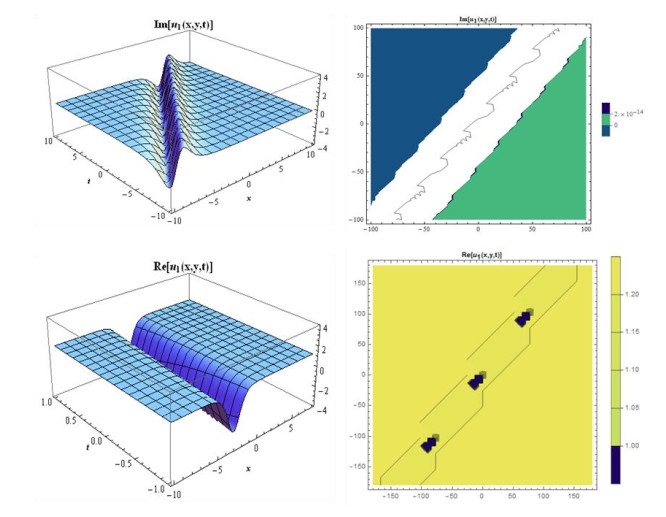
Citation: Péter Battyányi, Karim Nour. Normalization proofs for the un-typed μμ-calculus[J]. AIMS Mathematics, 2020, 5(4): 3702-3713. doi: 10.3934/math.2020239
[1] | Chander Bhan, Ravi Karwasra, Sandeep Malik, Sachin Kumar, Ahmed H. Arnous, Nehad Ali Shah, Jae Dong Chung . Bifurcation, chaotic behavior and soliton solutions to the KP-BBM equation through new Kudryashov and generalized Arnous methods. AIMS Mathematics, 2024, 9(4): 8749-8767. doi: 10.3934/math.2024424 |
[2] | Abdullahi Yusuf, Tukur A. Sulaiman, Mustafa Inc, Sayed Abdel-Khalek, K. H. Mahmoud . M−truncated optical soliton and their characteristics to a nonlinear equation governing the certain instabilities of modulated wave trains. AIMS Mathematics, 2021, 6(9): 9207-9221. doi: 10.3934/math.2021535 |
[3] | M. Hafiz Uddin, M. Ali Akbar, Md. Ashrafuzzaman Khan, Md. Abdul Haque . New exact solitary wave solutions to the space-time fractional differential equations with conformable derivative. AIMS Mathematics, 2019, 4(2): 199-214. doi: 10.3934/math.2019.2.199 |
[4] | Naher Mohammed A. Alsafri, Hamad Zogan . Probing the diversity of kink solitons in nonlinear generalised Zakharov-Kuznetsov-Benjamin-Bona-Mahony dynamical model. AIMS Mathematics, 2024, 9(12): 34886-34905. doi: 10.3934/math.20241661 |
[5] | Ghazala Akram, Maasoomah Sadaf, Mirfa Dawood, Muhammad Abbas, Dumitru Baleanu . Solitary wave solutions to Gardner equation using improved tan(Ω(Υ)2)-expansion method. AIMS Mathematics, 2023, 8(2): 4390-4406. doi: 10.3934/math.2023219 |
[6] | Behzad Ghanbari, Mustafa Inc, Abdullahi Yusuf, Dumitru Baleanu . New solitary wave solutions and stability analysis of the Benney-Luke and the Phi-4 equations in mathematical physics. AIMS Mathematics, 2019, 4(6): 1523-1539. doi: 10.3934/math.2019.6.1523 |
[7] | Ghazala Akram, Saima Arshed, Maasoomah Sadaf, Hajra Mariyam, Muhammad Nauman Aslam, Riaz Ahmad, Ilyas Khan, Jawaher Alzahrani . Abundant solitary wave solutions of Gardner's equation using three effective integration techniques. AIMS Mathematics, 2023, 8(4): 8171-8184. doi: 10.3934/math.2023413 |
[8] | Wei Gao, Gulnur Yel, Haci Mehmet Baskonus, Carlo Cattani . Complex solitons in the conformable (2+1)-dimensional Ablowitz-Kaup-Newell-Segur equation. AIMS Mathematics, 2020, 5(1): 507-521. doi: 10.3934/math.2020034 |
[9] | Aly R. Seadawy, Bayan Alsaedi . Contraction of variational principle and optical soliton solutions for two models of nonlinear Schrödinger equation with polynomial law nonlinearity. AIMS Mathematics, 2024, 9(3): 6336-6367. doi: 10.3934/math.2024309 |
[10] | Abdelkader Moumen, Khaled A. Aldwoah, Muntasir Suhail, Alwaleed Kamel, Hicham Saber, Manel Hleili, Sayed Saifullah . Investigation of more solitary waves solutions of the stochastics Benjamin-Bona-Mahony equation under beta operator. AIMS Mathematics, 2024, 9(10): 27403-27417. doi: 10.3934/math.20241331 |
Solving completely integrable models is very important for observing and meaning dynamical behaviors of the physical systems. The shallow water wave model is one of the completely integrable models illustrating many physical problems. Euler is the first derived the water wave model in the 18th century. Using many models in applied mathematics and in physics such as Boussinesq equations, KdV equation, Davey–Stewarts on equation, Kadomtsev–Petviashvili (KP) equation, Benjamin–Bona–Mahony (BBM) equation are derived by Euler equations. The Benney–Luke equation is also water wave approximation to the Euler equation.
