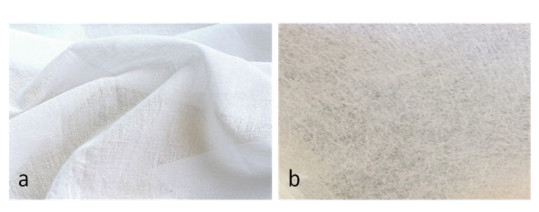
Citation: Albert Uchenna Ude, Che Husna Azhari. Lateral crashworthiness response of bombyx mori fibre/glass–fibre/epoxy hybrid composite cylindrical tubes-experimental[J]. AIMS Materials Science, 2019, 6(6): 1227-1239. doi: 10.3934/matersci.2019.6.1227
[1] | Albert Uchenna Ude, Che Husna Azhari . Crashworthiness response of natural silk-fibre glass hybrid reinforced epoxy cylindrical composite tubes under quasi-static load. AIMS Materials Science, 2019, 6(5): 852-863. doi: 10.3934/matersci.2019.5.852 |
[2] | Sanna Virtanen, Lisa Wikström, Kirsi Immonen, Upi Anttila, Elias Retulainen . Cellulose kraft pulp reinforced polylactic acid (PLA) composites: effect of fibre moisture content. AIMS Materials Science, 2016, 3(3): 756-769. doi: 10.3934/matersci.2016.3.756 |
[3] | M. Rajanish, N. V. Nanjundaradhya, Ramesh S. Sharma, H. K. Shivananda, Alok Hegde . Directional Interlaminar Shear Strength (ILSS) of nano-modified epoxy/unidirectional glass fibre composite. AIMS Materials Science, 2018, 5(4): 603-613. doi: 10.3934/matersci.2018.4.603 |
[4] | Md Shamsuddoha, Md Mainul Islam, Thiru Aravinthan, Allan Manalo, Luke P. Djukic . Effect of hygrothermal conditioning on the mechanical and thermal properties of epoxy grouts for offshore pipeline rehabilitation. AIMS Materials Science, 2016, 3(3): 832-850. doi: 10.3934/matersci.2016.3.832 |
[5] | Timothy K. Mulenga, Albert U. Ude, Chinnasamy Vivekanandhan . Concise review on the mechanical characteristics of hybrid natural fibres with filler content. AIMS Materials Science, 2020, 7(5): 650-664. doi: 10.3934/matersci.2020.5.650 |
[6] | Prashant Tripathi, Vivek Kumar Gupta, Anurag Dixit, Raghvendra Kumar Mishra, Satpal Sharma . Development and characterization of low cost jute, bagasse and glass fiber reinforced advanced hybrid epoxy composites. AIMS Materials Science, 2018, 5(2): 320-337. doi: 10.3934/matersci.2018.2.320 |
[7] | Dominik Flore, Konrad Wegener . Influence of fibre volume fraction and temperature on fatigue life of glass fibre reinforced plastics. AIMS Materials Science, 2016, 3(3): 770-795. doi: 10.3934/matersci.2016.3.770 |
[8] | Zulzamri Salleh, Md Mainul Islam, Jayantha Ananda Epaarachchi, Haibin Su . Mechanical properties of sandwich composite made of syntactic foam core and GFRP skins. AIMS Materials Science, 2016, 3(4): 1704-1727. doi: 10.3934/matersci.2016.4.1704 |
[9] | Sohel Rana, Subramani P, Raul Fangueiro, Antonio Gomes Correia . A review on smart self-sensing composite materials for civil engineering applications. AIMS Materials Science, 2016, 3(2): 357-379. doi: 10.3934/matersci.2016.2.357 |
[10] | Abdul Saboor Karzad, Moussa Leblouba, Zaid A. Al-Sadoon, Mohamed Maalej, Salah Altoubat . Modeling the flexural strength of steel fibre reinforced concrete. AIMS Materials Science, 2023, 10(1): 86-111. doi: 10.3934/matersci.2023006 |
Owing to properties such as strength-to-weight-ratio, corrosion inactiveness, stiffness, easy formability and other, composite structures has find its way into many manufacturing industries including but not limited to automobiles, aerospace, marine, sports and construction. Presently, their degree of acceptance and percentage of usage in fabrication of aerospace component parts has increased rapidly in the last decade; many automobile manufacturers have also increased their usage of composite component parts in their automobiles, citing government legislations, environment friendly materials, light weight, as well as aesthetics, to mention but a few. During the in-service time, unfortunately these component parts are prone to different kind of stresses and loadings. Failures due to induced stresses via tensile and compression loading on the composite structures has caused devastating damages in the past and has remained a hot research focus for some decades now. Researchers all around the globe are constantly in search of new materials with superior material characteristics or new approach that can answer to some drawbacks encountered during applications. One such drawback in the application of composites is the unpredictable failure characteristics of composites structures during external impact. Impact on a composite structure may be classified in the range of its velocity as, low, medium or high velocity; and in-terms of surface as axial, or transverse impact.
