are connected by the nodes on the concentric circles. The nodes is marked as Nmn, and m and n are the node's corners to describe the topology information of nodes in Michell Truss method. There are two definitions on the relationship of topology in Michell Truss as listed below.
Definition 1: On the same concentric circle, the sum of corner values of two nodes are equal, and it is also the complexity of the concentric circle q (the total number of concentric circles) [20]. For example, for the nodes Nmn and Nik, m + n = i + k = q.
Definition 2: All nodes on the same Michell Truss will have the same corner mark equal, and another corner mark is the order of the concentric circle. The right side graph in Figure 3(b) shows the nodes on one of the Michell Truss are Nm1,Nm2,⋯,Nmn, where the first corner mark values of these nodes are equal, and the second corner mark value is the order of the concentric circle where the node is located.
Through the intersection of the concentric circles and cutting lines, the nodes of the Michell Truss will be connected. The size of the concentric circle depends on three parameters: uniform angle α, complexity q and the angle of intersecting Michell Trusses θ. In Figure 4, four Michell Trusses are distributed to five concentric circles, whose radius values respectively equal the length of ON00,ON01,ON02,ON03,ON04 and equals r0,r1,r2,r3,r4.
There are two definitions on the relationship of geometric mathematics in Michell Truss as listed below.
Definition 3: The length of each Michell Truss is multiplied from the inner loop to outer loop, i.e., l0,l1,l2,l3,l4 with a multiplied relationship. According to properties of similar triangles, r0,r1,r2,r3,r4 are also with a multiplied relationship [20].
ln+1=kln,rn+1=krn,n=0,1,2,3,4 | (1) |
Where k=sinθsin(θ+α)=(r4r0)1/q.
As depicted in Figure 5, in △ON04N03, based on Sine Law, there is
r4sinθ=l4sinα=r3sin(α+θ) | (2) |
In △ON03N02, there is
r3sinθ=l3sinα=r2sin(α+θ) | (3) |
So, the multiplied relationship of Michell Truss is
l4l3=r4r3=sinθsin(θ+α) | (4) |
Definition 4: The Michell Trusses are orthogonal i.e., their angles are as close to 90° as possible. If trusses are orthogonal to each other, the truss will be the shortest and the strongest [21]. By modifying the Michell Trusses' length and complexity, the value of γ (the angle of Michell Trusses) can approach 90°. Figure 6(a) [21] shows the orthogonal properties of the Michell and Figure 6(b) shows the location of γ.
As such, in order to develop the equation related to γ, △ON04N03 needs to be located in quadrilateral ON04N03N02. If taking Cosine formula for ∠ON04N03, then the following equation is developed:
cosφ=r24+l24−r232r4l4 | (5) |
According to the boundary conditions and loads, the principal stress line can be calculated based on Michell Trusses method. Taking simply supported beams as an example, according to the geometric features of Michell Trusses: (a) the length of each trusses is multiplied; (b) the intersecting trusses are orthogonal, and the Michell Truss will be shown in Figure 7. In order to verify the consistency between the Michell Truss and the principal stress line in Mechanics, the method of drawing the principal stress field of the simply supported beam should be introduced: the beam is divided into uniform grids, and the stress states of all grid nodes constitute the beam's principal stress field [22]. The stress state of each node consists of σx,σy,σz, where
σx=MxIx,σy=MyIy,τ=FsS∗zIzt | (6) |
Where Fs is shear force, M is bending moment, Ix,Iy,Iz are polar moment of inertial and S∗z is moment.
Ix=hb312,Iy=bh312,Iz=th312 | (7) |
S∗z=∫AxdA=∫h/2xbxdx=b2(h24−x2) | (8) |
Then, we will get the direction angle α0 of principle stress of each node by the following formula
tan2α0=−2τxyσx−σy | (9) |
If placing the principal stress line arrived from the Michell Truss theory into the principal stress field, it is found that the tangent direction of the points on the principal stress line coincides with the direction of the nodes of the main stress field. In this case, Michell Truss is the principal stress line.