The KdV equation and the Benjamin–Bona–Mahony describe water waves that travel mainly in one direction. The Benney–Luke equation allows two-directional approximation to the Euler equations [1,2]. The KP equation is the 2D general form of KdV equation. It describes long wavelength water waves in a weak dispersion medium. The Benjamin–Bona–Mahony (BBM) equation is also known regularized long-wave equation is an improvement form of KdV equation. It is derived to model long waves propagation in nonlinear dispersion. The KP equation and the BBM equations are used to symbolize for acoustic waves in fluids, long wavelength surface wave in liquids.
In this study we consider the combined the two equations which is KP-BBM equation given as [3];
(ut+ux−a(u2)x−buxxt)x+kuyy=0, | (1) |
where a,b,k are constants and non-zero.
Many scientists have investigated the KP-BBM equation via various methods. In [4], the bifurcation of solitary waves of Eq. (1) is studied. The (3+1)-dimensional KP-BBM equation has been extracted to find analytical solutions by the auxiliary equation method [5]. Trigonometric and hyperbolic function solutions have been presented by new generalized (G′/G) expansion method [6]. The bell-shaped solitary wave and periodic wave solutions of KP-BBM equation have been obtained by bifurcation method and analyzed relation between of solutions under the different conditions [7]. The KP-BBM equation has been turned into Hirota bilinear form and obtained lump solutions by this way. The authors have investigated interactions lump-kink solutions and lump-soliton solutions [8].
In this work, we consider the Benney-Luke equation, the other model is derived from 3-dimensional Euler’s equation.
The Benney-Luke equation is given by [9,10]
utt−uxx+αuxxxx−βuxxtt+utuxx+2uxuxt=0, | (2) |
where are arbitrary constants such that, is the Bond number capturing the effects of surface tension and gravity forces. Eq. (2) models an approximation of the full water wave equation and is formally suitable to describe the two way propagation of water waves in the presence of surface tension. Firstly, Eq. (2) is presented by Benney and Luke [11]. There are comprehensive studies such as numerical studies, stability analysis, traveling wave solutions, analytical solutions, Cauchy problem on this equation in the literature [1,9,10,11,12,13,14,15].
The shallow water wave equations used in geophysical fluid dynamics, oceanography, coastal engineering and atmospheric science. Especially, in the past fifty years, solitary waves and soliton solutions have been intensively studied in mathematical, physical and engineering fields. Some powerful methods are recommended to find solitary wave solutions such as Hirota’s method [16], inverse scattering transform method [17], the solitary wave ansatz method [18,19], the tanh method [20], the extended auxiliary equation mapping, the extended direct algebraic mapping methods [21,22,23,24,25,26,27,28,29,30,31,32,33], Riemann–Hilbert method [34,35], the Lie symmetry method [36,37], and many others [38,39,40,41,42,43].
In this study, we focus on the sine-Gordon expansion method to construct to exact solutions of the KP-BBM equation and the Benney–Luke equation.
This paper rested as, the general properties of the mentioned method are given in Section 2. To obtain the soliton solutions the SGEM is applied to Eqs. (1) and (2), then 2D, 3D and contour simulations of the new solutions are plotted in Section 3. Finally, we give conclusion by submitted findings.