Literature review reveals that many research works have been carried out to investigate axial crushing behaviors of varied composite tubes of varied geometries [1,2,3,4,5,6,7,8,9,10], fewer investigations have been carried out on the lateral crashworthiness performance of composite structures [11,12,13,14] and no report was recorded on the lateral crashworthiness performance of bombyx mori silk fibre or bombyx mori silk fibre/glass–fibre/epoxy hybrid composite cylindrical tubes, the reason for which this investigation was carried out. Sebaey and Mahdi [15] reported that if an external object strikes a composite structure perpendicular to its surface, it can damage both its static and fatigue load-bearing capacities. Absobaia et al. [14] reported that segmented cotton fibre/epoxy and carbon fibre/epoxy composite tubes, are effective crushing elements when subjected to laterally deformation loading. They also reported that tissue mat glass fibres composite tubes suffer from low energy absorption. It was also reported by Majid et al. that stiffening the composite cylindrical shells with lozenge grid stiffeners can increase the specific energy absorption almost twice in comparison with the unstiffened composite shell; the grid-stiffened structures compressed between two rigid flat platens also had the highest specific energy absorption when compared with the unstiffened structures compressed by the cylindrical indenter [16]. Other recent investigations on laterally deformed composites includes [17,18,19,20]. It is well established that composite structures are very susceptible to external impact loads. Axial deformation of composites structures generates greater resistance to fracture than lateral deformation due to the reinforced laminate arrangements. This investigation was carried out to improved lateral strength deformation in composite materials without compromising their weight. Some of the examples where composite structures are subjected to lateral deformations include oil and water pipe lines; airplane frames structures and recently, some automobile structures. No investigation has been carried out on the response of bombyx mori/epoxy composite cylindrical tubes deformed laterally.
This investigation is then focused on the quasi-static lateral impact response of varied cylindrical composite tubes. Their responses were measured via peak load, energy absorption, crushing efficiency as well as the nature of tube fragmentation. The test results were displayed and analyzed in subsequent sections below.
The materials used in this investigation were glass fibre, woven bombyx mori natural silk fibres, supplied by Loxevi silk; epoxy resin type (DER 331) and hardener type (905-35). The method of fabrication was by mandrel assisted hand lay-up, three categories of specimen were fabricated (1) glass fibre reinforced epoxy composite cylindrical tubes, (2) bombyx mori reinforced epoxy composite cylindrical tubes, (3) glass fibre/bombyx mori fibre hybrid reinforced epoxy composite cylindrical tubes. The length of each composite tube specimen was 80 mm, with an internal diameter of 65 mm and thickness of 15 mm respectively. The samples of bombyx mori fibre and glass fibre used were shown in Figure 1, while the schematics diagrams of the cylindrical composite specimens, used in the test were shown in Figure 2. All composite samples were manufactured at an ambient temperature.
The machine used to perform the experiment was an automated INSTRON MTS 810 universal testing machine, with loading capacity of 250 kN. The crosshead speed was kept constant at 20 mm/min throughout the experiment. Two rectangular flat plates as fixtures mounted in opposite direction were use to perform the test. Data generated during the test were collected from the computerized system and further analyzed.
The results obtained from the tests conducted in this study were displayed and discuss here. The load-displacement curves results are presented from the average results of three tests, owing to the fact that the fracture energy is much dependent on the specific failure mechanism which can vary from test to test even if all parameters are unvaried. Three specimens were tested from each composite configuration and their average values recoded. Figures 3a–d, 4a–e, 5a–d, show case photographs of failure fragmentation captured during the quasi-static laterally compressed load test of the composite specimens. Figures 3e, 4f, 5e show the load/displacement and energy curves obtained from the experimental tests. In Figures 7–10, the bar-chart was used for comparison analysis of characteristics like, peak load, energy absorption capability, crushing force efficiency and other features measured during the experimental test.