Michell Truss Method and TO were independently applied in lightweight part design of the same spur gear. The basic of design data are shown in Table 1.
Parameters | Values |
Number of teeth, z | 24 |
Normal module | 6 mm |
Pressure angle | 20° |
Root diameter, d4 | 129 mm |
Gear body outer diameter, d3 | 119 mm |
Gear body inner diameter, d2 | 54 mm |
Hub diameter | 40 mm |
As depicted in Figure 8, Number of teeth z, Root diameter d4, Gear body outer diameter d3 and Gear body inner diameter d2 are the key boundary parameters of a spur gear.
In this application, gear has 24 teeth, which means the concentric circles that generate Michell Truss will be divided into 24 parts and uniform angle α will be 15°. According to the Geometry Information in Section 4.2, an equation with variables with trusses' angle γ and complexity q can be developed.
arccos1+sin2αsin2[90∘−12(α+γ)]−1(r4r0)2/q2sinαsin[90∘−12(α+γ)]−[90∘−12(α+γ)]−γ=0 | (10) |
When γ value is 90°, q is 4.44. Since q present the number of concentric circles, q should be an integer. Therefore, q is rounded by 4 and k values 1.34. Then, according to Eq (1), when r0 value is 40, diameter of concentric circles of each order can be calculated and they are listed in the Table 2.
Complexity | 0 | 1 | 2 | 3 | 4 |
Diameter value /mm | 129 | 96 | 72 | 54 | 40 |
Firstly, according to the concentric circle diameters of each order in Section 5.1.1, construct a frame with a set of concentric circles. Secondly, Michell Truss skeleton lines are drawn according to the topology information in Section 4.1. Lastly, expand outward the skeleton lines of Michell Truss to generate the final trusses with width. As depicted in Figure 9, the angle between each truss is close to 90°, which indicates that the trusses were approximately orthogonal and proves that the Michell Truss was designed successfully.
The design workflow is shown in Figure 10. Design method of gears in TO can be divided into 2 parts: (I) Topology Optimization solving, including 4 subprocesses: (a) transform spatial stress into plane stress, (b) mesh, (c) FEA and (d) Topology Optimization; (II) model reconstruction, including 3 subprocesses: (a) map the holes edges to the sketch, (b) combine the holes with the gear features and (c) stretch the drawing to generate the 3D model.
In the TO software, there are mainly three parameters in design and they are design domain, retention rate and degree of symmetry. By setting the retention rate to 30%, 40%, 50%, 60%, 70%, 80% and 90%, we get a series of gears after Topology Optimization in Figure 11.
Power-to-weight ratio is the ratio between the bearing capacity of a structure and its mass, which is used to evaluate the effect of lightweight. When 100%, the structure will behave well in lightweight and Mechanics. Table 3 has shown Mechanical behavior of a series of Topology Optimization gears, such as mass reduction, strength weakness and power-to-weight ratio. Figure 12 indicates: the gear with 60% retention rate, whose power-to-weight ratio was just over 100%, was determined to be the optimal design.
Retention rate in Topology Optimization /% | Mass reduction /% | Strength weakness /% | Power-to-weight ratio /% |
40 | 28.69 | 49.70 | 57.73 |
50 | 23.99 | 28.79 | 83.33 |
60 | 17.82 | 13.10 | 136.03 |
70 | 14.12 | 8.40 | 168.10 |
80 | 6.43 | 1.967 | 326.89 |
90 | 2.95 | 0.173 | 1705.20 |
In order to obtain the failure force of gears, a testing platform NHGearTest3000 had been constructed to simulate the loading process of a pair of gears when meshing in Figure 13. The platform consists of a Metal Gear, a Motor with variable-frequency drive (VFD) and a Fixed Shaft where Test Gear is fixed on the Motor by key while Metal Gear is fixed on the Fixed Shaft unrotated. There are two critical requirements for the installation: (a) the central axis of the two gears should be in the same horizontal position; (b) the center distance of the two gears equals the gear diameter.