In this section, we describe SGEM. Firstly, we need to explain how we get two significant equations. We suppose that the sine-Gordon equation is given as following [44,45,46,47];
uxx−utt=m2sin(u), | (3) |
Where u=u(x,t), mis a real constant. Applying the wave transform u=u(x,t)=U(ξ),ξ=x−ctto Eq. (3), we get the following nonlinear ordinary differential equation;
U″=m2(1−c2)sin(U), | (4) |
Where U=U(ξ),ξ and care the amplitude and velocity of the travelling waves, respectively. We integrate Eq. (4) and it can be written as follows;
[(U2)′]2=m2(1−c2)sin2(U2)+K, | (5) |
Where K is the constant of integration. Substituting K=0,w(ξ)=U2 and a2=m2(1−c2)in Eq. (5), it yields;
w′=asin(w). | (6) |
Setting a=1 in Eq. (6), gives;
w′=sin(w). | (7) |
Solving Eq. (7) by variables separable, we obtain the two significant equations as;
sin(w)=sin(w(ξ))=2peξp2e2ξ+1|p=1=sech(ξ), | (8) |
cos(w)=cos(w(ξ))=p2e2ξ−1p2e2ξ+1|p=1=tanh(ξ), | (9) |
Where p is the integral constant and non-zero.
We suppose that the general nonlinear partial differential equation of the following form;
P(u,ux,ut,uxx,utt,uxt,...)=0, | (10) |
where u=u(x,t). We consider the solution of Eq. (10) as following expression,
U(ξ)=n∑i=1tanhi−1(ξ)[Bisech(ξ)+Aitanh(ξ)]+A0. | (11) |
Eq. (11) can be rearranged according to Eq. (8) and Eq. (9) as follows;
U(w)=n∑i=1cosi−1(w)[Bisin(w)+Aicos(w)]+A0. | (12) |
Using the homogenous balance principle to determine the value ofnbetween the highest power nonlinear term and highest derivative in the ordinary differential equation. We suppose that the summation of coefficients of sini(w)cosj(w) with the same power is zero, this yields an equation system. With aid of the computational program, we solve the equation system to find the values of Ai,Bi,μandc.Finally, substituting the values of Ai,Bi,μandcinto Eq. (11), we get the new travelling wave solutions to the Eq. (10).
In this section, we will present the application of the SGEM to the KP-BBM and the Benney–Luke equations.
Let consider the following wave transform as,
u(x,y,t)=U(ζ),ζ=x+y−ct. | (13) |
Using above transformation into Eq. (1), we get the following ordinary differential equation by integrating twice with respect to ζ,
(1+k−c)U−aU2+bcU″=0. | (14) |
We choose the integration constant to be zero. Balancing between U″ and U2gives n=2.
For the value n=2, the Eq. (12) takes the form,
U(w)=B1sin(w)+A1cos(w)+B2cos(w)sin(w)+A2cos2(w)+A0. | (15) |
Differentiating Eq. (15) twice, yields
U″(w)=−2A1cos(w)sin2(w)−4A2cos2(w)sin2(w)+2A2sin4(w)+B1cos2(w)sin(w)−B1sin3(w)+B2cos3(w)sin(w)−5B2cos(w)sin3(w). | (16) |
Substituting Eq. (15) and Eq. (16) into Eq. (14), we have a polynomial in term of trigonometric functions. Equating to zero all sum of coefficients of the same power of the trigonometric functions, we get the following algebraic equation system. Putting the values of the coefficients into Eq. (15), we obtain the following cases.
Case 1: When we consider as A0=−2b(1+k)a(1+b),A2=3b(1+k)a(1+b),B2=3ib(1+k)a(1+b), c=1+k1+b,A1=B1=0, gives following complex mixed dark-bright soliton solution,
u1=−2b(1+k)a(1+b)−3ib(1+k)a(1+b)Sech(f(x,y,t))Tanh(f(x,y,t))+3b(1+k)a(1+b)Tanh2(f(x,y,t)), | (17) |
where f(x,y,t)=(1+k)t1+b−x−y. Considering suitable values of parameters, various figures may be observed as in Figures 1 and 2.
Case 2: When we take coefficients as, A2=−3A02,B2=3iA02,b=−aA02c,k=−1+c−aA02,A1=B1=0,gives the following,
u2=A0(1+−3e2ct+3e2(x+y)2(ect−iex+y)2). | (18) |
Considering suitable values of parameters, various figures may be observed as in Figures 3 and 4.
Case 3: If A2=−A0,b=aA0−6(1+k)+4aA0,c=1+k−2aA03,A1=B1=B2=0,enable to write the solution as,
u3=A0−A0Tanh2[x+y−t(1+k−2aA03)]. | (19) |
We consider suitable values of parameters at above solution, then some figures may be observed as in Figures 5 and 6.