As shown in Figures 3a–d, 4a–e, 5a–d, deformations were initiated from any of the four cardinal points of the cylindrical tube marked A, B, C and D as shown in Figure 3a. Figures 3e, 4f, 5e show the corresponding load/displacement and energy curves of the investigated composite cylindrical tubes.
Analyzing the deformation in Figure 3a–d, by referring to locations A, B, C and D, observations show that the two halves ACB and ADB of the cylindrical tubes undergo identical deformation, rising to the formation of elastic hinges under the load at points A, B, C and D respectively. This phenomenon is attributed to the stress built-up on those points due to compression load induced on the composite tube by the quasi-static load testing plates. As the compression load continues, the composite tube tends to deform symmetrically, with the loaded opposite sides C and D deforming inward and the other opposite sides A and B deforming outward. This report agrees partially with an observation reported by Abosbaia et al. [14]. Figure 3d, showed the final collapse nature as two adjacent eyes shape, a similar failure mode shape was observed by Abdewi et al. [11] who also worked with woven roving glass fibre/epoxy laminated composite tube.
Figure 3e displays the typical load-displacement deformation curve and failure mechanism history as well as energy absorption curve of glass fibre/epoxy composite tube under lateral quasi-static compression test. Observation show that the load maintained an increasing linear progression until it reaches the first peak load at 6.8 kN and 5.28 mm displacement. The first peak load corresponds to initiation of failure in the composite tube and marking an end to linear increase, in this case, micro to macro cracks, as seen in Figure 3b. It is good to note a slight shift observed on the load curve just before a drop in load was finally observed. This behaviour was attributed to matrix micro cracks and reloading response of reinforced fibre composites. Once the first peak load was attained, a slight drop in load associated with macro cracking failure at the four cardinal points was observed. The second peak load which is slightly higher than the first was as a result of fibre reloading, the matrix transfers the load to the reinforcing component, in this case glass fibres which sustained the load before finally breaking at a peak load of 8.76 kN and approximately 11.93 mm displacement. It was observed that the energy-displacement curve increased slightly nonlinear until it reaches 98.99 J at 18.27 mm displacement. It then maintained a low energy absorption until it reaches 100.05 J at 23.4 mm displacement.
Figure 4a–e displays the result of the quasi-static lateral compressive load test of bombyx mori/epoxy composite tube. The four points A, B, C and D introduced to help analyze the lateral deformation in the previous figure under glass–fibre composite tube was also applied here to help explain the results of the present composite tube. As seen in Figure 4c, the bombyx mori/epoxy composite tube showed a symmetrical deformation; elastic hinges under load were first observed at C and D, as the compressive deformation progressed, slight elastic hinges were also seen at point A and B. At this stage observation also shows that the structure formed two similar shapes like an eye adjacent to each other. This observation continued until complete crushing of the structure was attained, compaction of the upper and lower half of the composite cylindrical tube was also observed. The failure behavior agrees to a similar failure mode observed and reported by Abdewi et al. [11].
In Figure 4f, the load-displacement deformation curve gives an interpretation of the behaviour of bombyx mori/epoxy composite tube under lateral compressive load. The curve showed a very close similarity with the typical stress-strain deformation curve of ductile materials, reflecting the ductile nature of bombyx mori silk. First peak load was assumed to occur at 0.59 kN and 10.46 mm displacement, followed by a neatly formed arc shape, which further expressed the ductility of the material under investigations. Further increase noticed in the load-displacement profile was as a result of reloading effect of the reinforced composite tube, the second peak load occurred at approximately 0.88 kN and 49 mm displacement respectively. Observation show that the energy-displacement curve of bombyx mori/epoxy composite tube under lateral compressive load continued a nonlinear increase until it reaches 30.5 J energy absorption at 50.7 mm displacement.
Figure 5 show the response of bombyx mori/glass–fibre/epoxy hybrid composite under lateral compressive load. Hybrid reinforced composite are those composites which have a combination of two or more reinforcement fibres or particulates whether in nano, micro or macro sizes. Hybrid composite are formed with predetermined intentions to utilize the strength of each individual fibre and produce a hybrid composite with better properties compared to any of the individual constituent or its composites. In the current investigation, bombyx mori fibre has an excellent ductility and elasticity properties. It is among the best natural fibres with good tensile property. Glass fibre on the other hand has a very good compression strength property, but has poor tensile property and vey brittle. It is in-view of these individual excellent properties that the hybridization idea was build upon.