With the increase of the torque from the motor, the torque on Test Gear also increased. The motor's value was recorded when the gears got broken. According to the following Eq (11), the value of frequency could be converted to the value of failure force.
n=60fp,T=9550×Pn,F=TR | (11) |
In this paper, we selected the spur gear (Number of teeth is 24, Normal module is 6 mm and thickness is 24 mm) as the lightweight object. As depicted in Figure 14, Solid gear Figure 14(a), Topology Optimization gear Figure 14(b) and Michell Truss gear Figure 14(c) were produced by SLA and their mass are 380,302 and 297 g, respectively.
In this experiment, the value of frequency was recorded when gear's tooth fractured in Figure 15. Then, according to formula (11), the value of failure force can be calculated as follows:
(I) Solid gear Figure 14(a) is 663.125 N;
(II) Topology Optimization gear Figure 14(b) is 571.474 N;
(III) Michell Truss gear Figure 14(c) is 566.082 N.
The design efficiency of the two methods was compared by recording the time consumed in each link of the design.
In Section 5.2, we introduced Topology Optimization design method of gears which consists of 2 steps: (a) Topology Optimization solving. For a general FEA solving, the number of design variables is directly determined by the mesh resolution of the finite element model. the time T consumed by CPU in an iteration step can be roughly estimated as T∝O(n3) and T∝O(m), where n and m are respectively the number of design variables and the number of effective constraint functions at the optimal solution. (b) Model reconstruction. Since one part after traditional Topology Optimization method is generated based on pixel, and the CAD system defines the geometry of model by B-spline curve. In order to get the final optimal model, designers have to carry out complex reconstruction in geometry. (c) Reconstructed as many models as possible in order to select the best one. Topology Optimization is a problem where designers should explore weight reduction and keep stiffness to some extent. So, multiple groups of control experiments should be set through changing the retention rate, where time will be grown exponentially.
When it comes to Michell Truss Methodology in Sections 4, it is just solving an equation with its boundary parameters. Putting the boundary conditions of the gear into our self-designed software, the solution can be faster. Compared with the former method in Table 4, the latter shorten approximately 12.8 times design time.
Method | Time consuming process /h | Total time /h | ||
Topology Optimization | Default retention rate 50% | Test retention rate (30%, 40%, 60%, 70%, 80%, 90%) | 9.1 | |
Topology Optimization solving | Model reconstruction | Parallel design (× 6) | ||
0.5 | 0.8 | 7.8 | ||
Michell Truss Design | Construct topology and Geometry information | Drawing Michell Truss | 0.66 | |
0.33 | 0.33 |
Table 5 indicates: (a) in the aspect of mass, Michell Truss gear is very close to Topology Optimization gear, which proves that Michell Truss gear is the geometric interpretation of Topology Optimization gear; (b) in the aspect of failure force, Michell Truss gear is also very close to Topology Optimization gear, which proves that Michell Truss gear is equivalent to Topology Optimization gear mechanically; (c) in the aspect of power-to-weight ratio, Michell Truss gear is superior to Topology Optimization gear, it is because that Michell Truss gear is generated by B-spline curve instead of the discrete surfaces after Topology Optimization, which reduces the stress concentration and improve the comprehensive mechanical performance of the gear. Compared with Topology Optimization gear, Michell Truss gear is lighter and with a higher power-to-weight ratio, which proves that Michell Truss gear behaves better in mechanics behavior.
Type | Mass (g) | Weight reduction (%) | Failure force (N) | Strength reduction(%) | Power-to weight ratio(%) |
Solid gear Figure 14(a) | 380 | - | 663.125 | - | - |
Topology Optimization gear Figure 14(b) | 302 | 20.53 | 571.474 | 13.82 | 148.55 |
Michell Truss gear Figure 14(c) | 297 | 21.84 | 566.082 | 14.63 | 149.28 |
Two methods, Topology Optimization and Michell Truss Method, to design the lightweight spur gears are compared. Some conclusions are as follows:
(I) By defining design domains, loads, and boundary conditions, Topology Optimization can be easily applied to the design of lightweight gears. However, FEA, model reconstruction and multi-groups of controlled experiments are time consuming. However, if the Michell Truss Method is applied for the gear bodies, it can reduce the design time to be approximately 12.8 times compared with Topology Optimization. On the other hand, utilizing B-spline curve and replacing the discrete surface generated from Topology Optimization, it can reduce stress concentration and slightly improve the mechanical properties of the gear.