Case 4: Considering aswe find the
u4=−A0(e2(1+k)t1+b−e2(x+y)+4ie2(1+k)t1+b+x+y)2(e2(1+k)t1+b−iex+y)2. | (20) |
We found various figures for suitable values of parameters as Figures 7 and 8,
Let consider the following wave transform as,
u(x,t)=V(ζ),ζ=kx−ct. | (21) |
Using above transformation into Eq. (2), we get the following nonlinear ordinary differential equation,
(c2−k2)V″+(αk4−βk2c2)V4−3ck2V′V″=0. | (22) |
Integrating Eq. (22) with respect to ζonce, we find,
2(c2−k2)V′+2(αk4−βk2c2)V‴−3ck2(V′)2=0. | (23) |
After getting transform V′=U, we can write as
2(c2−k2)U+2(αk4−βk2c2)U″−3ck2U2=0. | (24) |
We choose the integration constant to be zero. Balancing between U″ and U2 gives n=2.
Substituting Eq. (15) and Eq. (16) into Eq. (24), we have a polynomial in term of trigonometric functions.
Equating to zero all sum of coefficients of the same power of the trigonometric functions, we get the following algebraic equation system. Putting the values of the coefficients into Eq. (15), we obtain the following cases.
Case 1: When we consider A0=−2iB23,A2=iB2,β=−12i(B2c+4α−2i+B2c),k=−(1+i)c√2i−B2c,A1=B1=0,gives the following complex mixed dark-bright soliton solution,
u1=13iB2(−ct−(1+i)cx√2i−B2c+3iSech[ct+(1+i)cx√2i−B2c]+3Tanh[ct+(1+i)cx√2i−B2c]). | (25) |
We consider suitable values of parameters to Eq. (25), then some figures may be observed as in Figures 9 and 10.
Case 2: If we take following coefficients, A0=c2−k2+5|c2−k2|3ck2,A2=−2|c2−k2|ck2,B2=2ic−2ick2,α=−|c2−k2|+c2k2βk4,A1=B1=0,enable to write the solution as,
u2=(c2−k2−|c2−k2|)(−ct+kx)+6i(c2−k2)Sech[ct−kx]−6|c2−k2|Tanh[ct−kx]3ck2. | (26) |
We consider suitable values of parameters at above solution, then some figures may be observed as in Figures 11 and 12.
Case 3: When the coefficients are taken as, A0=−2A23,B2=iA2,α=(2+A2c)(A2+2cβ)4c,k=−c√22+A2c,A1=B1=0,we find another dark soliton solution,
u3=13A2(−ct−cx√22+A2c−3iSech[ct+cx√22+A2c]+3Tanh[ct+cx√22+A2c]). | (27) |
Taking suitable values of parameters, various figures may be observed as in Figures 13 and 14.
Case 4: When we consider following coefficients,
A0=4k(−α+β)√(−1+4k2α)(−1+4k2β),A2=4k(α−β)√(−1+4k2α)(−1+4k2β),c=−k√−1+4k2α−1+4k2β,A1=B1=B2=0, |
gives the following,
u4=4k(−α+β)Tanh[kx+kt√−1+4k2α−1+4k2β]√(−1+4k2α)(−1+4k2β). | (28) |
We found various figures for suitable values of parameters as above Figures 15 and 16.
Case 5:A0=√2(α−β)√−α−β,A2=√2(−α+β)√−α−β,B2=√2(α−β)2α+β,c=√−α−β√2β,k=iβ,A1=B1=0,gives us,
u5=√2Sech[t√−α−β√2β−ix√β](−|α−β|√−α−β−(α−β)√α+βSinh[t√−α−β√2β−ix√β])i|α+β|. | (29) |
Taking suitable values of parameters in Eq. (29), we found some simulations as in Figures 17 and 18.
We would like to thank you for following the instructions above very closely in advance. It will definitely save us lot of time and expedite the process of your paper's publication.
We consider the sine-Gordon expansion method which is based on sine-Gordon equation to construct new type solution to Eq. (1) and Eq. (2). In the literature, there have been many techniques submitted such as Lie symmetry analysis, extended auxiliary equation mapping, extended direct algebraic mapping method, Hirota bilinear method, reductive perturbation technique. Kink, anti-kink solutions, lump solutions, line soliton, periodic waves and others have been shown by these mathematical tools. When we compare our results with other solutions, one can see that complex structure of obtained solutions are the feature that distinguishes it from others. Complex dark soliton, complex bright soliton solutions have more general structure than obtained by other techniques. In physics, complex calculus is considered to be of a formal mathematical, auxiliary type. Physical quantities can currently be defined by negative as well as by irrational number. Complex quantities extend some concepts as stability, convergence, conservation laws to reality. Consequently, complex-valued solutions can be verified in the experimental tests by physicist and engineers.