The deformation mode observed in Figure 5a–d shows that the ACB which formed the upper half of the cylinder and ADB the bottom part of the cylinder, deformed in dissimilar manners. It was evidence that ACB half of the cylinder collapsed into ADB half of the cylinder; elastic hinges were formed at points A, C and B; delamination and crack failures were seen on the bottom half of the cylindrical surface (see Figure 5b–d). The failure fragmentation mode was slightly deferent from the previous two observations; the combine synergy of the individual materials properties was responsible for the failure mode observed. In Figure 5e, it shows that the crushing load increased linearly until it reaches the highest peak load value of 31.9 kN at 5.3 mm displacement. A drop in the load curve was observed immediately after the peak load was attained, signaling that a major deformation has taken place within the cylindrical hybrid composite tube. A reloading effect was seen as the curve tends to rise, but further deformation led to other significant drops in the load curve till it finally reaches the last lower peak load of 20.7 kN at 9.95 mm displacement. The energy-displacement curve on the hand increased linearly at a fast rate until it reached 197.5 J and a slow increase was observed till it reached 229.7 J. The report agrees with Cihan et al. [21] report on the woven flax/e–glass hybrid composite, who also reported that hybridization gives rise to the development of new material properties. It was evident that the hybrid composite tube outperformed the other two composite tubes both in load carrying capacity and energy absorption capability when compared.
The crashworthiness characteristics of any structure could be estimated by knowing different parameters, these parameters are estimated and illustrated in the below sections.
The energy absorption capability can be estimated using total energy absorption (Et) and specific energy absorption (Es). Total energy absorbed could be estimated as the area under the load-displacement curve. This parameter is a function of materials density and the cross-sectional area of the specimen under investigation. The value of the energy could be obtained from the numerical integration of the load displacement curve. A comparison of the investigated tubes shows that, hybrid composite tube had a better energy absorption capability than the other tubes, see Figure 6.
Specific energy absorption on the other hand is defined as the amount of energy absorbed per unit mass of crushed material. It is a vital parameter when comparing the energy capability of different materials or different specimen geometry. Figure 7 shows the specific energy absorption behavior of the three composite investigated, the hybrid composite tube clearly outperformed the other tubes. Specific energy absorption (Es) can be estimated mathematically as Eq 1,
(1) |
where Pavg refers to average load, A is the cross-sectional area of tube under investigation, and ρ stands for the density of the composite tube.
The peak load of reinforced composite structure is the maximum carriability load which the structure was able to withstand before it deformed as captured in Figure 8. Reports from the literatures [1,11,22] stated that this parameter is influenced by both the material properties of the laminates used, and the geometric parameters of the composite structure. On the other hand, the average peak load (Figure 9) is also a very vital parameter to properly define the energy absorption capability of the reinforced composite structures. It is therefore of paramount important that we investigate and understand the changes which occurs within the average loads. A comparison of the present structures under investigation show that B.mori/glass/epoxy hybrid composite tube had a higher value of 45.16 kN to outperform the other structures with 17.23 and 0.93 kN respectively. The distribution of the average load values was similar to that of the peak load, with the hybrid composite structure also having a higher value than the other two structures. The evidence before us in this investigation has again proven that hybridization improves some crashworthiness parameters like loads and energy attenuations.
Crushing force efficiency (CFE) is measured are the ratio between average crushing and initial crushing failure of the composite tubes. This parameter is useful when measuring the performance of absorbers like the tubes under investigation. It is expressed mathematically as Eq 2,
(2) |
where Pmax and Pavg are the maximum initial crushing load and average crushing load, respectively. This parameter Figure 10 shows that B.mori fibre/epoxy composite tube performed better than the other tubes when compared.
Fragmentation in composite structure under compressive loads begins to occur when the applied load exceeds the elastic limit of the structure. If a structure is loaded in a way that the stresses at every point is within the elastic limit, visible deformation may not be seen as they are in very micro level, the stresses at this point are proportional to applied load. With increase in the applied load above the elastic limit, micro-macro cracks are initiated in the composite structure signaling onset of deformation. The regions where these cracks were noticed first are regions where the local stress built-up has reached the maximum capacity the structure can carry. In the present study, all three structures initiated cracks from ABC or D points, as shown previously in Figure 3a–d. The local stress increased at these points as the load is further increased. The recovery capabilities of the structures were also investigated; B.mori composite tube displayed a high degree of recovery after the load was removed. This behaviour is attributed to the ductility property of bombyx mori natural silk laminates, see Figure 11a–c.