(II) The algorithm of Topology Optimization is complex and is not conducive to explore weight reduction and stiffness, Michell Truss Method is an analytical method. By adjusting the design parameters of the formula in Michell Truss Method, it helps designers to grasp the relationship between the distribution of material and structural mechanical properties, to construct the optimally orthogonal Trusses.
(III) When dealing with low-dimensional gears such as those gears with fewer teeth or planar gears, this method can reduce considerable workload. As for high-dimensional gears, the effect will be more obvious.
This study was financially supported by Jiangsu Province Science and Technology Support Plan Project (No.BE2018010-2), Open-End Fund for Graduate Students (Nanjing University of Aeronautics and Astronautics) (No. kfjj20200512), National Natural Science Foundation of China (Grant No. 51775273), National Defence Basic Scientific Research Program of China (No.JCKY2018605C010), Frontiers of science and Technology Program of China (No. 18-163-12-ZT-004-063-01).
The authors declare that there is no conflict of interests regarding the publication of this paper.
[1] | W. Zhang, J. Zhu, T. Gao, Basic formulation of topology optimization, in Topology Optimization in Engineering Structure Design, ISTE Press, (2016), 1–9. |
[2] |
W. Chen, N. Dai, J. Wang, H. Liu, D. Li, L. Liu, Personalized design of functional gradient bone tissue engineering scaffold, J. Biomech. Eng., 141 (2019), 111004. doi: 10.1115/1.4043559
![]() |
[3] | T. Lewiński, T. Sokół, C. Graczykowski, Selected classes of spatial Michell's structures, in Michell Structures, Springer, (2019), 409–432. |
[4] | J. Deaton, D. Ramana, V. Grandhi, A survey of structural and multidisciplinary continuum topology optimization: post 2000, Struct. Multidiscip. Optim., 49 (2013), 1–38. |
[5] |
L. Stromberg, A. Beghini, W. Baker, G. Paulino, Topology optimization for braced frames: Combining continuum and beam/column elements, Eng. Struct., 37 (2012), 106–124. doi: 10.1016/j.engstruct.2011.12.034
![]() |
[6] | M. Biedermann, M. Meboldt, Computational design synthesis of additive manufactured multi-flow nozzles, Addit. Manuf., 35 (2020), 101231. |
[7] |
J. Liu, A. T. Gaynor, S. Chen, Z. Kang, K. Suresh, A. Takezawa, et al., Current and future trends in topology optimization for additive manufacturing, Struct. Multidiscip. Optim., 57 (2018), 2457–2483. doi: 10.1007/s00158-018-1994-3
![]() |
[8] |
T. H. Kwok, Y. Li, Y. Chen, A structural topology design method based on principal stress line, Comput. Aided Des., 80 (2016) 19–31. doi: 10.1016/j.cad.2016.07.005
![]() |
[9] | L. Krog, A. Tucker, G. Rollema, Application of topology, sizing and shape optimization methods to optimal design of aircraft components, Airbus UK, Altair Engineering, 2002. |
[10] |
J. Zhu, W. Zhang, L. Xia, Topology optimization in aircraft and aerospace structures design, Arch. Comput. Methods Eng., 23 (2016), 595–622. doi: 10.1007/s11831-015-9151-2
![]() |
[11] | S. Bi, J. Zhang, G. Zhang, Scalable deep-learning-accelerated topology optimization for additively manufactured materials, preprint, arXiv: 2011.14177. |