Complex numbers are particularly useful in explaining wave propagation. It is much easier to deal with the wave equation if we consider complex solutions. Since complex representation makes it much simpler to manage wave super-positions. If the refractive index of wave is enabled to be complex, the wave equation can be used to explain wave amplification and wave attenuation. In physical meaning, amplified waves are the fundamental basis for lasers when attenuated waves explain the absorption of light into black surfaces or the dissipation of sound into ambient heat [48].
Therefore, it is estimated that the results found in this paper may be used to explain such relationship of the governing models.
In this work, we have successfully performed SGEM to construct new complex combined dark-bright soliton solutions of the KP-BBM and the Benney–Luke equation. We have obtained many new soliton solutions. We observed that providing all solutions the mentioned two nonlinear partial differential equations by using a software. When we compare the SGEM with other analytical methods such as the extended tanh method, the new generalized (G′/G)-expansion method, the auxiliary equation method, we can deduce that this method is very effective and powerful tool for nonlinear models. To the best of our knowledge, these new complex combined dark-bright soliton solutions have been firstly submitted to the literature. It may be observed that wave behavior have shown their estimated wave propagations and distributions, physically, in Figures 1–18. Moreover, the submitted solutions may be helpful understanding physical phenomena especially in oceanography, geophysical science. The results show that the proposed method can be efficiently used to such completely integrable equations.
The authors declare no conflict of interest.
[1] | M. Parigot, Free Deduction: An Analysis of "Computations" in Classical Logic, In: A. Voronkov, editors. Logic Programming Lecture Notes in Artificial Intelligence 592, Berlin, Heidelberg: Springer-Verlag, 1992, 361-380. |
[2] | M. Parigot, λμ-calculus: An algorithmic interpretation of classical natural deduction, In: A. Voronkov, editors. Logic Programming and Automated Reasoning, LPAR 1992, Lecture Notes in Artificial Intelligence 624, Berlin, Heidelberg: Springer-Verlag, 1992, 190-201. |
[3] |
K. Nour, La valeur d'un entier classique en λμ-calcul, Archive Math. Logic, 36 (1997), 461-473. doi: 10.1007/s001530050076
![]() |
[4] |
P. de Groote, An environment machine for the λμ-calculus, Math. Struct. Comput. Sci., 8 (1998), 637-669. doi: 10.1017/S0960129598002667
![]() |
[5] | W. Py, Confluence en λμ-calcul [dissertation], University of Chambéry, 1998, 117. |
[6] |
A. Saurin, Böhm theorem and Böhm trees for the Λμ-calculus, Theor. Comput. Sci., 435 (2012), 106-138. doi: 10.1016/j.tcs.2012.02.027
![]() |
[7] | E. Polonovsky, Substitutions explicites, logique et normalisation [dissertation], Paris 7, 2004, 257. |
[8] | R. David, K. Nour, Arithmetical proofs of strong normalization results for symmetric lambda calculi, Fundamenta Informaticae, 77 (2007), 489-510. |
[9] | P. Battyányi, Normalization properties of symmetric logical calculi [dissertation], University of Chambéry, 2007, 118. |
1. | M.F. Uddin, M.G. Hafez, Z. Hammouch, H. Rezazadeh, D. Baleanu, Traveling wave with beta derivative spatial-temporal evolution for describing the nonlinear directional couplers with metamaterials via two distinct methods, 2021, 60, 11100168, 1055, 10.1016/j.aej.2020.10.030 | |
2. | Najva Aminakbari, Yongyi Gu, Wenjun Yuan, Meromorphic exact solutions of the (2 + 1)-dimensional generalized Calogero-Bogoyavlenskii-Schiff equation, 2020, 18, 2391-5455, 1342, 10.1515/math-2020-0099 | |