In this study, investigation of the behaviour of B.mori, glass and hybrid/epoxy fibres laminated composite tubes deformed laterally have been carried out experimentally under quasi-static laterally compressive load and below were the conclusions based on the results obtained from the test.
● A comparison of the three categories of cylindrical composite tubes investigated in this study has further shown that hybridization of reinforcement fibres can indeed produce materials with better properties in comparison with their individual composites.
● B.mori/epoxy composite tube performed better in crush force efficiency and rate of recovery after compression, this may be attributed to the ductile nature of B.mori natural silk.
● Failure mechanism was mainly micro to macro cracks due to induced stresses rising from continuous quasi-axial compressive load.
The authors are supported by the funding from the research fund of the Botswana International University of Science and Technology Palapye. University initiation grants No. R00073.
The authors would like to state that there is no conflict of interests. Email: udea@biust.ac.bw; husna.azhari@ukm.eng.
[1] |
Mamalis AG, Manolakos DE, Ioannidis MB, et al. (2004) Crashworthy characteristics of axially statically compressed thin-walled square CFRP composite tubes: experimental. Compos Struct 63: 347-360. doi: 10.1016/S0263-8223(03)00183-1
![]() |
[2] |
Ude AU, Ariffin AK, Azhari CH (2013) Impact damage characteristics in reinforced woven natural silk/epoxy composite face-sheet and sandwich foam, coremat and honeycomb materials. Int J Impact Eng 58: 31-38. doi: 10.1016/j.ijimpeng.2013.03.003
![]() |
[3] |
Ude AU, Eshkoor RA, Azhari CH (2017) Crashworthy characteristics of axial quasi-statically compressed bombyx mori composite cylindrical tubes: experimental. Fiber Polym 18: 1594-1601. doi: 10.1007/s12221-017-1235-1
![]() |
[4] |
Supian ABM, Sapuan SM, Zuhri MYM, et al. (2018) Hybrid reinforced thermoset polymer composite in energy absorption tube application: A review. Def Technol 14: 291-305. doi: 10.1016/j.dt.2018.04.004
![]() |
[5] |
Eshkoor RA, Ude AU, Oshkovr SA, et al. (2014) Failure mechanism of woven natural silk/epoxy rectangular composite tubes under axial quasi-static crushing test using trigger mechanism. Int J Impact Eng 64: 53-61. doi: 10.1016/j.ijimpeng.2013.09.004
![]() |
[6] |
Eshkoor RA, Ude AU, Sulong AB, et al. (2015) Energy absorption and load carrying capability of woven natural silk epoxy-triggered composite tubes. Compos Part B-Eng 77: 10-18. doi: 10.1016/j.compositesb.2015.03.017
![]() |
[7] |
Eshkoor RA, Oshkovr SA, Sulong AB, et al. (2013) Effect of trigger configuration on the crashworthiness characteristics of natural silk epoxy composite tubes. Compos Part B-Eng 55: 5-10. doi: 10.1016/j.compositesb.2013.05.022
![]() |
[8] |
Eshkoor RA, Oshkovr SA, Sulong AB, et al. (2013) Comparative research on the crashworthiness characteristics of woven natural silk/epoxy composite tubes. Mater Des 47: 248-257. doi: 10.1016/j.matdes.2012.11.030
![]() |
[9] |
Cormier JR, LaPlante G (2018) Study of the effects of low-velocity impact on a composite bicycle down tube. Compos Struct 198: 144-155. doi: 10.1016/j.compstruct.2018.05.007
![]() |
[10] |
Kathiresan M, Manisekar K (2017) Low velocity axial collapse behavior of E-glass fiber/epoxy composite conical frusta. Compos Struct 166: 1-11. doi: 10.1016/j.compstruct.2017.01.041
![]() |
[11] |
Abdewi EF, Sulaiman S, Hamouda AMS, et al. (2008) Quasi-static axial and lateral crushing of radial corrugated composite tubes. Thin Wall Struct 46: 320-332. doi: 10.1016/j.tws.2007.07.018