[12] |
A. Niels, A. Erik, S. Boyan, S. Ole, Giga-voxel computational morphogenesis for structural design, Nature, 550 (2017), 84-86. doi: 10.1038/nature23911
![]() |
[13] |
A. Joe, S. Ole, A. Niels, Large scale three-dimensional topology optimisation of heat sinks cooled by natural convection, Int. J. Heat Mass Tran., 100 (2016), 876–891. doi: 10.1016/j.ijheatmasstransfer.2016.05.013
![]() |
[14] |
E. Anton, J. Cory, M. Kurt, L. Martin, Large-scale parallel topology optimization using a dual-primal substructuring solver, Struct. Multidiscip. Optim., 36 (2008), 329–345. doi: 10.1007/s00158-007-0190-7
![]() |
[15] |
J. Zhang, B. Wang, F. Niu, G. Cheng, Design optimization of connection section for concentrated force diffusion, Mech. Based Des. Struct., 43 (2015), 209–231. doi: 10.1080/15397734.2014.942816
![]() |
[16] |
D. Gao, On topology optimization and canonical duality method, Comput. Method Appl. M, 341 (2018), 249–277. doi: 10.1016/j.cma.2018.06.027
![]() |
[17] |
K. Zhou, X. Li, Topology optimization of truss-like continua with three families of members model under stress constraints, Struct. Multidiscip. Optim., 43 (2011), 487–493. doi: 10.1007/s00158-010-0584-9
![]() |
[18] | R. Handschuh, G. Roberts, R. Sinnamon, D. Stringer, B. Dykas, L. Kohlman, Hybrid gear preliminary results-application of composites to dynamic mechanical components, NASA TM, (2012), 217630. |
[19] |
R. Ramadani, A. Belsak, M. Kegl, J. Predan, S. Pehan, Topology optimization based design of lightweight and low vibration gear bodies, Int. J. Simul. Model., 17 (2018), 92–104. doi: 10.2507/IJSIMM17(1)419
![]() |
[20] | A. Mazurek, W. Baker, C. Tort, Geometrical aspects of optimum truss like structures, Struct. Multidiscip. Optim., 43 (2010), 231–242. |
[21] | R. E. Skelton, M. C. de Oliveira, Optimal tensegrity structures in bending: The discrete Michell truss, J. Franklin Inst., 347 (2010), 257–283. |
[22] | K. Tam, C. Mueller, Stress line generation for structurally performative architectural design, ACADIA 2015: Comput. Ecologies, 2015. |
1. | Ganjun Xu, Ning Dai, Sukun Tian, Principal stress lines based design method of lightweight and low vibration amplitude gear web, 2021, 18, 1551-0018, 7060, 10.3934/mbe.2021351 | |
2. | Blagoja Nestorovski, Elena Angeleska, Nikola Avramov, D.P. Karaivanov, Load carrying capacities of gears with a lattice structure body, 2023, 387, 2261-236X, 02001, 10.1051/matecconf/202338702001 | |
3. | Kazuki Hayashi, Yoshiki Jikumaru, Yohei Yokosuka, Kentaro Hayakawa, Kenji Kajiwara, Parametric generation of optimal structures through discrete exponential functions: unveiling connections between structural optimality and discrete isothermicity, 2024, 67, 1615-147X, 10.1007/s00158-024-03767-1 | |
4. | Cemal İrfan Çalışkan, A novel synchronous scanning strategy in laser powder bed fusion and effect on mechanical properties of industrial gears, 2023, 128, 0268-3768, 2459, 10.1007/s00170-023-12109-2 | |
5. | Eduardo da Rosa Vieira, Daniel Milbrath de Leon, Rogério José Marczak, Optimization of plates reinforced with different initial slope and variable number of carbon fibers, 2023, 20, 1679-7825, 10.1590/1679-78257584 | |