3. | Jalil Manafian, Onur Alp Ilhan, Sherin Youns Mohyaldeen, Subhiya M. Zeynalli, Gurpreet Singh, New strategic method for fractional mitigating internet bottleneck with quadratic–cubic nonlinearity, 2021, 2008-1359, 10.1007/s40096-020-00373-2 | |
4. | Shafqat ur Rehman, Jamshad Ahmad, Modulation instability analysis and optical solitons in birefringent fibers to RKL equation without four wave mixing, 2021, 60, 11100168, 1339, 10.1016/j.aej.2020.10.055 | |
5. | Mohammad Safi Ullah, M. Zulfikar Ali, N.F.M. Noor, Novel dynamics of wave solutions for Cahn–Allen and diffusive predator–prey models using MSE scheme, 2021, 3, 26668181, 100017, 10.1016/j.padiff.2020.100017 | |
6. | S.C. Shiralashetti, Lata Lamani, Fibonacci wavelet based numerical method for the solution of nonlinear Stratonovich Volterra integral equations, 2020, 10, 24682276, e00594, 10.1016/j.sciaf.2020.e00594 | |
7. | Run-Fa Zhang, Sudao Bilige, Jian-Guo Liu, Mingchu Li, Bright-dark solitons and interaction phenomenon for p-gBKP equation by using bilinear neural network method, 2020, 96, 1402-4896, 025224, 10.1088/1402-4896/abd3c3 | |
8. | Behzad Ghanbari, Chun-Ku Kuo, Abundant wave solutions to two novel KP-like equations using an effective integration method, 2021, 96, 0031-8949, 045203, 10.1088/1402-4896/abde5a | |
9. | Mst Shekha Khatun, Md Fazlul Hoque, Md Azizur Rahman, A class of localized soliton and fractal pattern solutions of the (2 + 1)-dimensional modified dispersive long wave model, 2020, 95, 1402-4896, 085219, 10.1088/1402-4896/aba585 | |
10. | Seyyedeh Roodabeh Moosavi Noori, Nasir Taghizadeh, Modified differential transform method for solving linear and nonlinear pantograph type of differential and Volterra integro-differential equations with proportional delays, 2020, 2020, 1687-1847, 10.1186/s13662-020-03107-9 | |
11. | Dan Zhao, , Three-wave interactions in a more general (2+1)-dimensional Boussinesq equation, 2020, 135, 2190-5444, 10.1140/epjp/s13360-020-00629-9 | |
12. | Shahzad Sarwar, New soliton wave structures of nonlinear (4 + 1)-dimensional Fokas dynamical model by using different methods, 2021, 60, 11100168, 795, 10.1016/j.aej.2020.10.009 | |
13. | Xinting Hu, Muhammad Arshad, Lu Xiao, Naila Nasreen, Ambreen Sarwar, Bright-dark and multi wave novel solitons structures of Kaup-Newell Schrödinger equations and their applications, 2021, 60, 11100168, 3621, 10.1016/j.aej.2021.02.018 | |
14. | K. S. Al-Ghafri, E. V. Krishnan, Optical Solitons in Metamaterials Dominated by Anti-cubic Nonlinearity and Hamiltonian Perturbations , 2020, 6, 2349-5103, 10.1007/s40819-020-00896-1 | |
15. | Archana C. Varsoliwala, Twinkle R. Singh, Mathematical modeling of tsunami wave propagation at mid ocean and its amplification and run-up on shore, 2021, 24680133, 10.1016/j.joes.2021.03.003 | |
16. | Xin Zhao, Bo Tian, Qi-Xing Qu, He Li, Xue-Hui Zhao, Chen-Rong Zhang, Su-Su Chen, Kadomtsev-Petviashvili hierarchy reduction, soliton and semi-rational solutions for the (3+1)-dimensional generalized variable-coefficient shallow water wave equation in a fluid, 2021, 0020-7160, 1, 10.1080/00207160.2021.1915999 | |
17. | Yin Yang, Guoting Deng, Emran Tohidi, High accurate convergent spectral Galerkin methods for nonlinear weakly singular Volterra integro-differential equations, 2021, 40, 2238-3603, 10.1007/s40314-021-01469-8 | |
18. | Hadi Rezazadeh, Waleed Adel, Mostafa Eslami, Kalim U. Tariq, Seyed Mehdi Mirhosseini-Alizamini, Ahmet Bekir, Yu-Ming Chu, On the optical solutions to nonlinear Schrödinger equation with second-order spatiotemporal dispersion, 2021, 19, 2391-5471, 111, 10.1515/phys-2021-0013 | |