![]() |
[12] |
Fan Z, Shen J, Lu G (2011) Investigation of lateral crushing of sandwich tubes. Procedia Eng 14: 442-449. doi: 10.1016/j.proeng.2011.07.055
![]() |
[13] |
Mahdi ES, El Kadi H (2008) Crushing behavior of laterally compressed composite elliptical tubes: experiments and predictions using artificial neural networks. Compos Struct 83: 399-412. doi: 10.1016/j.compstruct.2007.05.009
![]() |
[14] |
Abosbaia AS, Mahdi E, Hamouda AMS, et al. (2005) Energy absorption capability of laterally loaded segmented composite tubes. Compos Struct 70: 356-373. doi: 10.1016/j.compstruct.2004.08.039
![]() |
[15] |
Sebaey TA, Mahdi E (2016) Crashworthiness of pre-impacted glass/epoxy composite tubes. Int J Impact Eng 92: 18-25. doi: 10.1016/j.ijimpeng.2015.11.007
![]() |
[16] |
Moeinifard M, Liaghat G, Rahimi G, et al. (2016) Experimental investigation on the energy absorption and contact force of unstiffened and grid-stiffened composite cylindrical shells under lateral compression. Compos Struct 152: 626-36. doi: 10.1016/j.compstruct.2016.05.067
![]() |
[17] | Ali AM, Robillard D, Masmoudi R, et al. (2019) Experimental investigation of bond and tube thickness effect on the flexural behavior of concrete-filled FPR tube under lateral cyclic loading. J King Saud Univ Eng Sci 31: 32-41. |
[18] |
Elahi SA, Rouzegar J, Niknejad A, et al. (2017) Theoretical study of absorbed energy by empty and foam-filled composite tubes under lateral compression. Thin Wall Struct 114: 1-10. doi: 10.1016/j.tws.2017.01.029
![]() |
[19] |
Liu Q, Xu X, Ma J, et al. (2017) Lateral crushing and bending responses of CFRP square tube filled with aluminum honeycomb. Compos Part B-Eng 118: 104-115. doi: 10.1016/j.compositesb.2017.03.021
![]() |
[20] |
Pol MH, Golshan NR (2019) Experimental investigation of parameters affected on behavior of composite tubes under quasi static and dynamic axial loading. Compos Part B-Eng 163: 471-486. doi: 10.1016/j.compositesb.2019.01.011
![]() |
[21] |
Cihan M, Sobey A, Blake JIR (2019) Mechanical and dynamic performance of woven flax/E-glass hybrid composites. Compos Sci Technol 172: 36-42. doi: 10.1016/j.compscitech.2018.12.030
![]() |
[22] |
Mamalis AG, Manolakos DE, Ioannidis MB, et al. (2005) On the response of thin-walled CFRP composite tubular components subjected to static and dynamic axial compressive loading: experimental. Compos Struct 69: 407-420. doi: 10.1016/j.compstruct.2004.07.021
![]() |
1. | Timothy K. Mulenga, Albert U. Ude, Chinnasamy Vivekanandhan, Techniques for Modelling and Optimizing the Mechanical Properties of Natural Fiber Composites: A Review, 2021, 9, 2079-6439, 6, 10.3390/fib9010006 | |
2. | Muhammad Nasir Amin, Waqas Ahmad, Kaffayatullah Khan, Ayaz Ahmad, A Comprehensive Review of Types, Properties, Treatment Methods and Application of Plant Fibers in Construction and Building Materials, 2022, 15, 1996-1944, 4362, 10.3390/ma15124362 | |
3. | Mehmet İskender Özsoy, Muhammet Muaz Yalçın, Lateral compression behavior of expanded polypropylene foam–filled carbon and glass fiber composite tubes, 2023, 65, 0025-5300, 1865, 10.1515/mt-2023-0120 | |
4. | Athul Joseph, Vishwas Mahesh, Vinyas Mahesh, Dineshkumar Harursampath, MAR Loja, Sumit Bhowmik, 2024, 9780323918664, 169, 10.1016/B978-0-323-91866-4.00003-2 | |
5. | Muhammet Muaz Yalçın, Mehmet İskender Özsoy, Lateral compression behavior of expanded polypropylene foam-filled carbon fiber reinforced polymer and aluminum/carbon fiber reinforced polymer composite tubes: An experimental study, 2023, 0731-6844, 10.1177/07316844231225034 |