6. | Cemal İrfan Çalışkan, Hamaid Mahmood Khan, Gökhan Özer, Mustafa Enes Bulduk, Mert Coşkun, Evaluation of Lattice Material Suitability for Additive Manufactured Gears under Compression Loads, 2025, 78, 0972-2815, 10.1007/s12666-024-03529-z | |
7. | Pengfei Yan, Dahai Zhang, Fangzhou Lu, Peifei Xu, Qingguo Fei, Design of the Truss Wing Structure Based on Principal Stress Trajectory Method, 2025, 0021-8669, 1, 10.2514/1.C038223 |
Parameters | Values |
Number of teeth, z | 24 |
Normal module | 6 mm |
Pressure angle | 20° |
Root diameter, d4 | 129 mm |
Gear body outer diameter, d3 | 119 mm |
Gear body inner diameter, d2 | 54 mm |
Hub diameter | 40 mm |
Complexity | 0 | 1 | 2 | 3 | 4 |
Diameter value /mm | 129 | 96 | 72 | 54 | 40 |
Retention rate in Topology Optimization /% | Mass reduction /% | Strength weakness /% | Power-to-weight ratio /% |
40 | 28.69 | 49.70 | 57.73 |
50 | 23.99 | 28.79 | 83.33 |
60 | 17.82 | 13.10 | 136.03 |
70 | 14.12 | 8.40 | 168.10 |
80 | 6.43 | 1.967 | 326.89 |
90 | 2.95 | 0.173 | 1705.20 |
Method | Time consuming process /h | Total time /h | ||
Topology Optimization | Default retention rate 50% | Test retention rate (30%, 40%, 60%, 70%, 80%, 90%) | 9.1 | |
Topology Optimization solving | Model reconstruction | Parallel design (× 6) | ||
0.5 | 0.8 | 7.8 | ||
Michell Truss Design | Construct topology and Geometry information | Drawing Michell Truss | 0.66 | |
0.33 | 0.33 |
Type | Mass (g) | Weight reduction (%) | Failure force (N) | Strength reduction(%) | Power-to weight ratio(%) |
Solid gear Figure 14(a) | 380 | - | 663.125 | - | - |
Topology Optimization gear Figure 14(b) | 302 | 20.53 | 571.474 | 13.82 | 148.55 |
Michell Truss gear Figure 14(c) | 297 | 21.84 | 566.082 | 14.63 | 149.28 |
Parameters | Values |
Number of teeth, z | 24 |
Normal module | 6 mm |
Pressure angle | 20° |
Root diameter, d4 | 129 mm |
Gear body outer diameter, d3 | 119 mm |
Gear body inner diameter, d2 | 54 mm |
Hub diameter | 40 mm |
Complexity | 0 | 1 | 2 | 3 | 4 |
Diameter value /mm | 129 | 96 | 72 | 54 | 40 |
Retention rate in Topology Optimization /% | Mass reduction /% | Strength weakness /% | Power-to-weight ratio /% |
40 | 28.69 | 49.70 | 57.73 |
50 | 23.99 | 28.79 | 83.33 |
60 | 17.82 | 13.10 | 136.03 |
70 | 14.12 | 8.40 | 168.10 |
80 | 6.43 | 1.967 | 326.89 |
90 | 2.95 | 0.173 | 1705.20 |
Method | Time consuming process /h | Total time /h | ||
Topology Optimization | Default retention rate 50% | Test retention rate (30%, 40%, 60%, 70%, 80%, 90%) | 9.1 | |
Topology Optimization solving | Model reconstruction | Parallel design (× 6) | ||
0.5 | 0.8 | 7.8 | ||
Michell Truss Design | Construct topology and Geometry information | Drawing Michell Truss | 0.66 | |
0.33 | 0.33 |
Type | Mass (g) | Weight reduction (%) | Failure force (N) | Strength reduction(%) | Power-to weight ratio(%) |
Solid gear Figure 14(a) | 380 | - | 663.125 | - | - |
Topology Optimization gear Figure 14(b) | 302 | 20.53 | 571.474 | 13.82 | 148.55 |
Michell Truss gear Figure 14(c) | 297 | 21.84 | 566.082 | 14.63 | 149.28 |