19. | S. N. Raw, P. Mishra, B. P. Sarangi, B. Tiwari, Appearance of Temporal and Spatial Chaos in an Ecological System: A Mathematical Modeling Study, 2021, 1028-6276, 10.1007/s40995-021-01139-8 | |
20. | Khalid K. Ali, M. S. Mehanna, On some new soliton solutions of (3 + 1)-dimensional Boiti–Leon–Manna–Pempinelli equation using two different methods, 2021, 28, 2576-5299, 234, 10.1080/25765299.2021.1927498 | |
21. | H. Jafari, K. Goodarzi, M. Khorshidi, V. Parvaneh, Z. Hammouch, Lie symmetry and μ-symmetry methods for nonlinear generalized Camassa–Holm equation, 2021, 2021, 1687-1847, 10.1186/s13662-021-03471-0 | |
22. | Na Zhao, Jalil Manafian, Onur Alp Ilhan, Gurpreet Singh, Rana Zulfugarova, Abundant interaction between lump and k-kink, periodic and other analytical solutions for the (3+1)-D Burger system by bilinear analysis, 2021, 35, 0217-9792, 2150173, 10.1142/S0217979221501733 | |
23. | M. Hafiz Uddin, U.H.M. Zaman, Mohammad Asif Arefin, M. Ali Akbar, Nonlinear dispersive wave propagation pattern in optical fiber system, 2022, 164, 09600779, 112596, 10.1016/j.chaos.2022.112596 | |
24. | Yan Cao, Hayder A. Dhahad, Fahd Jarad, Kamal Sharma, Ali A. Rajhi, A.S. El-Shafay, Shima Rashidi, Shahram Rezapour, S.A. Najati, Ayman A. Aly, Abdulaziz H. Alghtani, Muhammad Bilal Riaz, Extracting novel categories of analytical wave solutions to a nonlinear Schrödinger equation of unstable type, 2021, 31, 22113797, 105036, 10.1016/j.rinp.2021.105036 | |
25. | K. Hosseini, M. Mirzazadeh, D. Baleanu, N. Raza, C. Park, A. Ahmadian, S. Salahshour, The generalized complex Ginzburg–Landau model and its dark and bright soliton solutions, 2021, 136, 2190-5444, 10.1140/epjp/s13360-021-01637-z | |
26. | U.H.M. Zaman, Mohammad Asif Arefin, M. Ali Akbar, M. Hafiz Uddin, Analytical behavior of soliton solutions to the couple type fractional-order nonlinear evolution equations utilizing a novel technique, 2022, 61, 11100168, 11947, 10.1016/j.aej.2022.05.046 | |
27. | Mohammad Safi Ullah, Fahad Sameer Alshammari, M. Zulfikar Ali, Collision phenomena among the solitons, periodic and Jacobi elliptic functions to a (3+1)-dimensional Sharma-Tasso-Olver-like model, 2022, 36, 22113797, 105412, 10.1016/j.rinp.2022.105412 | |
28. | Muhammad Bilal, Jingli Ren, Usman Younas, Stability analysis and optical soliton solutions to the nonlinear Schrödinger model with efficient computational techniques, 2021, 53, 0306-8919, 10.1007/s11082-021-03040-5 | |
29. | Ziqiang Li, Jalil Manafian, Natig Ibrahimov, Afandiyeva Hajar, Kottakkaran Sooppy Nisar, Wasim Jamshed, Variety interaction between k-lump and k-kink solutions for the generalized Burgers equation with variable coefficients by bilinear analysis, 2021, 28, 22113797, 104490, 10.1016/j.rinp.2021.104490 | |
30. | Asıf Yokuş, Hatice Taskesen, Mohanad Alaloush, Betül Deniz Demirdaǧ, On the peakon solutions of some stochastic nonlinear evolution equations, 2021, 53, 0306-8919, 10.1007/s11082-021-03240-z | |
31. | Serbay Duran, Extractions of travelling wave solutions of (2 + 1)-dimensional Boiti–Leon–Pempinelli system via (Gʹ/G, 1/G)-expansion method, 2021, 53, 0306-8919, 10.1007/s11082-021-02940-w | |
32. | Abdullahi Yusuf, Tukur Abdulkadir Sulaiman, Evren Hincal, Dumitru Baleanu, Lump, its interaction phenomena and conservation laws to a nonlinear mathematical model, 2022, 7, 24680133, 363, 10.1016/j.joes.2021.09.006 | |
33. | Mohammad Asif Arefin, Md. Abu Saeed, M. Ali Akbar, M. Hafiz Uddin, Analytical behavior of weakly dispersive surface and internal waves in the ocean, 2022, 7, 24680133, 305, 10.1016/j.joes.2021.08.012 | |
34. | Jianming Qi, Qinghao Zhu, Further results about the non-traveling wave exact solutions of nonlinear Burgers equation with variable coefficients, 2023, 46, 22113797, 106285, 10.1016/j.rinp.2023.106285 | |
35. | Jasvinder Singh Virdi, Some New Solutions of Non Linear Evolution Equations With Mutable Coefficients, 2021, 7, 2297-4687, 10.3389/fams.2021.631052 | |
36. | Khalid K. Ali, M. S. Mehanna, M. Ali Akbar, Prasun Chakrabarti, Kenan Yildirim, Analytical Soliton Solutions of the Coupled Radhakrishnan-Kundu-Lakshmanan Equation via Three Techniques, 2022, 2022, 2314-4785, 1, 10.1155/2022/8419403 | |
37. | Souleymanou Abbagari, Alphonse Houwe, Serge Y. Doka, Thomas B. Bouetou, Mustafa Inc, Kofane T. Crepin, W-shaped profile and multiple optical soliton structure of the coupled nonlinear Schrödinger equation with the four-wave mixing term and modulation instability spectrum, 2021, 418, 03759601, 127710, 10.1016/j.physleta.2021.127710 | |
38. | U. H. M. Zaman, Mohammad Asif Arefin, M. Ali Akbar, M. Hafiz Uddin, Explore dynamical soliton propagation to the fractional order nonlinear evolution equation in optical fiber systems, 2023, 55, 0306-8919, 10.1007/s11082-023-05474-5 | |
39. | Chen Wang, Hou-ping Dai, Meng-jun Li, Ying-xin Feng, Higher-order breather, lump and hybrid solutions of (2 + 1)-dimensional coupled nonlinear evolution equations with time-dependent coefficients, 2023, 100, 0020-7160, 1860, 10.1080/00207160.2023.2219349 | |
40. | Laila A. AL-Essa, Mati ur Rahman, Analysis of Lie symmetry, bifurcations with phase portraits, sensitivity and diverse W − M-shape soliton solutions for the (2 + 1)-dimensional evolution equation, 2024, 525, 03759601, 129928, 10.1016/j.physleta.2024.129928 | |
41. | U. H. M. Zaman, Mohammad Asif Arefin, M. Ali Akbar, M. Hafiz Uddin, Shou-Fu Tian, Study of the soliton propagation of the fractional nonlinear type evolution equation through a novel technique, 2023, 18, 1932-6203, e0285178, 10.1371/journal.pone.0285178 | |
42. | S. M. Rayhanul Islam, Kamruzzaman Khan, Muhammad Aqeel, Investigating wave solutions and impact of nonlinearity: Comprehensive study of the KP-BBM model with bifurcation analysis, 2024, 19, 1932-6203, e0300435, 10.1371/journal.pone.0300435 | |
43. | Mohammad Izadi, Sandeep Kumar Yadav, Giriraj Methi, Two efficient numerical techniques for solutions of fractional shallow water equation, 2024, 9, 26668181, 100619, 10.1016/j.padiff.2024.100619 | |
44. | Nilkanta Das, S. Saha Ray, 2023, Bright and singular optical soliton solutions of modified nonlinear Schrödinger equation with conformable fractional derivative in deep water waves, 979-8-3503-2168-5, 1, 10.1109/ICFDA58234.2023.10153356 | |
45. | Neeraj Sharma, Manoj Mishra, Soumendu Jana, Generation, dynamics, and stability analysis of diffraction managed soliton in patterned metamaterial, 2024, 0972-8821, 10.1007/s12596-024-02421-9 | |
46. | Mehmet Şenol, Furkan Muzaffer Çelik, Analytical and numerical study on the solutions of a new (2+1)-dimensional conformable shallow water wave equation, 2024, 74, 1303-5991, 1, 10.31801/cfsuasmas.1441503 | |
47. | Osama Alkhazaleh, Osama Ala’yed, Manzoor Hussain, A Study of Solutions for Some Classes of PDEs Arising in Physics and Engineering Using Modified Reduced Differential Transform Method, 2025, 2025, 1110-757X, 10.1155/jama/6866952 | |
48. | Ikram Ullah, Muhammad Bilal, Javed Iqbal, Alamgir Khan, Zareen A. Khan, Novel travelling wave solutions to space-time fractional Cahn-Allen equation via generalized extended direct algebraic method, 2025, 1598-5865, 10.1007/s12190-025-02512-1 | |
49. | Aly R. Seadawy, Asghar Ali, Ahmet Bekir, Adem C. Cevikel, Murat Alp, Novel exact solutions to the fractional PKP equation via mathematical methods, 2025, 0217-7323, 10.1142/S0217732325500993 |